
Petroleum FRP pipe is increasingly used in the petroleum industry due to its unique properties that make it ideal for harsh environments. FRP, or Fiberglass Reinforced Plastic, offers excellent resistance to corrosion, chemicals, and extreme temperatures, making it well-suited for transporting petroleum products. In petroleum applications, pipes are exposed to aggressive chemicals and high pressures, which can lead to degradation in traditional materials like steel. Petroleum FRP pipe addresses these challenges by providing a lightweight, durable solution that requires less maintenance and ensures long-lasting performance. Its strength, combined with its corrosion resistance, makes it an essential component in modern oil and gas infrastructure.
What Are Petroleum FRP Pipes?
Petroleum FRP pipes are specialized pipes made from Fiberglass Reinforced Plastic, designed for use in the extraction, transportation, and storage of petroleum products. These pipes combine the strength of fiberglass with the corrosion-resistant properties of plastic resins, creating a composite material that is exceptionally durable and well-suited for the harsh environments typical in the petroleum industry. FRP pipe bell and spigot joints are commonly used in these systems, providing secure, leak-free connections that are essential for maintaining the integrity of pipelines under high pressure and challenging conditions. Petroleum FRP Pipe have the characteristics of high strength and high pressure resistance used in many industries like oil & fuel handling. Petroleum FRP pipes offer a reliable and long-lasting solution for managing petroleum resources efficiently, especially where traditional materials may fail due to corrosion, chemical exposure, or extreme temperatures.
GRP Pipe in Petroleum Applications
GRP, or Glass Reinforced Plastic, is a type of FRP that is specifically designed to handle the demanding conditions of petroleum operations. GRP pipes are used extensively in petroleum applications, including oil and gas extraction, refining, and transportation. These pipes offer several advantages that make them an excellent choice for the petroleum sector. Their corrosion resistance ensures they remain unaffected by the various chemicals and substances encountered in the petroleum extraction process. This characteristic is crucial for maintaining the integrity of pipelines and reducing the risk of leaks or failures.
In addition to corrosion resistance, GRP pipes are lightweight, which makes them easier to transport and install compared to traditional materials like steel or concrete. This ease of installation is particularly beneficial in remote or offshore petroleum sites where logistical challenges can increase the complexity and cost of pipeline construction. GRP pipes from GangLong Fiberglass are designed to withstand high pressures and temperatures, ensuring safe and efficient transport of petroleum products over long distances.
Used Fiberglass Pipe for Sale: Is It a Viable Option?
The idea of purchasing used fiberglass pipes for petroleum applications can be appealing due to potential cost savings. However, several factors must be carefully considered before opting for second-hand FRP pipes in a petroleum setting. One of the primary concerns is the condition of the used pipes. Over time, even durable materials like FRP can suffer from wear and tear, especially if they have been exposed to harsh chemicals, extreme temperatures, or physical stress.
When evaluating used fiberglass pipes, it is essential to conduct a thorough inspection and testing process to assess their structural integrity. This process involves checking for signs of damage, such as cracks, delamination, or corrosion. Non-destructive testing methods, like ultrasonic inspection, can help identify any internal flaws that may not be visible to the naked eye. It is also important to review the service history of the used pipes to understand the conditions they were exposed to and how they were maintained.
Another consideration when purchasing used fiberglass pipes is compliance with current industry standards. Over time, standards and regulations governing petroleum infrastructure may change, and older pipes may not meet the latest requirements. Ensuring that the used pipes comply with current standards is crucial for maintaining safety and avoiding potential legal and environmental liabilities.
While the cost savings of using second-hand FRP pipes can be significant, the potential risks must be weighed carefully. In some cases, the investment in new, high-quality FRP pipes from GangLong Fiberglass may be justified by the increased reliability, longer service life, and reduced risk of failure.
Inspection and Testing Procedures for Used Fiberglass Pipes
Before integrating used fiberglass pipes into a petroleum infrastructure, a rigorous inspection and testing process must be undertaken. Visual inspection is the petroleum dw frp pipe, where the pipes are examined for obvious signs of wear and damage, such as surface cracks, scratches, or discoloration. While visual inspection can reveal some issues, it is often not sufficient to assess the internal condition of the pipes.
Non-destructive testing methods, such as ultrasonic testing, provide a more comprehensive evaluation of the pipes’ internal structure. Ultrasonic waves are used to detect internal flaws, including delamination, voids, or wall thinning that could compromise the pipes’ integrity. Other methods like radiographic inspection and hydrostatic testing may also be employed to ensure the pipes can withstand the pressures they will encounter in service.
Chemical analysis is another important aspect of inspecting used fiberglass pipes. This analysis helps determine whether the resin and fiberglass have been compromised by exposure to harsh chemicals. Any degradation in the material can affect the pipe’s strength and corrosion resistance, potentially making it unsuitable for further use in petroleum applications.
After thorough inspection and testing, a decision can be made regarding the viability of the used pipes. Only pipes that pass all testing procedures and meet the necessary safety and performance standards should be considered for integration into petroleum infrastructure.
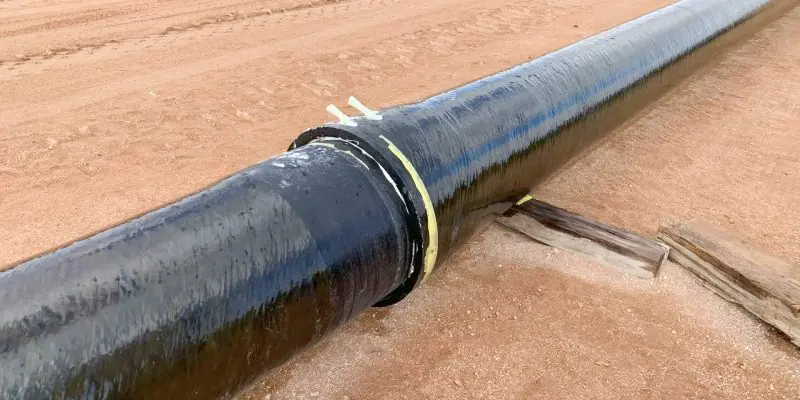
High Pressure Petroleum FRP Pipe
High Pressure Petroleum FRP Pipe refers to a composite pipe system designed specifically for use in the petroleum industry to handle high-pressure applications. These pipes are made from FRP (Fiberglass Reinforced Plastic), where the FRP pipe full form signifies its composition of fiberglass reinforcement and a polymer resin matrix. This combination provides exceptional strength, corrosion resistance, and durability, making it a reliable choice for demanding industrial environments.
Detailed Description
- Material Composition:
- Fibers: Glass fibers (commonly E-glass or S-glass) are used for strength and stiffness. In some cases, carbon fibers may be employed for enhanced properties.
- Resin Matrix: Thermosetting resins like epoxy, polyester, or vinyl ester provide chemical resistance and bind the fibers together.
- Applications in Petroleum Industry:
- Used for transporting crude oil, refined petroleum products, and natural gas.
- Suitable for environments with high pressure and corrosive conditions, such as offshore platforms, oil rigs, and chemical processing plants.
- Commonly employed in downhole tubing, gathering lines, and injection systems.
- Key Features:
- High Pressure Resistance: Designed to withstand operating pressures that can exceed 100 bar (1450 psi) or more, depending on the design and materials used.
- Corrosion Resistance: Excellent resistance to corrosion from harsh chemicals, seawater, and hydrocarbons, reducing maintenance costs and extending service life.
- Lightweight: Compared to traditional metal pipes like steel, FRP pipes are significantly lighter, simplifying handling, transportation, and installation.
- Low Thermal Conductivity: Offers insulation properties, reducing heat loss or gain during fluid transportation.
- Long Service Life: With proper installation and maintenance, these pipes can last decades under high-stress conditions.
- Manufacturing Process:
- Filament Winding: A common technique where fibers are impregnated with resin and wound around a rotating mandrel in specific patterns to achieve desired strength and performance characteristics.
- Pultrusion: For straight pipes, fibers are pulled through a resin bath and then shaped and cured in a heated die.
- Curing: Heat or UV curing ensures the resin hardens to form a robust, durable structure.
- Advantages over Metal Pipes:
- Corrosion-Free: Unlike steel, FRP does not rust or degrade in corrosive environments.
- Lower Weight: Reduces transportation and installation costs.
- Customizable Properties: The material composition can be tailored to specific project requirements.
- Reduced Lifecycle Costs: Lower maintenance needs and extended lifespan compared to traditional metal alternatives.
- Design Considerations:
- Pressure Rating: Pipes are designed for specific pressure classes based on the operational requirements.
- Temperature Range: FRP can operate within a wide temperature range but requires special consideration for extreme conditions (e.g., cryogenic or very high temperatures).
- Joint Systems: Includes threaded, flanged, or adhesive-bonded joints, ensuring secure and leak-proof connections.
High Pressure Petroleum FRP Pipes are increasingly popular in the oil and gas industry due to their superior performance, durability, and cost-effectiveness compared to traditional materials like steel and aluminum. Their adoption helps to meet the growing demand for sustainable and efficient infrastructure in challenging operating environments.
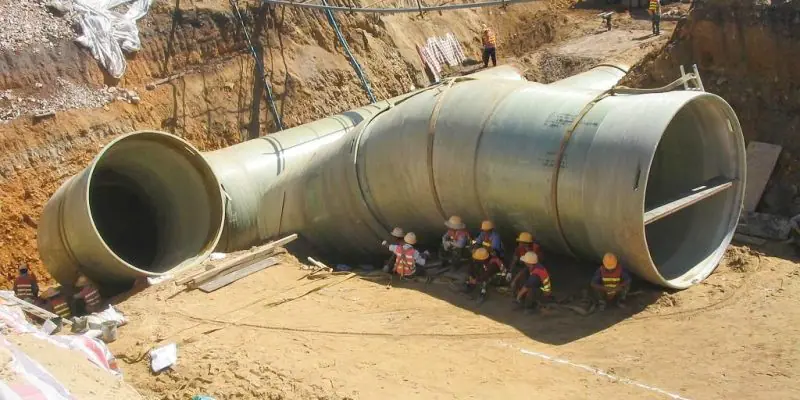
Petroleum FRP Pipe for Sale
1. Pricing
The price of Petroleum FRP (Fiber Reinforced Plastic) pipes varies significantly based on several factors:
- Pipe Dimensions: Larger diameter and thicker pipes typically cost more due to higher material usage.
- Example: A 6-inch diameter FRP pipe may cost $40–$100 per meter, while a 12-inch pipe could range from $150–$300 per meter.
- Pressure Rating: High-pressure pipes are priced higher due to the advanced materials and manufacturing techniques needed to meet the stress requirements.
- Material Type: Pipes reinforced with carbon fibers or advanced resins (e.g., epoxy or vinyl ester) are more expensive than those using standard glass fibers and polyester resin.
- Quantity Ordered: Bulk orders often qualify for discounts.
- Customization: Pipes with special coatings, fittings, or chemical resistance properties will cost more.
2. Cost Breakdown
- Material Costs: About 50–70% of the total cost is attributed to raw materials, including fibers, resin, and additives.
- Manufacturing Costs:
- Labor: Processes like filament winding or pultrusion require skilled labor.
- Curing and Quality Assurance: Testing for pressure and leak resistance adds to the cost.
- Logistics and Transportation: FRP pipes are lightweight but bulky, impacting shipping costs.
- Installation Costs: While FRP is easier to install than metal pipes, joining systems (e.g., adhesive bonding or flanged joints) may require specialized equipment.
3. Purchasing Options
- Direct Purchase from Manufacturers:
- Process: Contact manufacturers directly via their websites or sales teams for quotes. Provide detailed specifications like diameter, pressure rating, length, and quantity.
- Benefits: Lower costs, direct customization options, and technical support.
- Manufacturers: Examples include Hebei Aoliande, Shengli Xinda, and CNPS.
- Through Distributors:
- Process: Purchase through distributors or agents who represent multiple brands.
- Benefits: Faster delivery from local stock and options to mix and match products.
- Platforms: Alibaba, Made-in-China, or regional suppliers.
- Online Marketplaces:
- Platforms: Alibaba, IndiaMart, and ThomasNet.
- Benefits: Easy price comparison and access to customer reviews.
- Caution: Verify the authenticity of sellers to avoid counterfeit or substandard products.
4. Negotiation Tips for Better Pricing
- Bulk Orders: Always negotiate for discounts when ordering in large quantities.
- Customization Packages: Request all-inclusive pricing, including fittings and coatings.
- Shipping Terms: Opt for FOB (Free on Board) to minimize shipping costs or negotiate DDP (Delivered Duty Paid) if importing.
- Long-term Contracts: Consider establishing a supply contract to lock in lower prices for future orders.
5. Payment and Delivery
- Payment Terms:
- Small orders: Payment upfront.
- Large orders: 30% upfront, 70% upon delivery (common for international trade).
- Delivery Options:
- Standard lead time: 4–8 weeks, depending on production schedules and customization.
- Express manufacturing: Available for an additional cost.
By comparing prices, understanding cost factors, and choosing reliable suppliers, you can ensure an economical purchase of Petroleum FRP pipes tailored to your project’s requirements.
The Key of Petroleum FRP Pipe
Petroleum FRP pipe refers to Fiberglass Reinforced Plastic pipes specifically designed for use in the petroleum industry. These pipes are engineered to handle the unique challenges posed by the extraction, transportation, and storage of petroleum products. Petroleum FRP pipe is known for its durability, resistance to corrosion, and ability to withstand harsh environmental conditions, such as exposure to aggressive chemicals and high temperatures. The density of FRP pipe also plays a vital role in its performance, as higher density typically enhances strength and resistance to deformation under pressure.This makes it an ideal choice for the petroleum industry, where pipes are often subjected to extreme conditions that can degrade traditional materials. The lightweight nature of FRP, combined with its high strength, allows for easier installation and long-term reliability in petroleum-related projects.
The Key of Petroleum FRP Pipe for Oil and Gas Applications
Petroleum FRP pipe plays a critical role in the oil and gas industry, offering a reliable solution for transporting petroleum products safely and efficiently. One of the primary reasons FRP is used in this industry is its resistance to corrosion. Petroleum products often contain chemicals that can cause traditional materials like steel to corrode over time. Petroleum FRP pipe, on the other hand, resists chemical reactions, ensuring the pipe’s longevity and reducing the need for frequent maintenance or replacements.
Additionally, FRP’s ability to withstand high pressures makes it suitable for transporting petroleum over long distances, whether through pipelines or storage systems. The ability of petroleum FRP pipe to handle both high temperatures and high pressures without compromising its structural integrity further enhances its value in the petroleum sector. With increasing demands for safer and more durable materials in the oil and gas industry, petroleum FRP pipe continues to grow in importance.
Advantages of Petroleum FRP Pipe
The advantages of petroleum FRP pipe are numerous, making it a preferred choice for many petroleum-based applications. These benefits include:
Corrosion Resistance
Petroleum FRP pipe is highly resistant to corrosion, which is a common problem in the petroleum industry. Petroleum products, along with chemicals used during the extraction and refining processes, can quickly degrade traditional materials. However, the composite structure of FRP, reinforced with fiberglass and high-quality resins, ensures that it does not react with these chemicals, preventing corrosion and extending the lifespan of the pipe.
One of the primary benefits of GangLong Fiberglass tubing is its exceptional resistance to corrosion. In oil and gas wells, tubing is often exposed to corrosive substances like acids and saline water. Unlike steel, which corrodes under such conditions, fiberglass tubing from GangLong Fiberglass maintains its structural integrity, thereby extending the operational life of the well.
High Strength-to-Weight Ratio
Fiberglass tubing offers a remarkable balance of strength and weight, making it significantly easier to transport and install, especially in offshore drilling platforms where weight is a critical factor. The fiberglass tube strength ensures that despite its lightweight nature, the tubing can withstand high pressures and harsh downhole conditions, providing reliable performance in demanding oil and gas operations.
Lightweight and Strong
Despite being much lighter than traditional materials like steel, petroleum FRP pipe offers excellent strength, which makes it easier to transport and install. The reduced weight of FRP means that less labor and equipment are required for installation, saving both time and money. Furthermore, the strength of FRP ensures that it can handle the high pressures commonly encountered in oil and gas operations.
Temperature and Pressure Resistance
Petroleum FRP pipe is capable of withstanding extreme temperatures, making it ideal for use in high-temperature environments such as refineries and oil fields. The material is designed to maintain its structural integrity even when exposed to fluctuating temperatures. Similarly, uv resistant frp pipe ensures durability in outdoor applications, combining resistance to UV radiation with the ability to handle high pressures required for transporting petroleum products, making it equally effective for pipelines and storage systems.
Low Maintenance
Another significant advantage of petroleum FRP pipe is its low maintenance requirements. Traditional materials like steel often require frequent inspections and repairs due to corrosion or wear and tear. Petroleum FRP pipe, however, is much more durable and requires fewer repairs, reducing long-term maintenance costs. Its resistance to both chemical and environmental factors ensures that the pipes remain functional for extended periods without the need for costly repairs.
Environmentally Friendly
Petroleum FRP pipe is also considered environmentally friendly due to its long lifespan and lower maintenance needs. Its durability reduces the frequency of replacements, resulting in less waste. Furthermore, the energy required to produce FRP is lower than that of traditional materials, contributing to a reduced environmental impact. As industries move toward more sustainable practices, petroleum FRP pipe is becoming a key material in eco-friendly infrastructure.
GRP Pipe in Petroleum Applications
GRP (Glass Reinforced Plastic) is another material closely related to FRP, and it is commonly used in petroleum applications. While the terms FRP and GRP are sometimes used interchangeably, GRP specifically refers to a composite material that uses glass fibers for reinforcement. GRP pipes share many of the same advantages as FRP pipes, including corrosion resistance, strength, and durability, making them highly suitable for use in the petroleum industry.
How GRP Pipes Are Used in Petroleum Extraction, Transportation, and Storage
GRP pipes are widely used in the extraction, transportation, and storage of petroleum products. During the extraction process, GRP pipes are often used to transport raw petroleum from drilling sites to processing facilities. Their ability to withstand harsh environments, such as saltwater and corrosive chemicals, makes them a reliable choice for offshore oil rigs and other extraction locations.
In terms of transportation, GRP pipes are used in pipelines that carry petroleum over long distances. The lightweight nature of GRP allows for easier installation, even in remote or challenging terrain. Additionally, GRP’s resistance to both corrosion and high pressures ensures that the pipelines remain functional and safe for extended periods.
For storage, GRP pipes are often used in facilities where petroleum products are kept before being transported or processed. These storage systems require materials that can handle both chemical exposure and temperature fluctuations, making GRP an ideal solution.
Advantages of Using GRP Pipes for Petroleum Pipelines
GRP pipes offer several key advantages when used in petroleum pipelines:
- Corrosion Resistance: Like FRP, GRP pipes are highly resistant to corrosion caused by petroleum products and other chemicals. This resistance helps to extend the lifespan of the pipeline, reducing the need for costly replacements or repairs.
- Lightweight Design: The lightweight nature of GRP makes it easier to transport and install than traditional materials, resulting in faster project completion times and lower installation costs.
- High Strength and Durability: Despite being lightweight, GRP pipes offer impressive strength and durability, making them capable of handling the high pressures required in petroleum pipelines. This ensures that the pipelines remain reliable and safe over long distances.
- Temperature Resistance: GRP pipes are designed to withstand high temperatures, making them suitable for use in refineries and other facilities where temperature fluctuations are common.
Installation Techniques for Petroleum FRP Pipe
Proper installation of petroleum FRP pipe is essential to ensure its long-term performance. Installation techniques can vary depending on the specific application, but there are some general best practices to follow:
Pre-Installation Preparation
Before installation, it is important to ensure that the FRP pipes are properly stored and handled to prevent damage. Although FRP is highly durable, it can be susceptible to cracking if not handled correctly. Additionally, the installation site should be thoroughly prepared to ensure that the pipes are properly aligned and supported. If the system includes petroleum FRP pipe railings for added safety or structural support, these should also be inspected and aligned at this stage to ensure they do not interfere with the pipe’s installation process.
Joining Methods
Petroleum FRP pipe can be joined using a variety of methods, including adhesive bonding, mechanical connections, and flanged joints. The specific method used will depend on the application and the environmental conditions. Adhesive bonding is a common method for joining FRP pipes, as it provides a strong, watertight seal that can withstand the pressures and temperatures typically found in petroleum applications. FRP pipe racks can also play a role during the installation phase by keeping the petroleum pipes aligned properly for easier joining, especially in complex pipeline systems.
Support Systems
When installing petroleum FRP pipe, it is important to ensure that the pipes are properly supported to prevent sagging or damage over time. This is particularly important for long pipelines, where improper support can lead to stress on the pipes, potentially causing them to crack or break. The support system should be designed to accommodate the weight of the pipes and any external forces, such as wind or seismic activity.
Maintenance and Lifespan of Petroleum FRP Pipe
Petroleum FRP pipe offers a long lifespan with minimal maintenance requirements, making it an attractive option for long-term infrastructure projects. Regular inspections should be conducted to ensure that the pipes remain in good condition, but due to their resistance to corrosion and wear, FRP pipes generally require fewer repairs than traditional materials.
In addition to regular inspections, any damage to the pipes should be addressed promptly to prevent further degradation. While FRP is highly durable, cracks or other damage can compromise the integrity of the pipe, leading to potential leaks or failures. Fortunately, FRP pipes are easy to repair using specialized adhesives or mechanical connections, allowing for quick and efficient repairs.
The Future of Petroleum FRP Pipe in the Oil and Gas Industry
As the oil and gas industry continues to evolve, the use of petroleum FRP pipe is expected to grow. Advances in materials science are likely to further enhance the performance of FRP, making it an even more reliable and cost-effective solution for transporting petroleum products.
Emerging trends in the industry, such as the focus on sustainability and reducing environmental impact, are also driving the adoption of FRP materials. With its long lifespan, low maintenance requirements, and environmentally friendly production process, petroleum FRP pipe is well-positioned to play a key role in the future of the oil and gas industry. Manufacturers like GangLong Fiberglass are continuing to innovate and develop new FRP products to meet the evolving needs of this critical industry.
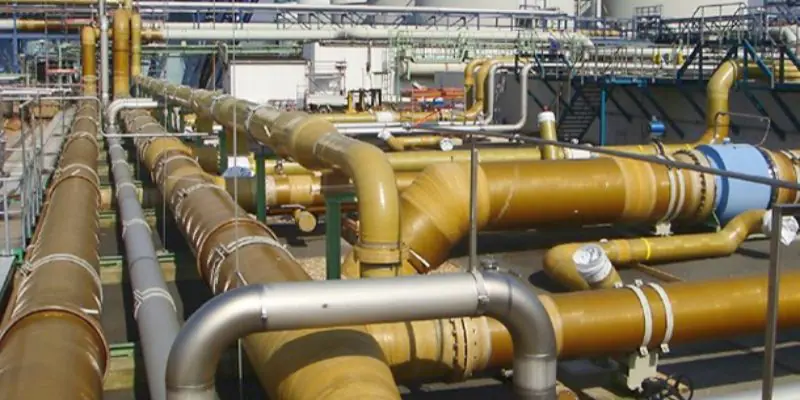
Effective Adhesive Bonding for FRP Pipe Bell and Spigot Joints
Petroleum Frp Pipe: Enhancing Durability and Performance in the Petroleum Industry
Petroleum FRP (Fiberglass Reinforced Plastic) pipes play a pivotal role in the petroleum industry, offering robust solutions for transporting various petroleum products. Their superior resistance to corrosion, harsh chemicals, and extreme environmental conditions makes them an essential component in ensuring safe and efficient operations. With their ability to endure the demands of offshore drilling sites, refineries, and long-distance pipelines, petroleum FRP pipes significantly reduce maintenance costs and improve infrastructure longevity.
GangLong Fiberglass Piping Systems
GangLong Fiberglass piping systems signify a major leap in the use of FRP pipes within the petroleum sector. Engineered to withstand the rigorous conditions of the petroleum industry, these systems excel in environments characterized by exposure to corrosive chemicals, high pressure, and temperature variations. The advanced composite materials used in GangLong Fiberglass pipes provide unparalleled strength and resistance against both internal and external corrosive elements.
One of the standout features of GangLong Fiberglass piping systems is their versatility. They are suitable for a wide array of petroleum applications, including wellhead connections, flow lines, and transportation pipelines. The multi-layer construction of these pipes allows them to handle high-pressure conditions without compromising their structural integrity, making them ideal for transporting crude oil, natural gas, and refined petroleum products.
Additionally, GangLong Fiberglass piping systems are designed to minimize maintenance needs, ensuring a long service life even in the most challenging conditions. The smooth inner surface of these pipes reduces friction and flow resistance, thereby enhancing the efficiency of fluid transport and leading to significant energy savings. This attribute is especially advantageous in large-scale petroleum operations where efficient fluid movement is crucial.
Benefits of GangLong Fiberglass Pipes in Petroleum Industries
GangLong Fiberglass pipes offer several critical benefits that make them the preferred choice in various petroleum industry applications. The foremost advantage is their exceptional corrosion resistance. In petroleum environments where pipes are frequently exposed to harsh chemicals, saltwater, and other corrosive substances, maintaining the integrity of the pipeline is crucial. GangLong Fiberglass pipes are designed to withstand such exposures, thereby reducing the risk of leaks and environmental contamination.
Another notable benefit is their capacity to endure high-pressure conditions. In petroleum extraction and transportation, pipelines are often subjected to extreme pressures that can compromise their integrity. GangLong Fiberglass pipes are engineered to handle these pressures without deformation or cracking, ensuring the secure transport of petroleum products. This high-pressure rating makes them particularly suitable for offshore drilling platforms and deep-well extraction sites.
Moreover, GangLong Fiberglass pipes are lightweight compared to traditional steel alternatives, which simplifies handling and installation. This feature is especially beneficial in remote or offshore locations where logistics can be complex and costly. The lightweight nature of these pipes translates to reduced labor costs and shorter installation times, without compromising on strength or durability. This combination of features makes GangLong Fiberglass pipes a reliable and cost-effective solution for petroleum infrastructure.
Case Studies of Petroleum Frp Pipe Systems in Action
The effectiveness of GangLong Fiberglass piping systems in the petroleum industry is well-documented through various case studies. In one example, an offshore oil platform needed a piping system capable of withstanding saltwater exposure, high pressure, and fluctuating temperatures. GangLong Fiberglass pipes were chosen for their corrosion resistance and robustness in harsh offshore environments. Over several years, these pipes demonstrated exceptional performance, maintaining structural integrity and ensuring the safe transport of oil and gas.
In another instance, a refinery struggling with corrosion issues in its steel piping system decided to replace it with GangLong Fiberglass pipes. This switch eliminated frequent maintenance and repair needs associated with steel pipes, providing a long-lasting solution. Additionally, the smooth interior of the GangLong Fiberglass pipes improved flow efficiency, resulting in lower energy costs for the facility.
These case studies underscore the reliability and versatility of GangLong Fiberglass piping systems in diverse petroleum industry environments. Their successful application highlights their role in enhancing the safety, performance, and longevity of petroleum infrastructure.
GRP Pipes in Petroleum Applications
Glass Reinforced Plastic (GRP) pipes, a subset of FRP pipes, offer remarkable performance in the petroleum industry. GRP pipes from GangLong Fiberglass are known for their high strength, corrosion resistance, and lightweight properties, making them suitable for various petroleum applications. In extraction processes, GRP pipes serve as production and flow lines, providing a dependable conduit for transporting crude oil and natural gas from wellheads to processing facilities.
GRP pipes are also utilized in the long-distance transportation of petroleum products. Their smooth internal surface minimizes friction losses, which enhances the efficiency of fluid flow. This efficiency is especially beneficial in extensive pipeline networks, where energy savings are substantial. GRP pipes are engineered to withstand thermal and mechanical stresses during the transport of petroleum products, ensuring safe and leak-free operations over long distances.
In storage and refinery environments, GRP pipes offer a superior alternative to traditional materials prone to corrosion and degradation. The inherent resistance of GRP to chemicals and UV radiation ensures that the pipes retain their performance characteristics over time, even in harsh conditions. This long-term durability results in lower maintenance costs and extends the service life of petroleum infrastructure, making GRP pipes a cost-effective choice for petroleum operations.
Best Practices for Installing FRP Pipe Bridge on Industrial Systems
Petroleum Frp Pipe in Oil and Gas Operations
Fiberglass tubing has become an indispensable component in oil and gas operations, particularly in downhole applications where the environment is harsh and demanding. Its exceptional ability to withstand the high pressures and temperatures encountered in oil wells, along with resistance to aggressive substances like brine, acids, and hydrocarbons, makes it a superior choice. By incorporating fiberglass tubing, the integrity of the well and the safety of the extraction process are significantly enhanced.
One of the foremost advantages of fiberglass tubing in oil and gas operations is its inherent corrosion resistance. Unlike traditional steel tubing, which often corrodes in the acidic and saline conditions prevalent in oil wells, fiberglass tubing remains unaffected. This resistance to corrosion drastically reduces the risk of tubing failure, thereby preventing costly downtime and mitigating potential environmental hazards. The longevity of fiberglass tubing ensures that wells can operate efficiently and safely over extended periods without the frequent maintenance associated with metal tubing.
Furthermore, fiberglass tubing offers a high strength-to-weight ratio, which translates to easier handling and installation. This feature is particularly beneficial in offshore drilling operations, where reducing weight on the drilling platform is crucial. The lightweight nature of fiberglass tubing not only simplifies installation but also contributes to lower transportation costs and safer handling procedures. GangLong Fiberglass provides fiberglass tubing specifically tailored to meet the stringent demands of oil and gas operations, ensuring optimal performance and durability in even the most challenging conditions.
Petroleum Frp Pipe: Tailored Solutions for Oil and Gas Operations
FRP pipe experts in the context of oil and gas operations focus on the qualification and compliance of fiberglass tubing to ensure suitability for demanding environments. These experts ensure that fiberglass tubing meets industry-specific standards for performance under high-pressure, high-temperature, and corrosive conditions commonly found in oil and gas extraction and transport. They perform rigorous testing and validation processes to verify the tubing’s durability, chemical resistance, and structural integrity. This ensures that fiberglass tubing is compliant with regulatory and safety standards, making it a reliable choice for critical oil and gas applications.
Fiberglass tubing plays a critical role in oil and gas operations, providing a corrosion-resistant and durable alternative to traditional metal tubing. In downhole applications, where the tubing is exposed to high pressures, temperatures, and corrosive substances, fiberglass tubing offers superior performance and longevity. This makes it an ideal choice for use in well casings, production tubing, and injection wells.
One of the key advantages of fiberglass tubing in oil and gas operations is its ability to withstand the harsh chemical environment encountered in these settings. Whether dealing with brine, hydrocarbons, or aggressive chemicals used in enhanced oil recovery processes, fiberglass tubing resists degradation, maintaining its integrity over time. This resistance not only extends the service life of the tubing but also reduces the risk of leaks and failures that could result in costly downtime or environmental incidents.
Fiberglass tubing is also much lighter than steel, which simplifies handling and installation. In offshore drilling operations, where weight is a critical factor, the use of lightweight fiberglass tubing can result in significant logistical and operational advantages. GangLong Fiberglass offers fiberglass tubing designed to meet the specific requirements of oil and gas operations, ensuring optimal performance and safety in challenging environments.
GangLong Fiberglass offers tailored fiberglass tubing and piping solutions designed to meet the unique requirements of oil and gas operations. By utilizing advanced composite materials and engineering techniques, GangLong Fiberglass provides products that enhance the safety, efficiency, and reliability of oil and gas infrastructure. In addition to the high-performance pipes, the China FRP pipe saddle is an integral part of the system, providing crucial support and stability. The saddle ensures that the pipes remain securely in place, preventing misalignment or damage during operations, and contributing to the overall durability and longevity of the infrastructure.
- Customizable Design: GangLong Fiberglass offers solutions tailored to specific operational requirements, such as large diameter fiberglass tubes for applications demanding greater capacity and strength. These tubes, along with options for various diameters, lengths, and pressure ratings, ensure operators have reliable and efficient solutions. The addition of fiberglass W beams further enhances structural integrity, providing a comprehensive approach to meeting the demands of oil and gas operations.
- Chemical Resistance: In addition to corrosion resistance, GangLong Fiberglass products offer resistance to a wide range of chemicals, including hydrocarbons, acids, and brine. This resistance ensures the safe transport of substances, preventing leaks and environmental contamination.
- Performance in Harsh Conditions: GangLong Fiberglass tubing and piping are engineered to perform under extreme conditions, including high-pressure environments, fluctuating temperatures, and exposure to aggressive substances. This performance capability makes them a preferred choice for both onshore and offshore oil and gas operations.
By incorporating GangLong Fiberglass tubing and piping solutions, oil and gas operators can enhance the integrity and performance of their infrastructure. These advanced materials not only provide a durable alternative to traditional steel but also contribute to safer and more efficient operations.
Best Practices for Ensuring Effective FRP Pipe Cladding
FAQs about Petroleum Frp Pipe
In the oil and gas industry, FRP stands for Fiberglass Reinforced Plastic, which is used extensively for piping, tanks, and other infrastructure due to its excellent resistance to corrosion, chemicals, and harsh environmental conditions. FRP piping is favored in oil and gas operations because it can withstand exposure to aggressive chemicals and high temperatures without degrading over time. This makes it a reliable solution for transporting oil, gas, and other chemicals. Additionally, FRP materials are lightweight, reducing the cost and complexity of transporting and installing them in remote or offshore locations. FRP’s durability and long lifespan make it an ideal choice for oil and gas projects that require robust, low-maintenance solutions.
While FRP pipes offer many advantages, there are a few disadvantages to consider. One of the main drawbacks is the higher initial cost compared to traditional materials like PVC or concrete. This higher cost is due to the specialized manufacturing process and materials used in FRP production. Additionally, FRP pipes can be more brittle than metals, which means they can be more prone to damage under impact or heavy loads. Handling and installation must be done carefully to avoid cracking or other damage. Furthermore, although FRP is highly resistant to corrosion, it may not perform as well in environments with constant UV exposure unless additional protective coatings are applied.
FRP (Fiberglass Reinforced Plastic) pipes and PVC (Polyvinyl Chloride) pipes differ in several key ways. FRP pipes are made from a combination of fiberglass and plastic resins, offering higher strength, greater durability, and superior resistance to corrosion compared to PVC. FRP pipes are commonly used in industrial and commercial applications where exposure to chemicals, high temperatures, or abrasive materials is a concern. On the other hand, PVC pipes are made from a type of plastic that is less resistant to extreme conditions, but they are often used in residential plumbing and irrigation due to their lower cost and ease of installation. While PVC is suitable for low-pressure applications, FRP is preferred for high-pressure, high-stress environments where long-term reliability is critical.
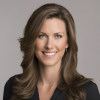
As the editor of GangLong Fiberglass, I have years of experience and in-depth research, focusing on cable tray products, fiberglass solutions, and grille systems. I incorporate years of industry insights and practical experience into every content, committed to promoting the progress of the industry. At GangLong Fiberglass, my commitment is reflected in every product, from innovative cable trays to durable fiberglass solutions and sturdy grille systems. As an authoritative voice in the industry, my goal is to provide valuable information to professionals and businesses and promote forward-looking solutions.