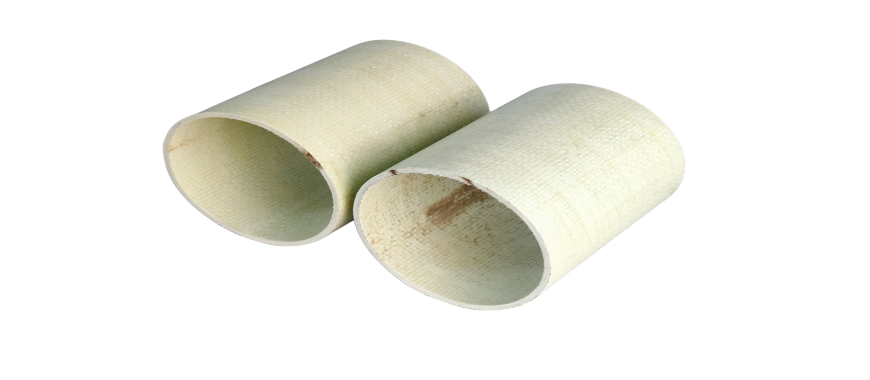
Double Bell Reka Couplings are crucial in the installation of FRP pipe systems, ensuring secure and leak-free joints. These couplings work by compressing two rubber gaskets, which provide a reliable seal between pipe sections. This compression mechanism is essential for maintaining the integrity of the FRP pipe system, preventing leaks and ensuring consistent performance. In the context of frp pipe data, understanding the role and functionality of Double Bell Reka Couplings is vital. FRP Pipe Data provides essential specifications, design parameters, and testing for high-strength, corrosion-resistant fiberglass pipes. They are an integral part of systems offered by GangLong Fiberglass, designed to enhance the durability and efficiency of FRP pipe installations across various industrial applications.
FRP Pipe Data Sources
FRP (Fiberglass Reinforced Plastic) pipes are a type of composite material widely used in various industries due to their strength, durability, and resistance to corrosion. The FRP pipe full form, referring to its composition of fiberglass reinforcement and plastic resin, highlights its ability to withstand harsh environments. Data sources related to these pipes typically include technical specifications, industry standards, material properties, and performance under different operating conditions.
- Material Properties of FRP Pipes: The primary data sources regarding the material properties of FRP pipes include technical documentation from manufacturers, research papers, and industry standards. These sources provide data on the mechanical properties such as tensile strength, flexural strength, modulus of elasticity, and impact resistance. Additionally, they contain information on the thermal expansion, density, and chemical resistance of the FRP material. The strength-to-weight ratio is a critical factor, making FRP pipes an attractive choice for many applications.
- Standards and Regulations: International and national standards organizations such as ASTM (American Society for Testing and Materials), ISO (International Organization for Standardization), and ASME (American Society of Mechanical Engineers) provide guidelines and specifications that dictate the manufacturing, testing, and installation of FRP pipes. These sources ensure that the pipes meet the necessary safety and performance standards. Standards like ASTM D2996 (Standard Specification for Filament-Wound Glass-Fiber-Reinforced Thermosetting-Resin Pipe) provide detailed requirements for the design and construction of FRP pipes.
- Performance Data: Data regarding the long-term performance of FRP pipes, including their durability under various environmental conditions, is available from manufacturers’ case studies, industry reports, and experimental research. These data sources often focus on how FRP pipes perform under factors like temperature fluctuations, exposure to chemicals, UV radiation, and mechanical loading. Long-term performance data is essential for ensuring that FRP pipes can withstand the conditions in which they will be used, such as in water treatment plants, chemical transport, and offshore applications.
- Cost and Market Data: Financial and market research sources provide data on the cost-effectiveness of FRP pipes compared to other materials, such as steel or PVC. These sources might include market analysis reports from firms like IBISWorld or Frost & Sullivan, and cost studies published in industry journals. These reports typically analyze the cost per meter of pipe, installation costs, and the lifetime cost savings of using FRP pipes in various applications.
- Installation and Maintenance Data: Information related to the installation process, maintenance practices, and troubleshooting of FRP pipes is often provided by technical guides from manufacturers or industry experts. Data in this area would include instructions on pipe jointing techniques, optimal installation conditions, recommended maintenance schedules, and common failure modes to be aware of. Maintenance data helps ensure the operational lifespan of FRP pipes is maximized.
- Environmental Impact Data: FRP pipes are also recognized for their environmental benefits, including their ability to reduce energy consumption during transportation and their recyclability. Environmental impact data is often available from sustainability reports, lifecycle analyses (LCAs), and environmental impact assessments conducted by independent organizations or industry bodies. These reports help stakeholders understand the environmental footprint of using FRP pipes, including aspects like raw material sourcing, manufacturing energy consumption, and disposal or recycling at the end of the pipe’s life.
Data sources for FRP pipes come from a wide range of technical, regulatory, financial, and environmental studies, all of which provide valuable information for engineers, manufacturers, and decision-makers in industries that utilize these pipes.
Testing and Certification of FRP Pipe Data
Testing and certification of FRP (Fiberglass Reinforced Plastic) pipes are essential to ensure their reliability, performance, and safety in various applications. The process involves rigorous assessments of material properties, mechanical strength, durability, and resistance to environmental factors. Below is a detailed explanation of the testing and certification data sources for FRP pipes:
Material Testing
Material testing of FRP pipes involves assessing the individual components that make up the composite material, such as the resin and fiberglass reinforcement. Testing typically includes the following:
- Tensile Strength: To evaluate the material’s ability to resist pulling forces, which helps determine its suitability for handling pressure in piping systems.
- Flexural Strength: This test measures the pipe’s ability to withstand bending forces without breaking, which is crucial for pipes used in applications with fluctuating or lateral forces.
- Compression Testing: Assesses the material’s behavior under compressive loads, which is important for determining how the pipe will perform under heavy-duty applications like underground or pressurized systems.
- Impact Resistance: This test evaluates the ability of the pipe to absorb energy from impacts or shocks without cracking or failing, ensuring the pipe can handle accidental hits or drops.
- Fatigue Testing: Assesses the durability of the pipe under cyclic loading conditions, simulating long-term wear and tear over time.
Data for these tests is typically found in technical documents provided by pipe manufacturers and in laboratory research reports. The results of these tests help define the material’s suitability for specific environments and pressure ratings.
Standardized Testing Protocols
Several international standards define the testing protocols for FRP pipes. These standards provide uniform methods for conducting tests and ensure that pipes meet the necessary safety and performance criteria. Some of the key standards include:
- ASTM D2996: Standard Specification for Filament-Wound Glass-Fiber-Reinforced Thermosetting-Resin Pipe. This standard specifies the requirements for the fabrication, testing, and use of FRP pipes, including stress testing, material properties, and dimensional tolerances.
- ASTM D3567: Standard Guide for Specifying and Selecting Filament-Wound FRP Pipe. This standard provides guidelines for selecting the right type of FRP pipe and includes testing procedures for burst pressure and other mechanical properties.
- ISO 14692: Petroleum and Natural Gas Industries — Glass-Reinforced Plastics (GRP) Piping. This international standard applies to FRP pipes used in the oil and gas industries, covering testing methods for long-term performance and pressure ratings.
- ASME RTP-1: This standard applies to the design, materials, and fabrication of FRP piping used in industrial applications. It includes guidelines for testing pipe strength, pressure, and chemical resistance.
Pressure Testing
One of the most crucial tests for FRP pipes is pressure testing, which ensures that the pipes can withstand the internal pressures they will encounter during use. Methods include:
- Hydrostatic Pressure Test: The pipe is filled with water and pressurized to a certain level to assess its ability to handle the intended operational pressure without failure. This test checks for leaks, cracks, and overall integrity.
- Burst Pressure Test: This test determines the maximum pressure at which the FRP pipe will burst, helping to define its safe operating pressure limits.
- Long-Term Pressure Testing: This type of testing simulates the pipe’s behavior over an extended period of time under constant internal pressure, evaluating factors like creep and material degradation.
Pressure testing data can be found in the certification reports and validation studies published by accredited testing agencies.
Certification Bodies
Various organizations and certification bodies provide third-party validation of FRP pipes, ensuring that the pipes meet the required safety and performance standards. Certification from recognized bodies can assure customers that the pipes will perform as expected in real-world applications. Some of the key certifying organizations include:
- Underwriters Laboratories (UL): Provides certification for the safety and performance of FRP pipes used in various industries. UL testing includes environmental resistance, flame retardance, and pressure ratings.
- NSF International: Certifies FRP pipes for drinking water systems, ensuring that the pipes are free from harmful chemicals and meet health safety standards.
- CE Marking: In Europe, FRP pipes can receive the CE mark, which indicates compliance with EU health, safety, and environmental regulations. This certification ensures that the pipes meet specific European Union standards for quality and safety.
- ISO 9001 Certification: Manufacturers of FRP pipes may also seek ISO 9001 certification for their quality management systems, demonstrating their commitment to consistent quality production processes.
Environmental and Chemical Resistance Testing
FRP pipes are often used in applications where they are exposed to harsh chemicals, extreme temperatures, or outdoor conditions. Testing in this area typically includes:
- Chemical Resistance Testing: Assesses the pipe’s ability to withstand exposure to various chemicals, including acids, bases, oils, and solvents. This is critical for industries such as chemical processing, wastewater treatment, and offshore oil and gas.
- UV and Weathering Testing: Simulates the effects of prolonged exposure to ultraviolet (UV) light and environmental conditions, ensuring that the pipe does not degrade or lose performance over time when used outdoors.
Data from these tests helps verify the suitability of FRP pipes for various environments and ensures they maintain their integrity throughout their service life.
Quality Assurance and Continuous Monitoring
Certification processes often require continuous monitoring and quality assurance throughout the manufacturing process. FRP pipe manufacturers may implement automated inspection systems to ensure consistent product quality. The quality control data typically includes:
- Visual Inspection: Ensures that there are no visible defects like cracks, voids, or delaminations in the FRP pipes.
- Dimensional Testing: Verifies that the pipes meet specified dimensions and tolerances, ensuring proper fitting and alignment during installation.
Manufacturers also perform batch testing for each production run to validate the consistency of material properties and pipe performance, providing additional data to certify each batch’s compliance with industry standards.
Testing and certification of FRP pipes are essential to ensure their performance, durability, and safety in a wide range of applications. Data from material tests, pressure tests, environmental tests, and certifications from recognized bodies all provide the necessary assurance that FRP pipes will meet industry standards and operate effectively under challenging conditions. These data sources are invaluable for manufacturers, engineers, and end-users who rely on FRP pipes for their strength, reliability, and long-term performance.
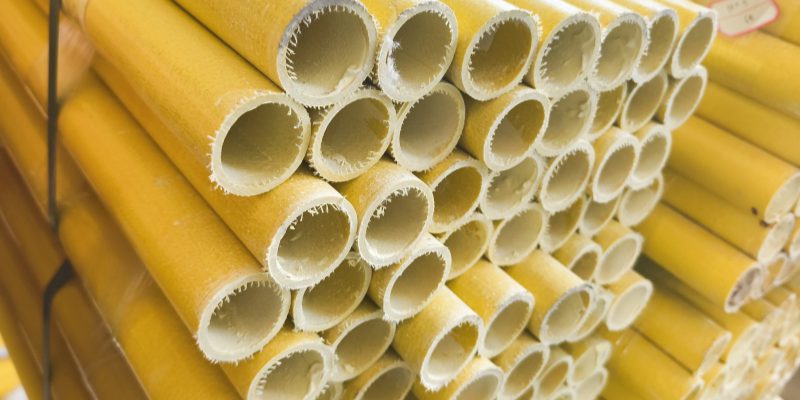
FRP Pipe Structure Types
FRP (Fiberglass Reinforced Plastic) pipes are available in several different structural types, each designed for specific applications and performance requirements. These structures are influenced by the materials used, the manufacturing processes, and the intended use of the pipes. Below is a detailed explanation of the various types of FRP pipe structures:
Filament-Wound FRP Pipes
Structure and Manufacturing:
- Filament-wound FRP pipes are made by winding continuous fiberglass filaments around a rotating mandrel, which is then impregnated with resin. This method allows for precise control over the pipe’s thickness, strength, and orientation of the reinforcing fibers.
- The process involves multiple layers of fibers being wound at varying angles (typically ± 55°, 90°) to create a pipe that is resistant to internal and external pressures, as well as to corrosion.
Key Characteristics:
- High strength-to-weight ratio.
- Excellent resistance to corrosion, making them ideal for use in chemical processing and wastewater applications.
- Ability to withstand high internal pressures, making them suitable for both low and high-pressure systems.
- Customized pipe designs based on specific load and pressure requirements.
Common Applications:
- Chemical plants.
- Wastewater treatment.
- Oil and gas industries.
- Water transport systems.
Continuous Laminate FRP Pipes
Structure and Manufacturing:
- Continuous laminate FRP pipes are manufactured using a process where layers of fiberglass mats and resin are stacked on top of each other. The fibers in the laminate are usually oriented in one direction, which helps provide strength in that specific direction.
- The layers are bonded together using thermosetting resins such as polyester, vinyl ester, or epoxy, which harden when heated or cured under pressure.
Key Characteristics:
- Provides good resistance to corrosion and high chemical resistance.
- Stronger in one direction (axial strength), making them suitable for applications that involve a consistent load or pressure in a particular direction.
- Less flexible compared to filament-wound pipes, which may make them more prone to damage in dynamic or fluctuating load conditions.
Common Applications:
- Storage tanks.
- Low to moderate pressure pipelines.
- Systems requiring high chemical resistance.
Dual-Laminated FRP Pipes
Structure and Manufacturing:
- Dual-laminated pipes combine layers of continuous filament-wound fibers and a second layer of continuous filament or fabric. This structure offers a balance of high-strength reinforcement and durability.
- The outer layer usually provides protection against environmental damage (e.g., UV rays, abrasion), while the inner layer focuses on corrosion resistance and chemical compatibility.
Key Characteristics:
- High resistance to chemical attack from both internal and external sources.
- Excellent impact and abrasion resistance.
- Superior durability in harsh environments, including high-temperature and corrosive applications.
- Enhanced structural integrity due to the combined materials.
Common Applications:
- Offshore and marine applications.
- Chemical transport and storage.
- Pipelines exposed to abrasive materials.
Hybrid FRP Pipes
Structure and Manufacturing:
- Hybrid FRP pipes are designed by combining different types of reinforcing fibers (e.g., fiberglass with carbon fibers or aramid fibers) to improve specific properties such as strength, conductivity, and resistance to impact.
- These pipes are generally manufactured through filament winding or other composite manufacturing methods, where the fibers are layered to provide specific performance characteristics.
Key Characteristics:
- Increased strength and stiffness compared to standard fiberglass pipes.
- Enhanced thermal conductivity (in the case of carbon fiber inclusion).
- Superior resistance to impact and mechanical damage.
- Designed for specialized applications requiring high-performance materials.
Common Applications:
- High-pressure systems.
- Structural applications requiring high impact resistance and strength.
- Aerospace or defense-related industries.
- Specialized chemical and petroleum transport.
Preformed FRP Pipes
Structure and Manufacturing:
- Preformed FRP pipes are shaped and molded into specific forms using a variety of techniques such as pultrusion, molding, or wrapping. These pipes may be produced in curved or flexible configurations, allowing them to fit various installation layouts or complex routing requirements.
- The manufacturing process typically involves combining continuous fiberglass strands with thermosetting resins that cure and harden into a rigid pipe structure.
Key Characteristics:
- Customizable shapes and sizes, offering versatility for installation in non-linear piping systems.
- Good corrosion resistance, although less common in extremely high-pressure environments.
- Lightweight and easy to transport and install.
Common Applications:
- Complex piping layouts.
- Agricultural irrigation systems.
- Installations where space constraints or curved paths are a factor.
Pultruded FRP Pipes
Structure and Manufacturing:
- Pultruded FRP pipes are made by continuously pulling fibers through a resin bath and then curing them in a heated die to form a rigid structure. Pultrusion is typically used to create pipes of consistent diameter and uniform thickness.
- These pipes are primarily reinforced with fiberglass, although other fibers can be used for enhanced properties. The process allows for the efficient production of high-strength, lightweight pipes.
Key Characteristics:
- Very high tensile and flexural strength, ideal for withstanding pressure and external stresses.
- Excellent resistance to chemical corrosion, including acids, alkalis, and solvents.
- Relatively low cost and simple manufacturing process compared to other FRP pipe types.
Common Applications:
- Water treatment facilities.
- Chemical processing.
- Underground piping systems where strength and durability are paramount.
Wrapped FRP Pipes
Structure and Manufacturing:
- Wrapped FRP pipes are created by wrapping multiple layers of fiberglass and resin around a core, which could be a metal or plastic pipe. This layering technique enhances the pipe’s strength and resistance to corrosion.
- The layers are wound at varying angles, providing excellent reinforcement and structural integrity.
Key Characteristics:
- High-strength, durable structure with good resistance to corrosive environments.
- Typically used for pipelines that require a combination of flexibility and strength.
- Cost-effective and suitable for moderate-pressure applications.
Common Applications:
- Oil and gas industry.
- Water supply systems.
- Agricultural and irrigation systems.
FRP pipes are highly versatile, and the structure type selected depends on the specific requirements of the application, including pressure resistance, corrosion resistance, strength, and flexibility. Filament-wound pipes are the most common due to their excellent strength-to-weight ratio and durability, while other types like continuous laminate and hybrid pipes offer specialized performance for specific industries. The right type of FRP pipe ensures that the system will operate efficiently and reliably for its intended lifespan.
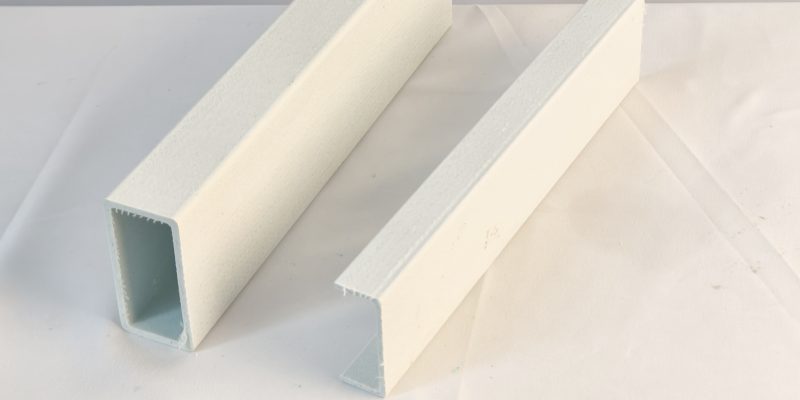
The Key of FRP Pipe Data: Joint Testing and Qualification Standards
Fibercast FRP pipe data involves extensive testing and qualification standards to ensure the performance, reliability, and durability of the pipes in various applications. Joint testing and qualification are crucial elements that validate the mechanical and chemical properties of FRP pipes. Testing standards like ASTM and BS play a vital role in establishing the quality benchmarks for these pipes, ensuring that they meet industry requirements.
What is the Importance of Joint Testing in FRP Pipes?
Joint testing is essential to guarantee the integrity of the connections between FRP pipe sections. Since these pipes are often used in critical applications such as chemical processing, water distribution, and wastewater treatment, the joints must be able to withstand pressure, mechanical stress, and chemical exposure without failure. Joint testing involves assessing the pipe’s ability to maintain a secure seal under various conditions, ensuring that leaks and failures do not occur.
FRP pipe data on joint testing includes the evaluation of flexible elastomeric seals, which are commonly used in the joints. The ASTM D 4161 standard outlines the testing methods for pipe joints using these seals. This standard ensures that the joints can maintain their integrity, even under deflected conditions. By adhering to these testing protocols, manufacturers like GangLong Fiberglass ensure that their FRP pipes deliver reliable performance across diverse industrial environments.
The FRP pipe MSDS typically provides detailed information on the composition, properties, hazards, and handling of the material. Here’s a general breakdown of the data typically found on an MSDS for FRP pipes:
- Chemical Composition: FRP pipes are composed primarily of fiberglass (glass fibers) embedded in a resin matrix, which can be polyester, epoxy, vinyl ester, or other types of resins. The MSDS will specify the exact formulation, including any additives, fillers, or curing agents used in the manufacturing process.
- Physical and Chemical Properties:
- Appearance: FRP pipes are usually rigid, translucent or opaque, and vary in color depending on the resin type.
- Density: The density of FRP pipes is typically around 1.8 to 2.1 g/cm³.
- Melting Point: FRP pipes themselves do not have a true melting point, as the resin matrix may decompose or degrade before reaching high temperatures.
- Boiling Point and Vapor Pressure: These properties are generally irrelevant for FRP pipes as they are solid materials.
- Health and Safety Hazards:
- Inhalation: Dust from cutting or grinding FRP pipes can be harmful if inhaled, causing respiratory issues or irritation. This is especially the case with fiberglass particles.
- Skin Contact: Direct contact with fiberglass or resins during cutting or handling may cause irritation, rashes, or allergic reactions.
- Eye Contact: Exposure to dust or resin splashes can irritate the eyes.
- Ingestion: Not typically a concern unless resin exposure occurs during handling, though ingestion of small amounts of fiberglass may cause gastrointestinal discomfort.
- Handling and Storage:
- Storage Conditions: FRP pipes should be stored in a cool, dry area, away from direct sunlight and sources of heat. Avoid exposure to excessive moisture or extreme temperature fluctuations.
- Handling Precautions: When cutting or handling FRP pipes, use personal protective equipment (PPE) such as gloves, safety goggles, and respirators to minimize exposure to dust and resin.
- Fire and Explosion Data:
- Flammability: FRP pipes may be flammable depending on the resin type, especially during high heat exposure. The MSDS will specify the flash point, auto-ignition temperature, and fire-fighting measures for specific types of resins used in the FRP pipes.
- Disposal Considerations:
- Disposal methods will depend on local regulations but may include recycling programs for the fiberglass composite or disposal at certified waste treatment facilities.
- Toxicological Information:
- Long-term exposure to fiberglass dust has been linked to respiratory conditions, including lung irritation or fibrosis. The resin may also have chemical hazards, such as irritation or sensitization upon prolonged contact with the skin.
This data is intended to guide safe handling and awareness of potential risks associated with FRP pipes. Always consult the specific MSDS for the exact product in use, as formulations can vary.
Chemical Resistance Testing: ASTM D 3681
Chemical resistance is a critical factor in the performance of FRP pipes, especially in industries where they are exposed to aggressive chemicals. The ASTM D 3681 standard is used to test the chemical resistance of FRP pipes in a deflected condition. This standard assesses how well the pipe can resist chemical attack while maintaining its structural integrity. FRP pipe data gathered from this test helps in understanding how the pipe will perform when exposed to different chemicals over time.
The chemical resistance testing involves exposing the pipe to specific chemicals and evaluating any changes in its physical properties. The deflected condition simulates the stress that the pipe might encounter in real-world applications. By meeting the ASTM D 3681 standard, FRP pipes demonstrate their ability to withstand harsh chemical environments, making them suitable for use in chemical processing plants and other demanding settings. GangLong Fiberglass ensures that its FRP pipes are rigorously tested to comply with this standard, providing customers with reliable and durable piping solutions.
Long-term Ring Stiffness and Creep Factor: BS 5480:1990
FRP pipe data also includes information on long-term ring stiffness and creep factor, which are critical for maintaining the pipe’s shape and structural integrity over extended periods. The BS 5480:1990 (Appendix L) standard outlines the methodology for determining these factors. Ring stiffness measures the pipe’s ability to resist external forces that can cause deformation, while the creep factor indicates how the pipe’s material behaves under prolonged stress.
Testing for ring stiffness involves applying a load to the pipe and measuring the amount of deflection that occurs. This data is crucial for applications where the pipes are subject to external pressures, such as buried pipelines. A high ring stiffness indicates that the pipe can resist deformation, ensuring a longer service life. Creep factor testing, on the other hand, assesses how the pipe’s material properties change over time when subjected to continuous stress. By understanding the creep behavior, engineers can predict the long-term performance of the pipe and design systems that account for these changes.
GangLong Fiberglass conducts these tests to ensure that their FRP pipes provide reliable performance in various conditions. By meeting the standards set by BS 5480:1990, their pipes demonstrate the necessary strength and durability to withstand the demands of different industrial applications.
Impact Resistance Testing: BS 5480:1990 (Appendix J)
Impact resistance is a vital aspect of FRP pipe data, as it determines how well the pipe can withstand mechanical shocks and sudden impacts without suffering damage. The BS 5480:1990 (Appendix J) standard provides the methodology for assessing the impact resistance of FRP pipes. This test involves subjecting the pipe to a controlled impact and evaluating any resulting damage.
Impact resistance testing is crucial for applications where the pipes might be exposed to mechanical forces, such as in construction sites or areas with heavy machinery. Pipes that pass this test demonstrate their ability to maintain structural integrity even when subjected to unexpected mechanical stresses. This characteristic is essential to prevent leaks and failures that could lead to costly repairs and downtime.
By adhering to the BS 5480:1990 impact resistance standard, manufacturers like GangLong Fiberglass ensure that their FRP pipes can endure harsh conditions without compromising performance. This testing provides customers with confidence in the durability and reliability of the pipes in various industrial settings.
Hydrostatic Design Basis: ASTM D 2992
FRP pipe data must include information on the pipe’s ability to withstand internal pressure. The ASTM D 2992 standard establishes the hydrostatic design basis for FRP pipes, determining their pressure capacity over time. This test involves subjecting the pipe to internal pressure and monitoring its response to identify its pressure rating.
Hydrostatic testing is crucial for applications where the pipes transport fluids under pressure, such as water distribution and chemical processing. The test provides insights into the pipe’s ability to handle the stresses imposed by pressurized fluids. By meeting the ASTM D 2992 standard, FRP pipes demonstrate their capability to operate safely under specified pressure conditions.
GangLong Fiberglass ensures that its FRP pipes are tested according to this standard, providing customers with accurate data on the pressure capacity of their products. This information is essential for engineers and designers when selecting the appropriate pipes for their projects, ensuring that the system operates safely and efficiently.
Ring-Bending Strain Performance: ASTM D 5365
The ring-bending strain performance of FRP pipes is a key aspect of FRP pipe data, as it indicates how well the pipe can withstand bending forces without cracking or failing. The ASTM D 5365 standard outlines the testing method for evaluating the long-term ring-bending strain of FRP pipes. This test assesses the pipe’s ability to endure bending loads, which can occur during installation or operation.
The testing involves applying a bending force to the pipe and monitoring its response over time. Pipes that pass this test show that they can flex without losing their structural integrity, making them suitable for installations where bending is required. This performance is particularly important for applications involving complex piping layouts or environments where the pipes must adapt to varying conditions.
GangLong Fiberglass conducts ring-bending strain testing to ensure that its FRP pipes provide reliable performance under bending loads. By meeting the ASTM D 5365 standard, their pipes offer flexibility and strength, reducing the risk of cracks and failures during service.
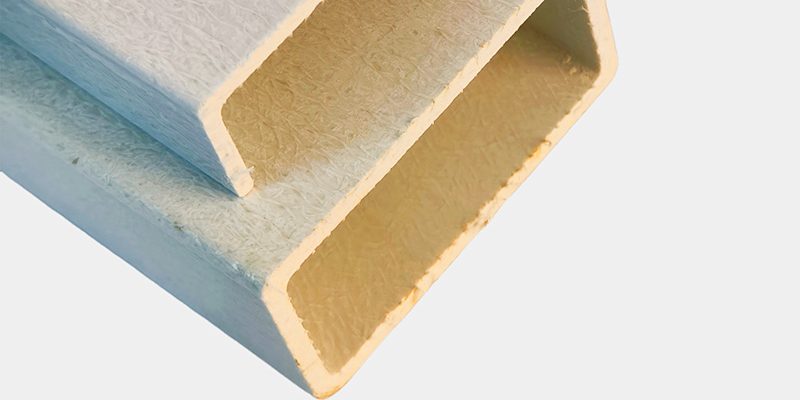
Product Qualification and Compliance
FRP pipe experts specialize in ensuring that FRP pipes meet rigorous standards for product qualification and compliance. These experts focus on verifying that the pipes adhere to industry standards for safety, durability, and performance under various environmental and operational conditions. They conduct tests on parameters like chemical resistance, mechanical strength, and pressure tolerance to confirm that the pipes comply with regulatory and client-specific requirements. Their expertise ensures that FRP pipes are reliable and certified for use in applications demanding high-quality and durable material solutions.
Product qualification is a vital component of FRP pipe data, encompassing all the tests and standards that the pipes must meet to be deemed suitable for industrial use. GangLong Fiberglass ensures that their FRP pipes are tested and qualified to meet a comprehensive range of standards, including chemical resistance, ring stiffness, impact resistance, hydrostatic design, and ring-bending strain performance.
Meeting these standards ensures that FRP pipes are reliable, durable, and fit for use in various applications. Qualification data provides customers with the assurance that the pipes can withstand the specific conditions they will encounter, minimizing the risk of failure and ensuring long-term performance.
By providing detailed FRP pipe data that includes qualification information, GangLong Fiberglass helps clients make informed decisions when selecting pipes for their projects. This data serves as a crucial reference for engineers, designers, and project managers, guiding them in choosing pipes that meet the required performance criteria.
The Key of FRP Pipe Data
FRP pipe data encompasses various specifications (such as CSI specifications FRP pipe) and properties that define the performance and suitability of fiberglass reinforced plastic pipes for diverse applications. This data includes material composition, mechanical properties, pressure ratings, and chemical resistance. GangLong Fiberglass provides detailed FRP pipe data to help engineers, designers, and installers choose the right piping solution for their specific needs. Understanding this data is crucial for ensuring the long-term reliability and safety of FRP piping systems in industries such as chemical processing, oil and gas, water treatment, and more.
Material Composition in FRP Pipe Data
Material composition is a critical aspect of FRP pipe data. FRP pipes are made of a composite material that consists of a polymer matrix reinforced with fiberglass. The resin used in the polymer matrix can vary depending on the intended application. Common resins include polyester, vinyl ester, and epoxy, each offering different levels of chemical resistance, thermal stability, and mechanical strength. The type of fiberglass reinforcement also influences the pipe’s properties. For instance, E-glass and S-glass fibers provide varying levels of strength and flexibility. GangLong Fiberglass incorporates high-quality resins and fibers into their FRP pipes, ensuring optimal performance based on the required specifications.
Mechanical Properties in FRP Pipe Data
Mechanical properties are essential elements in FRP pipe data, including tensile strength, compressive strength, flexural strength, and impact resistance. Tensile strength indicates the maximum stress the pipe can withstand while being stretched, while compressive strength measures the pipe’s ability to resist external pressure. Flexural strength represents the pipe’s resistance to bending forces, and impact resistance shows how well the pipe can absorb energy from sudden impacts without cracking or breaking. These mechanical properties are crucial for determining the pipe’s suitability for specific applications, such as high-pressure fluid transport or structural support in marine environments. GangLong Fiberglass provides detailed mechanical property data for its FRP pipes to guide engineers in selecting the right product for their projects.
Pressure Ratings in FRP Pipe Data
Pressure rating is a vital component of FRP pipe data, indicating the maximum internal pressure the pipe can safely handle. This rating is typically expressed in terms of pounds per square inch (psi) or bar. FRP pipes are designed to withstand various pressure levels, depending on factors such as pipe diameter, wall thickness, and resin type. High-pressure FRP pipes are commonly used in applications like oil and gas transportation, where the fluid’s pressure can be significant. GangLong Fiberglass offers a range of FRP pipes with different pressure ratings to meet the diverse needs of industries, ensuring safe and efficient fluid conveyance.
Chemical Resistance in FRP Pipe Data
Chemical resistance is a crucial factor in FRP pipe data, especially for applications involving corrosive fluids or harsh environmental conditions. FRP pipes are known for their excellent resistance to a wide range of chemicals, including acids, alkalis, solvents, and saltwater. This resistance is primarily determined by the type of resin used in the pipe’s construction. For example, vinyl ester resins offer superior chemical resistance compared to polyester resins. GangLong Fiberglass provides chemical resistance data for their FRP pipes, enabling users to select pipes that can withstand the specific chemicals they will encounter in their applications. This ensures long-term durability and minimizes the risk of corrosion-related failures.
Temperature Limits in FRP Pipe Data
Temperature limits are an important aspect of FRP pipe data. FRP pipes can operate within a wide range of temperatures, but their performance may vary depending on the resin type and fiber reinforcement used. The temperature limit indicates the maximum and minimum temperatures the pipe can handle without compromising its mechanical properties. For instance, epoxy-based FRP pipes generally have higher temperature resistance compared to polyester-based pipes. GangLong Fiberglass provides comprehensive temperature limit data for their FRP pipes, helping users choose pipes that will perform reliably under their specific temperature conditions, whether in hot industrial processes or cold outdoor installations.
Key Benefits of Using Petroleum FRP Pipe in Oil Industry
Lifespan and Maintenance in FRP Pipe Data
The lifespan and maintenance requirements of FRP pipes are key considerations in their selection. FRP pipe data includes information on the expected service life of the pipes under various conditions, such as exposure to UV radiation, chemicals, and temperature fluctuations. Maintenance guidelines outline routine inspection and cleaning practices to ensure the pipes remain in good condition. FRP pipes generally have a long lifespan and require minimal maintenance due to their resistance to corrosion and chemical attack. GangLong Fiberglass provides detailed information on the lifespan and maintenance of their FRP pipes, enabling users to plan for long-term, reliable operation.
Applications Referenced in FRP Pipe Data
FRP pipe data often references the range of applications for which the pipes are suited. This includes industries such as chemical processing, oil and gas, water and wastewater treatment, marine, and power generation. Each application has specific requirements in terms of chemical resistance, pressure ratings, temperature limits, and mechanical properties. By providing comprehensive FRP pipe data, GangLong Fiberglass ensures that their pipes can be matched to the demands of various environments, ensuring safe, efficient, and durable piping solutions for critical infrastructure projects.
Material Composition in FRP Pipe Data
Material composition is a vital element of FRP pipe data, detailing the types of resins and fiberglass reinforcements used in the pipe’s construction. The choice of resin, such as polyester, vinyl ester, or epoxy, influences the pipe’s chemical resistance, mechanical strength, and temperature tolerance. Fiberglass reinforcements like E-glass or S-glass provide the necessary structural integrity and flexibility. The combination of these materials determines the overall performance of the FRP pipe in specific environments. GangLong Fiberglass uses high-quality resins and fiberglass in their FRP pipes, optimizing them for applications that demand high corrosion resistance, strength, and longevity.
Mechanical Properties in FRP Pipe Data
FRP pipe data includes detailed information about the mechanical properties of the pipes, such as tensile strength, flexural strength, compressive strength, and impact resistance. Tensile strength indicates the pipe’s ability to resist stretching forces, while flexural strength measures its capacity to withstand bending stresses. Compressive strength assesses the pipe’s ability to endure crushing forces, and impact resistance evaluates how well the pipe can absorb shocks or sudden impacts. These mechanical properties are crucial for ensuring that FRP pipes can handle the physical demands of their intended applications, whether in fluid transport, structural support, or harsh industrial settings. GangLong Fiberglass provides precise mechanical property data for their FRP pipes, ensuring that they meet the necessary performance criteria for a wide range of uses.
Exploring Alternative Jointing Systems for FRP Pipes
FRP pipe data also covers jointing systems, which are essential for creating secure and leak-free connections between pipe segments. Various jointing methods are used for FRP pipes, each suited to specific application needs. One common technique is lamination, where fiberglass mats and polyester resin are applied to create a seamless bond between the pipe ends. This method, known as “butt-straps,” involves external and internal lay-up processes that provide a strong, chemical-resistant joint. Another method involves mechanical couplings, which allow for quick and reliable connections between FRP pipes and other materials. GangLong Fiberglass offers a range of jointing systems in their FRP pipe data, providing options that cater to different installation and operational requirements.
Chemical Resistance in FRP Pipe Data
Chemical resistance is a key feature in FRP pipe data, outlining the pipe’s ability to withstand exposure to various chemicals without degradation. FRP pipes are known for their excellent resistance to acids, alkalis, solvents, and other corrosive substances, making them ideal for use in chemical processing plants, wastewater treatment facilities, and other harsh environments. The level of chemical resistance is influenced by the type of resin used in the pipe’s construction. Vinyl ester resins, for instance, offer superior resistance to a broader range of chemicals compared to polyester resins. GangLong Fiberglass provides detailed chemical resistance data for their FRP pipes, allowing users to select pipes that can handle specific chemical exposures while maintaining their structural integrity.
Temperature Limits and FRP Pipe Data
FRP pipe data includes information about the temperature limits of the pipes, which is crucial for determining their suitability for different thermal environments. FRP pipes can operate within a wide temperature range, but their performance may vary depending on the resin type and reinforcement used. Temperature limits indicate the maximum and minimum temperatures the pipe can withstand without losing its mechanical properties or chemical resistance. Epoxy-based FRP pipes generally have higher temperature resistance, making them suitable for applications involving hot fluids or extreme temperature fluctuations. GangLong Fiberglass provides accurate temperature limit data for their FRP pipes, provide accurate FRP pipe schedule chart, ensuring they perform reliably in both high and low-temperature conditions.
Essential Guide to FRP Pipe Piles for Construction
Application of FRP Pipe Data
FRP (Fiberglass Reinforced Plastic) pipes are widely used in various industries due to their exceptional properties such as high strength, corrosion resistance, and lightweight design. These pipes are commonly applied in areas where traditional materials, such as metal or concrete, may not perform as effectively, especially in environments involving aggressive chemicals, extreme temperatures, or high pressures.
- Chemical Industry: FRP pipes are extensively used in the chemical industry for transporting corrosive fluids, including acids, bases, and solvents. Their resistance to corrosion makes them ideal for use in environments where traditional metal pipes would be subject to deterioration over time.
- Water Treatment Plants: In water treatment facilities, FRP pipes are utilized for the transportation of both raw and treated water. They help in ensuring the durability of the piping system as they resist the effects of water contaminants, chlorine, and other harsh substances commonly found in water treatment processes.
- Oil and Gas Industry: FRP pipes are increasingly used in the oil and gas industry for transporting oil, gas, and other fluids. These pipes provide significant advantages in offshore environments and other areas with harsh conditions, such as high-pressure systems and corrosive fluids. The lightweight nature of FRP also reduces transportation and installation costs.
- Power Generation: In power plants, FRP pipes are used for cooling water systems, as they can withstand high temperatures and are resistant to scaling and corrosion. Their use in heat exchangers and cooling systems helps to improve efficiency while maintaining a reliable, long-lasting pipeline.
- Mining Industry: FRP pipes are ideal for the mining industry, where they are used to transport slurry, chemicals, and water. They are particularly useful in underground mining operations and locations with abrasive materials, as their smooth interior surface minimizes wear and tear.
- Food and Beverage Industry: The food and beverage industry benefits from the non-reactive properties of FRP pipes, making them ideal for carrying liquids like milk, juices, and alcohol. The resistance to chemical reactions ensures that there is no contamination of the products, maintaining high-quality standards in the production process.
- Agricultural Irrigation Systems: FRP pipes are used in agricultural irrigation systems to distribute water across large areas. They are particularly advantageous in regions with high salinity or where corrosion-resistant materials are required to maintain the efficiency of the irrigation systems.
- Marine and Coastal Applications: FRP pipes are commonly used in marine and coastal areas for applications such as sewage systems, desalination plants, and marine cooling water pipelines. Their resistance to seawater corrosion makes them a suitable option for offshore installations.
FRP pipes are an essential solution across various industries, particularly in applications where corrosion resistance, strength, and reliability are crucial. Their growing use in modern infrastructure highlights their versatility and importance in ensuring efficient, long-lasting operations.
How FRP pipe shields protect pipes from corrosion and damage
FAQs about Frp Pipe Data
The maximum pressure that an FRP pipe can handle depends on several factors, including the pipe’s design, material composition, wall thickness, and the manufacturing process. Generally, FRP pipes can be designed to withstand pressures ranging from 150 psi to over 300 psi. However, some specially designed FRP pipes can handle even higher pressures. The specific maximum pressure rating for an FRP pipe is determined during the design phase, taking into account the application, environmental conditions, and safety factors. It’s important to consult the manufacturer’s specifications and industry standards, such as the ASME RTP-1 code, to determine the appropriate pressure rating for a given FRP piping system. Proper pressure rating ensures the safe and efficient operation of the system under various operating conditions.
FRP, or Fiberglass Reinforced Plastic, is a composite material commonly used in piping systems. It is composed of a polymer matrix reinforced with glass fibers, providing enhanced strength and durability. FRP piping is known for its excellent resistance to corrosion, making it ideal for transporting chemicals, acids, and other corrosive substances. Unlike traditional materials like steel or concrete, FRP does not corrode or rust, which significantly extends the life of the piping system. Additionally, FRP piping is lightweight, reducing installation and transportation costs. Its flexibility in design and installation makes it a preferred choice in industries like chemical processing, wastewater treatment, and oil and gas.
Calculating the weight of an FRP pipe involves determining the volume and density of the materials used. The formula to calculate the weight is:
Weight = Volume x Density.
To find the volume, you need the pipe’s outer diameter (OD), inner diameter (ID), and length. The volume of the pipe wall is the difference between the volume of the outer cylinder and the inner cylinder. After calculating the volume, multiply it by the density of the FRP material, which typically ranges from 1.6 to 2.0 grams per cubic centimeter. Manufacturers often provide specific density values for their FRP materials, so using their data can give a more accurate weight calculation. This calculation is crucial for transportation, installation, and structural support considerations in piping systems.
FRP (Fiberglass Reinforced Plastic) pipes are widely used in various industries due to their durability, corrosion resistance, and lightweight properties. However, there are some issues that can arise with their usage. One of the primary concerns with FRP pipes is their susceptibility to mechanical damage. While they are strong and durable, they are not impervious to impact. In certain situations, such as heavy handling or exposure to sharp objects, the pipes can crack or become damaged. Furthermore, FRP pipes can be more brittle at extremely low temperatures, making them prone to breaking or cracking under stress. Another issue with FRP pipes is their sensitivity to ultraviolet (UV) light, which can degrade the resin matrix used in the construction of the pipe. This degradation can reduce the pipe’s structural integrity and lead to failure over time if the pipes are not properly protected from UV exposure. Additionally, FRP pipes may require special considerations in terms of installation. Due to their lightweight nature, they can be more prone to movement or misalignment during installation, which could impact their performance. Finally, while FRP pipes are resistant to many chemicals, certain aggressive chemicals, such as concentrated acids or alkaline substances, may cause degradation of the pipe material.
HDPE (High-Density Polyethylene) and FRP (Fiberglass Reinforced Plastic) pipes are both popular materials used in various piping applications, but they differ in several key aspects. HDPE pipes are made from a thermoplastic material, while FRP pipes are composed of fiberglass strands embedded in a resin matrix, which is a thermoset plastic. The primary difference between the two lies in their structural composition, which directly influences their properties and performance. HDPE pipes are known for their excellent resistance to chemicals, impact, and abrasion. They are highly flexible, which makes them ideal for applications where the pipeline needs to bend or flex. On the other hand, FRP pipes are known for their high strength-to-weight ratio and are used in applications where resistance to corrosion is crucial, especially in industries such as chemical processing and wastewater management. FRP pipes can also withstand higher temperatures compared to HDPE pipes, making them suitable for higher temperature applications. However, HDPE pipes are more cost-effective and easier to install due to their flexibility and the availability of fittings. Another difference is that HDPE pipes tend to be more resistant to cracking under stress, while FRP pipes can be more brittle, especially in colder temperatures. Overall, the choice between HDPE and FRP pipes depends on the specific requirements of the application, including factors such as temperature resistance, chemical exposure, and flexibility.
FRP (Fiberglass Reinforced Plastic) and GRP (Glass Reinforced Plastic) pipes are essentially the same type of material, with the primary difference being in the terminology. Both FRP and GRP pipes are made using a composite material that consists of fiberglass fibers embedded in a resin matrix. The key difference lies in the use of the terms: FRP is a broader term that can refer to any type of composite material reinforced with fibers, including fiberglass, while GRP specifically refers to a type of FRP that uses glass fibers as the reinforcing material. Therefore, GRP pipes are a subset of FRP pipes. Both materials exhibit similar properties, such as excellent corrosion resistance, high strength-to-weight ratios, and the ability to withstand extreme conditions. GRP pipes are commonly used in industries such as water treatment, chemical processing, and oil and gas, where corrosion resistance and strength are crucial. On the other hand, the term “FRP” might be used in a broader context to describe various composite materials that could include different types of fibers, such as carbon fiber or aramid fibers, in addition to glass fibers. Despite the subtle difference in terminology, the properties and applications of FRP and GRP pipes are very similar, and in many cases, the terms are used interchangeably in the industry.
The pressure rating of an FRP (Fiberglass Reinforced Plastic) pipe depends on several factors, including the material composition, pipe dimensions, and the intended application. Generally, FRP pipes have pressure ratings ranging from 50 to 200 psi (pounds per square inch), with some high-performance grades capable of handling even higher pressures. The pressure rating is determined by the combined strength of the fiberglass reinforcement and the resin matrix used to fabricate the pipe. The type of resin, such as polyester, vinyl ester, or epoxy, used in the construction of the pipe can significantly impact its pressure rating. Additionally, the number of layers of fiberglass and the specific reinforcement method employed during manufacturing also play a role in determining the pressure rating. Typically, FRP pipes are designed to handle both internal pressure and external load conditions, making them suitable for a variety of fluid transportation applications, including water, chemicals, and gases. For high-pressure applications, special types of FRP pipes may be manufactured with increased reinforcement, allowing them to withstand pressures of up to 500 psi or more. It is important to note that the pressure rating of FRP pipes must be verified through testing and design calculations according to industry standards, such as ASME or ASTM, to ensure their suitability for a given application.
The ASME (American Society of Mechanical Engineers) Code for FRP (Fiberglass Reinforced Plastic) piping is outlined in ASME B31.3, which covers the design, materials, fabrication, installation, and testing of piping systems. Specifically, FRP piping is addressed in the context of process piping systems, particularly for industries such as chemical processing, power plants, and water treatment. The ASME B31.3 code establishes the requirements for the design of FRP pipes, including considerations for the materials of construction, wall thickness, and reinforcement needed to meet the necessary pressure and temperature ratings. The ASME code also provides guidelines for stress analysis, ensuring that the piping system can handle both internal and external loads, including those arising from thermal expansion, pressure surges, and vibration. It is essential for engineers and manufacturers to adhere to these codes to ensure that FRP piping systems are safe, reliable, and capable of performing under the demanding conditions of commercial and industrial applications. In addition to ASME B31.3, manufacturers and designers must also consult other relevant codes and standards, such as ASTM and ISO, which provide additional specifications for the fabrication, testing, and installation of FRP pipes.
The standard size of an FRP (Fiberglass Reinforced Plastic) pipe varies depending on the application, industry, and specific requirements. Typically, FRP pipes are available in nominal sizes ranging from 1 inch to 120 inches in diameter. The size range is generally classified according to the pipe’s outside diameter (OD), which is the most commonly referenced dimension. For small to medium-sized pipes, the standard sizes commonly range from 1 inch to 24 inches. Larger FRP pipes, used in industrial applications such as chemical processing, water treatment, and oil and gas pipelines, can reach diameters of up to 120 inches or more. FRP pipes can also be produced in custom sizes to meet the specific needs of a project. The wall thickness of the pipe is another important dimension that may vary depending on the pressure rating, load-bearing capacity, and application. Additionally, FRP pipes can be produced in both standard and custom lengths, depending on the needs of the installation. Standard lengths for FRP pipes are often 12 to 40 feet, though longer sections can be provided if necessary. It is important to work with experienced manufacturers to determine the appropriate size for an FRP pipe system based on factors such as flow capacity, pressure requirements, and environmental conditions.
The coefficient of thermal expansion (CTE) of FRP (Fiberglass Reinforced Plastic) pipes is an important property to consider when designing and installing piping systems, particularly in environments with significant temperature fluctuations. The CTE represents the amount by which a material expands or contracts with a change in temperature. For FRP pipes, the CTE is typically in the range of 10 to 20 x 10^-6/°C, which is lower than that of metals such as steel or aluminum. This means that FRP pipes exhibit relatively less expansion and contraction with changes in temperature compared to metals, making them suitable for applications where thermal stability is important. However, the CTE can vary depending on the specific type of resin used in the construction of the pipe and the fiberglass reinforcement. For instance, vinyl ester-based FRP pipes typically have a lower CTE compared to polyester-based pipes, due to the differences in the materials’ thermal properties. The lower CTE of FRP pipes can be advantageous in preventing thermal expansion issues, such as warping or misalignment, that may occur with other materials. In some cases, the installation of expansion joints or other thermal management solutions may still be necessary to accommodate any slight thermal expansion that occurs during temperature changes.
FRP (Fiberglass Reinforced Plastic) pipe is a type of composite pipe that consists of fiberglass fibers embedded in a resin matrix, typically polyester, vinyl ester, or epoxy. These pipes are designed to provide superior strength, corrosion resistance, and durability, making them suitable for a wide range of industrial and commercial applications. The fiberglass reinforcement gives the pipe its strength, while the resin matrix provides structural integrity and resistance to corrosion, chemicals, and environmental factors. FRP pipes are often used in applications where traditional materials like steel or PVC would be susceptible to corrosion or degradation, such as in chemical processing, water treatment, and wastewater systems. The lightweight nature of FRP pipes also makes them easier to transport and install compared to heavier materials, such as steel pipes. In addition to their resistance to corrosion, FRP pipes can withstand high temperatures and are often used in high-pressure systems. They are available in a wide range of sizes and configurations, from small-diameter pipes for fluid distribution to large-diameter pipes for industrial applications. While FRP pipes are durable and reliable, their brittleness at extremely low temperatures or under heavy impact should be taken into consideration during installation and handling.
The density of FRP (Fiberglass Reinforced Plastic) pipe varies depending on the specific materials used in its construction, including the type of resin and the amount of fiberglass reinforcement. Generally, the density of FRP pipes ranges from 1.4 to 2.0 g/cm³ (grams per cubic centimeter), which is significantly lower than that of metals like steel, which typically have a density of around 7.8 g/cm³. The relatively low density of FRP pipes is one of the key advantages that contribute to their lightweight properties, making them easier to handle, transport, and install compared to heavier pipe materials. The density of the pipe can vary depending on the ratio of resin to fiberglass used during manufacturing, as well as the type of resin (e.g., polyester, vinyl ester, or epoxy) and the design of the reinforcement layers. In applications where weight is a critical factor, such as in elevated or underground systems, the low density of FRP pipes can reduce the overall load on the structure. The reduced density also translates into cost savings for transportation and installation. However, the density of FRP pipes can also impact their mechanical properties, such as tensile strength and pressure rating, so these factors should be considered when selecting the appropriate pipe material for a specific application.
Calculating piping load involves assessing the forces that are acting on the piping system, including internal pressure, temperature-induced expansion, and external forces, such as weight and support conditions. To calculate the load, you need to consider the following factors:
Internal Pressure Load: The internal pressure inside the pipe creates a force that can cause the pipe to expand or contract. This load is calculated using the pipe’s pressure rating, diameter, and material strength.
Thermal Expansion Load: Changes in temperature cause the pipe to expand or contract, resulting in axial thermal forces. This can be calculated using the coefficient of thermal expansion (CTE) of the pipe material, the temperature change, and the length of the pipe.
Dead Load: This refers to the weight of the pipe itself, the fluid inside the pipe, and any additional components, such as valves or fittings. It is calculated based on the pipe’s density, length, and internal fluid weight.
Live Load: External forces that may be applied to the piping system, such as pressure from the surrounding environment or mechanical loads, are considered in the live load calculation.
Once all these loads are determined, they are combined to calculate the total load acting on the piping system. The calculation helps in selecting appropriate supports, expansion joints, and other accessories to ensure the piping system can safely withstand these loads without failure.
The allowable stress for FRP (Fiberglass Reinforced Plastic) pipe is the maximum stress that the material can withstand without experiencing failure. This stress depends on several factors, including the type of resin used (such as polyester, vinyl ester, or epoxy), the type and amount of fiberglass reinforcement, and the operating conditions of the pipe. Typically, the allowable stress for FRP pipes ranges between 6,000 to 15,000 psi (pounds per square inch), depending on these factors.
To calculate the allowable stress, designers often use industry standards such as ASME or ASTM, which provide guidelines for the design and analysis of FRP piping systems. The allowable stress is determined by applying a safety factor to the material’s ultimate tensile strength, which is the maximum stress the material can endure before breaking. The safety factor accounts for uncertainties in material properties, manufacturing variations, and potential stress concentrators, such as fittings or bends in the pipe.
The allowable stress must be checked against the internal pressure, external loads, and any other factors that might impact the pipe’s performance. In applications where FRP pipes are subjected to high pressures or temperatures, the allowable stress may be lower to ensure the integrity and safety of the piping system.
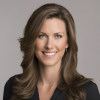
As the editor of GangLong Fiberglass, I have years of experience and in-depth research, focusing on cable tray products, fiberglass solutions, and grille systems. I incorporate years of industry insights and practical experience into every content, committed to promoting the progress of the industry. At GangLong Fiberglass, my commitment is reflected in every product, from innovative cable trays to durable fiberglass solutions and sturdy grille systems. As an authoritative voice in the industry, my goal is to provide valuable information to professionals and businesses and promote forward-looking solutions.