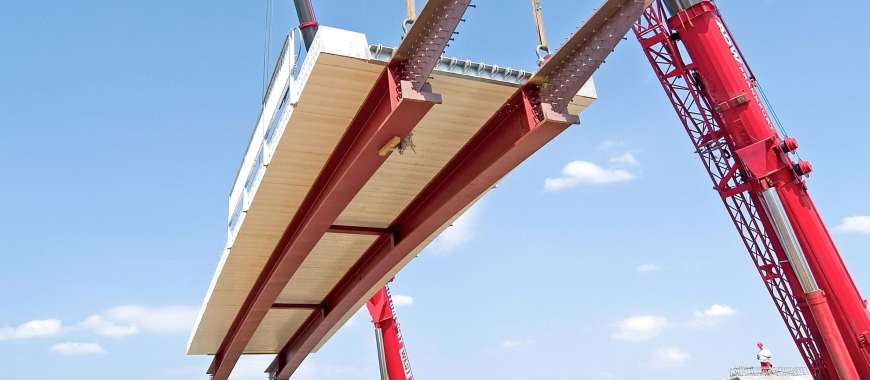
Fiberglass bridge beams are designed using span tables to determine their load-bearing capacity, ensuring optimal performance in various bridge applications. The span table for fiberglass beams and I-beams provides critical data on how these beams perform under different loads and spans, allowing engineers to select the correct beam size for specific projects. Fiberglass bridge beams offer several benefits, including superior strength-to-weight ratios, corrosion resistance, and reduced maintenance costs compared to traditional materials like steel or concrete. The use of fiberglass beams and I-beams in bridge construction has increased due to these advantages, making them a preferred choice for modern infrastructure projects where durability and sustainability are essential. GangLong Fiberglass specializes in manufacturing high-quality fiberglass bridge beams for various applications. Fiberglass bridge beams, or FRP beams, are lightweight, strong, corrosion-resistant, and ideal for girders, supports, and columns in harsh conditions.
What is Fiberglass Bridge Beams?
Fiberglass bridge beams are structural components used in the construction of bridges, primarily for pedestrian, bicycle, and light vehicular traffic. Made from Fiberglass Reinforced Plastic (FRP), these beams provide a lightweight yet highly durable alternative to traditional materials such as steel, concrete, or wood. Often paired with fiberglass reinforced plastic decking, they create a comprehensive solution that ensures excellent corrosion resistance, ease of installation, and long-term structural integrity in various environments, including harsh and corrosive conditions. Fiberglass bridge beams, produced by GangLong Fiberglass, are engineered to meet the demands of modern infrastructure projects while delivering superior performance.
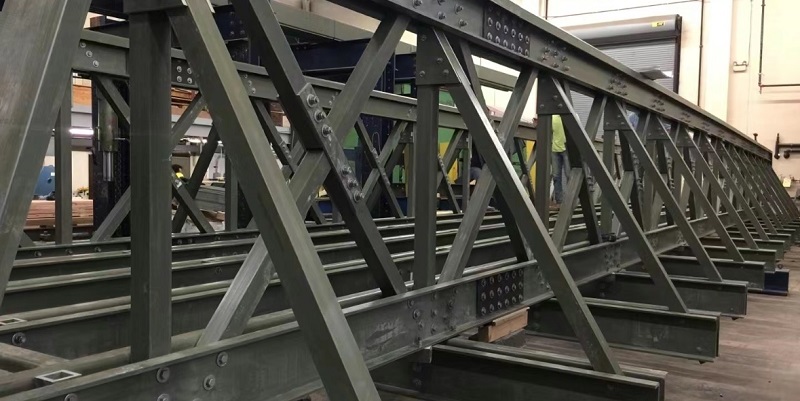
The Key of Fiberglass in Bridge Construction
Fiberglass bridge beams are becoming an increasingly popular choice in modern bridge construction due to their many advantages. Unlike steel or concrete, which can deteriorate over time due to exposure to moisture, chemicals, and varying temperatures, fiberglass bridge beams resist these environmental factors effectively. The core strength of fiberglass bridge beams comes from their composition, which includes a polymer matrix reinforced with glass fibers. This combination creates a material that is both strong and flexible, providing superior performance in areas prone to harsh weather conditions or corrosive elements such as saltwater or industrial pollutants.
Fiberglass bridge beams are also much lighter than their traditional counterparts. This significantly reduces the overall weight of the bridge structure, leading to simpler, more cost-effective construction processes. Lightweight beams also make it easier to transport and install the bridge components, especially in remote or difficult-to-access locations. Moreover, the reduced weight minimizes the need for heavy lifting equipment, cutting down on both labor costs and installation time.
Fiberglass Bridge Beams: Revolutionizing Modern Bridge Construction
Fiberglass bridge beams are a cutting-edge solution in bridge construction, providing numerous advantages over traditional materials such as steel and concrete. These beams, often made from fiberglass-reinforced polymers (FRP), offer significant strength, corrosion resistance, and reduced maintenance requirements. As infrastructure demands increase, fiberglass bridge beams have become a preferred choice for various types of bridges, including pedestrian, bicycle, and light vehicular bridges.
Benefits of Fiberglass Bridge Beams for Pedestrian Bridges
Fiberglass bridge beams offer several benefits when used in pedestrian bridges. These bridges are often built in locations where exposure to the elements is constant, such as in parks, along coastlines, or over rivers. Fiberglass bridge beams are perfectly suited for these settings due to their high resistance to environmental damage.
One of the most notable advantages of fiberglass bridge beams for pedestrian bridges is their ease of maintenance. Traditional materials like wood may require regular inspections, treatments, and replacements due to rot or insect damage, while steel might need frequent painting to prevent corrosion. Fiberglass bridge beams, on the other hand, require minimal maintenance because they are not susceptible to these forms of deterioration. Once installed, they can remain in place for decades with little more than routine inspections.
Fiberglass bridge beams also offer design flexibility, allowing architects and engineers to create aesthetically pleasing pedestrian bridges that blend seamlessly into their surroundings. The material can be molded into various shapes and sizes, making it suitable for both modern and traditional bridge designs. This versatility, combined with the long-lasting durability of fiberglass, makes it an excellent choice for pedestrian bridge projects.
Benefits of Fiberglass Bridge Beams for Vehicular Bridges
Fiberglass bridge beams are not limited to pedestrian use; they can also be employed in light vehicular bridges. Bridges for bicycles, golf carts, and other lightweight vehicles benefit greatly from the use of fiberglass bridge beams. The lightweight nature of the material reduces the overall load on the bridge structure, enabling the use of fewer or lighter support elements, which simplifies construction and reduces costs.
Fiberglass bridge beams from GangLong Fiberglass are designed to support the weight of light vehicular traffic while maintaining the same resistance to environmental factors as pedestrian bridges. For example, bridges used in golf courses or parks often face similar environmental challenges as pedestrian bridges, including exposure to moisture, chemicals, and UV rays. The strength and resilience of fiberglass bridge beams ensure that these structures remain safe and functional for years without the need for frequent repairs or replacements.
Case Study: Fiberglass Bridge Beams in Pedestrian and Bicycle Bridges
One successful application of fiberglass bridge beams can be found in a pedestrian and bicycle bridge installation in a coastal region. In this case, GangLong Fiberglass supplied the fiberglass bridge beams used in the construction of a bridge that needed to withstand constant exposure to saltwater and heavy winds. The use of traditional materials like steel or wood would have required extensive protective measures to combat corrosion, but fiberglass beams provided a low-maintenance solution that ensured the long-term viability of the bridge.
The beams were lightweight enough to be transported and installed with minimal equipment, reducing both labor costs and construction time. Since its installation, the bridge has required minimal maintenance, and its performance remains consistent despite exposure to harsh environmental conditions.
Fiberglass Bridges for Pedestrian and Vehicular Use
Fiberglass bridges have proven to be an ideal solution for both pedestrian and light vehicular use. Their lightweight construction allows for quicker installation, often reducing labor costs and minimizing the impact on surrounding environments. This is particularly important in projects where environmental preservation is a priority, such as in parks, nature reserves, and coastal areas.
In pedestrian applications, fiberglass bridges provide safe, sturdy crossings for walkers, cyclists, and equestrians. They are often used in boardwalks, park trails, and other recreational areas where maintaining a natural aesthetic is essential. Since fiberglass materials can be colored and textured, they blend well with natural surroundings without compromising on strength or durability.
What are the Cost Benefits of Fiberglass Bridge Beams?
Fiberglass bridge beams offer significant cost benefits throughout the lifecycle of a bridge. The initial cost of purchasing and installing fiberglass beams is often lower than that of traditional materials due to the reduced weight and ease of installation. The beams can be fabricated to precise specifications, reducing the need for on-site modifications and speeding up the construction process. For certain specialized infrastructure applications, components like fiberglass fuse tube can be integrated to enhance performance and safety, showcasing the versatility of fiberglass materials.
Over time, the savings continue due to the minimal maintenance requirements of fiberglass bridge beams. Unlike steel, which requires regular inspections for rust and corrosion, or wood, which must be treated for rot and insect damage, fiberglass beams remain structurally sound for decades with little to no upkeep. This reduces the long-term cost of ownership, making fiberglass bridge beams a highly cost-effective solution for both pedestrian and light vehicular bridges.
Additionally, the longevity of fiberglass bridge beams means fewer replacements over the life of the bridge, further contributing to long-term savings. In areas with particularly harsh environmental conditions, this durability can make the difference between a bridge that lasts a few decades and one that lasts several generations.
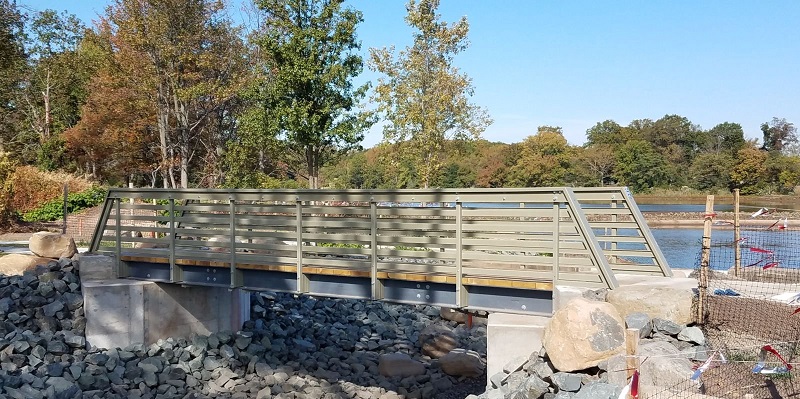
Cost Efficiency and Maintenance Benefits of Fiberglass Bridge Beams
Fiberglass bridge beams are not only strong and durable but also highly cost-efficient. The reduced weight of fiberglass beams lowers transportation costs, while their ease of installation reduces labor expenses. Moreover, the long-term maintenance benefits are substantial, as fiberglass requires minimal upkeep compared to traditional materials like steel or wood.
In addition to these cost savings, fiberglass bridge beams also have a longer lifespan, making them a wise investment for municipalities, private developers, and industrial operators looking for sustainable infrastructure solutions. Since fiberglass does not corrode, rot, or warp, the need for repairs and replacements is significantly reduced, further driving down the long-term costs associated with bridge maintenance.
How about the Environmental Impact of Fiberglass Bridge Beams?
Fiberglass bridge beams also offer environmental benefits. The production of fiberglass requires less energy than the production of steel or concrete, resulting in a smaller carbon footprint. Furthermore, because fiberglass bridge beams are lighter, they require less fuel for transportation to the installation site, further reducing environmental impact.
The long lifespan of fiberglass bridge beams also contributes to their sustainability. Fewer replacements mean less material waste over time, which is especially important in large infrastructure projects. Fiberglass bridge beams from GangLong Fiberglass can be designed with sustainability in mind, ensuring that they provide not only economic advantages but also environmental ones.
The Key of Installing Fiberglass Bridge Beams in Remote Locations
Fiberglass bridge beams are ideal for installation in remote or difficult-to-access locations due to their lightweight and easy-to-handle nature. In many cases, transporting heavy steel or concrete beams to remote sites can be both challenging and costly. The lightweight nature of fiberglass allows for the use of smaller vehicles and fewer resources to transport the beams, reducing both environmental and financial costs.
Once on site, the installation of fiberglass bridge beams requires minimal equipment. In some cases, the beams can be installed manually or with the help of light machinery, making them an ideal solution for bridges in rural areas, nature reserves, or other locations where heavy equipment might not be practical. The quick installation process also means that the bridge can be completed in less time, minimizing disruption to the surrounding area.
Benefits of Fiberglass Bridge Beams in Harsh Environments
Fiberglass bridge beams are particularly well-suited to environments where traditional materials would struggle to perform. Coastal regions, industrial zones, and areas with high levels of pollution can all benefit from the corrosion-resistant properties of fiberglass. Unlike steel, which can rust or degrade in the presence of saltwater or chemicals, fiberglass bridge beams from GangLong Fiberglass remain unaffected by these elements, maintaining their strength and integrity over time.
In addition to their corrosion resistance, fiberglass bridge beams are also resistant to UV radiation. This is particularly important in regions with high sun exposure, where UV rays can cause degradation in other materials. Fiberglass beams are designed to withstand years of exposure to the sun without becoming brittle or losing their structural integrity.
What are the Design Flexibilities of Fiberglass Bridge Beams?
Fiberglass bridge beams offer a high degree of design flexibility, making them suitable for a wide range of bridge applications. GangLong Fiberglass can manufacture beams in various shapes, sizes, and configurations to meet the specific needs of a project. Whether the bridge requires straight beams, curved sections, or complex geometries, fiberglass can be molded to fit the desired design.
This design flexibility extends to the aesthetic aspects of the bridge as well. Fiberglass bridge beams can be customized with various finishes and colors to blend in with the surrounding environment or to create a distinctive visual impact. This makes them an excellent choice for bridges in parks, urban areas, or other locations where aesthetics are important.
Fiberglass bridge beams are an innovative solution for modern bridge construction, offering a combination of durability, cost-effectiveness, and environmental benefits. Whether for pedestrian, bicycle, or light vehicular bridges, the versatility and resilience of fiberglass make it an ideal material for both current and future infrastructure projects.
The Key of Fiberglass Bridge Beams for Modern Infrastructure
Fiberglass bridge beams play a crucial role in modern infrastructure, offering several benefits over traditional materials. Their ability to resist environmental degradation and maintain strength over time makes them ideal for long-term bridge construction projects.
One of the primary advantages of fiberglass bridge beams is their lightweight nature, which makes them easier to transport and install. This feature is particularly beneficial in remote areas where heavy equipment might be difficult to deploy. By reducing the weight of the beams, construction crews can expedite the installation process without compromising on the strength and durability required for long-lasting structures.
Another important factor in using fiberglass bridge beams is their resistance to corrosion. Unlike steel, which is prone to rust when exposed to moisture, salt, and other corrosive agents, fiberglass is impervious to these conditions. This makes fiberglass bridge beams highly effective in coastal regions, areas with high humidity, or locations exposed to saltwater.
Furthermore, fiberglass bridge beams offer greater flexibility in design. Engineers can tailor the shape and size of the beams to meet specific project requirements, allowing for more creative and efficient bridge designs. The versatility of fiberglass materials also allows for better load distribution, minimizing the risk of stress concentrations that could lead to structural failures.
The Benefits of Fiberglass Bridge Beams for the Environment
In addition to their performance advantages, fiberglass bridge beams offer several environmental benefits. The production of fiberglass requires fewer raw materials and generates less waste compared to steel or concrete. Moreover, the long lifespan of fiberglass beams reduces the need for replacements, leading to lower resource consumption over the life of the bridge.
Fiberglass bridge beams also contribute to energy savings during transportation and installation. Since they are lighter than traditional materials, less energy is required to transport them to the construction site. Similarly, the reduced need for heavy machinery during installation means that less fuel is consumed, resulting in lower greenhouse gas emissions.
Additionally, the corrosion resistance of fiberglass bridge beams eliminates the need for chemical treatments or coatings that are often applied to steel or concrete to prevent rust and decay. This reduces the release of harmful chemicals into the environment and minimizes the maintenance-related environmental impact.
How about the Durability of Fiberglass Bridge Beams?
The durability of fiberglass bridge beams is one of their most defining characteristics. The composite material used in these beams is designed to endure harsh environmental conditions, including extreme temperatures, UV radiation, and chemical exposure. Over time, traditional materials like concrete and steel can degrade due to these factors, but fiberglass bridge beams retain their structural integrity for decades. In some applications, components like fiberglass fluted tube can be incorporated into the design to enhance structural performance and aesthetic appeal, further showcasing the versatility of fiberglass materials.
Fiberglass bridge beams are particularly useful in regions where bridges are subjected to constant wear and tear from traffic, weather, and environmental hazards. The inherent durability of fiberglass ensures that these beams can withstand repeated stress without cracking, bending, or weakening. This longevity reduces the need for frequent repairs or replacements, ultimately lowering maintenance costs over the life of the bridge.
Moreover, fiberglass bridge beams are not susceptible to the fatigue and creep that can affect other materials. This means they maintain their load-bearing capacity over time, even in high-stress applications. As a result, these beams provide a reliable solution for bridge structures that require long-lasting performance under demanding conditions.
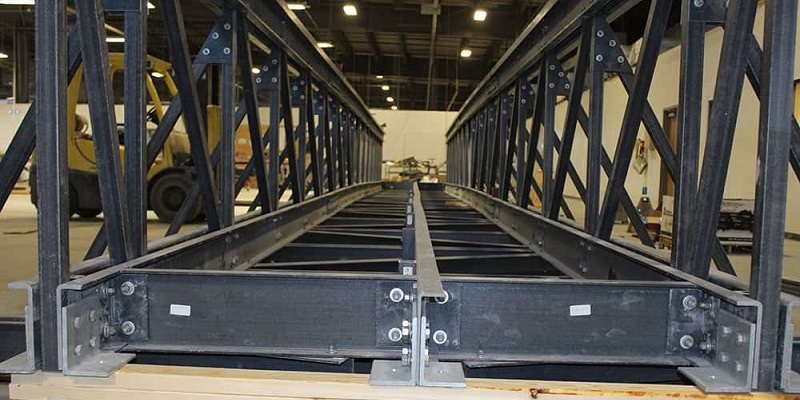
Installation Process for Fiberglass Bridge Beams
The installation process for fiberglass bridge beams is relatively straightforward and requires minimal heavy equipment compared to traditional construction materials. Below is a typical installation guide:
- Preparation of the Site: Before installing the fiberglass bridge beams, the site needs to be prepared. This includes clearing any obstructions and ensuring that the foundations are stable and ready to support the new beams. In some cases, existing structures may need to be removed or reinforced to accommodate the new beams.
- Beam Assembly: Depending on the project, fiberglass bridge beams may be shipped in sections or fully assembled. For larger projects, the beams are often assembled on-site to ensure proper alignment and reduce transportation costs. GangLong Fiberglass provides detailed assembly instructions, allowing construction teams to quickly and accurately assemble the beams.
- Positioning the Beams: Once assembled, the fiberglass bridge beams are carefully positioned onto the bridge piers or abutments. Due to their lightweight nature, the beams can be lifted using smaller cranes or hoists, which simplifies the installation process. Proper alignment is crucial to ensure that the beams distribute the load evenly across the structure.
- Securing the Beams: After positioning, the beams are secured in place using bolts, brackets, or other fastening systems as specified by the project’s engineering design. Fiberglass bridge beams can also be bonded to other structural components using adhesive systems specifically designed for composite materials.
- Final Inspection: Once the beams are installed and secured, the structure undergoes a final inspection to ensure that everything is properly aligned and meets safety standards. This includes checking the load-bearing capacity, reviewing the fastening systems, and confirming that the beams are free of any defects or damage.
Applications of Fiberglass Bridge Beams
Fiberglass bridge beams are versatile and can be used in a variety of applications across different types of bridges. Some common applications include:
- Pedestrian Bridges: Fiberglass bridge beams are ideal for lightweight pedestrian bridges due to their ease of installation and resistance to weathering. These bridges are commonly found in parks, recreational areas, and nature reserves where aesthetic appeal and durability are key considerations.
- Vehicular Bridges: Fiberglass bridge beams can also be used in small to medium-sized vehicular bridges. Their strength and resistance to corrosion make them suitable for roadways that cross over water bodies, ravines, or areas prone to flooding.
- Industrial Bridges: In industrial settings, fiberglass bridge beams are often used to construct bridges that transport heavy equipment or vehicles. Their ability to withstand chemical exposure and extreme temperatures makes them particularly useful in areas such as mining, oil refining, and chemical manufacturing plants.
- Temporary Bridges: Because they are lightweight and easy to install, fiberglass bridge beams are often used in the construction of temporary bridges for military or emergency purposes. These beams can be quickly deployed in disaster-stricken areas or remote locations where access is needed.
The Importance of the Challenges of Fiberglass Bridge Beams?
Despite their numerous benefits, there are some challenges associated with using fiberglass bridge beams. One of the primary challenges is the initial cost. Fiberglass materials tend to be more expensive than traditional materials like steel or concrete. However, this higher upfront cost is often offset by the reduced maintenance and longer lifespan of the beams.
Another challenge is the limited familiarity among construction crews and engineers. While fiberglass bridge beams are becoming more widely adopted, they still represent a relatively new technology in the civil engineering field. As a result, some teams may require additional training or experience to work effectively with fiberglass materials.
Lastly, the load-bearing capacity of fiberglass bridge beams may not be suitable for all types of bridges, particularly those that carry extremely heavy loads. In such cases, engineers may need to reinforce the beams with other materials or opt for hybrid designs that combine fiberglass with steel or concrete.
Maintenance and Longevity of Fiberglass Bridge Beams
Maintenance of fiberglass bridge beams is minimal compared to traditional materials, which require regular inspections, cleaning, and protection against corrosion. Fiberglass beams do not require protective coatings or painting, and they can endure decades of use with little to no intervention. In some designs, fiberglass two beams together can be utilized to enhance load-bearing capacity and structural stability, offering a tailored solution for projects requiring added strength and durability.
Regular visual inspections are typically sufficient to ensure the beams remain in good condition. This involves checking for any signs of surface damage, cracks, or wear. In the rare event of damage, fiberglass beams can be repaired using specialized bonding materials that restore their structural integrity.
Fiberglass bridge beams are expected to last at least 50 years or more, depending on environmental conditions and the specific application. This long service life, coupled with their low maintenance requirements, makes fiberglass bridge beams a cost-effective solution for long-term infrastructure projects.
GangLong Fiberglass offers a range of high-quality fiberglass bridge beams designed to meet the demands of modern construction projects. Their products are tailored to withstand challenging environmental conditions and deliver exceptional performance across a wide range of applications. By choosing fiberglass bridge beams, engineers and builders can take advantage of a material that offers unparalleled durability, versatility, and sustainability in bridge construction.
The Key of FRP Truss Bridges
FRP truss bridges are a prime example of how fiberglass materials can be utilized effectively in modern infrastructure projects. A truss bridge consists of a structure with interconnected triangular units, which provide stability and strength. The use of FRP for these bridges has gained popularity due to its durability, lightweight properties, and resistance to environmental factors like corrosion, UV radiation, and moisture.
Fiberglass truss bridges are particularly advantageous in areas prone to harsh weather conditions or environments with high humidity or salt content. Since FRP materials do not rust or corrode, these bridges can last significantly longer than traditional metal or wooden structures. They also require less maintenance, reducing the overall costs for municipalities and private entities responsible for upkeep.
Applications of FRP Truss Bridges
FRP truss bridges are used in a wide variety of applications, from pedestrian walkways and bicycle paths to light vehicular bridges in parks, golf courses, and nature reserves. These bridges can be designed to meet specific requirements, such as accommodating the weight of emergency vehicles, maintenance trucks, or even light vehicular traffic.
The versatility of FRP truss bridges allows them to be installed in remote or hard-to-reach areas. Since they are lightweight, they can be transported easily, even to sites where heavy machinery cannot access. This makes them ideal for projects in mountainous or rural regions where traditional construction methods would be challenging. Companies like GangLong Fiberglass are leading the way in providing custom-designed FRP truss bridges for a wide range of applications.
Exploring the Benefits of Fiberglass Bridge Decks
One of the key components of modern fiberglass bridge beams is the FRP bridge deck. Unlike traditional concrete or steel bridge decks, FRP decks are much lighter, making them easier to transport and install. They also offer significant resistance to corrosion and weathering, making them an ideal choice for long-term infrastructure projects. In certain applications, fiberglass deck steps can be integrated seamlessly with the deck to provide safe, durable, and lightweight access solutions, further enhancing the usability and versatility of fiberglass bridge systems.
Fiberglass bridge decks are particularly advantageous in regions with extreme temperatures or high levels of moisture, where other materials may degrade more quickly. These decks can withstand temperature fluctuations without expanding or contracting, ensuring a consistent and stable platform for vehicular or pedestrian traffic.
Long-Term Performance of Fiberglass Bridge Decks
The long-term performance of fiberglass bridge decks is a key factor in their increasing use. Since they do not rust or corrode, fiberglass decking require minimal maintenance over their lifespan. This reduces costs associated with repairs, repainting, or resurfacing that are common with traditional materials. Moreover, their lightweight nature means that the overall load on supporting structures, such as columns and beams, is reduced, which can extend the life of the entire bridge system.
Fiberglass bridge decks can also be customized to include anti-slip surfaces, UV protection, and various color options to match aesthetic requirements. These customizations, offered by companies like GangLong Fiberglass, provide flexibility for architects and engineers looking to incorporate both function and design into their projects.
How Fiberglass Tie Beams Improve Structural Stability and Safety
Fiberglass Bridge Beams in Vehicular Bridges
In light vehicular applications, fiberglass bridge beams are increasingly being used in places like parks, golf courses, and industrial facilities where vehicles such as maintenance trucks, utility vehicles, and emergency vehicles need access. The lightweight yet strong nature of fiberglass beams ensures that these structures can support vehicular loads without requiring the same level of foundation work as heavier materials.
Furthermore, fiberglass bridge beams offer excellent resistance to vehicular wear and tear, making them a cost-effective choice for long-term infrastructure. GangLong Fiberglass provides customized solutions for vehicular bridges, ensuring that each project meets the specific load-bearing requirements necessary for safe, efficient traffic flow.
The Advantages of Using Fiberglass I Beam Span Tables
Fiberglass I beam span tables are essential tools used by engineers to determine the load-bearing capacity of fiberglass beams based on their dimensions and the span length. These tables provide critical information on how much weight a beam can support without bending or breaking, ensuring the safety and stability of bridge structures.
By using fiberglass I beam span tables, engineers can optimize their designs, selecting the appropriate beam size for the required load. This ensures that the bridge will have sufficient strength while maintaining the lightweight advantages of fiberglass materials. The span table concept is particularly useful in projects where long spans are required, as fiberglass beams can be manufactured to withstand significant loads over extended distances.
Why Fiberglass Bridge Beams Outperform Traditional Materials
One of the most significant advantages of fiberglass bridge beams is their performance compared to traditional materials like steel or concrete. Fiberglass beams are significantly lighter, which makes them easier to transport, handle, and install. This results in reduced labor and transportation costs, making fiberglass an economical option for many infrastructure projects.
Fiberglass is also non-conductive and non-corrosive, making it an ideal choice for environments where electrical hazards or corrosion from moisture, chemicals, or saltwater may be a concern. Unlike steel, which can rust over time, fiberglass bridge beams maintain their structural integrity even in harsh conditions, reducing the need for frequent repairs or replacements.
How Fiberglass I Beam vs Steel Compares in Bridge Construction
Fiberglass I beams offer numerous benefits when compared to steel beams in bridge construction. While both materials provide strength and durability, fiberglass beams are much lighter, which reduces the overall load on supporting structures and foundations. This allows for more efficient designs, as less reinforcement is needed in the foundations, reducing the overall cost of construction.
Another critical advantage of fiberglass beams over steel is their resistance to corrosion. Steel beams, when exposed to moisture and salt, can rust and degrade over time. This is particularly problematic in coastal areas or regions with high humidity. Fiberglass, on the other hand, is impervious to such conditions, ensuring long-lasting performance without the need for costly maintenance.
Exploring Key Jointing Systems and Essential FRP Pipe Dat
Engineering Flexibility with Fiberglass Bridge Beams
Fiberglass bridge beams offer exceptional engineering flexibility, allowing for custom designs that meet specific project needs. Whether a project requires a pedestrian bridge, a vehicular crossing, or a decorative structure, fiberglass beams can be molded and shaped to fit unique design requirements. This flexibility extends to the load-bearing capabilities, as engineers can specify the exact size and strength of the beams based on the span and load requirements.
GangLong Fiberglass specializes in providing customized fiberglass bridge beams for a wide range of applications. Their engineers work closely with clients to develop tailored solutions that address the specific challenges of each project, ensuring optimal performance and longevity.
The Sustainability of Fiberglass Bridge Beams
As sustainability becomes an increasingly important consideration in infrastructure projects, fiberglass bridge beams offer an eco-friendly alternative to traditional materials. The production of fiberglass materials involves fewer carbon emissions compared to steel or concrete, and their lightweight nature reduces the energy required for transportation. Similarly, fiberglass battery spreader beam contributes to sustainability in industries where safety and non-conductivity are essential, offering an environmentally friendly solution for battery handling and other applications.
Additionally, the long lifespan and low maintenance requirements of fiberglass bridge beams contribute to their sustainability. With fewer resources needed for upkeep and replacement, these beams provide a long-term, environmentally friendly solution for modern bridge construction.
Why Choose Fiberglass Bridge Beams for Your Next Project?
Choosing fiberglass bridge beams for your next infrastructure project ensures a high-performance, cost-effective, and sustainable solution. These beams offer unmatched durability, resistance to environmental factors, and ease of installation, making them ideal for a wide range of applications, from pedestrian walkways to light vehicular bridges. With customization options available from GangLong Fiberglass, you can tailor the beams to meet specific project needs, ensuring optimal performance and long-term reliability.
Key Benefits of UV Resistant FRP Pipe in Harsh Environments
FAQs about Fiberglass Bridge Beams
Fiberglass beams are not as strong as steel when comparing tensile or compressive strength directly. Steel has a higher modulus of elasticity and can handle greater loads without deformation. However, fiberglass beams excel in other areas, such as being lightweight, corrosion-resistant, and non-conductive. This makes them ideal for environments where steel may degrade over time, such as in chemically aggressive or marine settings. For applications like bridge beams, fiberglass can be engineered to handle significant loads while offering benefits like reduced maintenance and longevity in harsh conditions. While fiberglass can’t match steel’s ultimate strength, it often provides sufficient structural capacity for specific use cases, especially when weight reduction or corrosion resistance is prioritized.
The strength of a fiberglass beam depends on its design, material composition, and intended application. Typically, fiberglass-reinforced plastic (FRP) beams have a tensile strength ranging from 30,000 to 100,000 psi, depending on the specific resin and fiber configuration. They also have a flexural strength that can exceed 30,000 psi, making them suitable for structural applications. While not as rigid as steel, fiberglass beams are flexible and can absorb impacts without cracking, making them durable. In bridge construction, fiberglass beams can support substantial loads while resisting environmental damage, making them ideal for lightweight and corrosion-resistant solutions. Their performance in real-world conditions often matches or surpasses expectations in corrosive or moisture-heavy environments.
Fiberglass I-beams are versatile structural components used in a variety of applications. In bridge construction, they are favored for their lightweight and corrosion resistance. They are also used in chemical plants, water treatment facilities, and marine infrastructure where exposure to corrosive elements is common. Fiberglass I-beams provide excellent durability and longevity, requiring minimal maintenance compared to traditional materials like steel or wood. Additionally, their non-conductive nature makes them ideal for electrical applications or environments with high electromagnetic interference. In bridges, they can serve as primary load-bearing components or reinforcement elements, ensuring safety while reducing installation costs and maintenance requirements.
Bridge beams can be made from various materials depending on design requirements and environmental considerations. Common materials include steel, reinforced concrete, and fiberglass-reinforced plastic (FRP). Steel beams are strong and versatile, often used in large, load-intensive bridges. Concrete beams are robust and cost-effective for shorter spans. Fiberglass beams are increasingly used for lightweight, corrosion-resistant applications, particularly in pedestrian or small vehicular bridges. These FRP beams resist environmental degradation and are easier to transport and install due to their reduced weight. Hybrid solutions combining these materials are also used to optimize strength, cost, and durability.
Fiberglass rebar, also known as GFRP (Glass Fiber Reinforced Polymer) rebar, cannot be bent in the same way as steel rebar. Its brittle nature means that attempting to bend it mechanically will result in cracking or breaking. Instead, GFRP rebar is manufactured in pre-bent shapes for specific applications where curves or bends are required. This material’s rigidity and resistance to deformation make it ideal for applications requiring straight reinforcements, such as bridge decks or marine structures. Its inability to bend after production is offset by its superior corrosion resistance and long-term durability in harsh environments.
Fiberglass is not inherently stronger than steel in terms of tensile or compressive strength. Steel typically has a tensile strength of around 60,000 to 100,000 psi, whereas fiberglass ranges from 30,000 to 100,000 psi. However, fiberglass is significantly lighter, often 4–5 times less dense than steel. This gives it a higher strength-to-weight ratio in certain applications. Fiberglass also has advantages in terms of corrosion resistance, chemical inertness, and flexibility, making it ideal for environments where steel might corrode or fail over time. While steel remains the go-to material for load-heavy applications, fiberglass can outperform it in specific contexts, such as bridge components in harsh environments.
Fiberglass rebar has a lower tensile strength than steel rebar, typically ranging from 60,000 to 120,000 psi compared to steel’s 70,000 to 150,000 psi. However, its strength-to-weight ratio is higher, making it more efficient in lightweight applications. Fiberglass rebar is also corrosion-resistant, non-conductive, and impervious to moisture, which makes it ideal for bridge decks, marine structures, and environments exposed to saltwater or chemicals. While not as strong in absolute terms, fiberglass rebar can often achieve the necessary performance for specific structural needs while offering longer-lasting benefits compared to steel.
Steel is often considered the strongest material for bridge construction due to its high tensile and compressive strength. However, advanced composites like carbon fiber and fiberglass-reinforced plastics (FRP) are gaining traction due to their excellent strength-to-weight ratios and resistance to environmental damage. Concrete reinforced with steel remains a dominant material for most bridges because of its affordability and strength. In cutting-edge applications, hybrid solutions combining steel, concrete, and FRP materials optimize strength, durability, and cost-effectiveness.
The weakest part of a bridge often depends on its design and materials. For beam bridges, the weakest points are typically the areas of maximum stress, such as the mid-span of the beams, where bending forces are highest. In suspension bridges, cables and anchorage points are critical stress zones. For fiberglass bridges, joints and connections between beams and other components can be weak points if not properly designed or installed. Environmental factors, such as corrosion or UV degradation, can also affect material strength over time.
Beam bridges typically span lengths of 50 to 250 feet, depending on the materials used. Steel or concrete beams allow for longer spans due to their strength and rigidity. Fiberglass beams, while lighter and corrosion-resistant, are best suited for shorter spans, usually under 100 feet, due to their lower stiffness compared to steel or reinforced concrete. Innovations in composite materials may extend the practical span of fiberglass beam bridges, especially in pedestrian or light-vehicular applications.
Fiberglass is valued for its combination of strength, lightweight properties, corrosion resistance, and durability. In bridge construction, it is used to create beams, rebar, and decking components that are resistant to environmental damage, such as moisture, salt, and chemicals. Fiberglass’s non-conductive nature also makes it ideal for applications requiring electrical insulation. Its use reduces maintenance costs and extends the lifespan of structures, particularly in challenging environments.
Fiberglass-reinforced plastic (FRP) materials can withstand compressive and tensile strengths ranging from 30,000 to 100,000 psi, depending on the resin, fiber composition, and manufacturing process. This strength makes fiberglass suitable for structural components in bridges, especially in environments where durability and resistance to corrosion are critical. While not as strong as steel in absolute terms, fiberglass often provides sufficient strength for its intended applications.
Fiberglass has a higher strength-to-weight ratio than aluminum, making it stronger in terms of relative performance for its weight. Aluminum, however, is stronger in terms of absolute tensile and compressive strength. Fiberglass is more resistant to corrosion and chemical exposure, while aluminum is prone to oxidation in certain environments. For bridge components, fiberglass is preferred for its durability, while aluminum may be used where greater rigidity is needed.
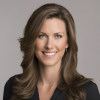
As the editor of GangLong Fiberglass, I have years of experience and in-depth research, focusing on cable tray products, fiberglass solutions, and grille systems. I incorporate years of industry insights and practical experience into every content, committed to promoting the progress of the industry. At GangLong Fiberglass, my commitment is reflected in every product, from innovative cable trays to durable fiberglass solutions and sturdy grille systems. As an authoritative voice in the industry, my goal is to provide valuable information to professionals and businesses and promote forward-looking solutions.