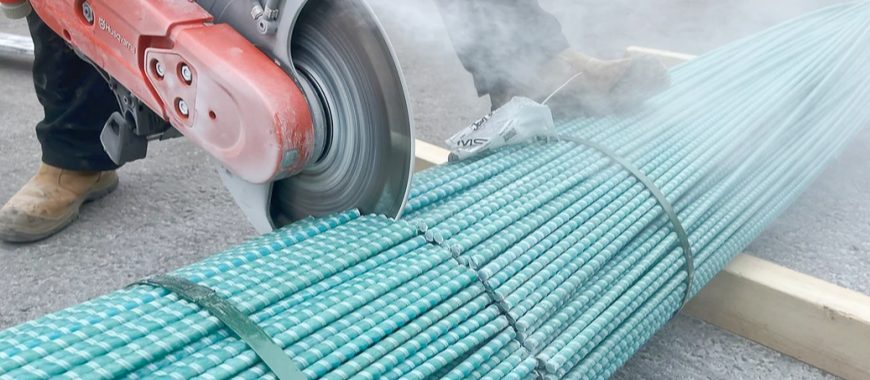
Fiberglass rebar, also known as GFRP (Glass Fiber Reinforced Polymer), is made from a combination of glass fibers and resin. The glass fibers provide the rebar with tensile strength, while the resin acts as a binder, holding the fibers together and offering corrosion resistance. Typically, fiberglass rebar contains around 75% glass fibers, making it both strong and lightweight. When considering what is fiberglass rebar made of, it is important to recognize its advantages over traditional steel rebar, including its resistance to rust, corrosion, and environmental degradation. However, fiberglass rebar does have some limitations, such as reduced flexibility compared to steel, which can make it more challenging to handle in certain applications.
What is Fiberglass Rebar Made Of
Fiberglass rebar, also known as GFRP (Glass Fiber Reinforced Polymer), is made from a combination of high-strength glass fibers and polymer resin. This combination of materials results in a product that offers a superior alternative to traditional steel rebar, particularly in environments where corrosion, rust, and environmental degradation are concerns. Fiberglass rebar has become a popular choice for construction projects, particularly in coastal and marine environments, as well as infrastructure projects like bridges and roads. To fully appreciate the benefits of GFRP, it is important to dive into the composition and properties that make it such an effective material.
The primary component in fiberglass rebar is glass fiber. These fibers are responsible for giving the material its high tensile strength, ensuring that it can support substantial loads. The glass fibers are typically arranged in continuous strands and are then embedded in a matrix of polymer resin. This resin acts as the binder, holding the fibers together and providing additional resistance to chemical and environmental degradation. The resulting combination of materials creates a product that is lightweight, strong, and resistant to the kinds of environmental damage that can significantly reduce the lifespan of traditional steel rebar.
The Key Components of Fiberglass Rebar
The main materials used in fiberglass rebar are glass fibers and resin. These components are combined to create a strong, flexible product that is highly resistant to the elements.
- Glass Fibers: The primary structural component of fiberglass rebar is the glass fibers themselves. These fibers are made from silica-based glass, known for its high tensile strength and ability to resist damage from moisture, chemicals, and extreme temperatures. The most commonly used glass type is E-glass, which is highly durable and provides excellent resistance to corrosion and environmental degradation. The fibers are drawn into long, thin strands that are then bundled together to create the core strength of the rebar.
- Resin: The glass fibers are bound together with a resin matrix that holds the fibers in place and gives the rebar its shape. The resin also plays a crucial role in protecting the fibers from exposure to the environment, providing a barrier that keeps out moisture, chemicals, and UV rays. The most common types of resins used in fiberglass rebar are thermosetting resins, such as epoxy, vinyl ester, or polyester. These resins cure into a solid, durable material that enhances the mechanical properties of the rebar.
When combined, these two materials create a rebar product that is not only lightweight and easy to handle but also capable of withstanding harsh conditions that would degrade traditional steel rebar.
The Key of the Composition of Fiberglass Rebar
To understand what is fiberglass rebar made of, it’s essential to recognize the precise role that each component plays in its structure. The glass fibers, which make up around 75% of the material, provide the backbone of the product. These fibers are highly resistant to tension and are responsible for the rebar’s impressive tensile strength. This high glass content is one of the key differences between GFRP and other composite materials, as it ensures that fiberglass rebar can perform well in demanding construction environments.
The polymer resin used in fiberglass rebar serves as a protective matrix that surrounds and supports the glass fibers. The resin not only holds the fibers in place but also offers chemical resistance, ensuring that the rebar does not degrade when exposed to moisture, saltwater, or other corrosive environments. This makes fiberglass rebar an excellent choice for infrastructure projects in coastal regions, where traditional steel rebar might quickly corrode. The polymer matrix also provides insulation properties, making fiberglass rebar non-conductive—a feature that is critical for certain projects, such as those in electrical and magnetic-sensitive environments.
Properties of Fiberglass Rebar
Understanding what is fiberglass rebar made of also involves knowing the specific properties that result from this unique combination of materials. Fiberglass rebar offers a range of fiberglass properties that make it a superior alternative to steel in many applications. One of its most notable features is its resistance to corrosion. Because fiberglass does not rust or corrode when exposed to moisture, it is ideal for use in marine environments, bridges, parking structures, and any other projects where steel rebar would be vulnerable to rusting.
Fiberglass rebar is also non-conductive, which means it does not carry electricity. This property is particularly important in environments where electromagnetic fields could interfere with sensitive equipment or processes. For example, in hospitals or laboratories, fiberglass rebar is often used to prevent any interference with medical or scientific devices. Its non-magnetic properties also make it suitable for military and aerospace applications, where even minor disruptions can have serious consequences.
Another important characteristic of fiberglass rebar is its lightweight nature. Because it is significantly lighter than steel, it is easier to transport and install, reducing labor costs and installation time. Despite its lighter weight, fiberglass rebar maintains excellent strength, ensuring that it can be used in both load-bearing and non-load-bearing structures. This combination of lightness and strength makes fiberglass rebar highly versatile, allowing it to be used in a wide variety of projects.
Fiberglass Rebar vs Steel
When comparing fiberglass rebar to steel, it is important to understand the key differences in material properties. While steel has been the standard material for reinforcing concrete for many years, fiberglass rebar offers several advantages that make it a superior choice in certain applications. One of the primary advantages of fiberglass rebar is its resistance to corrosion. Steel is highly susceptible to rust when exposed to moisture, and even with protective coatings, steel rebar can eventually degrade over time. Fiberglass rebar, by contrast, does not rust or corrode, making it ideal for projects in wet or coastal environments, much like the durability offered by fiberglass support columns in similar conditions.
In terms of weight, fiberglass rebar is significantly lighter than steel. This makes it easier to transport, handle, and install, which can result in lower labor costs and faster construction times. Despite its lighter weight, fiberglass rebar maintains excellent strength and can support substantial loads, making it suitable for use in both small and large-scale projects.
Fiberglass rebar is also non-conductive and non-magnetic, which makes it a better choice for projects where these properties are essential. For example, in environments with sensitive electronic equipment, steel’s conductivity can cause interference, whereas fiberglass rebar’s non-conductivity eliminates this concern.
How to Bend Fiberglass Rebar
Fiberglass rebar can be bent, but it requires different techniques compared to steel. Because fiberglass is more brittle, it cannot be bent on-site as easily as steel. Most bending must be done in a factory setting using specialized equipment. However, for projects that require large-radius bends, fiberglass rebar can often be adjusted on-site. It is important to follow proper bending procedures to avoid damaging the material and to ensure that it retains its strength and integrity.
For custom shapes and designs, it is often recommended to order pre-bent fiberglass rebar from the manufacturer. GangLong Fiberglass offers custom bending services to meet the specific needs of your project, ensuring that the rebar arrives at the site ready for installation.
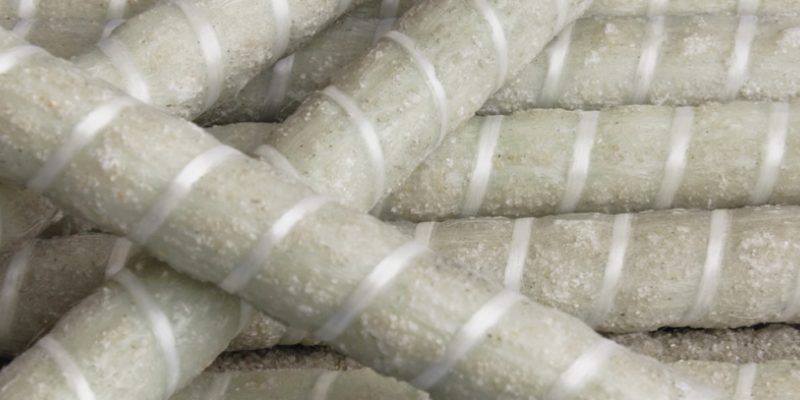
What is Fiberglass Rebar Made Of Disadvantages of Fiberglass Rebar
While fiberglass rebar has numerous advantages, it is also important to acknowledge some potential limitations when considering what is fiberglass rebar made of. One of the main drawbacks is its reduced flexibility compared to steel. Steel rebar can be bent and shaped more easily, making it ideal for projects where tight bends or complex shapes are required. While fiberglass rebar can be bent to a certain degree, it generally requires factory bending to achieve the desired shape, which can be less convenient for on-site adjustments.
Another potential limitation is the fact that fiberglass rebar is more brittle than steel. This means that it can be more prone to breaking if subjected to excessive impact or bending beyond its capacity. This brittleness must be taken into account during the installation process to avoid damaging the material. However, with proper handling and installation, fiberglass rebar can still provide excellent performance.
Advantages of Fiberglass Rebar
There are many advantages to using fiberglass rebar in construction projects. Its resistance to corrosion makes it an excellent choice for projects in wet or marine environments, while its lightweight nature reduces transportation and installation costs. Fiberglass rebar’s non-conductive and non-magnetic properties make it ideal for use in environments where these characteristics are essential, and its long lifespan ensures that structures reinforced with fiberglass rebar will remain strong and durable for decades. The inclusion of long glass fiber in the rebar enhances its strength and performance, further elevating its advantages.
- Corrosion Resistance
- Fiberglass rebar is highly resistant to corrosion, making it an ideal choice for environments exposed to moisture, chemicals, or salt, such as marine structures, bridges, and wastewater treatment plants. Unlike steel, it does not rust, reducing long-term maintenance costs.
- Lightweight
- It is approximately 75% lighter than steel rebar, making it easier to transport, handle, and install. This reduces labor costs and increases efficiency on construction sites.
- High Tensile Strength
- Fiberglass rebar has a tensile strength that is significantly higher than that of steel, providing strong reinforcement for concrete structures while maintaining durability.
- Non-Conductive and Non-Magnetic
- It is electrically non-conductive and non-magnetic, which is advantageous for applications in MRI rooms, electrical substations, and other environments where electromagnetic interference must be avoided.
- Resistance to Temperature Variations
- Fiberglass rebar maintains its integrity and strength in a wide range of temperatures, making it suitable for extreme climates.
- Long Service Life
- Due to its corrosion resistance and durability, structures reinforced with fiberglass rebar tend to have a longer service life, particularly in aggressive environments.
- Eco-Friendly
- It does not leach harmful chemicals into the environment and requires less frequent replacement compared to steel, reducing material waste over time.
Disadvantages of Fiberglass Rebar
- Higher Initial Cost
- Fiberglass rebar is typically more expensive upfront than traditional steel rebar. This can make it less appealing for projects with tight budgets, despite the potential for long-term savings.
- Lower Modulus of Elasticity
- Fiberglass rebar has a lower modulus of elasticity compared to steel, meaning it is less stiff and can deflect more under load. This property may limit its use in certain high-stress applications where rigidity is crucial.
- Brittle Nature
- Unlike steel, fiberglass rebar does not yield before breaking, meaning it can fail suddenly under excessive load. This makes proper design and load calculations critical to ensure safety.
- Limited Fire Resistance
- Fiberglass rebar may degrade when exposed to high temperatures for extended periods, potentially compromising the structural integrity of fire-exposed constructions.
- Compatibility with Concrete
- Its thermal expansion coefficient differs from that of concrete, which may lead to stress issues in certain conditions. Special considerations must be made during design and construction to mitigate this risk.
- Special Handling and Cutting Requirements
- Fiberglass rebar requires diamond-coated blades for cutting, as traditional steel cutting tools are not effective. This can increase handling complexity and costs.
- Limited Awareness and Adoption
- Many engineers and contractors are less familiar with fiberglass rebar compared to steel, which can lead to hesitation or improper usage in projects.
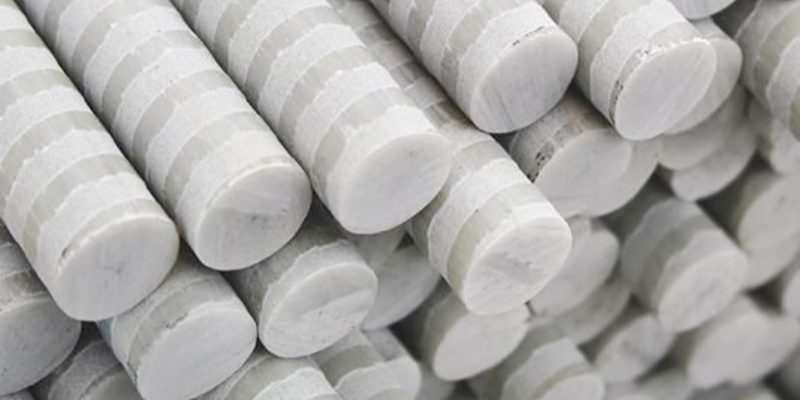
What Is Fiberglass Rebar Made of: Fiberglass Rebar for Sale
Fiberglass Rebar Price
When it comes to the price of fiberglass rebar, several factors must be considered. The cost of fiberglass rebar can vary depending on its composition, the manufacturing process, and market availability. Fiberglass rebar is generally more expensive upfront than traditional steel rebar, but the long-term benefits of using it can result in overall cost savings. Because fiberglass rebar is highly resistant to corrosion and does not require the same level of maintenance as steel, the long-term maintenance and repair costs are much lower, much like the durability and cost-effectiveness of a fiberglass composite panel in construction applications.
Additionally, the lightweight nature of fiberglass rebar reduces transportation and installation costs, which can further offset the higher initial cost. For large-scale projects, the reduced labor costs associated with easier handling and installation can provide significant financial savings. GangLong Fiberglass offers fiberglass rebar at competitive prices, and custom sizes can be produced to meet specific project requirements.
Average Price Range:
- Per Linear Foot: Fiberglass rebar typically costs between $0.65 and $2.50 per linear foot, depending on the size and specifications.
- Per Meter: Prices range from approximately $2 to $10 per meter, influenced by factors like diameter and manufacturer.
- Per Ton: While specific per-ton prices for fiberglass rebar are less commonly listed, estimates suggest costs ranging from $5,000 to $7,000 per ton, varying with market conditions and bulk purchasing agreements.
Fiberglass Rebar for Sale
For contractors and developers looking for fiberglass rebar for sale, GangLong Fiberglass offers a range of sizes and configurations to meet your project’s requirements. Whether you are working on a small residential project or a large commercial development, fiberglass rebar provides an excellent alternative to steel. GangLong Fiberglass specializes in producing high-quality fiberglass rebar that is designed to withstand harsh environmental conditions while providing long-lasting strength and durability.
When purchasing fiberglass rebar, it is important to consider the specific needs of your project, including load requirements, environmental conditions, and the desired shape and size of the rebar. GangLong Fiberglass can produce custom rebar to meet these specifications, ensuring that you get the best possible product for your project.
Exploring Key Jointing Systems and Essential FRP Pipe Data
What Is Fiberglass Rebar Made of: Fiberglass Rebar Uses
Fiberglass rebar is a strong, lightweight, and corrosion-resistant alternative to traditional steel rebar. Made from glass fibers and resin, it is widely used in construction and engineering applications where its unique properties offer significant advantages. Below are the main uses and applications of fiberglass rebar:
Infrastructure Projects
Fiberglass rebar is increasingly used in infrastructure projects where durability and resistance to corrosion are critical:
- Bridges and Overpasses: Ideal for bridge decks, retaining walls, and railings in corrosive environments like coastal areas or regions with heavy de-icing salt use.
- Tunnels: Fiberglass rebar is non-magnetic, making it suitable for electromagnetic-sensitive areas, such as tunnels for transportation or utility conduits.
- Parking Structures: Its resistance to chemicals and water makes it perfect for multi-level parking garages, where moisture and salt exposure are common.
Marine and Waterfront Structures
Because fiberglass rebar does not rust, it is an excellent choice for:
- Docks and Piers: Extends the lifespan of structures exposed to saltwater and harsh marine conditions.
- Seawalls and Breakwaters: Ensures long-term structural integrity in environments with continuous water contact.
- Fish Farms and Aquaculture Tanks: Its non-toxic nature makes it safe for aquatic life.
Industrial Applications
Fiberglass rebar is frequently used in industries where chemical exposure is a concern:
- Chemical Plants: Resistant to acids, alkalis, and other corrosive substances.
- Water Treatment Facilities: Provides longevity in structures exposed to aggressive water treatments and chemicals.
- Storage Tanks: Used in foundations and reinforcements for tanks holding corrosive materials.
Transportation and Roadways
Fiberglass rebar enhances the durability of transportation infrastructure:
- Pavements and Highways: Prevents cracking and deterioration caused by freeze-thaw cycles and de-icing salts.
- Railway Sleepers: A lightweight, non-conductive alternative to steel, reducing maintenance costs.
Buildings and Residential Construction
Fiberglass rebar is utilized in various residential and commercial building projects:
- Foundations: Prevents deterioration in damp or saline soils.
- Concrete Walls and Columns: Offers thermal insulation benefits and reduces thermal bridging in energy-efficient buildings.
- Retaining Walls: Provides structural stability without the risk of corrosion.
Energy and Utility Projects
Fiberglass rebar supports projects in the energy sector:
- Wind Farms: Reinforces concrete foundations for wind turbine towers in offshore and onshore settings.
- Power Plants: Non-conductive and corrosion-resistant properties make it suitable for electrical substations and nuclear power plant structures.
- Solar Farms: Used in ground-mounted systems to support solar panels.
Military and Defense
Its non-magnetic and non-conductive properties are advantageous for:
- Explosive Storage Facilities: Reduces risks associated with static electricity or magnetic interference.
- Radar and Communication Installations: Ensures signal integrity by minimizing electromagnetic interference.
Specialized Applications
Fiberglass rebar is also used in niche applications:
- Swimming Pools: Reinforces pool walls and floors without the risk of rusting, enhancing longevity.
- Sculptures and Monuments: Provides structural support while being lightweight and durable.
- Greenhouses: Used in concrete pathways and foundations due to its resistance to moisture and fertilizers.
Fiberglass rebar’s versatility and durability make it an excellent choice for a wide range of construction and engineering applications, especially in environments where traditional steel rebar would be prone to corrosion or other forms of degradation.
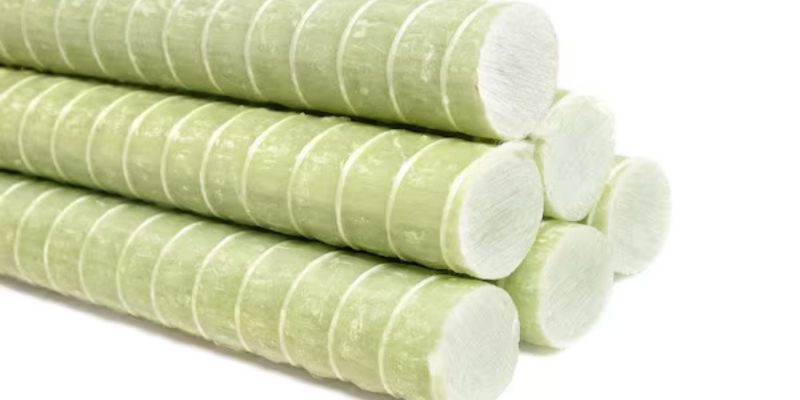
What Is Fiberglass Rebar Made of: The Manufacturing Process of Fiberglass Rebar
Fiberglass rebar, also known as GFRP (Glass Fiber Reinforced Polymer) rebar, is produced through a meticulous process involving advanced materials and techniques. Below is a step-by-step breakdown of its manufacturing process:
Raw Material Preparation
The production of fiberglass rebar begins with two primary components:
- Glass Fibers: These provide the structural strength of the rebar. The most commonly used type is E-glass (electrical grade) due to its high strength and durability.
- Resin: The glass fibers are impregnated with resin (usually epoxy, vinyl ester, or polyester) to form a composite material. The resin binds the fibers and protects them from environmental degradation.
Fiber Treatment
Glass fibers are treated to enhance their bonding properties and improve the compatibility with the resin:
- Sizing: A chemical coating (sizing) is applied to the fibers to ensure they bond well with the resin and remain durable under stress.
- Spooling: The treated fibers are wound onto spools to be used in the next stage of production.
Pultrusion Process
The pultrusion process is a continuous manufacturing method used to produce fiberglass rebar with consistent quality and uniform dimensions:
- Fiber Feed: Glass fibers are pulled from spools and aligned in a specific orientation (usually unidirectional) to ensure maximum tensile strength.
- Resin Bath: The fibers pass through a resin bath where they are thoroughly impregnated with resin. This step ensures the composite material has both strength and durability.
- Forming: The resin-impregnated fibers are passed through a heated die that shapes them into the desired diameter and profile of the rebar (typically round with ribs or surface deformations for better bonding with concrete).
- Curing: Inside the die, heat is applied to cure (harden) the resin. This creates a solid, rigid structure with the desired mechanical properties.
Surface Coating
To improve the bond between the fiberglass rebar and concrete, the surface is often textured or coated:
- Ribbing: Raised patterns or ribs are molded into the surface during the forming process.
- Sand Coating: Sand or other abrasive materials are applied to the surface while the resin is still wet or tacky to enhance adhesion to concrete.
Cutting and Sizing
The cured rebar exits the pultrusion machine as a continuous length. It is then:
- Cut to Size: Using automated cutting tools, the rebar is cut to standard lengths or custom sizes based on specific project requirements.
Key Features of the Process
- Efficiency: The pultrusion process allows for continuous, high-volume production.
- Customizability: Rebar can be manufactured in different diameters, lengths, and coatings to suit diverse applications.
- Environmental Considerations: Many manufacturers use low-emission resins and optimize the process to reduce waste.
Advantages of the Manufacturing Process
- Precision and Consistency: The automated nature of the pultrusion process ensures high-quality, uniform rebar.
- Cost-Effectiveness: Continuous production reduces labor and material costs.
- Adaptability: The process can accommodate variations in resin, fiber type, and design to meet specific project needs.
By leveraging advanced materials and technology, the manufacturing process of fiberglass rebar creates a superior product that meets the demanding needs of modern construction projects.
Key Benefits of UV Resistant FRP Pipe in Harsh Environments
What is Fiberglass Rebar Made Of the Environmental Benefits of Fiberglass Rebar?
Another advantage of fiberglass rebar is its environmental impact. Fiberglass rebar is considered more environmentally friendly than steel because it does not require chemical treatments to prevent corrosion. This eliminates the need for harmful coatings or galvanization processes that can release pollutants into the environment.
Furthermore, fiberglass rebar’s long lifespan and low maintenance requirements mean fewer resources are needed over the course of the structure’s life. Structures reinforced with fiberglass rebar require less frequent repairs and replacements, reducing the consumption of raw materials and the energy needed for construction activities.
By choosing fiberglass rebar, project developers can reduce their environmental footprint while also benefiting from the material’s performance and cost-efficiency.
Customization Options for Fiberglass Rebar
Fiberglass rebar can be customized to meet the specific needs of a project. Manufacturers like GangLong Fiberglass offer a range of options in terms of diameter, length, and resin type, allowing for a tailored solution that fits the unique demands of each application, all in accordance with the required fiberglass rebar specifications.
About what is fiberglass rebar made of,for example, projects that require additional durability or specific resistance to chemicals can choose specialized resins that enhance the performance of the rebar in these environments. Additionally, custom diameters can be specified to ensure that the rebar provides the necessary strength for a particular structure.
Custom lengths are also available, which can help minimize waste and reduce the need for cutting and splicing on-site. By working with a reputable manufacturer.
Applications of Fiberglass Rebar
Fiberglass rebar is used in a variety of applications where corrosion resistance, lightweight properties, and durability are essential. Some of the most common uses of fiberglass rebar include:
- Marine and Coastal Structures: In marine environments, structures such as seawalls, piers, docks, and bridges are constantly exposed to saltwater and moisture, which can quickly degrade steel rebar. Fiberglass rebar is an ideal solution for these environments due to its corrosion resistance and long lifespan.
- Bridges: Bridges, especially those in coastal areas or regions that use de-icing salts, are prone to corrosion when reinforced with steel. Fiberglass rebar provides a corrosion-resistant alternative that can significantly extend the life of the bridge, reducing the need for costly repairs and maintenance.
- Parking Structures: Parking garages are another environment where exposure to moisture, salt, and chemicals can degrade steel rebar. Using fiberglass rebar in these structures can prevent corrosion and ensure long-term durability.
- Tunnels: In tunnel construction, fiberglass rebar is used for its non-conductive properties and corrosion resistance. It is an excellent choice for projects where electromagnetic neutrality is important, or where exposure to moisture is a concern.
- Water Treatment Plants: Water treatment facilities are often exposed to chemicals and moisture that can corrode traditional steel rebar. Fiberglass rebar provides a durable, corrosion-resistant solution that can withstand these harsh environments.
How Fiberglass Tie Beams Improve Structural Stability and Safety
FAQs about What is Fiberglass Rebar Made of
Fiberglass rebar is increasingly seen as a strong alternative to steel rebar in certain applications, but whether it is “as good” as steel depends on the specific requirements of the project. Fiberglass rebar, made from glass fibers and resin, is lightweight and non-corrosive, making it an excellent choice in environments where steel would be prone to rust, such as marine structures, bridges, and chemical plants. It is also resistant to chemicals and moisture, making it ideal for projects that require long-term durability without regular maintenance.
In terms of strength, fiberglass rebar has a high tensile strength, which makes it suitable for reinforcing concrete in many applications. However, fiberglass rebar has lower compressive strength compared to steel, which means it may not be ideal for projects where extreme loads or impacts are expected. Additionally, fiberglass rebar is non-magnetic, making it beneficial for use in projects requiring electromagnetic neutrality, such as MRI rooms in hospitals.
Fiberglass rebar has many advantages, such as corrosion resistance and lightweight properties, but it also comes with some disadvantages that need to be considered in certain applications. One of the primary disadvantages of fiberglass rebar is its lower compressive strength compared to traditional steel rebar. This means that while fiberglass rebar excels in tensile applications, it may not be the best choice for projects that involve high compressive loads or require significant support for vertical structures.
Another disadvantage of fiberglass rebar is its sensitivity to high temperatures. Fiberglass rebar can lose its structural integrity when exposed to extreme heat, which limits its use in applications where fire resistance or exposure to high temperatures is a concern. For example, it may not be suitable for use in tunnels or industrial buildings where fire safety standards are stringent.
In addition, fiberglass rebar is more brittle than steel, meaning that it is more likely to crack or snap under impact or sudden stress. While it is very durable in terms of corrosion resistance, its brittleness can be a concern in situations where flexibility is required. Despite these disadvantages, fiberglass rebar remains an excellent choice for many applications, especially in corrosive or marine environments.
Fiberglass rebar is composed primarily of two key raw materials: glass fibers and resin. The glass fibers provide the strength and flexibility of the rebar, while the resin acts as a binder that holds the fibers together and gives the rebar its solid form. The combination of these materials creates a composite product that is lightweight yet strong and resistant to corrosion, making it ideal for reinforcing concrete in harsh environments.
The glass fibers used in fiberglass rebar are made from a type of glass known as E-glass, which is known for its high strength and resistance to moisture and chemicals. These fibers are woven or bundled together to form a reinforcement structure. E-glass fibers are not only strong but also lightweight, which makes fiberglass rebar much easier to transport and handle compared to steel rebar.
Fiberglass rebar has several downsides. First, it is brittle and lacks the ductility of steel, meaning it cannot bend under stress and may break under excessive loads. Second, it is more expensive than traditional steel rebar in many cases, especially for projects requiring large quantities. Third, it can degrade under ultraviolet (UV) exposure if not properly protected. Finally, its installation requires special tools and handling practices to avoid splinters or damage, adding complexity to construction workflows.
Fiberglass rebar can outperform metal rebar in specific applications, particularly where corrosion resistance is crucial, such as in marine or chemically aggressive environments. However, it is not universally better. Steel rebar is more versatile, stronger under tensile stress, and easier to handle in standard construction projects. Fiberglass lacks the ability to bend and deform, which is a critical property for absorbing loads in some structural designs. Its suitability depends on the project’s environmental and structural demands.
Fiberglass rebar can last for over 100 years if installed correctly and protected from UV exposure. It does not rust or corrode like steel, making it an excellent choice for environments exposed to moisture, salts, or chemicals. Proper installation and adherence to design specifications are essential to ensure its longevity.
No, fiberglass rebar will not bend. It is a rigid material and tends to break or crack when subjected to bending forces beyond its capacity. This lack of flexibility makes it unsuitable for projects that require significant reshaping or custom bending on-site. Special designs or pre-fabrication are necessary to accommodate its rigidity.
Fiberglass rebar can be cut using diamond blade saws, carbide-tipped saws, or abrasive wheels. These tools are preferred because they can cleanly cut through the fibers without causing fraying or splintering. Always use personal protective equipment (PPE) like gloves and goggles to prevent injuries from fiberglass splinters or dust during cutting.
Fiberglass rebar is not inherently stronger than steel in terms of tensile strength. However, it offers better strength-to-weight ratio and corrosion resistance. Steel rebar is much more robust in terms of bending, compressive strength, and overall load-bearing capacity. Fiberglass excels in lightweight, corrosion-resistant applications but does not replace steel’s strength in most structural uses.
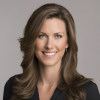
As the editor of GangLong Fiberglass, I have years of experience and in-depth research, focusing on cable tray products, fiberglass solutions, and grille systems. I incorporate years of industry insights and practical experience into every content, committed to promoting the progress of the industry. At GangLong Fiberglass, my commitment is reflected in every product, from innovative cable trays to durable fiberglass solutions and sturdy grille systems. As an authoritative voice in the industry, my goal is to provide valuable information to professionals and businesses and promote forward-looking solutions.