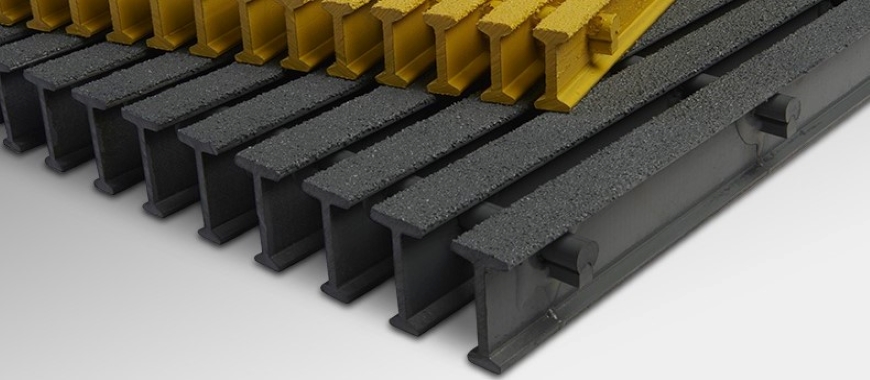
In the modern industrial landscape, the significance of FRP (Fiberglass Reinforced Plastic) grating can hardly be overstated. This composite material, celebrated for its strength, durability, and corrosion resistance, serves as the backbone for various infrastructure projects and industrial applications. A noteworthy element in the value chain of FRP grating is the role played by FRP grating manufacturers, who ensure the availability, quality, and innovation of these essential components. These manufacturers are not merely suppliers; they are pioneers at the forefront of material science, engineering solutions tailored to diverse environmental and operational demands. Through their expertise, FRP grating manufacturer contributes significantly to industries ranging from chemical processing to water treatment, and from marine applications to civil engineering. Their ability to produce grating options that meet stringent requirements for safety and performance makes them indispensable in the quest for more efficient, reliable, and sustainable construction and design solutions. GangLong Fiberglass, a leading FRP grating manufacturer, provides durable, lightweight, corrosion-resistant grating for diverse industrial applications.
What Is FRP Grating of FRP Grating Manufacturer
FRP (Fiberglass Reinforced Plastic) grating, similar to fiberglass reinforced plastic decking, which is emerging as a leading material in numerous industrial and commercial applications due to its unique combination of durability, strength, and versatility. This section will delve into the specifics of what makes FRP grating a revolutionary product and outline its distinct composition and benefits.
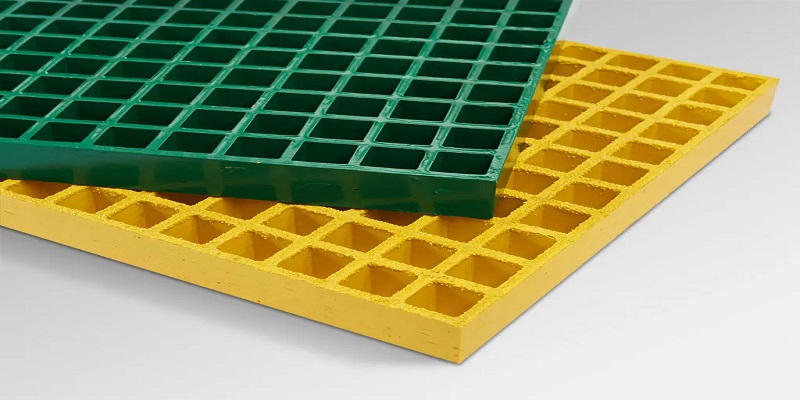
What is FRP Grating?
FRP grating is a composite material consisting of fiberglass reinforcements embedded within a plastic (polymer) matrix. This synergy of materials results in a product that leverages the best attributes of both components – the strength and rigidity of fiberglass and the corrosion resistance of plastics. Here are key aspects that define frp grating material:
- Composition: Made from interwoven strands of fiberglass and bathed in a polymer resin, it provides structural integrity and chemical resistance.
- Durability: Its resistance to corrosion, rot, and rust makes FRP grating an enduring option for various environments.
- Weight: Being lightweight, FRP grating is much easier to transport and install compared to traditional grating materials.
- Maintenance: With a resistance to many chemicals and environmental conditions, FRP requires less maintenance.
- Safety: Features like slip resistance and non-conductivity promote a safer working environment.
- Customization: It can be tailor-made in various shapes, sizes, and colors to meet project specifications.
- Cost-Effectiveness: Although the upfront cost might be higher, savings on maintenance and replacement costs make FRP a sensible long-term investment.
- Environmental Resistance: It withstands a vast spectrum of chemical exposures and environmental challenges with little to no effect.
Best Fiberglass Hot Rod Bodies For Custom Car Building Projects
The Advantages of FRP Grating Over Traditional Materials
The transition from traditional materials like steel and aluminum to FRP grating is driven by the latter’s unmatched benefits. These advantages encompass not just the operational and functional superiority of FRP but also its economic and environmental impacts. Some of these key advantages include:
- Corrosion Resistance: Superior resistance to corrosion means no additional costs for protective coatings or treatments.
- High Strength-to-Weight Ratio: Offers exceptional durability without the heaviness, facilitating easier handling and installation.
- Non-Magnetic: Its non-magnetic property makes it suitable for applications sensitive to magnetic interference.
- Thermal Stability: Exhibits excellent performance across a broad temperature range.
- Electrical Insulation: Provides safety in environments where electrical hazards are present.
- Aesthetic Flexibility: Can be engineered to specific aesthetic requirements without sacrificing functionality.
- Reduced Lifecycle Cost: The combined cost-saving features of durability, low maintenance, and longevity make FRP gratings economically favorable.
- Eco-Friendliness: The recyclable nature of FRP supports sustainable development goals.
The Role of FRP Grating Manufacturers
FRP grating manufacturers are pivotal in driving the adoption and innovation of FRP grating in the marketplace. Their contribution extends beyond mere production, touching upon aspects of design, sustainability, and technological advancements. Here are six key roles they play:
- Innovation and Customization: Manufacturers innovate to meet specific industry needs, offering customization in terms of sizes, colors, and finishes.
- Quality Assurance: They adhere to stringent quality standards, ensuring durability, reliability, and performance of FRP grating.
- Technical Support: Manufacturers provide invaluable technical advice and support, from product selection to installation guidelines.
- Sustainability Efforts: By incorporating environmentally friendly practices and materials, they contribute towards sustainable construction.
- Market Adaptation: They continuously adapt to market changes and demands, ensuring their products meet contemporary needs and regulations.
- Education and Awareness: Through outreach and information dissemination, manufacturers educate the market about the benefits and applications of FRP grating, fostering adoption and innovation.
FRP grating manufacturers are not just suppliers; they are invaluable partners in the development of safer, more efficient, and sustainable industrial environments.
A Guide to FRP Grating Manufacturers
Selecting the right FRP grating manufacturer is crucial for ensuring the quality, durability, and effectiveness of your FRP grating projects. This guide dives into the core of what makes a reliable FRP grating manufacturer, focusing on their manufacturing processes, standards, and the role of innovation and quality control in their operations.
Insights into the Manufacturing Processes and Standards
When exploring the capabilities of an FRP grating manufacturer, understanding their manufacturing processes and adherence to standards is fundamental.
- Raw Materials Selection: Top-tier manufacturers prioritize high-quality raw materials, sourcing premium-grade resin and fiberglass to ensure the final product’s strength and durability.
- Resin Systems: The choice of resin (polyester, vinylester, phenolic, etc.) is tailored to the application’s specific environmental and chemical exposure, optimizing product performance.
- Molding Techniques: Techniques such as pultrusion and molding (open mold and compression mold) are commonly employed, each having distinct advantages in terms of product consistency and dimensional accuracy, particularly with the use of a pultrusion mold, which ensures high precision in the manufacturing of composite materials.
- Surface Textures: They offer a variety of surface textures (gritted, concave, smooth) to match the slip resistance and aesthetic requirements of different applications.
- Quality Standards Compliance: Reputable manufacturers comply with international quality standards like ISO and ASTM, ensuring their products meet global benchmarks for safety and performance.
- Dimensional Accuracy: Precision in the manufacturing process ensures that the FRP grating meets exact specifications for fit and function, reducing installation time and costs.
- Environmental Considerations: Leading manufacturers incorporate sustainable practices, such as recycling raw materials and reducing emissions, into their production processes.
- Customization Capability: The ability to customize products in terms of dimensions, colors, and performance characteristics is a mark of an adaptable and customer-focused FRP grating manufacturer.
Innovation and Quality Control in Manufacturing
Innovation and stringent quality control are the backbones of an FRP grating manufacturer’s ability to deliver superior and reliable products.
- R&D Investment: Continuous investment in research and development is essential for pioneering new materials, designs, and manufacturing techniques that enhance product performance.
- Advanced Fabrication Technologies: Adoption of cutting-edge fabrication technologies ensures higher precision and efficiency in the manufacturing process.
- Quality Control Protocols: Implementing rigorous quality control measures at every stage of production, from raw material inspection to final product testing, guarantees consistency and reliability.
- Product Testing and Certification: Leading manufacturers subject their products to extensive testing, securing certifications that attest to their quality, safety, and performance.
- Training and Skill Development: Ongoing training programs ensure that the workforce is skilled in the latest manufacturing and quality control techniques.
- Feedback Integration: A system to integrate customer feedback into product development allows for continuous improvement and innovation.
- Safety Standards Adherence: Commitment to safety, both in terms of product usage and the manufacturing process, is a priority, with strict adherence to workplace safety and product safety standards.
- Collaboration with Industry Experts: Partnerships with academic and industry experts foster innovation and the adoption of best practices in FRP grating manufacturing.
By focusing on these aspects, an FRP grating manufacturer not only demonstrates their commitment to delivering superior products but also their dedication to driving the industry forward through innovation and quality excellence. Whether for industrial, commercial, or recreational applications, the right manufacturer can significantly impact the success and lifespan of FRP grating projects.
Types of FRP Grating Offered by Manufacturers
Type | Molded FRP Grating | Pultruded FRP Grating |
---|---|---|
Composition | Created by interlocking fibers and a resin matrix in a mold. | Made by pulling fibers through a resin bath and forming them using a continuous process. |
Strength | Good strength-to-weight ratio suitable for a wide range of applications. | Higher load-bearing capacity and is designed for longer spans and heavier loads. |
Corrosion Resistance | Highly resistant to a broad range of chemicals. | Exceptional resistance to chemical and corrosive environments. |
Installation | Easy installation due to lightweight design. | Often requires specialized equipment for installation due to its rigid nature. |
Cost | Generally lower initial cost compared to pultruded gratings. | Typically costs more but offers increased longevity in demanding environments. |
Surface | Often features a slip-resistant surface as a standard. | Can be manufactured with different profiles for slip resistance or designed to meet specific requirements. |
Application Areas and Specifications of Each Type
- Industrial Flooring: Molded FRP grating is widely used for industrial flooring due to its durability and safety features.
- Walkways and Platforms: Pultruded FRP grating provides the necessary support and stability for walkways and platforms in industrial settings.
- Water Treatment Facilities: FRP gratings’ resistance to corrosion makes it ideal for use in water treatment plants and other wet environments.
- Chemical Plants: The chemical resistance of pultruded grating often makes them the preferred choice for chemical plant applications.
- Marine Applications: Molded FRP grating is used in docks, marinas, and other marine environments due to its ability to withstand harsh weather and sea water.
- Architectural Projects: Pultruded grating is increasingly used for aesthetic applications in architectural projects due to its customizability and sleek appearance.
By understanding these aspects, consumers can make informed decisions when working with an FRP grating manufacturer that meets their specific needs.
Spotlight on FRP Grating Factory
The world of industrial flooring solutions has seen a rising star in recent years – FRP (fiberglass reinforced plastic) grating. With its robust properties and versatile applications, FRP grating has become a preferred material for a variety of industries. In this comprehensive exploration, we’ll focus on the intricacies of FRP grating factories, dive deep into their operation, understand the rigorous production processes and high standards for quality, compare them with reinforced fiberglass box manufacturers, and provide guidance on finding and collaborating with the right FRP grating manufacturer for customized solutions.
Deep Dive into the Operation of FRP Grating Factories
- Design and Engineering: The genesis of FRP grating is in its design. Engineers must balance factors such as load-bearing capacity, slip resistance, chemical resistance, and fire-retardancy to tailor products to specific industrial demands.
- Material Selection: Selecting quality raw materials is crucial to the final product’s performance. Typically, a combination of resin, fiberglass, and additives is used to form the grating, and the choice of each component can significantly affect the grating’s attributes.
- Molding Process: FRP grating manufacturers may employ different molding techniques, such as pultrusion or molding, to create the desired shapes and sizes. This process involves pulling the fibrous material through a resin mixture and then into a heated die, and each method has its unique advantages.
- Curing and Cooling: Once the FRP grating has been molded, it needs to be cured appropriately. This stage solidifies the material, giving it its strength and durability. Then, it’s cooled and taken for further processing or finishing.
- Trimming and Finishing: After cooling, the gratings are inspected, trimmed, and finished. Any excess material from the molding process is removed to ensure that the final product meets the precise dimensions and specifications.
- Quality Control: Stringent quality control measures are integral to the operation of FRP grating factories. These measures ensure the grating meets industry standards and the certifications required by various sectors, such as construction and marine.
Long Fiberglass Rods: Essential Uses For Gardening
Understanding the Production Processes and the Quality Emphasis
- Detailed Engineering Analysis: Before production begins, a detailed engineering analysis tailors the FRP grating to its intended use, whether that is for heavy industry, commercial infrastructure, or offshore platforms.
- Choice of Resin Systems: A thorough selection process for the resin system, considering the intended application’s environmental and mechanical stresses, is a turning point in ensuring quality.
- Fiber Weaving and Lay-Up: The method in which fibers are woven and laid up contributes to the finished product’s overall strength and durability, thus requiring careful precision and technique.
- Heat and Pressure Application: During production, the controlled application of heat and pressure is critical to achieving high-quality, consistent results.
- Continuous Quality Monitoring: Throughout the manufacturing process, ongoing quality monitoring is essential, including checks for thickness, weight, and environmental resistance.
- Testing and Certification: A comprehensive testing regime, which may include load testing, slip resistance, fire safety, and others, ensures compliance with standards and provides certifications that are often critical for end-users.
Finding the Right FRP Grating Manufacturer
Selecting a trustworthy FRP grating manufacturer is paramount for any industrial project. Here are eight essential tips to guide you:
- Accreditations and Certifications: Look for a manufacturer with recognized industry accreditations and product certifications, as these are indicators of reputable practices and high standards.
- Industry Experience: Consider the manufacturer’s experience in your industry. A company that has successfully completed projects similar to yours can provide insights and improved solutions.
- Manufacturing Capabilities: Assess whether the manufacturer’s facilities and technologies can meet your project’s scale and complexity.
- Customization: Verify the manufacturer’s ability to provide customization options tailored to your specific needs.
- Material Quality: Inquire about the source and quality of the materials used in manufacturing the FRP grating.
- Technical Support: Look for manufacturers that offer robust pre-sales technical support and can guide you through the selection process based on your performance requirements.
- After-Sales Service: A reliable FRP grating manufacturer will offer excellent after-sales service, addressing any issues with the product promptly and efficiently.
- Client Testimonials: Seek out and consider client testimonials and case studies that demonstrate the manufacturer’s track record of delivering quality products and services.
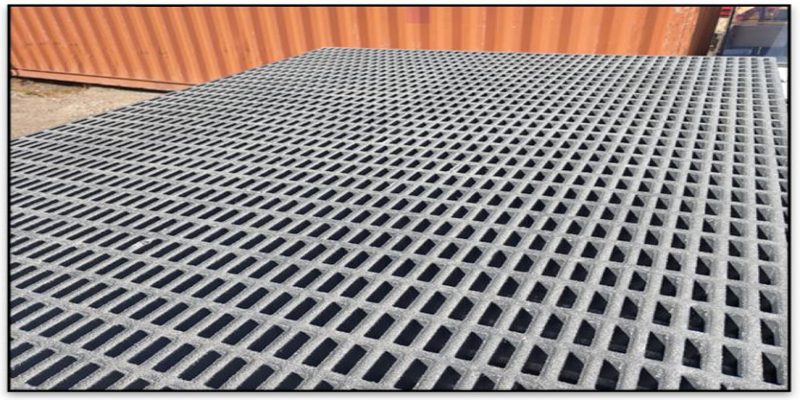
How to Connect with Manufacturers for Customized Solutions
- Define Your Requirements: Clearly convey the specific requirements and standards you need the FRP grating to meet, including dimensions, load capacities, and resistance properties.
- Open Communication Channels: Establish open lines of communication to ensure mutual understanding, timely updates, and feedback throughout the customization process.
- Engineering Collaboration: Work closely with the frp grating manufacturer’s engineering team to refine your design and ensure that the final product meets all technical specifications.
- Prototyping and Samples: Request prototypes or samples to test and verify the product’s suitability for your application before committing to a full order.
- Scalability of Production: Discuss the manufacturer’s scalability to ensure they can ramp up production to meet large orders if required.
- Lead Times and Delivery: Understand the manufacturer’s lead times and delivery schedules to ensure they align with your project timelines.
- NDA and IP Protection: If intellectual property is involved in your custom solution, secure non-disclosure agreements and discuss protection with the manufacturer to safeguard your designs.
By taking these measures, you will be better equipped to choose a trusted FRP grating manufacturer and receive high-quality, customized FRP grating solutions for your specific industrial needs.
Applications of FRP Grating of FRP Grating Manufacturer in Various Industries
Fiber-Reinforced Plastic (FRP) grating, due to its exceptional properties like corrosion resistance, high strength-to-weight ratio, and long lifespan, has found a vast array of applications across various industries. These industries benefit from FRP grating in terms of enhanced safety, reduced maintenance costs, and improved durability of installations. In this detailed exploration, we delve into the industrial and architectural uses of FRP grating, shine a light on its innovative applications through real-world case studies, and highlight popular FRP grating products from reputable FRP grating manufacturers, demonstrating the versatility and necessity of FRP in today’s industrial and architectural landscapes.
Overview of Industrial and Architectural Uses
FRP grating’s adaptability makes it a material of choice across a spectrum of applications. Here’s a closer look at where and how it is utilized:
- Chemical Processing Plants: Due to its corrosion resistance, FRP grating finds extensive use in harsh chemical environments, ensuring a longer lifespan of walkways and platforms.
- Maritime and Dock Facilities: The material’s durability against saltwater and its anti-slip properties are crucial for safety in marine applications.
- Water Treatment Facilities: Its robustness against temperature variations and corrosive substances makes it ideal for water treatment processes.
- Architectural Features: FRP grating is often used in aesthetic architectural designs due to its versatility in appearance and functionality.
- Oil and Gas Sector: The industry values FRP grating for its fire-retardant and corrosion-resistant characteristics, vital for offshore and onshore applications.
- Transportation Infrastructure: The lightweight yet strong nature of FRP grating supports its use in bridges, ramps, and platform constructions.
- Electrical and Telecommunications Areas: Non-conductive properties of FRP make it safe for use in environments where electrical safety is paramount.
Innovative Applications and Case Studies
Through real-world applications, the innovative potential of FRP grating is evident:
- Aerospace Facilities: Utilization of FRP grating in aerospace maintenance platforms showcases its strength and durability under high-tech conditions.
- Zoos and Aviaries: Its use in creating safe and durable habitats for wildlife in captivity highlights the environmental adaptability of FRP grating.
- Restoration of Historical Sites: FRP grating aids in the preservation of heritage, providing a durable alternative to traditional materials that blends with the original aesthetics.
- Recreational Parks: Adventure parks implementing FRP in obstacle courses demonstrate the material’s safety and versatility.
- Flood Defense Systems: Coastal defenses benefit from FRP’s resistance to corrosion and environmental elements, illustrating its significance in critical infrastructure protection.
- Solar Farms: The application of FRP grating for maintenance walkways in solar farms underlines its importance in sustainable energy sectors.
Featured FRP Grating Products
A selection of FRP grating products characterizes the wide-ranging applications and adaptability of this material:
- For Heavy-Duty Use: High-load capacity grating supports industries requiring robust infrastructure solutions.
- Safety First: Anti-slip grating products emphasize the commitment to worker safety in slippery or wet conditions.
- Fire Safety: Fire-retardant FRP grating products meet the rigorous fire codes of the oil and gas industry and other high-risk environments.
- Aesthetic Applications: Architectural grating blends strength with design flexibility, proving attractive for visual installations.
- Customization: Tailor-made solutions from FRP grating manufacturers cater to specific project requirements, ensuring both functionality and aesthetic appeal align with client needs.
By partnering with a trusted FRP grating manufacturer, industries can leverage the material’s benefits to suit various applications, from enhancing safety and durability to achieving specific architectural designs.
Fiberglass Columns Price: What to Expect
Types of FRP Grating Produced by FRP Grating Manufacturers
FRP (Fiberglass Reinforced Plastic) grating is a versatile and durable material used in a wide range of industrial applications. FRP grating manufacturers produce different types of grating to meet the specific needs of industries ranging from chemical plants to construction sites. Each type of grating is designed for unique environmental and operational requirements, with variations in strength, corrosion resistance, safety features, and installation processes. Below is an in-depth look at the three most commonly produced types of FRP grating: Molded FRP Grating, Pultruded FRP Grating, and Safety Grating.
Molded FRP Grating
Molded FRP grating is one of the most widely used types of FRP grating due to its unique manufacturing process and adaptability to various environments. It is created through a continuous molding process that involves embedding fiberglass strands within a resin matrix. This process produces a highly corrosion-resistant material that is both lightweight and extremely durable, making it suitable for applications in harsh environments, such as wastewater treatment facilities, chemical processing plants, and food processing areas.
One of the key advantages of molded FRP grating is its slip-resistant surface. The grating is often designed with a textured top that increases friction, preventing accidents in wet or slippery conditions. Molded grating is highly customizable, with manufacturers offering a wide range of panel sizes, colors, and thicknesses to meet specific aesthetic or functional requirements. The versatility of this product allows it to be used for walkways, platforms, mezzanines, and even stair treads. Molded FRP grating is also non-conductive, making it a safe choice for electrical or telecommunication installations.
The corrosion resistance of molded FRP grating is especially important in environments where exposure to chemicals, moisture, or UV rays is common. This type of grating is often specified for use in marine applications, chemical plants, and agricultural settings where traditional materials like metal grating would quickly degrade.
Pultruded FRP Grating
Pultruded FRP grating is produced using a unique process called pultrusion, where fiberglass strands are pulled through a resin bath and then into a heated die to cure. This method produces grating with a high strength-to-weight ratio, making it ideal for applications where heavy loads or high stress are anticipated. Pultruded FRP grating is known for its greater load-bearing capacity compared to molded FRP grating, making it the preferred choice for applications in manufacturing, construction, infrastructure projects, and other heavy-duty industries.
The pultrusion process allows manufacturers to control the fiber orientation, producing grating with optimal strength in both directions (bidirectional strength). As a result, pultruded FRP grating offers superior structural integrity and resistance to bending, flexing, or warping, even in extreme conditions. It is commonly used for industrial walkways, platforms, trench covers, and bridge decks, where the grating needs to support significant weight and withstand heavy traffic.
In addition to its high strength, pultruded FRP grating also offers excellent corrosion resistance, making it suitable for use in environments where exposure to chemicals, saltwater, or other corrosive elements is a concern. Its dimensional stability ensures that it retains its shape and strength over time, even under continuous exposure to challenging conditions.
Safety Grating
Safety grating is a specialized type of FRP grating designed to enhance safety in environments where slipping, falling, or accidents are a major concern. It features a textured or embossed surface that provides increased grip, reducing the risk of slips, especially in areas prone to spills, wet conditions, or ice. This type of grating is commonly used in chemical plants, offshore oil rigs, mining operations, and marine applications where workers are exposed to hazardous conditions.
What sets safety grating apart is its high visibility. Manufacturers often produce safety grating in bright colors like yellow or orange to increase its visibility, particularly in low-light or high-risk environments. The textured surface not only provides anti-slip properties but also enhances visibility, which is crucial in safety-critical areas.
Safety grating is designed to be easy to install and highly durable, ensuring that it can withstand frequent cleaning and exposure to chemicals or harsh weather conditions. Many safety grating systems also incorporate features like drainage holes or openings to allow for easy water flow, preventing the buildup of puddles or debris that could lead to safety hazards.
Safety grating is also designed with lightweight properties, making it easier to handle and install compared to traditional metal grating, reducing labor costs and minimizing downtime during installation or maintenance.
FRP grating manufacturers offer a range of products tailored to meet the needs of various industries, from heavy-duty applications to safety-focused environments. Whether you require the corrosion resistance and flexibility of molded FRP grating, the strength and load-bearing capacity of pultruded FRP grating, or the enhanced safety features of safety grating, these products provide reliable solutions for industries such as construction, chemical processing, marine, and infrastructure. The diverse properties of each type of FRP grating ensure that manufacturers can offer customized solutions for different operational and environmental challenges, providing both durability and safety in demanding conditions.
Advantages of High-Quality FRP Grating Produced by FRP Grating Manufacturers
High-quality FRP (Fiberglass Reinforced Plastic) grating, produced by reliable FRP grating manufacturers, offers an array of distinct advantages that make it a superior choice for a variety of industrial and commercial applications. With its unique properties, FRP grating provides numerous benefits that enhance safety, durability, and cost-efficiency. Below is a detailed look at the key advantages of high-quality FRP grating:
Exceptional Corrosion Resistance
One of the most significant advantages of high-quality FRP grating is its outstanding corrosion resistance. Unlike traditional materials such as steel or aluminum, FRP grating is resistant to a wide range of chemicals, acids, salts, and alkalis, making it ideal for use in environments where exposure to these substances is frequent. Industries such as chemical processing, water treatment, and oil and gas benefit from FRP grating’s ability to withstand harsh chemicals and extreme environmental conditions.
This corrosion resistance helps to reduce maintenance costs over time, as the material does not rust or degrade as quickly as metal alternatives. In turn, this extends the longevity of the grating, reducing the need for frequent replacements and repairs, which is particularly beneficial in high-maintenance industrial settings.
Lightweight and Easy to Handle
High-quality FRP grating is notably lightweight compared to traditional grating materials like metal. This lightweight property makes it significantly easier to transport and install without the need for heavy machinery or additional labor. Installation becomes more efficient, reducing overall project timelines and costs.
Because FRP grating is lighter, it also requires less structural support than metal grating. This savings on support structures translates into reduced construction and installation costs, making it an economical choice for projects where budget is a key consideration.
The ease of installation not only reduces installation time but also minimizes downtime in industrial settings. This makes high-quality FRP grating an ideal solution for environments that require quick and hassle-free installation, such as in maintenance-heavy industrial sites.
Superior Safety Features
Safety is one of the top priorities in industrial settings, and high-quality FRP grating excels in this area. The slip-resistant surface of FRP grating significantly enhances safety in wet or slippery conditions. This makes it an excellent choice for areas like walkways, catwalks, stair treads, and platforms, where the risk of slipping is high.
The non-slip surface is achieved through various designs, such as textured top surfaces or embedded anti-slip grit, ensuring that workers are safer in potentially hazardous environments like chemical plants, offshore rigs, and food processing facilities.
In addition to its slip-resistant properties, FRP grating is non-conductive, which reduces the risk of electrical hazards in applications where electrical equipment is present. This feature makes it suitable for use in electrical substations, telecommunication towers, and high-voltage environments, offering an extra layer of safety for both workers and equipment.
Eco-Friendly and Sustainable
High-quality FRP grating is also recognized for its eco-friendly benefits. The long lifespan of FRP grating means that it does not need to be replaced as often as other materials, reducing its overall environmental footprint. Additionally, FRP grating is recyclable, which makes it a more sustainable option for those looking to reduce the impact on the environment.
Many FRP grating manufacturers implement sustainable manufacturing practices, adhering to environmental standards during production. This can include the use of eco-friendly resins, efficient manufacturing techniques, and minimizing waste during the grating production process. For businesses that prioritize sustainability, choosing high-quality FRP grating helps align their operations with environmental goals while maintaining performance and durability.
Customization and Versatility
FRP grating is highly customizable, allowing manufacturers to produce grating that meets the specific needs of any project. High-quality FRP grating can be tailored in terms of color, size, mesh configuration, and thickness to meet both aesthetic and functional requirements. This flexibility ensures that FRP grating can be used in a wide variety of industries, from architectural applications to industrial infrastructure.
The versatility of FRP grating also extends to its ability to be produced in different resin types, including vinyl ester, polyester, and phenolic resins, each offering varying levels of resistance to different environmental factors like temperature, chemical exposure, and UV degradation. This variety makes FRP grating suitable for high-performance applications in extreme conditions, such as in marine environments or high-temperature industrial settings.
Cost-Effective
While the initial cost of high-quality FRP grating may be slightly higher than traditional materials like steel, the long-term cost savings more than justify the investment. FRP grating’s low maintenance and long lifespan significantly reduce repair and replacement costs, while its ease of installation cuts down on labor costs. Moreover, its lightweight nature and easy handling further reduce associated costs in transportation and setup.
For industries looking for a cost-effective yet durable solution, FRP grating provides an optimal balance between upfront costs and long-term benefits.
High-quality FRP grating produced by reputable FRP grating manufacturers offers a combination of durability, safety, eco-friendliness, and cost-effectiveness. Its corrosion resistance, lightweight properties, and safety features make it a superior choice for a range of industrial, commercial, and infrastructure applications. Additionally, its versatility and customization options make it adaptable to nearly any environment. By choosing FRP grating, businesses can reduce maintenance costs, improve safety, and contribute to more sustainable operations, all while benefiting from a long-lasting and high-performance material.
Factors Influencing the Pricing of FRP Grating by FRP Grating Manufacturers
The price of FRP (Fiberglass Reinforced Plastic) grating produced by FRP grating manufacturers is influenced by several critical factors. These factors vary depending on the specific requirements of the project, the type of grating, and the manufacturing process. Understanding these influencing factors can help buyers make informed decisions when purchasing FRP grating, balancing cost with performance and quality.
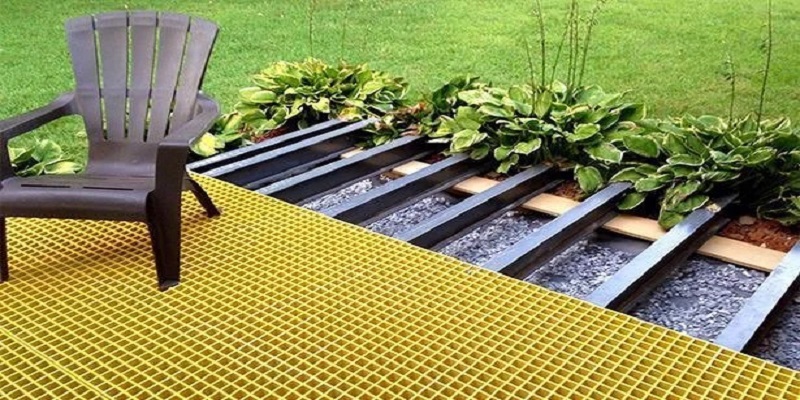
Below are the primary factors that impact the pricing of FRP grating:
Type of FRP Grating
Different types of FRP grating, such as molded FRP, pultruded FRP, and safety grating, have varying production methods and material costs, which directly affect their prices:
- Molded FRP Grating: Generally, molded grating is more cost-effective due to its simpler manufacturing process. However, the customization options, such as color, size, and thickness, can influence the price.
- Pultruded FRP Grating: Pultruded grating is typically more expensive than molded grating because the pultrusion process involves more complex machinery and higher material costs, producing stronger and more load-bearing grating.
- Safety Grating: Safety grating, with its textured surface for added slip resistance, may cost more due to the additional manufacturing steps and the materials used to enhance its grip and visibility.
Material and Resin Type
The choice of fiberglass and resin used in the production of FRP grating significantly affects pricing. Different resins offer varying degrees of performance, with premium resins like vinyl ester or phenolic resins offering superior resistance to harsh chemicals, heat, and UV degradation but at a higher cost. The most common resins include:
- Polyester Resin: This is the most affordable option and is widely used for general-purpose applications in industries where chemical resistance is not a primary concern.
- Vinyl Ester Resin: Offering enhanced chemical resistance and higher strength, vinyl ester resin is used in more demanding environments. It raises the cost of the grating due to its superior properties.
- Phenolic Resin: This resin offers the best fire resistance and is used in highly hazardous areas. It is the most expensive resin option, adding to the overall cost of the FRP grating.
Grating Size and Customization
The size, thickness, and mesh configuration of the FRP grating play a significant role in determining its price. Larger grating panels and custom configurations such as specific mesh patterns, hole sizes, or non-standard thicknesses require additional manufacturing steps and materials, which increase costs.
Customization options such as color, surface finish, or grip patterns can also affect pricing. For instance, high-visibility colors like bright yellow or orange for safety grating often come with a higher price tag due to the cost of dyes and the additional manufacturing complexity.
Load-Bearing Capacity
The load-bearing capacity of FRP grating is another factor that affects pricing. Higher strength and load capacity typically require more fiberglass reinforcement or specialized pultrusion techniques. As the load-bearing capacity increases, so does the material strength, which leads to higher production costs. Pultruded FRP grating, which is designed to support heavier loads, will generally be priced higher than molded grating, which is used for lighter-duty applications.
For applications like heavy-duty industrial platforms, walkways, or bridges, FRP grating with higher load-bearing capacity will be necessary, and the price will reflect this additional strength.
Production Volume and Order Size
The quantity of FRP grating ordered can significantly impact the unit price. Larger orders often benefit from bulk discounts, which can reduce the overall cost per panel. Manufacturers typically offer lower prices per unit for larger quantities because of economies of scale in production, material sourcing, and shipping costs.
Small, custom orders, on the other hand, may face higher per-unit costs due to the specialized nature of the order and the lack of bulk production. Customization and short production runs generally result in higher prices.
Manufacturing Process and Complexity
The manufacturing method also impacts pricing. Pultrusion, for example, is a more advanced and controlled process that requires specialized equipment, resulting in higher production costs compared to simpler molding processes. The complexity of the manufacturing process affects both the labor costs and the machinery used in production, which in turn influences the price of the grating.
Additionally, if the grating requires specific features such as anti-slip coatings, fire retardant properties, or other enhancements, these add to the production cost, further driving up the price.
Shipping and Handling Costs
The shipping and handling costs of FRP grating are influenced by the weight, size, and location of the order. Since FRP grating is generally lightweight but often bulky, the shipping cost can be affected by the dimensions of the grating panels and the distance between the manufacturer and the buyer. For large orders, shipping charges can be a significant part of the total cost.
Shipping costs are typically lower for manufacturers located closer to the end customer, and bulk shipments can reduce per-unit shipping costs.
Market Demand and Availability
The market demand for FRP grating and the availability of materials can also influence pricing. In times of high demand, such as during a construction boom or when supply chains are disrupted, prices may increase. Similarly, if raw materials such as fiberglass or specific resins become scarce, this can drive up production costs, which in turn affects the price of the final product.
Manufacturers may also adjust prices based on their production capacity and the demand for specific types of grating, such as safety grating, which may experience higher demand in specific industries.
The pricing of FRP grating produced by FRP grating manufacturers is influenced by a variety of factors, ranging from the type of grating and materials used to customization options, load-bearing capacity, and production volume. Understanding these factors helps buyers evaluate cost-effective solutions based on their specific needs while ensuring high performance and durability for their applications. When purchasing FRP grating, it is important to weigh both the short-term costs and the long-term benefits, such as reduced maintenance and extended longevity, that high-quality FRP grating offers.
Regulations and Standards FRP Grating Manufacturers Follow to Produce FRP Grating
FRP (Fiberglass Reinforced Plastic) grating manufacturers must adhere to a range of industry regulations and standards to ensure that the grating they produce meets safety, durability, and quality requirements. These standards are crucial for manufacturers to guarantee that their products perform reliably in demanding industrial environments, such as chemical plants, offshore platforms, and construction sites. Below are some of the key regulations and standards that FRP grating manufacturers should follow to produce high-quality FRP grating:
ASTM Standards (American Society for Testing and Materials)
The ASTM International standards are widely recognized in the FRP grating industry. These standards set the foundation for the manufacturing, testing, and performance criteria of FRP products. Some of the key ASTM standards that FRP grating manufacturers must follow include:
- ASTM D638 – Standard Test Method for Tensile Properties of Plastics
This standard defines how manufacturers should test the tensile strength of FRP grating, ensuring that the material can withstand the mechanical stresses typical in industrial applications. - ASTM D790 – Standard Test Methods for Flexural Properties of Unreinforced and Reinforced Plastics and Electrical Insulating Materials
This test measures the bending properties of FRP, ensuring that the grating can handle both static and dynamic loads without cracking or failure. - ASTM D256 – Standard Test Methods for Impact Resistance of Plastics and Electrical Insulating Materials
This standard measures the ability of FRP grating to absorb energy without breaking, ensuring that the grating is tough enough to handle impact from falling objects or heavy traffic. - ASTM F3059 – Standard Specification for Pultruded Fiber Reinforced Polymer (FRP) Structural Shapes
This standard specifically covers pultruded FRP products, ensuring that manufacturers meet the required mechanical and chemical resistance properties for grating systems.
By complying with ASTM standards, FRP grating manufacturers can provide products that are reliable, durable, and consistent with industry expectations.
ISO Standards (International Organization for Standardization)
The ISO standards are essential for manufacturers aiming to meet international quality and safety benchmarks. Some of the most relevant ISO standards for FRP grating production include:
- ISO 9001:2015 – Quality Management Systems
This certification ensures that FRP grating manufacturers maintain a high standard of quality management in their production processes. Compliance with ISO 9001 guarantees that manufacturers consistently meet customer and regulatory requirements and continually improve their processes. - ISO 14001:2015 – Environmental Management Systems
This standard focuses on environmental sustainability in the manufacturing process. FRP grating manufacturers must comply with ISO 14001 to reduce waste, manage energy consumption, and ensure that the production process minimizes environmental impact. - ISO 14644 – Cleanrooms and Associated Controlled Environments
Some FRP grating applications require highly clean environments (e.g., pharmaceutical or food processing plants). Manufacturers must adhere to this standard to ensure that their products meet the cleanliness and contamination control standards required by these industries.
NFPA Standards (National Fire Protection Association)
FRP grating manufacturers producing safety or fire-resistant grating must comply with NFPA standards, which are essential for ensuring that the materials meet fire safety requirements. Relevant standards include:
- NFPA 101 – Life Safety Code
This standard ensures that FRP grating products used in public spaces, industrial sites, and emergency evacuation routes provide safe, slip-resistant surfaces and comply with the necessary fire safety regulations. - NFPA 70 – National Electrical Code (NEC)
This standard is important for manufacturers who produce FRP grating for environments involving electrical systems. FRP grating must be non-conductive to reduce the risk of electrical hazards. Compliance with this code ensures that FRP grating is safe for use in electrical installations, such as substations and power plants. - NFPA 130 – Standard for Fixed Guideway Transit and Passenger Rail Systems
This standard applies to FRP grating used in transit systems. It defines the fire-resistance performance of materials in situations where passengers’ safety is at risk. FRP grating used in rail systems must meet specific flame spread and smoke development criteria.
OSHA Standards (Occupational Safety and Health Administration)
FRP grating manufacturers must also comply with regulations set by OSHA to ensure that their products meet workplace safety standards. Some relevant regulations include:
- OSHA 1910.22 – Walking-Working Surfaces
OSHA regulations require that walking surfaces, such as walkways and platforms, be safe and slip-resistant. FRP grating must meet these criteria to prevent slip-and-fall accidents, particularly in environments that involve water, chemicals, or other hazards. - OSHA 1926.1053 – Ladders
If FRP grating is used as part of a ladder system, it must meet OSHA’s safety regulations for durability, strength, and stability to prevent workplace accidents.
FRP grating manufacturers must ensure that their products adhere to these standards to minimize risks and ensure worker safety in industrial environments.
BS EN Standards (British Standards and European Norms)
For manufacturers supplying FRP grating to the European market, compliance with BS EN standards is essential. Some relevant standards include:
- BS EN 13706:2002 – Glass-reinforced plastics (GRP) – Pultruded profiles
This standard specifies the performance and testing criteria for pultruded GRP profiles, which apply to pultruded FRP grating. - BS EN 1493:2010 – Lifting platforms for vehicles
FRP grating used in automotive or transport facilities must meet the appropriate load-bearing and safety requirements under BS EN standards. - BS EN 1991-1-4 – Eurocode 1: Actions on Structures
This standard defines the wind load calculations for structures, including grating systems in exposed areas. Manufacturers of FRP grating used in construction must comply with these load specifications.
Fire Resistance and Smoke Development Standards
For certain applications, particularly in environments where fire safety is a critical concern, FRP grating manufacturers must comply with specific fire resistance standards. These standards ensure that FRP grating does not contribute to the spread of fire and minimizes smoke development.
- ASTM E84 – Standard Test Method for Surface Burning Characteristics of Building Materials
This test measures the flame spread and smoke development of materials, ensuring that FRP grating used in construction or public facilities meets fire safety requirements. - UL 723 – Standard for Test for Surface Burning Characteristics of Building Materials
UL 723 evaluates the fire resistance of materials used in buildings. FRP grating that passes this test is considered safe for use in fire-sensitive environments.
FRP grating manufacturers must adhere to a range of national and international standards to ensure that their products meet safety, quality, and performance requirements. Key standards such as ASTM, ISO, NFPA, and OSHA help manufacturers produce high-quality, durable, and safe FRP grating suitable for use across various industries, from chemical plants to construction sites. By following these regulations, manufacturers not only ensure compliance with legal requirements but also enhance the reliability, sustainability, and performance of their FRP grating products.
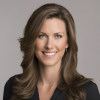
As the editor of GangLong Fiberglass, I have years of experience and in-depth research, focusing on cable tray products, fiberglass solutions, and grille systems. I incorporate years of industry insights and practical experience into every content, committed to promoting the progress of the industry. At GangLong Fiberglass, my commitment is reflected in every product, from innovative cable trays to durable fiberglass solutions and sturdy grille systems. As an authoritative voice in the industry, my goal is to provide valuable information to professionals and businesses and promote forward-looking solutions.