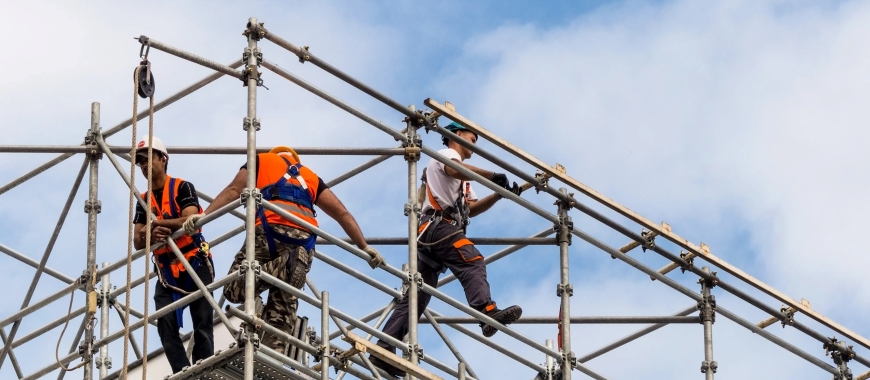
The construction and maintenance landscapes have long relied on the framework of scaffolding to provide secure and accessible platforms for workers at various heights. As an essential component of these temporary structures, scaffolding tubes bear the weight of progress, literally. However, the focus has shifted towards fiberglass scaffolding tubes as the industry seeks solutions that promise more than just functionality. Remarkable for their unique properties, fiberglass tubes stand apart from conventional steel or aluminum counterparts. These innovative tubes offer unmatched benefits like reduced weight, increased strength, and enhanced safety features, which are particularly advantageous in electrostatic-sensitive environments. By integrating these cutting-edge materials, construction projects can now achieve efficiency and safety that were previously unattainable, making fiberglass scaffolding tubes a focal point for modern architectural endeavors. The fiberglass scaffolding tube, 48.5mm OD and 6.65mm thick, is durable, lightweight, and ideal for contractors and chemical-prone sites.
What is Fiberglass Scaffolding Tube?
Fiberglass scaffolding tubes are cylindrical support structures utilized widely in the construction and maintenance sectors. Made primarily from fiberglass, a material consisting of extremely fine fibers of glass, these tubes are noted for their robustness and adaptability. Alongside these tubes, fiberglass rods are also gaining prominence for their versatility and ability to provide additional reinforcement in complex structural setups.
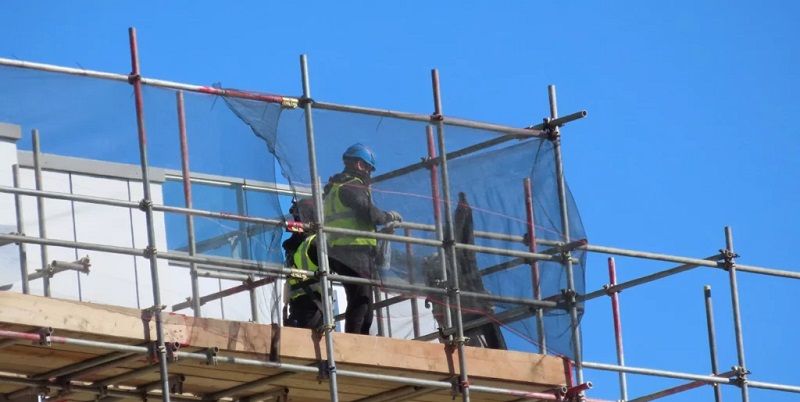
Process of Fiberglass Scaffolding Tube
- Fiber Production: The making of fiberglass begins with mixing silica sand, limestone, and other raw materials, melted at high temperatures to form molten glass which is then spun into fibers.
- Resin Application: These glass fibers are coated with a polymer resin, enhancing their strength and flexibility. In particular, hollow glass fiber is often utilized in this process due to its lightweight nature and excellent insulating properties. By combining the benefits of resin coating with the unique characteristics of Hollow Glass Fiber, the resulting material achieves superior performance, making it ideal for demanding structural and industrial applications.
- Pultrusion Process: The fibers, once coated, are pulled through a heated die, which shapes them into solid rods or tubes.
- Curing: After shaping, the material is cured at elevated temperatures to set the resin, providing structural integrity.
- Polishing and Cutting: The tubes are then polished to smoothen their surface and cut into standardized lengths suitable for scaffolding.
- Quality Checks: Each tube undergoes rigorous testing to ensure they meet safety and quality standards.
- Assembly: Sections of the tube are assembled into scaffolding frameworks suited for various job sites.
- Finishing: A final layer of protective coating may be applied to protect against environmental influences.
Key Features of Fiberglass Scaffolding Tubes
Fiberglass scaffolding tubes hold several advantageous features over traditional materials like steel or aluminum:
Lightweight: Fiberglass weighs significantly less than steel, reducing the overall weight of the scaffold and easing transport and installation processes.
High Strength: Despite their lighter weight, fiberglass tubes exhibit superior strength, capable of supporting considerable loads. This characteristic, often referred to as fiberglass tube strength, highlights the material’s ability to withstand significant stress without compromising its structural integrity. By leveraging fiberglass tube strength, industries benefit from a reliable and efficient solution for various heavy-duty applications, ensuring both safety and durability.
Non-Conductive: Safe for use in electrical environments as they do not conduct electricity.
Corrosion Resistance: Unlike metal scaffolds, fiberglass is resistant to corrosion, extending its lifespan even in harsh weather conditions.
Minimal Maintenance: Requires less maintenance than metal due to its resistance to rust and corrosion.
Thermal Insulation: Offers excellent thermal insulation properties, which can be crucial in specific working conditions.
Flexibility: More flexible than traditional materials, fiberglass can withstand bending and stress without permanent deformation.
UV Resistance: Typically coated with a UV-resistant material, making it suitable for outdoor use without degradation from sun exposure.
Cost-Effective Over Time: While initial costs might be higher, durability and lower maintenance lead to savings over time.
The unique blend of characteristics found in a fiberglass scaffolding tube makes it an invaluable tool in modern construction, promoting not just safety and efficiency but also a forward-thinking approach to building and maintenance work.
Custom Large Diameter Fiberglass Tube: Strong and Reliable
Benefits of Using Fiberglass Scaffolding Tube
The adoption of fiberglass scaffolding tubes in construction and maintenance projects brings a plethora of advantages. These tubes, apart from their basic functionality as a part of the scaffolding framework, offer unique benefits that enhance both safety and efficiency on site. Below are detailed insights into the key advantages:
- Non-Conductivity for Enhanced Safety: Fiberglass scaffolding tubes are non-conductive, making them extremely safe for electrical work environments where metal scaffolds could pose a significant risk of electrocution. This feature alone can significantly reduce workplace accidents related to electricity.
- Durability in Harsh Environments: Thanks to their corrosion-resistant nature, these tubes are ideal for use in environments that would typically degrade metal scaffolds, such as coastal areas with salty air or industrial sites with chemical exposure.
- Lightweight for Easier Handling and Transportation: Their lighter weight, compared to steel or aluminum, simplifies the process of setting up and moving scaffolding structures. This not only speeds up project timelines but also reduces labor costs and fatigue among workers, improving overall project efficiency.
- Longevity and Lower Lifetime Cost: The durability afforded by the fiberglass material translates into a longer lifespan for scaffolding, making it a cost-effective option in the long term despite possible higher upfront costs.
- Resistance to Weathering and Environmental Damage: Unlike metal scaffolds that can corrode over time, fiberglass scaffolding tubes are highly resistant to rain, snow, UV radiation, and temperature fluctuations, ensuring consistent performance regardless of weather conditions.
- Minimal Maintenance Requirements: The need for regular maintenance is significantly reduced with fiberglass scaffolding, as the tubes do not rust, corrode, or suffer from many of the issues that plague metal scaffolds.
- Improved Worker Comfort: The thermal insulation properties of fiberglass ensure that the tubes remain relatively cool to the touch under the sun and warmer in cold conditions, offering more comfortable handling and reducing the risk of temperature-related discomfort. This benefit is particularly evident in products like the refractory fiberglass insulation tube, which is specifically designed to provide excellent thermal resistance. By incorporating refractory fiberglass insulation tube technology, work environments not only enhance safety but also ensure that workers can handle materials more comfortably across varying weather conditions.
- Flexibility and Versatility: The inherent flexibility of fiberglass allows for scaffolding designs that might not be feasible with more rigid materials, offering creative solutions for complex construction challenges.
- Eco-Friendly Option: Fiberglass is a more environmentally friendly material compared to traditional scaffolding options. It requires less energy to manufacture and is recyclable, contributing to a smaller environmental footprint.
- Improved Project Image: Using modern materials like fiberglass for scaffolding can enhance the professional image of a construction project, showcasing a commitment to safety, innovation, and sustainability.
The utilization of a fiberglass scaffolding tube offers a broad spectrum of benefits that enhance the safety, efficiency, and sustainability of construction and maintenance projects. From the significant safety improvements provided by its non-conductive nature to the practical advantages of its lightweight and durable design, fiberglass scaffolding tubes represent a forward-thinking choice for modern construction needs.
Fiberglass Scaffolding Tube Sizes and Specifications
When it comes to setting the groundwork for any construction or maintenance project, knowing the specifics about the equipment you’re using is crucial. The versatility and efficacy of a fiberglass scaffolding tube lie not only in its material advantages but also in the variety of sizes and specifications it comes in. Here’s a comprehensive look at the common sizes available in the market and how these different dimensions cater to various project needs.
Common Sizes Available
- Diameter: Typically, fiberglass scaffolding tubes come in diameters ranging from 1.5 inches (38mm) to 2 inches (50mm). This variation allows for flexibility in scaffold design.
- Length: The length of these tubes can vary significantly, with common sizes being 5 feet (1.52 meters), 10 feet (3.04 meters), and 20 feet (6.10 meters). Custom lengths are also available to suit specific project requirements.
- Wall Thickness: Wall thickness usually ranges from 0.125 inches (3.2mm) to 0.2 inches (5mm), which plays a crucial role in determining the load-bearing capacity of the scaffold.
- Weight: Given their lightweight nature, even the larger tubes are relatively easy to handle, with weight typically proportional to the thickness and length of the tube.
- Load Capacity: Load capacities vary, often rated by the manufacturer, and are critically dependent on the length, diameter, and wall thickness of the tube.
- Custom Sizes: Beyond standard sizes, custom dimensions can be crafted to meet the unique needs of specific projects, providing a tailored scaffolding solution.
Customizable Large Fiberglass Tubes for Versatile Project Needs
Suitability for Various Types of Construction or Maintenance Work
- Light-Duty Tasks: Shorter and thinner fiberglass scaffolding tubes are typically employed for light-duty tasks where extensive height or heavy loads are not involved, such as minor repairs or indoor painting.
- Heavy-Duty Construction: Longer tubes with greater diameters and wall thickness are requisite for heavy-duty construction projects, providing the needed strength to support workers and materials at significant heights.
- Electrical Work: For projects involving electrical components, any size of the non-conductive fiberglass tube offers an essential safety advantage, minimizing the risk of electrical hazards. However, when working with such materials, it is important to consider precautions with fiberglass tube, such as ensuring proper handling to avoid damage or wear, which could compromise its insulating properties. By adhering to these precautions, you can maximize both safety and the longevity of the tube in various applications.
- Outdoor Projects: Longer and thicker tubes are preferred for outdoor projects to withstand environmental variables such as wind. Their corrosion resistance also makes them suitable for harsh weather conditions.
- Complex Architectural Designs: Custom-sized fiberglass scaffolding tubes can be adapted to complex designs, providing solutions for buildings with unconventional architecture where standard sizes may not suffice.
- Temporary Structures: Smaller, lighter tubes are often ideal for erecting temporary structures or stages, where ease of assembly and disassembly is a priority, without compromising safety.
- Industrial Maintenance: For industrial settings, especially where chemical exposure might occur, fiberglass tubes of varying sizes provide the necessary durability and resistance to corrosive substances, ensuring prolonged use.
The selection of a fiberglass scaffolding tube in appropriate sizes and specifications is fundamental to addressing the unique challenges of each construction or maintenance project. The wide range of dimensions available caters to various demands, from load capacity to project complexity, making fiberglass scaffolding an adaptable and reliable choice for modern construction practices.
Locating Fiberglass Scaffolding Tube
Scaffolding is a critical component in both construction and maintenance work. When it comes to using fiberglass scaffolding tubes, it is imperative to source these materials from reputable suppliers. Locating high-quality scaffolding components not only ensures safety but also affects the efficiency and reliability of the project at hand. Below we explore the importance of choosing reputable suppliers when locating fiberglass scaffolding tubes, underlining the factors that highlight their significance in the industry.
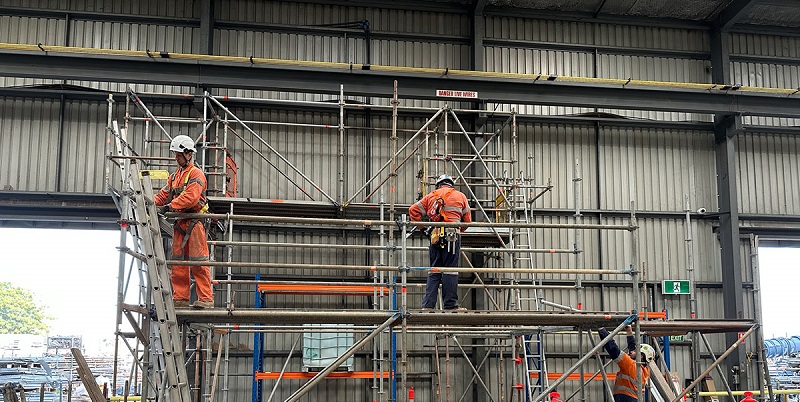
Importance of Choosing Reputable Suppliers:
- Safety: Reputable suppliers adhere to strict safety standards to prevent job-site accidents, ensuring that the fiberglass scaffolding tubes meet or exceed industry regulations.
- Quality Assurance: Reliable vendors guarantee high-quality products that are less likely to defect, ensuring the integrity of the scaffolding structures you build.
- Durability: Suppliers with a reputation for quality offer products that are designed to last and withstand the rigors of heavy use, reducing the frequency of replacements.
- Compliance with Standards: Professional suppliers ensure that their fiberglass scaffolding tubes comply with relevant standards such as OSHA or ANSI, which govern the construction industry.
- Product Testing and Certification: Certified suppliers often test their products rigorously and may hold third-party certifications that confirm their commitment to quality.
- Expertise and Advice: Knowledgeable suppliers can provide valuable advice on the most suitable types of fiberglass scaffolding tubes for specific projects, affecting overall work efficiency and safety.
- Availability of Products: A large and dependable supplier usually has a substantial inventory, resulting in better product availability and shorter lead times.
- Warranty and Support: Trustworthy suppliers often provide product warranties and after-sales support, offering peace of mind and assistance if any issues arise with the product.
- Customization Options: Reputable suppliers may offer custom solutions and are capable of catering to specific project needs that may not be met by standard sizes.
- Logistics and Delivery: Established suppliers are typically equipped with reliable logistics arrangements, ensuring the timely delivery of scaffolding tubes to the project site without undue delays.
In finding fiberglass scaffolding tubes, it is crucial to understand the implications of sourcing from trusted suppliers. These considerations can govern the project’s success and workers’ safety, emphasizing the need for careful selection of vendors in the construction industry. Beyond scaffolding, specialized products like the fiberglass vacuum tube also benefit from a meticulous sourcing process, as their performance and durability are vital in applications where precision and reliability are paramount. Remember, investing time and resources in locating the right supplier is not just about making an immediate purchase, but also about laying the groundwork for future projects that depend on high standards of safety and quality.
Pricing and Availability of Fiberglass Scaffolding Tube
Understanding the pricing and availability of fiberglass scaffolding tube is crucial for project planning and budgeting in construction and maintenance work. The price of fiberglass scaffold tube can vary widely based on a variety of factors, and availability can depend on multiple aspects, including customization options and stock levels. Below, we’ll delve into both these critical areas to help shed light on what to expect when sourcing these essential materials.
Fiberglass Scaffolding Tube Price Points and Factors Influencing the Cost
- Material Quality: Higher quality fiberglass materials will invariably cost more due to their enhanced durability and performance characteristics.
- Manufacturing Process: Advanced manufacturing processes that enhance the tube’s strength and durability can add to the production costs, reflecting in the price.
- Length and Diameter: The dimensions of the scaffolding tube play a significant role in pricing, with larger and thicker tubes requiring more material and thus costing more.
- Customization: Custom specifications for specific projects can lead to higher costs due to the additional labor and material adjustments needed.
- Quantity Ordered: Bulk orders often come with discounts, whereas purchasing smaller quantities might result in a higher price per unit.
- Market Demand and Supply Conditions: Global and local market conditions, including demand surges or material shortages, can significantly affect prices.
- Shipping and Handling Costs: The cost of logistics, including shipping and handling, especially for long-distance deliveries, can impact the overall cost of acquisition.
- Regulatory Compliance: Tubes meeting specific regulatory standards, such as those required for certain buildings or regions, may incur additional costs to ensure compliance.
Information on the Availability of Fiberglass Scaffolding Tubes
- Ready-Made Stocks: Many suppliers keep a standard range of fiberglass scaffolding tubes in stock, ensuring quick delivery for common sizes and specifications.
- Custom Orders: For projects requiring specific dimensions or performance features, custom orders can be placed, which might take additional time to fulfill due to the manufacturing process.
- Manufacturing Lead Times: The time from placing an order to delivery can vary, especially for custom or large-scale orders, depending on the supplier’s production capacity.
- Geographic Availability: The availability can also depend on your location, with urban centers typically having better access to suppliers and faster delivery times compared to remote areas.
- Seasonal Variability: During peak construction seasons, the demand for scaffolding tubes might increase, affecting availability and potentially leading to longer lead times.
- Supplier Stock Levels: Suppliers with larger inventories can offer better availability, but stock levels can fluctuate based on market demand and manufacturing schedules.
When planning for the purchase of fiberglass scaffold tube, both the pricing and availability must be taken into account to avoid project delays and to budget effectively. Understanding the factors that influence these aspects can help in making informed decisions and negotiations with suppliers, ensuring that your project proceeds smoothly within its financial and time constraints.
Fiberglass Scaffolding Tubes for Sale and Rental Options
When contemplating the best approach to acquiring fiberglass scaffolding tubes, the decision to buy or rent is pivotal. This choice hinges on various factors reflecting the project’s nature, duration, budget, and future needs. Understanding these considerations will ensure you opt for the most cost-effective and practical solution. Below we discuss key points to aid in this decision-making process.
How to Decide Whether to Buy or Rent Fiberglass Scaffolding Tubes
- Project Duration: For short-term projects, renting fiberglass scaffolding tubes may be more cost-effective, while purchasing may be better for long-term use.
- Frequency of Use: If your operations regularly require scaffolding, investing in purchasing makes financial sense over time compared to the recurring costs of rental.
- Storage Capabilities: Owning scaffolding requires adequate storage space to prevent damage. If space is limited, renting might be a more viable option.
- Budget Constraints: Initial investment for purchasing can be substantial. Rentals can alleviate upfront costs, especially for companies preferring operational expenses over capital expenditure.
- Maintenance and Upkeep: Owning means being responsible for maintenance, whereas rental companies typically handle it, reducing your workload and potential additional costs.
- Availability of Capital: If capital is readily available, buying may offer better long-term value. Companies with tighter cash flows may benefit from the flexibility of renting.
- Project Specificity and Customization: Projects needing customized solutions might necessitate purchasing, as rental options may not always meet specific requirements.
- Market Fluctuations: The rental market may offer more flexibility to adapt to industry changes without the sunk cost associated with owned equipment that may become obsolete.
Flexible Fiberglass Tube: Lightweight and Durable Options
Reputable Companies and Online Platforms for Fiberglass Scaffolding Tubes
- Cbro Fiberglass: Positioned at the forefront, Cbro Fiberglass offers a comprehensive array of fiberglass scaffolding tubes suitable for various applications. Their expertise ensures high-quality products whether for sale or rent, catering to the diverse needs of their clientele.
- Scaffolding Direct: Known for their extensive inventory, Scaffolding Direct provides both buying and renting options for fiberglass scaffolding tubes. Their competitive pricing and reliable customer service make them a go-to source.
- National Tool Hire Shops: Offering a wide range of scaffolding solutions, including fiberglass scaffolding tubes, this platform caters to both sales and rental needs. They are recognized for their flexible rental terms and nationwide availability, making it convenient for projects across different locations.
Choosing whether to buy or rent fiberglass scaffolding tube depends on carefully weighing these factors against your project’s specific demands and future expectations. Companies like Cbro Fiberglass, Scaffolding Direct, and National Tool Hire Shops serve as reliable sources, ensuring that high-quality scaffolding materials are accessible, whether for immediate use or for long-term scalability and efficiency in operations.
How to Choose a Fiberglass Scaffolding Tube
Choosing the right fiberglass scaffolding tube is crucial for ensuring project safety, efficiency, and cost-effectiveness. Start by considering the tube’s dimensions—fiberglass tubes typically feature a 48.5mm outer diameter and 6.65mm wall thickness, making them compatible with standard scaffolding accessories.
- Project Requirements: Assess the specific needs of your project. For chemical-heavy environments or electrical work, fiberglass tubes are ideal due to their corrosion resistance and non-conductive properties.
- Weight and Transport: Fiberglass tubes are lighter than steel, reducing transport costs and labor fatigue. This makes them a practical choice for frequent site relocations.
- Durability and Strength: Look for tubes made from high-stiffness, thick-walled, pulled fiberglass-reinforced polyester, which ensures long-term performance and resistance to erosion.
- Safety: Safety should be a top priority. Fiberglass scaffolding provides a reliable, sturdy build, reducing risks for workers in hazardous conditions.
By evaluating these factors, you can select the most suitable fiberglass scaffolding tube to meet your project’s demands while enhancing safety and efficiency.
Can a Fiberglass Scaffolding Tube Be Used in Any Environment?
While the fiberglass scaffolding tube is highly valued for its corrosion resistance, this does not mean it is suitable for every environment without limitation. Fiberglass tubes are designed to resist damage caused by chemical exposure, moisture, and rust, making them ideal for industries like chemical processing, marine settings, and electrical work. Their non-conductive and anti-corrosive properties give them a clear advantage over metal scaffolding in such conditions.
However, extreme environments with constant exposure to UV radiation, high temperatures, or abrasive particles may degrade fiberglass over time, affecting its strength and longevity. Although fiberglass is durable, it may not match the heat tolerance or mechanical toughness of steel in specific high-load or high-heat applications.
While fiberglass scaffolding tubes excel in resisting corrosion, understanding the unique environmental demands of your project is essential to determine their suitability.
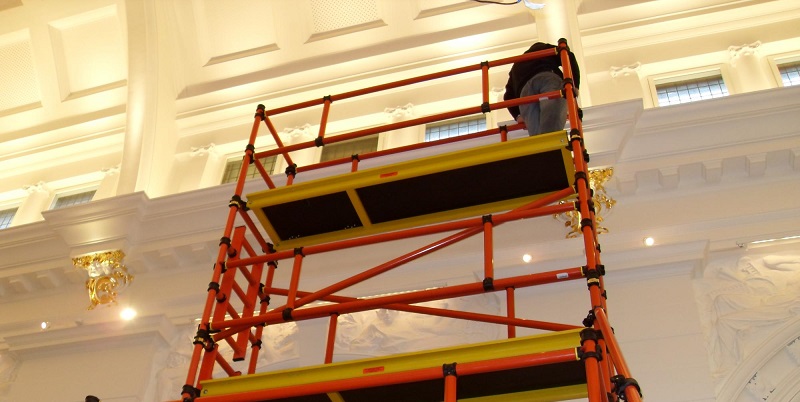
Can a Fiberglass Scaffolding Tube Be Used Around Electrical Hazards?
The fiberglass scaffolding tube is an excellent choice for environments with electrical hazards due to its non-conductive properties. Unlike metal scaffolding, fiberglass does not conduct electricity, making it significantly safer for workers operating near live wires, electrical installations, or power lines. This feature reduces the risk of electric shock, which is a critical safety consideration for electricians, maintenance workers, and contractors working in energized environments.
Additionally, fiberglass scaffolding maintains its structural integrity when exposed to electrical currents, ensuring stability and safety. However, it is essential to regularly inspect the tubes for cracks, chips, or damage, as these could compromise the non-conductive performance.
The fiberglass scaffolding tube is specifically designed to offer enhanced safety in electrically hazardous environments, making it a preferred option for projects requiring electrical insulation and worker protection.
How Does a Fiberglass Scaffolding Tube Protect People From Falls?
The fiberglass scaffolding tube plays a vital role in fall protection by providing a stable and durable framework for scaffolding systems. Its high stiffness and strength, achieved through thick-walled, pulled fiberglass-reinforced polyester construction, ensure the scaffolding can support significant weight and resist deformation under load. This stability is crucial in preventing platform wobbling or collapse, which are common causes of falls on construction sites.
Fiberglass scaffolding tubes are also compatible with standard safety components like guardrails, toe boards, and harness attachment points. When properly installed, these components create a safe working environment by minimizing fall risks.
Additionally, the lightweight nature of fiberglass scaffolding allows for precise assembly and secure connections, reducing errors that could compromise the scaffolding’s integrity. Unlike steel, fiberglass scaffolding does not corrode over time, ensuring a longer-lasting and reliable safety structure.
The fiberglass scaffolding tube protects workers from falls by offering a strong, stable, and durable platform, essential for maintaining safety in elevated work environments.
Key Factors to Consider When Inspecting and Maintaining Fiberglass Scaffolding Tube
Proper inspection and maintenance of fiberglass scaffolding tube are essential to ensure safety, durability, and performance over time. Unlike steel, fiberglass is resistant to corrosion, but it still requires regular checks to identify damage that may compromise its structural integrity. Here are the key factors to focus on:
- Surface Damage: Inspect the tubes for cracks, chips, dents, or scratches. While fiberglass is durable, impact damage can weaken the structure, especially if fibers are exposed or the protective coating is compromised.
- Chemical Exposure: If used in environments with chemicals, check for signs of erosion or discoloration. While fiberglass resists chemical damage, prolonged exposure to harsh substances may degrade its surface.
- UV Degradation: Long-term exposure to direct sunlight can weaken fiberglass material. Look for signs of fading, brittleness, or surface flaking, and consider protective coatings if UV exposure is frequent.
- Load-Bearing Capacity: Regularly assess whether the tubes are maintaining their designed load capacity. Any deformation, bending, or warping could signal a failure in structural integrity.
- Connections and Fittings: Ensure the tubes properly connect with scaffolding components, such as clamps and joints, and check for wear or misalignment that could create instability.
- Cleanliness: Keep the tubes clean and free from debris, dirt, or oil, which can make assembly difficult or hide damage. Use mild cleaning agents to prevent material degradation.
- Regular Inspections: Schedule routine inspections before and after each use to identify potential hazards early. Inspections should include visual checks and functional testing, especially for high-risk work environments.
By addressing these factors, the fiberglass scaffolding tube can be maintained in optimal condition, ensuring long-term safety, performance, and cost-effectiveness for any project.
Can a Fiberglass Scaffolding Tube Replace Aluminum or Steel Scaffolding Tubes?
The question of whether a fiberglass scaffolding tube can replace aluminum or steel scaffolding tubes depends on the specific requirements of the project. Fiberglass offers unique advantages, such as being non-conductive, corrosion-resistant, and lightweight, making it ideal for environments where electrical hazards, chemicals, or moisture are present. This makes fiberglass scaffolding tubes particularly suitable for electricians, chemical processing plants, and marine applications where steel or aluminum would corrode or pose electrical risks.
However, fiberglass scaffolding tubes are not universally superior to steel or aluminum. Steel tubes are preferred for projects demanding extremely high load-bearing capacity and durability under heavy loads, such as large-scale construction or industrial work. Aluminum tubes, on the other hand, are lightweight and strong, making them ideal for projects that require frequent setup and relocation, though they conduct electricity and are prone to corrosion over time.
While fiberglass tubes are lighter than steel and comparable to aluminum in weight, their load-bearing capacity is generally lower than steel, limiting their use for heavy-duty applications. Additionally, fiberglass tubes may degrade under prolonged UV exposure or in extremely high-temperature environments, where steel or aluminum would perform better.
A fiberglass scaffolding tube can replace aluminum or steel tubes in applications requiring safety, corrosion resistance, and non-conductivity, but steel or aluminum remains a better choice for heavy-duty, high-temperature, or large-scale projects. The choice ultimately depends on the environment, load requirements, and project priorities.
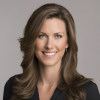
As the editor of GangLong Fiberglass, I have years of experience and in-depth research, focusing on cable tray products, fiberglass solutions, and grille systems. I incorporate years of industry insights and practical experience into every content, committed to promoting the progress of the industry. At GangLong Fiberglass, my commitment is reflected in every product, from innovative cable trays to durable fiberglass solutions and sturdy grille systems. As an authoritative voice in the industry, my goal is to provide valuable information to professionals and businesses and promote forward-looking solutions.