
High strength fiberglass sheets are advanced composite materials known for their exceptional durability and strength. Composed of fiberglass reinforced with high-performance resins, these sheets offer a lightweight alternative to traditional materials, making them ideal for various applications. In industries such as aerospace, automotive, and construction, high strength fiberglass sheets are increasingly favored for their ability to withstand harsh environments while maintaining structural integrity. Produced in fiberglass sheet factory, their resistance to moisture, chemicals, and UV radiation further enhances their longevity, ensuring reliable performance over time. As businesses seek innovative solutions to improve efficiency and reduce weight in their products, high strength fiberglass sheets emerge as a critical component in modern engineering and manufacturing processes. High strength fiberglass sheets are durable, flexible composites made from fiberglass and epoxy, ideal for impact-resistant, custom industrial applications.
What are High Strength Fiberglass Sheets?
High strength fiberglass sheets are advanced composite materials designed to deliver exceptional mechanical properties and durability. These sheets are specifically engineered to withstand high loads, stresses, and environmental factors. They are primarily made from fiberglass, a network of glass fibers that are woven together to form a strong, lightweight fabric, and are combined with high-performance resins like epoxy or polyester. The resin acts as a binding agent that holds the fiberglass together, enhancing its strength, impact resistance, and overall performance. High strength fiberglass sheets are favored in industries that demand superior materials, such as aerospace, automotive, and heavy-duty industrial applications.
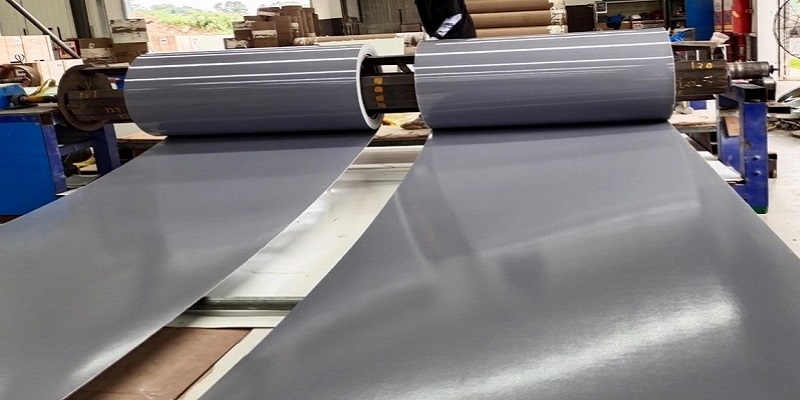
Composition and Manufacturing Process
The manufacturing process for high strength fiberglass sheets is a highly precise operation that combines raw materials, advanced technology, and expert craftsmanship to create a product with remarkable strength and durability. The process typically begins with the selection of fiberglass fabric or fiberglass mat, which is made from woven glass fibers. This fabric is then combined with a resin matrix—typically epoxy or polyester resin—which serves as the bonding agent.
Several techniques can be used to apply the resin to the fiberglass, including hand lay-up, vacuum bagging, and automated manufacturing processes. In the hand lay-up process, layers of fiberglass fabric are manually placed onto a mold, and resin is applied between each layer. Vacuum bagging is a more advanced technique, where the layers of fiberglass and resin are sealed in a vacuum, and the bag is evacuated to remove air and ensure optimal resin saturation. Automated processes, such as filament winding or RTM (Resin Transfer Molding), allow for more precise and consistent production.
After the fiberglass and resin layers are applied, the sheets are cured under heat and pressure. This curing process solidifies the resin, ensuring a strong bond between the fibers and resin, which results in a rigid, stable material with enhanced strength and performance. The curing also minimizes imperfections like voids and waves, leading to a smoother, more reliable final product. The end result is a high-strength fiberglass sheet that maintains excellent performance in a wide range of challenging environments.
Differences from Standard Fiberglass Sheets
High strength fiberglass sheets differ significantly from standard fiberglass sheets in several key areas:
- Strength: While standard fiberglass sheets offer reasonable strength for light-duty applications, they are not designed to withstand the high loads or stresses found in demanding environments. High strength fiberglass sheets, on the other hand, are engineered with higher tensile strength and flexural strength, making them ideal for applications where structural integrity is critical. These sheets are designed to resist bending, stretching, and deformation, even under heavy loads. High strength fiberglass sheets also tend to have better impact resistance and fatigue resistance, making them suitable for harsh environments and heavy-duty industrial applications.
- Applications: The enhanced properties of high strength fiberglass sheets enable their use in critical applications such as aerospace components, automotive parts, marine structures, and heavy-duty industrial settings. Fiberglass sheet uses extend beyond these high-performance applications, as standard fiberglass sheets are often used for less demanding tasks like insulation or lightweight coverings, where their durability and versatility make them an ideal choice.
- Performance: High strength fiberglass sheets are also engineered for superior thermal resistance and corrosion resistance, making them suitable for use in challenging environmental conditions, including exposure to chemicals, moisture, and extreme temperatures. The advanced resin formulations used in high-strength fiberglass sheets (especially epoxy resins) offer a level of protection against these factors that is far superior to that found in standard fiberglass products.
High strength fiberglass sheets are a specialized and advanced material that combines the inherent strength of fiberglass with the performance-enhancing properties of high-quality resins like epoxy or polyester. These sheets provide superior tensile strength, flexural strength, impact resistance, and thermal durability, making them an ideal choice for demanding applications in industries such as aerospace, automotive, marine, and heavy industry. The advanced manufacturing process, which involves resin infusion and curing, results in a highly reliable and stable material that can withstand high loads and challenging conditions. Whether for critical components or custom projects, high strength fiberglass sheets offer a level of performance that standard fiberglass sheets simply cannot match.
Fiberglass Air Box Installation for Performance Enhancement
Common Applications of High Strength Fiberglass Sheets
High strength fiberglass sheets are utilized in a wide range of industries due to their exceptional durability, lightweight properties, and high mechanical strength. Their unique characteristics make them ideal for various applications where performance and reliability are critical.
Aerospace
In the aerospace industry, high strength fiberglass sheets are commonly used for manufacturing aircraft components, such as wing structures, fuselage parts, and internal components. These sheets help reduce overall weight, which is essential for improving fuel efficiency and flight performance. The lightweight nature of high strength fiberglass sheets allows for increased payload capacity and enhanced aerodynamic efficiency. Additionally, their excellent resistance to moisture and corrosion ensures that aircraft components can withstand harsh environmental conditions encountered during flight.
Automotive
High strength fiberglass sheets are also widely applied in the automotive sector, particularly in the production of vehicle body parts. They are used to create lightweight panels, bumpers, and structural components, contributing to improved vehicle performance and fuel efficiency. The use of high strength fiberglass sheets allows manufacturers to reduce the weight of vehicles without compromising safety or structural integrity. Furthermore, these sheets offer excellent impact resistance, making them suitable for parts that require durability and longevity in the face of wear and tear.
Construction
In construction, high strength fiberglass sheets are employed for a variety of structural applications and reinforcement purposes. When used as high strength fiberglass sheets for windows, they play a crucial role in providing enhanced durability and resistance to environmental factors. These sheets can be found in building materials, such as panels and beams, where their strength ensures the longevity of structures. High strength fiberglass sheets for windows are also used in applications like roofing, where their lightweight nature and resistance to UV rays help enhance energy efficiency and durability.
Specific Products Made from High Strength Fiberglass Sheets
- Aircraft Wing Components: Lightweight, high-strength components that improve aerodynamics and reduce fuel consumption.
- Automotive Body Panels: Durable panels that enhance vehicle aesthetics and performance while maintaining structural integrity.
- Structural Beams and Panels: Reinforcement materials in construction that provide strength without adding excessive weight.
- Marine Applications: High strength fiberglass sheets are also utilized in boat hulls and other marine structures, benefiting from their resistance to water and corrosion.
High strength fiberglass sheets serve a vital role across multiple industries, including aerospace, automotive, and construction. Their unique properties enable innovative applications that enhance performance, durability, and efficiency in various products and structures.
Industries Where High Strength Fiberglass Sheets Are Not Suitable
While high strength fiberglass sheets offer exceptional durability, impact resistance, and strength, there are certain industries and applications where they are not ideal. Understanding where these sheets are unsuitable helps users make informed decisions about material selection for specific needs.
Beauty and Cosmetic Industries:
High strength fiberglass sheets are not designed for aesthetic or cosmetic purposes. In the beauty industry, materials are typically required to have smooth, flawless finishes and be suitable for direct contact with the skin. Fiberglass, especially in its raw form, can have rough edges or surface imperfections that may irritate the skin or compromise the desired appearance. Additionally, its rigid nature makes it unsuitable for flexible, lightweight products commonly used in beauty applications, such as makeup tools, packaging, or personal care items.
Food and Pharmaceutical Industries:
High strength fiberglass sheets are not typically used in food or pharmaceutical manufacturing due to concerns about contamination. Fiberglass materials, when improperly sealed or processed, can shed fine particles or fibers, which can pose a health risk in environments that require the highest standards of cleanliness and safety. Food and drug manufacturing require materials that are non-porous, easy to clean, and resistant to contamination, which is why alternatives like stainless steel, plastic, or glass are preferred in these fields.
Consumer Electronics:
While fiberglass composites are sometimes used in certain components of electronics, high strength fiberglass sheets are not commonly used for consumer electronics applications. The need for highly precise, thin, and flexible materials for devices like smartphones, laptops, or tablets makes fiberglass less suitable. Electronics also often require materials with excellent electrical insulation and thermal conductivity, which may not be optimized by high strength fiberglass sheets.
Textiles and Fashion:
High strength fiberglass sheets are not suitable for fashion or textile applications where flexibility, comfort, and breathability are essential. Fiberglass is inherently stiff and heavy, which makes it unsuitable for clothing, accessories, or fabrics where softness and flexibility are prioritized. While fiberglass might occasionally be used for structural or reinforcement purposes in fashion, it is not the material of choice for products intended to be worn directly on the body.
Medical Devices and Prosthetics:
In the medical field, the use of high strength fiberglass sheets is limited due to specific health and safety regulations. Materials used in medical devices or prosthetics must be non-toxic, biocompatible, and capable of withstanding sterilization processes. While fiberglass can be used in some medical applications, such as in orthopedic casting, high strength fiberglass sheets are typically not used for implants or devices that are in direct contact with sensitive tissues or organs due to concerns about biocompatibility and the potential release of harmful fibers.
While high strength fiberglass sheets are valuable in industries requiring strength, durability, and impact resistance, they are not suitable for applications in industries like beauty, food production, consumer electronics, fashion, or medical devices. These sheets are primarily intended for structural, industrial, and heavy-duty uses, where their mechanical properties shine. For industries with specific requirements, other materials that meet safety, flexibility, or aesthetic standards are more appropriate choices.
Pricing Information for High Strength Fiberglass Sheets
When considering high strength fiberglass sheets, understanding the pricing structure is essential for budgeting and decision-making. The cost of these sheets can vary widely based on several factors, including size, thickness, quality, and specific applications.
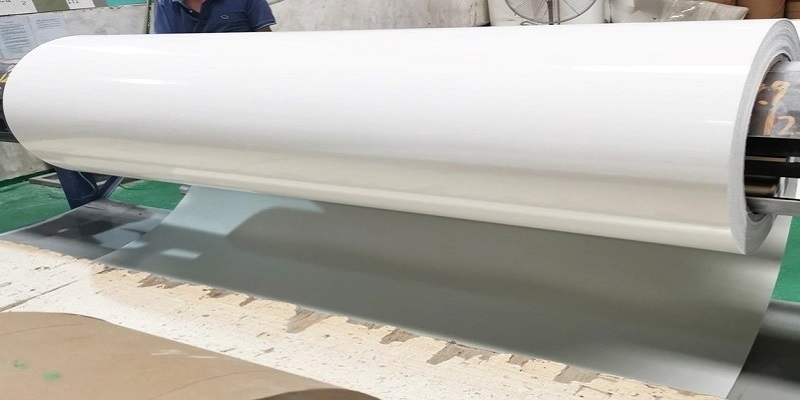
High Strength Fiberglass Sheets Price
The typical price range for high strength fiberglass sheets generally falls between $30 to $100 per square foot. However, this price can fluctuate based on the following factors:
- Size: Larger sheets tend to cost more due to the increased amount of raw materials used in production. Standard sizes may be more affordable than custom dimensions, which often come with additional fabrication costs.
- Thickness: Thicker sheets, which provide greater strength and durability, usually command higher prices. For example, a standard thickness of 0.125 inches may cost less than a thicker option of 0.250 inches, which offers enhanced performance characteristics.
- Quality: The quality of the fiberglass and resin used in the sheets significantly influences pricing. Higher-grade materials that offer superior mechanical properties, UV resistance, and chemical stability are typically priced at a premium.
Variations in Pricing Based on Applications and Custom Requirements
Pricing for high strength fiberglass sheets can also vary depending on the specific applications they are designed for. For instance:
- Aerospace Applications: Sheets intended for aerospace components often undergo rigorous testing and certification processes, resulting in higher costs compared to those used for less demanding applications.
- Custom Requirements: Custom orders tailored to specific project needs—such as unique shapes, colors, or enhanced features—can lead to increased prices. Customization requires additional labor and materials, which can affect the final cost.
- Bulk Orders: Purchasing high strength fiberglass sheets in bulk can lead to discounts and reduced per-unit pricing, making it a cost-effective option for large-scale projects.
- Supplier Differences: Prices may also vary between suppliers based on their production methods, overhead costs, and geographical location. It’s advisable to compare prices across multiple vendors to find the best deal.
High strength fiberglass sheets present a diverse pricing landscape influenced by size, thickness, quality, and application. Understanding these factors can help buyers make informed purchasing decisions while ensuring they select the right product for their specific needs.
Lightweight Fiberglass Top Box – Ideal for Storage
GangLong Fiberglass High Strength Fiberglass Sheets
GangLong Fiberglass is a well-known supplier that offers a wide range of industrial products, including high strength fiberglass sheets. Recognized for their extensive inventory and high-quality materials, GangLong Fiberglass is a go-to source for businesses and DIY enthusiasts seeking reliable solutions for various applications.
Overview of Types of High Strength Fiberglass Sheets Available at GangLong Fiberglass
At GangLong Fiberglass, customers can find several types of high strength fiberglass sheets tailored to meet different needs. These sheets typically include options such as:
- G10/FR4 Sheets: These are standard high strength fiberglass sheets made from epoxy resin and glass fabric. They are highly durable and flame-resistant, making them suitable for electrical applications and structural support.
- Laminate Sheets: Offered in various thicknesses and sizes, these sheets are designed for heavy-duty applications. They provide excellent mechanical strength and are often used in environments requiring superior performance under stress.
- Custom Fabrications: GangLong Fiberglass also provides custom cutting services, allowing customers to order high strength fiberglass sheets in specific dimensions tailored to their project requirements.
Associated Costs
The costs of high strength fiberglass sheets at GangLong Fiberglass can vary based on the type, thickness, and size of the sheets. Generally, prices for these sheets range from $30 to $120 per square foot, depending on the specific product and any customization needed. The high strength fiberglass sheet rate can also be influenced by the material grade, with G10 sheets typically being more affordable compared to specialty laminates designed for specific industrial applications.
Benefits of Purchasing from GangLong Fiberglass
Purchasing high strength fiberglass sheets from GangLong fiberglass offers several advantages:
- Reliable Shipping: GangLong fiberglass is known for its prompt shipping services, often offering same-day shipping on in-stock items. This ensures that customers receive their materials quickly, minimizing downtime for projects.
- Extensive Product Availability: With a vast selection of high strength fiberglass sheets, customers are likely to find exactly what they need. GangLong fiberglass’s comprehensive inventory includes various grades, thicknesses, and custom options.
- Detailed Product Information: The website provides detailed specifications, material properties, and application guidelines for each product. This helps customers make informed decisions based on their specific requirements.
- Customer Support: GangLong fiberglass has a reputation for excellent customer service, providing assistance in product selection and answering any inquiries related to their offerings.
High strength fiberglass sheets from GangLong fiberglass represent a reliable option for those in need of durable, high-performance materials. Their extensive range, combined with efficient shipping and customer support, makes GangLong fiberglass a preferred supplier for many industries and applications.
High Strength Fiberglass Sheets for Sale
Finding high strength fiberglass sheets for sale is essential for individuals and businesses looking to utilize this versatile material in various applications. Fortunately, there are numerous options available both locally and online, making it easier than ever to source these sheets.
Where to Find High Strength Fiberglass Sheets for Sale
- Local Suppliers: Many local hardware stores and specialty material suppliers carry high strength fiberglass sheet. Stores such as GangLong fiberglass, and local industrial supply companies often have a selection of fiberglass materials. Visiting these stores allows you to inspect the products in person and seek advice from knowledgeable staff regarding your specific needs.
- Online Retailers: Like GangLong fiberglass. It retailers typically offer a wider variety of products, including different grades and thicknesses, which may not be available locally.
- Manufacturer Direct Sales: Purchasing directly from manufacturers can also be an option. Many companies that produce high strength fiberglass sheets offer direct sales through their websites, providing access to bulk purchasing and potential discounts.
Tips for Comparing Prices and Quality
- Research Multiple Suppliers: Always compare prices from various suppliers to ensure you’re getting the best deal. Prices can vary significantly based on location, product type, and supplier reputation. Checking several sources helps identify the most competitive pricing.
- Review Product Specifications: Pay attention to the specifications of fiberglass sheets, such as thickness, strength ratings, and material composition. High strength fiberglass sheets should meet the requirements of your specific application, so understanding these details is crucial.
- Check Customer Reviews: Look for customer reviews and ratings for both the products and the suppliers. This feedback can provide insights into product quality and the reliability of the supplier, helping you make informed decisions.
- Inquire About Shipping Costs: When purchasing online, consider shipping costs, as they can significantly impact the overall price. Some suppliers may offer free shipping on larger orders or for local deliveries.
- Consider Custom Options: If you have specific requirements for your project, inquire about custom sizes or cuts. Many suppliers offer customization services, which can save time and effort in achieving the right dimensions for your needs.
Sourcing high strength fiberglass sheets for sale is accessible through local suppliers and various online retailers. By taking the time to compare prices, review specifications, and check customer feedback, you can ensure that you find the best value for your fiberglass sheet purchases.
High-Quality Aluminum Expanded Metal Grating for Industrial Use
High Strength Fiberglass Sheets Cost
Understanding the cost of high strength fiberglass sheets is essential for budgeting and planning your projects effectively.
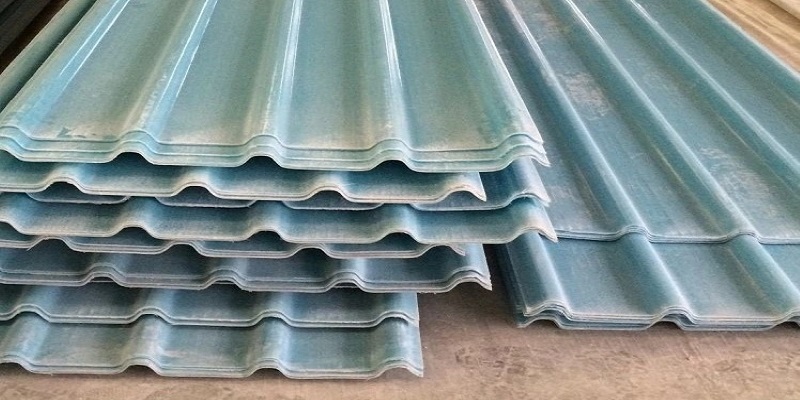
Factors Affecting the Cost of High Strength Fiberglass Sheets
- Material Quality: The quality of the fiberglass and resin used in manufacturing significantly impacts the price. Higher-grade materials that offer better strength, durability, and resistance to environmental factors (such as moisture, UV rays, and chemicals) typically come at a premium. For instance, sheets made from aerospace-grade fiberglass will be more expensive than standard options due to the stringent manufacturing processes and quality control measures in place.
- Customization Options: Customization can lead to additional costs for high strength fiberglass sheets. If you require specific sizes, shapes, or features tailored to your project, manufacturers may charge extra for these bespoke options. This could include customized thicknesses, surface finishes, or specific fiberglass weaves. While custom orders ensure that the sheets meet your exact needs, it’s important to factor in these costs when planning your budget.
- Market Demand and Supply Chain Considerations: The overall market demand for high strength fiberglass sheets can affect pricing. If there is a surge in demand due to trends in construction, aerospace, or automotive industries, prices may increase accordingly. Additionally, supply chain factors such as availability of raw materials, shipping costs, and production delays can influence the final price of the sheets. For example, disruptions in the supply chain, such as those caused by global events, may lead to shortages and higher prices.
Typical Price Ranges
Typically, high strength fiberglass sheets can range in price from $30 to $120 per square foot, depending on the factors mentioned above. Standard thicknesses and readily available sizes tend to fall at the lower end of this range, while specialized, high-performance sheets can reach the higher end.
When considering high strength fiberglass sheets, it is crucial to understand the various factors that influence their cost. By being aware of material quality, customization options, and market dynamics, you can make informed purchasing decisions that align with your budget and project requirements. Always compare prices from multiple suppliers to ensure you get the best value for your investment.
Benefits of Using High Strength Fiberglass Sheets
High strength fiberglass sheets offer a range of advantages that make them a popular choice across various industries. Their unique properties and capabilities provide significant benefits in both performance and cost-effectiveness.
Durability
One of the primary benefits of high strength fiberglass sheets is their exceptional durability. These sheets are highly resistant to moisture, chemicals, and UV rays, making them suitable for use in harsh environments. This resistance helps prevent issues such as rotting, corrosion, and degradation, ensuring that the sheets maintain their integrity over time. As a result, they require less frequent replacement, contributing to lower long-term costs.
Lightweight
High strength fiberglass sheets provide a strong yet lightweight alternative to traditional materials like metal. Their low weight facilitates easier handling and installation, reducing labor costs and the need for heavy machinery during transport. This characteristic is especially beneficial in applications where weight reduction is critical, such as in aerospace and automotive industries, where it can lead to improved fuel efficiency and performance.
Versatility
Another significant advantage is the versatility of high strength fiberglass sheets. They can be customized to fit a variety of applications, from aerospace components to construction materials. Available in multiple thicknesses, sizes, and finishes, these sheets can be tailored to meet specific project requirements. This adaptability allows them to be utilized in diverse sectors, including automotive, marine, and industrial manufacturing.
Cost-Effectiveness
While the initial cost of high strength fiberglass sheets may be higher than some alternatives, their long-term savings make them a cost-effective choice. Their durability translates into reduced maintenance costs and fewer replacements over time. Additionally, their lightweight nature can lower shipping and handling expenses, further enhancing their overall cost-effectiveness.
These advantages make high strength fiberglass sheets a reliable and efficient material choice for a wide range of applications. Whether used in demanding industrial settings or innovative design projects, they deliver outstanding performance and value.
FAQs About High Strength Fiberglass Sheets
The strongest fiberglass cloth is typically S-glass fiberglass, known for its superior strength and stiffness compared to other types like E-glass. S-glass can withstand higher tensile stresses and offers better impact resistance, making it ideal for applications that require high performance, such as in aerospace and military equipment. Additionally, S-glass has a higher resistance to thermal degradation, which enhances its durability under extreme conditions. For projects requiring maximum strength, S-glass is often recommended over other fiberglass options.
High strength fiberglass refers to fiberglass materials that have been engineered to provide enhanced mechanical properties, typically including E-glass and S-glass types. These materials are often used in applications where superior strength, stiffness, and durability are required, such as in aerospace components, automotive parts, and heavy-duty construction materials. High strength fiberglass sheets combine the lightweight nature of fiberglass with exceptional tensile and compressive strength, making them suitable for demanding applications where performance is critical.
The strength of fiberglass sheets can vary based on the type of fiberglass used and the specific resin formulations. Generally, fiberglass sheets exhibit high tensile strength, often ranging from 20,000 to 40,000 psi (pounds per square inch), depending on the specific type and grade of fiberglass. For instance, standard E-glass fiberglass sheets offer good strength and are commonly used in various applications. However, for applications that require greater strength, S-glass sheets can provide even higher tensile strength, making them more suitable for demanding environments.
While fiberglass is strong, it is generally not as strong as Kevlar, especially in terms of tensile strength and impact resistance. Kevlar is a high-performance synthetic fiber known for its exceptional strength-to-weight ratio, making it a preferred choice for applications such as body armor, aerospace, and high-stress components. Kevlar fibers can be several times stronger than steel on an equal weight basis. However, fiberglass has advantages, including lower cost, better insulation properties, and a wider range of applications. When choosing between the two, consider the specific requirements of your project, including factors like weight, cost, and the nature of the stresses involved.
The strongest type of fiberglass is woven roving fiberglass or S-glass fiberglass. S-glass is a high-performance material known for its superior strength-to-weight ratio compared to traditional E-glass, the most common type of fiberglass. S-glass offers higher tensile strength and resistance to stretching, making it ideal for applications requiring enhanced durability, such as in aerospace, military, and automotive industries. Woven roving fiberglass, which combines continuous fiberglass filaments into a woven fabric, also provides increased strength and structural integrity. This type of fiberglass is often used in the construction of boat hulls, wind turbine blades, and other high-stress applications. Woven roving fiberglass is durable and can be combined with resins to form solid, high-strength sheets suitable for various industrial purposes.
The strength of a fiberglass sheet depends on several factors, including the type of fiberglass used, the resin it’s combined with, and the layup or weave pattern. Generally, fiberglass sheets can have a tensile strength between 350 MPa (50,000 psi) and 900 MPa (130,000 psi). For example, E-glass fiberglass typically provides a tensile strength of 350-450 MPa, whereas S-glass can exceed 900 MPa, offering superior strength. The fiberglass sheet’s strength also depends on its thickness; thicker sheets tend to be stronger, though they are heavier. The strength of the sheet is further enhanced by the resin used in its production, with epoxy resins offering the best bonding strength for fiberglass applications. High-strength fiberglass sheets are commonly used in the automotive, aerospace, and construction industries, where durability and resistance to stress are crucial.
Fiberglass is generally stronger than plexiglass (acrylic) in terms of impact resistance, tensile strength, and overall durability. Fiberglass has a higher tensile strength, typically ranging between 350 and 900 MPa, depending on the type of fiberglass and its resin bonding. Plexiglass, on the other hand, has a tensile strength of around 70-100 MPa, which is much lower than that of fiberglass. Fiberglass is also more resistant to fatigue and stress cracking, making it more durable for high-stress environments. However, plexiglass is more transparent and is often chosen for applications where clarity is important. It’s also lighter and more easily shaped than fiberglass. While fiberglass is stronger and more durable in industrial applications, plexiglass is favored for its optical properties and ease of use in projects requiring transparency and lightweight materials.
1708 fiberglass refers to a specific type of woven fiberglass mat that features a combination of woven roving and chopped strand mat. This reinforcement is commonly used in boat building, automotive, and other heavy-duty composite applications. The “1708” designation indicates the weight of the material, which is 17 oz per square yard (around 580 g/m²). The weave structure offers excellent strength while maintaining flexibility, making it ideal for creating durable, high-strength fiberglass sheets and components. The chopped strand mat portion provides a random fiber orientation, enhancing bonding and strength, while the woven roving provides additional tensile strength in the direction of the weave. This combination makes 1708 fiberglass ideal for laminating larger surfaces and creating structures that need both structural integrity and flexibility.
Fiberglass on its own is not generally used for ballistic protection, but fiberglass composites can be engineered to absorb some of the energy from a bullet. For example, when combined with materials like Kevlar or carbon fiber, fiberglass composites can provide some level of bullet resistance, although they are not as effective as materials specifically designed for ballistic protection, such as bulletproof steel or ceramic plates. The fiberglass helps to distribute the energy of the bullet across a larger area, potentially preventing penetration. However, fiberglass alone is not typically used for bulletproofing purposes due to its lower impact resistance compared to specialized materials. Bulletproof vests or armored vehicles often use layers of fiberglass combined with stronger materials to increase protection from high-velocity impacts.
To make fiberglass stronger, several methods can be employed:
Use high-strength fiberglass: Opt for higher-grade fibers like S-glass instead of the more common E-glass. S-glass offers superior tensile strength and impact resistance.
Resin choice: Choose a high-quality resin, such as epoxy resin, which offers better bonding strength and resistance to environmental degradation compared to polyester or vinyl ester resins.
Layering: Increase the number of layers or plies of fiberglass, as more layers add to the material’s overall strength. The strength increases in proportion to the number of layers.
Proper curing: Ensure that the fiberglass is properly cured to optimize its strength. This means controlling the temperature and humidity during the curing process.
Reinforcements: Add other reinforcing materials, such as carbon fiber or Kevlar, for enhanced strength and durability.
You should avoid touching fiberglass directly because the fibers in the material can easily become airborne, posing a health risk if inhaled or when they come into contact with your skin. Fiberglass dust and particles can cause irritation to the skin, eyes, and respiratory system. When the tiny fibers come into contact with the skin, they can cause itching, redness, and even rashes, as they penetrate the outer layers of skin. Inhalation of fiberglass particles can lead to respiratory irritation and long-term health issues like asthma or pulmonary fibrosis. Protective gear such as gloves, long sleeves, and a mask should be worn when handling fiberglass to avoid direct contact with the material and minimize the risk of exposure to harmful dust.
The strongest fiberglass resin is typically epoxy resin, which is known for its superior bonding strength, durability, and resistance to both physical wear and environmental factors. Epoxy resins create an exceptionally strong bond with fiberglass, making them ideal for high-performance applications where strength, durability, and longevity are critical. Epoxy resin is also resistant to corrosion, heat, and moisture, making it perfect for use in marine, aerospace, and automotive industries. Other resins, such as polyester and vinyl ester, are also used with fiberglass but generally offer lower strength and less resistance to environmental factors compared to epoxy resin. Epoxy resin’s superior adhesion and resistance to fatigue make it the resin of choice for applications where maximum strength and longevity are required.
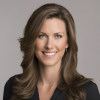
As the editor of GangLong Fiberglass, I have years of experience and in-depth research, focusing on cable tray products, fiberglass solutions, and grille systems. I incorporate years of industry insights and practical experience into every content, committed to promoting the progress of the industry. At GangLong Fiberglass, my commitment is reflected in every product, from innovative cable trays to durable fiberglass solutions and sturdy grille systems. As an authoritative voice in the industry, my goal is to provide valuable information to professionals and businesses and promote forward-looking solutions.