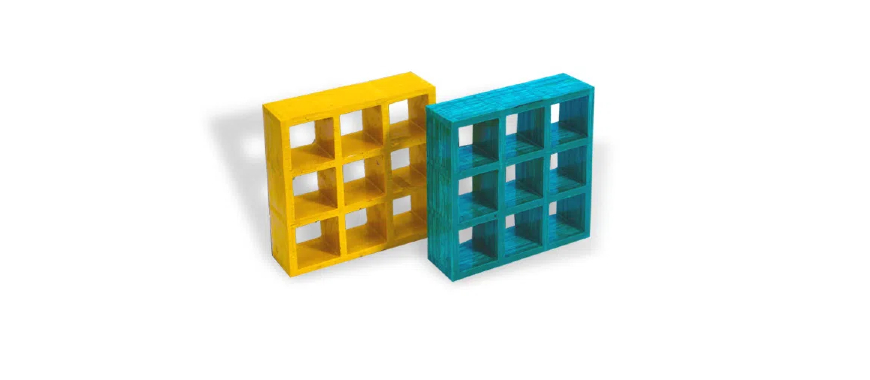
Lamina FRP is a combination of Fiberglass Reinforced Polymer (FRP) and plywood, creating durable, lightweight, and versatile panels. This innovative material is designed to offer excellent strength while maintaining a relatively low weight, making it ideal for various applications. Lamina FRP panels are commonly used in trailers, construction projects, and interior wall paneling. Their durability and ability to withstand harsh conditions make them a popular choice in both commercial and industrial sectors. Additionally, Lamina FRP’s versatility extends to transportation applications, where its lightweight nature helps improve efficiency and reduce fuel consumption. As a result, Lamina FRP has become a go-to material in industries that require strength, ease of use, and long-lasting performance.
What Are Lamina FRP Panels?
Lamina FRP panels are a type of composite material, combining Fiberglass Reinforced Polymer (FRP) with a substrate such as plywood. This combination results in a highly durable and versatile product that combines the strength of fiberglass with the flexibility and lightness of plywood. The FRP is bonded to the plywood or other substrates through a specialized manufacturing process, ensuring the panels are both robust and easy to handle. The primary appeal of Lamina FRP panels lies in their ability to combine the best qualities of both materials, making them ideal for a wide range of applications.
Lamina FRP: Definition and Composition
Lamina FRP panels consist of layers of FRP material bonded to a substrate, often plywood. This construction provides the panels with superior mechanical properties, such as high tensile strength and resistance to impact, while maintaining the versatility and ease of handling provided by the plywood. The fiberglass layer, which is infused with a resin, offers exceptional durability, while the plywood serves as the structural base, offering flexibility and ease of processing.
The combination of these two materials creates a panel that can withstand the demands of both commercial and industrial environments. This dual-material construction results in a balance of strength, flexibility, and lightweight characteristics, making Lamina FRP panels a popular choice in various sectors.
Lamina FRP and Features: Key Advantages and Applications
Lamina FRP panels come with a variety of features that make them ideal for use in tough environments. These features include:
- Impact-Resistant and Durable: Lamina FRP panels are designed to resist damage from impacts, making them highly durable in construction, transportation, and industrial applications. The fiberglass layer provides added strength, preventing cracks or dents under stress.
- Water and Chemical-Resistant Surfaces: One of the standout features of Lamina FRP panels is their resistance to moisture and chemicals. The FRP surface creates a waterproof barrier, making the panels perfect for use in areas prone to wet conditions or exposure to harsh chemicals. This quality ensures that the panels retain their integrity and performance even in challenging environments.
Thanks to these features, Lamina FRP panels are becoming increasingly popular in industries such as construction, trailers, and interior wall paneling, where durability and resistance to wear and tear are crucial.
Choosing the Right FRP Pipe Class for Your Project Needs
Types of Lamina FRP Panels
Lamina FRP panels come in several varieties, each designed for specific applications that require both strength and versatility. The primary types of Lamina FRP panels include FRP plywood panels and fiberglass reinforced plywood trailer panels. Each type offers unique benefits depending on the intended use, ranging from residential construction to heavy-duty transportation needs. These panels are chosen for their durability, resistance to environmental factors, and ability to provide both structural support and ease of handling.
FRP Plywood Panels
FRP plywood panels are a widely used type of Lamina FRP that combines the lightweight and flexible nature of plywood with the strength and durability of fiberglass. The most common thicknesses for these panels are 1/2″ and 3/4″, although custom thicknesses can be manufactured depending on specific requirements. These panels are commonly used in various industries, especially for applications where both structural integrity and impact resistance are critical.
- Common Thicknesses: The most common thicknesses of FRP plywood panels are 1/2″ and 3/4″. These thicknesses provide an optimal balance between strength and weight, ensuring the panels remain manageable while offering sufficient support and durability for various applications. The 1/2″ thickness is generally used for lighter-duty applications, while the 3/4″ thickness offers additional strength for more demanding uses.
- Applications: Lamina FRP plywood panels are widely used in trailers, recreational vehicles (RVs), and for structural reinforcements in buildings. The panels’ durability and lightweight nature make them ideal for use in the construction of trailer walls, floors, and ceilings, as well as in RV construction, where both strength and resistance to wear are needed. Additionally, they are used in structural applications where enhanced support is required.
Fiberglass Reinforced Plywood Trailer Panels
Fiberglass reinforced plywood trailer panels are a specialized version of Lamina FRP panels designed specifically for the transportation and cargo industry. These panels are engineered to meet the rigorous demands of heavy-duty applications, where strength, durability, and resistance to environmental factors are critical. The combination of fiberglass and plywood results in a high-performance panel suitable for various trailer and transport applications.
- Designed Specifically for Cargo and Transportation: These panels are tailored to meet the needs of the transportation industry. They are used primarily in the construction of cargo trailers, truck bodies, and other transport vehicles where the panels must withstand heavy loads, impacts, and the wear and tear of constant use. The FRP material enhances the panel’s ability to resist moisture, chemicals, and physical damage, ensuring long-lasting performance in demanding conditions.
- High Tensile Strength for Heavy-Duty Applications: One of the standout features of fiberglass reinforced plywood trailer panels is their high tensile strength. The fiberglass component provides additional reinforcement, allowing the panels to endure heavy-duty loads and harsh environments. These panels are ideal for applications such as cargo storage, truck body construction, and heavy-duty trailers, where traditional plywood may not provide sufficient strength or durability.
The two primary types of Lamina FRP panels—FRP plywood panels and fiberglass reinforced plywood trailer panels—offer unique advantages for a wide range of applications. Whether used for trailers, RVs, or structural reinforcements, these panels are designed to meet the highest standards of performance and reliability.
The Versatility of FRP Pipes Compared to Steel Pipe Options
Applications of Lamina FRP Panels
Lamina FRP panels are versatile and durable materials that find applications in various industries, including transportation, construction, commercial spaces, and custom fabrication. Their unique combination of fiberglass and plywood provides strength, flexibility, and resistance to environmental factors, making them an ideal choice for a wide range of uses. Whether for structural reinforcement, moisture resistance, or impact durability, Lamina FRP panels offer exceptional performance across different fields.
Transportation
Lamina FRP panels are widely used in the transportation industry, where their lightweight yet durable nature plays a crucial role in enhancing efficiency and ensuring long-lasting performance. These panels are often found in the construction of trailers, truck bodies, and other transport vehicles.
- Fiberglass-Reinforced Plywood Panels for Trailer and Truck Bodies: Lamina FRP panels are an essential material for the construction of trailer and truck bodies. The combination of plywood and fiberglass offers a robust structure that can withstand the rigors of transportation. Their ability to resist wear, impact, and weathering ensures that the vehicles remain in good condition for extended periods.
- Lightweight Yet Durable for Fuel Efficiency and Longevity: The lightweight properties of Lamina FRP panels help reduce the overall weight of vehicles, improving fuel efficiency and decreasing operating costs. At the same time, the panels’ durability ensures they withstand the demands of frequent loading and unloading, providing longevity and reducing the need for frequent repairs or replacements.
Construction
In the construction industry, Lamina FRP panels are valued for their strength, moisture resistance, and versatility. These panels are commonly used in both interior and exterior applications, providing a reliable and cost-effective solution for various building needs.
- Interior and Exterior Wall Panels: Lamina FRP panels are widely used for both interior and exterior wall panels in residential, commercial, and industrial buildings. They offer a smooth, easy-to-maintain surface that resists damage from impacts, scratches, and stains. Additionally, their ability to withstand extreme weather conditions makes them suitable for use in exterior walls, especially in areas where durability and low maintenance are required.
- Suitable for Moisture-Prone Areas Like Bathrooms and Basements: Due to their water-resistant properties, Lamina FRP panels are particularly well-suited for environments prone to high moisture levels, such as bathrooms and basements. These panels help prevent water damage, mold growth, and deterioration, ensuring the longevity of the structure while maintaining a clean and attractive appearance.
Commercial Spaces
Lamina FRP panels are also widely used in commercial spaces, particularly in environments that require strict sanitation and durability standards. These panels are a common choice for areas in the food industry, where cleanliness and resistance to chemicals and moisture are critical.
- USDA-Approved FRP Wall Panels for Commercial Kitchens and Food Processing: One of the standout features of Lamina FRP panels is their approval for use in USDA-regulated environments. These panels meet the standards required for use in commercial kitchens, food processing areas, and other facilities where hygiene and cleanliness are paramount. Their resistance to chemicals, water, and stains makes them an excellent choice for surfaces that need frequent cleaning and sanitizing.
Custom Fabrication
Lamina FRP panels are also favored in custom fabrication for their ability to be tailored to meet specific needs. These panels can be easily customized for a wide variety of applications, from recreational vehicles (RVs) to portable structures.
- Panels for RVs, Storage Units, and Portable Structures: The flexibility of Lamina FRP panels makes them ideal for custom fabrication in RVs, storage units, and portable structures. These applications benefit from the panels’ lightweight nature, which makes them easy to handle and transport, while the panels’ durability ensures that the finished structures are long-lasting and resistant to wear and tear. Lamina FRP panels are particularly valuable in RV construction, where both weight and strength are essential factors for ensuring stability and durability on the road.
The wide range of applications for Lamina FRP panels highlights their versatility, strength, and adaptability. From transportation to construction, commercial spaces, and custom fabrication, Lamina FRP panels continue to provide exceptional performance across multiple industries, making them an essential material for various high-performance needs.
Advantages of Using Bell and Spigot FRP Pipe Systems
Advantages of Lamina FRP Panels
Lamina FRP panels offer a wide range of advantages that make them a top choice for various industrial, commercial, and transportation applications. These panels combine the best properties of fiberglass and plywood, delivering unmatched strength, durability, and versatility. The following benefits are key reasons why Lamina FRP panels are favored across multiple sectors.
Durability
Lamina FRP panels are known for their impressive durability, making them highly suitable for demanding environments. The fiberglass surface of these panels offers significant protection against physical damage and wear over time.
- Fiberglass Surface Resists Scratches, Impacts, and Corrosion: The fiberglass layer on Lamina FRP panels acts as a protective shield, providing resistance against scratches, impacts, and corrosion. This makes the panels ideal for high-traffic areas or environments where physical stress is common. The resistance to corrosion ensures that these panels maintain their integrity even when exposed to harsh weather conditions or chemicals.
Versatility
Another major advantage of Lamina FRP panels is their versatility, which allows them to be customized for a wide range of applications and aesthetic preferences. Whether used in construction or transportation, these panels can be tailored to meet specific needs.
- Available in Various Thicknesses (e.g., 1/2″, 3/4″) and Sizes: Lamina FRP panels are available in multiple thicknesses and sizes, allowing them to be used in a variety of applications. The most common thicknesses include 1/2″ and 3/4″, but custom sizes and thicknesses can be produced to meet specific project requirements. This flexibility makes them adaptable for both light-duty and heavy-duty uses.
- Customizable Finishes for Aesthetic and Functional Needs: In addition to their functional benefits, Lamina FRP panels can be customized with various finishes. These finishes can be chosen for aesthetic appeal, such as glossy or matte surfaces, as well as for specific functional needs like slip resistance or added chemical protection. This adaptability makes Lamina FRP panels suitable for diverse applications, from interior wall cladding to outdoor structures.
Ease of Installation
Lamina FRP panels are also praised for their ease of installation, which contributes to lower labor costs and faster project completion times.
- Panels Are Lightweight and Easy to Cut and Install: The lightweight nature of Lamina FRP panels makes them easier to handle, cut, and install compared to heavier materials like concrete or traditional plywood. This reduces the overall effort and time required during installation, leading to faster project completion and cost savings on labor. Their flexibility also makes them easy to shape and fit into various spaces, whether for commercial kitchens, trailers, or building facades.
Cost-Effective
Lamina FRP panels provide long-term value, as their durability and low maintenance requirements contribute to significant cost savings over time.
- Long Lifespan Reduces Maintenance and Replacement Costs: One of the biggest advantages of Lamina FRP panels is their extended lifespan. Due to their durability, these panels are highly resistant to damage, which reduces the need for frequent maintenance or replacements. As a result, Lamina FRP panels offer a cost-effective solution in the long run, especially in environments where other materials might degrade quickly.
The numerous advantages of Lamina FRP panels—including their durability, versatility, ease of installation, and cost-effectiveness—make them an ideal choice for a wide range of applications. Whether used in construction, transportation, or commercial spaces, these panels provide a reliable and long-lasting solution that helps reduce both upfront and ongoing costs.
Installation Tips for Lamina FRP Panels
Installing Lamina FRP panels properly ensures their longevity and optimal performance. By following a few essential steps during preparation, adhesive application, and finishing, you can achieve a professional-quality installation. Below are key installation tips to help you get the best results with Lamina FRP panels.
Preparation
Proper preparation is the first step in ensuring that Lamina FRP panels adhere securely and function effectively. The surface onto which the panels are applied must be clean, dry, and smooth to create the ideal conditions for bonding.
- Clean and Dry the Substrate Before Installation: Before applying Lamina FRP panels, ensure the substrate is thoroughly cleaned and dried. Dust, dirt, grease, and moisture can interfere with the adhesion process, leading to poor bonding or potential damage over time. Use a mild detergent and water to clean the surface, and allow it to dry completely before proceeding with installation. If necessary, sand the surface to ensure smoothness and promote better adhesion.
- Use Appropriate Tools for Cutting Panels to Size: Cutting Lamina FRP panels to the required size is a key part of the installation process. Always use the right tools to ensure precise cuts without damaging the panels. A circular saw or table saw with a fine-toothed blade is ideal for cutting these panels. Be sure to wear protective gear, such as goggles and a dust mask, to protect yourself from debris during the cutting process. Properly measure and mark the panels before cutting to ensure accurate dimensions.
Adhesive Application
Applying adhesive properly is essential for ensuring that Lamina FRP panels are securely fixed to the substrate and will perform well over time. The adhesive should be applied evenly and with care.
- Apply FRP Adhesive Evenly Across the Surface: To achieve a strong bond, apply an even layer of FRP adhesive across the back of the Lamina FRP panel and the substrate. Avoid using excessive adhesive, as it may cause the panel to shift or bubble. A notched trowel or adhesive spreader can help ensure an even distribution. Follow the manufacturer’s guidelines for the recommended adhesive and application process to ensure the best results.
- Use Screws or Rivets for Additional Stability: While the adhesive will provide a strong initial bond, it is often beneficial to secure Lamina FRP panels with screws or rivets for added stability. This is particularly important in areas where the panels will face significant stress or impact, such as in trailers or industrial applications. Ensure that the fasteners are evenly spaced and driven in securely, but be careful not to over-tighten, as this can cause the panel to crack.
Finishing Touches
After the panels are installed, it’s important to focus on the finishing touches to prevent moisture from penetrating the edges and joints. Proper sealing helps ensure the longevity and effectiveness of the Lamina FRP panels.
- Seal Edges and Joints to Prevent Moisture Ingress: Once the Lamina FRP panels are in place, seal all edges and joints to prevent moisture from entering, which could cause damage over time. Use a high-quality silicone or polyurethane sealant to fill any gaps. Be sure to apply the sealant smoothly and evenly, ensuring complete coverage of all edges and seams. This step is especially crucial in areas prone to moisture, such as bathrooms, kitchens, or exterior applications. Proper sealing helps maintain the integrity of the panels and prevents mold, mildew, and other moisture-related issues.
By following these installation tips, you can ensure that your Lamina FRP panels are installed correctly, providing long-lasting performance and durability. Proper preparation, careful adhesive application, and thorough finishing touches are all essential steps in achieving a successful installation.
Pricing and Availability
When considering Lamina FRP panels for your project, it’s essential to understand the pricing structure and the factors that can influence the cost. Lamina FRP panels are available in various thicknesses, sizes, and finishes, which all contribute to their pricing. Knowing these factors can help you make an informed decision based on your budget and the specific requirements of your project.
Price Range
The cost of Lamina FRP panels can vary depending on their thickness and other specifications. Generally, the price range for standard panels is as follows:
- 1/2″ FRP Plywood: The price for 1/2″ Lamina FRP plywood typically ranges from $40 to $70 per panel. This thickness is suitable for lighter-duty applications and is commonly used for interior panels in trailers, RVs, and walls.
- 3/4″ FRP Plywood: The price for 3/4″ Lamina FRP plywood ranges from $50 to $100 per panel. This thicker panel is ideal for more demanding applications, including heavy-duty transport vehicles, industrial uses, and areas requiring additional durability.
These prices are approximate and can vary depending on factors such as location, vendor, and bulk purchase discounts.
Factors Affecting Cost
Several factors influence the cost of Lamina FRP panels, and understanding them can help you estimate the total cost for your project.
- Panel Size, Thickness, and Surface Finish: Larger panels or those with greater thickness typically cost more due to the additional material required for production. Additionally, Lamina FRP panels come in various surface finishes, such as smooth, textured, or matte, which can impact the overall cost. Custom finishes may increase the price compared to standard options.
- Fire-Rating and Customizations: If you require panels with fire-resistant properties or specific customizations, such as unique sizes or additional surface treatments, these factors will also influence the price. Fire-rated panels are often more expensive due to the specialized materials and processes involved in their manufacturing. Customization requests, whether for specific colors or performance characteristics, may also lead to higher costs.
By considering these pricing factors and understanding the specific needs of your project, you can choose the right Lamina FRP panels that meet both your functional and budgetary requirements. Availability may vary depending on your location and the specific product specifications, so it’s important to check with local suppliers or manufacturers for accurate pricing and delivery timelines.
FAQs about Lamina FRP
FRP laminate, short for Fiberglass Reinforced Plastic laminate, is a composite material made by combining a plastic resin with fiberglass. The resin is used to bond the fiberglass strands together, creating a strong, durable material that is both lightweight and resistant to a range of environmental factors, such as moisture, chemicals, and impacts. FRP laminates are commonly used for applications in which high strength and durability are required, such as in construction, transportation, and industrial environments.
The process of creating FRP laminate involves layering the fiberglass cloth with resin and then curing the material under heat and pressure. The resulting laminate is not only incredibly strong but also offers a smooth surface that can be easily cleaned and maintained. FRP laminates are often used for wall panels, ceilings, doors, and even flooring in various industries, offering an effective solution where traditional materials might fail due to their susceptibility to wear and environmental damage.
FRP (Fiberglass Reinforced Plastic) comes in several types, each suited to different applications based on their composition and intended use. The four main types of FRP include:
Pultruded FRP: Pultruded FRP is created by pulling continuous fibers through a resin bath and then curing them under heat. This process produces long, uniform shapes such as rods, beams, and panels. It is known for its high strength-to-weight ratio and is commonly used in structural applications like bridges, platforms, and railings.
Filament-Wound FRP: This type of FRP is produced by winding continuous fibers around a mold and applying resin. The process creates cylindrical or spherical shapes, such as pipes, tanks, and pressure vessels. It offers excellent mechanical properties and is often used in industries like chemical processing and oil and gas.
Sheet Molding Compound (SMC) FRP: SMC FRP is made by compressing a sheet of fiberglass mat and resin into a mold under heat and pressure. This process allows for the creation of complex shapes, often used in automotive parts, electrical enclosures, and other molded products requiring a smooth finish.
Resin Transfer Molding (RTM) FRP: RTM is used to produce high-quality FRP parts by injecting resin into a closed mold containing dry fiberglass mat or fabric. This method is typically used for complex, high-performance parts in industries such as aerospace, automotive, and marine.
FRP stands for Fiberglass Reinforced Plastic. It is a composite material made by combining a plastic resin with glass fibers. The glass fibers provide the material with strength and durability, while the resin holds the fibers together and provides shape. The combination of these materials creates a versatile, lightweight, and highly durable material that can be used in a wide range of applications.
The benefits of FRP include its resistance to corrosion, high strength-to-weight ratio, and ability to withstand harsh environmental conditions. These properties make FRP an excellent choice for applications in industries such as construction, automotive, aerospace, marine, and electrical. FRP can be molded into various shapes and sizes, offering versatility in its use. Additionally, FRP is highly customizable, with different types of resins and fiberglass reinforcement being used depending on the specific requirements of the application.
The cost of FRP (Fiberglass Reinforced Plastic) can vary widely depending on several factors, including the type of FRP, the thickness, the complexity of the product, and the intended use. Generally speaking, FRP is considered an affordable option compared to materials like steel, aluminum, or concrete, especially when considering its durability and performance.
Cost of FRP Sheets and Panels: Basic FRP sheets or panels typically range from $30 to $100 per panel, depending on thickness and surface finish. For example, 1/8-inch-thick FRP sheets can be relatively inexpensive, while thicker or customized panels may cost more.
Cost of Custom FRP Products: More specialized FRP products, such as pultruded profiles, filament-wound pipes, or complex molded items, can be more expensive. These products often require specific manufacturing processes and materials, which can increase costs. Custom FRP products used in industries like aerospace or automotive may cost several hundred dollars per unit.
Long-Term Cost Efficiency: While the initial cost of FRP may be higher than some conventional materials, its long lifespan, resistance to corrosion, and low maintenance requirements make it a cost-effective choice in the long run. FRP can last for decades without needing frequent repairs or replacements, providing significant savings over time.
The cost of FRP will depend on the specific product and its application, but it is generally considered a cost-efficient alternative to traditional materials.
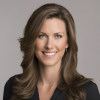
As the editor of GangLong Fiberglass, I have years of experience and in-depth research, focusing on cable tray products, fiberglass solutions, and grille systems. I incorporate years of industry insights and practical experience into every content, committed to promoting the progress of the industry. At GangLong Fiberglass, my commitment is reflected in every product, from innovative cable trays to durable fiberglass solutions and sturdy grille systems. As an authoritative voice in the industry, my goal is to provide valuable information to professionals and businesses and promote forward-looking solutions.