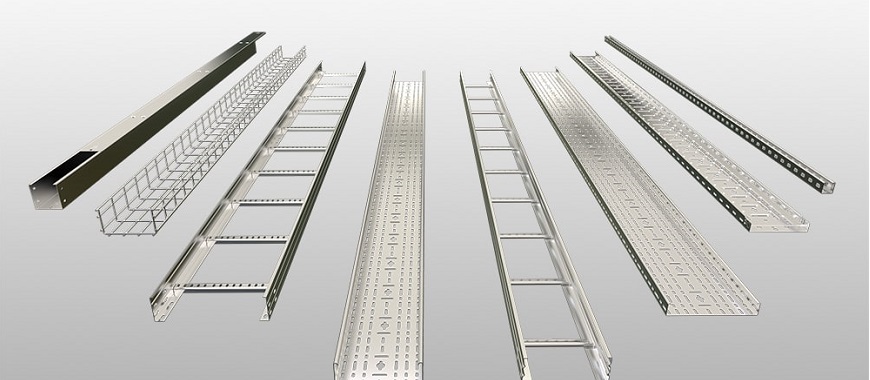
Cantilever cable trays are crucial for organizing and supporting cables in various settings. These trays are designed to provide stability and efficient load distribution, making them a preferred choice for modern cable management systems. They are often mounted on walls or ceilings, optimizing space while ensuring cables are secure and easily accessible. Cantilever cable tray systems simplify cable routing by offering robust support without requiring complex structural modifications. Their role extends beyond organization, contributing to safety by reducing cable clutter and potential hazards. In modern installations, cantilever designs are valued for their adaptability to different environments, including industrial, commercial, and residential spaces. This versatility makes cantilever cable trays an essential component in today’s cable management solutions.
Key Features and Finishes of Cantilever Cable Trays
Cantilever cable trays are essential for organizing and supporting cables in a wide range of installations. Their design prioritizes strength, durability, and adaptability, making them a reliable choice for modern cable management. Additionally, the inclusion of cable tray cantilever arms enhances their functionality by providing extended support for heavier loads. Below, we explore material options, finishes, and coatings that contribute to their performance and longevity.
Material Options for Cantilever Cable Trays
Cantilever cable trays are manufactured using materials like plastic, steel, and stainless steel, each offering unique benefits. The selection of materials is typically influenced by environmental conditions, load requirements, and installation types.
Plastic Cantilever Cable Trays
Plastic is lightweight and resistant to corrosion, making it suitable for environments with high humidity or exposure to chemicals. Its insulation properties also make it ideal for certain electrical applications. However, it may not provide the same load-bearing capacity as metal options, limiting its use in heavy-duty setups.
Steel Cantilever Cable Trays
Steel offers high tensile strength, making it suitable for supporting large cable bundles. It performs well in most environments but is prone to corrosion if not properly coated. Steel is commonly used in industrial and commercial installations requiring robust support.
Stainless Steel Cantilever Cable Trays
Stainless steel is highly durable and resistant to corrosion, even in harsh environments. It is ideal for outdoor installations or areas exposed to extreme temperatures. The material’s longevity often offsets its higher initial cost.
In combination with cable tray cantilever arms, these materials enable flexible and durable solutions for managing complex cable systems.
Available Finishes and Protective Coatings
The finish and protective coating applied to cantilever cable trays significantly impact their performance and lifespan. Popular options include electro-galvanized, hot-dip galvanized, and stainless steel finishes.
Electro-Galvanized Finishes
Electro-galvanization involves coating the surface of the tray with a thin layer of zinc. This process protects against rust and is suitable for indoor environments. While cost-effective, electro-galvanized finishes may not withstand prolonged exposure to moisture or chemicals.
Hot-Dip Galvanized Finishes
Hot-dip galvanization submerges the tray in molten zinc, creating a thicker and more durable coating. This finish is excellent for outdoor or industrial environments, offering better resistance to corrosion than electro-galvanized options. It is particularly useful for installations requiring high structural integrity.
Stainless Steel Finishes
Stainless steel finishes provide unmatched durability and resistance to corrosion. They are ideal for environments with constant exposure to water, chemicals, or extreme temperatures. While more expensive, stainless steel finishes ensure long-term performance, reducing maintenance costs.
The addition of cable tray cantilever arms further supports the weight and stability of these trays, ensuring a secure and efficient cable management system in various settings. These arms also benefit from protective coatings, enhancing their ability to withstand environmental stressors.
Applications and Use Cases of Cantilever Cable Trays
Cantilever cable trays are highly versatile, catering to diverse industries and installation environments. Their functionality, combined with cantilever arm for cable tray systems, ensures efficient cable management in industrial, commercial, and residential settings. Below, we delve into specific use cases and practical applications that demonstrate the value of cantilever cable trays
Cantilever Straddle Cable Hanger Systems
Cantilever straddle cable hanger systems play a crucial role in supporting large-scale cable installations. These systems ensure stability and prevent sagging by evenly distributing cable weight.
Industrial Applications
In industrial environments, such as factories and power plants, cantilever cable trays combined with straddle hangers manage extensive cable networks. Heavy-duty cables used for machinery and energy distribution require robust support, which these systems efficiently provide. The inclusion of cantilever arm for cable tray systems further enhances stability, even in high-vibration environments.
Commercial Settings
In commercial buildings like offices and shopping centers, cantilever cable trays and straddle cable hangers organize electrical wiring and communication cables. These systems maintain a neat arrangement, reducing the risk of accidents and ensuring easy access for maintenance.
Residential Use Cases
While less common, cantilever cable trays are sometimes used in residential buildings, particularly in smart home setups. They help organize cables for entertainment systems, security devices, and home automation, ensuring a clean and efficient arrangement.
The adaptability of cantilever arm for cable tray systems makes them indispensable for managing large-scale cable installations in any setting.
Integration with Cable Management Solutions
Cantilever cable trays seamlessly integrate with modern cable management solutions, offering optimal space utilization and structural efficiency. Their design simplifies installation and enhances access for maintenance and upgrades.
Wall-Mounted Systems
Wall-mounted cantilever cable trays are ideal for environments with limited floor space. Combined with cantilever arm for cable tray systems, they provide reliable support for heavy cables. These installations are common in data centers, where maximizing space is a priority.
Ceiling-Mounted Applications
Ceiling-mounted configurations are widely used in production facilities and warehouses. Cantilever cable trays in such setups ensure that cables are off the ground, minimizing tripping hazards and protecting wires from potential damage.
Examples from Data Centers
In data centers, cantilever cable trays are essential for managing vast networks of power and communication cables. The combination of trays and cantilever arm for cable tray solutions ensures that the system can handle heavy loads without compromising access or organization.
The integration of cantilever cable trays into various cable management solutions showcases their ability to enhance safety, efficiency, and accessibility in diverse environments. These benefits make them a preferred choice across industries.
Top Guidelines to Enhance Cable Tray Safety Practices
Installation Guidelines for Cantilever Cable Trays
Proper installation of cantilever cable trays ensures their long-term performance and structural reliability. By following mounting techniques and adhering to safety standards, these trays can effectively manage cables in diverse environments. Below, we explore the methods and considerations critical for installing cantilever cable trays.
Mounting and Support Techniques
The mounting process for cantilever cable trays is crucial to maintain stability and ensure even weight distribution. Proper support techniques maximize efficiency and prevent structural damage.
Positioning for Weight Distribution
To ensure durability, cantilever cable trays should be positioned to evenly distribute cable weight. Overloading or uneven distribution can strain the tray and its brackets, leading to premature wear or failure. Installers should calculate the expected load and place cantilever cable tray brackets at intervals that support the heaviest sections effectively.
Role of Brackets and Hangers
Brackets and hangers are vital for creating a stable installation. These components anchor the cantilever cable tray securely to walls or ceilings. GangLong Fiberglass emphasizes using high-quality brackets that resist deformation under pressure. Hangers complement brackets by providing additional support for longer trays or heavier loads. Together, they enhance the structural integrity of the system.
Practical Examples
For industrial setups, brackets are often spaced closer together to accommodate heavy cables. In contrast, residential installations typically use wider spacing, as cables are lighter. These variations highlight the flexibility of cantilever cable tray systems in managing diverse load requirements.
Safety and Compliance Requirements
Adhering to safety and compliance standards during installation ensures the reliability and longevity of cantilever cable trays. Proper planning also minimizes risks associated with electrical systems.
Meeting Electrical Standards
Cantilever cable trays must comply with electrical codes that dictate load limits and grounding requirements. Overloading a tray can compromise safety, making it essential to calculate the maximum allowable weight during planning. GangLong Fiberglass advises installers to follow regional codes and consult documentation to avoid errors.
Environmental Considerations
Environmental factors, such as moisture and temperature, can impact the durability of cantilever cable trays. For outdoor installations, corrosion-resistant materials and coatings are essential to prevent damage. Stainless steel trays or galvanized finishes are recommended for corrosive environments, as these materials resist weathering effectively.
Examples from Practice
In high-humidity areas, such as coastal regions, the use of stainless steel cantilever cable trays has proven effective in preventing rust. Similarly, for factories with high temperatures, heat-resistant materials ensure the tray maintains its structural integrity.
By adhering to safety standards and optimizing installation techniques, cantilever cable trays deliver reliable cable management across various applications. These measures also protect the investment by extending the tray’s operational lifespan.
Cantilever Brake Systems in Cable Tray Design
Cantilever brake systems play a significant role in enhancing the functionality and safety of cantilever cable tray designs. These systems utilize innovative mechanisms to ensure stability and proper weight distribution, making them indispensable in heavy-duty and high-load applications. Below, we explore their components and the specific benefits they offer in cable tray installations.
Role of Cantilever Brake Levers in Cable Systems
Cantilever brake levers provide critical control in cantilever cable tray systems by managing load stress and ensuring secure installations. Their integration is vital for safety and operational efficiency.
Application of Braking Mechanisms in Cantilever Cable Tray Designs
Braking mechanisms in cantilever cable tray designs allow for controlled handling of cables during installation and maintenance. These levers help secure cable trays, preventing unwanted movement or slippage that could lead to structural damage or cable misalignment. They are especially useful when adjusting the position of a tray or securing cables to minimize tension.
Advantages of Brake Levers in Installation Safety
Cantilever brake levers enhance safety by stabilizing the tray during critical operations. Installers rely on these mechanisms to prevent sudden shifts, particularly in environments with heavy or uneven cable loads. By maintaining alignment, brake levers reduce the risk of accidents and ensure long-term system reliability.
Practical Scenarios
In industrial applications, cantilever brake levers are often used in elevated cable tray installations. They provide added stability, ensuring that heavy-duty trays remain securely anchored during maintenance or expansion activities. GangLong Fiberglass integrates brake levers in their systems to ensure both safety and functionality.
Cantilever Brake Hanger and Straddle Cable Applications
Cantilever brake hangers and straddle cables work together to optimize load distribution and enhance the structural integrity of cantilever cable tray systems.
How Straddle Cables Enhance Load Distribution and Stability
Straddle cables are used to balance and support weight across cantilever cable trays. These components reduce the strain on brackets and arms by evenly distributing the load. By mitigating localized stress, straddle cables prevent deformation or failure of the tray over time.
Examples of Integration in Heavy-Duty Cantilever Designs
In heavy-duty installations, cantilever brake hangers combined with straddle cables are essential for maintaining system integrity. For instance, in manufacturing facilities with extensive electrical networks, these components ensure that cantilever cable trays can support large cable bundles without compromising stability. The inclusion of brake hangers prevents shifting or misalignment caused by vibrations from nearby machinery.
Real-World Applications
GangLong Fiberglass has implemented brake hangers and straddle cables in projects requiring high-capacity cable management. For example, in a data center setup, these components ensured that cantilever cable trays remained stable despite heavy cable volumes and regular maintenance operations.
By integrating brake systems and straddle cables, cantilever cable trays provide safe, reliable, and efficient cable management in various demanding environments. These features make them an essential component of modern cable tray designs.
Top Applications of Open Cable Tray in Industry
Selecting the Right Cantilever Cable Tray for Your Needs
Choosing the appropriate cantilever cable tray ensures efficient cable management, system durability, and safety across various applications. Proper selection depends on understanding load requirements, material compatibility, and environmental conditions. Below, we outline key criteria and comparisons to aid in selecting the ideal cantilever cable tray.
Criteria for Choosing Cantilever Cable Trays
When selecting a cantilever cable tray, several factors must be considered to match the system with its intended application.
Load Capacity
Understanding the weight that a cantilever cable tray must support is critical. Heavier loads require materials like steel or stainless steel, reinforced with brackets and hangers. Overestimating capacity ensures safety and prevents structural failure over time. Light-duty applications, such as residential wiring, can use lightweight materials like plastic.
Material Compatibility
The material of the cantilever cable tray must align with environmental conditions. For outdoor installations, corrosion-resistant materials like stainless steel or galvanized steel are ideal. Indoor environments may accommodate less resistant materials, provided they are durable enough for expected wear.
Environmental Suitability
The tray must withstand environmental factors, such as moisture, temperature fluctuations, and chemical exposure. In corrosive settings, stainless steel offers exceptional longevity. Hot-dip galvanized trays are effective in moderately challenging environments, while electro-galvanized trays are better suited for dry, indoor use.
Examples of Application Suitability
GangLong Fiberglass emphasizes the importance of matching tray selection to application needs. For example, in high-humidity environments, stainless steel ensures durability and prevents rust. Conversely, plastic trays work well in small-scale setups with minimal environmental stress.
Comparing Cantilever Cable Tray Options
Understanding the advantages and disadvantages of various cantilever cable tray materials and types helps in making an informed decision. The table below compares key features across material options.
Material | Advantages | Disadvantages | Best Applications |
---|---|---|---|
Plastic | Lightweight, corrosion-resistant, cost-effective | Lower load capacity, less durable under stress | Residential, small-scale setups |
Steel | High strength, suitable for heavy loads | Prone to corrosion without proper coating | Industrial and commercial environments |
Stainless Steel | Exceptional corrosion resistance, durable | Higher cost | Outdoor, corrosive, and high-temperature areas |
Electro-Galvanized | Cost-effective, moderate rust protection | Limited durability in wet environments | Indoor installations |
Hot-Dip Galvanized | Excellent corrosion resistance, long-lasting | Heavier than electro-galvanized | Industrial and outdoor settings |
Guidelines for Selection
GangLong Fiberglass recommends assessing the weight and volume of cables, the environment, and the potential for future expansion. For demanding industrial or outdoor use, stainless steel or hot-dip galvanized trays are optimal. Indoor installations can prioritize cost-effective options like electro-galvanized trays or plastic.
By evaluating these criteria and understanding material properties, you can select a cantilever cable tray that ensures reliable performance, safety, and adaptability for your needs.
Types and Sizes of Ice Bridge Cable Tray
Cantilever Cable Tray : Maintenance and Long-Term Performance
Proper maintenance is crucial to ensuring the durability and reliability of cantilever cable trays over time. Regular inspections, upkeep, and preventative measures can significantly extend their lifespan while maintaining safety and functionality. Below, we outline strategies for effective maintenance and how they contribute to long-term performance.
Regular Inspections and Upkeep
Regular inspections are essential for identifying potential issues before they escalate into major problems. These inspections focus on wear, corrosion, and structural integrity.
Checking for Wear and Damage
Wear and damage can occur due to environmental exposure, overloading, or improper installation. Inspect the cantilever cable tray and its components, including brackets and cantilever arms for cable tray, for signs of strain or deformation. Early detection of issues like bent supports or cracked coatings helps prevent further damage.
Monitoring Corrosion in Components
Corrosion is a common concern, particularly in outdoor or humid environments. Stainless steel trays resist corrosion better than other materials, but all types should be inspected regularly for rust or pitting. Replacing corroded sections ensures the tray continues to provide safe and reliable support.
Ensuring Structural Integrity
Structural integrity should be assessed by verifying that all bolts, screws, and cantilever arms for cable tray remain securely fastened. Loose connections can compromise the tray’s stability, especially under heavy loads. Corrective measures like tightening or replacing fasteners help maintain strength.
Examples of Maintenance Success
GangLong Fiberglass has highlighted instances where early inspections prevented costly replacements. For example, identifying minor rust on hot-dip galvanized trays allowed timely re-coating, extending the system’s usability by several years.
Prolonging the Lifespan of Cantilever Cable Trays
Taking preventative measures is key to ensuring the longevity of cantilever cable trays. Protective coatings and cleaning practices help reduce wear and tear over time.
Applying Protective Coatings
Protective coatings like galvanization and powder finishes are effective against rust and corrosion. Regular reapplication of coatings on cantilever cable tray surfaces maintains their resistance to environmental stressors. Stainless steel trays often require less frequent re-coating due to their inherent durability.
Cleaning Practices for Durability
Cleaning the tray system removes debris, dust, and chemicals that may accelerate corrosion or weaken structural components. Use mild cleaners to avoid damaging finishes, especially on galvanized surfaces. Cleaning brackets and cantilever arms for cable tray ensures these components also remain functional and corrosion-free.
Material Choice and Environmental Impact
Material selection directly affects maintenance frequency. Stainless steel trays, for instance, perform well in harsh conditions with minimal upkeep. Conversely, electro-galvanized trays may require more regular attention in moist environments to prevent rust.
Examples of Effective Preventative Measures
A manufacturing facility using GangLong Fiberglass products found that routine cleaning and re-coating of its hot-dip galvanized trays reduced maintenance costs by 30%. This approach also minimized downtime and enhanced system reliability.
With regular inspections and preventative care, cantilever cable trays deliver consistent performance, even in challenging conditions. These practices not only ensure safety but also protect your investment for years to come.
FAQs about Cantilever Cable Tray
The distance between supports for cable tray wire depends on the type of tray and the load it carries. Generally, cantilever cable tray systems require support spans of 6 to 12 feet for most installations. Heavier loads or specific materials, such as steel or stainless steel, may allow longer spans up to 20 feet. However, lighter trays like plastic or those used for smaller-scale installations may need closer supports to maintain structural integrity. It is essential to follow manufacturer guidelines and standards, such as the National Electrical Code (NEC), to ensure safety and compliance. Additionally, the use of cantilever arms for cable tray installations enhances support, allowing for stable and secure wire management over longer distances.
Cable trays are categorized into three main types based on their design and application. Ladder trays are commonly used for heavy-duty applications and offer superior support with ventilation for cables. Perforated trays, also known as solid-bottom trays, are ideal for applications requiring protection against dust and debris. Wire mesh trays, made of lightweight materials, are frequently used in commercial environments to manage smaller bundles of wires. Each type serves specific needs, and the selection depends on factors such as cable type, installation environment, and required load capacity. For cantilever cable tray systems, ladder trays are often preferred because they integrate well with cantilever arms for cable tray support, ensuring reliability in demanding setups.
Cables that are not specifically rated for cable tray use should never be installed on a cable tray system. For instance, flexible cords and cables not listed or labeled for tray installations are prohibited. Additionally, cables lacking proper flame-retardant properties, as required by NEC standards, should not be used. Non-rated cables can pose risks, including fire hazards and system failures, especially in industrial or commercial environments. Properly rated cables, such as those marked TC (tray cable) or MC (metal-clad cable), are suitable for cantilever cable tray installations. When installing a cantilever cable tray, always verify that the selected cables meet the required codes and standards for the specific application and environment.
Cable trunking and cable trays serve similar purposes but differ significantly in design and application. Cable trunking is an enclosed system designed to protect cables from external damage and environmental factors. It offers superior protection but lacks ventilation, which can lead to heat buildup in some applications. In contrast, a cable tray, including cantilever cable tray systems, provides an open structure that supports and organizes cables while allowing airflow to prevent overheating. Cable trays are often used in industrial or large-scale installations, whereas trunking is more common in small-scale, indoor environments requiring cable concealment. The integration of cantilever arms for cable tray installations further enhances their flexibility, making them suitable for complex layouts and heavier loads. The choice between the two depends on factors such as cable protection requirements, environment, and load capacity.
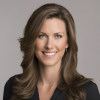
As the editor of GangLong Fiberglass, I have years of experience and in-depth research, focusing on cable tray products, fiberglass solutions, and grille systems. I incorporate years of industry insights and practical experience into every content, committed to promoting the progress of the industry. At GangLong Fiberglass, my commitment is reflected in every product, from innovative cable trays to durable fiberglass solutions and sturdy grille systems. As an authoritative voice in the industry, my goal is to provide valuable information to professionals and businesses and promote forward-looking solutions.