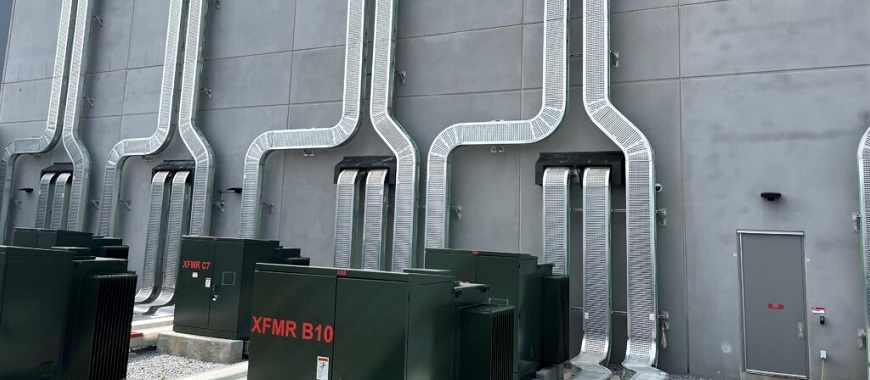
Overhead cable trays are essential components in industrial and commercial environments, ensuring organized and efficient cable management. Overhead cable tray systems—ladder & wire mesh trays—support power & data cables in long-span industrial applications. These systems provide a structured pathway for cables, reducing clutter and enhancing safety. Overhead cable tray solutions are widely utilized in power distribution, telecommunications, and data centers. By keeping cables elevated, they minimize potential damage from environmental factors or interference. Additionally, overhead cable tray systems improve accessibility, making it easier to inspect, maintain, and upgrade wiring networks. They are designed to handle varying load capacities, catering to both small-scale and large-scale installations. The implementation of overhead cable trays can significantly streamline cable management processes, reduce downtime, and enhance operational efficiency across various industries.
What is Overhead Cable Tray
An overhead cable tray—whether in ladder, trough, or solid‐bottom form—is a rigid support system mounted above ground level (on ceilings, ceiling supports, or suspended from structural beams) to carry, organize, and protect bundles of electrical power or data cables. These trays are engineered to create a continuous, unobstructed pathway that facilitates safe, efficient cable routing in a wide variety of environments.
Structure & Materials
- Ladder trays: Two longitudinal side rails connected by rungs, ideal for heavy cable loads and long spans.
- Wire mesh trays (basket trays): Constructed from welded wire grids, offering lightweight flexibility and excellent ventilation.
- Solid-bottom trays: Provide maximum cable protection from dust or debris.
- Common materials include aluminum (for corrosion resistance and lighter weight) and galvanized or stainless steel (for higher strength).
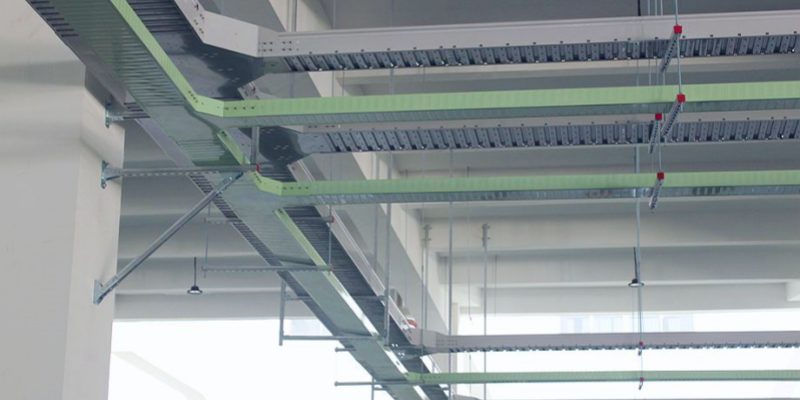
The Installation of Overhead Cable Tray
Proper installation of an overhead cable tray is essential for ensuring safety, efficiency, and reliability in cable management systems. This process involves careful planning, adherence to guidelines, and the use of appropriate tools and techniques. Effective overhead cable management is crucial for maintaining the functionality of cables in industrial and commercial environments.
Steps for Proper Installation
Planning and Design Considerations
Effective overhead cable tray installation begins with thorough planning and design. Assess the installation environment—ceiling height, cable types, and load requirements—and draft a layout plan showing tray routes, junctions, and support points. Select tray material, dimensions, and protective coatings to suit both current demands and future expansion. Confirm compliance with applicable building and electrical codes to ensure safety, structural integrity, and long-term system durability.
Tools and Equipment Needed for Installation
Installing overhead cable trays requires tools and equipment to ensure efficiency and safety. You will need drills, wrenches, measuring tools and cable tray measurement gauges, plus cable fasteners and a ladder or lift for high-level access. Verify all equipment is in good condition before beginning work. Choose mounting hardware—brackets, hangers, support struts—with the correct load rating and spacing to distribute weight evenly, prevent sagging, and maintain alignment.
Step-by-Step Installation Process
Begin the installation by marking the tray route on the ceiling or wall according to your design plan. Mount supports at specified intervals, then assemble and secure tray sections to these supports. Lay cables within the tray carefully, avoiding sharp bends or overcrowding. Apply identification labels to facilitate future maintenance or upgrades. Finally, inspect the entire system to verify stability, correct alignment, and compliance with safety and performance standards.
Safety Guidelines for Overhead Cable Tray Installation
Safety Measures During Installation
Safety is paramount when installing overhead cable trays. Installers must wear appropriate personal protective equipment (PPE) such as helmets, gloves, eye protection, and safety harnesses when working at height. Secure scaffolding or lifts should be used to access elevated areas, and tools and materials handled carefully to prevent falling objects. Clear communication among team members and the presence of properly trained personnel help avoid misunderstandings and ensure a smooth, accident-free installation.
Compliance with Electrical and Industrial Safety Standards
Adhering to relevant electrical and industrial safety standards is critical for overhead cable tray installation. These regulations specify support spacing, allowable load ratings, cable separation requirements, cable tray inspection procedures, and safe routing practices. Trays in high-risk areas may require fire-resistant materials, while grounding and bonding must follow code. Regular inspections and audits ensure standards are consistently met, maintaining system integrity, preventing hazards, and reducing the risk of regulatory penalties over the tray’s service life.
Emergency Procedures and First Aid
Preparing for emergencies is an essential safety guideline. A clear rescue plan and readily accessible first-aid kits must be in place before installation begins. Team members should be trained to perform basic first aid and recognize signs of shock, electrical burns, or falls. Emergency contact numbers and the location of the nearest medical facility should be posted conspicuously. Regular drills reinforce response protocols, ensuring quick, organized action if an incident occurs.
Overhead Cable Tray Applications in Industrial Setting
Overhead cable trays provide sturdy, organized pathways for power and data cables in industrial settings. Modular designs support heavy loads, simplify installation and maintenance, and adapt to harsh, high-density environments—boosting safety, scalability, and operational efficiency.
Heavy-Duty Installations
Overhead cable tray systems serve heavy-duty sites like power plants, oil refineries, and large manufacturing facilities by supporting substantial cable loads and resisting mechanical stresses. Ladder-type and enclosed trays offer the necessary strength and protection, while organized routing minimizes damage and downtime. Their modular design also permits straightforward capacity expansion as operational demands increase.
High-Capacity Cable Management
In data centers and automated production lines, overhead cable trays facilitate high-density cable routing to segregate power and data runs, reducing electromagnetic interference and optimizing performance. Wire mesh and ladder trays, with their open structures, enable rapid access for additions or reconfiguration. Scalability and clear labeling also streamline maintenance, keeping complex cable networks orderly and efficient.
Harsh Environmental Conditions
Overhead cable trays in corrosive or extreme environments—such as chemical plants, marine platforms, and wastewater treatment facilities—must withstand moisture, chemicals, and UV exposure. Fiberglass-reinforced plastic or polymer-coated steel trays resist degradation and prevent corrosion, ensuring long service life. Sealed or enclosed trays offer additional protection, safeguarding sensitive wiring against contaminants and harsh weather.
Renewable Energy Installations
In solar farms and wind turbine facilities, overhead cable tray systems manage long cable spans between array fields and central inverters. UV-stable, weather-resistant trays support both power and communication lines, reducing exposure risk and simplifying maintenance across vast outdoor sites. Their lightweight construction and adaptable fittings also ease installation on uneven terrain and over varied structural supports.
Simplify Projects with This B-Line Cable Tray Installation Guide
Cost Analysis of Overhead Cable Tray
Understanding the pricing dynamics of an overhead cable tray is essential for selecting cost-effective and reliable solutions. The pricing is influenced by several factors, and a detailed cost-benefit analysis can help balance initial investment with long-term advantages.
Factors Influencing Prices
Material Choices: Steel, Aluminum, and FRP
Material used in overhead cable trays significantly affects cost: steel trays are typically the most affordable and offer high strength but require corrosion-resistant coatings—adding roughly 15 % to their base price; aluminum trays cost about 30 % more than steel but are lightweight and naturally corrosion-resistant, reducing maintenance expenses; and FRP trays are 60 % pricier than steel alternatives but deliver exceptional chemical, moisture and UV resistance, making them ideal for harsh industrial or marine settings.
Size and Width Variations
Tray size and width have a direct impact on price because larger cross-sections require more material and fabrication effort. For instance, a 600 mm-wide tray typically costs about 1.5 times as much as a 400 mm-wide version. Custom dimensions further increase expenses due to specialized production. Accurately assessing current cable volume and forecasting growth helps select trays that balance cost efficiency with capacity needs, avoiding unnecessary overspending on oversized systems.
Load Capacity Requirements
Reinforced trays designed for heavy loads cost more due to thicker gauge materials, extra cross-members, or additional support features, often adding 25–50 % to the base price. Specifying the correct load capacity prevents tray sagging and structural failure under extensive cable bundles. Although initial expenses rise, choosing appropriate load ratings minimizes operational disruptions and replacement costs over the tray’s service life, ensuring safety and reliability in demanding industrial environments.
Cost-Benefit Analysis
Balancing Upfront Costs with Long-Term Savings
Although aluminum and FRP trays cost more initially, they reduce maintenance and replacement expenses over time. Their superior corrosion resistance and load capacity extend service intervals and minimize labor. This lowers total lifecycle costs by reducing downtime and repair frequency. Choosing premium materials and optimized designs ensures predictable budgeting and improved value across the system’s lifespan.
Quality Investment and Lifecycle Savings
Investing in quality cable trays ensures durability and consistent performance, lowering unforeseen expenses. Reputable suppliers provide robust warranties, expedited support, and spare parts, which buffer operational risks. Lifecycle cost analyses often show that premium materials pay back through reduced maintenance and longer service life. This positive return on investment typically materializes midway through the tray system’s expected lifespan, maximizing cost-effectiveness.
Installation & Construction Costs
Installation expenses vary by tray material and complexity. Tasks like precision cutting, alignment, grounding, and mounting hardware increase labor hours, especially for FRP with custom supports. Equipment rentals for lifts and specialized tools also add costs. Accurate planning and vendor coordination during design reduce surprises. Factoring in labor rates and accessory needs upfront prevents budget overruns and facilitates timely project completion.
Downtime Loss & Operational Efficiency
Unplanned maintenance or failures in cable tray systems can halt operations, incurring revenue losses and overtime costs. High-quality materials and corrosion-resistant designs minimize inspection frequency and repairs, supporting continuous workflows. In data centers or manufacturing plants, each hour of downtime may cost thousands in lost production. By reducing failure risk, robust trays improve operational efficiency, protect profitability, and strengthen resilience against interruptions.
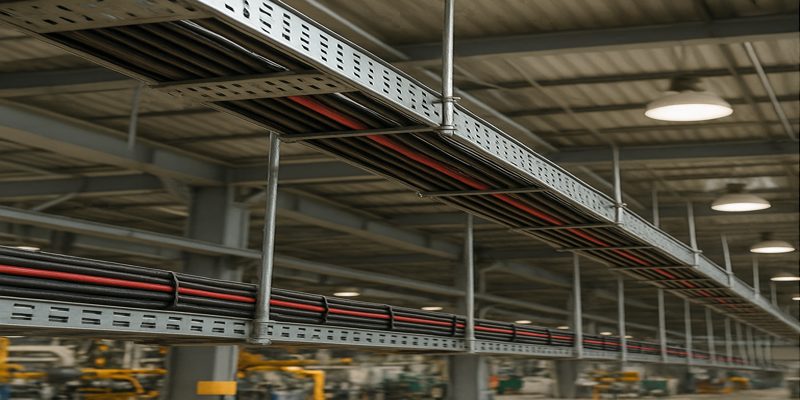
Advantages of Using High Quality Overhead Cable Trays
High-quality overhead cable trays play a crucial role in modern cable management systems, offering enhanced performance, durability, and safety. These trays are designed to optimize overhead cable tray routing systems, ensuring cables remain organized and protected across diverse industrial and commercial applications.
Durability and Strength Under Heavy Loads
High-quality overhead cable trays are built from robust materials like steel or reinforced plastics, enabling them to support heavy cable volumes without deforming or failing. Reinforced structures distribute weight evenly to prevent sagging and ensure long-term reliability, minimizing operational disruptions. In demanding industrial environments, these features provide peace of mind by maintaining structural integrity under the most challenging conditions.
Corrosion Resistance and Longevity
Corrosion-resistant materials such as aluminum and fiber-reinforced plastic (FRP) extend the lifespan of overhead cable trays, especially in environments exposed to moisture, chemicals, or extreme temperatures. By combating rust and degradation, these trays reduce maintenance requirements and avoid premature replacements. In applications like chemical processing or outdoor installations, this resilience delivers lasting performance, saving time and resources.
Improved Safety and Reliability
Secure routing provided by high-quality overhead cable trays minimizes the risk of cable damage, interference, and fire hazards. Effective organization prevents tangling and physical harm, ensuring consistent cable performance. Additional features like cable tray partition separate different cable types, reducing electromagnetic interference. Together, these measures enhance operational safety and reliability, protecting critical systems from costly downtime.
Enhanced Cable Organization and Maintenance
Overhead cable trays create clear, accessible pathways that simplify cable identification, upgrades, and repairs. Their open design promotes airflow around cables, preventing overheating and supporting optimal performance. Maintenance teams benefit from easy access during expansions or troubleshooting, which reduces labor time and operational downtime. This structured approach to cable management streamlines workflows and maximizes system uptime.
Installation Tips for Cable Trays Mounted in a Tunnel
Unique Features of Yellow Overhead Cable Tray
Yellow overhead cable trays are uniquely designed to enhance safety and functionality in industrial and commercial environments. These trays stand out for their visibility and practicality, making them an excellent choice for specific applications. Their use can simplify cable tray overhead installations and improve overall efficiency.
Visibility in Industrial Settings for Improved Safety
Yellow overhead cable trays offer exceptional visibility in busy industrial environments, making cable pathways easy to spot and reducing the risk of accidental interference such as tripping or equipment damage. The bright hue also acts as a visual warning in high-voltage or sensitive cable zones—common in power plants and chemical facilities—keeping personnel alert to potential hazards and ensuring safer work practices.
Applications in Marked Cable Zones and Hazard Areas
These trays are ideal for clearly demarcating distinct cable zones—whether separating power feeders from data circuits or defining restricted areas in tunnels, factories, and outdoor installations. By using yellow trays in hazardous or regulated spaces, companies can maintain compliance with safety standards and minimize accidents. Their robust construction ensures visibility and functionality even under demanding conditions.
UV and Chemical Resistance for Outdoor Durability
Yellow overhead cable trays often feature UV-stable coatings and corrosion-resistant materials to withstand prolonged sun exposure, rain, and chemical splashes. This ensures that the color doesn’t fade and the structural integrity remains intact over years of outdoor use. In petrochemical plants or coastal facilities where harsh weather and corrosive atmospheres prevail, this durability translates into lower maintenance and replacement costs.
Color-Coding for Workflow Optimization
In complex cable management schemes, color-coded trays streamline installation, maintenance, and troubleshooting by instantly identifying cable types, voltage levels, or network segments. Yellow trays can be paired with other colors to create an intuitive visual map of a facility’s wiring infrastructure. This organized approach reduces human error, accelerates repairs, and enhances overall operational efficiency.
Compliance with Overhead Cable Tray Standards
Compliance with cable standards in overhead cable tray systems is essential to ensure safety, efficiency, and reliability. Meeting these standards guarantees that the system functions effectively while adhering to industry regulations. Properly designed and installed overhead cable management trays contribute to smoother operations and reduced risks.
Importance of Meeting Cable Standards Overhead Tray Requirements
Key Industry Standards for Cable Tray Systems
Standards such as IEC 61537, NEMA VE 1/VE 2, and NEC Article 392 specify tray design, material selection, support spacing, and grounding requirements to ensure mechanical strength and electrical safety. They define maximum span lengths, corrosion-resistant materials for harsh environments, and mandatory electrical continuity for fault protection. Aligning installations with these guidelines ensures code compliance, extended service life, and predictable performance under diverse operational stresses.
Ensuring Compliance in Design and Installation
Design compliance begins with accurate layout planning—correct tray widths, support intervals, and cable fill ratios—and material specifications that meet regulatory requirements. During installation, crews must follow manufacturer guidelines for cutting, jointing, and grounding to avoid mechanical stress or electrical hazards. Proper separation of power and data circuits further reduces interference. Documented procedures and skilled supervision minimize rework and guarantee safe, code-compliant installations.
Regular Inspection and Maintenance Protocols
Scheduled inspections verify structural integrity, check for corrosion, ensure proper cable routing and grounding continuity, and identify loose fittings or coating damage. Incorporating periodic thermal imaging and electrical testing detects hotspots or insulation degradation early. A documented maintenance plan with defined inspection intervals and corrective actions preserves compliance, prevents costly failures, and extends service life, proactively safeguarding safety and performance.
Benefits of Standardized Cable Trays
Streamlined Maintenance and Upgrades
Standardized overhead cable trays feature uniform dimensions and fittings, making maintenance and upgrades faster and more predictable. Technicians can quickly identify cable routes and perform repairs or add new runs without dismantling adjacent sections. Compatibility with accessories—such as dividers, junctions, and covers—reduces custom fabrication. This consistency minimizes operational downtime and labor costs, enabling facilities to adapt their cable infrastructure efficiently as demands evolve.
Compatibility with Diverse Cable Types
A standardized tray system accommodates power, data, fiber-optic, and specialty cables within the same routing infrastructure. Proper partitioning and segregation capabilities prevent electrical interference and overheating, ensuring each cable type performs optimally. With modular components designed for different insulation thicknesses and bend radii, these trays support a facility’s changing networking and power distribution requirements, delivering flexible, reliable cable management in mixed-use environments.
Improved Safety and Organization
Standardized trays enhance workplace safety by enforcing clear cable pathways and reducing trip or snag hazards. Consistent labeling and color-coding options further aid quick identification during emergency response or routine inspections. Organized cable layouts also improve airflow, lowering operating temperatures and fire risk. By maintaining tidy, well-defined routing schemes, facilities benefit from safer conditions, simplified troubleshooting, and compliance with fire and electrical codes.
Scalable Design for Future Expansion
Standardized overhead cable trays allow easy integration of additional sections or upgraded components to support growth. Pre-engineered splice plates and extension kits streamline capacity increases without major rework. Facilities can plan modular expansions in phases, matching initial investments to current needs while reserving unused tray slots for future cabling. This scalability safeguards against over-buying and ensures the cable management system evolves cost-effectively with organizational demands.
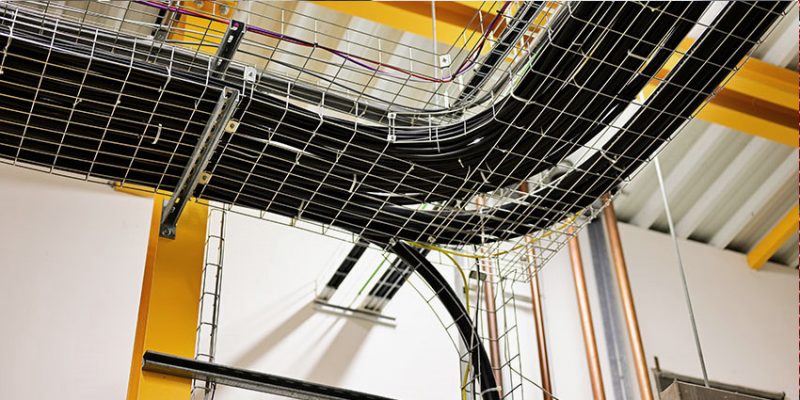
Key Applications for a Durable Cable Tray Tee
Wire Mesh Cable Trays in Overhead Systems
Wire mesh cable trays are a versatile and practical option for overhead cable tray installations. These trays combine flexibility, lightweight design, and ventilation benefits, making them a preferred choice in many scenarios. By integrating wire mesh trays into overhead cabling trays, businesses can achieve efficient and adaptable cable management.
Why Use Wire Mesh Cable Trays?
Lightweight and Flexible Design
Wire mesh cable trays feature a lightweight, open-grid construction that simplifies handling and installation while maintaining ample load-bearing strength. Their flexibility allows easy bending and custom shaping to accommodate route changes, elevation shifts, and complex layouts without extensive cutting or fabrication, and in double cable tray configurations they efficiently separate distinct cable groups within the same framework. This adaptability reduces labor hours and material waste, making wire mesh trays an efficient choice for overhead cable systems that demand both strength and versatility.
Ventilation Benefits for Cable Performance
The open mesh design promotes continuous airflow around cables, effectively dissipating heat generated by high-capacity power or data runs. Improved ventilation prevents overheating, extends cable lifespan, and reduces fire risk. Additionally, dust and debris naturally fall through the grid rather than accumulating on tray surfaces, minimizing maintenance and preserving optimal cable performance in environments with heavy particulate exposure.
Ease of Inspection and Maintenance
With unobstructed views of cable bundles, wire mesh trays enable quick visual inspections and fast access for repairs or additions, eliminating the need to dismantle solid covers or bottoms. Technicians can easily trace, label, and replace individual cables, streamlining troubleshooting and expansions. This clear accessibility reduces downtime and labor costs, ensuring that overhead cable management remains both safe and efficient throughout the system’s service life.
Applications of Wire Mesh Cable Trays
Small-Scale Installations
Wire mesh cable trays excel in small-scale settings like offices, retail spaces, and compact data closets where space is at a premium. Their lightweight, customizable design lets technicians fit trays into tight or irregular ceilings, keeping cable runs organized and accessible. Quick installation and simple reconfiguration support future upgrades without major disruption. GangLong Fiberglass offers mesh solutions tailored for these constrained environments to streamline overhead cable management.
Environments Requiring Frequent Modifications
In dynamic sites such as manufacturing floors, labs, or temporary construction zones, wire mesh trays deliver unmatched adaptability. Their open-grid design allows easy addition, removal, or rerouting of cables without cutting or major disassembly. When extra stability is needed, fiberglass mesh sheets can be integrated to reinforce spans. This flexibility minimizes downtime and labor costs, ensuring overhead cabling can evolve alongside changing operational demands.
High-Capacity Data Centers
High-density data centers demand cable management that combines strength with airflow, making wire mesh trays an ideal choice. The open structure supports heavy bundles of network and power cables while promoting cooling through unobstructed airflow. Trays can be configured in double-tier arrangements to separate power and data lines, enhancing organization and reducing interference. GangLong Fiberglass provides robust mesh systems designed to meet the rigorous requirements of modern data infrastructures.
FAQs about Overhead Cable Tray
The three main types of cable trays commonly used are ladder-type trays, solid-bottom trays, and wire mesh trays. Ladder-type trays consist of two side rails connected by rungs, providing excellent ventilation and easy cable access. Solid-bottom trays feature a completely enclosed design, offering maximum protection from dust, moisture, and other contaminants. Wire mesh trays, also called basket trays, have an open grid structure, making them lightweight and flexible for installations that may require frequent modifications. Each type has specific applications, and the selection depends on factors such as cable load, environmental conditions, and maintenance requirements.
Overhead cable is typically referred to as wiring or cabling installed in an elevated system to organize and protect cables. In an overhead cable tray system, the cables are securely supported and managed using trays mounted to ceilings or walls. This setup is often used in industrial, commercial, or data center environments where floor space is limited, and efficient cable routing is essential. Overhead cabling trays help reduce clutter, improve accessibility, and protect the cables from potential damage.
Cable trays are generally more cost-effective than conduit systems due to their ease of installation and material efficiency. Conduit systems require more labor and materials to install, as each cable must be individually enclosed. In contrast, overhead cable trays allow multiple cables to be organized and supported in one structure, significantly reducing installation time and complexity. Additionally, cable trays are easier to maintain and modify, making them a more affordable option for long-term cable management. However, the cost comparison depends on the specific project and environment.
Wireways and cable trays differ in design, purpose, and application. Wireways are enclosed channels used to protect and route electrical wiring, often in smaller or less demanding installations. They are typically used for control and power cables where protection from environmental factors is required. Cable trays, on the other hand, are open or semi-enclosed structures designed to support and organize larger volumes of cables in industrial or commercial settings. Overhead cable tray systems are often used for managing power, data, and communication cables. While wireways prioritize protection, cable trays focus on flexibility and scalability.
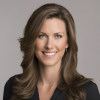
As the editor of GangLong Fiberglass, I have years of experience and in-depth research, focusing on cable tray products, fiberglass solutions, and grille systems. I incorporate years of industry insights and practical experience into every content, committed to promoting the progress of the industry. At GangLong Fiberglass, my commitment is reflected in every product, from innovative cable trays to durable fiberglass solutions and sturdy grille systems. As an authoritative voice in the industry, my goal is to provide valuable information to professionals and businesses and promote forward-looking solutions.