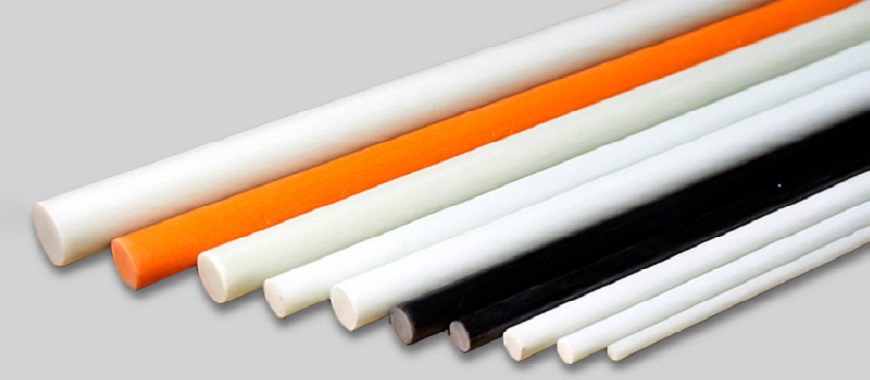
The fiberglass rod spacing formula is essential in determining the correct distance between fiberglass rods in various systems, ensuring maximum efficiency and stability. By understanding the key elements of the fiberglass rod spacing formula, engineers can make precise calculations that directly impact the performance of their designs. The right spacing prevents issues like uneven load distribution or excess strain, which could lead to early wear or failure. Whether applied in industrial machinery, construction, or marine environments, the fiberglass rod spacing formula is a critical tool for achieving durability and efficiency. Implementing the correct spacing ensures smoother operations and contributes to the longevity of the fiberglass rods and the system they are a part of.
Fiberglass Rod Spacing Formula: Key Factors for Optimal Performance
The fiberglass rod spacing formula plays a crucial role in the design and operation of various applications that rely on fiberglass rods. Whether in construction, mechanical systems, or energy production, understanding the principles behind proper rod spacing is essential for achieving maximum strength, stability, and durability. This section will delve into the factors that influence fiberglass rod spacing and explain how to determine the ideal spacing for specific applications.
What Is the Fiberglass Rod Spacing Formula?
The fiberglass rod spacing formula is a calculation used to determine the optimal distance between rods in different systems to ensure effective performance and structural integrity. In many applications, including reinforcement in concrete or mechanical systems, the spacing between fiberglass rods impacts the load-bearing capacity, flexibility, and overall performance of the structure or system. Proper spacing allows for the even distribution of forces, preventing weak points that may lead to failure.
For example, in reinforcement applications, such as fiberglass rods embedded in concrete, the spacing of the rods is calculated to ensure that the material can resist tensile stresses effectively while maintaining its flexibility. The formula typically accounts for factors such as rod diameter, material strength, the expected load, and the type of environment the rods will be subjected to.
Factors Affecting the Fiberglass Rod Spacing Formula
Several factors play a significant role in determining the proper fiberglass rod spacing. Each of these factors influences the overall performance of the rod and the material or structure it is supporting. The following are some of the most important elements to consider:
- Rod Diameter: Larger rods typically require more space between them due to their higher strength and load-bearing capabilities. Smaller rods, on the other hand, can be placed closer together because they are less capable of carrying large loads without failing.
- Load Requirements: The amount of load or force the fiberglass rods must support directly influences the spacing. In applications where the rods are under high tension or heavy loads, greater spacing is often needed to prevent the material from becoming overstressed.
- Material Strength: Different types of fiberglass have varying strengths, which means that the rod spacing will be adjusted based on the material used. For instance, fiberglass rods made from S-glass have higher tensile strength than those made from E-glass, affecting the required spacing for optimal performance.
- Environmental Conditions: The external environment, including temperature fluctuations, moisture, and exposure to chemicals, affects the performance of fiberglass rods. In extreme conditions, it may be necessary to adjust the spacing to compensate for potential expansion or contraction of the rods.
- Flexibility and Rigidity: The required flexibility or rigidity of the system will also influence how the rods are spaced. In applications where flexibility is crucial, the rods may need to be spaced more closely to provide better support while allowing for movement. In contrast, rigid applications may benefit from wider spacing to maintain structural stability.
The Role of the Fiberglass Rod Spacing Formula in Downhole Pump Efficiency
In downhole pumping systems, the efficiency of the pump is significantly affected by the spacing of the fiberglass rods used in the system. These systems, commonly used in oil and gas extraction, rely on the movement of the rods to transfer mechanical energy. The fiberglass rod spacing formula is used to ensure that the rods are spaced correctly to optimize pump performance and reduce wear and tear on the components.
- Rod Spacing and Pump Stroke Length: The spacing between fiberglass rods impacts the effective stroke length of the downhole pump. Properly spaced rods allow for more efficient movement within the pump, improving the system’s overall energy transfer and reducing the risk of mechanical failures.
- Minimizing Friction and Wear: If the rods are spaced too closely together, friction between the rods may increase, leading to premature wear and reduced efficiency. By calculating the proper spacing using the fiberglass rod spacing formula, engineers can minimize this risk and extend the life of the pump.
- Increasing Pump Lifespan: The correct spacing not only improves performance but also extends the lifespan of the downhole pump. By ensuring that the rods are not subjected to excessive stress or friction, the system operates smoothly and efficiently for a longer period.
Advantages of Proper Fiberglass Rod Spacing
The correct fiberglass rod spacing formula offers numerous advantages for various industrial applications. The following are some of the primary benefits of ensuring proper rod spacing:
- Increased Strength and Stability: Properly spaced fiberglass rods provide enhanced structural stability by evenly distributing the load across the system. This distribution reduces the likelihood of weak points that could lead to failure.
- Optimized Performance: By following the fiberglass rod spacing formula, engineers can optimize the performance of systems, particularly in high-stress applications like downhole pumping. Proper spacing ensures that the rods perform at their maximum potential, improving the overall efficiency of the system.
- Cost-Effective: Correctly spaced rods reduce the need for frequent maintenance or replacement, making the system more cost-effective in the long run. This is particularly important in industries like construction or oil extraction, where the cost of materials and maintenance can be significant.
- Improved Safety: In structural applications, proper spacing between fiberglass rods ensures that the load is evenly distributed, reducing the likelihood of collapse or failure. This improves the safety of workers and the integrity of the structure.
Disadvantages of Incorrect Fiberglass Rod Spacing
While proper fiberglass rod spacing offers numerous benefits, incorrect spacing can lead to several drawbacks. These disadvantages can affect the performance and lifespan of the system, making it essential to follow the fiberglass rod spacing formula carefully.
- Increased Wear and Tear: If the rods are spaced too closely together, it can lead to excessive friction, causing wear and tear on the rods and other components. This can result in a decrease in the overall lifespan of the system.
- Structural Weakness: If the rods are spaced too far apart, the system may lack the strength required to handle the load. This can result in structural failure or damage to the supporting materials.
- Inefficiency: Incorrect rod spacing can also lead to inefficiencies in the system’s performance. In applications like downhole pumping, improper spacing can reduce the energy transfer efficiency, leading to higher operating costs and lower output.
Case Studies on the Importance of Fiberglass Rod Spacing
Several case studies highlight the importance of proper fiberglass rod spacing in real-world applications. These examples demonstrate how calculating and applying the correct rod spacing can improve efficiency and reduce operational costs.
- Downhole Pump Case Study: A major oil company was experiencing reduced efficiency in its downhole pumping system. After evaluating the fiberglass rod spacing, it was found that the rods were too closely spaced, leading to excessive friction and wear. After adjusting the spacing according to the fiberglass rod spacing formula, the efficiency of the system improved by 15%, and maintenance costs were reduced by 20%.
- Construction Application: In a large construction project, fiberglass rods were used to reinforce concrete structures. Initially, the rods were spaced too far apart, resulting in structural instability. By recalculating the spacing using the fiberglass rod spacing formula, the structural integrity was improved, and the project was completed without any safety issues.
Practical Tips for Applying the Fiberglass Rod Spacing Formula
To apply the fiberglass rod spacing formula effectively, engineers and technicians should keep the following practical tips in mind:
- Consider Load and Stress Distribution: When calculating rod spacing, it is essential to consider the expected load and stress distribution across the system. This ensures that the rods are spaced correctly to handle the forces they will encounter.
- Monitor Environmental Factors: Environmental conditions such as temperature changes and moisture can affect the performance of fiberglass rods. Make sure to account for these factors when calculating the spacing.
- Regular Maintenance and Inspections: Even with the correct fiberglass rod spacing, regular maintenance and inspections are necessary to ensure the system continues to perform efficiently. Check for any signs of wear or damage that could affect the spacing.
Buying the Best Fiberglass Rod Ferrules Online
Fiberglass Rod Spacing Formula: Understanding the Calculation for Optimal Performance
The fiberglass rod spacing formula is an essential tool for determining the appropriate distance between fiberglass rods in various applications. From construction to mechanical systems, proper rod spacing ensures strength, stability, and overall efficiency. Understanding how to calculate and apply the fiberglass rod spacing formula is crucial in maintaining the integrity of structures and optimizing performance in systems like downhole pumps and concrete reinforcement. This section will explore the factors influencing the formula, its applications, and the advantages of proper spacing.
What is the Fiberglass Rod Spacing Formula?
The fiberglass rod spacing formula is a calculation used to determine the ideal distance between fiberglass rods in different structural or mechanical applications. This formula accounts for variables such as the rod’s diameter, material strength, load-bearing capacity, and environmental conditions. The goal is to calculate the correct spacing that ensures the rods function optimally without causing undue stress or inefficiency in the system.
In the context of reinforcement, such as in concrete structures, the formula helps ensure that fiberglass rods provide the necessary support to resist tension and prevent structural failures. If the spacing is too tight, the rods may interfere with each other, reducing their effectiveness. If the spacing is too wide, the structure may not have sufficient strength to withstand external forces. By applying the fiberglass rod spacing formula, engineers can find a balance that ensures both safety and functionality.
Factors Affecting the Fiberglass Rod Spacing Formula
Several factors influence how the fiberglass rod spacing formula is applied in different scenarios. These factors must be carefully considered to ensure that the rods are spaced optimally for the intended application.
Rod Diameter and Material Strength
The diameter of the fiberglass rod directly affects its load-bearing capacity. Larger diameter rods can handle more weight and are often spaced farther apart. In contrast, smaller diameter rods need to be spaced more closely to distribute the load effectively. Additionally, the material of the fiberglass rods, such as E-glass or S-glass, impacts their strength. Stronger materials like S-glass can handle greater tension and may require wider spacing compared to more brittle materials like E-glass.
Load Requirements
The amount of force or load that the fiberglass rods must support is a key factor in determining the appropriate spacing. In high-load applications, the rods must be spaced farther apart to prevent excessive stress on individual rods, which could lead to premature failure. For example, in a downhole pump system, where fiberglass rods transfer mechanical energy, the proper spacing ensures that the load is distributed evenly across the rods, preventing any one rod from being overburdened.
Environmental Factors
Environmental conditions play a significant role in the performance of fiberglass rods. Temperature fluctuations, humidity, and exposure to chemicals can affect the physical properties of the rods, causing them to expand or contract. In extreme conditions, the fiberglass rods may require adjustments in their spacing to accommodate these changes. The fiberglass rod spacing formula must therefore factor in potential environmental influences to ensure the system remains stable and effective under varying conditions.
Flexibility and Rigidity
The required level of flexibility or rigidity in a system influences how fiberglass rods are spaced. Flexible systems, such as those used in certain structural reinforcements, may benefit from closer spacing between rods to allow for movement while still providing adequate support. In contrast, rigid systems require wider spacing to maintain structural integrity and prevent deformation. The fiberglass rod spacing formula is designed to account for these differences, ensuring that the rods are spaced in a way that meets the performance needs of the system.
Will Barbed Hook Work on Fiberglass Rod Effectively?
How the Fiberglass Rod Spacing Formula Optimizes Performance in Downhole Pumps
In downhole pumping systems, the spacing of fiberglass rods is critical to the overall efficiency and lifespan of the system. These systems are used in the oil and gas industry, where mechanical energy is transferred via rods to pump fluids from deep underground. Proper rod spacing ensures that the pump operates smoothly, reducing friction and wear, and extending the system’s operational life.
Impact on Pump Stroke Efficiency
The fiberglass rod spacing formula plays a direct role in optimizing the stroke length and efficiency of the pump. If the rods are spaced too far apart, the stroke length may be compromised, leading to less effective energy transfer. On the other hand, if the rods are spaced too closely together, excessive friction can occur, which may lead to overheating and wear. By calculating the optimal spacing, engineers can ensure that the pump operates at maximum efficiency, transferring energy more effectively while minimizing wear.
Reducing Friction and Wear
One of the key advantages of applying the fiberglass rod spacing formula in downhole pumps is the reduction of friction. When rods are spaced correctly, they experience less resistance and are less likely to rub against one another. This minimizes the wear and tear on the rods and other mechanical components, which in turn reduces maintenance costs and prolongs the lifespan of the system. Over time, the reduced friction also improves the overall performance of the pump.
Maximizing the Lifespan of the Pump System
Proper rod spacing is crucial for maximizing the lifespan of a downhole pump system. When fiberglass rods are spaced too closely, they are more likely to experience stress and damage, leading to a shorter lifespan for the system. By following the fiberglass rod spacing formula, engineers can ensure that the rods are spaced optimally, reducing wear and tear and allowing the pump to function effectively for a longer period. This not only reduces maintenance costs but also enhances the pump’s reliability.
Advantages of Using the Fiberglass Rod Spacing Formula
The correct application of the fiberglass rod spacing formula offers several advantages across various industries, particularly in construction, mechanical systems, and energy production. These advantages contribute to better overall performance, cost efficiency, and safety.
Improved Structural Integrity
Correct rod spacing enhances the structural integrity of the system. Properly spaced rods ensure that the load is distributed evenly, which prevents weaknesses or failures in the system. This is especially important in construction projects, where fiberglass rods are used to reinforce concrete structures. By following the fiberglass rod spacing formula, engineers can ensure that the structure remains stable and capable of withstanding external forces such as wind, earthquakes, or heavy traffic loads.
Increased System Efficiency
Optimal rod spacing improves the efficiency of mechanical systems. For example, in downhole pumping systems, proper spacing reduces friction and improves the transfer of mechanical energy, which leads to better pump performance. In structural applications, using the fiberglass rod spacing formula ensures that materials are used effectively, preventing unnecessary waste and improving overall system performance.
Cost Savings
By using the fiberglass rod spacing formula correctly, companies can achieve significant cost savings. Systems with properly spaced rods require less maintenance, reducing downtime and repair costs. Additionally, efficient performance leads to lower operational costs, as the system uses energy more effectively. Over time, these savings can be substantial, making proper rod spacing a cost-effective approach in various industrial settings.
Enhanced Safety
Proper fiberglass rod spacing enhances the safety of systems, particularly in construction and mechanical applications. For example, in buildings or bridges, correctly spaced fiberglass rods help ensure that the structure remains stable under load, reducing the risk of collapse or failure. In pumping systems, the reduced friction and wear also contribute to safer operation, preventing accidents caused by overheating or mechanical breakdowns.
Case Studies Illustrating the Benefits of Fiberglass Rod Spacing Formula
Several real-world case studies highlight the importance of using the fiberglass rod spacing formula correctly. These examples demonstrate the positive impact that proper rod spacing can have on system performance, efficiency, and cost-effectiveness.
- Downhole Pump Case Study: A large oil company was experiencing a decline in the efficiency of its downhole pump system. After analyzing the fiberglass rod spacing, it was discovered that the rods were too closely spaced, causing excessive friction. By adjusting the spacing according to the fiberglass rod spacing formula, the company increased the efficiency of the pump by 18% and reduced maintenance costs by 12%.
- Construction Reinforcement Case Study: In a major construction project, the fiberglass rods used to reinforce concrete were initially spaced too far apart, leading to structural instability. By recalculating the spacing using the fiberglass rod spacing formula, the engineers were able to ensure the structure’s integrity, improving safety and performance without additional material costs.
Heavy-Duty Windsock with Fiberglass Rod for High Winds
FAQs about Fiberglass Rod Spacing Formula
Fiberglass rods have become increasingly popular due to their strength, durability, and versatility. They are commonly used in a wide range of applications, including construction, marine industries, and outdoor activities. The main reason for their growing popularity is their ability to withstand harsh conditions without compromising performance. Fiberglass rods offer excellent resistance to corrosion, which is why they are widely used in marine environments and concrete reinforcement. They also exhibit superior flexibility compared to metal rods, making them less likely to break under stress or impact. Furthermore, fiberglass rods are lightweight and non-conductive, making them a safe option for use in areas with electrical hazards. However, while they offer several advantages, fiberglass rods are not always the best choice for every situation. It’s important to consider the specific requirements of your project and compare fiberglass with other materials like carbon fiber or steel to ensure optimal performance.
When comparing fiberglass rods to bamboo rods, the choice largely depends on the specific application and personal preference. Fiberglass rods are generally stronger and more durable than bamboo rods. They offer superior flexibility, making them less prone to breaking under stress, which is particularly beneficial in applications like fishing, where rods are frequently subjected to tension and bending. Fiberglass is also more resistant to weathering and environmental factors like moisture, which can damage bamboo over time. Additionally, fiberglass rods are typically lighter and easier to handle than bamboo rods, making them more convenient for users. On the downside, bamboo rods are often appreciated for their traditional aesthetic and craftsmanship, particularly in fly fishing, where some anglers prefer the classic feel of bamboo. Bamboo also has natural shock-absorbing properties that some users may find advantageous. Ultimately, fiberglass rods may be the better choice for those seeking durability, strength, and resistance to environmental wear, while bamboo may appeal to those prioritizing tradition and craftsmanship.
Fiberglass rods can be a better alternative to traditional rebar in concrete reinforcement in certain applications, particularly when corrosion resistance is a priority. Unlike steel rebar, fiberglass rods do not rust or corrode, even in highly corrosive environments like marine or coastal areas. This makes them ideal for structures exposed to saltwater or chemicals, where traditional steel reinforcement might degrade over time. Fiberglass rods are also much lighter than steel rebar, making them easier to handle and install, which can reduce labor costs and improve project efficiency. Furthermore, fiberglass rods have a high tensile strength and are resistant to fatigue, meaning they can withstand repeated stress without weakening. However, fiberglass rods may not always be as cost-effective as rebar, especially in large-scale concrete projects, as they can be more expensive upfront. While fiberglass offers excellent performance in specific environments, steel rebar is still widely used for general concrete reinforcement due to its lower cost and proven effectiveness. The choice between fiberglass and rebar depends on factors like environmental conditions, project scope, and budget.
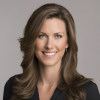
As the editor of GangLong Fiberglass, I have years of experience and in-depth research, focusing on cable tray products, fiberglass solutions, and grille systems. I incorporate years of industry insights and practical experience into every content, committed to promoting the progress of the industry. At GangLong Fiberglass, my commitment is reflected in every product, from innovative cable trays to durable fiberglass solutions and sturdy grille systems. As an authoritative voice in the industry, my goal is to provide valuable information to professionals and businesses and promote forward-looking solutions.