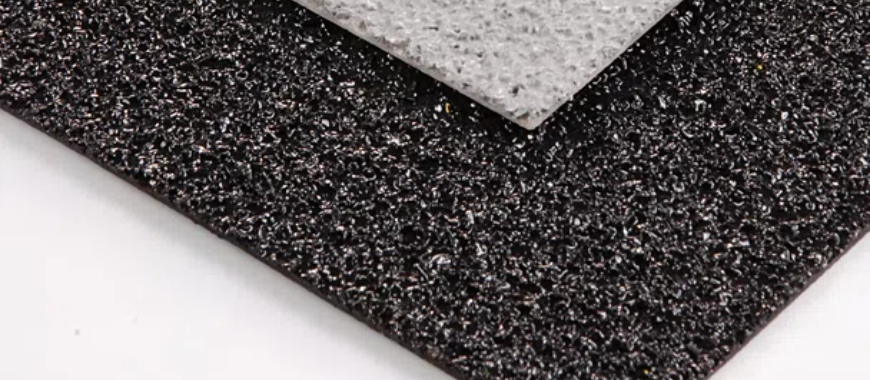
Fiberglass reinforced plastic (FRP) panels are a popular choice for various construction and industrial applications due to their strength, durability, and versatility. These panels are made by embedding fiberglass strands into a plastic matrix, offering enhanced resistance to impact, corrosion, and weathering. The fiberglass reinforced plastic panel 12 feet in length is particularly ideal for roofing and wall applications, as it provides sufficient coverage with fewer seams, reducing the potential for leaks. Compared to other materials like polycarbonate and corrugated plastic, FRP panels offer superior strength-to-weight ratios and better longevity, making them a cost-effective and reliable solution for both residential and commercial structures.
Types of 12-Foot Fiberglass Reinforced Plastic Panel 12 Feet
Fiberglass reinforced plastic panel 12 feet come in various types, each offering unique benefits depending on the intended application. These panels are designed to meet the specific needs of construction, industrial, and residential projects, offering a range of durability, weather resistance, and aesthetic appeal.
Fiberglass Reinforced Plastic Panel 12 Feet and Fiberglass Roof Panels 12-Foot: Durable and Weather-Resistant Options for Roofing Projects
Fiberglass roof panels 12-foot are highly valued for their robustness and resistance to harsh weather conditions. These panels are designed to withstand extreme temperatures, UV exposure, and heavy rainfall, making them ideal for roofing applications. The fiberglass construction ensures excellent strength-to-weight ratio, allowing for easy installation without sacrificing performance. These panels are also known for their long lifespan, requiring minimal maintenance while providing effective protection against leaks and corrosion over time.
Corrugated Plastic Roof Panels 12 Foot: Lightweight and Cost-Effective Solutions
For projects where affordability and ease of installation are paramount, corrugated plastic roof panels 12 foot provide an excellent option. These panels are lightweight yet strong, offering quick and easy installation without the need for heavy equipment. Their corrugated structure enhances their strength and durability, making them ideal for smaller projects or temporary roofing solutions. While they may not offer the same long-term durability as fiberglass options, corrugated plastic panels are a cost-effective choice for applications where budget is a primary consideration.
White Corrugated Fiberglass Panels: Ideal for Clean, Modern Aesthetics and UV Protection
White corrugated fiberglass panels are an ideal choice for those seeking a clean and modern look while ensuring effective UV protection. These panels offer the same durability and weather resistance as traditional fiberglass options but with an added aesthetic benefit. The white finish provides a bright, sleek appearance that can enhance the visual appeal of any structure. Additionally, the fiberglass reinforced plastic panel 12 feet in white offers superior UV protection, helping to reduce the potential for discoloration and deterioration caused by prolonged sun exposure.
Enhance Comfort with Fiberglass Insulation Ceiling Tiles
Benefits of Fiberglass Reinforced Plastic Panel 12 Feet
Fiberglass reinforced plastic panel 12 feet offers a wide range of benefits that make it a preferred choice for roofing applications. These panels are known for their resilience, durability, and long-term performance, providing significant advantages over traditional roofing materials. Below are the key benefits of using fiberglass roof panels.
High Impact and Weather Resistance
Fiberglass roof panels are engineered to resist both physical impacts and harsh weather conditions. Whether exposed to heavy winds, hail, or snow, these panels maintain their structural integrity. The robust fiberglass construction ensures that they won’t easily crack or break, even under pressure. Additionally, the panels are highly resistant to moisture, which helps to prevent water damage and mold growth, making them ideal for areas with unpredictable weather.
Superior Durability Compared to Traditional Materials
Fiberglass reinforced plastic panel 12 feet offers superior durability when compared to traditional roofing materials like asphalt shingles, wood, or metal panels. These fiberglass panels are less prone to wear and tear, ensuring a longer lifespan without frequent repairs or replacements. The material’s inherent strength allows it to withstand constant exposure to the elements, reducing the need for ongoing maintenance. Below is a table comparing the durability of fiberglass roof panels with other common roofing materials:
Material | Durability | Maintenance Needs |
---|---|---|
Fiberglass Reinforced Plastic Panel 12 Feet | High (resistant to impact, corrosion, and UV degradation) | Low (minimal maintenance) |
Asphalt Shingles | Moderate (prone to wear, cracking, and damage) | High (requires frequent repairs) |
Wood Shingles | Low (susceptible to rot, mold, and decay) | High (requires regular treatment) |
Metal Panels | High (resistant to rust but may dent) | Moderate (periodic inspection and cleaning) |
UV Protection for Long-Term Performance
Fiberglass roof panels are highly effective at blocking harmful UV rays, which can degrade other materials over time. The fiberglass reinforced plastic panel 12 feet is designed to resist UV radiation, preventing the panels from becoming brittle, discolored, or weak. This UV protection extends the lifespan of the roofing material, ensuring long-term performance without significant degradation. In addition, this protection also helps maintain the appearance of the panels, keeping them looking new for years.
Minimal Maintenance Requirements
One of the standout benefits of fiberglass roof panels is their minimal maintenance requirements. Unlike other roofing materials that may need regular repairs or cleaning, fiberglass panels are easy to maintain and keep in good condition. They are resistant to mold, mildew, and algae growth, reducing the need for frequent cleaning. Additionally, their weather-resistant properties prevent rust or corrosion, ensuring that the panels remain intact and functional for a long time with little effort required from the homeowner or contractor.
Best Spray Options for Fiberglass Insulation Adhesive
Applications of Fiberglass Reinforced Plastic Panel 12 Feet
Fiberglass reinforced plastic panel 12 feet is an incredibly versatile material, suitable for a wide range of applications across residential, commercial, and industrial settings. Its strength, durability, and resistance to various environmental factors make it an excellent choice for a variety of construction and design projects. Below are some key applications for these panels in different sectors.
Residential Uses: Sheds, Patios, and Greenhouses
In residential settings, fiberglass reinforced plastic panel 12 feet is commonly used in the construction of sheds, patios, and greenhouses. Its ability to withstand harsh weather conditions makes it ideal for outdoor structures. For sheds and patios, these panels provide reliable protection from rain, snow, and UV rays while maintaining an aesthetic appeal. In greenhouses, the panels allow natural light to penetrate, promoting plant growth, while also offering protection from the harmful effects of UV radiation. The panels are also lightweight, making them easy to install and handle, which is particularly useful in DIY residential projects.
Commercial Projects: Kitchens, Restrooms, and Interior Cladding
Fiberglass reinforced plastic panel 12 feet is increasingly used in commercial applications, especially in environments that require clean, durable surfaces. In commercial kitchens, these panels are ideal for creating hygienic, easy-to-clean wall coverings. They are resistant to staining, mold, and mildew, which are common concerns in such settings. Similarly, in restrooms, the panels provide a durable and low-maintenance solution for wall and ceiling cladding, with the added benefit of moisture resistance. FRP panels are also used in interior cladding for commercial buildings, offering a modern aesthetic with the added benefits of sound insulation and easy maintenance.
Industrial Settings: Chemical-Resistant Walling and Moisture-Prone Areas
In industrial settings, fiberglass reinforced plastic panel 12 feet is highly valued for its chemical resistance and ability to withstand harsh conditions. These panels are used for walling in factories, laboratories, and warehouses where exposure to chemicals or moisture is a concern. The panels’ resistance to corrosion and ability to handle exposure to acids, oils, and solvents make them an ideal choice for environments where other materials might degrade quickly. Additionally, in areas prone to high humidity, such as food processing plants or manufacturing facilities, the moisture-resistant properties of these panels help prevent mold and mildew growth, ensuring a safer and more hygienic workspace.
What Is Double Faced Fiberglass Insulation Used For?
Installation Tips for Fiberglass Reinforced Plastic Panel 12 Feet
Installing fiberglass reinforced plastic panel 12 feet for roofing applications requires careful planning and the right tools to ensure a smooth and effective process. By following the right steps and using the appropriate materials, you can achieve a durable and long-lasting roof. Below are some essential installation tips that can help you maximize the benefits of fiberglass roof panels.
Tools and Adhesives Needed for Easy Installation
To install fiberglass reinforced plastic panel 12 feet effectively, having the right tools is essential. Here’s a list of tools and materials you will need for a successful installation:
- Measuring tape: Accurate measurements are essential to ensure the correct alignment of panels.
- Circular saw: A circular saw with a fine-tooth blade is necessary for cutting fiberglass panels without causing damage.
- Drill with a set of masonry or wood bits: Drilling holes for fasteners or screws is necessary for securing the panels to the framework.
- Screws or nails: Use corrosion-resistant screws or nails that are suitable for outdoor applications.
- Adhesive: A strong, weather-resistant adhesive is necessary to bond the panels to the roofing structure, particularly in areas where extra adhesion is required.
- Rubber gaskets: These are used with screws to ensure a tight, water-resistant seal.
By ensuring you have these tools and materials ready before beginning installation, you can complete the job more efficiently and with less risk of damaging the panels.
Tips for Installing Corrugated Panels for Optimal Strength
When installing fiberglass reinforced plastic panel 12 feet in a corrugated design, it’s important to follow specific techniques to optimize the strength and durability of the roof. Here are a few installation tips:
- Align the panels properly: Ensure the corrugated panels are aligned in the correct direction (usually with the ridges running parallel to the slope of the roof). This enhances the strength and drainage capacity of the roof.
- Overlapping seams: When laying multiple panels, make sure to overlap the seams by at least one or two corrugations to prevent water from seeping through. This is crucial for weatherproofing.
- Use appropriate fasteners: Fasteners should be placed in the crests of the corrugations, not in the troughs, to ensure a secure fit and prevent potential leaks. Make sure each fastener is tightly secured, but be careful not to overtighten, as this can damage the fiberglass.
- Install in the correct weather: For optimal installation, avoid doing it in extreme temperatures (either too hot or too cold), as fiberglass panels can become brittle or difficult to work with in such conditions. Installing on a dry day also ensures proper adhesive bonding.
By following these tips, you can ensure that the corrugated panels provide the maximum strength and long-term durability.
Maintaining Panels for Maximum Durability
Proper maintenance of fiberglass reinforced plastic panel 12 feet is essential to ensure its long-lasting performance. Here are some tips for maintaining your panels:
- Regular cleaning: Fiberglass panels can accumulate dirt, debris, and algae, so it’s important to clean them regularly with a soft brush or cloth. Use a mild detergent and water solution to avoid damaging the surface. Avoid abrasive cleaners that could scratch the panels.
- Inspect for damage: Periodically check for cracks or chips, especially after extreme weather events. If any damage is found, seal the cracks with a suitable repair adhesive or patch kit to prevent further deterioration.
- Check fasteners and seals: Over time, the screws or nails used to fasten the panels may loosen. Inspect the fasteners regularly and tighten or replace them if necessary. Additionally, check the rubber gaskets around the fasteners to ensure they remain intact and watertight.
- Protect from UV damage: Although fiberglass panels are UV-resistant, prolonged exposure to intense sunlight can cause gradual wear. If you live in a region with extreme sun exposure, consider applying a UV-resistant coating to prolong the life of the panels.
By following these maintenance tips, you can help extend the lifespan of your fiberglass reinforced plastic panel 12 feet, ensuring it continues to protect your structure for many years.
Why Choose Fiberglass Reinforced Plastic Panel 12 Feet
White corrugated fiberglass reinforced plastic panel 12 feet is becoming an increasingly popular choice for various construction projects due to its combination of aesthetic appeal, functional benefits, and long-lasting durability. These panels are specifically designed to offer both visual and performance advantages that make them ideal for modern buildings, industrial settings, and residential applications. Below are the main reasons why you should consider using white corrugated fiberglass panels for your next project.
Aesthetic Appeal for Modern and Clean Designs
One of the primary reasons for choosing white corrugated fiberglass panels is their sleek and modern appearance. The clean, bright finish of these panels adds a contemporary touch to any building or structure. The white color complements various architectural styles, making it ideal for both residential and commercial applications where aesthetics are a priority. Whether you’re using them for roofing, wall cladding, or even greenhouse installations, the visual appeal of white corrugated fiberglass panels elevates the overall design, offering a neat and polished look that blends well with any environment. Furthermore, the reflective surface of these panels can help create a clean and bright atmosphere indoors, enhancing the overall lighting in the space.
Heat-Reflective Properties to Keep Interiors Cool
Another significant advantage of using fiberglass reinforced plastic panel 12 feet in white is its heat-reflective properties. The white finish helps to reflect sunlight, significantly reducing the amount of heat absorbed by the structure. This makes it particularly useful in climates with high temperatures or areas with prolonged sun exposure. By reflecting heat away, these panels help to keep the interior of buildings cooler, reducing the need for artificial cooling systems and improving energy efficiency. This can lead to lower energy costs over time and a more comfortable indoor environment, especially in buildings like greenhouses, sheds, or warehouses that might be subjected to high thermal loads.
Long-Lasting and Versatile for Multiple Applications
White corrugated fiberglass reinforced plastic panel 12 feet is also highly durable and versatile, making it suitable for a wide range of applications. The combination of fiberglass and plastic ensures that these panels are resistant to cracking, warping, or breaking under harsh conditions. Their resistance to moisture, chemicals, and UV radiation ensures they maintain their strength and appearance for many years, even in demanding environments. Whether you’re using them for residential sheds, patios, commercial kitchens, or industrial facilities, these panels can withstand various conditions without the need for frequent repairs or replacements.
The long-lasting nature of these panels also makes them a cost-effective solution, as they require minimal maintenance and have a longer lifespan compared to other materials like wood, metal, or traditional plastic panels. Their versatility allows them to be used in a variety of settings, from roofing and wall cladding to agricultural structures, making them a reliable investment for any construction project.
By choosing white corrugated fiberglass reinforced plastic panel 12 feet, you are opting for a durable, attractive, and highly functional material that provides both aesthetic and practical benefits for a wide array of applications.
FAQs about Fiberglass Reinforced Plastic Panel 12 Feet
Fiberglass Reinforced Plastic (FRP) panels are available in various lengths to suit a wide range of construction and industrial applications. The most common lengths for FRP panels are typically between 8 feet and 12 feet, with 12-foot panels being especially popular due to their ease of use for larger roofing and wall projects. However, FRP panels can also be custom-cut or purchased in longer lengths depending on specific project requirements. For example, panels as long as 20 feet or more are available for applications like large industrial roofs or exterior wall cladding, which require minimal seams for better protection against weather elements. When selecting the appropriate length for your project, it’s important to consider the total area you need to cover, as well as the ease of handling and transport of the panels. Standard 12-foot panels are often preferred for their balance between coverage and practicality, reducing installation time while still being manageable for most installation teams.
While Fiberglass Reinforced Plastic (FRP) panels offer excellent durability and resistance, there are several more affordable alternatives available, depending on the intended application. One common and cheaper alternative to FRP is polycarbonate panels, which are often used in roofing and greenhouse construction. Polycarbonate offers some similar benefits, including UV protection and lightweight properties, at a lower cost. Another option is corrugated plastic panels, which are typically used for lighter-duty applications like sheds and small roofing projects. These panels are less durable than FRP and may not offer the same chemical and weather resistance, but they are a more budget-friendly option for simpler, short-term needs. PVC panels are also an alternative, offering a lower-cost solution for applications requiring moderate impact resistance. Although these materials may not provide the same long-term durability or strength as FRP, they can still serve well for certain applications, especially where budget constraints are a primary concern.
While Fiberglass Reinforced Plastic (FRP) panels offer numerous benefits, such as durability, weather resistance, and low maintenance, they are not without their disadvantages. One of the primary drawbacks is their higher initial cost compared to other materials like PVC or corrugated plastic panels. This can make them less appealing for projects with tight budgets. Another disadvantage is that FRP panels can be difficult to repair if damaged. While they are tough and resistant to many types of damage, cracks or punctures require specialized repair kits or the replacement of entire panels, which can add to maintenance costs. Additionally, FRP can be prone to UV degradation over time if the protective coating wears off, leading to a loss of strength and discoloration. Finally, although FRP panels are lightweight, they can be tricky to handle during installation due to their size, particularly for larger panels, requiring extra care to avoid cracks or breakage. In certain industrial applications, fire resistance can also be a concern as FRP is flammable unless treated with fire-retardant coatings.
Although Fiber Reinforced Plastic (FRP) and fiberglass are closely related, they are not exactly the same. Fiberglass refers specifically to the fiber material itself, which is made from glass fibers that provide strength and flexibility. Fiber Reinforced Plastic (FRP), on the other hand, is a composite material made by combining fiberglass with a plastic resin, typically polyester or epoxy, to create a strong, durable product. This composite material offers enhanced properties, such as resistance to corrosion, impact, and weathering, making it more suitable for various applications, including in construction, automotive, and industrial settings. In summary, fiberglass is a key component of FRP, but the two terms refer to different stages of the material’s composition. Fiberglass provides the reinforcing fiber, while FRP is the final, finished composite product that combines those fibers with plastic for increased functionality. Therefore, while the terms are often used interchangeably, FRP is a broader term encompassing multiple composite materials, of which fiberglass is a part.
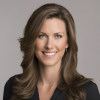
As the editor of GangLong Fiberglass, I have years of experience and in-depth research, focusing on cable tray products, fiberglass solutions, and grille systems. I incorporate years of industry insights and practical experience into every content, committed to promoting the progress of the industry. At GangLong Fiberglass, my commitment is reflected in every product, from innovative cable trays to durable fiberglass solutions and sturdy grille systems. As an authoritative voice in the industry, my goal is to provide valuable information to professionals and businesses and promote forward-looking solutions.