
Fiberglass reinforced plastic particles (FRP) are a composite material formed by embedding fiberglass into plastic. The fiberglass fibers, often made from glass, carbon, or aramid, significantly enhance the mechanical properties of plastic, contributing to increased strength, durability, and flexibility. These fiberglass reinforced plastic particles act as reinforcement, providing structural integrity and resistance to impact, moisture, and temperature changes. The glass fibers, in particular, are known for their high tensile strength and lightweight nature, making them ideal for use in various industries. The inclusion of fiberglass particles improves the overall performance of plastic materials, making them more suitable for demanding applications, such as automotive, construction, and aerospace manufacturing. These particles are crucial in elevating the material’s resistance to wear and tear, while also allowing it to maintain a high level of flexibility without compromising on strength.
Composition and Manufacturing of Fiberglass Reinforced Plastic Particles
Fibers and Polymers
Fiberglass reinforced plastic particles are created by combining fibers such as glass fiber, carbon fiber, and aramid fiber with various types of polymers. Glass fiber is the most common material used in FRP due to its excellent tensile strength, resistance to high temperatures, and low weight. Carbon fibers, while more expensive, offer superior strength and stiffness, making them ideal for applications that demand high performance. Aramid fibers, known for their impact resistance and flexibility, are also used in certain specialized FRP products.
The polymers that bind these fibers together play a crucial role in the properties of fiberglass reinforced plastic particles. Common polymers include epoxy, polyester, and vinyl ester. Epoxy resins provide exceptional adhesion and chemical resistance, while polyester resins are favored for their cost-effectiveness and ease of processing. Vinyl ester resins, a hybrid of epoxy and polyester, offer improved resistance to corrosion and are often used in demanding environments.
Particle Creation
The process of creating fiberglass reinforced plastic particles involves several steps to break down and prepare the raw fiberglass materials. Initially, the fiberglass is processed through techniques like grinding, chopping, or milling. These methods reduce the glass fibers into fine particles or short strands, which are then mixed with the polymer matrix. The size and shape of the particles are critical, as they directly influence the final product’s performance and properties, including its strength, flexibility, and durability.
Grinding involves using mechanical force to break the fiberglass into small particles, while milling uses rotary tools to cut the material into uniform sizes. Both methods allow for precise control over the dimensions of the fiberglass particles, ensuring consistency in the final composite material.
Combining Fiber and Plastic
Once the fiberglass particles are prepared, they are combined with polymer resins during the molding or extrusion process. Molding involves shaping the mixture into specific forms, often under heat and pressure, allowing the polymer to fully bond with the fiberglass particles. This process creates a solid, durable composite material that is ideal for a range of applications, from automotive parts to construction materials.
In extrusion, the polymer and fiberglass mixture is forced through a mold, where it solidifies into continuous shapes, such as sheets, tubes, or profiles. Both techniques ensure that the fiberglass particles are evenly distributed throughout the plastic matrix, maximizing the performance of the final product. The combination of fiberglass and polymer results in a material that is both lightweight and strong, with excellent resistance to environmental factors such as UV radiation and moisture.
What Is Double Faced Fiberglass Insulation Used For?
Benefits of Fiberglass Reinforced Plastic Particles
Fiberglass reinforced plastic particles offer numerous advantages that make them a popular choice in various industries. By integrating fiberglass into plastic, these particles significantly enhance the performance and functionality of the base material. The combination of fiberglass and plastic results in a composite that is not only more durable but also more versatile in its applications.
Enhanced Strength
Fiberglass reinforced plastic particles contribute to increased tensile and impact strength, making the composite material highly resistant to breakage and deformation under stress. The glass fibers within the particles provide excellent reinforcement, improving the ability of the plastic to withstand heavy loads and mechanical stresses. This enhanced strength is especially beneficial in industries like automotive, aerospace, and construction, where materials must endure extreme conditions without compromising on structural integrity.
Improved Durability
Fiberglass reinforced plastic particles also enhance the durability of plastics, providing resistance to wear, corrosion, and high-impact forces. The presence of fiberglass prevents the plastic from degrading quickly under harsh environmental conditions, such as exposure to chemicals, moisture, or UV radiation. This increased durability extends the lifespan of products made with FRP, reducing the need for frequent repairs or replacements. In marine and outdoor applications, where materials are subjected to saltwater and temperature fluctuations, fiberglass-reinforced plastic particles offer long-term reliability and performance.
Lightweight yet Strong
One of the standout features of fiberglass reinforced plastic particles is the balance they strike between strength and weight. The addition of fiberglass allows plastic to retain its lightweight properties while gaining significantly in terms of strength and rigidity. This makes FRP an ideal material for use in industries where both lightweight and strength are essential, such as automotive, aerospace, and marine. For example, in the automotive industry, the use of FRP can reduce vehicle weight, contributing to better fuel efficiency without sacrificing safety or durability. Similarly, in aerospace and marine applications, the strength-to-weight ratio of fiberglass-reinforced plastic particles is crucial for maintaining performance while keeping overall weight to a minimum.
Additional Benefits of Fiberglass Reinforced Plastic Particles
- Resistance to Environmental Factors: FRP particles offer excellent resistance to temperature extremes, humidity, and chemical exposure, making them suitable for challenging environments.
- Improved Moldability: The process of integrating fiberglass particles with polymers allows for easy molding into complex shapes, which is valuable for producing custom parts and components.
- Cost-Effectiveness: While fiberglass-reinforced plastic materials are generally more expensive than standard plastics, their superior performance and durability can reduce long-term maintenance costs and increase the value of the finished product.
These benefits highlight why fiberglass reinforced plastic particles are a preferred choice for applications demanding high performance, longevity, and versatility.
Fiberglass Electrical Insulation for Industrial and Home Use
Common Applications of Fiberglass Reinforced Plastic Particles
Fiberglass reinforced plastic particles are widely used in various industries due to their unique combination of strength, durability, and lightweight properties. These particles are integral to the creation of high-performance composite materials that are utilized in applications ranging from automotive manufacturing to aerospace, construction, and sports equipment. Below are some of the most common and impactful applications of fiberglass reinforced plastic particles.
Automotive Industry
In the automotive industry, fiberglass reinforced plastic particles play a crucial role in the production of lightweight and durable parts for vehicles. The integration of fiberglass with plastic allows for the manufacturing of components such as bumpers, panels, fenders, and interior parts that require both strength and reduced weight. Using FRP materials helps automakers meet stringent fuel efficiency standards by reducing the overall weight of vehicles, while still providing the necessary impact resistance and structural integrity. The lightweight nature of fiberglass reinforced plastic particles also helps improve the vehicle’s performance, fuel economy, and handling, making it a key material for modern vehicles.
Aerospace and Marine
The aerospace and marine industries also benefit from the use of fiberglass reinforced plastic particles. In aerospace, the demand for lightweight materials that do not compromise on strength is critical. Fiberglass reinforced plastic particles are used in aircraft components, including wings, fuselage panels, and tail sections, to reduce weight and improve fuel efficiency. FRP composites also offer high resistance to temperature fluctuations, moisture, and corrosion, making them ideal for aerospace applications that operate under harsh environmental conditions.
Similarly, in the marine industry, FRP is used in the construction of boats, ships, and other watercraft. The use of fiberglass reinforced plastic particles in boat hulls, decks, and structural components ensures durability, impact resistance, and long-lasting performance in challenging marine environments. The reduced weight of these composites also enhances fuel efficiency and overall performance, while maintaining the required strength and integrity in harsh, saltwater conditions.
Construction and Infrastructure
Fiberglass reinforced plastic particles are widely utilized in the construction and infrastructure sectors, particularly in applications where corrosion resistance and strength are required. FRP materials are used in the production of panels, reinforcements, pipes, and structural components for buildings, bridges, and industrial plants. In environments prone to chemical exposure, moisture, or high levels of humidity, such as wastewater treatment plants or chemical processing facilities, fiberglass reinforced plastic particles provide an effective solution. These materials are resistant to corrosion from chemicals, salts, and moisture, significantly extending the lifespan of infrastructure and reducing maintenance costs.
Additionally, FRP is used in the construction of lightweight panels for exterior cladding, ceilings, and partitions. Its ability to withstand extreme weather conditions and provide excellent thermal and acoustic insulation makes it an ideal material for modern construction projects.
Sports Equipment
In the sports equipment industry, fiberglass reinforced plastic particles are used to manufacture high-performance composite materials for various types of gear. The strength and flexibility provided by fiberglass make it ideal for products such as bicycles, skis, snowboards, tennis rackets, and golf clubs. The lightweight properties of FRP allow athletes to use equipment that is both strong and easy to handle, enhancing their performance.
For example, in cycling, the use of fiberglass reinforced plastic particles in bike frames and wheels offers improved strength and durability while reducing weight. This makes bikes faster and more maneuverable, without sacrificing performance or safety. Similarly, in the production of sports gear, such as racquets or clubs, FRP materials contribute to enhanced power, control, and durability, making them favored by professional athletes and enthusiasts alike.
These examples illustrate how fiberglass reinforced plastic particles are transforming industries by offering a balance of strength, lightness, and durability, which are critical in various demanding applications.
Top Uses of Fiberglass Insulation Strips in Construction
Types of Fiberglass Reinforced Plastic Particles
Fiber reinforced plastics (FRP) come in various forms, each with its own distinct properties and applications. The incorporation of fiberglass reinforced plastic particles into these composites enhances their performance in terms of strength, durability, and weight. Below are the most common types of FRP, each characterized by the type of fiber used in the composite material.
Glass Fiber Reinforced Plastic (GFRP)
Glass fiber reinforced plastic (GFRP) is one of the most widely used types of FRP, primarily due to its excellent combination of strength, weight, and cost-effectiveness. GFRP is made by embedding glass fibers into a polymer matrix, typically using resins such as epoxy, polyester, or vinyl ester. The fiberglass reinforced plastic particles in GFRP contribute significantly to the composite’s high tensile strength and impact resistance, making it suitable for a wide range of applications.
Properties and Benefits of GFRP
- Lightweight: GFRP offers a favorable strength-to-weight ratio, making it ideal for applications where weight reduction is critical without compromising strength.
- Corrosion Resistance: The inclusion of glass fibers in the polymer matrix makes GFRP resistant to corrosion, making it especially useful in harsh environments such as marine and industrial applications.
- Durability: GFRP is highly durable and has a long lifespan, even under extreme conditions. It resists wear, weathering, and chemical exposure.
- Cost-Effectiveness: Compared to other fiber-reinforced composites like carbon fiber, GFRP is more affordable, making it an attractive choice for many industries.
Common Uses of GFRP
GFRP is used in a wide range of applications, including:
- Automotive parts such as bumpers, fenders, and door panels.
- Marine components like boat hulls, decks, and structural reinforcements.
- Construction materials such as reinforced panels, pipes, and rebar.
- Consumer goods like sports equipment and electronics casings.
Carbon Fiber Reinforced Plastic (CFRP)
Carbon fiber reinforced plastic (CFRP) is a high-performance composite known for its exceptional strength-to-weight ratio. Unlike GFRP, which uses glass fibers, CFRP incorporates carbon fibers, which are stronger and lighter but more expensive. The addition of carbon fibers to the polymer matrix provides superior mechanical properties, making CFRP ideal for advanced applications where both strength and low weight are crucial.
Differences Between GFRP and CFRP
While both GFRP and CFRP are fiber reinforced plastics, there are key differences between the two:
- Strength-to-Weight Ratio: CFRP has a much higher strength-to-weight ratio than GFRP. This makes it more suitable for applications where maximum performance is required without adding unnecessary weight.
- Cost: CFRP is significantly more expensive than GFRP, which limits its use to industries where its superior properties justify the higher cost.
- Stiffness and Durability: CFRP is stiffer than GFRP, making it more suitable for high-stress applications like aerospace and motorsports. It also has superior fatigue resistance and can handle higher impact forces without failing.
Common Uses of CFRP
CFRP is commonly used in industries where performance and lightweight properties are paramount:
- Aerospace applications such as aircraft fuselages, wings, and landing gear.
- Automotive components, especially in high-performance vehicles, like sports cars and racing cars.
- Sports equipment, including bicycles, tennis rackets, and golf clubs.
- Medical devices and tools that require lightweight and high-strength materials.
Other Fiber Reinforced Composites
In addition to GFRP and CFRP, other fiber reinforced plastic composites are used in specialized applications. These materials incorporate fibers such as aramid (Kevlar), basalt, and natural fibers into the polymer matrix, each offering unique characteristics suited to particular needs.
Aramid Fiber Reinforced Plastics (Kevlar)
Aramid fibers, most commonly known by the brand name Kevlar, are high-strength, lightweight fibers with excellent resistance to abrasion and impact. These fibers are used in applications that require exceptional toughness and protection. Aramid fiber reinforced plastics are often used in:
- Ballistic protection (e.g., bulletproof vests).
- Protective clothing and gloves.
- Aerospace components where high impact resistance is essential.
Basalt Fiber Reinforced Plastics
Basalt fibers are derived from volcanic rock and offer properties similar to glass fibers but with added benefits in terms of thermal stability and resistance to harsh environmental conditions. Basalt fiber reinforced plastics are used in:
- High-temperature applications where traditional glass fibers may not perform well.
- Electrical insulation components.
- Construction materials in areas with high humidity or extreme temperatures.
Natural Fiber Reinforced Plastics
In addition to synthetic fibers like glass and carbon, there is growing interest in using natural fibers such as hemp, flax, and jute in fiber reinforced plastics. These natural fiber composites offer environmental benefits due to their renewable nature and biodegradability. They are often used in:
- Automotive components as a sustainable alternative to traditional plastics.
- Packaging materials.
- Eco-friendly construction products.
These various types of fiber reinforced plastics, including those with fiberglass reinforced plastic particles, offer distinct advantages based on the fibers used, and each type is selected based on the specific demands of the application. Whether for lightweight strength, durability, impact resistance, or cost-efficiency, the right choice of fiber can significantly enhance the performance of the final composite material.
Challenges and Considerations in Using Fiberglass Reinforced Plastic Particles
While fiberglass reinforced plastic particles (FRP) offer a wide range of benefits in terms of strength, durability, and versatility, there are several challenges and considerations that need to be addressed when using these materials. These challenges span across production costs, environmental concerns, and material compatibility, and must be carefully managed to maximize the potential of FRP composites.
Cost and Production
One of the most significant challenges in using fiberglass reinforced plastic particles is the relatively high cost of production. The production of FRP materials typically involves the combination of high-quality fibers with expensive resin systems, which can drive up material costs. The process of manufacturing these composites often requires specialized equipment and skilled labor, further adding to the expense. Additionally, the scaling of production to meet high-volume demands can be challenging due to the complexity of the manufacturing process, including the precision needed to incorporate fiberglass particles evenly into the polymer matrix.
To overcome these challenges, manufacturers are exploring more efficient production techniques, such as automated processes and advances in resin formulations, which could help reduce costs while maintaining performance. However, the cost of fiberglass reinforced plastic particles remains a barrier to widespread adoption in certain industries, particularly those that are highly cost-sensitive.
Recycling and Disposal
Another significant concern surrounding the use of fiberglass reinforced plastic particles is the environmental impact associated with recycling and disposal. Unlike traditional plastics, which can often be recycled through established systems, FRP materials present difficulties in recycling due to the complexity of their composite structure. The fiberglass particles, once integrated into the polymer matrix, are difficult to separate from the resin, making the recycling process more complicated and costly.
Moreover, when FRP materials reach the end of their life cycle, they may not degrade easily in the environment, contributing to waste accumulation. As the demand for more sustainable materials grows, there is an increasing need to develop better methods for recycling fiberglass reinforced plastic particles. Some researchers are investigating the use of specialized chemical processes or mechanical techniques to break down and recycle FRP, but effective, widespread recycling solutions are still in development.
The disposal of FRP materials can also be problematic. While the materials themselves are durable, they do not always break down efficiently in landfills. This issue has led to growing concerns about the environmental impact of large-scale FRP production and disposal, and the need for more sustainable disposal methods is becoming more urgent.
Material Compatibility
Fiberglass reinforced plastic particles interact with different types of plastics in specific ways, and ensuring compatibility is critical for achieving the desired properties in the final product. Not all polymers are suitable for use with fiberglass particles, and selecting the right combination of materials is essential to maximize the performance and durability of the composite.
For example, some plastics may not bond well with fiberglass, leading to weak spots or delamination in the final product. This can result in reduced mechanical properties, such as lower tensile strength or impact resistance. The type of resin used also plays a crucial role in the effectiveness of the fiberglass reinforcement. Epoxy resins, for instance, provide excellent bonding and performance with fiberglass, while polyester resins might not offer the same level of adhesion or resistance to environmental factors.
Therefore, it is essential to carefully consider the compatibility of fiberglass reinforced plastic particles with the specific resin and polymer matrix used in an application. Manufacturers must test and optimize material combinations to ensure that the final product meets performance standards for strength, durability, and other key properties.
These challenges—cost, recycling, and material compatibility—are significant considerations when working with fiberglass reinforced plastic particles. While the benefits of FRP materials are clear, addressing these issues will be key to unlocking their full potential in a wide range of applications. As technology advances, solutions to these challenges are likely to emerge, making FRP composites more accessible, sustainable, and efficient for industries worldwide.
FAQs about Fiberglass Reinforced Plastic Particles
Fiberglass reinforced plastic (FRP) is a composite material made by embedding glass fibers within a polymer matrix. The chemical composition of FRP involves two main components: the reinforcement material (glass fibers) and the matrix material (resins). The glass fibers are made primarily from silica (SiO2), along with other compounds such as alumina (Al2O3), boron oxide (B2O3), and calcium oxide (CaO). These fibers provide strength, durability, and resistance to mechanical stress. The resin matrix, often composed of polymers like epoxy, polyester, or vinyl ester, binds the glass fibers together and gives the composite its form and structure. The polymer resins are typically made from carbon-based molecules, including compounds like styrene and ethylene, depending on the specific type of resin used. This combination of glass fibers and resin results in a material that is strong, lightweight, and resistant to corrosion, making FRP ideal for use in automotive, aerospace, construction, and other industries.
While fiberglass reinforced plastic (FRP) offers many benefits, there are also several disadvantages to consider when using this material. One of the primary drawbacks is its relatively high cost of production. The manufacturing process, which involves the combination of glass fibers and specialized resins, can be expensive, particularly when high-performance resins like epoxy are used. This makes FRP less cost-effective compared to other materials, especially in industries that require large quantities of material.
Another significant disadvantage is the difficulty of recycling FRP. The composite nature of the material, with glass fibers embedded in a polymer matrix, makes it challenging to separate and reuse the components. As a result, FRP is often not recyclable through standard recycling processes, leading to environmental concerns regarding its disposal. Additionally, while FRP is strong and durable, it is also brittle and can fracture under extreme impact, making it unsuitable for applications that require high flexibility or shock absorption.
Furthermore, fiberglass dust created during cutting or grinding can be harmful to human health if proper precautions are not taken. Long-term exposure to this dust can cause respiratory issues, skin irritation, or eye damage, which makes the handling of FRP materials more challenging during manufacturing or construction processes.
Fiberglass reinforced plastic (FRP) is a composite material made by combining glass fibers with a polymer resin matrix. The glass fibers, which are typically made of silica-based compounds, provide the reinforcement that gives FRP its strength and durability. The resin, which can be composed of various types of polymers such as epoxy, polyester, or vinyl ester, holds the fibers together and gives the composite its form and shape. This combination creates a material that is both lightweight and strong, with enhanced resistance to corrosion, wear, and environmental factors.
FRP is commonly used in a wide range of industries, including automotive, aerospace, construction, and marine applications. The material’s ability to resist degradation from chemicals, UV light, and moisture makes it ideal for use in harsh environments. Additionally, FRP is versatile and can be molded into various shapes and sizes, making it suitable for producing complex components and structures. The combination of these properties makes FRP a popular choice for applications where both strength and weight reduction are important.
Recycling fiberglass reinforced plastic (FRP) presents significant challenges due to the composite nature of the material. FRP consists of glass fibers embedded in a polymer matrix, and the strong bond between these two components makes it difficult to separate and recycle the individual materials. Unlike traditional plastics, which can often be melted down and reused, FRP cannot easily be broken down for reuse in the same way. This means that the recycling of FRP is not as straightforward as that of other materials.
However, there are ongoing efforts to develop more sustainable recycling methods for FRP. Some advanced processes, such as chemical recycling or pyrolysis, are being explored to break down the polymer resin and recover the glass fibers for reuse. In certain cases, mechanical grinding can be used to repurpose the material, such as in the production of new FRP components or as filler material in construction applications. Despite these efforts, large-scale recycling of FRP is still in the early stages, and more research is needed to make the process more efficient and commercially viable. Until then, many FRP products end up in landfills or are incinerated, raising concerns about the environmental impact of their disposal.
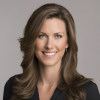
As the editor of GangLong Fiberglass, I have years of experience and in-depth research, focusing on cable tray products, fiberglass solutions, and grille systems. I incorporate years of industry insights and practical experience into every content, committed to promoting the progress of the industry. At GangLong Fiberglass, my commitment is reflected in every product, from innovative cable trays to durable fiberglass solutions and sturdy grille systems. As an authoritative voice in the industry, my goal is to provide valuable information to professionals and businesses and promote forward-looking solutions.