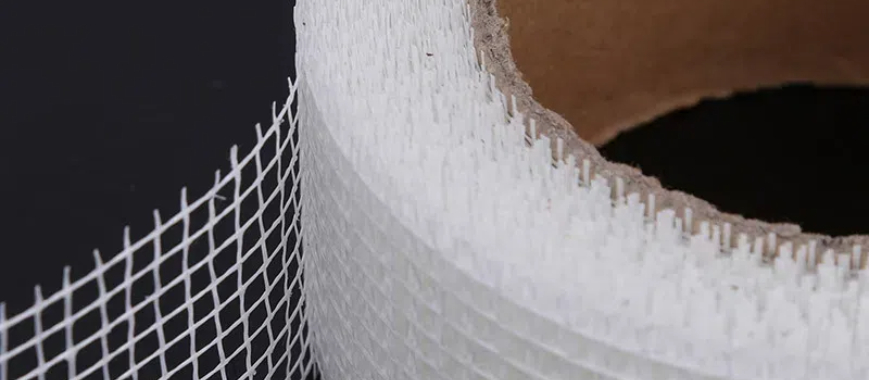
Fiberglass Reinforced Plastic (FRP) is a composite material made by combining fiberglass fibers with a polymer resin, typically epoxy, polyester, or vinylester. The fiberglass reinforcement provides enhanced strength, while the resin binds the fibers together, forming a durable and lightweight material. FRP offers a remarkable combination of properties, such as high tensile strength, corrosion resistance, and low maintenance needs, making it ideal for various applications, from construction to transportation. Fiberglass reinforced plastic pros include its versatility, superior durability, and resistance to environmental factors, which make it a preferred choice for products requiring long-lasting performance. As a result, FRP is used in industries ranging from automotive to infrastructure, offering an ideal solution for demanding environments.
Fiberglass Reinforced Plastic Pros: A Comprehensive Look at Its Properties
Fiberglass Reinforced Plastic (FRP) combines fiberglass and resin to create a highly versatile material with impressive properties that make it suitable for a wide range of applications. In this section, we will explore the key mechanical, thermal, and chemical properties of FRP, demonstrating why fiberglass reinforced plastic pros make it a preferred material in various industries.
Mechanical Properties of FRP
High Strength-to-Weight Ratio: Light Yet Strong
One of the standout features of FRP is its high strength-to-weight ratio. Fiberglass fibers provide significant strength without adding excessive weight. This makes FRP an excellent choice for applications where reducing weight while maintaining structural integrity is crucial, such as in the automotive and aerospace industries. This unique combination ensures that FRP parts can withstand heavy loads while being easy to transport and handle.
Durability and Impact Resistance
FRP is known for its exceptional durability. The fiberglass reinforcement makes the material resistant to wear and tear, while the resin provides a solid bond that enhances its strength. This combination ensures that FRP components can handle heavy impacts without cracking or breaking. As a result, FRP is often used in environments where materials are subjected to mechanical stress, such as in construction and transportation.
Corrosion Resistance: Ideal for Harsh Environments
Fiberglass reinforced plastic pros are particularly evident in its ability to resist corrosion. Unlike metals, which can rust and degrade over time when exposed to moisture or chemicals, FRP does not corrode, making it highly suitable for use in harsh environments. Whether exposed to saltwater in marine applications or chemicals in industrial settings, FRP remains unaffected, ensuring longevity and reducing the need for frequent maintenance.
Non-Conductivity: Safe for Electrical Applications
FRP is non-conductive, meaning it does not conduct electricity. This property makes it an ideal choice for applications that require electrical safety. FRP is commonly used in electrical enclosures, utility poles, and other electrical infrastructure to prevent electrical hazards. Its non-conductivity also makes it safer in high-voltage environments compared to metallic materials.
Thermal and Chemical Resistance
High-Temperature Resistance: FRP’s Ability to Withstand Extreme Heat
Fiberglass reinforced plastic pros also include its impressive thermal resistance. FRP can withstand high temperatures without losing its structural integrity. This makes it suitable for applications that involve exposure to heat, such as in the automotive, aerospace, and manufacturing industries. FRP components can operate at temperatures far higher than many plastic materials, ensuring reliability even under extreme conditions.
Chemical Resistance: Its Ability to Resist a Wide Range of Chemicals
FRP’s chemical resistance is another reason for its widespread use. The material can withstand exposure to a variety of chemicals, including acids, alkalis, and solvents, without deteriorating. This makes it ideal for use in industries like chemical processing, oil and gas, and waste treatment, where equipment is regularly exposed to harsh chemicals. Its resistance to chemical damage ensures that FRP parts maintain their strength and performance over time.
Versatility in Manufacturing
Can Be Molded into Complex Shapes
One of the key advantages of FRP is its ability to be molded into complex shapes. The material can be formed into intricate designs during the manufacturing process, allowing for customized parts that meet specific functional and aesthetic requirements. This molding capability makes FRP suitable for a variety of applications, from structural components to decorative finishes, across different industries.
Customization Options for Specific Applications
Fiberglass reinforced plastic pros also include its ability to be tailored to meet the needs of different applications. Whether it’s adjusting the resin composition for better heat resistance or modifying the fiberglass weave for enhanced strength, FRP can be customized in many ways to suit specific requirements. This level of flexibility is crucial in industries where specialized materials are needed for unique challenges, such as in the production of bespoke machinery or infrastructure.
The mechanical, thermal, and chemical properties of FRP make it a material of choice for industries that demand durability, strength, and safety. The advantages of fiberglass reinforced plastic, including its high strength-to-weight ratio, impact resistance, corrosion resistance, and versatility, contribute to its growing popularity across various sectors.
High Temperature Fiberglass Insulation for Industrial Applications
Fiberglass Reinforced Plastic Pros: The Key Advantages That Set It Apart
Fiberglass Reinforced Plastic (FRP) offers several advantages that make it a go-to material for a range of industries. From its durability and strength to its cost-effectiveness and environmental sustainability, FRP stands out as a versatile and reliable option. In this section, we will discuss the key advantages of using FRP and how they contribute to its popularity across multiple sectors.
Lightweight and High Strength
One of the most significant advantages of fiberglass reinforced plastic pros is its combination of high strength and low weight. The use of fiberglass reinforcement ensures that FRP maintains exceptional strength while being much lighter than many traditional materials like metals or concrete.
- Easier transportation and handling: The lightweight nature of FRP makes it easier to handle during manufacturing, transportation, and installation. This reduces logistical costs and makes FRP products more manageable in large-scale projects.
- Strength without the bulk: Despite its lightness, FRP doesn’t sacrifice strength. Its high strength-to-weight ratio makes it suitable for applications where heavy materials would be impractical, such as in aerospace, automotive, and construction industries.
Corrosion Resistance
Corrosion is a major concern in many industries, especially those involving exposure to harsh environmental conditions. One of the most notable fiberglass reinforced plastic pros is its resistance to corrosion, which makes it ideal for use in a variety of challenging environments.
- Suitable for use in marine, industrial, and outdoor environments: FRP is resistant to corrosion from saltwater, chemicals, and other harsh elements. This makes it an excellent material for marine applications, such as boat hulls and dock structures, as well as industrial applications exposed to chemicals.
- Longer lifespan: Unlike metals, which rust over time, or wood, which can rot, FRP maintains its structural integrity for much longer. This long lifespan reduces the need for frequent replacements, offering cost savings over time.
Low Maintenance
Fiberglass reinforced plastic pros also extend to its low maintenance needs. Unlike other materials that require regular upkeep to remain in good condition, FRP is virtually maintenance-free.
- No need for painting or coating: FRP doesn’t require frequent painting or coating to protect against environmental wear and tear. This makes it a low-maintenance solution that saves both time and money in the long term.
- Resistance to wear and tear: The inherent durability of FRP ensures that it remains functional and visually appealing for extended periods without degradation, reducing the need for regular repairs.
Design Flexibility
FRP offers significant flexibility when it comes to design, making it a preferred material for custom applications.
- Can be molded to meet specific design needs: FRP can be molded into virtually any shape or size, allowing it to be tailored to meet unique design specifications. This makes it an excellent choice for industries that require bespoke components, such as automotive and architecture.
- Availability of different colors, textures, and sizes: Whether you need a specific color for aesthetic purposes or a particular texture for functional reasons, FRP can be manufactured to suit your exact needs. This versatility makes it easy to integrate into various products and designs.
Environmental Sustainability
With growing concern over environmental impact, fiberglass reinforced plastic pros include its sustainability, offering several eco-friendly benefits.
- Non-toxic and recyclable: FRP is made from non-toxic materials and can be recycled at the end of its life cycle, making it a more environmentally friendly option compared to materials like metals or plastics.
- Longer lifespan reduces material waste: The durability of FRP means fewer replacements are needed, reducing overall material waste. This makes it a sustainable choice for long-term projects and environmentally conscious consumers.
Cost-Effectiveness
While the initial cost of FRP might be higher than other materials, the long-term benefits make it a cost-effective choice.
- Initial cost may be higher but offers long-term savings: The durability, low maintenance, and extended lifespan of FRP mean fewer repairs and replacements over time. This leads to significant savings in the long run, making FRP a more economical choice compared to traditional materials that require frequent upkeep.
- Reduced downtime: The strength and resilience of FRP also contribute to reduced downtime in industries where material failure can lead to costly delays. This efficiency makes FRP a cost-effective option for businesses that prioritize productivity and reliability.
Fiberglass Reinforced Plastic Pros
The advantages of fiberglass reinforced plastic are numerous and wide-ranging. Its lightweight nature, combined with high strength, makes it ideal for transportation and handling. The corrosion resistance and low maintenance requirements ensure its longevity in even the harshest environments. The design flexibility and environmental sustainability add to its appeal, while the cost-effectiveness ensures long-term savings. Whether in construction, automotive, marine, or other industries, fiberglass reinforced plastic pros make it a top choice for durable, reliable, and sustainable materials.
What Is Encapsulated Fiberglass Insulation and Its Benefits?
Fiberglass Reinforced Plastic Pros: Exploring Its Versatile Applications
Fiberglass Reinforced Plastic (FRP) is widely used across numerous industries due to its unique combination of strength, durability, and versatility. From industrial environments to transportation, construction, and electronics, the fiberglass reinforced plastic pros make it a material of choice for various applications. In this section, we will explore some of the most common uses of FRP, highlighting how its properties make it an ideal solution for different needs.
Industrial Applications
Fiberglass reinforced plastic is heavily utilized in industrial settings, where its durability and resistance to harsh environments are key advantages.
- Used in tanks, pipes, and structural components for industrial environments: FRP is widely employed in industries that require heavy-duty materials, such as in the production of tanks, pipes, and other structural components. Its resistance to corrosion makes it an ideal choice for environments where metal parts would rust or degrade over time.
- Suitable for chemical processing plants and wastewater treatment facilities: The chemical resistance of FRP makes it particularly well-suited for use in chemical processing plants, where equipment must withstand exposure to harsh chemicals. It is also commonly used in wastewater treatment facilities, where its resistance to both chemicals and water ensures that FRP components can last for many years without deterioration.
Construction and Architecture
In construction, FRP is valued for its lightweight nature, strength, and flexibility, making it a popular material for both structural and aesthetic applications.
- FRP in construction: Used for flooring, walls, and exterior facades: Due to its high strength-to-weight ratio, FRP is used in various construction applications, such as flooring, walls, and even exterior facades. Its corrosion resistance is particularly useful in areas exposed to moisture or chemicals, ensuring that buildings and structures remain in good condition for longer.
- Lightweight and durable materials for building design: In architectural design, FRP is often chosen for its ability to provide both structural integrity and aesthetic flexibility. It can be molded into complex shapes, allowing for unique, customized designs, all while maintaining the lightweight and durable qualities needed in modern construction projects.
Transportation
The transportation industry benefits greatly from the fiberglass reinforced plastic pros, especially in sectors where strength, lightweight, and corrosion resistance are critical.
- Aerospace and automotive industries utilize FRP for parts that require strength and low weight: FRP is widely used in the aerospace and automotive industries for components that must combine strength and low weight, such as body panels, interior parts, and structural components. Its ability to reduce overall weight without sacrificing durability is particularly valuable in both sectors, as it helps improve fuel efficiency and performance.
- Increased fuel efficiency and reduced emissions: By replacing heavier materials, FRP helps reduce the overall weight of vehicles, which in turn leads to better fuel efficiency and lower emissions. This makes it an eco-friendly choice in an industry that is continuously seeking ways to reduce environmental impact.
Marine and Outdoor Uses
The unique properties of fiberglass reinforced plastic make it particularly well-suited for use in marine environments, where exposure to water and harsh conditions is a concern.
- Boat hulls, docks, and other marine applications due to FRP’s water resistance: FRP is widely used in the marine industry due to its exceptional water resistance and durability. Boat hulls, docks, and other watercraft components are often made from FRP, as it can withstand prolonged exposure to water without deteriorating or corroding.
- Resistant to saltwater and other corrosive elements: In addition to being resistant to freshwater, FRP is also resistant to saltwater, making it ideal for use in marine applications. This ability to resist corrosion from salt and other harsh elements ensures the longevity and reliability of marine structures and vehicles.
Electronics and Electrical Applications
The fiberglass reinforced plastic pros also extend to the electronics and electrical industries, where its non-conductivity and durability are essential.
- Used in creating insulated parts for electronics, power transmission equipment, and enclosures: FRP is commonly used to create insulated parts for electronics, such as circuit boards and enclosures. Its non-conductive nature makes it an excellent material for preventing electrical conductivity and ensuring the safe operation of electronic devices.
- Enclosures and protective covers for electrical equipment: FRP is often used for making enclosures for electrical components, such as transformers, motors, and power transmission equipment. Its resistance to environmental factors, such as moisture, dust, and chemicals, makes it an ideal material for protecting sensitive electrical systems.
Fiberglass Reinforced Plastic Pros in Common Applications
Fiberglass reinforced plastic pros make it an incredibly versatile material, with applications ranging from industrial tanks and pipes to lightweight components in transportation and marine vessels. In construction and architecture, its design flexibility and durability are highly valued, while in electronics, its insulating properties provide safety and reliability. Whether used for structural integrity, aesthetic flexibility, or environmental resistance, FRP continues to prove its worth across various industries, making it a material of choice for applications demanding strength, durability, and low maintenance.
Why Shallow Fiberglass Tubs Are Perfect for Small Bathrooms
Fiberglass Reinforced Plastic Pros: Addressing the Disadvantages
While fiberglass reinforced plastic (FRP) offers numerous advantages, it also has some limitations that should be considered before choosing it for specific applications. Despite the fiberglass reinforced plastic pros, there are a few drawbacks that can affect its performance in certain conditions. In this section, we will discuss the primary disadvantages of FRP, including brittleness, repair challenges, and its limited temperature range.
Brittleness and Difficulty in Repair
Despite its impressive strength, FRP can be prone to brittleness, particularly under extreme stress or impact.
- Prone to cracking or shattering under extreme stress: One of the significant drawbacks of FRP is its tendency to crack or shatter when subjected to sudden impacts or heavy stress. Although it is resistant to wear and tear, it lacks the flexibility of some other materials like metals or rubber, which can absorb impact better. In applications where high impact resistance is essential, such as in high-stress mechanical environments, this brittleness can become a limiting factor.
- Challenges with repairs and maintenance in comparison to other materials: Repairing FRP can be more complicated than fixing metals or plastics. Since FRP consists of layered materials (fiberglass and resin), any damage to the surface requires a detailed repair process to restore the material’s strength and appearance. Unlike metals, which can be welded or patched up more easily, FRP repairs often involve specialized techniques, such as re-layering the fiberglass and applying a resin that matches the original material. This repair complexity can lead to higher maintenance costs and longer downtime in industrial settings.
Limited Temperature Range
Fiberglass reinforced plastic pros include its ability to withstand a wide range of environmental conditions. However, it also has limitations when exposed to high temperatures.
- Can degrade or lose strength at temperatures above 100°C (depending on the resin type): While FRP is highly resistant to temperature fluctuations, it does have an upper limit. Depending on the resin type used, FRP can begin to degrade or lose its structural strength when exposed to temperatures exceeding 100°C. This makes it unsuitable for high-heat environments, such as those found in some industrial processes or in applications like engine parts or high-performance machinery. As the resin softens or breaks down, the integrity of the fiberglass reinforcement is compromised, which can lead to material failure.
- Limited resistance to prolonged exposure to heat: In addition to its vulnerability to high temperatures, FRP is also susceptible to degradation when exposed to prolonged heat. This is especially relevant in industries where materials are subjected to consistent heat sources, such as power plants or manufacturing facilities dealing with hot chemicals. To mitigate this, specialized heat-resistant FRP formulations may be used, but these options are often more expensive and may still have a lower threshold compared to other materials like metals.
Disadvantages
Although the fiberglass reinforced plastic pros offer remarkable durability, strength, and versatility, the material also has its limitations. FRP’s brittleness and difficulty in repairing damage can present challenges, particularly in high-stress applications. Additionally, its limited temperature range means that it may not be the best choice for environments subject to extreme heat. While these disadvantages are important to consider, they can often be mitigated by choosing the right resin formulations and incorporating FRP in environments where its benefits outweigh the drawbacks.
Fiberglass Reinforced Plastic Pros: Environmental Considerations and Design Limitations
Fiberglass Reinforced Plastic (FRP) is often praised for its durability, strength, and versatility. However, despite the fiberglass reinforced plastic pros, its environmental impact and design limitations are important factors to consider when evaluating its suitability for different applications. In this section, we will explore the environmental concerns associated with the production and disposal of FRP, as well as its limitations in certain design applications.
Environmental Impact of FRP
While fiberglass reinforced plastic pros include its recyclability, the production process of FRP can have significant environmental consequences. Understanding these environmental impacts is essential for making informed decisions about using FRP in various industries.
- While recyclable, the production process of FRP can involve harmful chemicals and high energy use: One of the most notable environmental drawbacks of FRP is the production process. The manufacturing of FRP involves the use of resins, which are typically derived from petroleum-based products, and fiberglass, which requires energy-intensive processes to create. The production of these materials often involves harmful chemicals, such as styrene, which can release volatile organic compounds (VOCs) into the atmosphere. Additionally, the process can be energy-intensive, contributing to higher carbon emissions compared to other materials with less complex manufacturing processes.
- Challenges with disposal and recycling: While FRP is technically recyclable, the process is not always straightforward. The materials used in FRP, especially when it is combined with certain resins, can make recycling more difficult and less economically viable. Unlike metals or plastics, which can be easily melted down and reused, FRP requires specialized processes for recycling, and often, it ends up in landfills. This leads to concerns over the long-term environmental impact, particularly since FRP products can take years to degrade naturally.
Design Limitations of FRP
Fiberglass reinforced plastic pros certainly make it a versatile material, but it does come with some design limitations that could affect its use in certain applications.
- Although versatile, certain complex applications may still face limitations in flexibility and moldability: FRP is a highly adaptable material, capable of being molded into a variety of shapes and sizes. However, it does have its limits when it comes to extremely complex or intricate designs. For example, while it can be molded into curved or custom shapes, the molding process may not be as flexible as other materials like metals or plastics, especially for designs with fine details or very thin sections. This limitation can affect its use in applications where intricate features or high precision are required.
- Difficulty in achieving ultra-thin structures: In some design scenarios, the ability to create extremely thin, lightweight structures may be compromised. While FRP is strong and light, achieving ultra-thin components can be challenging due to the thickness and weight of the fiberglass and resin layers. This can limit its use in applications where minimal material thickness is essential, such as in certain aerospace or electronics designs.
Environmental Impact and Design Limitations
While fiberglass reinforced plastic pros offer a range of benefits, its environmental impact and design limitations must be carefully weighed in the decision-making process. The production of FRP can be energy-intensive and involve harmful chemicals, which can contribute to environmental pollution. Additionally, while FRP is recyclable, the recycling process is not always efficient, leading to waste management challenges. On the design front, while FRP offers versatility, it may not always be the best material for highly complex or ultra-thin structures. As industries continue to seek more sustainable and flexible materials, it is important to consider these factors when choosing FRP for specific applications.
FAQs about Fiberglass Reinforced Plastic Pros
Fiberglass reinforced plastic (FRP) offers numerous advantages, making it a popular choice in various industries. One of the key benefits is its high strength-to-weight ratio. This means that FRP is much lighter than metals, yet still retains exceptional strength, making it an ideal material for applications requiring both durability and ease of handling. In addition, FRP is highly corrosion-resistant, which makes it suitable for environments where metals would typically rust or degrade. This is especially advantageous in industries such as marine, chemical processing, and wastewater treatment.
Another notable advantage of FRP is its flexibility in design. It can be molded into complex shapes, offering significant customization options for a wide range of applications, from construction to automotive and aerospace. Additionally, FRP requires minimal maintenance, as it is resistant to wear and tear, reducing the need for frequent repairs or replacements. Finally, thermal and chemical resistance are important properties of FRP, allowing it to withstand extreme temperatures and exposure to a variety of chemicals without degrading.
Glass Reinforced Plastic (GRP) shares many of the same advantages as fiberglass reinforced plastic (FRP), but its specific benefits are often emphasized in different contexts, particularly in construction and marine applications. One of the key advantages of using GRP is its durability. GRP is resistant to corrosion, making it highly suitable for use in coastal or industrial environments where traditional materials like metals would rust or corrode over time. This makes GRP an ideal choice for marine structures such as boat hulls, docks, and piers, as well as architectural facades in harsh weather conditions.
Another significant benefit is lightweight construction. GRP components are significantly lighter than alternatives like steel or concrete, which not only reduces the weight of the overall structure but also makes transportation and handling easier. GRP also offers thermal insulation properties, providing better energy efficiency when used in building construction or industrial applications. It is also low-maintenance, requiring little upkeep over its lifespan due to its resistance to environmental factors. This combination of durability, low weight, and minimal maintenance makes GRP a highly cost-effective and versatile material.
Fiberglass, the primary reinforcing material in many composite products like FRP and GRP, offers several unique advantages that make it a valuable material across industries. Strength and lightness are among its most well-known properties. Despite being lightweight, fiberglass has high tensile strength, making it ideal for applications that require strength without the added weight of traditional metals. This is especially beneficial in industries like aerospace, automotive, and sports equipment manufacturing.
Fiberglass is also highly versatile in terms of design. It can be woven into various fabric patterns and combined with resins to create composites that can be molded into complex shapes, making it an ideal material for custom designs. Furthermore, fiberglass is known for its corrosion resistance, which makes it a durable option in environments exposed to moisture, chemicals, and saltwater. Its thermal and electrical insulating properties are another advantage, especially in the construction and electronics industries, where heat and electrical conductivity can be a concern. Finally, fiberglass is eco-friendly, as it can be recycled in certain conditions, contributing to more sustainable production practices.
Glass Fiber Reinforced Polymer (GFRP) combines the benefits of both fiberglass and polymer resins, offering a material that is both lightweight and strong. One of the main advantages of GFRP is its high strength-to-weight ratio, similar to that of fiberglass, but enhanced by the polymer matrix that binds the glass fibers. This makes GFRP particularly valuable in applications like construction, automotive, and transportation, where both strength and low weight are critical.
Another key benefit of GFRP is its corrosion resistance. Like fiberglass, GFRP is highly resistant to the damaging effects of moisture, chemicals, and environmental factors. This makes it an excellent material choice for use in marine environments, as well as in infrastructure such as bridges and pipelines, where corrosion could otherwise lead to costly maintenance and replacements. GFRP is also highly flexible in terms of design; it can be molded into intricate shapes and customized to suit specific needs, making it an ideal material for tailored applications. Additionally, GFRP is low maintenance, requiring minimal upkeep compared to other materials like steel or concrete. This reduces overall operational costs and extends the lifespan of products made from GFRP.
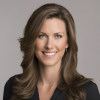
As the editor of GangLong Fiberglass, I have years of experience and in-depth research, focusing on cable tray products, fiberglass solutions, and grille systems. I incorporate years of industry insights and practical experience into every content, committed to promoting the progress of the industry. At GangLong Fiberglass, my commitment is reflected in every product, from innovative cable trays to durable fiberglass solutions and sturdy grille systems. As an authoritative voice in the industry, my goal is to provide valuable information to professionals and businesses and promote forward-looking solutions.