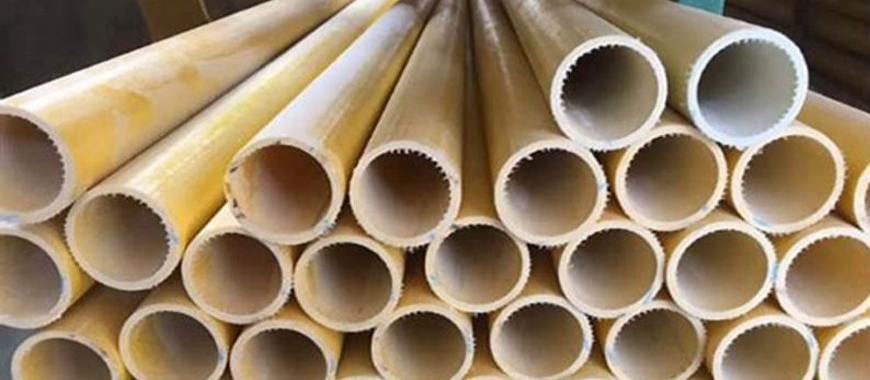
High temperature FRP pipe, or Fiber Reinforced Polymer pipes, are advanced composite materials made from a polymer matrix reinforced with fibers, designed for resilience and performance under extreme conditions. These pipes uniquely combine durability and resistance to corrosion with an ability to withstand high temperatures, making them ideally suited for demanding industrial applications. In sectors such as chemical processing, power generation, and oil and gas extraction, where materials are frequently exposed to both corrosive substances and high thermal loads, the high temperature resistance of these FRP pipes ensures reliability and longevity. Their specialized construction not only handles significant thermal stress but also contributes significantly to operational efficiencies and safety improvements in industrial processes. High temperature FRP pipe, made from a fiber-reinforced polymer matrix, offers corrosion resistance and strength, withstanding -29°C to 149°C.
The Benefits of High Temperature FRP Pipe
Selecting high temperature resistant frp pipe brings numerous advantages over traditional materials in a range of demanding applications.
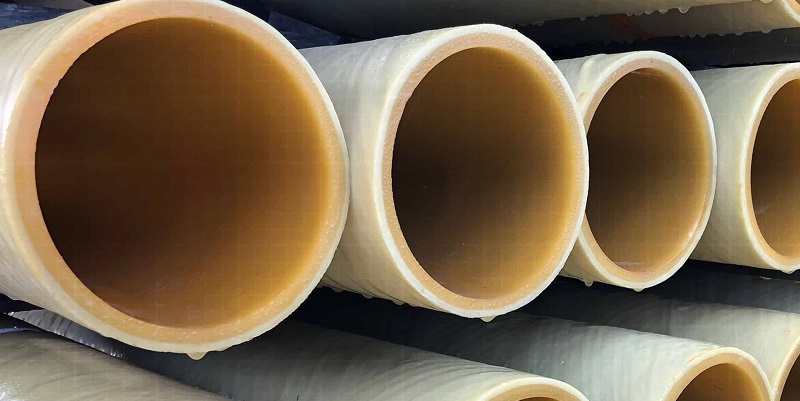
Corrosion Resistance
High temperature FRP pipes are highly resistant to corrosion caused by a wide range of chemicals, including acids, alkalis, and solvents. Unlike steel, which can rust, or concrete, which can degrade over time in harsh environments, FRP pipes maintain their integrity even in the most aggressive settings. This makes them ideal for industries such as chemical processing, wastewater treatment, and marine applications, where prolonged exposure to corrosive substances is common.
Lightweight Design
FRP pipes are significantly lighter than traditional materials like steel or concrete, often weighing only a fraction of their counterparts. This lightweight nature reduces transportation costs, simplifies handling during installation, and minimizes the need for heavy equipment, saving both time and labor costs. Their ease of installation also makes them a preferred choice for projects in remote or hard-to-reach areas.
High Strength-to-Weight Ratio
Despite their lightweight composition, high temperature FRP pipes boast impressive strength. Their strength-to-weight ratio is superior to many traditional materials, meaning they can withstand high pressures and structural loads while remaining easy to transport and install. This combination of strength and lightness ensures long-lasting and reliable performance, even under demanding conditions.
Thermal Insulation
FRP pipes exhibit excellent thermal insulation properties, which help maintain the temperature of the fluids they transport. Unlike metal pipes, which often require additional insulation to prevent heat loss or gain, FRP pipes provide a built-in thermal barrier. This feature is particularly beneficial in applications involving high-temperature fluids, as it reduces energy costs associated with maintaining fluid temperatures.
Low Thermal Conductivity
The low thermal conductivity of FRP pipes further enhances their energy efficiency. By minimizing heat loss, these pipes help industries reduce their overall energy consumption, leading to lower operational costs. This characteristic also helps maintain system performance in high-temperature environments, ensuring steady operation over time.
Impact Resistance
FRP pipes are highly resistant to physical impacts, making them less prone to cracks, dents, or breaks. This resilience ensures reliability in scenarios where external forces or accidental impacts could compromise other materials. The impact resistance of FRP pipes reduces the risk of downtime and costly repairs, making them an excellent choice for industrial and infrastructural applications.
Flexible Design Options
One of the standout features of FRP pipes is their versatility in design. They can be manufactured to meet specific requirements, including unique shapes, sizes, and configurations. This flexibility enables tailored solutions for complex piping systems or unique industrial challenges that traditional materials may not be able to address. Whether for high-pressure systems or intricate layouts, FRP pipes can be customized to fit the exact needs of a project.
Reduced Maintenance
The durability and corrosion resistance of FRP pipes translate to minimal maintenance requirements over their lifetime. Unlike metal pipes that may need frequent inspections, repairs, or coatings to prevent corrosion, FRP pipes require only occasional checks to ensure optimal performance. This low-maintenance nature leads to significant cost savings over time, particularly in industries with extensive piping networks.
Extended Lifecycle
High temperature FRP pipes are designed for longevity, with a lifespan that often exceeds traditional materials by several decades. Their resistance to wear and tear, combined with their ability to withstand harsh environmental conditions, ensures they remain functional far longer than steel, concrete, or other alternatives. This extended lifecycle reduces the need for frequent replacements, saving both time and resources.
Environmentally Friendly
FRP pipes are an environmentally sustainable option for modern industries. Their extended lifespan means fewer resources are required for replacements, and their recyclability contributes to reducing waste. Additionally, their lightweight design lowers energy consumption during transportation and installation. These factors make FRP pipes a greener choice for businesses aiming to reduce their environmental footprint while maintaining high performance.
By providing detailed explanations of each benefit, this expanded overview highlights why high temperature FRP pipes are a superior choice for various industrial applications. Their unique combination of durability, efficiency, and versatility positions them as a reliable and cost-effective solution in demanding environments.
Key Advantages of Using China FRP Irrigation Pipe in Farming
How High Temperature FRP Pipes Work
The functionality and resilience of high temperature FRP pipes are grounded in their unique material composition and the advanced technology used in their construction.
Advanced Material Composition
High temperature FRP (Fiberglass Reinforced Plastic) pipes are manufactured using a composite material made from a polymer matrix reinforced with fibers. This composition is ideally suited to withstand high temperatures while maintaining strength and flexibility.
Thermal Resistance Technology
The polymer matrix used in high temperature FRP pipes insulation is engineered to resist degradation at elevated temperatures. This is accomplished by incorporating thermosetting resins which, once cured, create a heat-resistant network that maintains the structural integrity of the pipe.
Fiber Reinforcement
The addition of fibers, typically glass, carbon, or aramid, provides the necessary reinforcement to the polymer matrix. This reinforcement significantly enhances the pipe’s mechanical strength and resistance to high temperatures and harsh environmental conditions.
Resin Application Techniques
The resin, which acts as a binder for the fibers and provides chemical resistance, is carefully applied during manufacturing. Techniques like filament winding and pultrusion are used, allowing for uniform distribution and optimal penetration of the resin throughout the fiber layers.
Layering for Durability
High temperature FRP pipes consist of multiple layers, each serving a specific function — from the internal liner that offers chemical resistance, to the structural layer that provides strength, to the outer surface that adds UV protection and additional resistance to environmental factors.
Controlled Curing Process
After the pipes are shaped, they undergo a controlled curing process. This process involves the application of heat to activate the resin, ensuring it hardens into a solid state that binds the fibers together, forming a robust and durable composite material.
Precision Design and Manufacturing
The design and manufacture of high temperature FRP pipes are conducted using precise calculations and state-of-the-art techniques to ensure the pipes can withstand specific temperature ranges, pressures, and chemical exposures.
Seamless Construction
Unlike traditional pipes that are welded or joined in segments, high temperature FRP pipes can be created in long, continuous lengths using seamless construction techniques. This eliminates weak points and potential failure sites, enhancing the overall integrity and reliability of the piping system.
Customization for Specific Applications
High temperature FRP pipes can be customized to meet the demanding requirements of various applications. Adjustments can be made to the fiber types, resin formulas, and pipe dimensions to optimize performance under specific operational conditions, including extremely high temperatures and corrosive environments.
The combined effect of these advanced materials, sophisticated construction techniques, and innovative design protocols is what enables high temperature FRP pipes to perform exceptionally well under the most demanding conditions, distinguishing them as a superior choice in industries where reliability and durability are paramount.
Applications of High Temperature FRP Pipe
High temperature FRP pipes have become an integral component in a variety of industries due to their ability to withstand elevated temperatures and their resistance to corrosive substances. Their unique material properties provide longevity and durability, making them ideal for challenging industrial environments.
Industries and Use Cases
Chemical Processing: The chemical industry frequently utilizes high temperature FRP pipes for transporting aggressive and corrosive chemicals. These pipes are designed to resist chemical erosion, thus ensuring safe and continuous flow of materials without degradation over time.
Oil and Gas: In the oil and gas sector, high temperature FRP pipes are used for flow lines, injection lines, and as part of fire suppression systems. Their high-temperature tolerance makes them suitable for handling the thermal stresses associated with hydrocarbon processing and transportation.
Power Generation: Cooling towers and geothermal power plants use high temperature FRP pipes to circulate water and steam. The material’s resistance to heat and corrosion makes it superior to traditional materials, which might corrode or fail under such stress.
Pulp and Paper Industry: The paper and pulp industry relies on high temperature FRP pipes for piping caustic and steam solutions critical to the papermaking process. These pipes withstand the industrial processes that involve high temperatures and caustic chemicals.
Waste Incineration Plants: FRP pipes can withstand the acidic environments and high temperatures found in waste incineration plants, making them ideal for flue gas ducting and ash handling systems.
Marine and Offshore: High temperature FRP pipes are used for offshore firefighting systems and for transportation of oil and chemicals. The saltwater environment is highly corrosive, and the thermal stability of FRP pipes ensures longevity and reliability in such settings. Furthermore, the inherent FRP pipe stiffness provides the necessary resistance to external pressures and mechanical stresses, making them well-suited for the demanding conditions of marine and offshore applications.
Fluids and Gases Transported
Sulphuric Acid: In the chemical industry, high temperature FRP pipes are commonly used for transporting concentrated sulphuric acid, a highly corrosive substance, especially at elevated temperatures.
Crude Oil: The oil industry uses high temperature FRP pipes to transport crude oil which can be very hot, both from the point of extraction and during the refining process.
Steam: High temperature FRP pipes transport steam in power generation and industrial processing due to the pipes’ ability to handle the heat and corrosive condensate associated with steam.
Chlorine Gas: Chlorine gas is transported using high temperature FRP pipes in the chemical processing industry due to its highly corrosive nature and the need for materials that can withstand degradation.
Brine Solutions: High temperature FRP pipes are ideal for moving hot brine solutions in industries such as salt production and geothermal energy due to their corrosion resistance and heat tolerance.
Hydrochloric Acid: Used extensively within chemical processing and metal refining industries, hydrochloric acid requires piping solutions like high temperature FRP pipes which can handle both the corrosiveness and the temperature of the fluid.
These examples showcase the suitability of high temperature resistant frp pipe across various industries and in handling a wide range of hot fluids and gases. Their use is grounded in the need for reliable, durable, and corrosion-resistant transport of materials in high-temperature environments.
Design and Manufacturing of High Temperature FRP Pipe
The creation of high temperature FRP (Fiberglass Reinforced Plastic) pipes incorporates an intricate process, focusing on both the resilience of materials and their capacity to withstand extreme environments. Withstanding high temperatures, corrosive substances, and physical strains requires a well-thought-out design and manufacturing approach. The segments below detail the process and essential design aspects that equip these pipes to fulfill rigorous specifications.
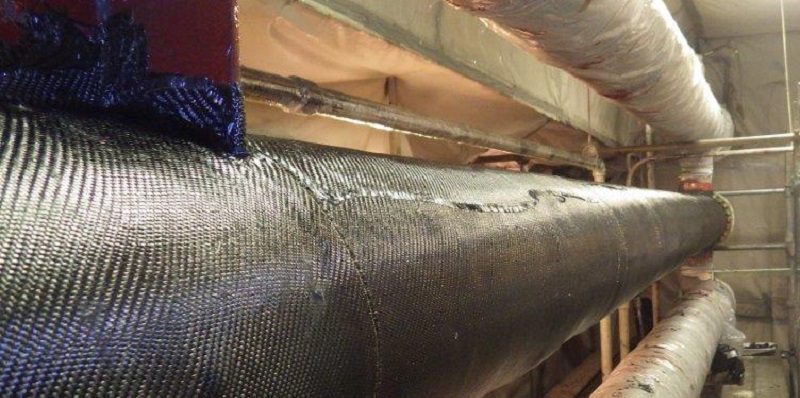
Overview of the Manufacturing Process
Material Selection: The selection of suitable resin systems such as epoxy, vinyl ester, and phenolic resins marks the initial step. These systems are chosen for their ability to endure high temperatures and corrosive settings.
Reinforcement Layering: Continuous fiberglass or carbon fiber strands are layered to provide structural strength. The fibers’ orientation significantly influences the pipe’s flexibility and resilience.
Resin ImpregnationThe reinforcement material undergoes impregnation with resin through methods like hand lay-up or filament winding, emphasizing uniform distribution and the reduction of air voids.
Curing Process: The pipes are then cured under controlled heat and pressure, facilitating the cross-linking of the resin which enhances the product’s mechanical properties and thermal resistance.
Secondary Processing: Additional machining or modifications are performed as required, tailoring the pipes for specific fittings or applications.
Quality Control: Quality assurance measures are integral, focusing on the consistency, density, and uniformity of the resin-fiber composition, ensuring compliance with industry standards.
Protective Coatings: Protective outer coatings are applied to increase resistance against environmental factors such as UV exposure, saltwater, and chemicals.
Key Design Features that Contribute to Temperature Resistance
The chemical formulation of the resin used in temperature resistant frp pipe is optimized to enhance thermal resistance and ensure stability at higher temperatures.
Resin Formulation: The resin’s chemical makeup is carefully formulated to boost its thermal resistance, ensuring stability under elevated temperatures.
Fiber Type and Orientation: The choice and arrangement of fibers (fiberglass, carbon) are precisely chosen based on expected thermal stresses, enhancing the pipe’s thermal stability and mechanical strength.
Wall Thickness: A thicker wall provides better insulation and heat resistance, making these pipes apt for high-temperature applications.
Interior Lining: Some pipes feature interior linings made from materials like PTFE or ceramic, offering an additional shield against heat and chemical corrosion.
Heat-Resistant Additives: Thermal stabilizers and flame retardants are mixed into the resin to improve its capacity to endure high temperatures.
Seamless Construction: Manufacturing techniques yield a seamless design, minimizing potential weak points vulnerable to high-temperature stress.
Thermal Expansion Accommodation: Designs include features to manage thermal expansion and contraction, preventing structural damage due to temperature changes.
External Finishing: The outer surface may be engineered to reflect heat or provide additional insulation, enhancing the pipe’s overall thermal resistance.
These meticulous steps in design and manufacturing ensure that high temperature FRP pipes are equipped to handle, without fail, the severe conditions they are built for, maintaining structural integrity and operational reliability where conventional pipes might not suffice.
Key Considerations When Selecting High Temperature FRP Pipe
In the domain of industrial piping, the implications of working under high-temperature and chemically corrosive conditions are significant. It is essential to focus sharply on pipe material selection to ensure safety, efficiency, and longevity of the piping system. High temperature FRP pipes are a standout choice due to their resilience and adaptability to these tough environments. Yet, pinpointing the right kind of FRP pipe is not a one-size-fits-all process. Careful consideration of various nuanced factors is necessary to choose an FRP pipe that matches the unique demands of your specific application.
Factors to Consider Regarding Temperature and Chemical Exposure
Before delving into the selection criteria for your FRP pipe, it’s essential to approach this decision with a detailed analysis of the environmental conditions the pipe will encounter. The interaction between high temperature and chemical exposure can pose significant risks to the structural integrity of the pipe and to the safety of the operation. Let’s look at the key factors that come into play.
Temperature Range: Verify that the high temperature FRP pipe can withstand your system’s temperature fluctuations. An ideal pipe would maintain its properties both at peak and operational temperatures.
Thermal Conductivity: Evaluate the pipe’s ability to insulate against heat transfer. Effective insulation is critical where temperature maintenance is key or when protecting nearby equipment and personnel.
Coefficient of Thermal Expansion: Consider the expansion and contraction of the pipe material with temperature variations, particularly in relation to FRP pipe thermal expansion. Choosing a pipe that can accommodate these physical changes is essential to avoid cracks and structural stress.
Chemical Compatibility: Ensure the compatibility of the pipe material with the chemicals it will carry or be exposed to. Analyze not only direct contacts, like the material being transported but also environmental exposures, such as vapors or spills.
Corrosion Resistance: The pipe should be able to resist corrosion from both the chemicals it carries and the environment it operates in. Factor in the specific type of corrosion anticipated and the longevity expected of the material in such conditions.
Pressure Ratings: High temperature FRP pipes must also meet the necessary pressure requirements, an essential aspect considering the dynamic nature of fluids at elevated temperatures.
UV Resistance: For applications where UV light is a concern, evaluate the pipe’s resistance to UV radiation, can refer to the UV resistant frp pipe. UV degradation can compromise the integrity of the pipe over time if not accounted for.
Fire Resistance: In environments where fire hazards exist, the fire-retardant properties of FRP pipes are of paramount importance. Look for materials that not only resist igniting but also minimize smoke production.
Aging and Wear: Project the long-term behavior of the high temperature FRP pipe within your operational context, factoring in wear and tear, fatigue, and how aging might affect its performance characteristics.
How to Choose the Right FRP Pipe for Your Needs
Now that we’ve outlined the environmental factors at play, the next step is to marry those considerations with the attributes of the FRP pipe, particularly the FRP pipe pressure rating.The selection process must be methodical and based on a good understanding of the application’s requirements. Here’s a detailed guide to choosing the right FRP pipe.
Assess the Application: Detailed knowledge of the operation conditions is fundamental. This includes an understanding of the temperatures, pressures, and chemical exposures that will impact the FRP pipe.
Engage Manufacturers: Consult with manufacturers to leverage their knowledge. They can often provide insights beyond the data sheets and help refine your selection to meet your precise needs.
Secure Technical Data: Get comprehensive technical data pertaining to the FRP materials on your radar. Look into their mechanical and thermal resilience, chemical resistance, and industry certifications.
Consider Cost and Performance: Balance the cost against expected performance gains. While initial investment is important, factor in operation costs and anticipated lifespan to gain a true sense of value.
Installation Provisions: Each FRP pipe may come with specific requirements for installation. Consider these logistical nuances, such as how the pipes will be joined, supported, or spaced. Additionally, attention should be given to FRP pipe deflection, ensuring that the pipes are adequately supported to prevent excessive bending or sagging under load, which could compromise their performance or longevity.
Customization Opportunities: Some applications may benefit from custom-tailored FRP pipes with particular specifications. Inquire about modifications that can grant your piping system an edge in efficiency.
Research Past Implementations: Investigate case studies where high temperature FRP pipes have been used in similar situations. These can offer insights into unforeseen challenges and best practices.
Verify Quality and Standards: Your chosen FRP pipe should conform to all relevant quality and industry standards. Quality assurance protocols like ASTM or ISO can lend credibility to your choice.
Post-Sale Services: Evaluate the manufacturer’s customer support infrastructure. Pre-planned support for maintenance, technical troubleshooting, and warranty claims is indispensable for the smooth operation of any pipeline system.
Careful contemplation of these guidelines can substantially aid in choosing a high temperature FRP pipe that not only meets the immediate needs of your operation but also ensures performance over time, adapting as necessary to the evolving industrial landscape.
Installation and Maintenance of High Temperature FRP Pipe
High-temperature Fiber Reinforced Plastic (FRP) pipes are pivotal in various industrial applications due to their resistance to corrosive environments and ability to withstand high temperatures. Proper installation and maintenance are essential to maximize their longevity and performance. This guide will delve into the best practices for installing high-temperature FRP pipes and provide maintenance tips to ensure they continue to operate effectively at high temperatures.
Best Practices for Installation to Ensure Longevity and Performance
When it comes to installing a high-temperature FRP pipe, there are several key considerations to keep in mind. These practices are designed to ensure that the pipe is installed correctly and can operate effectively for its intended lifespan:
Pre-Installation Inspection: Before installation, thoroughly inspect each high-temperature FRP pipe for any signs of damage or defects. Any issues should be addressed before proceeding with the installation.
Correct Handling and Storage: High-temperature FRP pipes should be handled with care to prevent damage. Store them on a flat surface and avoid stacking materials on top that could cause deformation or damage.
Use Appropriate Tools: Use the right tools and equipment designed for working with FRP materials. Avoid using tools that may cause damage to the pipe’s surface.
Follow Manufacturer’s Instructions: Each high-temperature FRP pipe may have specific installation requirements. Follow the manufacturer’s guidelines closely for the best results.
Proper Jointing Techniques: Use the recommended jointing techniques, such as high-temperature FRP pipe adhesive bonding or mechanical joining, as specified by the manufacturer, to ensure a secure and leak-proof connection.
Support and Anchorage: Install adequate support and anchorage as per the design specifications to prevent sagging and to accommodate thermal expansion or contraction.
Avoid Direct Heat Sources: Although designed to withstand high temperatures, direct exposure to flames or other heat sources should be avoided to prevent damage to the FRP material.
Inspection and Testing: Once installed, conduct a thorough inspection and perform any recommended tests (such as pressure testing) to ensure the integrity and readiness of the piping system.
Solutions from a Trusted Wholesale FRP Anticorrosion Pipe Factory
Maintenance Tips to Keep Pipes Operating at High Temperatures
Maintaining high-temperature FRP pipes is crucial to ensure they continue to operate efficiently. Here are several maintenance tips.
Regular Inspections: Regularly inspect the high-temperature FRP pipe for signs of wear, damage, or leaks. Promptly address any issues discovered.
Clean Regularly: Keep the pipes clean from debris, chemicals, or other materials that could cause damage or blockages.
Monitor Temperature and Pressure: Regularly monitor the operating temperature and pressure within the pipes. Ensure they remain within the specified limits for the FRP material.
Check for Chemical Compatibility: Continuously ensure that the chemicals being transported are compatible with the FRP material to prevent degradation.
Protect from UV Radiation: If applicable, protect the pipes from prolonged exposure to UV radiation, which can degrade the FRP material over time.
Maintain Supports and Anchorage: Regularly inspect and maintain the pipe supports and anchorage to ensure they remain effective.
Handle Repairs Promptly: If damage or leakage occurs, handle repairs promptly using recommended methods and materials to restore integrity.
Audit Thermal Insulation: Regularly check and maintain any thermal insulation to ensure it remains effective in maintaining the desired temperature levels.
Documentation and Reporting: Keep detailed records of installations, inspections, maintenance activities, and repairs to aid in future maintenance planning and ensure compliance with any regulatory requirements.
By adhering to these installation and maintenance practices, the lifespan and performance of high temperature FRP pipe can be maximized, ensuring they continue to operate effectively and safely in high-temperature environments.
How to Choose the Right High Temperature FRP Pipe Manufacturer
Selecting the right manufacturer for high temperature FRP pipes is crucial to ensure quality, durability, and long-term performance.
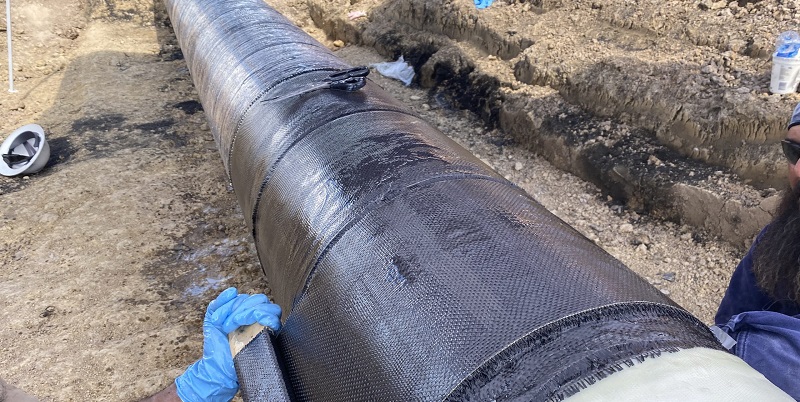
Here are key factors to consider when evaluating potential manufacturers to make an informed decision:
Industry Experience and Expertise
Look for manufacturers with extensive experience in producing high temperature FRP pipes. A company with a proven track record and expertise in handling complex requirements is more likely to deliver high-quality products that meet industry standards.
Certification and Compliance
Ensure the manufacturer complies with relevant industry standards and holds certifications such as ISO 9001 for quality management. Certifications indicate that the manufacturer adheres to rigorous quality control processes during production.
Material Quality
Inquire about the materials used in the production of high temperature FRP pipes. The resin, fibers, and other components should be of superior quality and tailored for high-temperature applications. Manufacturers who provide detailed information about their material specifications demonstrate transparency and reliability.
Customization Options
Every application has unique requirements. Choose a manufacturer that offers customization options, such as specific pipe sizes, configurations, and chemical resistance properties, to ensure the product meets your exact needs.
Testing and Quality Assurance
Reputable manufacturers conduct rigorous testing on their high temperature FRP pipes, including pressure tests, thermal performance evaluations, and chemical resistance assessments. Verify the manufacturer’s testing protocols to ensure the pipes can withstand demanding operating conditions.
Technical Support and Expertise
Select a manufacturer that provides strong technical support, including consultation on pipe selection, installation guidance, and troubleshooting. Manufacturers with a dedicated technical team can help you optimize the performance of the piping system.
Production Capacity and Lead Times
For large-scale projects, evaluate the manufacturer’s production capacity and ability to meet deadlines. A manufacturer with a robust production system can deliver the required quantity of pipes within your project timeline without compromising on quality.
Reputation and Reviews
Research the manufacturer’s reputation in the industry by reading customer reviews, case studies, and testimonials. Positive feedback from other clients indicates reliability and customer satisfaction. Additionally, request references to get firsthand insights into the manufacturer’s performance.
After-Sales Service
A good manufacturer provides comprehensive after-sales service, including warranties, maintenance support, and prompt responses to queries. This ensures long-term support and peace of mind throughout the pipe’s lifecycle.
Cost-Effectiveness
While cost is an important factor, avoid compromising quality for a lower price. Compare quotes from multiple manufacturers and evaluate the overall value, considering factors like durability, customization, and technical support, rather than focusing solely on the upfront cost.
By carefully evaluating these factors, you can choose a high temperature FRP pipe manufacturer that meets your specific requirements and delivers reliable products for demanding applications.
Key Considerations Before, During, and After Buying High Temperature FRP Pipe
When buying high temperature FRP pipes, careful evaluation is essential to ensure that the product meets your needs and performs reliably in your application. Below is a detailed guide divided into two parts: matters to consider before purchasing and during and after purchasing.
Matters to Consider Before Purchasing High Temperature FRP Pipe
Understand Your Application Requirements
- Clearly define the operating conditions, such as temperature range, pressure, chemical exposure, and fluid type. This will help you choose a pipe with the right specifications.
- Determine the pipe dimensions, length, and configuration needed for your system.
Verify Manufacturer Credibility
- Research potential manufacturers for experience, certifications, and industry reputation.
- Ensure they specialize in high temperature FRP pipes and have a proven track record in similar applications.
Check Material Specifications
- Ensure the pipe materials, such as the resin and reinforcement fibers, are suitable for high-temperature and corrosive environments.
- Verify the pipe’s resistance to the chemicals and physical stresses it will encounter.
Review Customization Options
- If your application has unique requirements, confirm that the manufacturer can customize the pipe design, size, or chemical resistance properties.
Evaluate Quality Assurance Processes
- Inquire about the manufacturer’s testing protocols, including tests for temperature resistance, pressure tolerance, and durability.
Compare Pricing and Delivery Terms
- Obtain quotes from multiple manufacturers to ensure competitive pricing.
- Assess the production capacity and delivery timeline to ensure the project schedule is not compromised.
Inspect Sample Products
- Request product samples or visit the manufacturer’s facility to assess the quality and finish of their FRP pipes.
Matters to Consider During and After Purchasing High Temperature FRP Pipe
Inspect the Delivered Products
- Upon delivery, check the pipes for any visible defects, such as cracks, uneven surfaces, or other signs of damage.
- Verify that the delivered products match the specifications agreed upon during the purchase.
Follow Installation Guidelines
- Ensure the installation team follows the manufacturer’s guidelines, including proper joint assembly and alignment techniques.
- Use the recommended adhesives, couplings, or fittings to maintain system integrity.
Plan for Proper Support Systems
- Install adequate pipe supports to prevent sagging or strain on joints, especially for long pipe runs or high-pressure systems.
Check for Compliance
- Confirm that the installed FRP pipe system complies with all local codes and industry standards.
Monitor Initial Operation
- After installation, closely monitor the system during its initial operation to detect any leaks, unusual noises, or other performance issues.
Schedule Regular Maintenance
- Establish a maintenance plan to inspect the pipes periodically for signs of wear, aging, or damage.
- Address minor issues promptly to prevent larger, costlier problems.
Maintain Records and Documentation
- Keep all documentation related to the purchase, including warranties, installation guidelines, and maintenance recommendations.
- These records are essential for future reference and warranty claims, if needed.
By paying attention to these factors before, during, and after purchasing high temperature FRP pipes, you can ensure a seamless buying experience and reliable long-term performance of your piping system.
Important Considerations When Using High Temperature FRP Pipe
When using high temperature FRP pipes, it is essential to follow specific guidelines to ensure their optimal performance and longevity. These considerations address factors related to installation, operation, and maintenance to maximize the benefits of this advanced material. Below are key points to keep in mind:
Temperature Limits
While high temperature FRP pipes are designed to withstand elevated temperatures, it is critical to adhere to the manufacturer’s specified maximum temperature limits. Prolonged exposure to temperatures beyond the pipe’s tolerance range can lead to degradation of the resin matrix, reducing the pipe’s structural integrity and performance.
Proper Support and Alignment
FRP pipes require adequate support to prevent sagging or misalignment, especially in long runs. Use appropriately spaced pipe supports to distribute the load evenly and avoid concentrated stresses. Proper alignment during installation is crucial to minimize strain on joints and connections, which could otherwise lead to leaks or failure over time.
Chemical Compatibility
Although high temperature FRP pipes are resistant to a wide range of chemicals, it is important to confirm their compatibility with the specific chemicals or fluids being transported. Certain aggressive substances or combinations may exceed the pipe’s resistance capacity, necessitating additional liners or coatings for protection.
Installation Environment
Pay attention to the environment during installation. High temperature FRP pipes should not be subjected to excessive bending or impact forces, as this can cause microcracks or damage to the pipe wall. Additionally, avoid direct contact with sharp or abrasive surfaces that might compromise the outer layer of the pipe.
Joint and Connection Integrity
Ensure proper assembly of joints and connections using the recommended adhesive or coupling techniques provided by the manufacturer. Improperly secured joints can lead to leaks or failures, especially under high-pressure or high-temperature conditions. Periodic inspection of joints is advisable to maintain system integrity.
Thermal Expansion and Contraction
FRP pipes, like most materials, expand and contract with temperature changes. Incorporate expansion joints or flexible couplings to accommodate thermal movement, particularly in systems with significant temperature fluctuations. This prevents undue stress on the pipe system and ensures long-term reliability.
Avoid Overloading
While high temperature FRP pipes are strong, they have specific load-bearing limits. Avoid exceeding these limits by accounting for internal pressure, fluid weight, and external loads during the design phase. Overloading can lead to deformation or premature failure of the pipe.
UV Protection
If the pipes are exposed to direct sunlight for extended periods, consider applying UV-resistant coatings or wraps. Prolonged UV exposure can degrade the outer layer of the FRP pipe, affecting its performance and lifespan.
Regular Inspection and Maintenance
Schedule regular inspections to identify and address potential issues such as surface damage, joint wear, or signs of aging. While FRP pipes are low-maintenance, early detection of minor problems can prevent more significant failures and reduce overall repair costs.
Compliance with Standards
Ensure that the FRP pipes meet relevant industry standards and certifications for your specific application. Adhering to these standards guarantees that the pipes are manufactured and installed to handle the operating conditions they will encounter.
By considering these matters, users can ensure the safe and effective use of high temperature FRP pipes, prolong their lifespan, and maximize their performance in industrial applications.
FAQs about High Temperature FRP Pipe
Yes, Fiber Reinforced Plastic (FRP) can withstand high temperatures, but the specific maximum temperature it can handle depends on the resin system used in the composition of the FRP. Generally, FRP is designed to endure sustained temperatures up to a certain point without losing its structural integrity or physical properties. High-temperature FRP pipes are specifically manufactured to handle elevated temperatures, making them suitable for use in industries like chemical processing, power generation, and exhaust systems. It is important to choose the right type of FRP material based on the specific temperature requirements of your application.
The temperature limit for FRP pipes can vary significantly depending on the resin type used in the manufacturing of the FRP. Typical epoxy resins can withstand up to approximately 300°F, while advanced phenolic resins might handle temperatures up to 350°F or more. Special high-performance resins have been developed that can endure even higher temperatures, but these materials may come at an increased cost. Always consult with the manufacturer for exact temperature ratings and ensure the FRP pipe’s suitability for your specific high-temperature application.
FRP is moderately heat resistant, making it a viable option for many applications that involve elevated temperatures. The degree of heat resistance, however, depends on the resin matrix and the reinforcement used in the FRP composite. High-temperature FRP pipes are specially fabricated with materials that enhance their thermal stability and resistance to heat degradation. For environments requiring resistance to very high temperatures, specific types of FRP with high-temperature resins should be used to ensure performance and durability.
For high-temperature applications, the best types of plastic pipes are typically those made from thermosetting plastics such as FRP (Fiber Reinforced Plastic) and CPVC (Chlorinated Polyvinyl Chloride). CPVC pipes are popular for hot water delivery as they can withstand temperatures up to about 200°F. FRP pipes, however, are superior when it comes to handling very high temperatures, often up to 300°F or more depending on the resin used. FRP offers the additional benefits of high strength and resistance to corrosion, making it an excellent choice for industrial applications involving high temperatures and aggressive chemicals.
FRP (Fiberglass Reinforced Plastic) pipes can typically withstand temperatures up to 200°F (93°C) under normal conditions. However, with specialized resin systems, such as epoxy or phenolic resins, they can handle temperatures as high as 300°F (149°C) for specific applications. The maximum temperature depends on the type of resin used in the pipe’s construction, as different resins exhibit varying thermal resistance. Beyond these limits, the structural integrity of the FRP pipe may deteriorate due to resin softening or thermal expansion mismatch between the resin and fiberglass. Manufacturers often provide specific thermal ratings and recommend operational limits to ensure long-term performance. For applications involving high-temperature fluids or gases, consulting with the manufacturer for a tailored solution is crucial. Additionally, thermal cycling and prolonged exposure to elevated temperatures should be considered, as these factors may reduce the pipe’s lifespan over time.
FRP can generally withstand temperatures ranging from -20°F (-29°C) to 200°F (93°C) in standard configurations. However, advanced resin systems such as vinyl ester, epoxy, or phenolic resins allow FRP to endure higher temperatures, up to 300°F (149°C) or more in specific cases. The actual thermal resistance depends on the resin-to-fiber ratio, fiber orientation, and operational environment. Prolonged exposure to extreme temperatures, particularly above the resin’s glass transition temperature (Tg), can lead to material degradation, reduced mechanical strength, and potential failure. It’s critical to consider the specific chemical and thermal environment, as exposure to high temperatures combined with aggressive chemicals can exacerbate damage. Thermal insulation layers can also be integrated into FRP systems to enhance temperature tolerance. Consulting the pipe manufacturer for the most suitable resin and configuration for high-temperature applications is essential to ensure reliability and safety.
For high-temperature applications, PEEK (Polyether Ether Ketone) and PPSU (Polyphenylsulfone) are among the best choices for plastic pipes. These materials can withstand temperatures exceeding 300°F (149°C) without significant loss of mechanical properties. PEEK, in particular, can handle continuous exposure to temperatures up to 480°F (250°C), making it ideal for extreme environments. PPSU offers excellent thermal stability and is widely used in industrial and medical applications. Alternatively, CPVC (Chlorinated Polyvinyl Chloride) is a more cost-effective option, with a maximum service temperature of around 200°F (93°C). When selecting a high-temperature plastic pipe, considerations such as thermal expansion, chemical resistance, and mechanical stress should be factored in. For applications requiring a combination of strength and thermal resistance, FRP pipes with high-performance resins are also a competitive option, blending the advantages of composites with heat-resistant properties.
One of the primary challenges with FRP pipes is their susceptibility to damage under prolonged exposure to extreme temperatures beyond their design limits. High temperatures can soften the resin, leading to reduced mechanical strength and potential deformation. Additionally, FRP pipes are vulnerable to thermal cycling, which can cause microcracks and delamination over time. Chemical compatibility is another issue; certain aggressive chemicals may degrade the resin matrix, compromising structural integrity. Mechanical vulnerabilities, such as susceptibility to impact damage, can also be a concern during installation or operation. While FRP pipes offer excellent corrosion resistance, improper fabrication or installation can lead to joint failures or leaks. Cost can be a factor, as high-performance resin systems for better temperature tolerance increase expenses. Proper design, installation, and regular maintenance are crucial to mitigating these challenges and ensuring the long-term performance of FRP piping systems.
Fiberglass itself, as a reinforcement material, can withstand extremely high temperatures, typically up to 1000°F (538°C) without melting. However, the overall heat resistance of an FRP pipe is limited by the resin system used to bond the fiberglass. Standard resins, like polyester, cap the operating temperature around 200°F (93°C), while specialized resins, such as epoxy or phenolic, extend the range to approximately 300°F (149°C). At elevated temperatures, the resin is the weak link, as it softens, loses adhesion, or degrades chemically. In contrast, the fiberglass remains stable but may lose its structural function if the resin matrix deteriorates. For applications requiring extreme heat resistance, silica or ceramic fibers may be used as alternatives to traditional fiberglass. Incorporating thermal barriers and selecting high-temperature resins can significantly enhance the heat tolerance of fiberglass-reinforced systems for demanding applications.
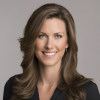
As the editor of GangLong Fiberglass, I have years of experience and in-depth research, focusing on cable tray products, fiberglass solutions, and grille systems. I incorporate years of industry insights and practical experience into every content, committed to promoting the progress of the industry. At GangLong Fiberglass, my commitment is reflected in every product, from innovative cable trays to durable fiberglass solutions and sturdy grille systems. As an authoritative voice in the industry, my goal is to provide valuable information to professionals and businesses and promote forward-looking solutions.