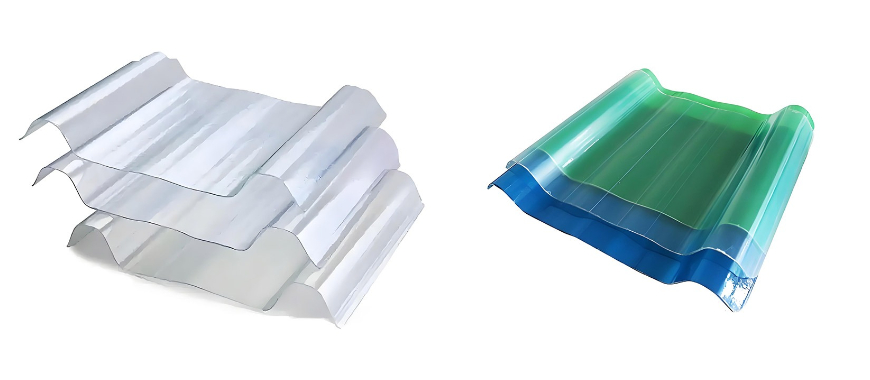
Fiberglass Reinforced Plastic (FRP) panels are composite materials made from fiberglass and resin, often reinforced with additional materials to enhance their strength and durability. These panels are widely used in various industries, including construction, agriculture, and petrochemicals, due to their versatility and excellent performance under harsh conditions. Lows fiberglass reinforced plastic pannel, for example, offers outstanding resistance to moisture, corrosion, and environmental stress, making it ideal for both indoor and outdoor applications. The importance of selecting the right FRP panels cannot be overstated, as they provide critical benefits such as long-lasting durability, superior moisture resistance, and the ability to withstand extreme temperatures. Proper selection ensures the longevity and efficiency of structures in demanding environments.
Why Choose Lows Fiberglass Reinforced Plastic Pannel?
Fiberglass Reinforced Plastic (FRP) panels have become an essential material in various industries due to their remarkable combination of durability, strength, and resistance to harsh conditions. The Lows fiberglass reinforced plastic pannel, in particular, offers several advantages that make it a top choice for construction, agriculture, and chemical industries. Let’s explore why these panels are favored across multiple applications.
Lows Fiberglass Reinforced Plastic Pannel: Durability and Strength in Challenging Environments
Lows fiberglass reinforced plastic pannel is known for its exceptional strength and resilience. These panels are designed to withstand heavy impacts, making them ideal for environments where materials are exposed to physical stress. Whether in construction, transportation, or manufacturing, FRP panels can resist cracking or breaking, even when subjected to high loads or extreme weather conditions. This makes them an excellent long-term investment, as they require minimal maintenance while providing continued performance.
Corrosion Resistance
One of the standout features of the Lows fiberglass reinforced plastic pannel is its resistance to corrosion. Unlike traditional metal panels that can degrade quickly when exposed to moisture or harsh chemicals, FRP panels are naturally resistant to corrosion. This quality makes them especially valuable in areas with high moisture content, such as agricultural facilities, or in environments where exposure to chemicals or salts is common, such as petrochemical plants. The ability of FRP to maintain its integrity under such conditions ensures that it outperforms many other materials, making it a durable and reliable choice.
Fire Resistance
Another key advantage of certain types of Lows fiberglass reinforced plastic panel is their fire resistance. Many FRP panels are designed with fire-retardant properties, offering crucial protection in environments where fire safety is a concern. These panels typically come with fire ratings that ensure they meet specific standards, preventing the spread of flames in case of fire. This fire-resistant characteristic makes them highly suitable for use in industrial applications, warehouses, and other places where fire hazards are prevalent.
The Lows fiberglass reinforced plastic pannel offers a combination of durability, corrosion resistance, and fire resistance, making it a superior choice for a wide range of applications. Choosing the right FRP panel can significantly enhance the longevity and safety of structures, ensuring they stand up to the toughest environmental and operational challenges.
Is Fiberglass Reinforced Plastic Flammable? Fire Safety Explained
Types of Lows Fiberglass Reinforced Plastic Pannel Available
Fiberglass Reinforced Plastic (FRP) panels are available in a variety of styles and configurations to meet the diverse needs of different industries and applications. The Lows fiberglass reinforced plastic pannel, for example, comes in several types, each offering distinct features to suit specific environmental and operational requirements. Below, we explore the most common types of FRP panels and their benefits.
Smooth White FRP Panels
Smooth white FRP panels are one of the most popular choices for applications in kitchens, bathrooms, and other high-humidity areas. These panels are typically smooth and glossy, providing a sleek and modern appearance. The smooth surface not only enhances the aesthetic appeal but also facilitates easy cleaning, which is essential in environments where hygiene is a priority. In addition, Lows fiberglass reinforced plastic pannel in smooth white is resistant to moisture, preventing mold and mildew buildup, making it a preferred option for areas exposed to frequent water exposure.
Textured FRP Panels
Textured FRP panels, as the name suggests, feature a textured surface that provides an added level of grip and aesthetic appeal. These panels are often used in applications where both functionality and appearance are important, such as in commercial kitchens, public restrooms, or industrial settings. The texture not only enhances the visual appeal of the installation but also increases slip resistance, making it a safer choice for areas where wet or slippery conditions may occur. The Lows fiberglass reinforced plastic pannel with textured surfaces offers both durability and enhanced safety, making it ideal for high-traffic areas.
Other Features
Lows fiberglass reinforced plastic pannel offers a range of additional features that enhance its functionality. These panels are typically waterproof, making them highly resistant to water damage and ideal for use in wet environments such as food processing facilities, swimming pools, or agricultural buildings. Furthermore, many FRP panels are UV-resistant, meaning they can withstand prolonged exposure to sunlight without fading, cracking, or losing strength. This makes them a great option for outdoor applications, such as roofing and exterior wall cladding. The ease of cleaning is another important feature, as FRP panels generally require minimal maintenance and can be wiped down easily, ensuring a hygienic and aesthetically pleasing environment.
The Lows fiberglass reinforced plastic panel comes in various types designed to meet the specific needs of different industries. Whether you require smooth white panels for high-humidity environments or textured panels for enhanced grip and visual appeal, FRP panels offer versatile solutions with added benefits like waterproofing, UV resistance, and easy maintenance. These features make Lows fiberglass reinforced plastic pannel a reliable choice for a wide range of applications.
Grounding Fiberglass Reinforced Plastic: Safety Considerations
Reinforced Plastic Panel Selection for Lows Fiberglass Reinforced Plastic Pannel
When selecting the right Lows fiberglass reinforced plastic pannel for a particular project, several factors must be considered. These include the size of the panels, cost-effectiveness in comparison to other materials, and customer feedback regarding performance and reliability. Below, we explore these important aspects in detail to help guide the decision-making process.
Different Panel Sizes and Their Typical Uses
Lows fiberglass reinforced plastic pannel comes in a variety of sizes to accommodate different applications. The most common sizes are 4×8 and 4×10 feet, although custom sizes are often available for specialized needs. Below is a breakdown of these panel sizes and their typical uses:
Panel Size | Typical Use |
---|---|
4x8 feet | Ideal for smaller residential or commercial spaces, such as bathrooms, kitchens, and storage rooms. |
4x10 feet | Used for larger areas requiring fewer seams, such as warehouse walls, industrial facilities, and agricultural buildings. |
Lows fiberglass reinforced plastic panel in these sizes is perfect for both wall and ceiling applications, providing durability, moisture resistance, and ease of installation. The 4×8 panels are particularly popular for smaller residential or light commercial projects, while the 4×10 panels are often chosen for larger commercial or industrial applications, reducing the number of seams and improving aesthetics.
Cost-Effectiveness Compared to Other Materials
When comparing the cost-effectiveness of Lows fiberglass reinforced plastic panel to other common materials like plywood, metal, or drywall, it becomes clear that FRP panels offer long-term savings despite a slightly higher initial cost. While plywood and drywall might seem less expensive upfront, they often require more frequent repairs, maintenance, and replacement due to wear and tear. On the other hand, the durability, resistance to moisture, and ease of cleaning of FRP panels reduce the need for costly repairs over time. Below is a comparison of the typical costs and benefits of each material:
Material | Initial Cost | Durability | Maintenance Cost | Suitability for Moisture-Prone Areas |
---|---|---|---|---|
Lows Fiberglass Reinforced Plastic Panel | Moderate to High | Very High | Low | Excellent |
Plywood | Low | Moderate | Moderate to High | Poor to Moderate |
Metal (Steel or Aluminum) | High | High | Moderate | Excellent |
Drywall | Low | Low to Moderate | High | Poor |
As shown, Lows fiberglass reinforced plastic pannel is more cost-effective in the long run due to its low maintenance needs and high durability, especially in environments with high moisture or chemical exposure. Although the initial cost might be higher than plywood or drywall, the extended lifespan and minimal upkeep needed make it a more economical choice for many commercial, industrial, and residential applications.
Customer Reviews and Ratings
Customer feedback on Lows fiberglass reinforced plastic panel is generally positive, with many users praising its strength, ease of installation, and resistance to moisture. Many have found it to be a reliable material for both residential and commercial projects. Below are some key insights from customer reviews:
Positive Experiences:
- Durability: Customers frequently highlight the exceptional durability of Lows fiberglass reinforced plastic pannel. It stands up well to harsh environments, including high humidity and exposure to chemicals, making it an ideal choice for commercial kitchens, agricultural facilities, and industrial buildings.
- Easy to Clean: Many users appreciate how easy it is to clean the smooth surface of the panels. This is particularly important in spaces that require high levels of hygiene, such as hospitals or food processing areas.
- Cost Efficiency: Customers have found Lows fiberglass reinforced plastic panel to be a cost-effective option when considering long-term durability and reduced maintenance costs.
Common Concerns:
- Installation: Some customers note that while the panels are relatively easy to install, cutting and handling them can be a bit tricky, particularly in confined spaces or for those with less experience working with FRP materials.
- Initial Cost: A few customers have mentioned that the initial cost of Lows fiberglass reinforced plastic panel is higher compared to traditional materials like drywall or plywood. However, many acknowledge that the benefits in terms of durability and maintenance savings justify the higher upfront investment.
Lows fiberglass reinforced plastic pannel is a strong contender for various applications due to its durability, cost-effectiveness, and positive customer feedback. Whether you’re looking to install panels in a high-moisture area or need a reliable solution for an industrial setting, this product provides both long-term value and high performance.
How to Access Fiberglass Bass Boat Plans PDF for Building
Applications of Lows Fiberglass Reinforced Plastic Pannel
Lows fiberglass reinforced plastic pannel is a versatile material with a wide range of applications across various sectors. Thanks to its durability, moisture resistance, and easy maintenance, these panels are widely used in both residential and commercial environments, as well as in industrial settings where toughness and longevity are essential. Below, we discuss some of the most common applications of FRP panels.
Home Applications
Lows fiberglass reinforced plastic panel is an excellent choice for use in residential areas, particularly in spaces that are exposed to high moisture levels. In bathrooms, kitchens, and garages, these panels provide waterproof, mold-resistant properties that make them ideal for environments where other materials might deteriorate quickly. For instance, in bathrooms, the Lows fiberglass reinforced plastic pannel offers a moisture barrier that prevents water from seeping into walls, avoiding potential mold growth and long-term damage.
Similarly, in kitchens, where spills, humidity, and grease are common, these panels offer a low-maintenance solution that’s easy to wipe clean and resistant to staining. Garages, often exposed to humidity or potential chemical spills, can benefit from the durability and chemical resistance of these panels, keeping surfaces intact for years. The smooth and waterproof nature of Lows fiberglass reinforced plastic pannel makes these installations both functional and aesthetically appealing, enhancing the longevity of spaces prone to moisture.
Industrial Applications
In industrial settings, Lows fiberglass reinforced plastic panel is used extensively in factories, warehouses, and chemical plants. These environments often involve exposure to harsh chemicals, moisture, and extreme conditions, making Lows fiberglass reinforced plastic pannel the ideal material for these types of applications.
In factories and warehouses, the robust nature of FRP panels helps resist wear and tear from heavy machinery, impact, and foot traffic. The panels’ strength and resistance to chemicals ensure that they maintain their integrity even in aggressive environments. Moreover, their ability to withstand exposure to high levels of humidity or corrosive substances makes them perfect for use in chemical plants and manufacturing facilities, where metal or wood would quickly degrade.
The installation of Lows fiberglass reinforced plastic pannel in these industrial environments helps protect structural components from damage while providing a long-lasting, cost-effective solution. The corrosion resistance of these panels also reduces the need for frequent replacements, saving businesses time and money.
Commercial Uses
Lows fiberglass reinforced plastic panel plays a vital role in commercial settings, particularly in industries that require high hygiene standards. These include food processing areas, hospitals, schools, and other public spaces.
In food processing plants, the panels’ smooth, non-porous surface makes them highly effective at preventing the buildup of bacteria, mold, or other contaminants. Since these surfaces are easy to clean, maintaining a high level of sanitation becomes much easier, helping businesses comply with health and safety regulations. Additionally, Lows fiberglass reinforced plastic panel is resistant to food acids and oils, making it an ideal choice for kitchens and food handling areas.
In hospitals and healthcare facilities, hygiene is a top priority, and the antimicrobial properties of Lows fiberglass reinforced plastic panel help prevent the growth of harmful pathogens. These panels are also durable enough to withstand the frequent cleaning processes necessary in medical environments without deteriorating over time.
Schools and educational institutions benefit from the use of Lows fiberglass reinforced plastic pannel in classrooms, corridors, and other high-traffic areas. Their ability to resist staining, moisture, and wear makes them a practical solution for areas that see heavy use, while also ensuring that the space remains clean and hygienic. Moreover, the ease of installation and low maintenance needs are additional advantages in commercial settings where time and resources are limited.
The versatility of Lows fiberglass reinforced plastic pannel makes it an essential material across a wide array of applications. Whether it’s used in residential spaces, industrial environments, or commercial facilities, the durability, moisture resistance, and ease of maintenance offered by these panels make them an excellent choice for a variety of demanding environments. From bathrooms and kitchens to food processing plants and hospitals, Lows fiberglass reinforced plastic panel ensures reliable, long-lasting performance.
Installation Tips for Lows Fiberglass Reinforced Plastic Pannel
Proper installation of Lows fiberglass reinforced plastic pannel ensures optimal performance, longevity, and durability. Whether you are installing these panels in a residential, industrial, or commercial setting, careful attention to the installation process will result in better adhesion, a more aesthetically pleasing finish, and extended service life. Below, we outline key pre-installation considerations, step-by-step installation instructions, and maintenance tips to ensure your Lows fiberglass reinforced plastic pannel performs at its best.
Pre-Installation Considerations
Before beginning the installation of Lows fiberglass reinforced plastic panel, it is crucial to plan and prepare for a smooth and long-lasting setup. Below are some essential pre-installation tips to consider:
Choosing the Right Adhesive and Sealants
Selecting the correct adhesive and sealants is vital for ensuring strong adhesion and durability. Lowes fiberglass reinforced plastic (FRP) panel typically requires a high-strength adhesive that is specifically formulated for use with FRP materials. When asking what adhesive to use on fiberglass reinforced plastic, a polyurethane or epoxy-based adhesive is often recommended, as these products bond well with fiberglass and provide strong, long-lasting adhesion. Additionally, make sure the sealants used for joints and seams are moisture-resistant to prevent water infiltration and maintain the integrity of the installation.
Preparing the Surface for Optimal Adhesion and Longevity
Proper surface preparation is essential to achieving a durable and secure installation. The surface to which the Lows fiberglass reinforced plastic pannel will be adhered should be clean, dry, and smooth. Any dirt, dust, grease, or moisture must be removed before installation to prevent poor adhesion and ensure the panels stay in place. If the surface is uneven, use a leveling compound to create a smooth, even base. For the best results, the surface should also be free of any mold or mildew to prevent future growth after the panels are installed.
Step-by-Step Installation Guide
Once you’ve completed the necessary preparations, follow these step-by-step instructions for installing Lows fiberglass reinforced plastic panel on walls or ceilings:
- Measure and Mark: Begin by measuring the area where the panels will be installed. Use a level to draw a straight reference line along the area to ensure that the panels are aligned correctly. For ceiling installations, ensure that the spacing is appropriate to support the weight of the panels.
- Cutting the Panels: To fit the Lows fiberglass reinforced plastic pannel into your space, you may need to cut the panels. Use a fine-toothed saw or a utility knife with a scoring tool to cut the panels. If you need to cut around obstacles like pipes or outlets, measure carefully and use a jigsaw for more complex cuts. Always wear protective gloves and eyewear when cutting to avoid injury.
- Applying Adhesive: Apply the adhesive evenly across the surface where the panel will be mounted. Use a notched trowel to spread the adhesive in thin, consistent layers. Make sure the adhesive coverage is complete to ensure strong bonding.
- Positioning the Panels: Carefully press the Lows fiberglass reinforced plastic panel onto the prepared surface. Start at one edge and press the panel firmly into place, moving across the entire panel to avoid air bubbles or gaps. For larger panels, you may need to secure the panels temporarily with adhesive strips or tacky glue until the main adhesive sets.
- Sealing Joints and Edges: Once the panels are securely attached, seal all joints, seams, and edges with a silicone-based sealant to prevent water or moisture from seeping behind the panels. Apply the sealant smoothly and evenly, making sure to fill any gaps. Allow the sealant to cure fully before using the space.
- Finishing Touches: Once all panels are installed, add finishing trims or moldings as necessary. This will provide a clean, professional look while also securing the edges of the panels.
Maintenance and Care
Proper maintenance and care will ensure that your Lows fiberglass reinforced plastic pannel remains functional and attractive over time. Here are some tips to keep your panels in top condition:
Tips on Cleaning
Lows fiberglass reinforced plastic pannel is easy to clean, which is one of its major benefits. Use a mild soap solution or non-abrasive cleaner to wipe down the surface regularly. For tougher stains, a gentle scrub with a soft brush may be required. Avoid using harsh chemicals or abrasive cleaners, as they can damage the surface of the panels.
Preventing Scratches
Although FRP panels are highly durable, it is still important to prevent scratches that could mar the surface. When cleaning, use a soft cloth or sponge to avoid scratching. Additionally, avoid using sharp or rough tools when working near the panels. If you need to place objects on the panel surface, ensure they are placed gently to avoid gouging or denting.
Maintaining Long-Lasting Performance
To maintain the long-lasting performance of your Lows fiberglass reinforced plastic panel, perform routine checks for any signs of damage, such as cracking or peeling. If any damage is found, repair it promptly to prevent further issues. Keep the panels free from excessive moisture buildup behind them by ensuring proper ventilation, especially in high-humidity areas like bathrooms or kitchens. Regular maintenance will extend the life of your panels and preserve their performance in the long run.
Proper installation and maintenance of Lows fiberglass reinforced plastic pannel are essential to achieving optimal results and ensuring the panels provide years of reliable service. By selecting the right adhesives, preparing the surface properly, following step-by-step installation guidelines, and maintaining the panels with care, you can ensure that your Lows fiberglass reinforced plastic pannel will perform well and look great for many years to come.
FAQs about Lows Fiberglass Reinforced Plastic Pannel
While FRP (Fiberglass Reinforced Plastic) panels offer numerous benefits, they also come with certain disadvantages. One of the primary drawbacks is the initial cost. Compared to traditional materials like plywood or drywall, FRP panels are generally more expensive upfront. While their long-term durability can offset this initial investment, the higher initial price may be a barrier for some budget-conscious projects.
Another disadvantage is that cutting and handling FRP panels can be challenging. They require specific tools, such as a fine-toothed saw or a utility knife, to ensure clean cuts. Incorrect handling or cutting can lead to cracks or chips along the edges, which may require additional work.
Additionally, UV degradation is a concern, especially in outdoor environments. While FRP panels are resistant to many chemicals and moisture, prolonged exposure to direct sunlight can cause the material to fade or weaken unless UV-resistant coatings are applied.
Lastly, aesthetic limitations may be a drawback for some users. While modern FRP panels come in a variety of colors and textures, they may not always meet aesthetic preferences for all applications, particularly in high-end residential design where natural wood or other materials are preferred.
For those seeking a cheaper alternative to FRP panels, plywood or MDF (Medium-Density Fiberboard) can be cost-effective options. Plywood, in particular, is widely available and offers a relatively low cost compared to FRP, making it a common choice for interior applications like cabinetry, paneling, and flooring. While plywood is not as moisture-resistant as FRP, it can be treated with waterproof sealants to improve its performance in wet environments.
Another cheaper alternative is drywall, which is often used in residential construction for walls and ceilings. Drywall is relatively inexpensive and provides a smooth, paintable surface. However, it is not as durable as FRP and is more susceptible to water damage, mold growth, and impact damage.
Vinyl panels can also be a more affordable option, especially for interior wall applications. Vinyl is cheaper than FRP, though it doesn’t offer the same level of durability or resistance to harsh chemicals. It is more suitable for applications that do not require high impact or chemical resistance.
While these alternatives are generally more budget-friendly, they may not match FRP in terms of long-term durability, resistance to moisture, or ease of maintenance.
Fiberglass Reinforced Plastic (FRP) has many advantages, but it also has some notable disadvantages. One of the biggest concerns is the environmental impact. Manufacturing FRP panels involves the use of fiberglass and synthetic resins, which are not biodegradable. Disposal of FRP panels at the end of their life cycle can be challenging, as they are not easily recyclable, contributing to environmental waste.
Health risks associated with fiberglass are another disadvantage. When cutting or sanding FRP panels, tiny fiberglass particles can be released into the air. These particles can irritate the skin, eyes, and respiratory system if proper safety measures (like wearing protective gear) are not followed.
Additionally, cost is another significant drawback. While FRP panels are durable and long-lasting, they typically come at a higher initial price compared to traditional materials such as plywood or drywall. This may not make them a viable option for every budget, particularly in large-scale or commercial applications.
Finally, installation complexity can be a disadvantage for DIY enthusiasts. Cutting and handling FRP panels require specialized tools, and the installation process can be labor-intensive, particularly when dealing with large panels or intricate designs.
Fiberglass Reinforced Plastic (FRP) is a highly versatile and durable material that offers a range of benefits for various applications, making it a good option in many situations. It excels in resistance to moisture, chemicals, and corrosion, making it ideal for environments like bathrooms, kitchens, industrial facilities, and chemical plants where these factors can cause damage to other materials. FRP panels are lightweight yet strong, offering superior performance under impact while remaining easy to handle during installation.
Additionally, FRP panels are known for their low maintenance requirements. They are easy to clean and maintain, with a smooth, non-porous surface that resists mold and mildew growth. This makes them especially suitable for spaces where hygiene is a priority, such as hospitals, food processing areas, and schools.
However, like any material, FRP has limitations. While it is durable, it is not impervious to UV radiation, which can cause fading and degradation over time unless treated with UV-resistant coatings. Additionally, the initial cost can be higher than some other materials, which may be a consideration for budget-conscious projects.
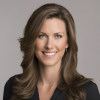
As the editor of GangLong Fiberglass, I have years of experience and in-depth research, focusing on cable tray products, fiberglass solutions, and grille systems. I incorporate years of industry insights and practical experience into every content, committed to promoting the progress of the industry. At GangLong Fiberglass, my commitment is reflected in every product, from innovative cable trays to durable fiberglass solutions and sturdy grille systems. As an authoritative voice in the industry, my goal is to provide valuable information to professionals and businesses and promote forward-looking solutions.