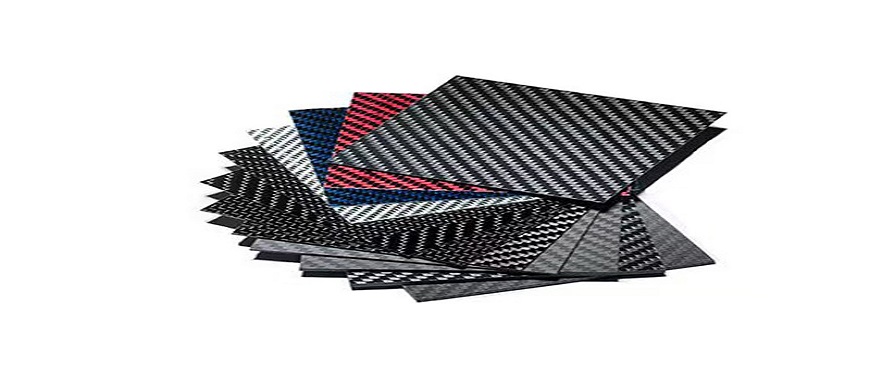
Carbon fiber and fiberglass are two of the most widely used materials in composite manufacturing, offering exceptional strength and durability. Both materials play a critical role across various industries, including automotive, aerospace, sports, and construction, due to their lightweight yet strong properties. While carbon fiber is known for its superior strength-to-weight ratio, fiberglass is renowned for its versatility and cost-effectiveness. This article will focus on comparing carbon fiber and fiberglass density, two key factors that significantly influence the performance, cost, and application of these materials. By understanding the differences in carbon fibre and fiberglass density, manufacturers and engineers can make informed decisions based on specific project needs and material requirements.
Fiberglass and Carbon Fibre and Fiberglass Density: A Weight and Density Comparison
Understanding the carbon fibre and fiberglass density is crucial for making informed decisions in material selection for various applications. Both materials are widely used in composite manufacturing due to their unique properties, but their differences in density significantly influence their weight, strength, and performance in different environments. In this section, we will explore the density ranges of both fiberglass and carbon fiber, and how their weight differences impact real-world applications like vehicles, sports gear, and structural components.
Fiberglass Density
Fiberglass is one of the most commonly used composite materials due to its strength, versatility, and relatively low cost. The typical density of fiberglass, specifically E-glass, ranges around 2.55 g/cm³. This relatively high density, compared to some other composites, directly influences the material’s weight and strength characteristics.
Impact of Fiberglass Density on Weight and Strength
The fiberglass density is a key factor in determining the material’s overall weight. Its density ensures that fiberglass remains strong and durable, making it ideal for applications where durability and resistance to wear are prioritized over lightweight properties. For example, fiberglass is frequently used in boat hulls, industrial tanks, and insulation materials, where strength and longevity are more important than reducing weight.
While it’s heavier than carbon fiber, fiberglass’s cost-effectiveness and ability to endure harsh environments make it the material of choice for certain applications. Moreover, its relatively low density provides a good balance between strength and weight for applications that don’t demand extreme weight reduction, such as in construction or automotive industries.
Carbon Fiber Density
Carbon fiber, on the other hand, offers a much lower density, typically around 1.55 g/cm³ for standard carbon fiber. This difference in density gives carbon fiber a remarkable strength-to-weight ratio, making it a superior choice for industries where performance and weight reduction are critical.
The Relationship Between Carbon Fiber Density and Its Strength-to-Weight Ratio
Carbon fiber’s low carbon fibre and fiberglass density results in a significantly lighter material, while its high tensile strength allows it to maintain superior strength despite the reduced weight. This makes carbon fiber an excellent choice for high-performance applications such as aerospace, automotive, and sports equipment, where reducing weight is essential without sacrificing strength. The low density of carbon fiber allows manufacturers to produce lightweight yet extremely strong components that enhance fuel efficiency, speed, and overall performance.
Weight Difference: Carbon Fiber vs Fiberglass in Real-World Applications
Let’s compare the overall weight and flexibility of carbon fiber and fiberglass across various real-world applications.
Application | Carbon Fiber | Fiberglass |
---|---|---|
Vehicles (e.g., car panels) | Lightweight, high strength | Heavier, but durable |
Sports Gear (e.g., bicycles) | Extremely light, stiff | Heavier, but more flexible |
Aerospace Components | Low weight, high strength | Heavier, less ideal for weight-sensitive parts |
Structural Components (e.g., bridges) | Light, high performance | Durable, cost-effective but heavier |
Flexibility and Weight in Structural Components
While carbon fiber offers an excellent strength-to-weight ratio, fiberglass is often used in structural components where its weight, though higher, is less of a concern compared to cost and durability. For instance, fiberglass might be preferred for constructing less weight-sensitive structures like certain types of pipes, tanks, or boat hulls, where long-term durability is the priority. In contrast, carbon fiber is often chosen for aerospace or automotive components, where even a small reduction in weight can lead to significant performance benefits.
Understanding the fiberglass carbon fiber density is essential for selecting the right material for a given application. Carbon fiber excels in performance-driven applications due to its lightness and strength, while fiberglass continues to be a reliable choice for applications requiring durability at a more affordable cost.
Key Advantages of Fiberglass Reinforced Plastic Sign Solutions
Fiberglass and Carbon Fibre and Fiberglass Density: A Comparison with Kevlar for Performance
When evaluating materials for high-performance applications, it’s crucial to consider not only the strength and durability but also the density and weight of the fibers used. This section will explore how carbon fibre and fiberglass density compare to Kevlar, another popular material in the composite industry. By understanding the distinct characteristics of these three fibers—carbon fiber, fiberglass, and Kevlar—engineers and manufacturers can make informed decisions about which material best suits their specific needs.
Kevlar Fiber Overview
Kevlar is a high-strength synthetic fiber made from the aromatic polyamide family, widely known for its impressive strength and impact resistance. With a density of around 1.44 g/cm³, Kevlar is significantly lighter than both carbon fiber and fiberglass, giving it unique properties that are especially advantageous in certain applications.
Density, Weight, and Strength Balance in Kevlar
The relatively low carbon fibre and fiberglass density compared to Kevlar means that while Kevlar is extremely light, it also provides outstanding tensile strength, making it an ideal material for use in protective gear, armor, and some aerospace applications. Its low density doesn’t come at the expense of strength—Kevlar’s molecular structure allows it to absorb and dissipate energy effectively, which is why it is often used in body armor and ballistic applications.
In terms of balance, Kevlar offers an attractive trade-off: its low density makes it lighter than fiberglass, but it is not as stiff as carbon fiber, which can be both a strength and a limitation depending on the application. While it is not as stiff or strong as carbon fiber in load-bearing applications, its superior impact resistance makes it an excellent choice for protective equipment.
Applications of Each Fiber
Let’s compare how carbon fiber, fiberglass, and Kevlar are applied across various industries, based on their density, weight, and performance characteristics.
Carbon Fiber Applications
- Automotive Industry: Carbon fiber is often used in automotive parts like body panels, frames, and interior components, where reducing weight is essential for improving performance, fuel efficiency, and speed. Its low density gives it a clear advantage in weight-sensitive areas without sacrificing strength.
- Aerospace: In aerospace components, carbon fiber is crucial for making lightweight, high-strength parts such as wings, fuselages, and interior structures. The carbon fibre and fiberglass density is carefully considered to achieve the necessary balance between weight and structural integrity.
- Sports Equipment: Carbon fiber is commonly found in sports gear like bicycles, tennis rackets, and golf clubs. Its lightweight yet stiff nature offers high performance, especially in competitive sports, where reducing weight can improve speed and maneuverability.
Fiberglass Applications
- Construction and Infrastructure: Fiberglass is commonly used for making pipes, tanks, and insulating materials. While it is heavier than carbon fiber and Kevlar, its density ensures durability and resistance to environmental factors. The material is cost-effective and provides excellent strength in structures that don’t require the extreme weight savings offered by carbon fiber.
- Boating and Marine: Fiberglass is the go-to material for building boat hulls, where its relatively high density offers a good balance between strength, durability, and cost. Although not as light as carbon fiber, its durability and ease of manufacturing make it a preferred choice for boat builders.
- Wind Energy: Fiberglass is also used in wind turbine blades, where its density and strength are well-suited for handling the stresses of wind power generation.
Kevlar Applications
- Protective Gear: Kevlar is most famous for its use in personal protective gear like bulletproof vests, helmets, and gloves. Due to its low density, it allows for lightweight yet extremely durable protection from impact, cuts, and abrasions. The combination of low weight and high impact resistance makes it ideal for military and law enforcement applications.
- Automotive Parts: While Kevlar is not typically used for structural components in vehicles, it is often integrated into tires, brake pads, and other components that require impact resistance and durability without adding significant weight.
- Aerospace and Defense: Kevlar’s lightweight and high-strength properties make it useful in aircraft and defense applications, particularly for components that must resist high-speed impacts, like aircraft skins and military vehicle armor.
Complementary Roles: Carbon Fiber, Fiberglass, and Kevlar
Each of these fibers has distinct strengths, and they are often used together in hybrid composites to take advantage of their complementary properties. For instance, a combination of carbon fibre and fiberglass density may be used in a part where carbon fiber provides high stiffness and strength, while fiberglass offers flexibility and impact resistance. Similarly, adding Kevlar to a carbon fiber composite can enhance the material’s impact resistance and toughness without significantly increasing the weight.
- Hybrid Composites in Aerospace: Carbon fiber can be used for strength, fiberglass for impact resistance, and Kevlar for energy absorption. This combination allows aerospace manufacturers to optimize weight, strength, and durability for critical components.
- Protective Gear: In ballistic vests, layers of Kevlar are often combined with carbon fiber or fiberglass to maximize protection while minimizing weight. The density of Kevlar provides energy absorption, while the stiffness of carbon fiber or the flexibility of fiberglass ensures the composite performs well under various conditions.
The carbon fibre and fiberglass density plays a crucial role in determining the performance and suitability of these materials for specific applications. While carbon fiber offers the best strength-to-weight ratio, Kevlar’s low density and high impact resistance, along with fiberglass’s versatility and durability, allow manufacturers to choose the right fiber—or combination of fibers—based on the performance, cost, and weight requirements of the project. Each material excels in different areas, and their complementary properties often make them ideal for use in combination across industries.
Safer Cleaning Alternatives To Pumice Stone On Fiberglass Tub
Cost Comparison: Fiberglass and Carbon Fibre and Fiberglass Density
When choosing between fiberglass and carbon fiber for a particular application, cost is a key factor to consider, along with the carbon fibre and fiberglass density. While both materials offer distinct benefits in terms of strength, weight, and durability, their cost structures differ significantly. This section will delve into the cost comparison between fiberglass and carbon fiber, explore the reasons behind their price differences, and discuss how density impacts the cost-performance balance of each material.
Fiberglass Cost
Fiberglass is one of the most affordable composite materials on the market, particularly when compared to carbon fiber. The manufacturing process for fiberglass is relatively simple and cost-effective, contributing to its lower price point. Fiberglass is produced by melting glass and pulling it into thin fibers, which are then woven into cloth or used as reinforcement in composite materials. This mass production capability allows manufacturers to produce large quantities at a low cost, making it ideal for applications where cost is a primary concern.
Cost-Effectiveness in Mass Production
The carbon fibre and fiberglass density also plays a role in the cost structure of fiberglass. Because fiberglass is denser and heavier than carbon fiber, it’s generally less expensive to produce. Its density allows for the creation of larger, bulkier products at a lower cost compared to the more lightweight, high-performance carbon fiber. Applications that don’t require the extreme weight savings or high performance of carbon fiber, such as boat hulls, construction materials, and insulation, are well-suited for fiberglass due to its cost-effectiveness in mass production.
For example, in the marine industry, fiberglass is the preferred choice for boat hulls, where durability and strength are necessary but weight reduction is not as critical. Similarly, fiberglass is commonly used in building materials like pipes, tanks, and insulation, where its strength and versatility make it an ideal and affordable choice.
Carbon Fiber Cost
While fiberglass is relatively affordable, carbon fiber is significantly more expensive. The primary reason for this cost difference is the complex production process involved in creating carbon fiber. Carbon fiber is produced through a highly controlled process where organic polymers (like polyacrylonitrile) are spun into fibers and then heated to high temperatures in an oxygen-free environment (carbonization). This process is energy-intensive and requires specialized equipment, which adds to the material’s overall cost.
Justification for Higher Cost
The high cost of carbon fiber is justified by its superior performance characteristics. Despite its carbon fibre and fiberglass density being lower than fiberglass, carbon fiber offers exceptional strength, stiffness, and lightweight properties. These qualities make it indispensable for high-end applications, such as aerospace, automotive, and high-performance sports equipment, where the need for both strength and lightweight design is critical. For example, in aerospace, carbon fiber is used in the construction of aircraft components, where even a small reduction in weight can lead to significant performance improvements and fuel efficiency. In the automotive industry, carbon fiber is used in high-performance car parts, where its lightweight nature helps to improve speed and handling.
The superior strength-to-weight ratio of carbon fiber makes it an essential material for industries where performance and safety are paramount, such as in race cars, military vehicles, and medical equipment. The cost is a trade-off for the incredible performance benefits it offers in these specialized applications.
Cost vs. Density: A Comparison
Both carbon fibre and fiberglass density play a critical role in determining the material’s cost-effectiveness, performance, and application suitability. Below is a comparison that illustrates how cost is influenced by both the density of the materials and their performance capabilities.
Material | Density (g/cm³) | Average Cost per kg | Typical Applications | Advantages | Disadvantages |
---|---|---|---|---|---|
Fiberglass | 2.55 | $2 - $5 | Boat hulls, insulation, construction, tanks | Affordable, versatile, durable | Heavier, lower performance |
Carbon Fiber | 1.55 | $20 - $100 | Aerospace, automotive, sports gear | Lightweight, high strength-to-weight ratio | Expensive, complex manufacturing |
Influence of Density on Cost and Performance
As shown in the table, carbon fibre and fiberglass density have a direct relationship with the cost and performance of these materials. Fiberglass, with its higher density, is cheaper to produce but lacks the lightweight strength that carbon fiber offers. This makes fiberglass a better choice for applications where performance and weight are less critical, and cost-effectiveness is a priority. In contrast, carbon fiber’s lower density makes it lighter and stronger, but this comes at a higher cost, which is justified by its superior performance in demanding applications.
In terms of cost vs. density, the key takeaway is that fiberglass is ideal for bulk production in industries where performance requirements are less stringent, whereas carbon fiber, despite its higher cost, is essential for high-performance, lightweight applications where the advantages in strength and weight reduction justify the higher price.
When deciding between fiberglass and carbon fiber, the cost must be carefully weighed against the carbon fibre and fiberglass density and the specific performance requirements of the application. Fiberglass remains the more affordable option for mass production and applications where durability and cost are more important than weight and strength. In contrast, carbon fiber offers superior performance in weight-sensitive, high-strength applications, making it worth the investment for industries that demand the best in terms of material performance, despite its higher cost.
How To Choose The Best Kit To Redo Fiberglass Tub
Fiberglass and Carbon Fibre and Fiberglass Density: A Comparison in Pickleball Paddles
When it comes to choosing the right material for pickleball paddles, carbon fibre and fiberglass density play a crucial role in determining the performance and feel of the paddle. Each material has its own set of characteristics that cater to different player preferences, making the decision between fiberglass and carbon fiber essential for optimizing play style and comfort. In this section, we will explore how both materials compare in terms of their density, weight, and performance in pickleball paddles.
Fiberglass in Pickleball Paddles
Fiberglass is a popular material choice for recreational and entry-level pickleball paddles, thanks to its balance of strength, flexibility, and cost-effectiveness. While it is heavier than carbon fiber, its higher carbon fibre and fiberglass density contributes to its durability and ability to withstand impacts, making it ideal for players who prioritize longevity over extreme weight reduction.
Characteristics of Fiberglass in Pickleball Paddles
- Strength and Flexibility: Fiberglass provides an excellent balance between strength and flexibility. This makes it a great choice for recreational players who need a paddle that offers a good mix of power and control.
- Higher Density: The relatively higher density of fiberglass, around 2.55 g/cm³, results in paddles that have a slightly heavier feel compared to those made of carbon fiber. This increased weight can help some players generate more power on their shots, especially in situations where control is less critical.
- Durability: The material’s durability makes fiberglass paddles ideal for beginners or recreational players who might not yet have developed the precision and consistency that advanced players require.
- Affordability: Fiberglass is more affordable compared to carbon fiber, which means paddles made from fiberglass are often priced lower, making them more accessible for those just starting out or playing casually.
- Impact Absorption: The flexible nature of fiberglass allows it to absorb some of the shock from hitting the ball, reducing vibrations that might affect the player’s arm and hand.
Carbon Fiber in Pickleball Paddles
Carbon fiber, with its lower carbon fibre and fiberglass density (approximately 1.55 g/cm³), is favored by more advanced players who require a paddle that provides high performance, precision, and power. The reduced density of carbon fiber contributes to the overall lightness and stiffness of the paddle, allowing for quicker reaction times and enhanced control during gameplay.
Advantages of Carbon Fiber in Pickleball Paddles
- Lighter Weight: One of the main benefits of carbon fiber is its low density, which results in a lightweight paddle that is easier to maneuver. This is particularly beneficial for advanced players who need a paddle that allows for fast swings and precise control.
- Higher Strength-to-Weight Ratio: Carbon fiber’s superior strength-to-weight ratio makes it ideal for players who prioritize power and precision in their shots. The stiff nature of the material ensures that there is less flex during ball contact, leading to more direct and powerful hits.
- Enhanced Precision: The stiffness of carbon fiber enhances the paddle’s responsiveness, allowing advanced players to have better control over their shots. This precision is essential in high-level play, where every inch of control matters.
- Vibration Reduction: Carbon fiber helps reduce vibrations, providing a smoother feel on contact. This is particularly useful for players who experience discomfort or fatigue in their hands or arms after extended play.
- Performance for Competitive Players: Carbon fiber paddles are often used in competitive and professional pickleball, where performance is the primary factor. The lightweight and durable nature of carbon fiber helps players generate faster swings and hit with greater accuracy.
Density Considerations and Impact on Performance
The carbon fibre and fiberglass density significantly impacts the feel, weight, and overall performance of pickleball paddles. Here are a few key considerations based on the material’s density:
- Weight: The higher density of fiberglass results in a slightly heavier paddle, which can be an advantage for generating power, especially in more casual play. In contrast, the lighter carbon fiber paddles offer faster reaction times and increased maneuverability, which are important in high-speed competitive play.
- Power and Control: Fiberglass’s flexibility allows for more power during slower swings, while carbon fiber’s stiffness delivers precision and power in fast-paced environments. Players who need more control might lean toward carbon fiber, while those seeking a bit more force behind their shots might prefer fiberglass.
- Vibration and Comfort: Both materials offer vibration reduction, but carbon fiber is generally better at absorbing vibrations, offering a more comfortable feel during intense play. For players with joint issues or who are sensitive to vibrations, carbon fiber paddles may be the better choice.
When choosing between fiberglass and carbon fiber for pickleball paddles, carbon fibre and fiberglass density plays an essential role in determining the material’s suitability for a given player’s needs. Fiberglass is ideal for recreational players or those just starting out, offering strength and a good balance of weight and flexibility at an affordable price. Carbon fiber, with its lower density, offers the performance benefits of lightweight, stiffness, and enhanced control, making it better suited for advanced players seeking precision and power in their game. The choice of material ultimately depends on the player’s experience level, playing style, and performance requirements.
Carbon Fibre and Fiberglass Density in Helmets: Enhancing Safety and Performance
When it comes to helmets, whether for motorcycles, sports, or safety gear, the materials used are critical to ensuring both protection and comfort. Among the most commonly used materials are carbon fibre and fiberglass density, which play a vital role in the helmet’s ability to absorb impact and provide safety. In this section, we will explore how both fiberglass and carbon fiber are used in helmets, focusing on their density and safety features, as well as their role in protecting the wearer during high-impact scenarios.
Fiberglass Helmets
Fiberglass is one of the most commonly used materials in the construction of motorcycle helmets and sports helmets due to its balance of durability, weight, and cost-effectiveness. Fiberglass helmets offer an excellent compromise between high performance and affordable pricing, making them a popular choice for both recreational and professional use.
Key Characteristics of Fiberglass Helmets
- Durability: The high carbon fibre and fiberglass density of fiberglass contributes to its excellent durability, making it resistant to wear and tear over extended use. This durability is crucial for ensuring that helmets maintain their protective properties over time.
- Impact Resistance: The higher density of fiberglass helps improve the helmet’s ability to absorb and distribute the force of an impact. The denser material helps the helmet maintain its structural integrity under pressure, ensuring that the energy from a collision is effectively spread out across the shell, reducing the risk of injury.
- Weight: While fiberglass helmets are slightly heavier than those made with carbon fiber, their weight is typically manageable and provides a solid, protective feel. The added weight does not significantly impact comfort, and for many users, the trade-off is worth it for the added durability and safety.
- Cost-Effectiveness: Fiberglass helmets are often more affordable than those made with carbon fiber, making them an excellent option for recreational riders or athletes who need reliable protection at a lower price point. The affordability of fiberglass is largely due to the material’s relatively simple production process compared to carbon fiber.
- Impact Absorption and Layering: Fiberglass helmets often utilize multiple layers of material to improve impact resistance. The higher density allows the helmet to compress and absorb energy more effectively, minimizing the impact force on the head and reducing the risk of traumatic brain injury.
Carbon Fiber Helmets
Carbon fiber is used in high-performance helmets due to its superior strength-to-weight ratio, making it an ideal material for riders or athletes seeking maximum safety with minimal weight. Helmets made from carbon fiber are often seen in professional sports and racing, where reducing weight while maintaining high safety standards is crucial.
Key Characteristics of Carbon Fiber Helmets
- Lightweight Design: One of the main advantages of carbon fiber is its lower carbon fibre and fiberglass density (around 1.55 g/cm³), which allows for a significantly lighter helmet without compromising strength. This is a critical factor in helmets for high-speed sports like motorsports, cycling, and skiing, where less weight means reduced neck strain and faster movement.
- Superior Impact Resistance: Despite its lighter weight, carbon fiber is incredibly strong and rigid. Its higher strength-to-weight ratio provides enhanced impact resistance, allowing the helmet to absorb force more efficiently during an accident or collision. Carbon fiber’s ability to maintain its shape under impact makes it one of the most reliable materials for protective helmets.
- Comfort and Aerodynamics: Due to its lightweight nature, carbon fiber helmets are more comfortable for extended use, reducing fatigue during long rides or sports events. In addition, the aerodynamic properties of carbon fiber helmets improve performance, especially in racing and cycling, where wind resistance is a key factor.
- Higher Cost: The production of carbon fiber helmets is more complex and costly compared to fiberglass, which is reflected in the price. However, the cost is justified by the material’s superior performance, particularly in high-end applications where every gram counts, and the highest levels of safety are necessary.
Fiberglass vs. Carbon Fiber: Density and Safety
The carbon fibre and fiberglass density directly influences how well these materials perform in helmets, particularly when it comes to absorbing impacts and maintaining the structural integrity of the helmet. Here’s a comparison of how the two materials affect safety:
- Impact Resistance: Fiberglass, with its higher density, provides a more solid and substantial feel, making it effective in absorbing impact forces. While carbon fiber is lighter, its strength-to-weight ratio means it can absorb high-impact forces more efficiently than fiberglass, providing superior protection in certain high-risk situations.
- Weight and Comfort: While fiberglass helmets are heavier, this can contribute to a more durable design that is better suited for long-term use without compromising too much on comfort. Carbon fiber helmets, on the other hand, are designed to be lightweight, reducing neck strain and fatigue, which is critical for professional athletes or motorcyclists engaged in long rides or races.
- Cost Considerations: As mentioned earlier, fiberglass helmets are more affordable due to the material’s cost-effectiveness, while carbon fiber helmets are priced higher due to the complex manufacturing process and superior performance characteristics. However, for users looking for the highest levels of protection, the investment in a carbon fiber helmet is often seen as worth it for the combination of lightweight design and advanced impact resistance.
Both fiberglass and carbon fiber helmets offer excellent protection, but the choice between the two materials depends largely on the user’s needs and preferences. Fiberglass helmets are ideal for those who prioritize durability and cost-effectiveness, with a focus on solid impact resistance. The higher carbon fibre and fiberglass density of fiberglass provides a heavier, yet durable, helmet design. In contrast, carbon fiber helmets offer superior lightweight performance, making them the go-to choice for professional athletes and those seeking the best in high-end safety and comfort. Understanding the relationship between carbon fibre and fiberglass density and helmet performance can help riders and athletes select the right helmet for their specific safety requirements.
FAQs about Carbon Fibre And Fiberglass Density
Yes, fiberglass is generally heavier than carbon fiber. The density of fiberglass typically ranges around 2.55 g/cm³, while carbon fiber has a much lower density of about 1.55 g/cm³. This difference in density makes carbon fiber significantly lighter than fiberglass, which contributes to carbon fiber’s popularity in applications where weight reduction is critical, such as in aerospace, automotive, and high-performance sports gear.
Despite being heavier, fiberglass offers excellent durability and impact resistance, making it ideal for certain applications, such as boat hulls, industrial components, and safety equipment, where weight is less of a concern. The increased density of fiberglass also contributes to its ability to absorb shock and reduce vibrations, which is a benefit in many construction and recreational applications.
The density of fiberglass typically ranges around 2.55 g/cm³, depending on the specific type of fiberglass used (for example, E-glass, S-glass, etc.). This density is higher compared to carbon fiber, which has a density of approximately 1.55 g/cm³. The higher density of fiberglass contributes to its relatively heavier weight, but this also provides the material with excellent durability and impact resistance.
Fiberglass is often used in applications where weight is not the primary concern but where strength, rigidity, and cost-efficiency are important. Its higher density allows it to absorb impact more effectively and makes it suitable for industries such as construction, automotive, and marine. Despite being heavier than carbon fiber, fiberglass remains an attractive option because of its cost-effectiveness and versatility.
The density of fiberglass also allows it to be used in a variety of products, including helmets, boat hulls, storage tanks, and even in the production of insulation. In these contexts, fiberglass’s heavier weight can actually be an advantage, as it adds to the material’s overall stability and ability to withstand wear and tear.
The density of carbon fiber is significantly lower than that of fiberglass, with a typical value around 1.55 g/cm³. This makes carbon fiber one of the lightest and strongest materials available, with a high strength-to-weight ratio that makes it particularly valuable in performance-driven industries like aerospace, automotive, and sports equipment manufacturing.
The low density of carbon fiber is one of the key reasons it is favored in applications where reducing weight is critical without compromising strength. For example, carbon fiber is commonly used in the construction of lightweight yet durable components for airplanes, racing cars, and high-performance bicycles, where even small weight reductions can have a substantial impact on efficiency and speed.
In addition to its low density, carbon fiber also exhibits excellent rigidity and high tensile strength, making it an ideal material for applications that require both strength and lightness. Its density is a key factor that enables it to offer superior performance compared to other materials like fiberglass, especially in industries where weight reduction is paramount.
Yes, carbon fiber and fiberglass can be used together, and in fact, combining these materials is quite common in various industries. When used in tandem, carbon fiber and fiberglass complement each other by taking advantage of the unique properties of each material. This combination is often referred to as a hybrid composite, where the materials are layered or woven together to achieve desired performance characteristics.
The primary benefit of using both materials together is that it allows manufacturers to optimize for both strength and cost. Carbon fiber’s low density and high strength-to-weight ratio provide superior strength and lightweight properties, while fiberglass, with its higher density, offers added durability and impact resistance. This combination is often used in products where both lightweight performance and durability are required but where cost is also a consideration.
For example, in the automotive and aerospace industries, hybrid composites made of carbon fiber and fiberglass are commonly used to create parts that need to balance high strength, low weight, and cost-effectiveness. The use of both materials can also enhance the overall structural integrity of a product, making it more resistant to wear and tear while maintaining a relatively light weight. Additionally, the flexibility of combining these materials allows for a variety of design options that meet specific performance and budget requirements.
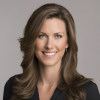
As the editor of GangLong Fiberglass, I have years of experience and in-depth research, focusing on cable tray products, fiberglass solutions, and grille systems. I incorporate years of industry insights and practical experience into every content, committed to promoting the progress of the industry. At GangLong Fiberglass, my commitment is reflected in every product, from innovative cable trays to durable fiberglass solutions and sturdy grille systems. As an authoritative voice in the industry, my goal is to provide valuable information to professionals and businesses and promote forward-looking solutions.