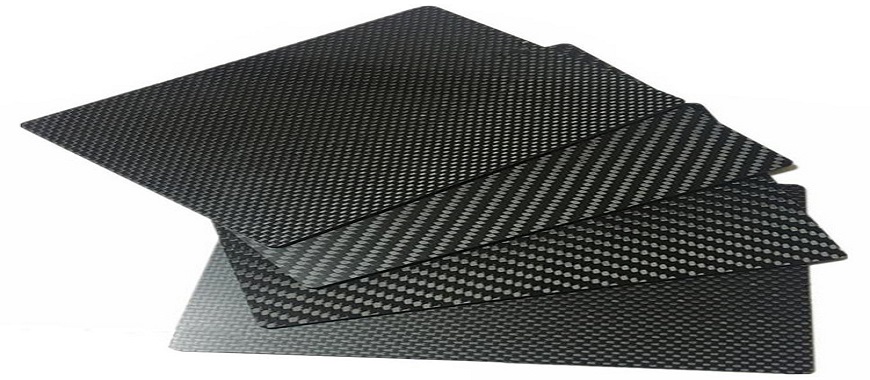
In automotive design, materials like fiberglass or carbon fiber for car weight play a crucial role in reducing vehicle weight, which directly influences performance. Both materials are widely used for their ability to enhance efficiency and durability. Weight reduction is essential in the automotive industry, as it leads to improved fuel efficiency, better handling, and faster acceleration. Lighter vehicles require less energy to move, which translates to reduced fuel consumption and emissions. This article aims to compare fiberglass or carbon fiber for car weight, focusing on their differences in strength, cost, and weight. By understanding these materials’ properties, manufacturers can make informed decisions about optimizing vehicle performance while balancing cost and structural integrity.
What is the Materials: Fiberglass or Carbon Fiber for Car Weight
When considering materials for automotive design, two of the most popular options for reducing car weight are fiberglass and carbon fiber. Both materials offer unique properties that contribute to better vehicle performance, but they differ significantly in composition, strength, cost, and application.
Fiberglass
Fiberglass is a composite material made from glass fibers that are woven into a cloth and then impregnated with resin to form a rigid structure. The process results in a lightweight, strong, and durable material that is resistant to corrosion. However, fiberglass is relatively flexible compared to carbon fiber, which gives it certain advantages and limitations depending on the application.
Fiberglass is commonly used in automotive body panels, including parts like hoods, bumpers, and fenders. It is especially popular in motorsports, including racing cars, due to its ability to withstand high impacts without shattering. The material is also used in other lightweight automotive structures, such as door panels and wheel wells. While it offers excellent strength for its weight, fiberglass tends to be less rigid than carbon fiber, which can impact performance in applications where stiffness is critical.
Carbon Fiber
Carbon fiber, on the other hand, is made from carbon atoms bonded in a crystalline structure. This material is typically used in a composite form, where carbon fibers are combined with resin to create a lightweight yet incredibly strong and rigid structure. Carbon fiber is renowned for its superior strength-to-weight ratio, meaning it provides exceptional strength without adding significant weight to the vehicle.
This material is often used in high-performance cars, sports cars, and racing vehicles, where minimizing weight is essential for achieving optimal performance. Carbon fiber is especially valued in applications requiring high rigidity and durability, such as chassis components, body panels, and structural reinforcements. The material’s low weight and high rigidity contribute to enhanced handling, acceleration, and overall vehicle dynamics.
Key Differences in Fiberglass or Carbon Fiber for Car Weight
Both fiberglass and carbon fiber are integral to weight reduction in vehicles, but each material has distinct properties. Fiberglass is typically more affordable and easier to work with, making it a popular choice for mass-market vehicles and applications where cost is a consideration. On the other hand, carbon fiber offers unparalleled strength and rigidity but comes at a significantly higher price. Choosing between fiberglass or carbon fiber for car weight depends on the specific needs of the vehicle, balancing factors such as performance, cost, and intended use.
Practical Fixes For Light Coming Through Fiberglass Tub
Fiberglass or Carbon Fiber for Car Weight: A Detailed Comparison of Fiberglass vs. Carbon Fiber for Car Weight
When it comes to reducing vehicle weight, both fiberglass and carbon fiber are popular choices, but they differ significantly in terms of weight, strength, and applications. Understanding these differences can help manufacturers make the best decision for specific automotive needs, whether it’s improving fuel efficiency, handling, or overall performance.
Is Fiberglass Lighter than Carbon Fiber?
While both fiberglass and carbon fiber are considered lightweight materials compared to traditional metals like steel, carbon fiber is generally lighter than fiberglass. This is primarily due to its superior strength-to-weight ratio. Carbon fiber’s crystalline structure makes it much stronger and more rigid than fiberglass, allowing manufacturers to use less material while still achieving the same, or even superior, performance. This higher strength-to-weight ratio makes carbon fiber ideal for high-performance applications where weight savings are critical.
For example, in lightweight racing cars and sports vehicles, carbon fiber is often used for components like body panels, chassis, and interior parts. In these applications, the reduced weight improves acceleration, fuel efficiency, and handling, which are key factors in high-speed performance. On the other hand, while fiberglass is still a relatively lightweight material, it does not offer the same level of strength and rigidity, making it less effective for high-performance applications where even small reductions in weight can make a significant difference.
Practical Weight Reduction in Cars
Using carbon fiber for weight reduction in vehicles can have a profound impact on performance. By replacing heavier materials such as steel or aluminum with carbon fiber, manufacturers can reduce the overall weight of the vehicle without sacrificing structural integrity or safety. This weight reduction is particularly valuable in performance vehicles, where every kilogram saved can lead to significant improvements in speed, handling, and fuel efficiency.
Some practical examples of carbon fiber use in weight reduction include car body panels, hoods, and roofs. For instance, sports cars and luxury vehicles often feature carbon fiber hoods, which are significantly lighter than traditional steel hoods, reducing the car’s overall weight and improving aerodynamics. Similarly, carbon fiber roofs are increasingly used in high-performance vehicles to lower the center of gravity, which enhances handling and stability, especially during high-speed maneuvers.
In contrast, fiberglass can still play a significant role in weight reduction, but it is typically used in less critical components. Fiberglass is often seen in applications like bumpers, fenders, and side panels in everyday cars and racing vehicles, where reducing weight is important, but ultimate strength and rigidity are less critical. While fiberglass can still contribute to weight savings, it does not offer the same level of performance enhancement as carbon fiber.
Factor | Fiberglass | Carbon Fiber |
---|---|---|
Weight | Relatively lightweight but heavier than carbon fiber. | Lighter than fiberglass due to superior strength-to-weight ratio. |
Strength | Strong enough for many automotive applications, but more flexible. | Much stronger and more rigid, ideal for high-performance applications. |
Durability | Durable and resistant to impacts and abrasions. | Extremely durable, resistant to fatigue, and maintains rigidity. |
Flexibility | More flexible, which allows for better impact absorption. | More rigid and less flexible, can crack or shatter under extreme stress. |
Applications | Commonly used for body panels, bumpers, fenders, and side panels. | Often used in high-performance components like body panels, hoods, and roofs. |
Performance Impact | Helps reduce weight, but less effective for high-performance needs. | Major performance improvements in handling, acceleration, and fuel efficiency due to significant weight reduction. |
Cost | More cost-effective and widely used in everyday and racing vehicles. | More expensive due to manufacturing processes and material costs. |
Practical Use for Weight Reduction | Used for non-critical components where weight reduction is important but high performance is not the main goal. | Used in critical areas where performance is paramount, such as racing cars, sports cars, and luxury vehicles. |
Ideal for | Everyday vehicles, racing cars, and less demanding performance applications. | High-performance, racing, and luxury vehicles that require maximum strength and lightness. |
Ultimately, the choice between fiberglass or carbon fiber for car weight depends on the desired performance outcome. Carbon fiber provides a more effective solution for those looking for maximum weight reduction, particularly in high-performance or racing vehicles. However, fiberglass remains a cost-effective option for reducing weight in applications where strength and performance requirements are less stringent.
Best Methods To Fix Mineral Etching In Fiberglass Tub
Strength and Durability: Fiberglass or Carbon Fiber for Car Weight
When it comes to the strength and durability of materials used for reducing car weight, both fiberglass and carbon fiber have distinct advantages. While they are both lightweight and contribute to better vehicle performance, their differences in strength and durability make them suitable for different automotive applications. This section will explore the strengths of both materials, and how these properties influence their use in the automotive industry.
Fiberglass Strength
Fiberglass, although strong, is generally more flexible compared to carbon fiber. It is made by weaving glass fibers into a fabric and then impregnating them with resin, which gives it a lightweight and durable structure. The material is resistant to impacts and abrasions, making it ideal for body panels, fenders, and bumpers in many vehicles. These properties make fiberglass an excellent choice for parts that need to endure everyday wear and tear, such as in commuter cars or vehicles that undergo regular collisions or rough conditions.
However, fiberglass has comparatively lower tensile strength than carbon fiber. This means it is more prone to bending or flexing under high stress, which could be a disadvantage in performance vehicles or in areas that experience constant vibration or heavy forces. While fiberglass is durable and can withstand moderate impacts, it does not perform as well as carbon fiber in high-stress situations where rigidity and strength are paramount.
Carbon Fiber Strength
On the other hand, carbon fiber is known for its exceptional tensile strength, which makes it much stronger than fiberglass. Carbon fiber’s crystalline structure provides high resistance to tension, allowing it to maintain its shape and integrity even under intense pressure. This property is particularly useful in automotive applications where structural strength and rigidity are crucial.
Carbon fiber is far more rigid than fiberglass and is less likely to flex under stress, which is why it is favored in critical structural components of performance cars, sports cars, and racing vehicles. In these high-performance applications, where safety, handling, and performance are key, carbon fiber is used in areas such as chassis, structural reinforcements, and body panels. Its high strength-to-weight ratio enables manufacturers to create lighter components that do not compromise durability or performance. Carbon fiber’s rigidity helps enhance aerodynamics, control, and acceleration by reducing the flexing that could negatively affect vehicle dynamics.
Carbon fiber is particularly well-suited for environments where vehicles undergo high speeds, sharp turns, or intense acceleration. It is often found in components like racing car roll cages, suspension parts, and even brake systems, where strength and durability are critical.
Comparing Strength and Durability: Fiberglass vs. Carbon Fiber for Car Weight
When choosing between fiberglass or carbon fiber for car weight, the decision largely depends on the specific requirements of the vehicle. Fiberglass, while flexible and durable, is better suited for non-structural parts or areas where moderate strength is required. Carbon fiber, with its superior tensile strength and rigidity, is ideal for performance-driven vehicles, racing cars, or any automotive application where maximum strength and durability are needed.
Fiberglass is a more cost-effective solution for weight reduction and durability in less demanding applications, while carbon fiber provides the ultimate strength and performance for high-end vehicles where every detail matters in terms of structural integrity and vehicle dynamics.
How to Repair Fiberglass Reinforced Plastic: A Beginner’s Guide
Cost Considerations: Fiberglass or Carbon Fiber for Car Weight
When deciding between fiberglass or carbon fiber for car weight, cost is a major factor that influences material selection. The financial implications of using these materials can vary greatly, not only because of their price per unit but also due to the manufacturing processes involved. Understanding the cost differences between fiberglass and carbon fiber is crucial for manufacturers when optimizing a vehicle’s design while balancing performance and budget.
Fiberglass Cost
Fiberglass is a cost-effective material widely used in both mass-market and high-performance vehicles. Its affordability is one of the main reasons why it is popular in automotive applications. Fiberglass is produced by weaving glass fibers into a fabric and impregnating them with resin, a process that is relatively inexpensive compared to carbon fiber production. Additionally, the raw materials for fiberglass are more readily available, which helps to keep the overall cost low.
Fiberglass is often used in non-critical parts of a vehicle, such as body panels, bumpers, and wheel wells. These components require good durability and impact resistance but do not necessarily need the high-strength, rigid properties that carbon fiber provides. Using fiberglass for these parts allows manufacturers to save significantly on production costs, particularly in vehicles where performance is important but not the top priority. For example, many standard consumer vehicles and even some racing vehicles opt for fiberglass in areas that are less exposed to high stresses or safety concerns, making it a practical and budget-friendly solution for weight reduction.
Carbon Fiber Cost
In contrast, carbon fiber is much more expensive due to its complex manufacturing process and the high cost of raw materials. The process of making carbon fiber involves the use of high-temperature ovens and specialized equipment to transform precursor materials (like polyacrylonitrile) into carbon fibers. This process is time-consuming and requires precise conditions, making carbon fiber production significantly more costly than fiberglass production.
Because of these high manufacturing costs, carbon fiber is typically reserved for luxury vehicles, high-performance cars, and racing vehicles where weight reduction and structural integrity are paramount. The cost of carbon fiber can sometimes be several times higher per kilogram compared to fiberglass. As a result, it is not typically used for general consumer vehicles unless the vehicle is positioned as a high-performance or premium model.
While carbon fiber carries a higher upfront cost, it provides significant long-term benefits in performance vehicles. The material’s superior strength-to-weight ratio allows manufacturers to reduce the overall weight of the vehicle without compromising safety or performance. This results in better acceleration, fuel efficiency, and handling, which are critical factors for luxury and performance cars. Additionally, the durability and rigidity of carbon fiber help extend the lifespan of critical vehicle components, leading to long-term savings on maintenance and repairs. Thus, while the initial investment is higher, carbon fiber can offer better value over time in high-performance applications.
Balancing Cost and Performance: Fiberglass or Carbon Fiber for Car Weight
When choosing between fiberglass or carbon fiber for car weight, manufacturers must consider both the short-term cost and long-term performance benefits. Fiberglass offers a more economical solution, particularly for non-structural or less-critical components, where weight reduction is still important but does not require the same level of strength and rigidity. Carbon fiber, while expensive, is ideal for applications where performance is the primary concern, such as in sports cars, racing vehicles, and luxury automobiles, where its advantages in strength, rigidity, and weight reduction provide a clear return on investment.
Ultimately, the choice between fiberglass and carbon fiber hinges on the specific needs of the vehicle. For mass-market vehicles or those with a focus on cost-effectiveness, fiberglass offers a practical and budget-friendly solution. For high-end or performance vehicles, carbon fiber’s benefits in weight reduction and durability can justify the higher initial cost, making it the material of choice for manufacturers aiming to push the boundaries of vehicle performance.
Other Key Factors: Fiberglass or Carbon Fiber for Car Weight
When selecting materials for weight reduction in vehicles, fiberglass or carbon fiber for car weight are not only evaluated based on their strength, durability, and cost but also on other key factors like flexibility, ease of repair, and safety. Each material brings unique characteristics that impact the overall performance, safety, and maintenance of a vehicle. Understanding these factors can help manufacturers and engineers make more informed decisions when designing vehicles that balance performance with practical considerations.
Flexibility
One of the key differences between fiberglass and carbon fiber is flexibility. Fiberglass is inherently more flexible than carbon fiber, which can be both an advantage and a disadvantage depending on the application.
- Fiberglass’s Flexibility:
- Fiberglass can absorb impacts better than carbon fiber due to its ability to flex and bend without cracking. This makes it ideal for areas of the car that experience high levels of impact or vibration, such as bumpers, side panels, and undercarriage components. The flexibility of fiberglass allows these parts to withstand collisions or abrasions without breaking or shattering, making it a more forgiving material in certain automotive applications.
- This flexibility also helps prevent damage in low-impact accidents. For example, in a minor collision, a fiberglass component may flex and return to its original shape, minimizing the need for costly repairs.
- Carbon Fiber’s Brittleness:
- On the other hand, carbon fiber is much stiffer and more rigid. While this rigidity provides significant performance benefits in structural components, it also makes the material more prone to cracking or shattering under extreme stress or impact. Carbon fiber’s brittleness means that in high-impact or high-vibration situations, it may fail suddenly, leading to more severe damage to the vehicle and its components. For example, a carbon fiber body panel might crack upon a high-speed collision, necessitating a complete replacement.
Due to fiberglass’s superior flexibility, it may be a better option for areas of the car that are frequently exposed to impacts or vibrations, such as bumpers, side skirts, or certain interior components.
Repairability
Another key consideration in choosing fiberglass or carbon fiber for car weight is the ease of repair. While both materials offer unique benefits in terms of strength and performance, their repair processes differ significantly.
- Fiberglass Repair:
- Fiberglass is relatively easy to repair compared to carbon fiber. In the event of damage, fiberglass can be patched or re-molded using standard repair techniques, and the materials needed for repairs are readily available and relatively inexpensive. This makes fiberglass a more cost-effective option for parts that might need frequent repairs, such as exterior body panels in everyday vehicles or vehicles involved in motorsports.
- Fiberglass repairs are typically less labor-intensive and can be done quickly, which is especially important for race cars or vehicles where downtime is costly. The material can be sanded, reshaped, and refinished without requiring advanced equipment or high technical expertise.
- Carbon Fiber Repair:
- Repairing carbon fiber is more challenging and expensive. Due to its complex manufacturing process and specialized nature, repairing carbon fiber components often requires precise methods, including the use of autoclaves and curing processes. When carbon fiber cracks or shatters, it cannot simply be patched up with basic materials; instead, it typically needs to be replaced or undergoes a much more involved repair process.
- The high cost and technical nature of carbon fiber repairs make it less practical for high-traffic or heavily used components of the vehicle, unless performance is the top priority and the repair costs can be justified.
Safety
The safety implications of using fiberglass or carbon fiber for car weight must also be carefully considered. Both materials affect the safety and crashworthiness of a vehicle, but they do so in different ways.
- Fiberglass Safety:
- Fiberglass, with its flexibility, absorbs energy in a way that enhances safety in certain collision scenarios. The ability of fiberglass to flex under impact helps disperse energy and reduce the severity of injuries to passengers. This makes fiberglass particularly useful in areas like bumpers or side panels, where the goal is to minimize damage to the vehicle and protect occupants in low-velocity accidents.
- However, fiberglass is not as effective at handling very high-impact collisions, especially at high speeds, where its flexibility may not be enough to prevent extensive damage.
- Carbon Fiber Safety:
- Carbon fiber, with its high rigidity, offers superior strength in protecting against structural deformation during high-speed collisions. The material’s resistance to bending and cracking allows it to maintain the integrity of critical components like the chassis, providing better protection in more severe impacts.
- However, because of its brittleness, carbon fiber components can shatter or crack upon extreme stress, which could pose safety concerns in certain types of accidents. This is particularly true in situations where the carbon fiber components are exposed to sudden, intense forces.
Overall, the safety of using fiberglass or carbon fiber for car weight depends on the vehicle’s intended use and the specific components being made from these materials. Carbon fiber may be more suitable for safety-critical areas requiring high strength, such as the vehicle’s frame or structural reinforcements, while fiberglass is better suited for areas where flexibility and energy absorption are more important, like body panels and non-structural components.
Summary of Key Factors
- Flexibility: Fiberglass is more flexible and can absorb impacts better than carbon fiber, which is more rigid and prone to cracking under stress.
- Repairability: Fiberglass is easier and more cost-effective to repair, while carbon fiber repairs are more complex and expensive.
- Safety: Fiberglass offers better energy absorption in low-impact collisions, while carbon fiber provides superior structural integrity in high-impact scenarios but can be prone to brittleness.
The decision to use fiberglass or carbon fiber for car weight is influenced not only by performance goals but also by factors such as flexibility, repairability, and safety. The unique properties of each material make them suitable for different applications within a vehicle, depending on the trade-offs between cost, durability, and crashworthiness.
FAQs about Fiberglass Or Carbon Fiber For Car Weight
Carbon fiber is generally lighter than fiberglass due to its superior strength-to-weight ratio. While both materials are used to reduce the weight of vehicles, carbon fiber outperforms fiberglass in terms of its ability to achieve significant weight savings with less material. The key difference between the two is that carbon fiber’s molecular structure, which is made up of carbon atoms bonded in a crystalline formation, gives it incredible strength while maintaining a lightweight profile. In contrast, fiberglass is made from glass fibers and is typically bulkier for the same amount of strength.
In practical terms, carbon fiber parts are usually lighter than fiberglass components of the same size and thickness, making it the preferred material for high-performance applications such as racing cars and sports vehicles, where every kilogram counts. However, while carbon fiber offers weight-saving benefits, it is more expensive and requires more specialized manufacturing techniques, which is why fiberglass is still used in many applications where weight reduction is important, but cost is a factor.
The amount of weight carbon fiber can save on a car depends on the specific components being replaced and the total size of the vehicle. On average, carbon fiber can reduce the weight of a car by up to 40% compared to using traditional materials like steel or aluminum, particularly in critical structural components such as the body panels, chassis, and interior parts. For example, a carbon fiber hood can be about 50% lighter than a steel hood, and a full carbon fiber body can shave hundreds of pounds off a car’s overall weight.
The savings in weight contribute directly to improved fuel efficiency, better acceleration, and enhanced handling. In high-performance vehicles or sports cars, reducing weight is crucial for achieving faster speeds and sharper turns. However, it’s important to note that carbon fiber is not always used for every component in a car due to its high cost, so weight savings can vary depending on the extent of carbon fiber use.
Yes, carbon fiber can make your car lighter. This material is famous for its high strength-to-weight ratio, which means it is stronger than steel but significantly lighter. In automotive applications, carbon fiber is often used to replace heavier materials like steel or aluminum, especially for performance parts like body panels, hoods, roofs, and interior structures. By using carbon fiber in place of traditional materials, car manufacturers can reduce the overall weight of the vehicle, leading to benefits such as improved fuel efficiency, faster acceleration, and better handling.
The lightness of carbon fiber helps to lower the car’s overall mass, which results in less energy being required to move the vehicle. This is especially important for sports cars, race cars, and high-performance vehicles, where every kilogram counts. Carbon fiber parts, while expensive, offer a significant advantage in weight reduction compared to fiberglass and other materials, making them ideal for cars where weight reduction is crucial.
Fiberglass cars can be lighter than traditional vehicles made from steel, but they are generally heavier than those made from carbon fiber. Fiberglass is lighter than steel and aluminum, which is why it is often used in car manufacturing to reduce weight and improve fuel efficiency. Fiberglass body panels, for instance, are commonly used in racing cars, kit cars, and some production vehicles due to their ability to lower the overall weight of the car while still offering good strength and durability.
However, while fiberglass offers weight-saving benefits over metals, it does not provide the same level of performance as carbon fiber in terms of strength-to-weight ratio. A fiberglass car will still be heavier than a carbon fiber car with similar dimensions because fiberglass has a lower strength-to-weight ratio compared to carbon fiber. Despite this, fiberglass remains a cost-effective material for reducing weight, especially in non-critical parts like body panels or bumpers, where ultimate strength is not as essential as in structural components.
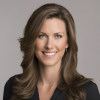
As the editor of GangLong Fiberglass, I have years of experience and in-depth research, focusing on cable tray products, fiberglass solutions, and grille systems. I incorporate years of industry insights and practical experience into every content, committed to promoting the progress of the industry. At GangLong Fiberglass, my commitment is reflected in every product, from innovative cable trays to durable fiberglass solutions and sturdy grille systems. As an authoritative voice in the industry, my goal is to provide valuable information to professionals and businesses and promote forward-looking solutions.