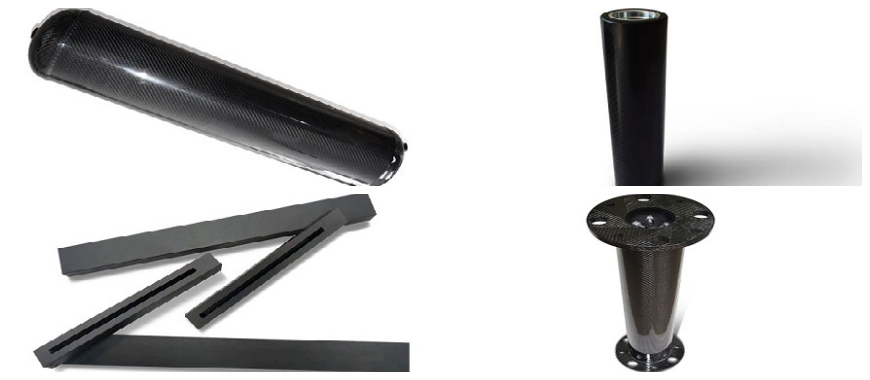
Fiberglass epoxy carbon fiber composites are among the most widely used materials in industries ranging from aerospace to sports equipment. Both fiberglass and carbon fiber offer distinct advantages due to their unique properties. Fiberglass is known for its affordability, flexibility, and ease of use, making it ideal for general-purpose applications. It is relatively lightweight and durable, though not as strong as carbon fiber. On the other hand, carbon fiber is stronger, lighter, and stiffer, providing superior performance, especially in high-stress environments. Both materials rely on epoxy resin as a binding agent, which plays a crucial role in enhancing their strength, durability, and resistance to environmental factors. The main differences between these materials lie in their cost, weight, and durability, with carbon fiber being the more expensive but higher-performance option.
What is Fiberglass Epoxy Carbon Fiber and How Does it Work?
Fiberglass epoxy carbon fiber is a combination of three advanced materials: fiberglass fabric, epoxy resin, and carbon fiber. These materials are often used together to create composite materials with exceptional strength, durability, and versatility. To understand how fiberglass epoxy carbon fiber works, it’s essential to look at each component and how they function together in various industries.
Fiberglass Fabric and Its Composition
Fiberglass fabric is made from woven strands of glass fibers, which are known for their strength, low weight, and resistance to corrosion. The fibers are typically drawn from molten glass and then woven into sheets or mats. The structure of fiberglass fabric can vary, ranging from very fine threads to thicker strands depending on the intended use. These fabrics are often used as the foundation for composite materials, providing the framework for the epoxy resin to bond to.
The composition of fiberglass fabric is key to its performance in different applications. It provides the necessary reinforcement to withstand mechanical stresses, such as tension, compression, and shear forces. When combined with epoxy resin, the fabric gains even more strength, making it suitable for high-performance environments, such as the marine and automotive industries.
The Role of Epoxy Resin in Bonding and Enhancing the Strength of Fiberglass Composites
Epoxy resin plays a crucial role in bonding fiberglass fabric together and enhancing its overall strength. As a thermosetting polymer, epoxy resin undergoes a chemical reaction when mixed with a hardener, causing it to cure and form a solid, durable structure. This bonding process creates a strong link between the individual fiberglass fibers, which significantly increases the material’s mechanical properties, such as tensile strength, rigidity, and resistance to impact.
In the case of fiberglass epoxy carbon fiber, epoxy resin is often used to bond the carbon fiber to the fiberglass fabric, creating a composite material that offers superior performance. The resin also improves the material’s resistance to environmental factors like moisture, chemicals, and UV radiation. Additionally, epoxy resin’s ability to cure at room temperature makes it ideal for manufacturing processes that require precise control over the material properties.
Common Applications of Fiberglass Epoxy Carbon Fiber in Various Industries
Fiberglass epoxy carbon fiber composites are used extensively across multiple industries due to their high strength-to-weight ratio and versatility. Here are some of the key industries where these materials are commonly applied:
Marine Industry
In the marine industry, fiberglass epoxy carbon fiber is widely used for boat hulls, decks, and other structures. These materials offer excellent resistance to water and corrosion, ensuring that boats and ships maintain their structural integrity even in harsh conditions. The combination of fiberglass fabric and epoxy resin helps create lightweight, yet extremely strong boats that are both durable and fuel-efficient.
Automotive Industry
The automotive industry benefits from the use of fiberglass epoxy carbon fiber composites in components like body panels, chassis, and reinforced parts. The lightweight nature of these materials contributes to better fuel efficiency and performance, while their strength and impact resistance improve safety and durability. Additionally, the aesthetic appeal of carbon fiber’s sleek appearance is often a deciding factor in high-end sports cars and performance vehicles.
Construction Industry
In construction, fiberglass epoxy carbon fiber composites are used for reinforcing concrete structures, particularly in seismic retrofitting and bridge construction. These materials offer enhanced durability and resistance to environmental factors like moisture, chemicals, and temperature fluctuations. They also provide an effective solution for improving the strength of structures without adding excessive weight.
The use of fiberglass epoxy carbon fiber composites in construction can help reduce maintenance costs and increase the lifespan of critical infrastructure.
Fiberglass epoxy carbon fiber combines the unique properties of each material to create a composite that is stronger, more durable, and lighter than traditional materials. This versatile composite is increasingly used across various industries for applications that demand high-performance and longevity.
Best Adhesives for Bonding Fiberglass Reinforced Plastic
What is Carbon Fiber Epoxy and How Does it Differ in Fiberglass Epoxy Carbon Fiber Applications?
Carbon fiber epoxy is a composite material made by combining carbon fibers with an epoxy resin. This combination results in a material known for its exceptional strength, stiffness, and durability, making it ideal for high-performance applications across various industries. To understand why carbon fiber epoxy is so effective, it’s essential to explore the properties of carbon fiber as a material and how it interacts with epoxy resin to create a composite that excels in performance.
Understanding Carbon Fiber and Its Superior Strength-to-Weight Ratio
Carbon fiber is a lightweight, high-strength material made up of thin strands of carbon atoms bonded together in a crystalline structure. This structure gives carbon fiber its remarkable strength-to-weight ratio, which is much higher than that of traditional materials like steel or aluminum. Because carbon fiber is both incredibly strong and lightweight, it is used extensively in industries where performance and weight are critical, such as aerospace, automotive, and sports equipment.
The superior strength-to-weight ratio of carbon fiber means that it can withstand significant stress and load without adding much weight to the product. This makes carbon fiber a top choice for applications that require materials to perform under extreme conditions while keeping the overall weight to a minimum.
The Interaction Between Carbon Fiber and Epoxy Resin
Epoxy resin is a thermosetting polymer that hardens when mixed with a hardening agent, resulting in a solid, durable material. When combined with carbon fiber, epoxy resin acts as a binding agent that helps the carbon fibers maintain their alignment, thus maximizing the strength of the composite. The epoxy resin is known for its excellent adhesive properties, ensuring that the carbon fibers stay in place and don’t shift or move under stress.
The interaction between carbon fiber and epoxy resin is crucial because the resin not only binds the fibers together but also helps distribute loads and stress across the material. This results in a composite that is both strong and resistant to environmental factors such as heat, moisture, and chemicals. The epoxy resin’s ability to form a tough, resilient shell around the carbon fibers contributes significantly to the overall performance of carbon fiber epoxy materials.
How Carbon Fiber Epoxy Creates Stronger, Stiffer, and More Durable Composites
When carbon fiber is combined with epoxy resin, the resulting composite material becomes much stronger, stiffer, and more durable than either material alone. The carbon fiber provides the strength and stiffness, while the epoxy resin enhances the material’s toughness and resistance to environmental degradation. This synergy between the two components results in a composite material that can endure significant wear and tear while maintaining its integrity.
The unique properties of fiberglass epoxy carbon fiber composites make them suitable for applications where both strength and weight are critical. For example, in the aerospace industry, carbon fiber epoxy composites are used in the construction of aircraft parts, where every gram of weight saved can result in improved fuel efficiency. In the automotive industry, carbon fiber epoxy is used in performance parts like body panels and chassis to improve speed and handling.
Additionally, carbon fiber epoxy composites have superior fatigue resistance compared to other materials, meaning they can withstand repeated stress cycles without losing strength. This makes them ideal for products that experience continuous loading and unloading, such as sports equipment, marine structures, and even protective gear.
Fiberglass epoxy carbon fiber composites are known for their high strength-to-weight ratio, excellent durability, and resistance to environmental factors. The combination of carbon fiber and epoxy resin creates a material that is not only stronger and stiffer but also more durable, making it perfect for high-performance applications that demand the best in terms of material properties.
Are Fiberglass Reinforced Plastics Good for Cars? Find Out
Fiberglass Epoxy Carbon Fiber: Comparing Weight and Strength
When choosing between fiberglass and carbon fiber for a project, understanding the differences in their weight and strength is critical. Both materials offer impressive performance characteristics, but their unique properties make them suited to different applications. In this section, we will explore the weight differences, strength-to-weight ratios, and durability of fiberglass and carbon fiber, with a particular focus on their use in high-performance scenarios.
Weight Difference: Fiberglass vs. Carbon Fiber
The weight of a material plays a significant role in determining its suitability for various applications. Fiberglass is heavier compared to carbon fiber, largely due to its composition. Fiberglass is made from glass fibers that are woven together and then coated with a resin to form a solid structure. While it is still relatively lightweight compared to metals, it is heavier than carbon fiber.
Carbon fiber, on the other hand, is made up of carbon atoms bonded in a crystalline structure, which provides a much lighter material than fiberglass. This is one of the reasons carbon fiber is preferred in industries like aerospace, automotive, and high-performance sports equipment, where reducing weight is essential for optimal performance.
In applications where weight is a critical factor, such as in racing cars, drones, and even aerospace components, fiberglass epoxy carbon fiber composites provide a clear advantage. These composites are much lighter than fiberglass alone, offering improved fuel efficiency, speed, and overall performance. The lighter weight of carbon fiber means that structures and products can be designed with greater precision and less mass, leading to improved performance and efficiency.
Strength-to-Weight Ratio: Why Carbon Fiber Has a Clear Advantage
The strength-to-weight ratio is one of the most important factors when choosing between fiberglass and carbon fiber, especially in high-performance applications. This ratio compares the material’s strength to its weight, and the higher the ratio, the better the material performs in terms of strength relative to its weight.
Carbon fiber has a significantly higher strength-to-weight ratio than fiberglass, which is one of the primary reasons it is often chosen for applications where high strength and low weight are essential. Carbon fiber is known for its exceptional tensile strength—meaning it can withstand a great deal of pulling or stretching force without breaking. It also maintains its structural integrity under compression, making it a versatile material for a wide range of uses.
In contrast, fiberglass is not as strong as carbon fiber, though it still has a relatively high strength-to-weight ratio compared to metals like steel or aluminum. However, when comparing fiberglass epoxy carbon fiber composites, the latter clearly outperforms in terms of strength, making it the material of choice in industries where performance, safety, and durability are critical.
For example, in high-performance vehicles such as racing cars or motorcycles, carbon fiber composites are used to reduce weight while ensuring that the vehicle can withstand the extreme forces of acceleration, braking, and handling. This is because carbon fiber provides the necessary strength without adding the excess weight that could compromise speed and agility.
Durability and Flexibility in High-Impact Scenarios
Another critical factor when comparing fiberglass and carbon fiber is their durability and flexibility, particularly in high-impact scenarios. Both materials have good durability, but they behave differently under stress.
Fiberglass is more flexible than carbon fiber, which can make it more resistant to cracking or shattering in certain impact situations. This flexibility makes fiberglass epoxy carbon fiber composites more suitable for applications where the material needs to bend or flex under load without breaking. For example, fiberglass is commonly used in the construction of boat hulls or certain types of protective gear, where the ability to absorb impact without cracking is vital.
However, carbon fiber excels in high-impact scenarios when strength and stiffness are paramount. Due to its high stiffness, carbon fiber does not bend as much as fiberglass and is more likely to crack or shatter under high stress or impact. However, the high strength and low weight of carbon fiber allow it to withstand significant forces without deforming or failing. In sports equipment, such as bicycles, tennis rackets, or golf clubs, carbon fiber is used to maximize performance by providing a lightweight yet strong material that enhances speed, control, and power.
In vehicles, carbon fiber composites are often used in structural components like the frame and body panels, where impact resistance and weight savings are essential. The superior strength of carbon fiber helps to absorb and distribute impact forces more efficiently, providing protection while maintaining the structural integrity of the vehicle.
Fiberglass Epoxy Carbon Fiber for Superior Performance
Both fiberglass and carbon fiber have their strengths, but when comparing weight and strength, carbon fiber—especially when combined with epoxy resin—clearly offers superior performance. The lightweight nature of carbon fiber, coupled with its high strength-to-weight ratio, makes it ideal for applications that require both performance and minimal weight. While fiberglass may offer more flexibility and impact resistance in certain scenarios, carbon fiber is unmatched in terms of overall strength, stiffness, and durability, particularly when combined with epoxy resin in fiberglass epoxy carbon fiber composites.
Whether it’s for sports equipment, high-performance vehicles, or cutting-edge aerospace technology, fiberglass epoxy carbon fiber continues to be the material of choice for applications where every gram counts, and strength is non-negotiable.
4×8 Fiberglass Reinforced Plastic Panels: Benefits and Applications
Can You Use Fiberglass Epoxy Carbon Fiber Resin on Carbon Fiber?
When working with composite materials, it’s important to understand which types of resins are most suitable for specific fibers. A common question that arises is whether fiberglass resin, particularly polyester resin, can be used on carbon fiber. While it is possible to use fiberglass resin on carbon fiber, it is generally not recommended for high-performance applications due to several important reasons. In this section, we will explain why fiberglass resin may not be the best choice for carbon fiber, the advantages of carbon fiber epoxy resin, and the potential challenges when using fiberglass resin in carbon fiber composites.
Why Fiberglass Resin (Specifically Polyester Resin) Might Not Be Suitable for Carbon Fiber
Fiberglass resin, particularly polyester resin, is a common resin used with fiberglass to create lightweight and durable composites. However, polyester resin is not an ideal choice for bonding with carbon fiber for several reasons. Polyester resin has a lower adhesion strength when compared to epoxy resin, which can lead to weaker bonds between the resin and the carbon fibers. This reduced adhesion strength may compromise the structural integrity of the composite, especially under high stress or in demanding applications.
Carbon fiber has unique properties that require a resin specifically designed to complement its strength and stiffness. Epoxy resin, commonly used in carbon fiber composites, has superior bonding properties that help it adhere more strongly to the carbon fibers, creating a more robust and durable composite. In contrast, polyester resin does not bond as effectively with carbon fiber, potentially resulting in delamination, cracking, or other forms of failure over time.
Additionally, polyester resin tends to be more brittle than epoxy resin, which means that composites made with fiberglass resin may lack the flexibility and impact resistance needed for high-performance applications. For carbon fiber applications that require flexibility, durability, and strength, using fiberglass epoxy carbon fiber composites with epoxy resin is generally the better choice.
Why Carbon Fiber Epoxy Resin Is the Preferred Option for Carbon Fiber Repairs
When it comes to carbon fiber repairs, epoxy resin is widely regarded as the best option. Epoxy resin offers several advantages over fiberglass resin, especially in the context of repairing carbon fiber components or creating high-performance carbon fiber composites. Some of the key reasons why carbon fiber epoxy resin is the preferred option include:
- Superior Adhesion: Epoxy resin provides a much stronger bond to carbon fiber than polyester resin. This ensures that the fibers remain securely in place, even under extreme stress or exposure to harsh conditions. The high adhesion strength is crucial for maintaining the structural integrity of the composite.
- Enhanced Durability: Carbon fiber epoxy resin composites are more resistant to environmental factors such as heat, moisture, UV rays, and chemicals. This makes them more suitable for outdoor and industrial applications, where durability and long-term performance are essential.
- Better Mechanical Properties: Epoxy resin enhances the mechanical properties of carbon fiber, including strength, stiffness, and impact resistance. This is particularly important in applications where the composite will be exposed to high loads or dynamic forces, such as in aerospace, automotive, or sports equipment.
- Flexibility in Repair: Epoxy resin is more versatile for repairs because it can be precisely applied to damaged areas, ensuring a seamless bond between the new resin and the existing carbon fiber. This results in a repair that restores the material’s original strength and performance.
For these reasons, when working with carbon fiber, especially for repairs or when maximum performance is required, carbon fiber epoxy resin is the preferred choice.
Potential Challenges and Downsides of Using Fiberglass Resin on Carbon Fiber
While it is possible to use fiberglass resin on carbon fiber, there are several challenges and downsides that may arise from using this combination. The following are some of the key issues to be aware of:
Poor Bonding
Fiberglass resin, particularly polyester resin, does not bond as well to carbon fiber as epoxy resin does. The weaker adhesion between the resin and the carbon fibers can lead to delamination, where the resin starts to separate from the fibers. This separation weakens the composite, making it more prone to failure, especially under high stress or when exposed to environmental factors such as heat or moisture.
Compromised Strength and Performance
The combination of fiberglass resin and carbon fiber results in a composite that may not perform as well as one made with epoxy resin. Polyester resin is more brittle and less flexible than epoxy, which compromises the overall strength and impact resistance of the composite. In applications where high performance is critical, such as in aerospace or automotive industries, the reduced strength and durability of a fiberglass resin-carbon fiber composite can be a significant drawback.
Reduced Long-Term Durability
Fiberglass resin is less resistant to UV rays, moisture, and chemicals compared to epoxy resin. Over time, exposure to these elements can cause the resin to degrade, weakening the composite material. Carbon fiber composites made with fiberglass resin may suffer from faster wear and tear, leading to a shorter lifespan and reduced overall performance.
Difficulty in Achieving Optimal Curing
Fiberglass resin requires different curing conditions compared to epoxy resin. Polyester resin, in particular, needs to be mixed with a catalyst and typically requires heat for proper curing. Achieving the right curing conditions is critical to ensuring the composite has the necessary strength and durability. If not cured properly, the resin may not harden fully, leading to weaker bonds and reduced performance.
Fiberglass Epoxy Carbon Fiber Composites for Optimal Performance
While it is technically possible to use fiberglass resin on carbon fiber, it is not the ideal choice for high-performance applications or carbon fiber repairs. The primary issue is that fiberglass resin, particularly polyester resin, does not bond as effectively to carbon fiber as epoxy resin, which can compromise the overall strength, durability, and performance of the composite. For best results, especially in demanding applications, carbon fiber epoxy resin should be used to ensure a strong, durable bond and optimal performance.
Fiberglass epoxy carbon fiber composites offer the best of both worlds—strong bonding, superior durability, and high mechanical properties—making them the preferred choice for applications requiring lightweight, high-strength materials. Whether for repairs or new carbon fiber structures, using epoxy resin with carbon fiber ensures the highest level of performance and longevity.
The Different Types of Fiberglass Epoxy Carbon Fiber
Carbon fiber is a versatile and high-performance material that is widely used in various industries, from aerospace to automotive to sports equipment. Depending on the application, different grades of carbon fiber may be used, each with its own set of properties. This section will explore the different types of carbon fiber, including 3K carbon fiber, aluminized carbon fiber, and other varieties, discussing their benefits, uses, and how they compare in terms of performance, appearance, and application.
3K Carbon Fiber: What It Is, Its Uses, and Its Benefits
3K carbon fiber is one of the most common and popular types of carbon fiber used in composite materials. The term “3K” refers to the number of filaments (or “k”) that make up the carbon fiber tow. In this case, 3K means that each strand of the carbon fiber consists of 3,000 individual filaments. This configuration is a balance between strength, flexibility, and weight, making it ideal for a wide range of applications.
Key Properties of 3K Carbon Fiber
- Strength-to-Weight Ratio: 3K carbon fiber offers a good balance between strength and weight. This makes it suitable for applications that require materials to be lightweight yet strong, such as in the aerospace and automotive industries.
- Flexibility: While still stiff, 3K carbon fiber is more flexible than higher-grade carbon fibers (such as 6K or 12K) due to the smaller number of filaments per tow. This makes it easier to handle and form into various shapes.
- Durability: 3K carbon fiber has a high tensile strength, which means it can withstand a lot of stress before breaking. It also offers resistance to environmental factors such as UV rays, moisture, and temperature fluctuations.
Uses of 3K Carbon Fiber
- Automotive Components: Many car manufacturers use 3K carbon fiber to produce lightweight yet durable parts, such as body panels, spoilers, and interior components.
- Sports Equipment: 3K carbon fiber is commonly used in making lightweight and high-performance sports equipment such as bicycles, golf clubs, and tennis rackets.
- Aerospace: In the aerospace industry, 3K carbon fiber is used in the manufacturing of aircraft components, where both strength and low weight are crucial.
- Industrial Applications: It is also found in various industrial applications such as drones, machinery, and tooling, where high strength and precision are required.
Benefits Compared to Other Carbon Fiber Grades
- Affordability: 3K carbon fiber is more affordable than higher grades such as 6K and 12K carbon fiber, making it a popular choice for many industries.
- Versatility: Due to its balanced properties, 3K carbon fiber is versatile and can be used in a wide range of applications.
- Easier Handling: The smaller number of filaments makes 3K carbon fiber easier to handle during manufacturing and repair processes.
Aluminized Carbon Fiber: Appearance, Performance, and Application
Aluminized carbon fiber is another interesting variation of carbon fiber that is used in specialized applications. As the name suggests, aluminized carbon fiber is carbon fiber that has been coated with a layer of aluminum. This process creates a composite material that combines the benefits of carbon fiber’s strength and aluminum’s reflective and heat-resistant properties.
Key Properties of Aluminized Carbon Fiber
- Enhanced Thermal Resistance: The aluminum coating provides additional heat resistance, making aluminized carbon fiber ideal for high-temperature environments where other carbon fiber grades might struggle.
- Corrosion Resistance: The aluminum coating offers increased resistance to corrosion, particularly in environments exposed to moisture or chemical substances.
- Reflective Surface: The aluminum layer reflects heat and light, which can be useful in applications where temperature control is important.
Uses of Aluminized Carbon Fiber
- Aerospace and Aviation: Aluminized carbon fiber is often used in high-temperature areas of aircraft and spacecraft, where both heat resistance and structural strength are needed.
- Automotive: In high-performance vehicles, aluminized carbon fiber can be used for components that are exposed to extreme heat, such as engine parts or exhaust systems.
- Military and Defense: Aluminized carbon fiber is sometimes used in military applications, including protective gear and vehicle components, where both heat resistance and strength are crucial.
Benefits Compared to Other Carbon Fiber Grades
- Thermal Protection: Aluminized carbon fiber excels in applications where heat resistance is necessary, making it more suitable than standard carbon fiber in certain environments.
- Corrosion Resistance: The aluminum coating offers protection against corrosion, which is a major advantage in harsh environments such as marine or industrial applications.
- Reflectivity: The reflective properties of the aluminum layer help control temperature in sensitive equipment, making aluminized carbon fiber ideal for some aerospace and defense applications.
Other Types of Carbon Fiber
In addition to 3K and aluminized carbon fiber, there are several other types of carbon fiber, each designed for specific uses. Some of the most notable ones include:
6K and 12K Carbon Fiber
- 6K and 12K Carbon Fiber refer to carbon fiber tows made of 6,000 and 12,000 filaments, respectively. These grades offer increased strength compared to 3K carbon fiber but tend to be stiffer and less flexible. They are often used in applications where maximum strength is required, such as in heavy-duty automotive parts, military vehicles, and structural components in aerospace.
High Modulus Carbon Fiber (HMCF)
- High Modulus Carbon Fiber is known for its increased stiffness compared to standard carbon fiber. This makes it ideal for applications where rigidity is critical, such as in racing car chassis, aerostructures, and some sports equipment.
Ultra High Modulus Carbon Fiber (UHM)
- Ultra High Modulus Carbon Fiber is designed for applications that require exceptional stiffness and strength. UHM carbon fiber is typically used in advanced engineering applications, such as spacecraft, military-grade armor, and other ultra-high-performance structures.
Choosing the Right Type of Carbon Fiber for Your Needs
The choice between different types of carbon fiber depends on the specific application and the performance requirements. 3K carbon fiber is versatile and widely used due to its balanced properties, making it suitable for a wide range of industries. Aluminized carbon fiber, on the other hand, offers additional thermal and corrosion resistance, making it ideal for high-temperature and harsh environments. For maximum strength and stiffness, higher grades such as 6K, 12K, and high modulus carbon fiber are more suitable.
In any case, understanding the specific characteristics of fiberglass epoxy carbon fiber composites, and how different grades of carbon fiber behave in terms of strength, flexibility, and durability, is essential to selecting the right material for your project.
FAQs about Fiberglass Epoxy Carbon Fiber
While it’s technically possible to use fiberglass resin, particularly polyester resin, with carbon fiber, it’s generally not recommended for high-performance applications. Fiberglass resin, such as polyester resin, is not as compatible with carbon fiber as epoxy resin. The main issue is that polyester resin does not bond well to carbon fiber, which can compromise the strength and durability of the composite material. When polyester resin is used with carbon fiber, the bond is weaker, and the resin may not fully saturate the fibers, leading to reduced structural integrity.
Epoxy resin, on the other hand, is specifically designed to create a strong and durable bond with carbon fiber. It offers better adhesion, increased strength, and durability. If you’re working on a project that requires high strength-to-weight ratios and maximum performance, such as automotive parts or aerospace components, epoxy resin is the preferred choice. Using fiberglass resin with carbon fiber is typically suited for non-critical applications where strength is not the primary concern.
Yes, epoxy resin will adhere to carbon fiber very effectively. In fact, epoxy is the most suitable resin for bonding with carbon fiber due to its superior adhesion properties. Epoxy resin creates a strong chemical bond with the carbon fiber, ensuring maximum strength, stiffness, and durability in composite materials. When carbon fiber is combined with epoxy resin, the resulting composite structure exhibits excellent mechanical properties, including a high strength-to-weight ratio, making it ideal for demanding applications such as aerospace, automotive, and sports equipment manufacturing.
The reason epoxy adheres so well to carbon fiber is due to its molecular structure. Epoxy resins contain functional groups that react chemically with the fibers, creating a robust bond that is resistant to environmental factors like moisture, temperature fluctuations, and UV exposure. This is why epoxy is the go-to choice for carbon fiber projects, particularly those where performance and reliability are critical.
Bonding carbon fiber to fiberglass requires a resin system that can effectively bond both materials together while ensuring a strong and durable composite structure. The most common method for bonding these two materials is using epoxy resin, which works well with both carbon fiber and fiberglass.
To achieve a solid bond between carbon fiber and fiberglass, follow these steps:
Surface Preparation: Clean and roughen the surfaces of both the carbon fiber and fiberglass to ensure better adhesion. You can use sandpaper or a grinder to slightly abrade the surfaces, increasing their surface area and allowing the resin to bond more effectively.
Apply Epoxy Resin: Once the surfaces are prepared, apply an epoxy resin designed for composite bonding. Make sure to thoroughly saturate the carbon fiber with the epoxy resin before pressing it against the fiberglass.
Curing: After the epoxy resin is applied, allow it to cure at the recommended temperature and time. This ensures that the resin hardens properly, creating a strong bond between the two materials.
Epoxy resin is particularly effective because it can bond to both fiberglass and carbon fiber, offering a strong and reliable connection that maximizes the performance of the composite material.
The best epoxy resin for carbon fiber is one that is specifically formulated for use with composite materials. There are many high-quality epoxy resins on the market, but it’s essential to choose one that provides excellent adhesion, durability, and flexibility for carbon fiber applications. Some key factors to consider when selecting epoxy resin for carbon fiber are:
Viscosity: A low-viscosity epoxy resin is ideal because it allows the resin to fully saturate the carbon fiber without creating air bubbles. This ensures the fibers are properly bonded and the composite has a smooth, even finish.
Cure Time: Depending on your project, you may need an epoxy with a specific curing time. Some epoxy resins are fast-curing, while others take longer to cure. Fast-curing resins are useful for projects that require quick turnaround times, while slow-curing epoxies offer more work time and can improve the final bond strength.
Durability: Look for epoxy resins that offer resistance to environmental factors like moisture, UV rays, and temperature changes. High-performance epoxy resins for carbon fiber are designed to maintain their strength and adhesion properties even in harsh conditions.
Flexibility: For some applications, a resin that offers a bit of flexibility is necessary. This is especially true for parts that may experience dynamic loads or movement.
Some popular brands known for producing high-quality epoxy resins for carbon fiber applications include West System, System Three, and Epoxyworks. Always ensure the epoxy resin is designed specifically for carbon fiber to achieve optimal performance and strength in your composite materials.
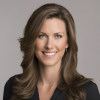
As the editor of GangLong Fiberglass, I have years of experience and in-depth research, focusing on cable tray products, fiberglass solutions, and grille systems. I incorporate years of industry insights and practical experience into every content, committed to promoting the progress of the industry. At GangLong Fiberglass, my commitment is reflected in every product, from innovative cable trays to durable fiberglass solutions and sturdy grille systems. As an authoritative voice in the industry, my goal is to provide valuable information to professionals and businesses and promote forward-looking solutions.