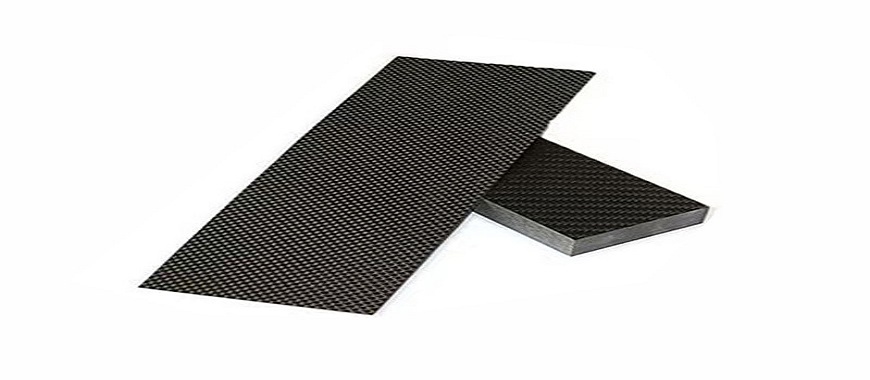
Carbon fiber weave refers to the interlacing of carbon fibers into various patterns to create a fabric. This weaving process plays a crucial role in the overall performance of carbon fiber products. By adjusting the weave pattern, manufacturers can influence the material’s strength, flexibility, and appearance, making it highly versatile for different applications. For example, a carbon fiber weave can be made using patterns like plain weave, twill, or satin, each offering unique properties. The significance of carbon fiber weave lies in its ability to combine durability with a lightweight design, making it ideal for industries like aerospace, automotive, and sports equipment. Carbon fiber weave’s enhanced mechanical properties, combined with its sleek, modern aesthetic, make it a preferred material in high-performance products. It’s not just strong but also highly resistant to corrosion, further boosting its utility across diverse sectors.
Types of Carbon Fiber Weave
When it comes to carbon fiber, the type of weave used significantly affects its properties and applications. Understanding the different carbon fiber weave patterns can help in choosing the right material for specific needs, whether it’s for automotive, aerospace, or sporting goods. Below are the main types of carbon fiber weaves, each with unique characteristics and suitable uses.
Plain Weave
Description
Plain weave is the most basic and traditional type of weave carbon fiber. In this pattern, the fibers alternate over and under each other, creating a simple grid-like structure. It is often referred to as a 1×1 weave, meaning one fiber crosses over one other fiber at a time.
Characteristics
The balanced nature of plain weave makes it ideal for applications that require a combination of strength and flexibility. This weave pattern provides consistent mechanical properties in both directions (warp and weft), ensuring reliability and performance in various environments. Plain weave also tends to be more affordable due to its simplicity, making it a cost-effective choice for many industries.
Applications
- Automotive Parts: The balanced strength and durability of plain weave carbon fiber make it perfect for use in automotive components like hoods, body panels, and interior trims.
- Consumer Electronics: Lightweight yet strong, plain weave is used in the production of mobile phone cases, laptop shells, and other consumer products.
- Aerospace Components: Its versatility and structural integrity make it suitable for non-critical aerospace components like interior panels and non-load-bearing parts.
Twill Weave
Description
Twill weave is more intricate than plain weave and creates a distinct diagonal pattern. In this style, each fiber crosses over two others, forming a “step” pattern that gives the material a unique appearance. The most common twill weaves are 1×1, 2×2, and 4×4, with the number representing the number of fibers the weave pattern crosses over.
Characteristics
Twill weave offers a higher strength-to-weight ratio compared to plain weave, as it is more flexible and resistant to damage. The interlacing pattern results in a smoother finish and improved draping characteristics, which makes it suitable for more complex shapes. The increased flexibility and strength of twill weave provide enhanced performance in demanding applications.
Popular Types
- 1×1 Twill Weave: The most basic version, with fibers crossing over one and under one.
- 2×2 Twill Weave: Each fiber crosses over two others, creating a more pronounced diagonal pattern and a smoother finish.
- 4×4 Twill Weave: Offers even more flexibility and strength, commonly used in high-performance applications.
Applications
- High-End Sports Equipment: The flexibility and aesthetic appeal of twill weave make it a popular choice for items like bicycles, skis, and high-performance sports gear.
- Luxury Automotive Parts: Twill weave is often used in luxury car parts, such as spoilers, mirrors, and interior panels, where both strength and visual appeal are important.
- Motorcycles: For components like fairings and bodywork, twill weave provides the durability needed in high-speed, high-stress environments.
Satin Weave
Description
Satin weave uses a higher number of fibers crossing over one another, resulting in a smooth, lustrous finish. This weave type is characterized by a very soft and shiny surface, which makes it stand out visually while maintaining the strength properties of carbon fiber.
Characteristics
Satin weave carbon fiber is incredibly flexible and offers enhanced stiffness and strength. The smooth finish results in a more refined, glossy appearance, which is ideal for high-end, performance-based applications. The increased flexibility also makes it easier to form into complex shapes, while still maintaining the material’s overall strength.
Applications
- Aerospace Components: The high stiffness and strength-to-weight ratio of satin weave make it perfect for critical aerospace parts, such as fuselage panels and structural reinforcements.
- Performance Automotive Parts: High-performance vehicle components, like brake systems, body panels, and suspension parts, benefit from the strength and flexibility of satin weave.
Unidirectional Carbon Fiber
Description
Unlike traditional woven carbon fiber, unidirectional carbon fiber features fibers that are oriented in a single direction. This weave provides maximum strength and stiffness along the length of the fibers, making it a superior choice when strength is required along one axis.
Characteristics
Unidirectional carbon fiber is prized for its high strength-to-weight ratio along the fibers’ axis. The material offers minimal flexibility perpendicular to the fiber direction, making it ideal for applications that require rigidity and high tensile strength along a single axis. It is typically used in structural applications where flexibility in other directions is not a concern.
Applications
- Aerospace: In the aerospace industry, unidirectional carbon fiber is used for structural reinforcement and lightweight components that must withstand high-stress loads, such as wing spars and fuselage components.
- Wind Turbine Blades: The strength and rigidity provided by unidirectional carbon fiber make it ideal for use in wind turbine blades, which require high strength to endure environmental forces while maintaining minimal weight.
- Structural Reinforcement: In construction and civil engineering, unidirectional carbon fiber is employed to reinforce buildings, bridges, and other structures that need additional support without significantly increasing weight.
Each type of carbon fiber weave offers distinct advantages, depending on the desired application. Understanding these differences allows manufacturers to select the appropriate weave pattern, ensuring optimal performance in various industries. Whether you’re working with automotive parts, aerospace components, or sports equipment, choosing the right woven carbon fiber is essential for achieving the best results.
Is Fiberglass Carbon Fiber Fire Suppression Effective in Safety?
Specialized Carbon Fiber Weave Fabrics
In addition to the basic carbon fiber weaves, specialized carbon fiber fabrics offer enhanced properties and performance characteristics that cater to specific applications. These fabrics often combine carbon fiber with other materials to improve impact resistance, wear resistance, and other factors, making them ideal for highly demanding industries such as aerospace, defense, and automotive. Below, we’ll explore two of the most notable specialized carbon fiber fabrics: Kevlar fabric and prepreg carbon fiber.
Kevlar Fabric
Overview of Kevlar and Its Unique Properties
Kevlar is a high-performance synthetic fiber known for its extraordinary strength, durability, and resistance to wear and abrasion. It is often recognized for its use in bulletproof vests and protective gear, thanks to its exceptional tensile strength and lightweight nature. Kevlar fibers are made from aromatic polyamide, which provides high impact resistance and low weight, making it the material of choice for applications requiring protection from high-stress forces, impact, and ballistic threats.
Comparison with Carbon Fiber Weave
While both Kevlar and carbon fiber are incredibly strong materials, they have different properties that make them suitable for various applications. Below is a comparative analysis of Kevlar and carbon fiber:
Property | Kevlar | Carbon Fiber |
---|---|---|
Strength | High tensile strength | Stronger in tension (pulling forces) |
Impact Resistance | Superior impact resistance | Less resistant to impacts |
Abrasion Resistance | Excellent wear resistance | Moderate abrasion resistance |
Weight | Light and flexible | Lightweight but stiffer |
Flexibility | Highly flexible | More rigid, less flexible |
Cost | Generally more expensive | Usually less expensive |
Applications
- Protective Gear: Kevlar is commonly used in the production of body armor, bulletproof vests, helmets, and gloves due to its high resistance to ballistic impacts and abrasions.
- Bulletproof Vests: The material’s ability to absorb and dissipate energy from high-speed projectiles makes it the ideal choice for law enforcement and military personnel.
- Automotive Reinforcement: In the automotive industry, Kevlar is often used to reinforce body panels and other components, offering high impact resistance while maintaining low weight.
Prepreg Carbon Fiber
Definition
Prepreg carbon fiber refers to carbon fiber that has been pre-impregnated with resin before being molded and cured. This process involves the application of resin to carbon fiber threads or fabrics in a controlled manner to achieve a specific resin-to-fiber ratio. Prepreg carbon fiber eliminates the need for further resin application during the molding process, allowing for precise control over the resin content, resulting in higher-quality and more consistent composite materials.
Characteristics
Prepreg carbon fiber offers several advantages over traditional wet-layup methods:
- Precise Resin Control: The resin is evenly distributed throughout the fiber, ensuring optimal strength-to-weight ratios and consistent mechanical properties.
- Reduced Waste: The pre-impregnation process minimizes excess resin, leading to less material waste and improved environmental sustainability.
- Enhanced Quality: The pre-impregnation ensures a higher level of consistency and uniformity in the final product, reducing the likelihood of defects.
Applications
- Aerospace: Prepreg carbon fiber is heavily used in aerospace applications for structural components such as fuselages, wings, and other load-bearing parts. The superior strength-to-weight ratio is crucial for reducing weight while maintaining structural integrity.
- High-Performance Sports Equipment: Sports equipment like bicycles, skis, and race car components often utilize prepreg carbon fiber for its strength, light weight, and precision. The material ensures high performance while minimizing weight.
- Luxury Automotive Parts: Prepreg carbon fiber is a popular choice in the luxury automotive industry for parts like body panels, hoods, and interior components, where strength, weight reduction, and aesthetics are important factors.
Prepreg carbon fiber’s ability to provide superior control over the resin content, along with its consistent quality and high performance, makes it an indispensable material for industries where reliability and precision are paramount.
Both Kevlar fabric and prepreg carbon fiber are integral to specialized applications, offering unique advantages depending on the required strength, flexibility, and impact resistance. These specialized materials enhance the capabilities of carbon fiber weaves, allowing it to be tailored for specific demands in various industries, from military protection to aerospace engineering.
Is Carbon Fiber Itchy Like Fiberglass? Find Out!
What is Carbon Fiber Weave Composites
Carbon fiber composites are a critical component in industries that require materials with exceptional strength, low weight, and high durability. These composites are created by combining carbon fiber weave fabrics with resins or other matrix materials to form solid, versatile composites that offer superior mechanical properties. Understanding carbon fiber composites, their benefits, and common types is essential for industries ranging from automotive to aerospace.
What are Carbon Fiber Composites?
Carbon fiber composites are materials made by combining carbon fiber weave fabrics with a resin or matrix material to create a solid structure that leverages the unique properties of carbon fibers. The resulting material is significantly stronger and lighter than traditional materials like steel or aluminum, while maintaining excellent stiffness and resistance to wear and tear. Carbon fiber composites are used in many advanced applications due to their exceptional performance characteristics.
These composites can be tailored for specific needs by selecting different matrix materials, resins, or the type of carbon fiber weave used. This allows manufacturers to produce a wide variety of composites suited for different environments and stress conditions.
Benefits of Carbon Fiber Composites
The use of carbon fiber weave in composites brings several advantages that make it ideal for demanding applications. Here are some key benefits of carbon fiber composites:
- Increased Strength: The carbon fiber’s high tensile strength ensures that composites made with carbon fiber weave are incredibly strong, providing superior load-bearing capabilities.
- Reduced Weight: One of the primary reasons for the popularity of carbon fiber composites is their light weight. Carbon fiber is much lighter than metals like steel, making it ideal for industries where weight reduction is critical, such as aerospace and automotive.
- High Stiffness: Carbon fiber composites offer excellent stiffness, which is crucial for applications requiring precise shape retention under stress.
- Enhanced Durability: The inherent strength and corrosion resistance of carbon fiber weave make it highly durable, even under extreme conditions, making it ideal for use in harsh environments like aerospace and marine applications.
- Superior Fatigue Resistance: Carbon fiber composites have a higher resistance to fatigue compared to metals, meaning they can withstand repeated stress without deteriorating.
- Design Flexibility: The ability to combine carbon fiber weave with various matrix materials and resins allows for greater design flexibility. Manufacturers can create customized properties for specific performance needs.
Common Types of Carbon Fiber Composites
There are several types of carbon fiber composites, each with its own set of manufacturing processes and applications. Understanding these different types helps in selecting the right composite material for specific needs.
Prepreg Composites
Prepreg composites are made by impregnating carbon fiber with a resin matrix before the molding process. The resin is carefully applied to the carbon fibers in a controlled environment, ensuring that the correct resin-to-fiber ratio is maintained. Prepreg composites offer excellent performance and consistency, with precise control over the material properties.
- Advantages: Prepreg composites result in less waste and improved quality control because the resin is evenly distributed throughout the fiber. This allows for higher performance in critical applications where precision is paramount.
- Applications: Prepreg composites are commonly used in aerospace, high-performance automotive parts, and sports equipment due to their superior strength-to-weight ratio and structural integrity.
Wet Layup Composites
Wet layup is a more traditional method for making carbon fiber composites, where carbon fiber fabrics are layered and then saturated with resin. This process is often done manually or using machines, and it requires the resin to be applied at the time of the layup.
- Advantages: Wet layup is a relatively simple and cost-effective method of manufacturing carbon fiber composites, making it ideal for prototypes, small-scale production, or less demanding applications.
- Applications: Wet layup composites are used in industries such as marine, automotive, and construction, where large, low-cost structures are required, but high-end performance is not critical.
Vacuum Bagged Composites
Vacuum bagging is a technique where carbon fiber fabric is laid up and then sealed in a vacuum bag. The vacuum pressure ensures that the resin is evenly distributed throughout the fiber, which is then cured under heat and pressure.
- Advantages: Vacuum bagging enhances the uniformity of the composite, improving the strength and performance characteristics of the finished material. It also reduces the amount of excess resin, leading to lighter and stronger composites.
- Applications: Vacuum bagged composites are often used in aerospace, automotive, and marine industries, where the precision and quality of the final product are critical.
Applications in Various Industries
Carbon fiber composites are widely used across multiple industries due to their impressive combination of strength, weight reduction, and durability. Here are some of the main industries that benefit from carbon fiber weave composites:
- Automotive Industry: Carbon fiber composites are used to reduce weight in vehicles, improving fuel efficiency and performance. Parts like body panels, hoods, and interior components are often made from carbon fiber composites to enhance both strength and aesthetics.
- Aerospace Industry: Due to their high strength-to-weight ratio, carbon fiber composites are extensively used in aircraft and spacecraft components, including fuselages, wings, and engine parts. The material helps to reduce fuel consumption while maintaining structural integrity.
- Marine Industry: In the marine industry, carbon fiber composites are used in boat hulls, masts, and other components where high resistance to corrosion and environmental damage is required, along with minimal weight.
- Sports Equipment: Carbon fiber composites are commonly found in high-performance sports equipment such as bicycles, skis, golf clubs, and racing car parts. The combination of strength and light weight makes it ideal for these applications, where performance is key.
Understanding carbon fiber weave composites and their manufacturing processes enables industries to choose the right material for their specific applications, improving performance, reducing weight, and increasing durability. Whether in aerospace, automotive, marine, or sports, these composites continue to be a cornerstone of advanced manufacturing techniques.
Is Aerocanard Fiberglass or Carbon Fiber? A Comprehensive Comparison
Choosing the Right Carbon Fiber Weave
Selecting the right carbon fiber weave for a specific application is essential to optimize performance, durability, and aesthetics. Different types of carbon fiber weaves offer unique characteristics in terms of strength, flexibility, appearance, and more. Understanding these factors will help you choose the best weave for your needs, whether you’re designing a high-performance automotive part, an aerospace component, or a piece of sporting equipment.
Factors to Consider When Selecting a Weave
When selecting a carbon fiber weave, there are several key factors to take into account that can significantly affect the performance and outcome of your composite material. These factors include application-specific requirements, material choice, and intended aesthetic or functional goals. Here are the main considerations:
- Application-Specific Requirements:
- Strength: Depending on the application, you may need a weave that offers maximum tensile strength, such as unidirectional carbon fiber or 2×2 twill weaves. For applications that require high-strength performance, these weaves excel at bearing heavy loads.
- Weight: For applications where reducing weight is a priority, carbon fiber weaves that are lightweight, like the 1×1 or 2×2 twill, are excellent choices. These provide strength without adding unnecessary bulk.
- Flexibility: If flexibility is needed, such as in parts that require some bend or formability, a plain weave might be suitable, as it allows for moderate flexibility while maintaining strength.
- Aesthetic Preferences: For parts where appearance matters, such as consumer products or visible automotive components, the weave pattern can be a significant consideration. Satin weave is often chosen for its smooth, shiny finish, which is visually appealing in many applications.
- Material Choice:
- Plain Weave: This is the most commonly used carbon fiber weave and offers a balanced combination of strength and flexibility. It is typically chosen for its simplicity and moderate cost, making it ideal for structural components where strength and flexibility are balanced, such as automotive parts and sporting goods.
- Twill Weave: The twill weave is known for its diagonal pattern and offers superior flexibility and strength over the plain weave. Twill weaves, especially 2×2 and 4×4 variations, are used in more complex applications like high-end automotive parts, aerospace components, and luxury consumer products due to their enhanced durability and sleek finish.
- Satin Weave: Satin weave produces a smooth, lustrous finish, making it a go-to choice for applications where appearance is a key factor. This weave provides excellent aesthetic appeal while still maintaining good mechanical properties. It is ideal for visible parts where high gloss and a professional look are desired.
Recommendations
When it comes to choosing the right carbon fiber weave, here are some recommendations based on specific needs and applications:
- For High-Strength, Lightweight Parts: If you need carbon fiber components that offer both strength and minimal weight, consider using unidirectional or 2×2 twill weaves. Unidirectional carbon fiber provides maximum strength in one direction, making it perfect for structural components that bear heavy loads along a single axis, such as aerospace parts or automotive frames. The 2×2 twill weave offers a great balance of strength, flexibility, and weight reduction, making it a versatile choice for high-performance applications.
- For Aesthetic Finishes: If the appearance of the finished product is important, particularly for consumer products or visible parts in automotive or sports equipment, satin weave is highly recommended. Satin weave’s smooth, glossy finish gives the product a high-end look, making it ideal for parts like car interiors, decorative panels, or any component where aesthetics play a significant role.
- For Flexibility and Moderate Strength: Plain weave is a good option when you need a balance between strength, flexibility, and cost-effectiveness. It’s often used in more general applications such as automotive body panels, sporting goods, and some structural components. The plain weave offers a high degree of versatility, making it suitable for many industries, especially when a moderate level of strength is required without the need for extreme rigidity or flex.
Choosing the right carbon fiber weave involves understanding the specific requirements of your application, considering both performance characteristics and aesthetic preferences. By selecting the appropriate weave, you can achieve optimal strength, weight, flexibility, and appearance, ensuring that the final product performs as expected and meets all design goals.
Applications of Carbon Fiber Weave
The versatility of carbon fiber weave has made it an essential material in a wide range of industries. From aerospace to consumer goods, the strength, lightweight properties, and aesthetic appeal of carbon fiber woven fabrics make it the go-to choice for high-performance applications. Here’s an in-depth look at how carbon fiber weave is utilized across various sectors.
Aerospace Industry
In the aerospace sector, carbon fiber weave is used extensively to manufacture lightweight and durable components for aircraft and spacecraft. The need for materials that offer high strength-to-weight ratios is critical in this field, where even small reductions in weight can lead to significant improvements in fuel efficiency and overall performance.
- Aircraft Fuselages and Wing Components: Aircraft manufacturers use carbon fiber weave for key structural parts like fuselages, wing spars, and tail sections. The material provides the necessary strength to withstand the forces encountered during flight while keeping the weight of the aircraft to a minimum. The ability to reduce weight directly translates into better fuel efficiency, lower operating costs, and enhanced range for aircraft.
- Spacecraft Parts: In spacecraft, carbon fiber weave is used in components such as heat shields, structural frames, and engine components. These materials must endure extreme temperatures, high velocities, and intense vibrations, making carbon fiber’s resistance to fatigue, high strength, and thermal stability ideal for these applications.
- Benefits in Aerospace: The combination of carbon fiber weave with other composite materials allows for the creation of advanced, high-performance components that are not only lighter but also provide better fuel efficiency and longer service lives. The flexibility in design and material composition also allows manufacturers to meet the complex demands of modern aviation and space exploration.
Automotive Industry
In the automotive industry, carbon fiber weave is increasingly being used to reduce vehicle weight while improving performance and safety. The automotive sector demands materials that not only contribute to reduced weight but also improve safety, performance, and fuel efficiency, making carbon fiber a perfect fit for modern vehicles.
- Reducing Vehicle Weight: Automotive manufacturers use carbon fiber weave in body panels, chassis, and other structural components to reduce the overall weight of the vehicle. By using carbon fiber parts in place of traditional metal parts, cars can achieve significantly lighter weights, which results in improved acceleration, handling, and braking performance.
- Enhancing Performance and Fuel Efficiency: Lighter vehicles consume less fuel and produce fewer emissions, contributing to better fuel economy and lower environmental impact. Carbon fiber parts can help improve a vehicle’s overall performance while maintaining strength and durability.
- High-End Automotive Parts: Luxury sports cars and racing vehicles use carbon fiber weave extensively for components like hoods, spoilers, and interior panels. The material’s lightweight nature, combined with its strength and ability to absorb impacts, provides both performance advantages and enhanced safety features.
- Electric Vehicles (EVs): Carbon fiber is particularly beneficial in electric vehicles, where reducing weight can help offset the heavy batteries. This is especially important for improving range and efficiency, and carbon fiber weave plays a crucial role in this sector.
Sports Equipment
The use of carbon fiber weave in sports equipment is widespread, especially for products that require a balance of high strength, low weight, and durability. Carbon fiber’s unique properties allow for the creation of high-performance gear that offers superior performance and comfort.
- Bicycles: The bicycle industry has embraced carbon fiber weave roll for both road bikes and mountain bikes. The material is used in frames, handlebars, forks, and wheels, offering reduced weight without sacrificing strength. Carbon fiber bicycle frames are not only lighter but also absorb road vibrations better, providing a smoother ride.
- Tennis Rackets and Golf Clubs: Carbon fiber weave is commonly found in the construction of tennis rackets and golf clubs, where its lightweight and stiff nature contribute to better power, control, and maneuverability. Tennis rackets, for example, use carbon fiber to increase strength and reduce the overall weight, improving swing speed and performance.
- Snowboards and Skis: In winter sports, carbon fiber weave is used to construct lightweight yet durable skis and snowboards. The material enhances both the stiffness and flexibility of the equipment, offering better responsiveness on snow while maintaining strength and stability.
- Fishing Rods and Hockey Sticks: The sporting goods industry has also seen a rise in carbon fiber weave usage in equipment like fishing rods and hockey sticks. The material provides enhanced durability and strength while keeping the equipment lightweight and easy to handle.
Consumer Goods
Beyond industrial applications, carbon fiber weave has become a popular choice in the consumer goods sector, where its strength, durability, and sleek appearance are highly valued. The material is used in a range of products that benefit from its lightness, resilience, and aesthetic appeal.
- Luxury Phone Cases: The rise of carbon fiber in consumer electronics has led to the creation of high-end phone cases. These cases offer enhanced protection while maintaining a slim profile, providing both durability and aesthetics. The carbon fiber weave also adds a premium feel, appealing to consumers who seek both functionality and style.
- Luggage: High-end luggage brands use carbon fiber weave to produce lightweight yet highly durable suitcases and bags. The material’s strength ensures that the luggage can withstand rough handling during travel, while its lightness makes it easier to carry and maneuver.
- Wallets and Bags: Luxury fashion brands incorporate carbon fiber weave into wallets, backpacks, and briefcases to combine durability with sleek, modern aesthetics. The use of carbon fiber adds a futuristic and high-tech appeal to everyday accessories.
- Watches and Jewelry: Carbon fiber is increasingly being used in luxury watches and jewelry, offering a blend of modern design and exceptional performance. The lightweight, strong, and scratch-resistant nature of carbon fiber makes it a preferred choice for high-end timepieces and stylish jewelry pieces.
- Eyewear: The strength and lightness of carbon fiber weave also lend themselves well to the eyewear industry. Frames made from carbon fiber are durable, flexible, and lightweight, providing both comfort and style for premium eyeglass and sunglass brands.
The versatility of carbon fiber weave in consumer goods highlights the material’s ability to balance high strength with aesthetic appeal, making it a favored choice in luxury products where both performance and visual impact matter.
From aerospace and automotive to sports and consumer products, carbon fiber weave continues to revolutionize industries by offering an unmatched combination of strength, weight reduction, and design flexibility. Whether it’s for improving fuel efficiency in vehicles or enhancing performance in sports equipment, the applications of carbon fiber weave are vast and continue to grow as technology evolves.
FAQs about Carbon Fiber Weave
The weave of carbon fiber refers to the pattern in which the individual carbon fibers are woven together to form a fabric-like material. These woven fibers are then typically impregnated with resin to form a composite material, which is used in various applications like automotive parts, aerospace components, sporting equipment, and consumer goods. The primary goal of the weave is to enhance the material’s strength, durability, and flexibility.
There are several types of carbon fiber weaves, each designed for specific performance characteristics. The most common weave patterns include plain weave, twill weave, satin weave, and unidirectional weave. Plain weave is the simplest, where fibers cross each other at right angles in a crisscross pattern, offering balanced strength and flexibility. Twill weave, with its diagonal pattern, provides increased flexibility and a smoother finish, making it suitable for applications requiring more complex performance. Satin weave has an even more pronounced finish, offering superior aesthetic qualities and flexibility, often used in luxury consumer goods.
Understanding the weave is essential when selecting carbon fiber for different applications, as each pattern offers different mechanical properties, including strength, weight, and flexibility.
The strongest carbon fiber weave depends on the specific application and desired properties, but generally, unidirectional carbon fiber is considered the strongest weave in terms of tensile strength. In a unidirectional weave, all the carbon fibers are aligned in a single direction, providing maximum strength along that axis. This makes it ideal for applications where strength in one direction is crucial, such as in aerospace and automotive structural components.
However, when it comes to balanced strength in multiple directions, 2×2 twill weave is another highly regarded option. The 2×2 twill weave has fibers that cross over each other at a 45-degree angle, creating a more complex structure that balances strength and flexibility. This weave is used in high-performance applications, such as in luxury vehicles and high-end sports equipment, where strength and durability are required in multiple directions.
For components that require the highest performance in all directions, a combination of different weaves, such as using unidirectional carbon fiber in areas that require maximum strength and twill or plain weave in areas that need balanced flexibility, may be used.
Forged carbon fiber and woven carbon fiber differ significantly in their manufacturing processes and resulting properties, though both are forms of carbon fiber composites.
Woven Carbon Fiber: Woven carbon fiber consists of threads of carbon that are woven together into a fabric. These fibers are then typically impregnated with resin to create a strong composite material. The weave structure adds strength, flexibility, and resistance to stress in multiple directions. Common weaves include plain weave, twill weave, and satin weave, each providing distinct mechanical properties and aesthetic finishes. Woven carbon fiber is primarily used in applications where the material needs to be lightweight yet strong and durable, such as in the automotive and aerospace industries.
Forged Carbon Fiber: Forged carbon fiber is made from chopped carbon fibers that are compressed into molds under heat and pressure, often without the need for a fabric weave. The result is a solid, dense material that is highly resistant to impact and can be molded into complex shapes more easily than woven carbon fiber. While it is not as lightweight as woven carbon fiber, forged carbon fiber is often used for parts that require superior impact resistance and complex geometry, such as automotive components, sports equipment, and consumer products.
While carbon fiber offers numerous advantages, such as its lightweight nature, high strength-to-weight ratio, and exceptional durability, there are also some notable downsides that need to be considered before using it in certain applications.
Cost: One of the most significant drawbacks of carbon fiber is its high cost compared to other materials like steel or aluminum. The manufacturing process for carbon fiber is intricate and labor-intensive, which makes the material expensive to produce. This can drive up the overall cost of products made with carbon fiber, which may not be justifiable for some applications, especially in industries where cost efficiency is a top priority.
Brittleness: While carbon fiber is incredibly strong, it is also relatively brittle. This means that, while it can handle a lot of pressure, it is more susceptible to cracking or shattering under impact or excessive stress compared to more ductile materials like metals. This characteristic makes carbon fiber less suitable for applications where impact resistance or toughness is a primary concern, such as in some structural components.
Manufacturing Complexity: The production of carbon fiber requires specialized equipment and processes, which can be time-consuming and expensive. This makes mass production of carbon fiber components challenging, especially for industries where high volumes are required. Additionally, carbon fiber materials can be difficult to repair if damaged, adding further complexity to their use in certain industries.
Environmental Impact: Carbon fiber production is energy-intensive, and recycling carbon fiber remains a significant challenge. While some progress has been made in developing recycling technologies, it is not as straightforward as recycling metals, which can lead to environmental concerns related to its disposal.
Despite these drawbacks, carbon fiber remains a preferred material for many high-performance applications where its benefits outweigh the disadvantages, particularly in industries like aerospace, automotive, and sports equipment.
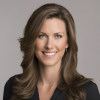
As the editor of GangLong Fiberglass, I have years of experience and in-depth research, focusing on cable tray products, fiberglass solutions, and grille systems. I incorporate years of industry insights and practical experience into every content, committed to promoting the progress of the industry. At GangLong Fiberglass, my commitment is reflected in every product, from innovative cable trays to durable fiberglass solutions and sturdy grille systems. As an authoritative voice in the industry, my goal is to provide valuable information to professionals and businesses and promote forward-looking solutions.