- Home
- Carbon Fiberglass
Purchase Carbon Fiberglass Composite Materials
Carbon Fiberglass is tough and its more flexible nature enables it to withstand stress and physical abuse more easily.
Carbon Fiberglass combines the best attributes of carbon fibers and fiberglass to offer exceptional strength and durability. This material’s performance is largely driven by the fiber properties, with the fibrous reinforcement carrying most of the load. Known for its superior compressive and flexural strength, Carbon Fiberglass provides the highest strength-to-weight ratio available, surpassing other reinforcements and many traditional building materials.
Its sleek, black appearance adds an aesthetic edge, making it a popular choice in high-performance applications like aerospace, automotive, and sports equipment. However, it’s worth noting that Carbon Fiberglass is generally more expensive and can fail suddenly without warning when it reaches its strength limit.
The unique characteristics of Carbon Fiberglass make it suitable for applications requiring low weight and high stiffness. When compared to other materials like Fiberglass Fabric Cloth or Chopped Strand Mat, which also offer valuable properties for composite construction, Carbon Fiberglass stands out for its high strength and resistance to environmental factors.
Simplifying Your Life: Key Functionalities
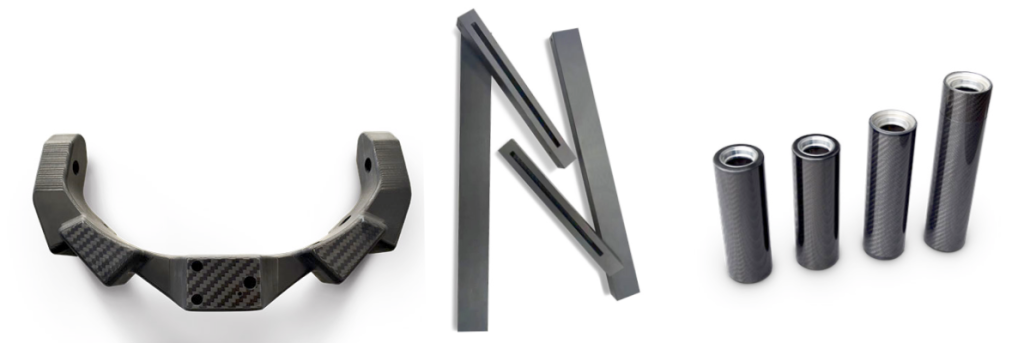
Attribute | Details |
---|---|
Product Name | Carbon Fiberglass Fabric |
Material | 100% Carbon Fiber, Carbon/Fiberglass Hybrid |
Weave Type | Twill, Plain, Stripe, 3D |
Weight Range | 200gsm - 300gsm |
Thickness | Lightweight to Very Lightweight |
Width | 50cm - 150cm (Customizable) |
Length | 100m per roll (Customizable) |
Shape | Roll |
Color Options | Black, Gold, Custom |
Surface Treatment | Electroplated, Plating, Special Coating |
Key Features | Abrasion-Resistant, Waterproof, Anti-static, Heat-Insulation, Flame Retardant, Chemical-Resistant, Radiation-Resistant, Stretchable |
Usage | Automotive, Sports Equipment, Fishing Tackle, Bags & Luggage, Apparel-Workwear, Outdoor-Tents, Industry, Home Décor, Fashion Accessories, Hospital, Shoes |
Place of Origin | Hebei, China |
Brands | GangLong Fiberglass |
MOQ | 10 meters |
Packaging | Carton Box, Roll |
Delivery Time | 3-10 days |
News
- Exploring the Benefits of Carbon Fiber Apparel
- How to Work with Carbon Fiber Successfully
- Carbon Fiber Suit: The Future of Lightweight Armor
- Is Carbon Fiber Armor the Future of Protection?
- Why White Carbon Fiber is Popular in Automotive Design
- Transparent Carbon Fiber Sheets: Strength Meets Clarity in Design
- Chopped Carbon Fiber Mat for Lightweight Reinforcement
- Carbon Fiber EG Hatch: Upgrade Your Civic Today
- The Benefits of Using Structural Carbon Fibre in Engineering
- How Many Layers of Layered Carbon Fiber Are Needed?
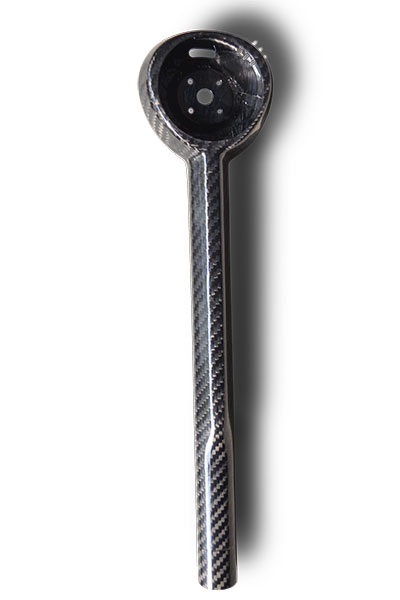
What is Carbon Fiberglass?
Carbon fiberglass is a specialized composite material that combines the unique properties of carbon fiber and fiberglass. This fusion creates a material that leverages the strengths of both components to achieve a superior balance of strength, durability, and weight.
Definition and Composition
Carbon fiberglass is a composite material that integrates carbon fiber and fiberglass into a single, highly effective material. The primary components of carbon fiberglass are:
Carbon Fiber: Carbon fibers are thin, strong crystalline filaments of carbon that have remarkable strength-to-weight ratios. They are renowned for their high tensile strength and stiffness, which makes them ideal for applications requiring high strength and low weight.
Fiberglass: Fiberglass is made from fine fibers of glass and is known for its durability, flexibility, and resistance to corrosion. It is often used to reinforce other materials to improve their mechanical properties.
The production of carbon fiberglass sheets involves several key processes: Material Preparation: The process begins with the preparation of both carbon fibers and fiberglass. Carbon fibers are produced by heating polyacrylonitrile (PAN) fibers to high temperatures in an inert atmosphere. Fiberglass, on the other hand, is made by melting glass and drawing it into fine fibers. Weaving: The prepared carbon fiber part and fiberglass are woven into fabric forms. These fabrics are often arranged in layers to create a strong composite. The weaving patterns can vary depending on the desired properties of the final product. Layering and Lamination: The woven fabrics are layered and impregnated with a resin, typically epoxy, to bind the fibers together. This resin is crucial as it provides the material with its final structural integrity and resistance to environmental factors. Curing: Once the fabric layers are set in place, the resin needs to be cured. This is often done by heating the composite in an autoclave or oven, where the resin hardens and the composite reaches its final strength. Finishing: After curing, the carbon fiberglass sheets are trimmed, cut, and finished to meet specific dimensional and surface quality requirements. This step ensures that the sheets are ready for their intended applications.Typical Manufacturing Processes Used to Create Carbon Fiberglass Sheets
Carbon Fiberglass Properties
Carbon fiberglass exhibits a range of properties that make it a highly desirable material for various applications. These properties stem from the unique combination of carbon fiber and fiberglass, which together create a material with exceptional characteristics.
Strength and Durability
One of the most notable properties of carbon fiberglass is its enhanced strength and durability. The composite combines the high tensile strength of carbon fibers with the toughness and impact resistance of fiberglass.
Carbon Fiber Contribution: Carbon fibers are known for their remarkable strength-to-weight ratio. They are capable of withstanding significant loads and stresses without deforming or breaking. When integrated into a fiberglass matrix, they significantly increase the overall strength of the composite material.
Fiberglass Contribution: Fiberglass adds toughness and resistance to wear and tear. It helps distribute stress more evenly across the material, reducing the likelihood of localized failures. This combination results in a composite that is both strong and durable, making it suitable for demanding environments and applications.
Carbon fiberglass achieves a balance between rigidity and flexibility, which is essential for many applications. Rigidity: The carbon fibers in the composite provide substantial rigidity. This characteristic is important for applications where structural stability and resistance to deformation are critical, such as in aerospace components or sports equipment. Flexibility: Despite its rigidity, carbon fiberglass also offers some degree of flexibility. This is due to the fiberglass component, which can bend without breaking. The ability to flex without losing structural integrity makes carbon fiberglass versatile for use in applications that require a combination of strength and adaptability. The weight and density of carbon fiberglass are crucial factors that influence its usability in various industries. Comparison with Pure Carbon Fiber: Carbon fiberglass is generally heavier than pure carbon fiber but lighter than pure fiberglass. While pure carbon fiber is known for its exceptionally low weight, carbon fiberglass offers a more balanced weight-to-strength ratio. This makes it a suitable choice for applications where both weight and strength need to be optimized. Comparison with Pure Fiberglass: Compared to pure fiberglass, carbon fiberglass is considerably lighter while providing superior strength. This advantage is particularly valuable in industries where reducing weight is crucial, such as in the automotive and aerospace sectors. Carbon fiberglass performs well under varying environmental conditions, including extreme temperatures and exposure to chemicals. Thermal Resistance: Carbon fiberglass has good thermal stability. It can maintain its structural integrity across a broad range of temperatures. This property makes it suitable for applications that involve heat exposure, such as in automotive parts and industrial components. Chemical Resistance: The fiberglass component enhances the chemical resistance of the composite. Carbon fiberglass is resistant to many acids, alkalis, and solvents. This resistance helps in prolonging the material’s lifespan when exposed to harsh chemical environments.Flexibility and Rigidity
Weight and Density
Thermal and Chemical Resistance
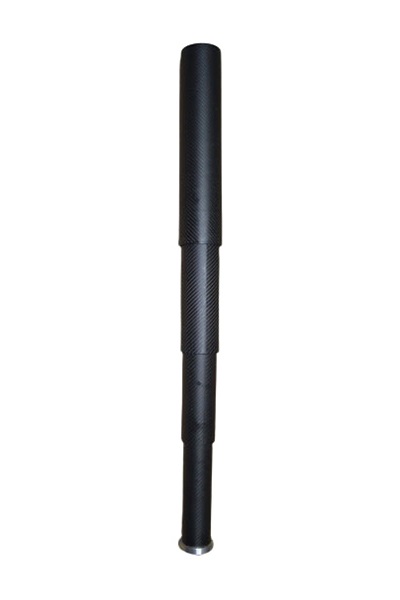

Carbon Fiberglass Size
Carbon fiberglass size refers to a special chemical coating or treatment applied to carbon or fiberglass fibers. This coating plays a crucial role in ensuring that the fibers bond properly with resins or other materials during the manufacturing of composite materials. Here’s a more detailed explanation:
What is Carbon Fiberglass Size?
“Size” is a protective and bonding agent that is applied to carbon or fiberglass filaments during their production process. It is typically a resin or chemical solution that helps the fibers maintain their integrity and performance when woven into fabrics or used in composite structures.
Purpose of Carbon Fiberglass Size:
Protecting the Fibers: Carbon and fiberglass fibers are extremely delicate and can easily break or become damaged during processing, handling, or when exposed to environmental factors like moisture or UV radiation. The size provides a layer of protection, preventing the fibers from damage.
Enhancing Fiber-Resin Bonding: In the creation of composite materials (e.g., carbon fiber reinforced plastic or fiberglass reinforced plastic), the fibers need to bond effectively with the resin. The size ensures that there is better adhesion between the fiber and the matrix (resin), which is crucial for the mechanical properties of the finished product. Without proper bonding, the composite material may fail under stress.
Improved Processability: The size improves the handling characteristics of the fibers, making them easier to weave, braid, or process into various forms like prepregs, rovings, or fabrics. This ensures that the fibers do not fray or break during the manufacturing process.
Optimizing Mechanical Performance: The right size can also influence the mechanical properties of the final composite, such as strength, flexibility, or heat resistance. This is especially important in high-performance applications like aerospace, automotive, and sporting goods, where the materials must meet strict performance criteria.
Types of Sizes:
The composition of the size depends on the intended application and the type of fiber used:
- Epoxy-based Size: Commonly used for carbon fiber composites, as epoxy resins offer strong adhesion to carbon fibers and excellent mechanical properties.
- Polyester or Vinyl Ester-based Size: Typically used for fiberglass fibers, these resins offer good bonding and are cost-effective for applications like boat hulls and certain automotive parts.
- Silane-based Size: Silanes are often used as coupling agents to enhance the bond between fibers and resins, particularly in the case of fiberglass.
Impact of Incorrect Sizing
- Weak Bonding: If the size is inadequate or improperly applied, it can lead to poor bonding between the fibers and the resin, resulting in lower overall strength and durability of the composite.
- Fiber Damage: Improperly sized fibers may become brittle or break during processing, leading to a loss of material integrity and defects in the final product.
- Process Issues: Without the right size, fibers might be difficult to handle, leading to issues like fraying or difficulty in weaving, which complicates production processes.
CCcarbon fiberglass size is a critical component in the manufacture of composite materials, as it ensures fiber protection, proper bonding with resins, and overall quality in the final product. Different sizes are chosen based on the type of fiber, the desired properties of the composite, and the application in which it will be used.
Carbon Fiberglass Strength
Carbon fiberglass strength refers to the mechanical strength characteristics of composite materials made from carbon fibers and fiberglass. These materials combine the unique properties of carbon fibers and fiberglass to create a high-performance material with superior strength-to-weight ratios, making them ideal for demanding applications in aerospace, automotive, sports, and industrial fields.
Strength of Carbon Fiber
Carbon fiber itself is known for its exceptional strength and stiffness, along with its low weight. The key aspects of carbon fiber strength include:
- Tensile Strength: Carbon fiber has very high tensile strength, meaning it can withstand a significant amount of stretching or pulling force before breaking. Tensile strength values for carbon fibers can range from 2,000 MPa (megapascals) to 6,000 MPa, depending on the type of fiber (standard modulus, intermediate modulus, or high modulus).
- Compressive Strength: Carbon fibers also possess good compressive strength, but they are typically more susceptible to buckling under compression compared to other materials like steel or aluminum.
- Stiffness (Modulus of Elasticity): Carbon fibers are also very stiff (high modulus of elasticity), which means they resist deformation under stress. This is crucial for applications where rigidity is required, such as in aerospace or structural components.
Strength of Carbon Fiberglass Composites
When carbon fiber and fiberglass are combined into a single composite material, they create a hybrid that can offer enhanced properties from both fibers:
Strength-to-Weight Ratio: Carbon fiberglass composites typically have an excellent strength-to-weight ratio, making them ideal for applications that require both strength and reduced weight. This is particularly valuable in industries like aerospace, automotive, and sports equipment, where lightweight but strong materials are crucial.
Balanced Properties: By blending carbon fibers with fiberglass, manufacturers can achieve a balance between the high strength and stiffness of carbon fiber and the flexibility and impact resistance of fiberglass. This results in a composite material that is both strong and tough, making it more versatile than either fiber alone.
Layering for Performance: In composite materials, carbon and fiberglass can be layered to optimize strength. For example, the outer layers might be carbon fiber for strength and stiffness, while the inner layers could be fiberglass for improved impact resistance and cost-effectiveness.
Factors Affecting Strength
The strength of carbon fiberglass composites depends on various factors, including:
- Fiber Content: The ratio of carbon fiber to fiberglass in the composite material influences its overall strength. Higher carbon fiber content typically results in higher strength and stiffness.
- Resin Matrix: The type and quality of the resin (epoxy, polyester, vinyl ester, etc.) used to bind the fibers together also plays a significant role in the material’s strength. Epoxy resins, for example, are known for their strong bonding capabilities and high mechanical properties.
- Manufacturing Process: The way the composite is manufactured (e.g., hand lay-up, filament winding, prepreg, or resin transfer molding) affects the alignment and bonding of the fibers, which can influence the final strength of the material.
- Orientation of Fibers: The orientation of the fibers in the composite affects its strength in different directions. For example, if the fibers are aligned in the direction of the load, the composite will be stronger in that direction. Multi-directional layups can help achieve strength in multiple directions.
Carbon fiberglass composites offer a unique combination of high strength, stiffness, and toughness, making them ideal for applications requiring a lightweight yet durable material. By leveraging the strengths of both carbon fiber and fiberglass, manufacturers can optimize their performance characteristics for specific needs, offering a balance between cost and high-end strength and impact resistance. The result is a versatile material that excels in industries ranging from aerospace to sports equipment.
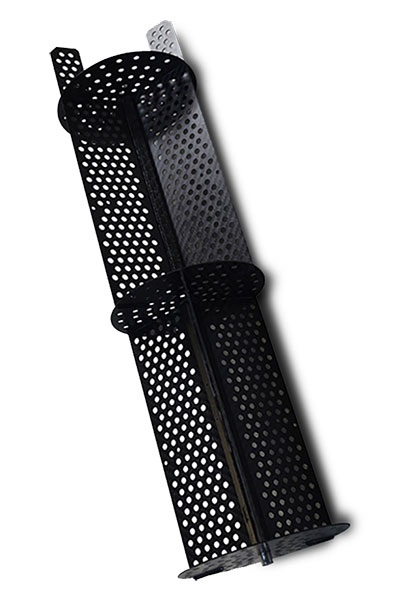
Thank you for your interest in our products. To receive our pricelist or for any inquiries, please fill out the form below. We will get back to you within 24 hours.
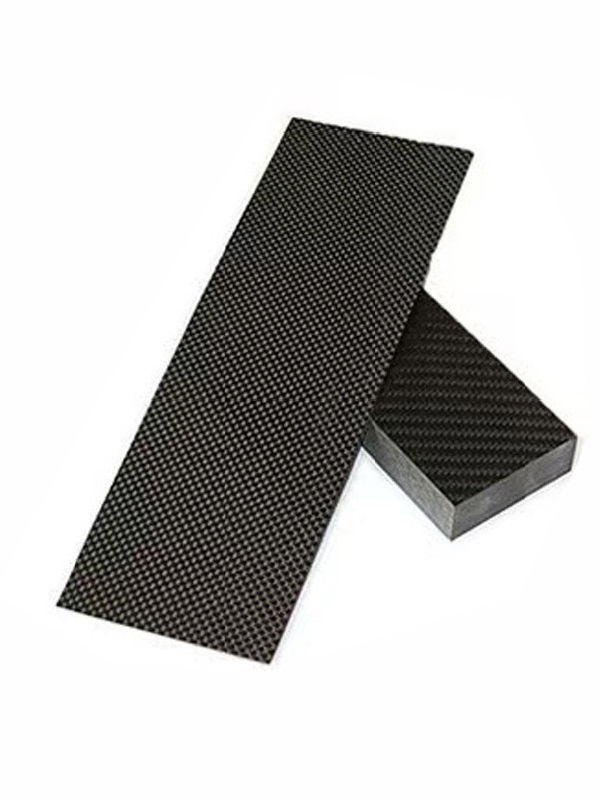
Carbon Fiberglass Price
Understanding the pricing of carbon fiberglass involves considering various factors that influence its cost. These factors can vary widely depending on the specifics of the material and its intended use.
Pricing Factors
Several key factors influence the price of carbon fiberglass:
Production Complexity: The manufacturing process for carbon fiberglass is more complex than for standard fiberglass. This complexity includes the preparation of carbon fibers, the weaving process, and the curing of the composite. The advanced technology and equipment required for producing high-quality carbon fiberglass contribute to its higher cost.
Material Quality: The quality of the raw materials used in carbon fiberglass affects its price. Higher-grade carbon fibers and resins result in better performance characteristics and durability, which are reflected in the cost. Premium materials typically lead to a higher price point for the final product.
Market Demand: Demand for carbon fiberglass in various industries such as aerospace, automotive, and sports equipment can drive up prices. When demand is high and supply is limited, prices tend to increase. Conversely, in periods of lower demand, prices may stabilize or decrease.
The price range for carbon fiberglass products can vary based on their type, size, and application. Here are some general price ranges: Carbon Fiberglass Sheets: The cost of carbon fiberglass sheets typically ranges from $30 to $150 per square meter. Prices can vary based on the thickness, weave pattern, and quality of the material. Specialty sheets with specific properties or certifications may be priced higher. Other Products: For carbon fiberglass products like rods, tubes, or custom-made components, prices can vary even more. For example, carbon fiberglass tubes might range from $50 to $200 per meter depending on their diameter and wall thickness. Comparing the cost of carbon fiberglass with other composite materials provides insight into its value relative to alternatives: Pure Carbon Fiber: Pure carbon fiber is generally more expensive than carbon fiberglass. The high strength-to-weight ratio and advanced production processes involved in making carbon fiber contribute to its higher cost. Carbon fiberglass offers a more cost-effective option while still providing substantial strength and durability. Fiberglass: Traditional fiberglass is less expensive than carbon fiberglass. While fiberglass provides good strength and durability, it lacks the superior performance characteristics of carbon fibers. The lower cost of fiberglass is attributed to its simpler production process and material properties.Price Range
Cost Comparison
The Differences between Fiberglass and Carbon Fiberglass
The main differences between fiberglass and carbon fiberglass (also known as carbon fiber reinforced fiberglass) stem from the materials themselves—carbon fiber and fiberglass—and their resulting properties. While both are used in composite materials, they offer distinct advantages and are suitable for different applications based on their specific characteristics.
Here’s a detailed comparison of fiberglass vs. carbon fiberglass:
Material Composition
- Fiberglass:
- Fiberglass is made from fine fibers of glass, typically E-glass or S-glass. These fibers are woven into fabrics or roving and then bonded with a resin to form composite materials.
- It is primarily composed of silica (sand) and other oxides like alumina.
- Carbon Fiberglass:
- Carbon Fiberglass: This composite combines carbon fibers with fiberglass to create a material that leverages the strengths of both components, making it stronger and more durable than typical materials, while also answering the question of how hard is carbon fiber. Carbon fibers provide exceptional strength and stiffness, while fiberglass adds toughness and impact resistance. This combination results in a material that is lightweight, strong, and durable.
- Carbon fiberglass refers to a composite material made by combining carbon fiber with fiberglass. This hybrid material blends the strength and stiffness of carbon fiber with the toughness and flexibility of fiberglass.
- Carbon fiber is made from carbon atoms bonded in long chains, which makes it extremely strong and lightweight.
Strength and Stiffness
- Fiberglass:
- Fiberglass is strong but not as stiff or strong as carbon fiber. Its tensile strength typically ranges from 1,000 MPa to 2,500 MPa, depending on the grade of fiberglass.
- Fiberglass has a lower modulus of elasticity, meaning it is more flexible and less rigid than carbon fiber.
- Carbon Fiberglass:
- Carbon fiber is significantly stronger and stiffer than fiberglass. Its tensile strength can range from 2,000 MPa to 6,000 MPa.
- Carbon fiberglass composites combine the best of both worlds: carbon fiber provides strength and stiffness, while fiberglass contributes additional flexibility and impact resistance.
Weight
- Fiberglass:
- Fiberglass is heavier than carbon fiber. While it is still considered lightweight compared to metals like steel and aluminum, its weight-to-strength ratio is lower than that of carbon fiber.
- Carbon Fiberglass:
- Carbon fiber is incredibly lightweight, which makes carbon fiberglass composites much lighter than pure fiberglass. The addition of carbon fiber in the composite significantly improves the strength-to-weight ratio, making it a preferred material for applications requiring both strength and low weight.
Cost
- Fiberglass:
- Fiberglass is much more affordable than carbon fiber. It is commonly used in industries where cost is a primary concern, such as boat manufacturing, construction, and some automotive applications.
- Carbon Fiberglass:
- Carbon fiber is expensive to produce, and incorporating it into a composite material makes carbon fiberglass composites more costly than pure fiberglass materials. However, carbon fiberglass offers superior performance and is typically used in high-performance applications.
Durability and Resistance to Fatigue
Fiberglass:
- Fiberglass is known for its good impact resistance and fatigue resistance. It’s not as brittle as carbon fiber, which can make it a better choice for applications requiring more toughness or energy absorption under impact.
- However, fiberglass can degrade over time when exposed to UV rays and moisture, leading to a reduction in its mechanical properties.
Carbon Fiberglass:
- Carbon fiber is more prone to brittleness and can fail catastrophically under high impact or sudden stress, especially if the resin matrix is not designed to handle it. However, it’s much more resistant to corrosion, UV damage, and extreme temperatures than fiberglass.
- Carbon fiberglass composites have better overall fatigue resistance compared to pure fiberglass due to the higher strength and stiffness provided by carbon fibers, although they may still be more prone to damage from impact.
Flexibility
- Fiberglass:
- Fiberglass is more flexible than carbon fiber, which makes it better at absorbing impact and preventing cracking or shattering when subjected to sudden forces.
- Carbon Fiberglass:
- The addition of carbon fiber makes carbon fiberglass composites stiffer than fiberglass alone, which reduces flexibility. However, the fiberglass in the mix helps retain some level of toughness and impact resistance.
Environmental Impact
- Fiberglass:
- Fiberglass production involves high energy consumption and the material is not biodegradable. Additionally, when fiberglass is disposed of, it can contribute to environmental waste.
- Carbon Fiberglass:
- Carbon fiber, like fiberglass, is not biodegradable, but carbon fiber production generally has a higher environmental impact due to the more energy-intensive manufacturing process. Recycling carbon fiber composites is currently an area of active research, but it remains challenging and less widespread than fiberglass recycling.
The choice between fiberglass and carbon fiberglass depends on the specific requirements of the application, such as strength, weight, cost, and durability.
- Fiberglass is a more affordable and flexible material that offers good overall performance, especially for applications where toughness, impact resistance, and cost-efficiency are important.
- Carbon fiberglass composites combine the strength, stiffness, and lightweight properties of carbon fiber with the toughness of fiberglass, making them ideal for high-performance applications like aerospace, automotive racing, and sports equipment. However, they come at a higher cost and are more prone to damage from impact.
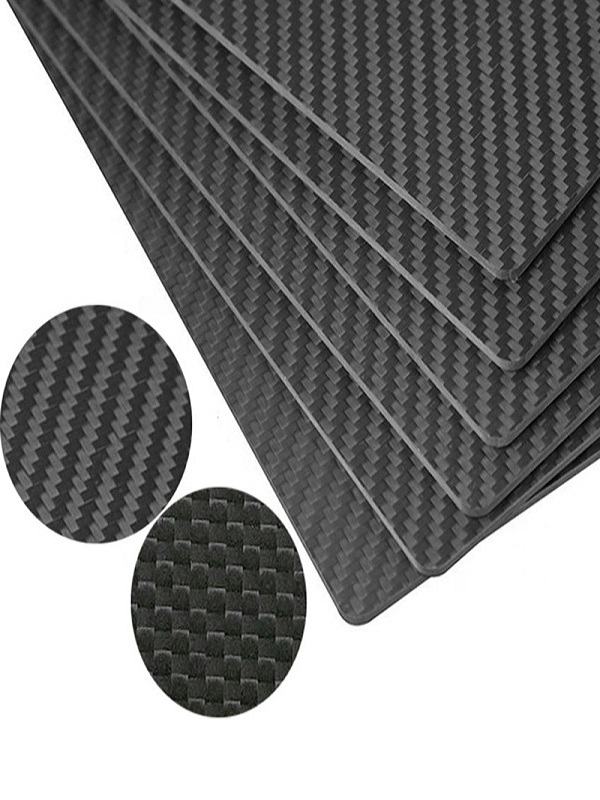
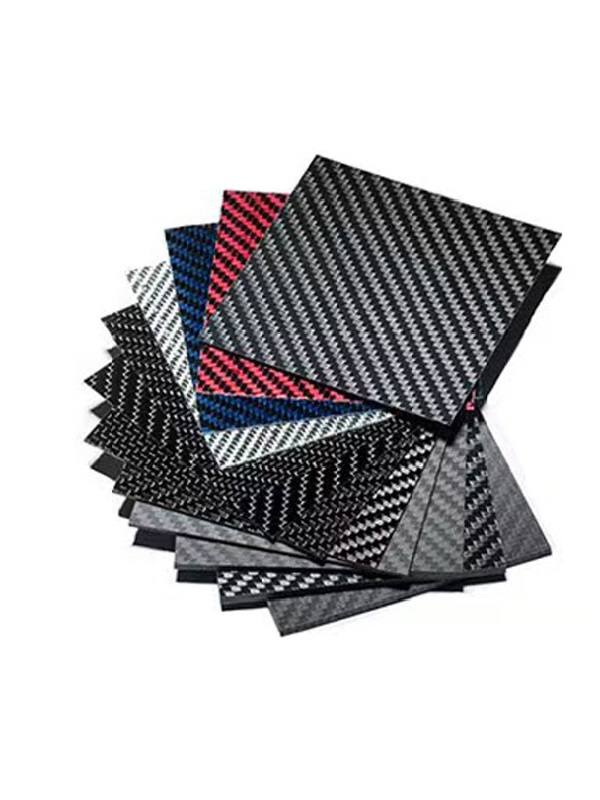
Fiberglass vs. Carbon Fiber Weight Difference
Understanding the weight differences between fiberglass, carbon fiber, and carbon fiberglass is crucial for selecting the appropriate material for various applications. Each material offers distinct weight characteristics that influence their suitability for different uses.
Weight Analysis
When comparing the weight of carbon fiber, fiberglass, and carbon fiberglass, it is important to consider each material’s density and weight-to-strength ratio:
Carbon Fiber: Carbon fiber is known for its exceptionally low weight while maintaining high strength. The density of carbon fiber typically ranges from 1.5 to 2.0 grams per cubic centimeter (g/cm³). This low density is one of the key reasons carbon fiber is favored in high-performance applications where weight reduction is crucial, such as in aerospace and high-end sports equipment.
Fiberglass: Fiberglass has a higher density compared to carbon fiber. The density of standard fiberglass usually ranges from 2.5 to 2.7 g/cm³. While fiberglass is heavier than carbon fiber, it still provides a good balance of strength and weight for many applications. Its greater weight is offset by its lower cost and ease of manufacturing. Carbon Fiberglass: Carbon fiberglass combines carbon fibers with fiberglass, resulting in a composite material that has a weight density somewhere between that of pure carbon fiber and standard fiberglass. The density of carbon fiberglass generally falls between 1.9 and 2.3 g/cm³. This balanced density provides a compromise between the ultra-lightweight properties of carbon fiber and the more cost-effective, heavier nature of fiberglass. The weight differences among these materials have significant implications for their use in various industries: Aerospace: In the aerospace industry, where minimizing weight is critical for fuel efficiency and performance, carbon fiber is often the material of choice. Its low weight and high strength make it ideal for aircraft and spacecraft components. Carbon fiberglass can also be used in aerospace applications where a balance of weight and cost is required. Automotive: For automotive applications, the weight of materials affects fuel efficiency and handling. Carbon fiber is used in high-performance and luxury vehicles to reduce weight and improve performance. Carbon fiberglass offers a more cost-effective option for automotive parts where some weight savings are desired but budget constraints are a consideration. Construction: In construction, the weight of materials impacts ease of handling and structural load considerations. Fiberglass is commonly used in construction due to its durability and relatively lower cost, despite its higher weight. Carbon fiberglass might be chosen for specialized construction applications where both strength and weight reduction are important but at a more economical price point compared to pure carbon fiber.Impact on Applications
Choosing The Right Carbon Fiberglass
Choosing the right carbon fiberglass composite material for your application depends on various factors, including performance requirements, cost considerations, environmental conditions, and manufacturing capabilities. Here’s a detailed guide to help you select the most appropriate carbon fiberglass based on key factors:
Determine the Application Requirements
Start by understanding the specific needs of your project, such as:
- Strength: How much tensile strength and stiffness do you need? Do you require a high strength-to-weight ratio or more flexibility and impact resistance?
- Durability: Will the composite be exposed to high temperatures, UV light, moisture, or harsh chemicals?
- Weight: How important is weight reduction in your application? For instance, in aerospace or automotive applications, the weight reduction is crucial, so choosing a composite with a high carbon fiber content will be important.
- Impact Resistance: Consider if the material will need to withstand sudden impacts or vibrations. Some hybrid carbon fiberglass materials combine the stiffness of carbon fiber with the impact resistance of fiberglass, making them ideal for specific applications like sporting goods or industrial equipment.
Balance Between Carbon Fiber and Fiberglass Content
The ratio of carbon fiber to fiberglass plays a major role in determining the composite’s properties:
- High Carbon Fiber Content (70-80% or more):
- Strength: Provides the highest strength-to-weight ratio, making it suitable for applications where performance and rigidity are key, such as in aerospace, high-performance automotive, and sports equipment.
- Stiffness: The material will be very stiff and resistant to deformation, making it ideal for parts that need to retain their shape under load (e.g., wing spars, car chassis, or bicycle frames).
- Cost: This will be a more expensive option due to the higher carbon fiber content.
- Balanced Carbon Fiber and Fiberglass (50-70% carbon fiber):
- Strength and Toughness: This ratio provides a good balance between strength and impact resistance. It’s suitable for applications like marine equipment, industrial tools, and some automotive parts, where both high performance and durability are needed, but cost is still a concern.
- Flexibility: This composite will have better flexibility and impact resistance compared to a high-carbon-fiber-only composite.
- Low Carbon Fiber Content (30-50% carbon fiber):
- Cost-Effective Option: For applications where cost-efficiency is more critical than top-tier strength and rigidity, a lower carbon fiber content may be suitable. This option is commonly used in structural panels or less demanding automotive parts.
Select the Right Resin Matrix
The resin matrix used in combination with carbon fiber and fiberglass plays an essential role in the overall performance of the composite. The choice of resin affects the strength, weight, thermal resistance, and cost:
- Epoxy Resins: Ideal for high-performance applications, as they provide excellent bonding strength with both carbon fiber and fiberglass, as well as superior mechanical properties. Epoxy composites are commonly used in aerospace, automotive, and sporting goods industries.
- Polyester Resins: These are cost-effective and provide good overall strength and durability, but they tend to be less resistant to temperature and environmental degradation compared to epoxies. Polyester resins are often used in marine and construction applications.
- Vinyl Ester Resins: These resins combine the best aspects of polyester and epoxy, offering good corrosion resistance, moderate mechanical properties, and affordability. Vinyl ester composites are commonly used in marine, automotive, and industrial applications.
Consider Environmental and Service Conditions
The conditions in which the composite will be used significantly influence the choice of carbon fiberglass material:
- Temperature: If the composite will be exposed to extreme temperatures, carbon fiber composites with high thermal stability should be chosen. Epoxy resin-based composites perform well in high-temperature environments compared to polyester or vinyl ester resins.
- UV Exposure: Carbon fiber is generally resistant to UV degradation, but the resin matrix can degrade under UV exposure. If the composite will be used outdoors (e.g., marine applications), consider UV-stable resins or coatings to protect the material.
- Moisture and Chemical Exposure: If the composite will be exposed to moisture or chemicals, such as in marine or industrial applications, consider using carbon fiberglass with resins that offer chemical resistance (e.g., vinyl ester or epoxy resins).
Manufacturing Process and Design Flexibility
Different manufacturing techniques can be used to produce carbon fiberglass composites, and the process chosen will depend on the application and desired performance characteristics:
- Hand Lay-Up or Wet Lay-Up: This is one of the simplest and most cost-effective processes. It involves layering fibers and resin by hand and is ideal for producing large components like boat hulls or industrial panels.
- Prepreg Lay-Up (Pre-impregnated Fibers): This method uses fibers pre-coated with resin and is typically used in high-performance applications. It ensures uniform resin distribution and is ideal for parts that need high strength and stiffness (e.g., automotive parts, aerospace components).
- Resin Transfer Molding (RTM): RTM is used for high-quality, large-scale production of composite parts. This process is common in the automotive and aerospace industries, where precision and consistent quality are critical.
- Filament Winding: This method involves winding fibers onto a mold in a controlled pattern. It is commonly used for cylindrical or tubular structures, such as pressure vessels and pipes.
- Compression Molding: Used to produce parts with intricate shapes, compression molding is suitable for medium to large-volume production and is common in automotive and consumer goods.
Performance Criteria to Consider
When selecting carbon fiberglass, ensure the material meets specific performance criteria for your application:
- Tensile Strength: Choose the right carbon fiber grade (e.g., standard modulus, intermediate modulus, high modulus) to match your strength requirements.
- Flexural Strength: Consider the bending strength needed for the part. Higher carbon fiber content typically results in higher flexural strength.
- Impact Resistance: If the material will be subject to high-impact forces, look for a carbon fiberglass composite with sufficient fiberglass content to provide energy absorption.
- Fatigue Resistance: Carbon fiberglass composites with well-distributed fibers and a strong resin matrix offer better fatigue resistance, ideal for applications subjected to repetitive stress.
Cost Considerations
The cost of carbon fiberglass composites depends on factors like carbon fiber content, the type of resin, and the manufacturing process. Consider the following:
- Higher Carbon Fiber Content = Higher Cost: Carbon fiber is expensive, so using it in greater quantities increases the material cost.
- Resin Type: Epoxy and vinyl ester resins tend to be more expensive than polyester, so factor in resin costs when deciding on your composite formulation.
- Manufacturing Method: Processes like prepreg lay-up and autoclave curing tend to be more expensive and labor-intensive than hand lay-up methods, which may not be necessary for lower-performance applications.
Testing and Certification
For critical applications, especially in aerospace or automotive industries, ensure the carbon fiberglass composite meets industry standards and passes necessary testing and certifications:
- ASTM standards for tensile, flexural, and impact testing.
- ISO standards for material quality and testing, particularly in regulated industries.
- Certifications like SAE (Society of Automotive Engineers) for automotive parts or FAA (Federal Aviation Administration) for aerospace components.
Choosing the Right Carbon Fiberglass
Choosing the right carbon fiberglass composite requires a balance between performance, durability, cost, and the specific needs of your application. Consider the following:
- For high-performance, weight-sensitive applications (aerospace, automotive racing), opt for a high carbon fiber content and epoxy resin.
- For marine, construction, or industrial applications, where cost is a significant factor, a carbon fiberglass hybrid with a higher fiberglass content might be more appropriate.
- Consider the manufacturing method and ensure it aligns with your desired production scale, whether you’re making small, custom parts or large, mass-produced items.
Ultimately, selecting the right carbon fiberglass composite involves understanding your material’s requirements, balancing performance with cost, and aligning the material selection with the manufacturing processes at your disposal.
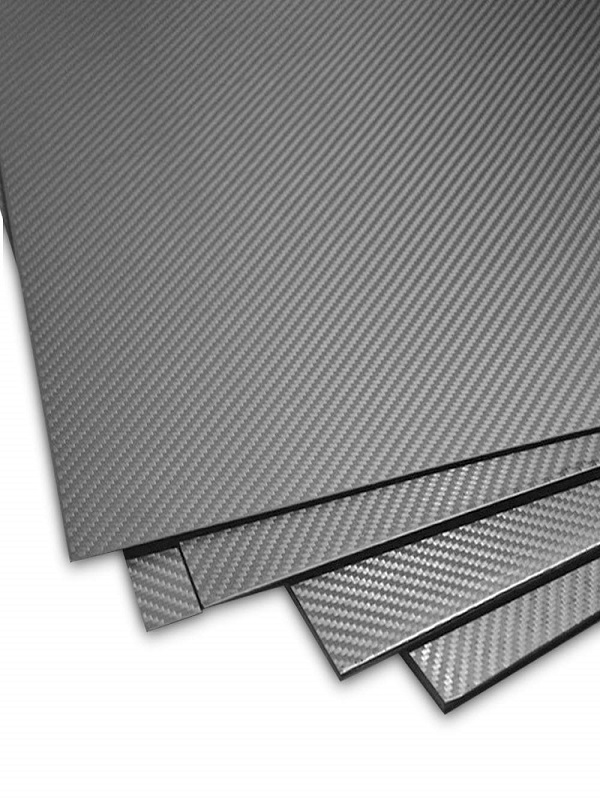
Purchase High-Strength, Lightweight Carbon Fiberglass
Carbon fiber is an exceptionally strong, lightweight, and rigid material made from fine, durable carbon crystalline filaments. Produced through a process of heating and stretching carbon strands, these fibers are woven together to create high-performance fabrics. Known for their superior strength-to-weight ratio, carbon fiber materials are widely used in aerospace, marine, automotive, sports equipment, and high-end consumer products where strength and weight reduction are critical.
Versatile Forms of Carbon Fiber Materials
Carbon fiber is available in multiple forms, including:
- Woven Fabrics – Offers excellent strength and flexibility for structural applications.
- Braided Sleeves & Tow – Ideal for reinforcing complex shapes and structures.
- Unidirectional Sheets – Provides high tensile strength in one direction for precision applications.
- Carbon Fiber Tape – Used for targeted reinforcement and repairs.
These materials are commonly combined with resins or metals to create composite materials with enhanced mechanical properties, replacing traditional steel and aluminum components in lightweight structural applications.
Ganglong Fiberglass – Your Trusted Supplier of Carbon Fiber Reinforcements
Ganglong Fiberglass supplies a wide range of carbon fiber reinforcement materials, including fabrics, sleeves, tow, and tapes. We enforce strict quality control measures to ensure our products meet the highest manufacturing standards, delivering maximum strength and aesthetic perfection.
Key Benefits of Our Carbon Fiberglass Materials
- High Strength-to-Weight Ratio – Exceptional rigidity with minimal weight.
- Waterproof & Corrosion-Resistant – Ideal for marine and automotive use.
- Aerodynamic Properties – Reduces drag and enhances performance.
- Thermal & Electrical Conductivity – Suitable for high-tech applications.
- Structural Reinforcement – Perfect for aerospace, automotive, and sports industries.
Ideal Applications
- Aerospace & Automotive – Enhances performance while reducing weight.
- Marine Engineering – Provides durability and corrosion resistance.
- Sports Equipment – Used in bicycles, golf clubs, and racing gear.
- Consumer Electronics – Creates sleek, high-tech, and durable designs.
Ganglong Fiberglass ensures that every carbon fiber product is engineered for precision, durability, and peak performance. Whether you need lightweight reinforcements, customized woven patterns, or structural composite solutions, we offer top-tier materials at competitive prices.
Contact us today to explore our carbon fiberglass materials and find the best solution for your project!
FAQs about Carbon Fiberglass
Is carbon fiber stronger than fiberglass?
Can carbon fiber stop a bullet?
What's stronger, Kevlar or carbon fiber?
Is Kevlar carbon fiber bulletproof?
Is fiberglass as strong as Kevlar?
Is carbon fiber actually stronger than steel?
Why does carbon fiber cost so much?
How to tell carbon fiber from fiberglass?
Why is carbon fiber so tough?
What is the strongest composite material?
Is carbon fiber stronger than leather?
Can carbon fiber and fiberglass be used together?
Why can't you touch carbon fiber?
Is Kevlar stronger than fiberglass?
Why is carbon fiber not used more?
What fiberglass looks like carbon fiber?
Is carbon fiber resin the same as fiberglass resin?
Can you use carbon fiber without resin?
How can you tell fiberglass from carbon fiber?
Can you build a house with carbon fiber?
What is carbon fiber fiberglass?
Is carbon fiber cheaper than fiberglass?
What is the best epoxy to use with carbon fiber?
Does carbon fiber do well with heat?
What is carbon fiber used for?
What are the disadvantages of carbon fiber?
Cost: Carbon fiber is expensive to produce and work with, which limits its use to high-end or critical applications.
Brittleness: Carbon fiber composites can be brittle, making them more prone to cracking or shattering under certain types of stress, such as impact or sharp blows.
Complex manufacturing process: Working with carbon fiber requires specialized techniques, equipment, and expertise, which increases the complexity and cost of manufacturing.
Repairability: If a carbon fiber structure is damaged, it is often difficult and costly to repair. In some cases, the entire part may need to be replaced.
Is carbon fiber stronger than steel?
Why is carbon fiber so expensive?
Is carbon fiber safe for humans?
Why do car guys love carbon fiber?
Is carbon fiber waterproof?
Why do people buy carbon fiber?
What is the difference between fiberglass and carbon fiber?
What is the strongest material for a car?
Where is carbon fiber most used?
Is fiberglass or carbon fiber hull better?
What is the longest lasting hull material?
What is the strongest type of fiberglass?
What is the lifespan of a fiberglass hull?
Which type of hull is most efficient?
Is fiberglass stronger than Kevlar?
Is there a better material than carbon fiber?
What are the pros and cons of fiberglass vs carbon fiber?
Cost-Effective: Much cheaper than carbon fiber.
Durability: Good impact resistance and long lifespan.
Easier to Repair: Repairs are less costly and more straightforward.
Widely Available: Easier to source and work with.
Cons of Fiberglass:
Heavier: Heavier than carbon fiber, leading to lower performance in speed and fuel efficiency.
Lower Strength: Not as strong or stiff as carbon fiber.
Pros of Carbon Fiber:
Lightweight: Much lighter than fiberglass, improving speed and efficiency.
High Strength and Stiffness: Superior tensile strength and rigidity.
Aesthetic Appeal: High-tech appearance and often used in luxury or high-performance products.
Cons of Carbon Fiber:
Expensive: Significantly more costly than fiberglass.
Brittle: Can be more prone to cracking under sharp impacts.
Difficult to Repair: Repairs are more complex and expensive.
Is carbon fiber good for boats?
What material is better than fiberglass?
What weakens fiberglass?
UV Exposure: Prolonged exposure to sunlight can degrade the resin, leading to weakening and brittleness.
Moisture Infiltration: Water ingress can cause delamination and degradation of the resin matrix.
Physical Damage: Impact or stress can cause cracks, which may spread and weaken the structure.
Chemical Exposure: Certain chemicals, including some solvents and fuels, can degrade the resin and weaken the fiberglass composite.
Poor Maintenance: Lack of regular maintenance, such as cleaning and inspection, can lead to gradual deterioration.
Thank you for your interest in our products. To receive our pricelist or for any inquiries, please fill out the form below. We will get back to you within 24 hours.