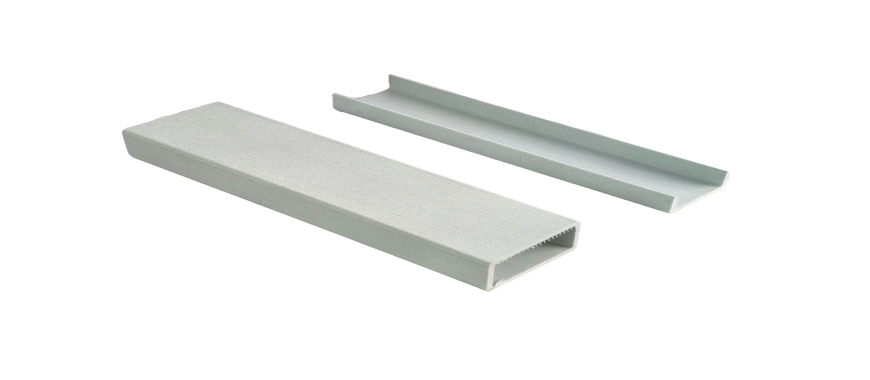
Epoxy FRP pipe is a fiberglass-reinforced plastic pipe that uses epoxy resin as its matrix material. The epoxy resin significantly enhances the pipe’s mechanical properties, including strength, durability, and chemical resistance. In epoxy FRP pipe, the epoxy resin bonds with the fiberglass, creating a robust and reliable composite structure. This combination allows the pipe to withstand harsh environmental conditions, such as exposure to corrosive chemicals, extreme temperatures, and high pressure. Epoxy FRP pipe is widely used in industries like chemical processing, water treatment, and oil and gas, where long-lasting performance and resistance to corrosion are essential. Its superior qualities make it a preferred choice for challenging industrial applications. Epoxy FRP pipe offers high chemical resistance, strength, a 150 psi pressure rating, and a C-veil + UV inhibitor exterior for weather and corrosion protection.
What is Epoxy FRP Pipe
Epoxy FRP pipe is a type of fiberglass-reinforced plastic pipe that utilizes an epoxy resin matrix to bind the glass fibers, resulting in a composite material that exhibits exceptional strength, durability, and corrosion resistance. FRP pipe bell and spigot joints are often used with epoxy FRP pipes, providing secure and leak-proof connections that are critical for maintaining pipeline integrity under pressure. Epoxy FRP pipe is designed to handle a variety of industrial applications where traditional piping materials may not perform as effectively. With its superior chemical resistance, high strength-to-weight ratio, and ability to withstand harsh environmental conditions, epoxy FRP pipe has become a preferred choice for industries such as chemical processing, water treatment, and oil and gas. GangLong Fiberglass produces high-quality epoxy FRP pipes that meet stringent industry standards, ensuring reliable performance and long service life.
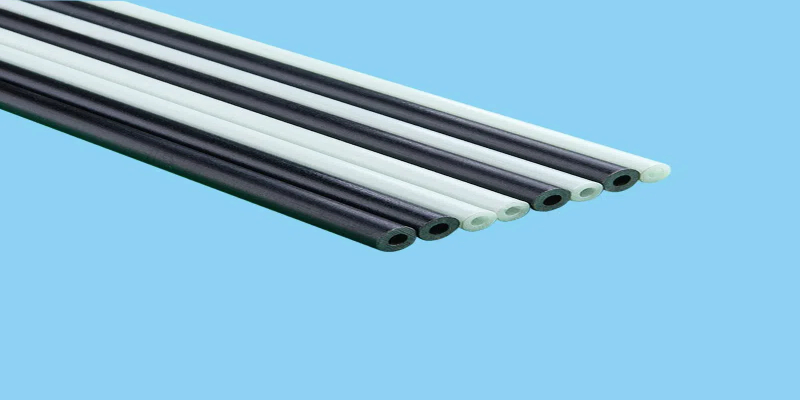
What are the Benefits of Epoxy FRP Pipe
Epoxy FRP pipe offers several distinct advantages over traditional piping materials, making it an attractive option for a wide range of industrial applications. Here are some key benefits of using epoxy FRP pipe:
- Corrosion Resistance: One of the most significant advantages of epoxy FRP pipe is its excellent resistance to corrosion. The clear epoxy resin for FRP pipe acts as a protective barrier, preventing the pipe from being damaged by corrosive substances such as acids, bases, and salts. This corrosion resistance makes epoxy FRP pipe ideal for applications involving aggressive chemicals, seawater, and other corrosive environments.
- High Strength-to-Weight Ratio: Epoxy FRP pipe boasts a high strength-to-weight ratio, making it significantly lighter than traditional materials like steel and concrete while providing comparable or even superior strength. This lightweight nature facilitates easier handling, transportation, and installation, reducing labor costs and time. Despite its lightweight design, epoxy FRP pipe can withstand high pressures and mechanical loads, ensuring reliable performance in demanding applications.
- Temperature and Chemical Stability: Epoxy resin has excellent temperature and chemical stability, allowing epoxy FRP pipe to maintain its structural integrity in extreme temperatures and when exposed to a wide range of chemicals. This stability makes epoxy FRP pipe suitable for applications involving high-temperature fluids, aggressive chemicals, and fluctuating operating conditions.
- Smooth Inner Surface: The smooth inner surface of epoxy FRP pipe minimizes friction loss, promoting efficient fluid flow and reducing energy consumption in pumping systems. This characteristic is particularly advantageous in applications such as water distribution and chemical processing, where maintaining optimal flow rates is essential.
- Long Service Life: Epoxy FRP pipe is designed for long-term performance, often providing a service life of 50 years or more. Its resistance to corrosion, chemical attack, and environmental factors means that it requires minimal maintenance and offers a cost-effective solution for fluid transport over its lifespan.
These benefits make epoxy FRP pipe an ideal choice for industries that require reliable, efficient, and durable piping solutions capable of withstanding challenging conditions.
Epoxy FRP Pipe vs. Traditional Piping Materials
Epoxy FRP pipes offer numerous advantages over traditional piping materials such as steel, PVC, and concrete. While each material has its own set of characteristics, epoxy FRP pipe stands out in several key areas:
- Corrosion Resistance: Traditional materials like steel are prone to corrosion when exposed to moisture, chemicals, or seawater, leading to reduced service life and increased maintenance costs. In contrast, epoxy FRP pipe is inherently resistant to corrosion, making it an excellent choice for applications involving corrosive fluids or harsh environmental conditions. This resistance eliminates the need for protective coatings or liners, further reducing maintenance requirements.
- Weight: Steel and concrete pipes are heavy and require specialized equipment for transportation, handling, and installation. Epoxy FRP pipe is significantly lighter, allowing for easier and more cost-effective installation. Its lightweight nature also reduces the need for heavy-duty supports and foundations, lowering overall project costs.
- Ease of Installation: Epoxy FRP pipe’s lightweight design and ease of handling result in faster and more efficient installation compared to traditional materials. The use of adhesive bonding for joints simplifies the installation process, eliminating the need for welding or complex mechanical connections. This ease of installation translates to shorter project timelines and reduced labor costs.
- Durability and Longevity: While traditional materials like steel may suffer from corrosion and require frequent maintenance, epoxy FRP pipe is designed for long-term durability. Its resistance to chemical attack, abrasion, and environmental factors ensures a long service life, reducing the need for replacements and minimizing downtime.
- Thermal Insulation: Epoxy FRP pipe has low thermal conductivity, providing inherent thermal insulation. This property helps maintain the temperature of fluids being transported, reducing the need for additional insulation materials and improving energy efficiency in heating or cooling processes.
These advantages highlight the superiority of epoxy FRP pipe over traditional materials, making it the preferred choice for many modern industrial applications.
The Manufacturing Process of Epoxy FRP Pipe
The manufacturing process of epoxy FRP pipe involves several key steps, each contributing to the pipe’s final properties and performance. The following is an overview of the process used by GangLong Fiberglass to produce high-quality epoxy FRP pipes:
- Mandrel Preparation: The process begins with preparing the mandrel, which serves as the mold around which the glass fibers are wound. The mandrel’s shape and size determine the dimensions of the final pipe. It is coated with a release agent to facilitate easy removal of the pipe after curing.
- Filament Winding: Continuous long glass fibers are impregnated with epoxy resin and wound onto the mandrel in a precise pattern. The winding pattern, angle, and fiber tension are controlled to achieve the desired mechanical properties. By varying the winding angle and pattern, manufacturers can tailor the pipe’s strength, stiffness, and pressure rating to meet specific application requirements.
- Curing: After the fibers are wound onto the mandrel, the pipe is cured to harden the epoxy resin and create a solid composite structure. Curing is typically achieved through controlled heating, which accelerates the chemical reaction between the resin and hardener. The result is a strong, rigid pipe with a smooth inner and outer surface.
- Mandrel Removal: Once the pipe is fully cured, it is removed from the mandrel. The release agent applied earlier ensures that the pipe can be easily detached without damaging its surface.
- Finishing and Inspection: The finished pipe undergoes inspection and finishing processes to ensure it meets the required specifications. This may include trimming the ends, applying protective coatings, and conducting quality control tests to verify the pipe’s dimensions, strength, and performance.
This manufacturing process results in an epoxy FRP pipe that offers superior strength, corrosion resistance, and durability, making it suitable for demanding industrial applications.
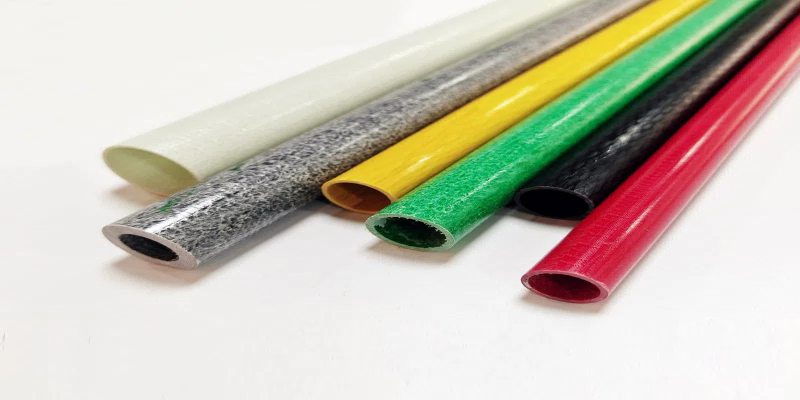
Design Considerations for Epoxy FRP Pipe Systems
When designing an epoxy FRP pipe system, several factors must be taken into account to ensure optimal performance and reliability:
- Pressure and Temperature Ratings: The pipe’s design must account for the operating pressure and temperature conditions it will encounter. Epoxy FRP pipes can be customized to meet specific pressure and temperature requirements, making them suitable for various industrial applications.
- Chemical Compatibility: The epoxy resin used in the pipe must be compatible with the fluids being transported. GangLong Fiberglass offers a range of resin systems that provide excellent chemical resistance to various substances, ensuring the pipe’s long-term integrity.
- Support and Anchoring: Proper support and anchoring are essential for maintaining the structural integrity of the piping system. Epoxy FRP pipes should be supported at regular intervals to prevent sagging and movement. Expansion joints and anchors may be required to accommodate thermal expansion and contraction.
- Jointing and Fittings: The choice of joints and fittings is crucial for ensuring leak-free connections in the piping system. GangLong Fiberglass provides a variety of fittings, including flanges, elbows, and tees, designed to work seamlessly with epoxy FRP pipes. Proper installation techniques and adhesive application are essential for achieving secure joints.
By addressing these design considerations, engineers can create epoxy FRP pipe systems that are tailored to the specific requirements of their applications, ensuring reliable and efficient operation.
Epoxy FRP Pipe: Enhancing Performance and Durability
Epoxy FRP pipe represents a significant advancement in piping technology. By integrating fiberglass with epoxy resin, it offers exceptional strength, durability, and resistance to environmental factors. Epoxy serves as the matrix material, binding the fiberglass fibers and providing a rigid, resilient structure. This combination results in a piping solution that excels in industries where other materials might fail, such as chemical processing, water treatment, and oil and gas. The unique properties of epoxy resin, including its high mechanical strength, chemical resistance, and thermal stability, make epoxy FRP pipe an ideal choice for environments that demand robust performance and long-lasting durability. Moreover, when combined with rigid fiberglass tubing, the resulting structure further enhances the system’s overall performance, ensuring reliability even under extreme conditions.
The Role of Epoxy in FRP Pipes
Epoxy plays a crucial role in the construction of FRP pipes. It acts as the matrix that holds the fiberglass fibers together, creating a composite material that offers a high level of mechanical strength and resilience. Epoxy resin is known for its excellent adhesive properties, which ensure a strong bond between the fibers, resulting in a pipe that can withstand high pressures, mechanical stress, and thermal fluctuations. The incorporation of epoxy in FRP pipes, including FRP pipe piles, not only enhances their physical properties but also provides superior resistance to corrosion and chemical degradation, making these pipes suitable for a wide range of industrial applications.
Mechanical Strength and Structural Integrity
Epoxy FRP pipe is renowned for its mechanical strength. The epoxy resin binds the fiberglass strands in a manner that distributes stress evenly throughout the pipe’s structure. This ensures that the pipe can handle high internal pressures and mechanical loads without cracking or deforming. The epoxy resin’s rigidity also contributes to the pipe’s structural integrity, providing a stable and durable solution for transporting fluids in demanding environments. This strength makes epoxy FRP pipes particularly well-suited for applications that involve high-pressure systems, such as chemical transport and industrial processing, where maintaining a leak-proof and reliable piping network is essential.
Chemical Resistance of Epoxy FRP Pipe
Epoxy resin is inherently resistant to a wide range of chemicals, including acids, alkalis, solvents, and salts. This chemical resistance is transferred to the entire structure when used in the construction of FRP pipes or FRP pipe bridges, making both highly suitable for environments where exposure to aggressive substances is common. In particular, Epoxy FRP pipe can withstand corrosive chemicals that would typically degrade or corrode other piping materials. This property makes it an excellent choice for chemical processing plants, wastewater treatment facilities, and any application where the pipe may come into contact with harsh substances. The chemical resistance of epoxy FRP pipes also contributes to their longevity, reducing the need for frequent replacements or repairs.
Thermal Stability and Temperature Tolerance
Epoxy FRP pipes exhibit exceptional thermal stability, allowing them to operate effectively in a wide range of temperatures. The epoxy resin used in these pipes can withstand both high and low temperatures without losing its structural integrity or performance characteristics. This makes epoxy FRP pipe suitable for applications involving hot fluids or environments where temperature fluctuations are frequent. The thermal stability of epoxy ensures that the pipe remains intact and functional even when subjected to extreme temperature conditions, minimizing the risk of thermal degradation or failure. This feature is particularly important in industries such as oil and gas, where piping systems may be exposed to varying temperature extremes.
Contribution to Pipe Longevity
One of the most significant advantages of using epoxy in FRP pipes is the extended lifespan it provides. Epoxy FRP pipes are designed to endure harsh conditions, including mechanical stress, chemical exposure, and temperature fluctuations, without showing signs of wear or degradation. The epoxy resin acts as a protective barrier, shielding the fiberglass from environmental factors that could otherwise weaken the pipe over time. This results in a piping solution that offers a longer service life compared to many traditional materials. The durability and longevity of epoxy FRP pipes reduce maintenance costs and downtime, making them a cost-effective choice for long-term applications.
Design Flexibility and Customization
Epoxy FRP pipes offer a high degree of design flexibility, allowing them to be customized to meet specific project requirements. The filament winding process used in their construction can be adjusted to produce pipes with different diameters, lengths, and wall thicknesses, catering to various applications. Additionally, the epoxy resin formulation can be modified to enhance specific properties, such as chemical resistance or thermal stability, depending on the intended use of the pipe. This customization extends to fittings and joints, enabling the creation of complex piping systems that are tailored to the unique needs of each installation. The ability to customize epoxy FRP pipe makes it a versatile solution for a wide range of industrial and commercial applications.
Quality Standards and Compliance
Epoxy FRP pipes are manufactured to meet stringent quality standards and industry regulations. These standards cover various aspects of the pipes, including their mechanical properties, chemical resistance, pressure ratings, and safety features. Compliance with standards such as ASTM, ISO, and other relevant industry certifications ensures that epoxy FRP pipes are suitable for use in critical applications where safety and performance are paramount. Manufacturers like GangLong Fiberglass adhere to these standards to provide customers with reliable products that meet the specific requirements of their projects. Quality control measures during the manufacturing process include rigorous testing for pressure resistance, leak-proof performance, and material consistency, ensuring that each pipe meets the highest standards of quality and durability.
The Strength of Fibercast FRP Pipe in Industrial Settings
Installation and Maintenance of Epoxy FRP Pipe
Installation of Epoxy FRP Pipe
Proper installation of epoxy FRP (Fiber Reinforced Plastic) pipes is critical to their long-term performance, ensuring the system operates efficiently and remains free from damage or leaks. The process begins with proper handling and storage of the pipes before installation. Epoxy FRP pipes are generally lightweight and easier to handle than traditional materials like steel, but care must be taken to avoid dropping or striking the pipes, as this could damage the material or disrupt the resin’s structural integrity.
Key Installation Steps:
- Site Preparation: The installation site must be clean, level, and free from debris. Ensure that the foundation where the pipes will be laid is solid and stable to prevent settling or shifting over time. For underground installations, proper trenching and backfilling are necessary to provide adequate support.
- Cutting and Joining Pipes: Epoxy FRP pipes are often delivered in standard lengths, but they may need to be cut to specific sizes on-site. Cutting should be done using a non-abrasive tool, such as a diamond blade or pipe cutter, to avoid damaging the material. It is important to ensure smooth and even cuts at the ends to ensure tight and secure connections.
- Joining Methods: Epoxy FRP pipes can be connected using various joining techniques:
- Adhesive Bonding: This is a popular method for joining FRP pipes, where specially formulated adhesives are used to bond pipe ends. The adhesive should be compatible with the pipe’s resin and ensure a watertight seal. Proper surface preparation, such as cleaning and abrading the pipe ends, is essential for ensuring strong adhesion.
- Flanges: Flanged joints are widely used for larger diameter pipes and allow for easy disassembly and maintenance. Flanges are bolted together and sealed with a gasket. Proper alignment and torque are crucial to ensure that the flanges form a leak-free connection.
- Mechanical Couplings: These couplings provide a flexible, secure connection and are especially useful when pipes need to be disassembled or realigned periodically. Mechanical couplings are equipped with rubber seals or gaskets, ensuring a tight fit and leak-free operation.
- Installation Considerations: During installation, care should be taken to avoid over-tightening joints or flanges, as this may cause stress on the material and lead to failure. Additionally, epoxy FRP pipes should be supported with appropriate brackets or hangers to avoid sagging, especially in long stretches or horizontal installations. For underground or submerged installations, special coatings or protective layers may be applied to protect the pipes from external stress and environmental damage.
- Testing: Once the pipes are installed, pressure testing is essential to ensure that there are no leaks and that the entire system is working as expected. Pressure testing should be done according to industry standards and the specific pressure ratings of the pipes. This ensures that the system is fully sealed before use.
Maintenance of Epoxy FRP Pipe
While epoxy FRP pipes require less maintenance compared to traditional materials like steel, routine care is essential to preserve their long-term functionality and prevent issues like leaks or reduced performance. Maintenance practices for epoxy FRP pipes focus on monitoring their condition and ensuring they are free from physical damage, corrosion, or other signs of wear.
Key Maintenance Practices:
- Routine Inspections: Regular inspections are essential for identifying any signs of damage, wear, or leakage in the system. Inspections should focus on joints, flanges, and couplings, as these are common areas where issues may arise. It’s also important to check for any signs of physical damage from external forces, such as impacts or abrasions. In high-stress environments, such as offshore or industrial settings, more frequent inspections are recommended.
- Leak Detection: Even though epoxy FRP pipes are resistant to corrosion, leaks can still occur at joints or due to accidental damage. During inspections, look for any signs of moisture around pipe joints or unusual pressure drops in the system. If a leak is detected, prompt repairs should be made, and the damaged section should be replaced or re-sealed using the appropriate methods.
- Cleaning and Maintenance of Interior Surfaces: The interior surface of epoxy FRP pipes is smooth, which helps to minimize friction loss and prevents the buildup of scale and other debris. However, over time, particularly in systems carrying chemicals, mineral deposits or biofilms may form inside the pipes. To maintain optimal flow, it is important to periodically clean the interior using appropriate cleaning solutions and methods that are safe for epoxy FRP. Some chemical-resistant cleaning agents or pressure washing may be used, but care must be taken not to damage the pipe’s interior lining.
- Protection from UV Exposure: While epoxy FRP pipes are resistant to many environmental factors, extended exposure to ultraviolet (UV) radiation can degrade the resin over time. UV protection coatings or paints can be applied to the exterior of the pipes to prevent UV damage, especially when the pipes are used in outdoor or sun-exposed environments.
- Handling and Storage: Proper handling and storage of epoxy FRP pipes during operation are essential for preventing accidental damage. Pipes should be supported adequately to prevent sagging, and they should be kept away from areas where they may be exposed to heavy impacts. If repairs or replacement are necessary, make sure to use appropriate tools and methods to avoid further damage to the pipe.
- Repairs and Replacements: Although epoxy FRP pipes are durable, accidents or prolonged exposure to extreme conditions can cause localized damage. Small cracks or damage to the pipe can often be repaired with epoxy resin or a suitable patching material. For large-scale damage, such as cracks that affect the structural integrity of the pipe, replacement may be necessary. Properly trained professionals should perform these repairs or replacements to ensure the pipe’s continued safety and performance.
By following these best practices for installation and maintenance, epoxy FRP pipes can deliver reliable, long-term performance in demanding environments. The combination of correct installation methods, routine inspections, cleaning, and occasional repairs will ensure that the pipes maintain their durability and resistance to corrosion, thus minimizing downtime and reducing the need for costly replacements.
How Density of FRP Pipe Impacts Performance and Durability
What are the Key Features of Epoxy FRP Pipe
Epoxy FRP pipe is characterized by several key features that make it an excellent choice for demanding industrial applications:
- Superior Corrosion Resistance: Epoxy FRP pipe is known for its outstanding resistance to corrosion. The epoxy resin matrix provides a protective barrier that shields the pipe from the damaging effects of chemicals, acids, alkalis, and salts. This resistance is especially valuable in environments where traditional materials like steel and concrete are prone to corrosion, resulting in frequent maintenance and reduced service life.
- High Strength and Stiffness: The combination of fiberglass reinforcement and epoxy resin results in a pipe with a high strength-to-weight ratio. Epoxy FRP pipes are strong and stiff, capable of withstanding high internal pressures and mechanical loads while remaining lightweight. This feature makes them suitable for applications where strength and structural integrity are paramount.
- Temperature and Chemical Stability: Epoxy FRP pipes are designed to maintain their properties across a wide range of temperatures. They can handle both high and low temperatures without becoming brittle or losing their strength. Additionally, the epoxy resin matrix is chemically stable, ensuring that the pipe retains its performance even when exposed to aggressive chemicals.
- Smooth Interior Surface: The inner surface of epoxy FRP pipe is smooth, reducing friction losses and promoting efficient fluid flow. This characteristic helps reduce energy consumption in pumping systems and prevents the buildup of deposits inside the pipe, maintaining optimal flow rates.
- Lightweight and Easy to Install: Despite their strength, epoxy FRP pipes are lightweight compared to traditional materials like steel and concrete. This makes them easier to transport, handle, and install, resulting in reduced labor costs and faster project completion times.
These features make epoxy FRP pipe a versatile and reliable solution for fluid transport in a variety of challenging environments.
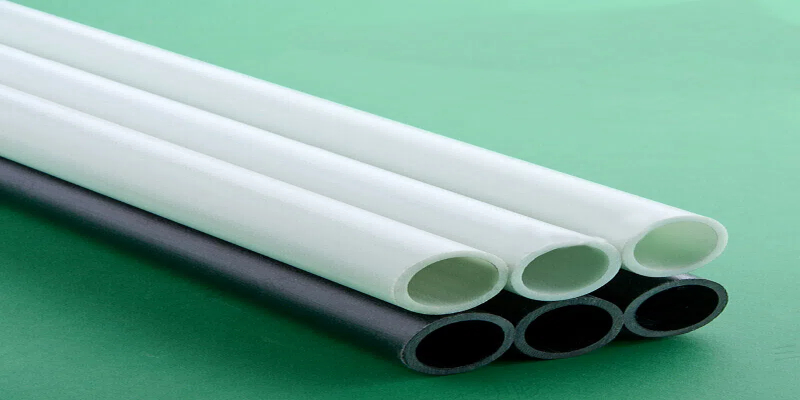
Applications of Epoxy FRP Pipe
Chemical Processing
In the chemical processing industry, epoxy FRP pipes are essential for transporting aggressive chemicals, acids, alkalis, and solvents. These pipes are favored due to their exceptional corrosion resistance, which is critical in environments where other materials would quickly degrade. Epoxy resins, which are used to bind the glass fibers, are highly resistant to most chemicals, allowing epoxy FRP pipes to safely handle substances that would normally erode or corrode traditional materials like steel or PVC.
Additionally, these pipes are used in chemical reactors, where they help safely manage reactive chemicals at various temperatures and pressures. In storage tanks and waste treatment systems, the pipes ensure that toxic byproducts or chemicals do not leak or cause environmental harm. Their durability and chemical stability reduce maintenance needs and downtime, improving the overall efficiency of chemical manufacturing processes.
Water Treatment and Distribution
Epoxy FRP pipes are extensively used in water treatment and distribution systems because they offer an excellent balance of strength, corrosion resistance, and smooth internal surfaces. In water treatment plants, epoxy FRP pipes transport potable water, wastewater, and process fluids without leaching harmful substances into the water. This is a critical factor for maintaining the purity and quality of water in both municipal and industrial water treatment facilities.
The smooth interior surfaces of these pipes help minimize friction losses, which improves water flow efficiency and reduces energy consumption over time. Whether used for freshwater pipelines or wastewater systems, epoxy FRP pipes prevent the buildup of scale and biofilm, which can clog pipes made from other materials. Their resistance to microbial growth and external environmental factors makes them an ideal solution for long-term, sustainable water distribution and treatment.
Oil and Gas
In the oil and gas industry, epoxy FRP pipes are utilized to transport various fluids such as crude oil, natural gas, and produced water. These pipes excel in environments where corrosive agents like seawater, hydrocarbons, and chemicals can accelerate the degradation of traditional materials such as steel. Epoxy FRP pipes provide a cost-effective and long-lasting solution to these challenges, particularly in offshore applications and pipeline systems.
For offshore platforms, these pipes are often used in risers and flowlines, which transport oil and gas from the seabed to production facilities. Their resistance to seawater corrosion ensures that they can withstand harsh marine environments. Additionally, in refineries and gas treatment facilities, epoxy FRP pipes handle the transportation of chemicals and water, while their mechanical strength ensures they can manage high-pressure fluids without failure. They are also used in injection systems, where their durability under high pressure and temperature is critical.
Industrial Waste Management
Epoxy FRP pipes are a vital component of industrial waste management systems due to their ability to safely transport and contain hazardous or toxic materials. Industries such as manufacturing, mining, and pharmaceuticals generate corrosive and toxic waste byproducts that require secure handling to prevent environmental contamination. Epoxy FRP pipes offer a safe solution by resisting the corrosive effects of acidic or alkaline waste, chemicals, and even radioactive substances.
These pipes are used in various applications, including the transportation of liquid waste, wastewater treatment, and the containment of hazardous fluids in landfills or waste treatment facilities. Their resistance to chemical degradation and environmental stress ensures the integrity of waste containment systems, preventing costly leaks and environmental accidents. Epoxy FRP pipes contribute to maintaining safety and compliance with environmental regulations while minimizing operational interruptions in waste management processes.
Power Generation
In power generation facilities, epoxy FRP pipes are an essential part of cooling water systems, flue gas desulfurization units, and other processes that involve the transport of corrosive fluids and gases. Power plants rely on efficient cooling systems, often involving the use of large volumes of water. Epoxy FRP pipes are well-suited to this task due to their ability to resist the corrosion caused by water, chemicals, and high temperatures.
For flue gas desulfurization systems, which are designed to reduce sulfur dioxide emissions from power plants, epoxy FRP pipes ensure the safe transport of sulfuric acid and other byproducts. These pipes’ durability and resistance to aggressive chemicals make them invaluable in preventing corrosion, scaling, and premature failure of plant components. In addition, their high thermal stability makes them suitable for use in processes that involve steam, hot gases, or high-temperature fluids, all of which are common in power generation.
These detailed applications showcase the broad range of uses for epoxy FRP pipes across industries that require high performance, durability, and resistance to harsh conditions. Their versatility, combined with their ability to withstand extreme chemicals, temperatures, and mechanical stress, makes them a reliable choice for fluid transport, containment, and protection in critical industrial settings.
Cutting FRP Pipe with Precision: Tools and Techniques to Use
FAQs about Epoxy Frp Pipe
Yes, epoxy bonds well to FRP (Fiberglass Reinforced Plastic), making it one of the most effective adhesives for this material. Epoxy adhesives are specially formulated to create strong, durable bonds between the resin matrix in FRP and other surfaces, including metal, wood, and concrete. When used correctly, epoxy forms a rigid, chemical-resistant bond that enhances the strength of FRP structures. To ensure optimal bonding, the FRP surface must be properly prepared. This typically involves cleaning the surface of any dirt, grease, or other contaminants, followed by light sanding to create a rough texture that allows the epoxy to adhere better. Once the surface is prepared, the epoxy is applied and allowed to cure, resulting in a bond that can withstand various stresses, such as pressure, temperature changes, and chemical exposure. Epoxy is often chosen in FRP applications where a reliable, long-lasting bond is needed.
Epoxy FRP refers to a type of fiberglass-reinforced plastic that uses epoxy resin as its matrix material. In FRP construction, fibers such as glass or carbon are embedded in a resin matrix to form a composite material. When epoxy is used as the resin, the resulting FRP offers superior mechanical strength, chemical resistance, and thermal stability compared to other types of resin, such as polyester or vinyl ester. Epoxy FRP is widely used in high-performance applications where durability and environmental resistance are critical, such as in aerospace, automotive, and chemical processing industries. The epoxy resin provides excellent adhesion to the reinforcing fibers, ensuring that the composite maintains its integrity under mechanical stress and harsh environmental conditions. The combination of epoxy resin and reinforcing fibers makes epoxy FRP an ideal material for structural components, piping systems, and other critical infrastructure.
In piping, FRP stands for Fiberglass Reinforced Plastic. It is a composite material made by reinforcing a plastic matrix (often polyester, vinyl ester, or epoxy resin) with fiberglass fibers. FRP piping is highly valued for its corrosion resistance, lightweight properties, and strength, making it an excellent choice for industries where these characteristics are required, such as chemical processing, water treatment, and oil and gas. Unlike traditional piping materials like metal or concrete, FRP piping is non-corrosive, meaning it doesn’t rust or degrade when exposed to harsh chemicals, moisture, or extreme temperatures. This quality extends the lifespan of FRP piping, reducing maintenance costs and downtime. Additionally, FRP pipes are much lighter than metal alternatives, making them easier to transport and install. This combination of durability, lightweight design, and corrosion resistance makes FRP a reliable material for various piping systems in industrial and commercial applications.
GRP stands for Glass Reinforced Plastic, also known as Glass Fiber Reinforced Polymer (GFRP). It refers to a composite material made by combining glass fibers with a polymer matrix, typically a resin such as epoxy, polyester, or vinyl ester. This combination results in a material that is both strong and lightweight, offering excellent resistance to corrosion, chemicals, and environmental stress.
GRP pipes are commonly used in applications that require high durability, such as in the transportation of chemicals, water, and wastewater. They are also utilized in industries like oil and gas, agriculture, and power generation due to their ability to withstand harsh conditions. GRP pipes are also resistant to scaling, ensuring minimal maintenance and longer lifespans compared to traditional piping materials.
GRP pipes, though widely used for their excellent strength and corrosion resistance, also come with some drawbacks. One major disadvantage is their vulnerability to UV degradation if not properly coated or treated. Over time, prolonged exposure to sunlight can weaken the resin, causing the pipe to deteriorate.
Additionally, GRP pipes are susceptible to cracking under extreme impact or shock loading, especially when the pipe is exposed to freezing conditions or significant mechanical stress. This can lead to costly repairs or replacement.
The installation of GRP pipes also requires skilled labor, and they can be difficult to modify once installed. The initial cost of GRP pipes can be higher than that of other materials, especially when considering the specialized manufacturing processes involved in producing them. Furthermore, GRP pipes are not suitable for certain high-pressure or high-temperature applications.
Despite their many advantages, FRP pipes do have some drawbacks. One of the main disadvantages is their relatively high upfront cost. Manufacturing FRP pipes requires specialized materials, and the production process is more expensive compared to traditional piping materials like PVC or steel.
FRP pipes also have limitations when it comes to handling high-impact situations. While they are generally durable, they can become brittle over time if exposed to UV radiation or extreme temperatures unless they are specially treated or coated.
Another disadvantage is that FRP pipes are more difficult to repair compared to traditional pipes. If damaged, repairs often require professional intervention. Additionally, FRP pipes may not be suitable for certain applications where mechanical flexibility is a high priority, as they are more rigid compared to other flexible pipe options.
The three main types of plastic pipes are PVC (Polyvinyl Chloride), CPVC (Chlorinated Polyvinyl Chloride), and PEX (Cross-Linked Polyethylene). Each type has its own unique characteristics and uses.
PVC pipes are widely used in plumbing, drainage, and irrigation systems. They are known for being lightweight, durable, and resistant to corrosion, but they cannot withstand high temperatures or certain chemicals.
CPVC pipes are similar to PVC but are chlorinated, which makes them more resistant to high temperatures and certain chemicals. CPVC is often used in hot water supply systems and industrial applications.
PEX pipes are flexible and often used in plumbing systems for both hot and cold water. They are easy to install due to their flexibility and resistance to freezing, but they are not suitable for outdoor or UV-exposed applications.
FRP pipes, particularly those made with epoxy resin, are used in a wide variety of applications due to their strength, corrosion resistance, and lightweight properties. They are commonly used in industries such as water treatment, chemical processing, oil and gas, and mining. These pipes are ideal for transporting aggressive chemicals, acidic or alkaline fluids, and wastewater because they resist corrosion and degradation from harsh environments.
They are also used in the construction of pipelines for cooling systems, desalination plants, and fire suppression systems. In addition, FRP pipes are popular in sewage systems and for handling slurries or abrasive materials. The durable nature of FRP ensures longevity and minimal maintenance, making them a cost-effective solution for industries with demanding conditions. Their resistance to environmental factors such as UV rays, temperature extremes, and moisture further extends their range of applications.
FRP pipes, especially those made with epoxy resins, are known for their ability to be designed with varying degrees of flexibility. However, compared to other piping materials like PVC or rubber, FRP pipes are not as flexible. Epoxy FRP pipes are typically rigid but can tolerate minor bending within their design specifications. Their flexibility is mostly determined by the type of fibers used (such as carbon fiber or glass fiber) and the specific resin that binds the fibers.
In general, these pipes are favored for their structural integrity, resistance to corrosion, and durability under high-pressure conditions rather than their flexibility. If flexibility is required, the design of the FRP pipe can be adjusted, but in most applications, rigidity and strength are more important. Therefore, while FRP pipes are somewhat flexible, they are not as flexible as other pipe materials specifically designed for flexibility.
FRP (Fiber Reinforced Plastic) and GRP (Glass Reinforced Plastic) pipes are both composite materials used in piping systems, but the main difference lies in the type of reinforcement used. FRP pipes use various fibers such as carbon, aramid, or glass to reinforce the plastic, while GRP pipes specifically use glass fibers as reinforcement. The reinforcement in both cases strengthens the material and makes it more durable.
The resins used in these pipes can also differ. GRP pipes generally use epoxy or polyester resins, whereas FRP pipes can use a broader range of resins depending on the specific requirements of the application. In terms of performance, both types of pipes offer high strength, chemical resistance, and light weight, making them ideal for industrial applications. However, FRP pipes are more versatile because of the wider variety of fibers and resins used, offering customization for different applications.
Yes, epoxy can stick to fiberglass, and it forms a strong, durable bond. In fact, fiberglass is often used as a reinforcement material in epoxy composites. The surface of the fiberglass needs to be properly prepared for the epoxy to adhere effectively. This typically involves cleaning the fiberglass surface to remove any dirt, oils, or contaminants and roughening the surface slightly through sanding to increase the bonding area. Once these steps are completed, the epoxy resin will bond well with the fiberglass, creating a strong and stable structure. This combination of epoxy and fiberglass is widely used in applications like boat hulls, automotive parts, and FRP pipes due to its strength, durability, and resistance to harsh environments.
When compared to PVC (Polyvinyl Chloride), several types of pipes offer greater strength. FRP (Fiber Reinforced Plastic) pipes, for example, are often stronger than PVC due to the reinforcement provided by fiberglass or other fibers embedded in the resin matrix. These pipes are especially strong in terms of tensile strength and impact resistance. Similarly, HDPE (High-Density Polyethylene) pipes are known for their toughness and flexibility, making them a suitable alternative to PVC in certain applications. Metal pipes, such as steel or ductile iron pipes, are also generally stronger than PVC, offering higher pressure ratings and greater structural strength, though they tend to be heavier and more susceptible to corrosion. The choice of material depends on the specific strength and durability requirements of the application.
Epoxy generally adheres to most materials, but there are some surfaces that it struggles to bond with. These include materials that are extremely smooth or non-porous, such as Teflon, silicone, or polyethylene. These materials have low surface energy, which makes it difficult for epoxy to form a strong bond. Additionally, epoxy does not bond well with materials that are coated with wax, oil, or dirt, as these contaminants interfere with the adhesion process. For best results, surfaces should be clean, dry, and free of any oils or coatings. In some cases, surface preparation such as sanding or priming may be required to ensure proper adhesion.
FRP (Fiber Reinforced Plastic) pipes are typically made using one of three types of resin: polyester, vinyl ester, or epoxy. Each resin has distinct properties suited for specific applications. Polyester resin is commonly used in general applications due to its cost-effectiveness and good resistance to corrosion, particularly in water and sewage systems. Vinyl ester resin offers improved resistance to aggressive chemicals and high temperatures, making it ideal for chemical processing plants. Epoxy resin is known for its excellent strength and resistance to heat and chemicals, often used in applications requiring high-performance materials. The choice of resin affects the overall mechanical properties, durability, and resistance to various environmental factors, which is why selecting the appropriate resin for each project is essential.
FRP (Fiber Reinforced Plastic) pipes generally have a temperature limit ranging from -50°F to 250°F (-46°C to 121°C), although this can vary depending on the type of resin used. Thermosetting resins like polyester or vinyl ester are commonly used in FRP pipes and offer good resistance to heat. For high-temperature applications, resins such as epoxy can be used to provide enhanced thermal stability. However, beyond these temperature limits, the material’s mechanical properties could degrade, leading to reduced performance or potential failure. FRP pipes can also be customized to handle specific temperature ranges by selecting the appropriate resin and fiber reinforcement. Therefore, understanding the specific application requirements is essential when choosing an FRP pipe for high-temperature environments.
The pressure rating for FRP (Fiber Reinforced Plastic) pipes varies depending on several factors, including the type of resin, fiber reinforcement, and wall thickness. In general, FRP pipes can have pressure ratings ranging from 50 psi to over 1,000 psi. The specific pressure rating is determined based on the pipe’s design parameters and its intended use. For example, in water treatment or chemical industries, FRP pipes are typically designed to handle moderate to high pressure levels. The strength of the reinforcing fibers (such as glass or carbon) and the resin used also contribute to the overall pressure tolerance of the pipe. Manufacturers often provide specific pressure ratings based on rigorous testing to ensure the safety and reliability of the pipes under various operating conditions.
The life expectancy of a GRP (Glass Reinforced Plastic) pipe typically ranges from 50 to 70 years, similar to other types of FRP pipes. This extended life expectancy is largely due to the corrosion-resistant properties of glass fibers, which are particularly beneficial in industries dealing with water, sewage, and chemicals. GRP pipes are designed to handle various environmental factors such as UV radiation, temperature fluctuations, and pressure changes, making them ideal for long-term use in challenging conditions. Factors like operating pressure, temperature, exposure to harsh chemicals, and proper installation can influence the longevity of GRP pipes. Regular inspection and maintenance can also help ensure that the pipes remain in good condition over time.
FRP (Fiber Reinforced Plastic) and GRP (Glass Reinforced Plastic) pipes are both composite materials made of a resin matrix reinforced with fibers, but the key difference lies in the type of reinforcing fiber used. FRP pipes can be made using various fibers such as carbon, aramid, or glass, while GRP pipes specifically use glass fibers as reinforcement. This gives GRP pipes excellent strength, corrosion resistance, and low weight, making them ideal for applications in water treatment, chemicals, and oil industries. FRP pipes, with their broader fiber options, can be designed for more specialized requirements, including high-strength applications or resistance to particular chemicals. Both types of pipes are lightweight, corrosion-resistant, and durable, but GRP pipes tend to be more common due to the cost-effectiveness and availability of glass fibers.
The design life of an FRP (Fiber Reinforced Plastic) pipe typically ranges from 50 to 70 years, depending on factors like the specific resin used, operating conditions, and maintenance. FRP pipes are known for their excellent corrosion resistance, which makes them durable in harsh environments. They are commonly used in industries such as chemical, oil, and water treatment, where longevity is crucial. The pipes can withstand extreme chemical exposure and resist wear from abrasives, which helps extend their service life. However, it’s important to note that the design life also depends on factors like temperature, pressure, and exposure to UV radiation. Regular inspection and maintenance can also help in prolonging the lifespan of FRP pipes.
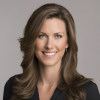
As the editor of GangLong Fiberglass, I have years of experience and in-depth research, focusing on cable tray products, fiberglass solutions, and grille systems. I incorporate years of industry insights and practical experience into every content, committed to promoting the progress of the industry. At GangLong Fiberglass, my commitment is reflected in every product, from innovative cable trays to durable fiberglass solutions and sturdy grille systems. As an authoritative voice in the industry, my goal is to provide valuable information to professionals and businesses and promote forward-looking solutions.