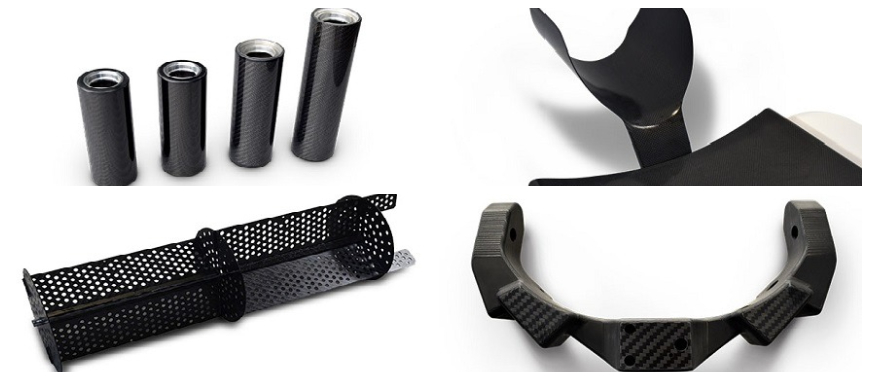
Fiberglass cloth vs carbon fiber are two of the most widely used materials in the manufacturing of high-performance components. Fiberglass, known for its strength and lightweight properties, is often used in industries like construction, automotive, and aerospace. Carbon fiber, on the other hand, offers even greater strength-to-weight ratios and is a key material in advanced engineering applications. Both materials are commonly combined to create composite materials that benefit from the unique properties of each. The combination of fiberglass cloth and carbon fiber is particularly valued for its ability to create durable, lightweight products that are both strong and resistant to wear and corrosion. These materials play a critical role in producing everything from high-end vehicles to sporting equipment.
Fiberglass Cloth vs Carbon Fiber: Weight Difference Explained
Fiberglass Weight
Fiberglass is a composite material made from fine fibers of glass, and its weight is a key factor in determining its suitability for various applications. Fiberglass typically has a density of around 2.5 g/cm³, which makes it relatively heavier than carbon fiber but still lightweight compared to many metals. It is often chosen for applications where weight is not the primary concern but strength and durability are essential. Its density gives fiberglass its solid and robust properties, making it an ideal choice for construction materials, boat hulls, and even insulation products.
Despite its weight, fiberglass is still preferred in applications where its affordability and ease of manufacturing are prioritized over weight reduction. Additionally, fiberglass is highly resistant to environmental factors such as moisture and corrosion, which makes it ideal for long-lasting structural components in both industrial and commercial settings.
Carbon Fiber Weight
Carbon fiber, known for its extremely low density, typically weighs about 1.6 g/cm³, making it significantly lighter than fiberglass cloth. Fiberglass, on the other hand, generally weighs around 2.5 g/cm³, which is noticeably heavier than carbon fiber. This lightweight characteristic of carbon fiber is what makes it a top choice for high-performance applications, especially where strength and weight are critical factors, such as in the aerospace, automotive, and sports industries. The lower weight of carbon fiber, combined with its high tensile strength, makes it particularly valuable in industries requiring both high structural integrity and reduced weight, such as the manufacturing of race cars, aircraft, and advanced sporting equipment.
When comparing fiberglass cloth vs carbon fiber, the difference in weight plays a significant role in the material’s application. Fiberglass cloth is typically favored for projects where weight is less of a concern, such as in construction and certain automotive applications, offering good durability and flexibility at a lower cost. However, carbon fiber excels in scenarios where performance is the priority, and the reduction of weight plays a crucial role in improving overall efficiency and functionality. This high strength-to-weight ratio allows for the design of lighter yet stronger structures, making carbon fiber the material of choice for applications in which reducing weight can significantly enhance performance—whether it’s in racing, high-end automotive parts, or advanced sporting equipment.
Advantages of Fiberglass Cloth Carbon Fiber
- Lower Density of Carbon Fiber: Carbon fiber’s significantly lower density compared to fiberglass makes it the superior material for applications requiring lightweight yet high-strength components.
- Strength-to-Weight Ratio: Carbon fiber’s strength-to-weight ratio is much higher than that of fiberglass, allowing for lightweight components without compromising on strength.
- Cost Efficiency: Fiberglass, being more affordable than carbon fiber, is the material of choice in applications where cost is a more significant factor than weight reduction.
- Durability: Both fiberglass and carbon fiber offer excellent resistance to corrosion, but fiberglass is more suitable for applications where environmental durability is necessary but weight is less critical.
- Flexibility in Manufacturing: Fiberglass can be easily molded into various shapes and forms, making it ideal for large, complex designs, while carbon fiber’s lightweight and rigidity make it perfect for precision-engineered components.
Each material has its specific advantages depending on the particular needs of the application. When combined, fiberglass cloth and carbon fiber can create composite materials that harness the benefits of both, offering optimal strength, weight, and durability for advanced applications.
Advantages of Fiberglass Reinforced Plastic Solar Panel Systems
Fiberglass Cloth vs Carbon Fiber: Comparing Fiberglass, Carbon Fiber, and Kevlar
What is Kevlar?
Kevlar is a unique synthetic fiber made from aramid (aromatic polyamide) polymers. It is renowned for its exceptional strength-to-weight ratio and is often used in high-performance applications requiring toughness and durability. Unlike fiberglass cloth vs carbon fiber, which are made from glass and carbon filaments, respectively, Kevlar is an organic fiber that provides superior resistance to impacts, abrasions, and heat. Its resilience and flexibility make it an ideal choice for protective gear, such as bulletproof vests, and other safety applications.
While carbon fiber cloth vs fiberglass are both exceptional materials, they serve different purposes. Fiberglass cloth is known for its flexibility and impact resistance, making it highly suitable for applications where durability and cost-efficiency are paramount. It is often used in the construction of boat hulls, tanks, and industrial components. On the other hand, carbon fiber is favored in industries where weight reduction and high strength are critical. Its exceptional rigidity and high strength-to-weight ratio allow it to be used in aerospace, automotive, and high-performance sporting goods, such as racing bicycles and professional-grade pickleball paddles.
Kevlar’s unique properties are a result of its molecular structure, which consists of long, rigid molecules that are tightly bound together. This structure allows it to absorb and dissipate energy from impacts, providing unmatched protection in hostile environments. Kevlar is also highly resistant to chemicals and has excellent thermal stability, making it suitable for extreme conditions. While carbon fiber excels in scenarios where performance and weight reduction are crucial, and fiberglass cloth is ideal for flexible, durable applications, Kevlar stands out in terms of impact protection and energy absorption.
Strength and Durability
Each of these three materials—fiberglass, carbon fiber, and Kevlar—offers a distinctive combination of strength, durability, and performance benefits. While they each excel in different areas, they are all integral in various industries, from automotive to protective gear. Let’s break down their key strengths:
- Carbon Fiber: Known for its outstanding strength and rigidity, carbon fiber has one of the highest strength-to-weight ratios among materials. It is incredibly stiff and does not easily bend, making it ideal for high-performance applications where structural integrity is paramount.
- Fiberglass: While slightly less stiff than carbon fiber, fiberglass offers excellent toughness and flexibility. It is highly resistant to impact and can bend without breaking, making it well-suited for applications where some degree of flexibility is needed, such as in boat hulls and insulation.
- Kevlar: Kevlar’s defining characteristic is its abrasion resistance and energy absorption. Unlike carbon fiber and fiberglass, Kevlar excels in protective applications where the material must withstand high impacts or abrasions without breaking down. Its flexibility makes it a preferred material in items like bulletproof vests, helmets, and gloves.
Applications and Performance
Each of these materials shines in specific applications, depending on the desired performance characteristics.
- Carbon Fiber: Carbon fiber is commonly used in the automotive, aerospace, and sports industries. Its lightweight yet strong properties make it ideal for use in high-performance vehicles, such as race cars, motorcycles, and even airplanes. It is also used in advanced sporting equipment, such as bicycles, tennis rackets, and golf clubs, where strength and minimal weight are critical.
- Fiberglass: Fiberglass is a popular material in the construction and marine industries. It is often used in the production of boat hulls, where its toughness and flexibility allow for long-lasting durability in harsh water conditions. Additionally, fiberglass is used in insulation, pipes, and roofing materials due to its resistance to corrosion and environmental degradation.
- Kevlar: The primary applications for Kevlar are in protective gear. Its high tensile strength and ability to absorb impact energy make it the material of choice for bulletproof vests, body armor, and helmets. It is also used in cut-resistant gloves, high-performance tires, and military gear. Kevlar’s resistance to abrasion and heat allows it to perform well in environments where other materials might fail.
Advantages of Fiberglass Cloth Carbon Fiber and Kevlar
- Strength-to-Weight Ratio: Carbon fiber is unparalleled in terms of its strength-to-weight ratio, offering the most rigidity with the least amount of mass. This makes it ideal for applications where every gram counts.
- Toughness and Flexibility: Fiberglass provides a balance of toughness and flexibility, making it suitable for large structures and components that require durability but can afford some degree of bending.
- Impact and Abrasion Resistance: Kevlar excels in environments that demand exceptional protection from impacts, abrasions, and sharp objects. Its ability to absorb and dissipate energy makes it irreplaceable in safety equipment.
- Corrosion Resistance: Both fiberglass and Kevlar are highly resistant to corrosion, whereas carbon fiber’s resistance is more dependent on the type of resin used to bond it. This gives fiberglass and Kevlar an edge in harsh environmental conditions.
- Manufacturing Flexibility: Fiberglass is particularly flexible in terms of manufacturing, allowing it to be molded into intricate shapes and used for a wide range of applications. Carbon fiber is less flexible but highly precise, while Kevlar’s flexibility makes it suitable for applications that require a soft but strong material.
Each of these materials—fiberglass cloth carbon fiber and Kevlar—brings unique advantages depending on the performance needs of the product. Whether for lightweight strength, impact resistance, or flexibility, they play critical roles in advancing technology across various industries.
Finding the Perfect Oval Fiberglass Tub for Sale
Fiberglass Cloth vs Carbon Fiber: A Comparison of Strength
Fiberglass Strength
Fiberglass cloth vs carbon fiber: Fiberglass is a composite material made from woven glass fibers that are bonded together with a resin. Its inherent strength comes from the glass fibers, which provide excellent resistance to impacts and stress. Fiberglass cloth is often used in applications where toughness and durability are critical, but flexibility is still required. Its ability to absorb impacts without shattering or breaking makes it an excellent choice for environments where materials will be subjected to physical stress, such as in the automotive, marine, and construction industries.
When comparing fiberglass cloth vs carbon fiber, both materials offer distinct advantages. Fiberglass is generally more affordable, versatile, and easier to work with, making it ideal for applications that require cost-effectiveness without sacrificing strength. However, carbon fiber is superior when it comes to strength-to-weight ratio and stiffness. While fiberglass cloth provides good durability and impact resistance, carbon fiber offers higher performance in areas that demand rigidity and minimal weight, such as in aerospace, high-end automotive parts, and sporting equipment. Carbon fiber’s lighter weight makes it the preferred choice for performance-driven applications, while fiberglass excels in environments where durability and toughness are the main requirements.
One of the key strengths of fiberglass, particularly evident in fiberglass lagging cloth, is its ability to withstand bending and deformation without losing structural integrity. This flexibility makes it ideal for applications requiring resilience, such as boat hulls that must endure impacts from waves and debris. Additionally, fiberglass lagging cloth is highly resistant to corrosion and extreme temperatures, making it a reliable choice for outdoor, marine, and industrial environments. Its dual role as both a protective and insulating material underscores its versatility.
Despite being more flexible than carbon fiber, fiberglass is not as stiff and does not have the same high tensile strength. However, its ability to perform in a wide range of temperatures, resist chemical exposure, and handle moderate stress makes it suitable for many structural applications where weight and rigidity are less critical than impact resistance.
Carbon Fiber Strength
Carbon fiber, on the other hand, is known for its exceptional tensile strength and stiffness. It has one of the highest strength-to-weight ratios of any material, making it an ideal choice for applications that require high structural integrity while minimizing weight. Carbon fiber is made from thin filaments of carbon that are bonded together, typically using a polymer resin. This gives it an incredibly rigid structure, which allows it to maintain its shape and resist bending under heavy loads.
The superior tensile strength of carbon fiber makes it ideal for applications where high strength and stiffness are critical. In contrast to fiberglass, carbon fiber is not as flexible, meaning it is more likely to crack or break under stress if not properly supported. However, its stiffness is precisely why it is used in high-performance applications such as aerospace, automotive, and sporting goods. Carbon fiber’s ability to resist stretching and deformation under load makes it a preferred choice for structural components like aircraft wings, race car frames, and bicycle frames.
Carbon fiber’s strength also allows it to be used in thinner layers compared to fiberglass, which reduces the overall weight of a structure without sacrificing its integrity. Its resistance to corrosion and fatigue further enhances its durability, making it a material of choice in environments where both performance and longevity are required.
Key Differences in Strength: Fiberglass Cloth Carbon Fiber
- Tensile Strength: Carbon fiber has significantly higher tensile strength than fiberglass. It can withstand greater amounts of stress before breaking or stretching, making it more suitable for structural applications where high load-bearing capacity is essential.
- Flexibility: Fiberglass is more flexible than carbon fiber, which makes it a better choice in situations where the material needs to bend or absorb impacts without shattering. This flexibility is useful in applications like boat hulls, storage tanks, and insulation.
- Stiffness: Carbon fiber is much stiffer than fiberglass, which means it provides superior rigidity in structural components. This stiffness is crucial for applications like aerospace components, where maintaining the shape of a structure under stress is critical.
- Impact Resistance: While both materials offer good impact resistance, fiberglass has the advantage in terms of toughness. It can absorb more energy before fracturing, making it suitable for use in environments where the material is exposed to harsh conditions or physical impacts.
- Fatigue Resistance: Carbon fiber’s high tensile strength and low flexibility make it less susceptible to fatigue under repeated stress, whereas fiberglass is more prone to wear and tear over time, especially under conditions of constant stress or vibration.
Both fiberglass cloth carbon fiber and carbon fiber have unique strength properties that make them ideal for different applications. Fiberglass offers excellent flexibility and impact resistance, while carbon fiber excels in high-stress, high-performance applications requiring stiffness and tensile strength. Understanding the specific needs of a project will help in selecting the material that provides the best balance of strength and durability for the intended use.
Key Advantages of Fiberglass Reinforced Plastic Sign Solutions
Fiberglass Cloth vs Carbon Fiber: The Role of Materials in Pickleball Paddles
Fiberglass Paddles
Fiberglass cloth vs carbon fiber is an important consideration when choosing materials for pickleball paddles. Fiberglass is one of the most common materials used in the production of recreational pickleball paddles. Known for its strength, flexibility, and affordability, fiberglass provides a balanced combination of performance and cost-effectiveness. Fiberglass pickleball paddles are particularly popular among recreational players and beginners, as they offer a good mix of durability and playability without breaking the bank. The flexibility of fiberglass allows for a forgiving feel, which helps players generate power while maintaining control over the ball. It also has excellent impact resistance, making it durable enough for regular use. In contrast, carbon fiber paddles are typically preferred by advanced players seeking enhanced power, precision, and lighter weight, although they come at a higher cost. The choice between fiberglass cloth and carbon fiber ultimately depends on the player’s needs, with fiberglass being ideal for casual or beginner players and carbon fiber better suited for competitive play.
The inherent flexibility of fiberglass allows it to provide a forgiving feel on the paddle, making it easier for players to generate power while maintaining control over the ball. Additionally, fiberglass paddles are known for their durability, offering a longer lifespan than paddles made from other materials like wood or plastic. This makes them an excellent choice for players who want a reliable, long-lasting paddle without investing in higher-end materials.
The affordability of fiberglass paddles also makes them a great option for casual players or those just starting to play pickleball. They provide an entry-level option with good overall performance, allowing players to enjoy the game without committing to a high-cost investment.
Carbon Fiber Paddles
Carbon fiber is increasingly used in the production of high-performance pickleball paddles due to its exceptional strength-to-weight ratio and its ability to provide enhanced power and precision. Carbon fiber paddles are typically favored by advanced players or those seeking to maximize their performance on the court. The lightweight nature of carbon fiber allows for quicker reactions and faster ball handling, making it easier to control the paddle and make precise shots.
One of the main advantages of carbon fiber in pickleball paddles is its ability to generate greater power with less effort. The stiff, rigid nature of carbon fiber allows players to hit the ball with more force while maintaining control, which is particularly important for competitive play. Carbon fiber paddles also tend to provide a more responsive and solid feel compared to fiberglass paddles, which helps players make sharper, more accurate shots.
In addition to its power and precision, carbon fiber is incredibly lightweight, allowing players to swing the paddle with speed and agility. This is particularly advantageous for players who rely on fast-paced reactions and quick movements on the court.
Advantages of Fiberglass Cloth Carbon Fiber in Pickleball Paddles
- Durability and Longevity: Fiberglass paddles are more durable and resistant to wear and tear than other materials, making them an ideal choice for recreational players who need a long-lasting paddle.
- Cost-Effectiveness: Fiberglass paddles are generally more affordable, making them accessible for casual players or those who are new to the game of pickleball.
- Power and Precision: Carbon fiber paddles provide enhanced power with less effort, giving players the ability to hit stronger shots while maintaining control.
- Lightweight Nature: Carbon fiber’s lightness allows for quicker reaction times, which is crucial for players who need to adjust quickly to fast-moving balls during a game.
- Stiffness and Control: Carbon fiber offers more rigidity and a solid feel during gameplay, providing advanced players with better control over their shots.
- Flexibility and Forgiveness: Fiberglass offers a more flexible, forgiving feel that helps recreational players make more consistent shots and adds to the overall comfort during play.
Both fiberglass cloth carbon fiber and carbon fiber paddles cater to different types of players. Fiberglass paddles are ideal for casual and recreational players seeking a balance of affordability, durability, and versatility. Carbon fiber paddles, on the other hand, are tailored for players who want high performance, power, and precision, and are often used in competitive settings. By understanding the unique properties of these materials, players can choose the right paddle to enhance their game and meet their specific needs on the court.
Fiberglass Cloth vs Carbon Fiber: Materials in Automotive Hoods and Parts
Fiberglass Automotive Hoods
Fiberglass cloth vs carbon fiber: Fiberglass is a widely used material in the automotive industry, particularly for the production of hoods in standard and mass-produced vehicles. It offers an excellent balance of strength, durability, and affordability, making it a popular choice for manufacturers aiming to reduce costs while still maintaining a high level of performance. Fiberglass cloth automotive hoods are known for their excellent impact resistance, which is crucial in protecting the vehicle’s engine and components from damage in the event of a collision or accident. In comparison, carbon fiber offers superior strength-to-weight ratio and stiffness, making it a popular choice in high-end or performance vehicles where weight reduction and structural integrity are paramount. While fiberglass cloth provides a cost-effective, durable option for mass-produced cars, carbon fiber is favored in premium and performance cars due to its enhanced strength and lightweight properties, contributing to improved performance and fuel efficiency. The choice between fiberglass and carbon fiber ultimately depends on the vehicle’s design requirements and the importance placed on cost versus performance.
One of the main advantages of fiberglass in automotive applications is its ability to be molded into complex shapes with ease. This makes fiberglass an ideal material for mass production, as it can be efficiently shaped using molds and produced in large quantities at a relatively low cost. Furthermore, fiberglass is resistant to corrosion, which ensures the longevity of automotive parts exposed to the elements, such as hoods, which are frequently exposed to rain, snow, and road salts.
Fiberglass also offers a good level of thermal insulation, making it useful in regulating engine temperatures. It is a highly versatile material that can be reinforced with other materials, such as resins or coatings, to improve its strength and performance. The lightweight nature of fiberglass contributes to fuel efficiency, though it is not as light as carbon fiber.
Carbon Fiber Automotive Hoods
Carbon fiber is used in high-performance and luxury vehicles where reducing weight and maximizing strength are critical. The use of carbon fiber in automotive hoods is more common in high-end sports cars, race cars, and luxury vehicles, where the performance benefits are particularly pronounced. Carbon fiber automotive hoods are known for their superior strength-to-weight ratio, which provides a significant reduction in vehicle weight compared to fiberglass hoods.
One of the key advantages of carbon fiber in automotive hoods is its ability to significantly reduce the overall weight of the vehicle, contributing to improved acceleration, handling, and fuel efficiency. By reducing the weight of the hood, carbon fiber helps improve the vehicle’s power-to-weight ratio, which is a crucial factor in performance cars. The high stiffness of carbon fiber also allows for more rigid, structurally sound hoods that provide enhanced protection during a collision.
Carbon fiber is also incredibly resistant to corrosion, unlike some metals, which is especially beneficial for vehicles that are exposed to harsh environments. Its lightweight nature allows for better vehicle dynamics, making it a material of choice for racing cars where every gram counts. While the material is more expensive than fiberglass, the performance and aesthetic benefits of carbon fiber make it a preferred choice for manufacturers of high-performance cars.
Material Selection for Automotive Hoods
When it comes to selecting materials for automotive hoods, the choice between fiberglass cloth carbon fiber depends on a variety of factors, including weight, cost, and performance. Both materials offer unique benefits and are suitable for different types of vehicles. Here’s a comparison of the two materials based on these critical factors:
- Weight: Carbon fiber is significantly lighter than fiberglass, offering a considerable weight reduction. This makes carbon fiber an ideal choice for performance cars, where every kilogram of weight saved can improve acceleration, handling, and fuel efficiency. Fiberglass, while heavier, still provides a reduction in weight compared to traditional steel or aluminum hoods, but it doesn’t offer the same level of weight savings as carbon fiber.
- Cost: Fiberglass is much more cost-effective than carbon fiber, making it the go-to material for mass-produced vehicles and everyday cars. Manufacturers can use fiberglass to produce hoods and other parts at a lower cost, which is essential for keeping prices competitive. On the other hand, carbon fiber is more expensive due to its production process and the material’s properties, making it more suited for luxury or performance vehicles where cost is less of a concern.
- Performance: In terms of performance, carbon fiber excels in strength, rigidity, and lightweight properties, which make it ideal for high-performance cars, race cars, and vehicles where performance is the top priority. Carbon fiber’s stiffness also contributes to enhanced aerodynamics and overall vehicle dynamics. Fiberglass, while not as strong or stiff as carbon fiber, offers a good balance of strength, impact resistance, and flexibility, making it suitable for regular passenger vehicles that do not require the extreme performance characteristics provided by carbon fiber.
- Durability and Longevity: Both fiberglass and carbon fiber offer excellent durability and resistance to corrosion. Fiberglass is more prone to cracking under impact, but it can withstand moderate collisions without serious damage. Carbon fiber, though less prone to cracking, can be more susceptible to damage from high impacts, but its superior strength and stiffness make it more resilient in high-performance scenarios.
Fiberglass cloth carbon fiber materials each have their place in automotive design, particularly for hoods and other body parts. Fiberglass is an excellent choice for mass-produced vehicles where cost, impact resistance, and durability are key concerns. It offers a balance of performance and affordability, making it ideal for everyday use. On the other hand, carbon fiber’s high strength-to-weight ratio, lightweight properties, and enhanced performance make it the material of choice for high-end performance cars, sports vehicles, and luxury cars. Understanding the specific needs of the vehicle and the trade-offs between weight, cost, and performance will help manufacturers choose the appropriate material for their automotive designs.
FAQs about Fiberglass Cloth VS Carbon Fiber
Both fiberglass and carbon fiber are strong, durable materials, but their performance characteristics make them suitable for different applications. The choice between the two largely depends on the specific needs of the project.
Fiberglass is an affordable, versatile material known for its flexibility and impact resistance. It is ideal for applications where weight savings are less of a concern and where durability and toughness are prioritized. Fiberglass is also highly resistant to corrosion and can be used in a variety of industries, including automotive, marine, and construction. It provides a good balance of strength and flexibility, making it well-suited for products that may experience regular wear and tear, such as boat hulls or insulation.
Carbon Fiber, on the other hand, is stronger and stiffer than fiberglass. It has a much higher strength-to-weight ratio, making it perfect for applications where weight reduction is critical, such as in aerospace, high-performance vehicles, or sports equipment. Carbon fiber excels in applications that require maximum rigidity, such as structural components. However, it is more expensive and less flexible than fiberglass, making it less ideal for applications that require bending or absorbing impacts.
Yes, fiberglass cloth significantly adds strength to materials in various applications. Fiberglass cloth is made by weaving fine glass fibers into a fabric, which is then impregnated with resin to create a composite material. The resulting material is incredibly strong and durable, making it ideal for reinforcing other materials.
Fiberglass cloth is commonly used in industries such as construction, automotive, and marine applications, where it enhances the structural integrity of products like boat hulls, storage tanks, and automotive parts. The cloth can be layered to create a strong, rigid composite that can withstand high stress and impact. Its primary advantage is its ability to provide added strength without significantly increasing weight, which makes it suitable for a wide range of products that require both strength and lightweight properties.
Additionally, fiberglass cloth is highly resistant to corrosion, making it an excellent choice for long-term durability. It also offers flexibility, meaning it can be shaped to fit various molds or forms without cracking. This combination of strength, flexibility, and resistance to environmental factors is why fiberglass cloth is often chosen to enhance the strength of a wide variety of products.
The choice between carbon fiber and fiberglass pickleball paddles depends largely on the player’s skill level, playing style, and preference for performance characteristics.
Fiberglass pickleball paddles are typically more affordable and are often used by recreational players or those just starting out. Fiberglass paddles offer a good balance of strength and flexibility, making them forgiving and easier to control. The flexibility of fiberglass also helps players generate more power with less effort, which is beneficial for beginners. Additionally, fiberglass paddles are durable and resistant to wear, making them a solid option for casual play.
Carbon fiber pickleball paddles, on the other hand, are designed for high-performance play. Carbon fiber is much stiffer and stronger than fiberglass, which means it provides greater power and precision for advanced players. The increased rigidity of carbon fiber allows for faster reaction times and better control when hitting fast balls, making it ideal for competitive players. While carbon fiber paddles are generally more expensive, they offer a superior strength-to-weight ratio, making them lighter and easier to handle during intense play.
While carbon fiber is an incredibly strong and lightweight material, there are a few materials that might outperform it in specific areas, depending on the application:
Graphene: Graphene is often considered stronger and more conductive than carbon fiber. It is a single layer of carbon atoms arranged in a two-dimensional lattice and is about 200 times stronger than steel. While carbon fiber excels in terms of tensile strength and rigidity, graphene is highly flexible and offers exceptional conductivity, making it ideal for applications in electronics, energy storage, and advanced composites. However, graphene is still in the early stages of development and is not as widely used as carbon fiber in everyday products.
Kevlar: Kevlar is another material that can outperform carbon fiber in certain applications, particularly in terms of impact resistance and toughness. Kevlar is a synthetic fiber known for its resistance to abrasion and high tensile strength. It is often used in bulletproof vests, body armor, and other protective gear. While carbon fiber is stiffer and more rigid, Kevlar is more flexible and better suited for high-impact applications.
Titanium: In some cases, titanium may be a better alternative, especially in applications where strength and corrosion resistance are paramount. Titanium is extremely strong, lightweight, and resistant to corrosion, making it ideal for aerospace, medical, and automotive industries. While carbon fiber has a higher strength-to-weight ratio, titanium is better for applications where toughness, durability, and heat resistance are more important.
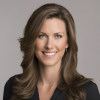
As the editor of GangLong Fiberglass, I have years of experience and in-depth research, focusing on cable tray products, fiberglass solutions, and grille systems. I incorporate years of industry insights and practical experience into every content, committed to promoting the progress of the industry. At GangLong Fiberglass, my commitment is reflected in every product, from innovative cable trays to durable fiberglass solutions and sturdy grille systems. As an authoritative voice in the industry, my goal is to provide valuable information to professionals and businesses and promote forward-looking solutions.