- Home
- Fiberglass Fabric Cloth
High Quality Fiberglass Fabric Cloth Supplier
Fiberglass Fabric Cloth is a widely used reinforcement material in composite construction and repair. Known for its strength, affordability, and versatility, this woven fabric is essential for building molds, creating composite parts, and making repairs.Fiberglass Fabrics Cloth comes in different weights and characteristics, each suited to specific applications. It offers excellent strength and low weight when combined with resin, making it a popular choice in various industries, including marine, automotive, construction, and aerospace.
As a commonly used reinforcement, Fiberglass Fabric Cloth continues to be favored for its ease of handling and ability to deliver durable, high-quality composite parts. Fiberglass fabric cloth, made of woven glass fibers, is lightweight, strong, durable, non-flammable, and ideal for bonding, reinforcement, repair, and composite parts.
Simplifying Your Life: Key Functionalities
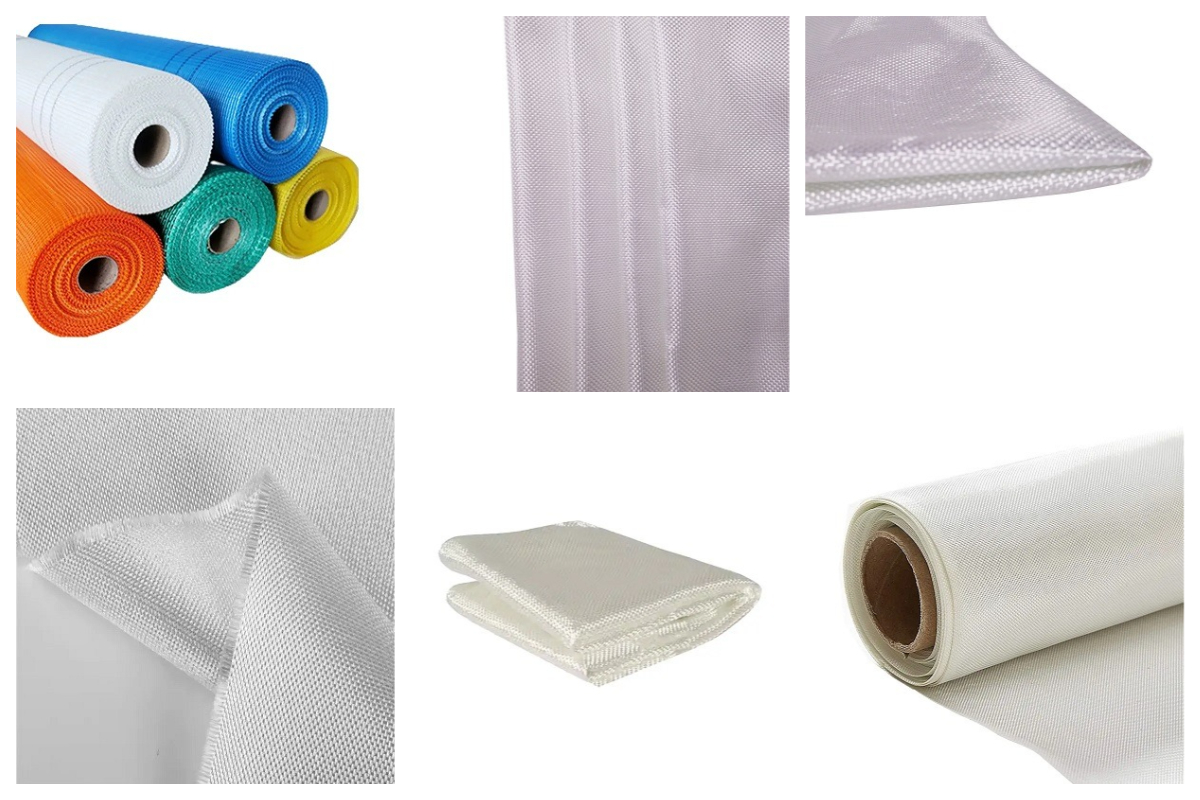
Attributes | Details |
---|---|
Place of Origin | Hebei, China |
Brand Name | GangLong Fiberglass |
Width | Customizable |
Thickness | Customizable |
Length | Customizable |
Weave Type | Plain Weave, |
Processing Services | Cutting, Punching, Welding, Bending |
Material | 100% Fiberglass |
Temperature Resistance | High Temperature Resistance |
Advantages | Insulation, Heat Resistance, Corrosion Resistance, High Mechanical Strength |
Features | High Temperature Resistance |
Color | Gray, Red, Black, White, Orange Red, Green, Blue, Yellow or Customized |
Keywords | Fiberglass Cloth |
Certificate | EN1869:1997 |
Application | Wall / Roof Covering Cloth / Fiberglass Mesh Cloth / Removable Insulation Cover / Fire and Smoke Curtain / Fire Blanket |
News
- Exploring the Benefits of Carbon Fiber Apparel
- How to Work with Carbon Fiber Successfully
- Carbon Fiber Suit: The Future of Lightweight Armor
- Is Carbon Fiber Armor the Future of Protection?
- Why White Carbon Fiber is Popular in Automotive Design
- Transparent Carbon Fiber Sheets: Strength Meets Clarity in Design
- Chopped Carbon Fiber Mat for Lightweight Reinforcement
- Carbon Fiber EG Hatch: Upgrade Your Civic Today
- The Benefits of Using Structural Carbon Fibre in Engineering
- How Many Layers of Layered Carbon Fiber Are Needed?
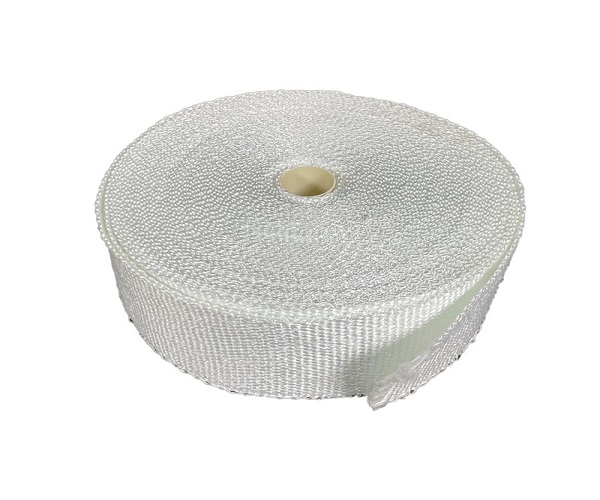
Leading Fiberglass Fabric Cloth Supplier
When looking for high-quality fiberglass fabric cloth, one prominent manufacturer to consider is GangLong Fiberglass. With a long-standing reputation in the industry, GangLong Fiberglass is renowned for its advanced materials and fiberglass products.
High-Quality Fiberglass Fabric for Superior Performance
Ganglong Fiberglass is a leading manufacturer and supplier of premium fiberglass fabric, delivering durable and high-performance materials for a wide range of applications. Our fiberglass cloth is designed for optimal wet-out with epoxy or polyester resin, ensuring strong adhesion, high peel strength, and excellent durability.
All our fiberglass fabric is manufactured in China to the highest quality standards, ensuring exceptional performance and reliability.
Ganglong Fiberglass – A Trusted Industry Leader
Founded in 2014, Ganglong Fiberglass has rapidly grown into a leading global manufacturer and supplier of fiberglass products. Headquartered in Hebei, China, we have expanded our reach with 30 strategic service centers across the United States, United Kingdom, Germany, and France. Our extensive logistics network ensures fast, efficient, and high-quality service for our diverse global clientele.
At Ganglong Fiberglass, we prioritize:
- Uncompromising Quality – Our ISO-certified manufacturing process guarantees that every product meets or exceeds international standards. From raw material selection to final inspection, our rigorous quality control procedures ensure consistency and reliability.
- Innovation & Development – We continuously invest in research and development, utilizing cutting-edge technologies to create advanced, high-performance fiberglass products that cater to evolving industry needs.
- Sustainability & Eco-Friendly Solutions – Our commitment to sustainability drives us to use environmentally friendly materials and energy-efficient manufacturing processes, minimizing our impact on the planet. Our products are designed for long service life and recyclability, making them a responsible choice for eco-conscious customers.
Why Choose Ganglong Fiberglass?
- Premium fiberglass fabric with excellent resin absorption
- Strong, impact-resistant, and durable materials
- Industry-leading quality control and ISO-certified manufacturing
- A global presence with fast and efficient logistics
- Commitment to innovation and sustainability
By choosing Ganglong Fiberglass, you are investing in high-quality fiberglass fabrics that provide long-lasting performance while supporting a more sustainable future.
For bulk orders or custom-cut fiberglass solutions, contact us today to find the best fiberglass fabric for your needs!
GangLong Fiberglass has been a leader in the production of fiberglass for 10 years, and our commitment to innovation and quality is evident in their diverse range of products. We offer a variety of fiberglass fabrics, including woven roving, chopped strands, and specialty fabrics designed for various applications. Whether you need fiberglass cloth for automotive, marine, or construction purposes, GangLong Fiberglass provides reliable solutions that meet rigorous industry standards.
One of the key advantages of choosing GangLong Fiberglass is our comprehensive support and technical expertise. Our website features detailed product specifications, application guides, and even technical support to help you select the right fiberglass fabric for your needs. This ensures that you get not only a high-quality product but also the assistance you might need for successful application.
In addition to their product quality, GangLong Fiberglass is committed to sustainability and environmental responsibility. We focus on reducing their environmental footprint while maintaining high standards of manufacturing. This dedication to both quality and sustainability makes GangLong Fiberglass a reliable choice for anyone in need of fiberglass fabric cloth.
What is Fiberglass Fabric Cloth
Fiberglass fabric cloth, commonly referred to as fiberglass cloth, is a versatile and widely used reinforcement material in composite construction and repair. It is made of woven glass filaments of varying sizes, giving it exceptional tensile strength, dimensional stability, and resistance to high heat and fire. This material serves as the backbone of many structural applications in industries like marine, automotive, and construction. Its affordability and ease of handling make it one of the most commonly used reinforcement materials in the composite industry.
When used in conjunction with resin, such as polyester or epoxy, fiberglass cloth transforms into a rigid, strong, and durable composite. Resin saturates the woven fibers, binding them together and curing into a hardened structure that is resistant to water, UV damage, and environmental stresses. Lightweight fiberglass cloth is ideal for creating a smooth, clear surface and serves as an effective waterproofing layer when applied over wood or other surfaces. Heavier fiberglass cloth, on the other hand, offers increased strength, stiffness, and laminate thickness, making it suitable for structural reinforcements.
Fiberglass fabric cloth is commonly used in mold making, fiberglass repair, and wood reinforcement projects. In marine construction, it is prized for its ability to create waterproof laminates that resist UV rays and high temperatures, ensuring longevity in harsh environments. For insulation purposes, fiberglass cloth can withstand temperatures up to 1000°F, making it ideal for protecting equipment and pipes. Variants like thermal insulation cloth, rewettable cloth, and impregnated cloth cater to specific needs. Thermal insulation cloth is often used for repairing and covering pipe insulation, while rewettable cloth, coated with a special binder, can be molded into any shape and dried into a durable form. Impregnated fiberglass cloth is pre-treated with a solution for enhanced strength and flexibility.
Fiberglass cloth is available in a variety of weights, widths, and lengths to meet the unique demands of each project. Its durability, fire resistance, and ability to create strong yet lightweight composites make it indispensable in a wide range of applications, from boat building to industrial insulation. Overall, fiberglass fabric cloth combines affordability, versatility, and performance, maintaining its position as a key material in both commercial and industrial settings.
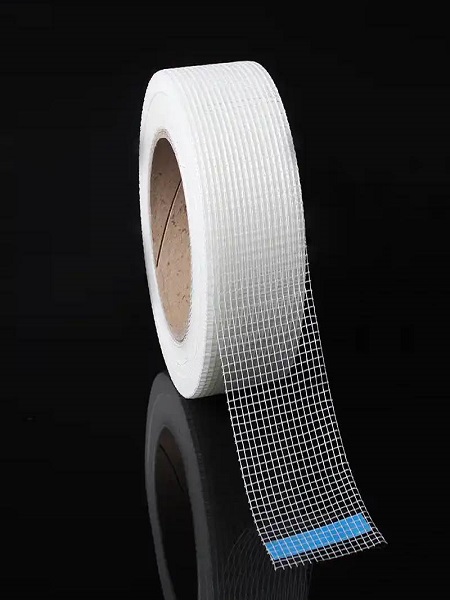
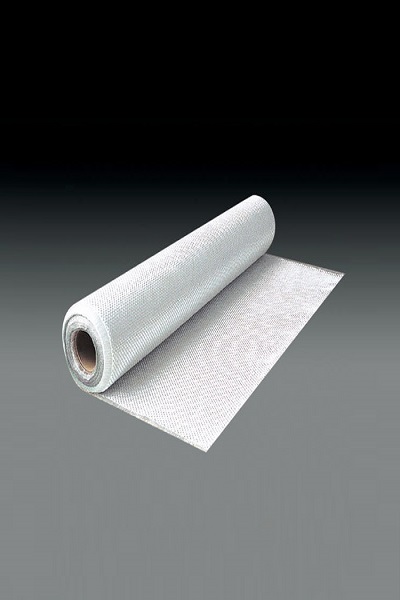
Common Sizes of Fiberglass Fabric Cloth: Advantages and Application Scenarios
Fiberglass fabric cloth comes in various sizes and weights to suit a wide range of applications. These sizes are typically categorized by width and weight
Woven Fiberglass Tape (0.5–12 inches wide)
This narrow format is ideal for targeted reinforcement, edge sealing, and repair work. The smaller widths (0.5–2 inches) are commonly used in joining seams or strengthening corners, while wider tapes (up to 12 inches) are suitable for localized reinforcement in larger structures like pipes or joints.
Standard Fiberglass Cloth (27–60 inches wide)
This cloth provides broad coverage for larger projects. Widths of 27–38 inches are commonly used in applications like small-scale composite repairs and creating molds. Wider formats, such as 50–60 inches, are ideal for large-scale applications like boat hulls, vehicle components, or industrial laminates.
Lightweight Fiberglass Cloth (0.5 ounces per square yard)
This ultra-lightweight fabric is perfect for projects requiring a smooth, clear finish, such as surfboards, kayaks, or lightweight protective layers. It’s especially useful for creating a waterproof barrier without adding significant weight.
Mid-Weight Fiberglass Cloth (4–6 ounces per square yard)
These are the most popular and versatile options, with applications ranging from boat building to repairing composite parts. Mid-weight cloth offers a balance of strength, flexibility, and ease of handling, making it suitable for laminates requiring moderate thickness and durability.
Heavy Fiberglass Cloth (Tool-Grade)
Heavier fabrics are used in structural applications where maximum strength and rigidity are required. These are common in industrial reinforcements, load-bearing structures, and tooling applications where thickness and impact resistance are essential.
Applications Based on Size
- Small Repairs: Woven tape (narrow widths) and lightweight cloth for precise reinforcement and smooth finishes.
- Marine Applications: Mid-weight and wide fiberglass cloth for boat hulls, decks, and waterproof laminates.
- Structural Reinforcement: Heavy cloth for tools, industrial molds, and load-bearing components.
- Decorative or Lightweight Projects: Ultra-lightweight cloth for clear-coated finishes on wood or composites.
By offering a variety of widths and weights, fiberglass fabric cloth caters to an extensive array of needs, from small-scale repairs to heavy-duty industrial applications.
Fiberglass Cloth and Resin Compatibility
Why Fiberglass Fabric Cloth Requires Resin for Effective Use
Fiberglass fabric cloth must be used with resin to create a durable, rigid, and waterproof composite structure. On its own, fiberglass cloth is a flexible material with high tensile strength, but it lacks rigidity and cannot maintain a solid shape. Resin, such as epoxy, polyester, or vinyl ester, saturates the cloth, binding the fibers together and curing into a hardened structure. This combination leverages the strength of the fiberglass and the rigidity of the resin to produce a composite material that is strong, lightweight, and resistant to environmental factors.
Resin also fills the gaps between the fibers, creating a smooth, impermeable surface that is resistant to water, chemicals, and UV damage. Without resin, fiberglass cloth would absorb moisture and degrade over time, compromising its structural integrity. The synergy between fiberglass cloth and resin is what makes this combination essential for applications like boat building, automotive parts, and repairs.
When working with Fiberglass Fabric Cloth, selecting the right resin is crucial for achieving the desired strength, durability, and finish of your project. The most commonly used resins with Fiberglass Fabric Cloth are polyester, epoxy, and vinyl ester, each offering distinct properties that make them suitable for different applications. Polyester Resin: This is the most widely used resin in fiberglass applications due to its affordability and ease of use. Polyester resin is ideal for projects that do not require extreme strength or environmental resistance, such as automotive bodywork, general repairs, and non-critical structural components. However, it tends to be less flexible and can be prone to cracking under stress. Epoxy Resin: Known for its superior strength and durability, epoxy resin is often the go-to choice for high-performance applications. It provides excellent adhesion to Fiberglass Fabric Cloth and is highly resistant to water, chemicals, and environmental degradation. Epoxy resin is ideal for use in marine environments, aerospace components, and any project where long-term durability is essential. Although more expensive than polyester, the added strength and longevity often justify the cost. Vinyl Ester Resin: Offering a middle ground between polyester and epoxy, vinyl ester resin combines the affordability of polyester with the enhanced chemical and environmental resistance of epoxy. It is particularly well-suited for applications where exposure to harsh environments, such as chemical tanks or marine structures, is a concern. Vinyl ester is also more flexible than polyester, reducing the risk of cracking in high-stress areas. Working with Fiberglass Fabric Cloth and resin requires attention to detail to achieve the best results. Here are some practical tips to help you navigate the process: Mixing Ratios: Always follow the manufacturer’s recommended mixing ratios for resin and hardener. Accurate measurements are essential for ensuring proper curing and achieving the desired strength. Using too much or too little hardener can result in incomplete curing, leaving the composite weak or tacky. Application Methods: When applying resin to Fiberglass Fabric Cloth, use a roller or brush to ensure even saturation. Start by applying a thin layer of resin to the surface before laying down the fiberglass cloth, then carefully work the resin into the cloth, ensuring that it is fully saturated without air bubbles. For larger projects, consider using a squeegee to distribute the resin evenly and remove excess material. Curing Times: The curing time for resin varies depending on the type used and the ambient conditions. It’s essential to allow adequate time for the resin to fully cure before handling or applying additional layers. Rushing the process can lead to weak bonds and compromised structural integrity. Be mindful of temperature and humidity, as these factors can affect curing times. Common Mistakes to Avoid: One of the most common mistakes when working with Fiberglass Fabric Cloth and resin is applying too much resin, which can lead to a heavy, brittle composite with excess resin pooling. Another mistake is not adequately wetting out the fiberglass, resulting in dry spots that weaken the final product. Ensure that all layers of fiberglass are thoroughly saturated with resin, but avoid over-applying.Choosing the Right Resin
Application Tips
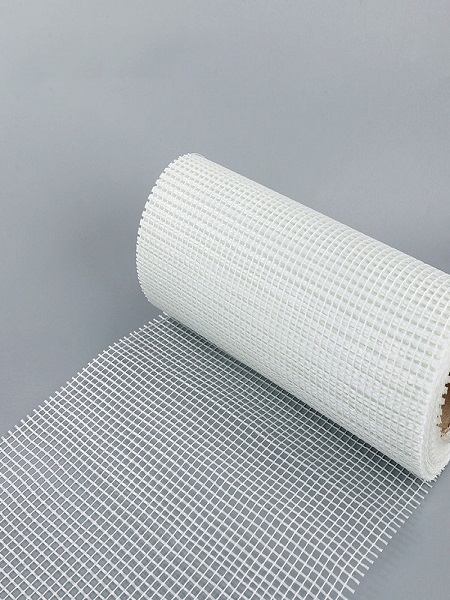
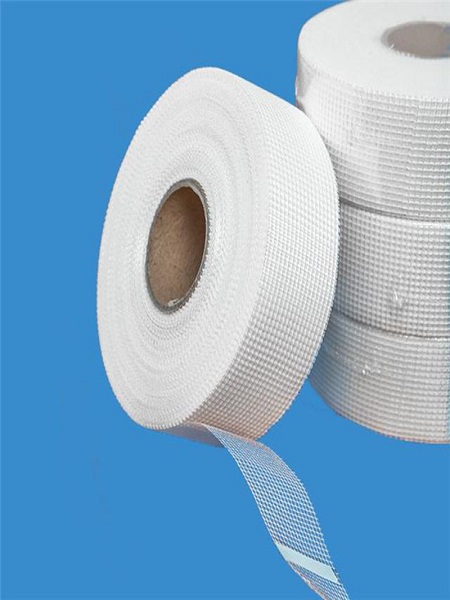
Essential Accessories for Fiberglass Fabric Cloth: Uses and Effects
When working with fiberglass fabric cloth, specific accessories are essential for achieving optimal results. These tools are designed to simplify the application process, enhance the quality of the final composite, and ensure efficiency.
Fiberglass Roller
Fiberglass rollers are used to remove air bubbles trapped between the fiberglass cloth and resin during application. Bubbles can weaken the laminate and compromise its waterproofing. Using a fiberglass roller ensures even resin distribution, eliminates voids, and enhances the strength and durability of the composite.
Fiberglass Shears
These specialized shears are designed for cutting fiberglass cloth precisely and cleanly. They prevent fraying and ensure that the fabric edges are neat, which is crucial for accurate fitting and layering in composite construction or repair projects.
Brushes and Smear Rollers
Brushes are used to apply resin evenly across the fiberglass cloth, ensuring proper saturation. Smear rollers help spread the resin smoothly, preventing excess buildup and improving the overall finish of the laminate. Together, they ensure that the resin fully penetrates the fabric, creating a strong bond between the layers.
Effects of Using Accessories Together
When these accessories are used in combination, they ensure a streamlined and efficient fiberglassing process. Precise cutting with shears ensures perfect fitting, while resin application with brushes and smear rollers achieves thorough saturation. The fiberglass roller then removes air bubbles, resulting in a strong, smooth, and defect-free laminate. This synergy enhances the strength, durability, and appearance of the final composite structure, making these tools indispensable in fiberglass work.
Weaving Types of Fiberglass Fabric Cloth and How to Choose the Right One
Fiberglass fabric cloth is available in different weave types, each offering unique characteristics suited to various applications. The weaving pattern affects the fabric’s strength, flexibility, cost, and ease of handling, making it crucial to select the right one based on project requirements.
Plain Weave
The plain weave is the simplest and most affordable option. It features a consistent over-and-under pattern, which makes it hold together well when cut. However, it is the least flexible of the weave types, limiting its use in projects with complex curves or shapes. It is best suited for flat or slightly curved surfaces where cost efficiency and stability are priorities.
Twill Weave
Twill weave offers a balance between flexibility, strength, and cost. The weave pattern alternates in a staggered manner, making it more flexible than plain weave while still maintaining moderate strength. Twill weave is often chosen for projects that require both functionality and aesthetics, as it provides a smoother, more attractive finish. It is ideal for applications like boat decks or composite panels with gentle contours.
Satin Weave
The satin weave is the most flexible of the three, featuring a pattern where one weft yarn floats over 3–7 warp yarns before interlacing. This design results in a flatter, smoother fabric that conforms well to complex shapes and curves. Satin weave fiberglass cloth is moderately strong and is preferred for high-end applications requiring superior drapability and finish, such as in aerospace components or intricate marine structures.
Choosing the Right Weave
Use plain weave for straightforward, budget-friendly projects on flat or slightly curved surfaces.
Opt for twill weave when a balance of flexibility, strength, and appearance is desired for moderately contoured designs.
Choose satin weave for highly complex shapes and premium finishes where maximum flexibility and aesthetics are crucial.
By combining these weaving types with the appropriate resin, fiberglass fabric cloth forms a durable composite material, widely used in marine, aerospace, and structural applications. Understanding the properties of each weave ensures the creation of robust and tailored composite parts for any project.
Thank you for your interest in our products. To receive our pricelist or for any inquiries, please fill out the form below. We will get back to you within 24 hours.
Applications of Fiberglass Fabric Cloth
Fiberglass fabric cloth, also known as fiberglass fabric, is a highly versatile reinforcement material used across numerous industries due to its exceptional strength, lightweight nature, and durability. Its unique properties make it suitable for a wide range of applications, from industrial manufacturing to recreational equipment.
Reinforcement in Composites
Fiberglass fabrics are integral to the composite manufacturing process. Combined with resins like epoxy, polyester, or vinyl ester, they create strong, lightweight composite structures with excellent tensile strength, stiffness, and impact resistance.
Marine Industry
Widely used in shipbuilding, fiberglass cloth is applied with resin to construct durable and watertight hulls. Layered in multiple directions, it enhances structural integrity and stiffness in boats and marine vessels.
Automotive Industry
Fiberglass fabrics are essential in automotive manufacturing, where they are used to produce lightweight body panels, interior components, spoilers, and other structural parts. Their high strength-to-weight ratio, corrosion resistance, and design flexibility make them a preferred material.
Aerospace Industry
In aerospace applications, fiberglass fabrics are used to manufacture aircraft components like fuselages, wings, fairings, and interior panels. They are valued for their strength, durability, and resistance to extreme temperatures.
Building and Construction
In construction, fiberglass fabrics reinforce concrete structures, increasing their strength and durability. Applications include composite bridges, building facades, and roofing systems. Fiberglass prevents cracking and extends the lifespan of concrete.
Electrical Insulation
Fiberglass fabrics with specialized electrical insulation properties are used in circuit boards, motor components, and insulation bushings. Their thermal and electrical resistance make them ideal for electronic and electrical applications.
Thermal Insulation
Fiberglass fabrics serve as thermal insulation materials in high-temperature applications, such as insulation blankets, oven mitts, fireproof clothing, and curtains.
Industrial Applications
Industries use fiberglass fabrics for filtration systems, conveyor belts, pipe and tank insulation, industrial gaskets, and seals. Their strength and resistance to harsh environments make them ideal for these uses.
Sports and Recreation
In sports and recreational equipment, fiberglass cloth is used to manufacture items like surfboards, paddleboards, kayaks, and snowboards. Its lightweight and durable properties enhance performance and longevity.
Fiberglass fabric cloth’s versatility and unique characteristics make it indispensable in industries requiring materials with high strength, durability, and light weight, supporting applications from everyday products to high-performance industrial and aerospace components.
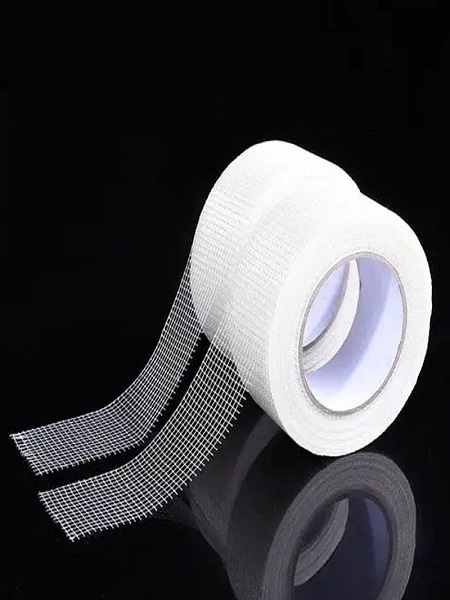
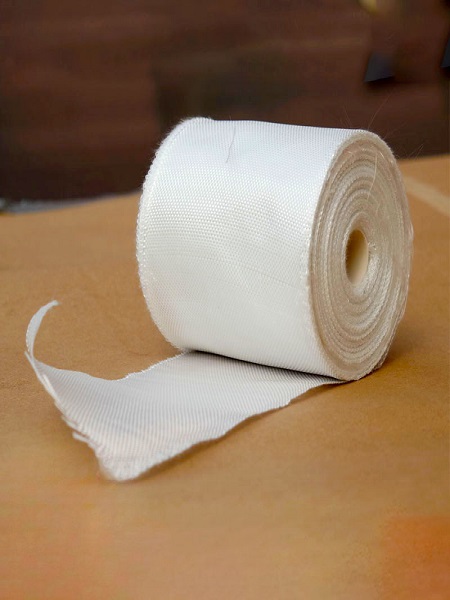
How to Choose the Right Fiberglass Fabric Cloth
Selecting the appropriate fiberglass fabric cloth depends on your specific application and the desired balance of strength, appearance, and cost. The three main types—standard fiberglass cloth, woven roving, and fiberglass mat—each offer unique characteristics that suit different projects.
Fiberglass Cloth
Standard fiberglass cloth is woven in a right-angle weave pattern and is available in various thicknesses. Lightweight cloth is ideal for general repairs, surface protection, and applications requiring a smooth finish. Heavier cloth is better suited for adding bulk and strength in multi-layer laminates. This type is versatile and works well for visible areas due to its smooth texture and neat finish.
Woven Roving
Woven roving is a coarse-textured, reinforced fiberglass fabric that is stronger and more affordable than standard cloth. It is commonly used in boat building, especially between layers of fiberglass mat in lamination projects, to enhance structural strength. However, woven roving is not ideal for high-visibility areas because its coarse weave can cause “print-through,” requiring excessive resin to hide. It is best paired with chopped strand mats for large-scale structural builds.
Fiberglass Mat
Fiberglass mat, also known as chopped strand mat (CSM), consists of fine, randomly arranged glass fibers held together by a binder. It is an economical choice often used to add thickness to laminates in boat building and other structural projects. However, since fiberglass mat lacks inherent strength, it should always be combined with other materials like woven roving or standard cloth for reinforcement.
Choosing the Right Material for Your Project
Use standard fiberglass cloth for projects requiring a smooth finish, such as visible surfaces or lightweight, general-purpose applications.
Opt for woven roving for structural reinforcement in larger builds, such as boat hulls, where strength and cost-efficiency are critical.
Choose fiberglass mat when adding bulk or thickness to laminates, especially in conjunction with other fiberglass materials for strength.
By understanding the properties of these fiberglass materials and their appropriate applications, you can select the best option to ensure a successful and durable outcome for your project.
Fiberglass Fabric Cloth Price
Price Factors
The price of Fiberglass Fabric Cloth can vary widely depending on several key factors, each of which plays a significant role in determining the final cost. One of the primary factors is the quality of the material itself. Higher-quality Fiberglass Fabric Cloth often comes with a higher price tag due to the superior raw materials used in its production, as well as the precision and care taken during the manufacturing process. This higher quality translates into better performance, durability, and longevity, making it a worthwhile investment for projects that demand the best.
Another factor that influences the price is the weave pattern of the fabric. Different weave patterns, such as plain weave, twill, or satin, offer varying levels of strength, flexibility, and ease of use. More complex weaves, which provide enhanced performance characteristics, are typically more expensive due to the additional manufacturing complexity involved. The weight of the fabric, measured in ounces per square yard, also affects the price. Heavier fabrics, which offer greater strength and rigidity, generally cost more than lighter ones.
The supplier from whom you purchase the Fiberglass Fabric Cloth can also impact the price. Established suppliers with a reputation for quality and customer service may charge more, but they often provide added value in the form of product guarantees, technical support, and reliable shipping. Conversely, purchasing from less reputable sources might offer initial cost savings but could lead to quality issues or delays, ultimately costing more in the long run. Balancing cost with quality is essential when selecting Fiberglass Fabric Cloth. While it might be tempting to opt for the lowest-priced option, considering the material’s performance and durability can help ensure you get the best value for your investment. Investing in high-quality fabric might have a higher upfront cost, but it can save you money over time by reducing the need for repairs or replacements. When comparing prices for Fiberglass Fabric Cloth from different suppliers and retailers, it’s important to look beyond the initial price tag. Start by checking the specifications of the fabric, ensuring that you’re comparing similar products in terms of quality, weave pattern, and weight. Once you’ve identified equivalent products, compare the base prices across different suppliers. In addition to the base price, consider any additional costs that might affect the total price you pay. Shipping costs can vary significantly depending on the supplier’s location and the size of your order. Some suppliers may offer free shipping for large orders, while others might charge a premium, especially for expedited delivery. Taxes and potential import duties (if buying internationally) should also be factored into your calculations. Another aspect to consider is the supplier’s return policy and warranty. A slightly higher price might be justified if the supplier offers a comprehensive return policy or a product warranty that ensures you’re covered if the material doesn’t meet your expectations or if there are any defects. To find the best deals, it’s helpful to shop around and request quotes from multiple suppliers, especially if you’re purchasing in bulk. Some suppliers might be willing to offer discounts for large orders or for repeat customers. Additionally, keep an eye out for seasonal sales, promotions, or bulk-buying discounts that can reduce the overall cost.Price Comparison
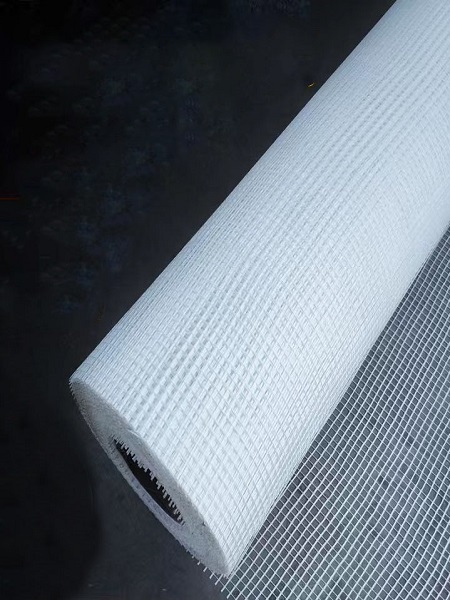
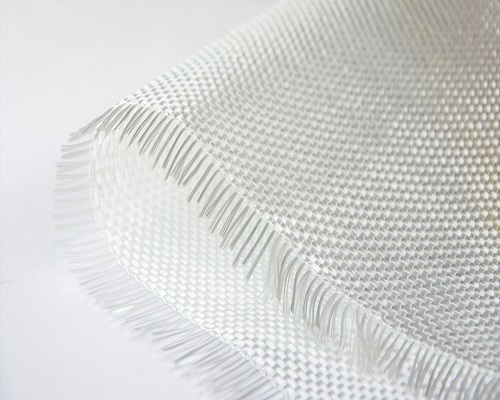
Why Are Fiberglass Fabric Cloths Sold in Different Weights?
Fiberglass fabric cloths are sold in various weights, ranging from 2 ounces to 40 ounces per square yard, to accommodate the diverse requirements of different applications. The weight of the cloth directly influences its thickness, strength, flexibility, and ease of use, making it a crucial factor in material selection.
Lightweight Fiberglass Cloth (2–6 ounces)
Lightweight cloths, such as 4-ounce fiberglass, are versatile and commonly used for projects like canoe and kayak construction. They conform well to curved surfaces and are easy to wet out with resin, making them suitable for applications requiring a smooth finish or for covering intricate shapes.
Medium-Weight Fiberglass Cloth (6–10 ounces)
Medium-weight cloths are ideal for larger areas or projects needing greater durability and strength, such as boat repairs. Cloths in this range strike a balance between thickness and ease of handling, offering sufficient toughness to withstand daily wear and tear.
Heavyweight Fiberglass Cloth (Above 10 ounces)
Cloths over 10 ounces are thicker and stronger but are more challenging to wet out and less suitable for contours or corners. For such applications, it is often better to use multiple layers of lightweight cloth to achieve the required thickness while maintaining ease of application.
Benefits of Weight Variations
Offering fiberglass fabric cloths in different weights allows users to tailor their material choices to specific project needs. Lighter cloths provide flexibility and smooth finishes for small or detailed work, while heavier cloths deliver strength and durability for large, flat surfaces. By layering lightweight cloths, users can achieve a thick laminate without compromising on conformability, making weight variations a practical and essential feature of fiberglass fabric products.
Difference Between Fiberglass Fabric Cloth and Fiberglass Mat
Fiberglass fabric cloth and fiberglass mat are both reinforcement materials used in composite applications, but they differ significantly in structure, strength, and application.
Fiberglass Fabric Cloth
Fiberglass cloth consists of glass fibers woven into a right-angle weave pattern. It is available in various weave styles and thicknesses, each designed for specific uses. Fiberglass cloth offers high tensile strength, stiffness, and durability, making it suitable for structural applications. Its woven structure ensures consistency and stability, making it ideal for projects requiring smooth finishes, precision, and strength, such as boat building, automotive parts, and aerospace components.
Fiberglass Mat
Fiberglass mat, also called chopped strand mat (CSM), is made of randomly oriented glass fibers, typically 1–2 inches long, held together by a resin-infused binder. Unlike fiberglass cloth, mats have a sheet-like structure with no specific weave. They are primarily used to add thickness to laminates and provide bulk to composite layers. However, fiberglass mats lack the tensile strength of cured cloth and are not suitable for load-bearing or structural applications.
Key Differences
- Structure: Cloth is woven with aligned fibers, while mats are made of random fibers held by a binder.
- Strength: Fiberglass cloth is stronger and better for structural applications, whereas mats are weaker and used mainly for bulk and thickness.
- Application: Cloth is ideal for precise and durable work; mats are used as fillers or to create non-structural laminates.
Understanding these differences allows users to select the appropriate material for their specific project needs, ensuring the desired balance of strength, durability, and cost-effectiveness.
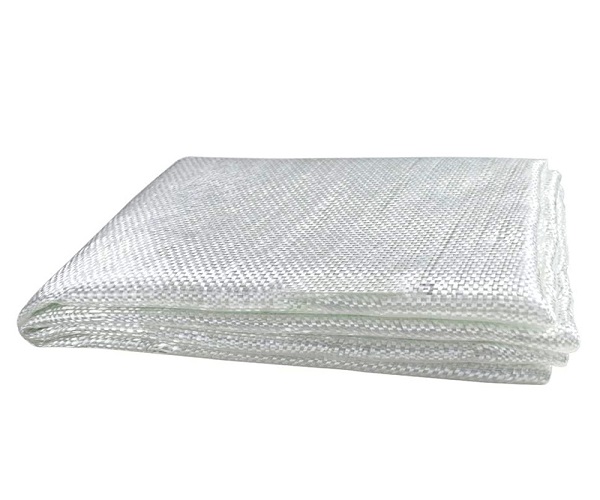
FAQs about Fiberglass Fabric Cloth
What’s the Difference Between Fiberglass Mat and Fiberglass Cloth?
On the other hand, fiberglass mat consists of randomly oriented short fibers that are pressed together and held in place by a binder. The random orientation of the fibers in the mat provides good bulk and thickness, making it excellent for applications where filling and building up layers is essential, such as in molding and repairs. However, fiberglass mat is not as strong as fiberglass cloth and is more prone to absorbing resin, which can make the final composite heavier. Additionally, fiberglass mat generally results in a rougher surface finish compared to the smooth, even finish provided by fiberglass cloth. Choosing between the two depends on the specific requirements of your project—whether you need the strength and smooth finish of fiberglass cloth or the thickness and build-up capabilities of fiberglass mat.
What Can I Use Instead of Fiberglass Cloth?
Another alternative is Kevlar, known for its high impact resistance and toughness. Kevlar is often used in applications where abrasion resistance and durability are key, such as in bulletproof vests, protective gear, and high-impact components. It’s also commonly combined with other materials like carbon fiber to provide a balance of strength, flexibility, and impact resistance.
For more environmentally friendly options, natural fibers such as hemp, flax, and bamboo are gaining popularity. These materials are used in bio-composites, offering a sustainable alternative to synthetic fibers. While not as strong as fiberglass or carbon fiber, natural fibers can be suitable for less demanding applications, particularly where sustainability is a priority. Lastly, certain types of fabrics, such as polyester or nylon, can be used in less demanding applications, particularly when lightweight reinforcement is needed without the high strength requirements.
Can Fiberglass Be Made into Fabric?
Fiberglass fabric is widely used in the production of composite materials, where it is combined with resin to create strong, durable structures. The fabric serves as the reinforcement that gives the composite its strength and rigidity, while the resin binds the fibers together and provides a protective outer layer. The resulting composite material is used in numerous industries, including marine, automotive, aerospace, and construction, for applications ranging from boat hulls and car panels to aircraft components and building reinforcements.
Fiberglass fabric is valued for its resistance to heat, corrosion, and chemical damage, making it suitable for use in environments where these factors are a concern. It’s also used in insulation products, fireproofing materials, and in the creation of molds for various industrial and artistic applications. The versatility and high-performance characteristics of fiberglass fabric make it an essential material in many fields.
What is fiberglass fabric used for?
What is the strongest fiberglass cloth?
How many layers of fiberglass cloth should I use?
What can I use instead of microfiber cloth?
What is poor man's fiberglass?
Do I need to sand between layers of fiberglass?
Is fiberglass cloth waterproof?
What is fiberglass cloth used for?
Composite Reinforcement: Used as a reinforcement material in composite structures, such as boat hulls, automotive parts, and aerospace components. It provides added strength and rigidity to the composite material.
Mold Making: Applied in the production of molds for casting or forming other materials. Fiberglass cloth creates strong, durable molds that can withstand repeated use.
Repair Work: Utilized for repairing damaged fiberglass structures, such as surfboards, canoes, and car body panels. The cloth reinforces the repair area, restoring structural integrity.
Insulation: Employed in thermal insulation applications, particularly in environments where high temperatures are present. Fiberglass cloth helps to prevent heat transfer and provides fire resistance.
Protective Coatings: Used in coatings for tanks, pipes, and other industrial equipment to protect against corrosion and chemical exposure.
When to use fiberglass cloth?
High Strength and Rigidity Are Required: When you need to reinforce a structure and add tensile strength, such as in boat building or automotive repairs.
Smooth Surface Finish Is Important: Fiberglass cloth provides a smoother finish compared to chopped strand mat, making it ideal for applications where appearance matters, like surfboards or car body panels.
Durability and Long-Term Performance Are Needed: In environments exposed to harsh conditions, such as marine or industrial settings, fiberglass cloth adds durability and extends the life of the structure.
Precision and Detailed Work Are Needed: For detailed or precision work, such as in aerospace or complex mold making, fiberglass cloth provides consistent performance and ease of handling.
Does fiberglass cloth go bad?
Moisture Exposure: Prolonged exposure to moisture can weaken the fibers and lead to mold growth, which can compromise the integrity of the cloth.
UV Light: Extended exposure to direct sunlight can cause the fibers to break down over time, reducing their strength.
Contamination: Dirt, dust, and chemicals can contaminate the cloth, affecting its bonding properties with resin.
To maintain its quality, fiberglass cloth should be stored in a cool, dry place, away from direct sunlight and chemicals. When stored properly, fiberglass cloth can last for many years.
How strong is fiberglass fabric?
Tensile Strength: Fiberglass fabric typically has a tensile strength ranging from 25,000 to 75,000 psi (pounds per square inch), depending on the specific type of cloth.
Strength-to-Weight Ratio: Fiberglass fabric has an excellent strength-to-weight ratio, making it a preferred material in applications where weight savings are important, such as in aerospace and marine industries.
Directional Strength: Because fiberglass fabric is woven, it provides directional strength along the weave's orientation, making it particularly strong in the directions of the fibers.
Overall, fiberglass fabric provides a combination of high strength, lightweight, and resistance to environmental factors, making it ideal for structural reinforcement and demanding applications.
Can fiberglass cloth stop a bullet?
What is the strongest bullet proof fabric?
What material is 100% bulletproof?
What is the thinnest material that can stop a bullet?
Is fiberglass cloth safe to touch?
Is fiberglass stronger than Kevlar?
How thick does fiberglass need to be to stop a bullet?
What material can stop a 9mm bullet?
Kevlar: Often used in bulletproof vests.
UHMWPE (Ultra-High-Molecular-Weight Polyethylene): Used in lightweight body armor.
Ballistic Steel: Heavy but effective in stopping 9mm bullets.
Ceramic Plates: Used in body armor to stop higher-velocity rounds.
These materials are specifically designed for ballistic protection and are tested to meet specific standards for stopping 9mm rounds.
What can stop an AK-47 bullet?
Level III or IV Body Armor Plates: Typically made from ceramic, steel, or polyethylene, these plates are designed to stop high-velocity rifle rounds, including those from an AK-47.
Ballistic Glass: Thick, multi-layered glass used in armored vehicles can stop bullets from an AK-47.
Concrete Walls: Depending on thickness, concrete can stop rifle bullets, including those from an AK-47.
What are the three types of fiberglass cloth?
Plain Weave: Features a simple over-under weave pattern, providing a good balance of strength and flexibility.
Twill Weave: Has a diagonal pattern, making it more pliable and easier to conform to complex shapes. It offers higher strength and better drapeability than plain weave.
Satin Weave: Also known as harness weave, it has a smoother surface and is easier to drape over complex contours, providing high strength in multiple directions.
What is the lightest bulletproof material?
How much heat can fiberglass cloth withstand?
What can luse instead of fiberglass cloth?
Carbon Fiber: Offers superior strength and stiffness compared to fiberglass, but it is more expensive.
Kevlar: Provides excellent impact resistance and is lighter than fiberglass. It is used in applications requiring high strength and durability, such as bulletproof vests.
Basalt Fiber: Made from volcanic rock, basalt fiber has similar properties to fiberglass but with better thermal and chemical resistance.
Natural Fibers: Materials like hemp, flax, and jute are eco-friendly alternatives, although they typically offer lower strength compared to synthetic fibers.
Polyester or Nylon Fabric: For non-structural applications, heavy-duty polyester or nylon fabrics can be used, particularly where flexibility and durability are more important than strength.
What is the best tool for cutting fiberglass cloth?
What can luse instead of microfiber cloth?
Cotton Cloths: Soft, absorbent, and gentle on surfaces, ideal for general cleaning and polishing.
Chamois Leather: Often used for drying cars, chamois is highly absorbent and gentle on paint.
Linen Cloths: Durable and absorbent, linen is good for cleaning glass and delicate surfaces.
Terry Cloth: Thick and absorbent, terry cloth towels are excellent for heavy-duty cleaning tasks.
Bamboo Fiber Cloths: Eco-friendly and naturally antibacterial, bamboo cloths are a good alternative for various cleaning applications.
How do you get fabric to stick to fiberglass?
Surface Preparation: Clean the fiberglass surface thoroughly to remove any dust, grease, or contaminants.
Adhesive Application: Apply a thin, even layer of epoxy resin or contact cement to the fiberglass surface. For a strong bond, epoxy resin is usually preferred.
Positioning the Fabric: Lay the fabric onto the adhesive-coated surface, smoothing it out to eliminate air bubbles and wrinkles.
Securing the Fabric: Use a roller or brush to press the fabric firmly onto the surface, ensuring good contact between the fabric and the adhesive.
Curing: Allow the adhesive or resin to cure completely according to the manufacturer's instructions before handling or applying additional layers.
Is fiberglass fabric safe?
What temperature can fiberglass cloth withstand?
Does fiberglass cloth insulate?
Which is stronger fiberglass mat or fiberglass cloth?
What is an alternative to glass fiber?
Carbon Fiber: Stronger and stiffer than glass fiber, often used in high-performance applications.
Kevlar: Known for its impact resistance and high tensile strength, used in bulletproof vests and other protective gear.
Basalt Fiber: Offers similar properties to glass fiber but with enhanced thermal and chemical resistance.
Natural Fibers: Such as flax, hemp, or jute, are used in eco-friendly composites, though they typically provide lower strength compared to synthetic fibers.
Aramid Fiber: Another high-strength, lightweight material used in aerospace and military applications.
What is the difference between fiberglass cloth and fiberglass mat?
Structure: Made from continuous glass fibers woven into a fabric. The weave can vary (plain, twill, satin), offering different levels of flexibility and strength.
Strength: Provides higher tensile strength and is stronger than fiberglass mat. The directional weave of the cloth offers superior strength along the fiber's orientation.
Applications: Used in applications requiring high strength, rigidity, and a smooth finish, such as in boat building, automotive parts, and aerospace components.
Fiberglass Mat (Chopped Strand Mat):
Structure: Made from short, randomly oriented glass fibers that are held together with a binder. The fibers are chopped and laid randomly, creating a non-woven mat.
Strength: Provides uniform strength in all directions but is generally less strong than fiberglass cloth due to the shorter, random fiber lengths.
Applications: Often used to build thickness and bulk in composite structures, as well as to provide a smooth surface finish in layups. It’s commonly used as a base layer or for reinforcement in lower-stress applications.
What is fiberglass cloth advantages and disadvantages?
High Strength-to-Weight Ratio: Provides excellent strength without adding much weight, making it ideal for structural reinforcement.
Durability: Resistant to corrosion, moisture, and various chemicals, making it suitable for harsh environments.
Versatility: Can be used in a wide range of applications, including marine, automotive, aerospace, and industrial settings.
Smooth Finish: The woven structure allows for a smoother finish, which is important for aesthetic or aerodynamic applications.
Non-Conductive: Does not conduct electricity, making it safe for electrical insulation applications.
Disadvantages:
Skin Irritation: Handling fiberglass cloth can cause itching and irritation due to the tiny glass fibers.
Cost: Generally more expensive than fiberglass mat, especially when using higher-grade weaves or specialized fabrics.
Limited Flexibility: While it can conform to curves, it is less flexible than fiberglass mat, making it harder to use on very complex shapes without wrinkles or folds.
Requires Proper Handling: To achieve the best results, fiberglass cloth needs to be correctly handled and applied with appropriate resin.
Is fiberglass cloth and resin waterproof?
Does fiberglass cloth stretch?
How many layers of fiberglass mat to use?
General Repairs: For small repairs or patches, 2-3 layers are usually sufficient.
Structural Components: For structural components or parts subject to higher stress, 4-6 layers may be needed.
Boat Hulls or Thick Laminates: In boat building or when creating thick laminates, up to 8-12 layers might be used, often alternating with layers of fiberglass cloth for added strength.
It's important to follow specific design requirements and testing to determine the exact number of layers needed for a particular application.
What is the purpose of fiberglass cloth?
Strengthen Structural Components: In boats, cars, aircraft, and industrial applications where lightweight strength is crucial.
Create Smooth Finishes: When combined with resin, fiberglass cloth creates a smooth, strong surface that is suitable for painting, sanding, or finishing.
Resist Corrosion: Fiberglass cloth is resistant to moisture, chemicals, and UV light, making it ideal for outdoor and marine environments.
Provide Electrical Insulation: Due to its non-conductive nature, fiberglass cloth is also used as an electrical insulator in various applications.
What are the different weights of fiberglass cloth?
4 oz/yd² (135 g/m²): Lightweight cloth used for applications where minimal weight is critical, such as in model making, surfboards, or lightweight panels.
6 oz/yd² (200 g/m²): A versatile mid-weight cloth used in boat building, automotive parts, and general repairs. Offers a good balance of strength and ease of handling.
10 oz/yd² (340 g/m²): Heavier cloth used for more robust structural applications, where greater strength and durability are required, such as in large boat hulls or industrial components.
The choice of weight depends on the specific application, with lighter weights being used for fine finishes and heavier weights for structural reinforcement.
What type of fiberglass cloth is used for boats?
Thank you for your interest in our products. To receive our pricelist or for any inquiries, please fill out the form below. We will get back to you within 24 hours.