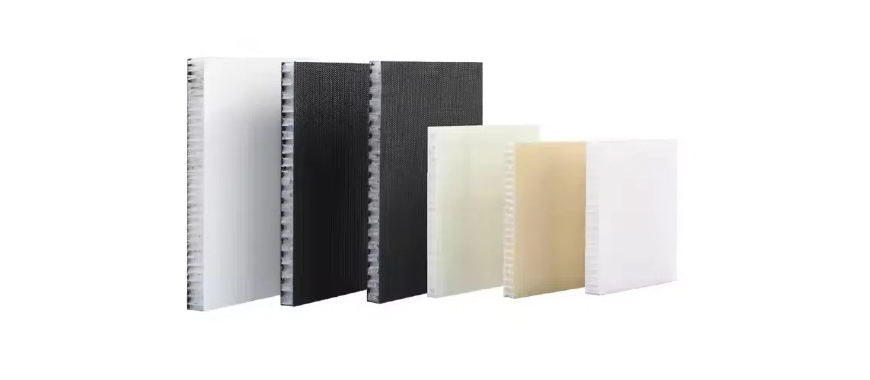
Fiberglass Reinforced Plastic Decking is made of thermosetting plastic resin reinforced by fine glass fibers and with nonslip surfaces. Fiberglass reinforced plastic decking is a cutting-edge material increasingly favored for outdoor decking solutions. Composed of fiberglass embedded within a durable polymer matrix, this type of decking offers unparalleled strength and longevity, outperforming traditional materials like wood or metal. The rise in popularity of fiberglass reinforced plastic decking is attributed to its exceptional resistance to corrosion, lightweight nature, and extended lifespan, making it ideal for a wide range of applications, from residential patios to commercial platforms and industrial walkways. As the demand for more resilient and versatile decking materials grows, fiberglass reinforced plastic decking stands out as a superior choice for modern construction needs.
Benefits of Fiberglass Reinforced Plastic Decking
Fiberglass Reinforced Plastic (FRP) decking offers numerous advantages that make it an excellent choice for a variety of applications, including industrial, commercial, and even residential projects. Here’s a detailed explanation of its benefits:
Exceptional Strength and Durability
FRP decking is known for its high strength-to-weight ratio. Despite being lightweight, it is incredibly strong and can support heavy loads without significant deformation. The material’s durability ensures long-term performance even in demanding environments.
- Resistant to Wear and Tear: FRP decks do not easily crack, warp, or corrode, making them ideal for high-traffic areas.
- Impact Resistance: The material absorbs and disperses shock effectively, reducing the risk of structural damage.
Corrosion Resistance
One of the standout benefits of FRP decking is its exceptional resistance to corrosion. Unlike traditional materials such as steel or wood, FRP is unaffected by moisture, saltwater, chemicals, and other corrosive agents.
- Marine and Coastal Applications: Perfect for docks, piers, and waterfront structures.
- Industrial Environments: Suitable for areas exposed to harsh chemicals and extreme conditions.
Low Maintenance
FRP decking requires minimal maintenance compared to traditional materials.
- No Painting or Coating: Unlike steel, FRP does not require regular painting or protective coatings.
- Easy Cleaning: Dirt, grime, and spills can be easily washed off with water or mild detergents.
- Long Lifespan: The material’s resistance to weathering and wear significantly reduces maintenance costs over time.
Lightweight and Easy Installation
FRP decking is lightweight, which simplifies transportation and installation.
- Reduced Labor Costs: Its lightweight nature makes it easier to handle, requiring less manpower.
- Fast Installation: Pre-fabricated FRP panels can be quickly assembled, reducing downtime and project duration.
Safety Features
FRP decking enhances safety in several ways:
- Anti-Slip Surface: Many FRP decks come with textured or grit surfaces, providing excellent slip resistance even in wet or oily conditions.
- Fire Resistance: Certain FRP formulations offer fire-retardant properties, enhancing safety in high-risk environments.
- Non-Conductive: FRP is non-conductive, making it safe for electrical installations and reducing the risk of shocks.
Design Flexibility
FRP decking can be customized to meet specific project requirements.
- Variety of Shapes and Sizes: It can be molded into various designs to suit architectural and functional needs.
- Color Options: Available in a range of colors that resist fading over time.
- Customizable Load Capacities: Tailored to handle specific weight and stress requirements.
Environmental Benefits
FRP is an eco-friendly option due to its long lifespan and reduced need for replacements.
- Sustainable Material: The durability of FRP reduces waste associated with frequent repairs or replacements.
- Energy Efficiency: Lightweight panels require less energy for transportation.
Cost-Effectiveness
Although the initial cost of FRP decking may be higher than traditional materials, it proves to be cost-effective in the long run.
- Lower Maintenance Costs: Reduced need for repairs, coatings, or replacements.
- Extended Service Life: The material’s durability leads to fewer replacements over time.
FRP decking combines durability, safety, low maintenance, and environmental benefits, making it a superior alternative to traditional decking materials. Its wide range of applications and adaptability further enhance its value in modern construction and design.
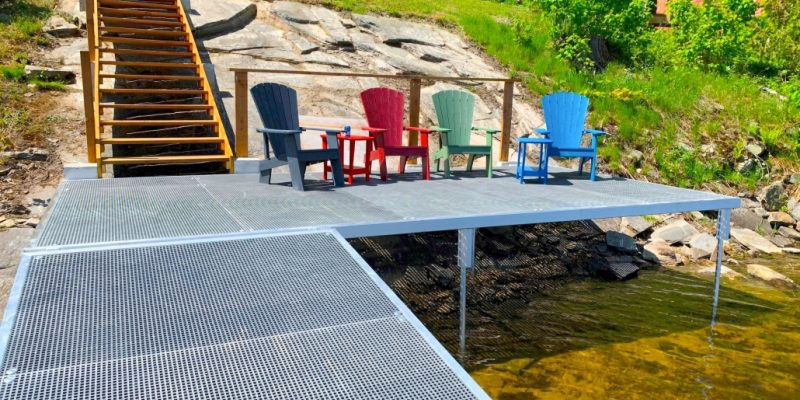
Fiberglass Reinforced Plastic Decking Resin Types
Fiberglass Reinforced Plastic (FRP) decking is made using different types of resins, each tailored to meet specific performance requirements. The choice of resin affects the decking’s strength, chemical resistance, temperature tolerance, and overall durability. Here’s a detailed breakdown of the most common resin types used in FRP decking:
Polyester Resin
Polyester resins are widely used in FRP decking due to their balance of performance and cost-effectiveness.
- Advantages:
- Cost-Effective: Among the most economical resins for FRP manufacturing.
- Good Corrosion Resistance: Suitable for environments with mild to moderate exposure to chemicals.
- Quick Curing: Allows for efficient production processes.
- Versatility: Can be used for general-purpose applications.
- Limitations:
- Not as durable under extreme chemical or high-temperature exposure compared to other resin types.
Vinyl Ester Resin
Vinyl ester resins provide enhanced performance in environments requiring higher resistance to chemicals and heat.
- Advantages:
- Superior Chemical Resistance: Excellent for acidic, alkaline, and solvent-rich environments.
- High Durability: Offers greater resistance to cracking and moisture absorption than polyester.
- Thermal Stability: Can withstand higher temperatures without degrading.
- Limitations:
- Higher cost compared to polyester resin.
- Slightly more challenging to process.
Epoxy Resin
Epoxy resins are known for their exceptional strength, adhesion, and resistance to various environmental factors.
- Advantages:
- Outstanding Strength: High mechanical properties and excellent load-bearing capacity.
- Exceptional Adhesion: Bonds strongly to reinforcing fibers, enhancing structural integrity.
- Chemical and Moisture Resistance: Suitable for environments with aggressive chemical exposure.
- Thermal and Electrical Insulation: Performs well under high temperatures and electrical exposure.
- Limitations:
- Higher cost compared to both polyester and vinyl ester resins.
- Slower curing process can extend production times.
Phenolic Resin
Phenolic resins are used in applications that demand excellent fire resistance and thermal stability.
- Advantages:
- Fire Resistance: Outstanding performance in high-temperature environments.
- Low Smoke and Toxicity: Emits less smoke and toxic gases when exposed to fire, enhancing safety.
- Chemical Resistance: Performs well against various chemicals, including acids and bases.
- Limitations:
- More brittle compared to epoxy and vinyl ester resins.
- Higher manufacturing costs.
Polyurethane Resin
Polyurethane resins are known for their flexibility and impact resistance, making them ideal for dynamic loading conditions.
- Advantages:
- High Impact Resistance: Excellent for areas subject to frequent or heavy impacts.
- Abrasion Resistance: Performs well in environments with abrasive conditions.
- Good Flexibility: Reduces the risk of cracking under stress.
- Limitations:
- Moderate chemical resistance compared to vinyl ester and epoxy resins.
- Higher cost than polyester resins.
Comparative Summary of Resin Types
Resin Type | Strength | Chemical Resistance | Fire Resistance | Cost | Typical Applications |
---|---|---|---|---|---|
Polyester | Moderate | Moderate | Low | Low | General-purpose decking. |
Vinyl Ester | High | High | Moderate | Moderate | Marine and industrial decking. |
Epoxy | Very High | Very High | Moderate | High | High-performance industrial decking. |
Phenolic | Moderate | Moderate | Very High | High | Fire-safe industrial and public decking. |
Polyurethane | Moderate | Moderate | Low | Moderate | High-impact and abrasion-resistant decking. |
Choosing the Right Resin
The choice of resin for FRP decking depends on several factors:
- Environmental Conditions: Corrosion, temperature, and fire risks.
- Load Requirements: Mechanical strength and durability needs.
- Budget Constraints: Balancing cost with performance requirements.
- Safety Standards: Fire resistance or non-toxicity needs in specific industries.
Selecting the appropriate resin ensures that the FRP decking meets the functional and environmental demands of the application while maintaining cost efficiency and long-term performance.
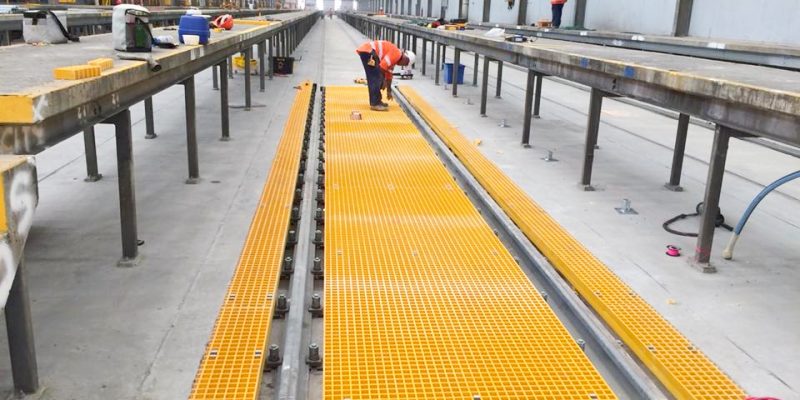
Enhancing Safety with Anti Slip Decking Strips on Fiberglass Reinforced Plastic Decking
Purpose
Fiberglass reinforced plastic decking is renowned for its durability, corrosion resistance, and lightweight properties, making it a preferred choice for various outdoor applications. To further enhance safety, particularly in environments prone to moisture or heavy foot traffic, fiberglass reinforced plastic decking is often equipped with anti-slip decking strips. These strips are crucial in providing an extra layer of protection, ensuring that the decking surface remains safe and slip-resistant even in the most challenging conditions.
Anti-slip decking strips for fiberglass reinforced plastic decking are typically secured using specialized screws that are designed to hold firmly in place without damaging the decking material. These screws, often made of stainless steel or other corrosion-resistant materials, are crucial for maintaining the integrity of the decking over time. The installation process is straightforward yet precise—ensuring that each strip is securely fastened to prevent any movement or detachment, which could compromise safety. Proper installation is key, as improperly secured strips may not perform effectively, leading to potential hazards.
One of the leading manufacturers, GangLong Fiberglass, offers a range of anti-slip strips specifically designed for fiberglass reinforced plastic decking. These strips are engineered to withstand various environmental stresses, from heavy rain to intense sun exposure, without degrading or losing their grip. The use of high-quality screws and the precise installation method recommended by GangLong Fiberglass ensures that these strips remain effective for years, even in high-traffic areas.
Applications
Anti-slip decking strips on fiberglass reinforced plastic deck find their application in a variety of environments where safety is paramount. Around swimming pools, for example, the combination of water and bare feet creates a significant risk of slipping. Fiberglass reinforced plastic decking, when enhanced with anti-slip strips, provides a reliable solution to this problem. The strips ensure that even when the surface is wet, the risk of slipping is greatly minimized, making it safe for both children and adults.
Another common application is in stairways, particularly those exposed to the elements. Stairs are naturally high-risk areas, and when they become wet, the danger of slipping increases significantly. By adding anti-slip strips to fiberglass reinforced plastic deck used on stairs, the risk of accidents is greatly reduced. These strips provide the necessary traction, ensuring that each step is secure even in adverse weather conditions.
High-traffic areas, such as public walkways or industrial platforms, also benefit from the installation of anti-slip decking strips on fiberglass reinforced plastic decking. These environments are often subject to continuous foot traffic, and any slip or fall can lead to serious injuries. By equipping fiberglass reinforced plastic decking with anti-slip strips, companies can ensure a safer environment for both employees and visitors. For example, in industrial settings like those managed by GangLong Fiberglass, a leader in FRP solutions, the addition of anti-slip strips to their fiberglass reinforced plastic decking installations has significantly reduced the incidence of workplace accidents related to slips and falls.
Moreover, these strips are not only functional but also aesthetically pleasing, blending seamlessly with the overall design of the decking. Available in various colors and finishes, they can be customized to match the specific needs of any project, whether it’s a commercial building, a public park, or a residential deck. The use of anti-slip strips on fiberglass reinforced plastic decking is a practical, effective, and long-lasting solution to enhancing safety in a wide range of applications.
This dual benefit of safety and aesthetic appeal makes anti-slip decking strips an essential addition to any fiberglass reinforced plastic decking installation, particularly in areas where safety cannot be compromised. Whether in residential, commercial, or industrial settings, these strips provide the necessary assurance that the decking surface will remain secure, even under the most challenging conditions.
Exploring the Construction and Versatility of Fiberglass Reinforced Plastic Decking Boards
Construction and Materials
Fiberglass reinforced plastic decking boards represent a significant advancement in decking technology, offering a combination of durability, strength, and versatility that surpasses traditional materials like wood or metal. The construction of these decking boards involves embedding high-strength glass fibers within a polymer matrix, typically using thermosetting resins such as polyester or vinyl ester. This process creates a composite material that is not only incredibly strong but also resistant to many of the environmental challenges that plague traditional decking materials.
One of the key advantages of fiberglass reinforced plastic decking boards is their inherent resistance to rot and rust. Unlike wood, which can decay over time due to moisture exposure, or metal, which can corrode when exposed to air and water, fiberglass reinforced plastic decking is impervious to these elements. This makes it an ideal choice for outdoor applications, especially in environments where moisture and humidity are prevalent. For example, GangLong Fiberglass, a leading manufacturer of fiberglass reinforced plastic decking, has documented that their FRP boards maintain structural integrity even after years of exposure to coastal conditions, where saltwater and humidity are constant threats.
Fiberglass reinforced plastic decking boards are designed to withstand a wide range of environmental stresses, including UV radiation and extreme temperatures. The polymer matrix acts as a protective barrier, preventing the long glass fibers from degrading and ensuring that the boards retain their mechanical properties over time. This durability translates to a longer lifespan compared to traditional materials, reducing the need for frequent replacements and thus lowering long-term maintenance costs. Companies like GangLong Fiberglass have reported that their clients experience significantly reduced maintenance expenses after switching to fiberglass reinforced plastic decking boards, with some installations remaining maintenance-free for over 15 years.
Design Versatility
Beyond their robust construction, fiberglass reinforced plastic decking boards also offer unparalleled design versatility. Available in a wide array of styles, colors, and finishes, these boards can be customized to meet the specific aesthetic and functional requirements of any project. Whether it’s a sleek, modern deck for a residential property or a heavy-duty platform for an industrial site, through cutting the deck and fiberglassing ensures that the decking boards are properly fitted and reinforced, maximizing both performance and design flexibility.
The variety of finishes available with fiberglass reinforced plastic decking boards includes smooth, gritted, and textured surfaces, each offering different levels of slip resistance and tactile feel. For instance, a smooth finish might be preferred for a residential patio where barefoot comfort is a priority, while a gritted finish would be ideal for a marine platform where slip resistance is crucial. The ability to choose from these finishes allows architects and designers to tailor the decking to the specific needs of the environment.
In addition to surface finishes, fiberglass reinforced plastic decking boards are available in a range of colors that can either blend seamlessly with the surrounding landscape or make a bold design statement. Colors are typically molded into the resin during the manufacturing process, ensuring that they do not fade or peel over time. This is particularly advantageous in commercial settings where maintaining a clean and consistent appearance is important. For example, in a case study by GangLong Fiberglass, a commercial boardwalk project utilized custom-colored fiberglass reinforced plastic decking boards to match the natural tones of the surrounding environment, resulting in a visually cohesive and durable outdoor space.
Moreover, the adaptability of fiberglass reinforced plastic decking extends to its structural capabilities. These boards can be manufactured in various thicknesses and profiles to accommodate different load-bearing requirements. In industrial applications, where platforms and walkways must support heavy equipment and foot traffic, thicker and more robust fiberglass reinforced plastic decking boards can be used to ensure safety and stability. Conversely, in residential settings where weight is less of a concern, thinner boards can be employed to achieve a more delicate appearance without sacrificing durability.
The versatility of fiberglass reinforced plastic decking boards is further enhanced by their ease of installation. Unlike traditional materials that may require specialized tools or techniques, FRP boards can be cut, drilled, and fastened using standard woodworking tools, making them accessible to both professional contractors and DIY enthusiasts. This ease of installation, combined with the material’s lightweight nature, reduces labor costs and speeds up the construction process, as reported by several contractors in the construction industry.
Fiberglass reinforced plastic decking boards offer a unique combination of strength, durability, and design flexibility that makes them suitable for a wide range of applications. Whether it’s for a residential deck, a commercial boardwalk, or an industrial platform, these boards provide a reliable and aesthetically pleasing solution that stands the test of time.
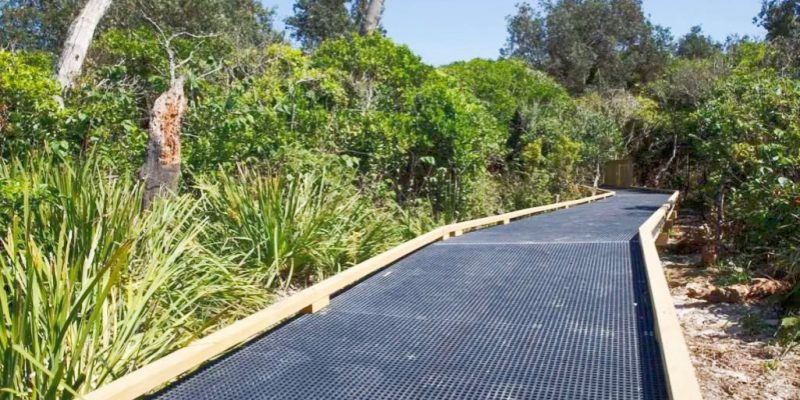
Understanding China FRP Winding Pipe: Key Features Explained
Fiberglass Reinforced Plastic Decking Installation Guidelines
Installing FRP decking requires adherence to specific guidelines to ensure safety, durability, and optimal performance. Below is a detailed step-by-step guide to the installation process:
Pre-Installation Preparation
Planning and Design
- Evaluate Site Conditions: Assess the site for load requirements, environmental factors (e.g., exposure to chemicals, moisture, or UV), and compliance with local building codes.
- Deck Layout: Plan the layout, including panel dimensions, support spacing, and alignment.
- Safety Requirements: Identify safety needs, such as anti-slip surfaces and handrails, if applicable.
Material Inspection
- Check for Damage: Inspect FRP panels for cracks, delamination, or other visible defects.
- Verify Specifications: Ensure that the panels match the project requirements, including dimensions, resin type, and surface texture.
- Prepare Tools and Hardware: Gather the necessary tools, such as saws with diamond-tipped blades, drills, fasteners, and lifting equipment.
Substructure Preparation
- Ensure Stability: Verify that the supporting structure is level, properly anchored, and capable of bearing the expected load.
- Corrosion Resistance: Use corrosion-resistant materials for the substructure, such as stainless steel or galvanized steel, especially in harsh environments.
Cutting and Drilling Panels
- Cutting:
- Use diamond-tipped blades or carbide saws for clean cuts.
- Wear appropriate protective equipment to avoid exposure to fiberglass dust.
- Cut panels slightly larger than required and adjust during installation for a precise fit.
- Drilling:
- Use a high-speed drill with a carbide bit.
- Drill holes slightly larger than fastener diameters to allow for thermal expansion and contraction.
Placement of Panels
Panel Alignment
- Align the panels with the support structure, ensuring even spacing and proper orientation of the textured or gritted surface for slip resistance.
- Leave a small gap (usually 1/8″ to 1/4″) between panels to accommodate thermal expansion.
Handling
- Lift and place panels using appropriate lifting equipment to avoid damage or injury. Avoid dragging panels on rough surfaces to prevent scratches or abrasions.
Fastening Panels
- Fasteners:
- Use corrosion-resistant fasteners (e.g., stainless steel or FRP-specific fasteners).
- Ensure that fasteners are compatible with the decking material to prevent galvanic corrosion.
- Spacing:
- Fasten panels at all points of contact with the supporting structure, typically at every 12″ to 18″.
- Secure edges and corners firmly to prevent lifting or movement.
- Washer Usage:
- Install washers between fasteners and the decking to distribute load evenly and avoid localized stress.
Sealing and Edge Protection
- Sealing:
- Apply sealant to exposed edges to prevent moisture ingress, especially in marine or wet environments.
- Edge Protection:
- Install edge guards or cover plates to protect panel edges from damage and enhance safety.
Post-Installation Inspection
Structural Integrity
- Verify that all panels are securely fastened and properly aligned.
- Check for gaps, uneven surfaces, or loose fasteners and rectify as needed.
Safety Features
- Ensure that anti-slip surfaces are correctly oriented and functional.
- Verify compliance with design specifications and safety standards.
Maintenance Recommendations
- Regular Cleaning:
- Remove debris, dirt, and spills using water or mild detergents to maintain slip resistance and aesthetic appearance.
- Inspection:
- Periodically inspect for damage, such as cracks, delamination, or loosening of fasteners.
- Repairs:
- Replace damaged panels or fasteners promptly to maintain structural integrity.
Installation Tips
- Thermal Expansion:
- Account for thermal expansion and contraction during installation, especially in regions with significant temperature fluctuations.
- Environmental Considerations:
- Use UV-resistant panels in areas exposed to direct sunlight for prolonged periods.
- Opt for additional corrosion-resistant coatings in highly acidic or saline environments.
- Safety Compliance:
- Follow local codes and standards for load capacities, slip resistance, and fire safety.
By following these guidelines, FRP decking can be installed efficiently and safely, ensuring a long service life with minimal maintenance requirements. Proper planning and adherence to installation best practices are key to achieving a durable and high-performing FRP decking system.
Accessibility and Consumer Insights for Anti-Slip Decking Strips with Fiberglass Reinforced Plastic Decking from GangLong Fiberglass
Availability and Accessibility
Fiberglass reinforced plastic decking is increasingly favored by both homeowners and commercial builders, thanks to its strength, durability, and ease of maintenance. GangLong Fiberglass offers a wide range of anti-slip decking strips specifically designed to enhance safety when used with fiberglass reinforced plastic decking. These products are readily accessible through the GangLong Fiberglass website, allowing customers to conveniently browse and purchase the best materials for their decking projects.
One of the key benefits of purchasing fiberglass reinforced plastic decking and anti-slip strips directly from GangLong Fiberglass is the guarantee of product quality and reliability. GangLong Fiberglass works closely with trusted manufacturers to ensure that all products meet high industry standards for durability and safety. The anti-slip strips available on the GangLong Fiberglass website are engineered to provide superior traction on wet or slippery surfaces, making them an essential addition for outdoor spaces. Each product is thoroughly tested to ensure performance, giving consumers confidence that they are investing in reliable and long-lasting materials.
Additionally, GangLong Fiberglass provides comprehensive customer support, including expert guidance on product selection, installation instructions, and warranties. For those new to decking projects, GangLong Fiberglass’s website offers detailed product descriptions, installation tutorials, and customer reviews to help users make informed decisions. The accessibility of high-quality fiberglass reinforced plastic decking and anti-slip strips through GangLong Fiberglass, coupled with the brand’s robust support resources, ensures that customers can confidently choose the best products for their projects.
Consumer Considerations
When selecting anti-slip decking strips for use with fiberglass reinforced plastic decking, consumers should take several important factors into account to ensure they choose the best product for their needs. Key considerations include the size, material compatibility, and installation process, all of which can impact the effectiveness and durability of the strips.
First, the size of the anti-slip strips is a critical factor. Measuring the width and length of the fiberglass reinforced plastic decking boards ensures that consumers select strips that provide optimal coverage. Strips that are too small or too large may not provide sufficient slip resistance, diminishing their safety benefits. GangLong Fiberglass offers anti-slip strips in a variety of sizes to match different decking dimensions, ensuring a perfect fit for any project.
Material compatibility is another essential factor to consider. Anti-slip strips must be designed specifically for use with fiberglass reinforced plastic decking to ensure proper adhesion and durability. GangLong Fiberglass provides clear product descriptions, specifying which anti-slip strips are designed for fiberglass decking. This helps consumers avoid compatibility issues, ensuring they get the right product for maximum safety and performance.
The installation method is also crucial. While some anti-slip strips are easy to install, others may require more advanced techniques. Consumers should evaluate their comfort level with installation before purchasing. GangLong Fiberglass provides detailed installation guides, and many products come with the necessary hardware, such as screws or adhesive, to make installation easier. For those who prefer professional installation, GangLong Fiberglass can connect customers with experts to ensure that the anti-slip strips are installed correctly on fiberglass decking.
In addition to size, compatibility, and installation, consumers should also consider the durability and maintenance requirements of the anti-slip strips. High-quality strips designed for fiberglass reinforced plastic decking are typically low-maintenance and resistant to wear. GangLong Fiberglass offers product warranties, providing added peace of mind for customers. A strong warranty indicates the durability and quality of the product, which is especially important for outdoor applications where decking is exposed to harsh weather conditions.
When purchasing anti-slip decking strips for fiberglass reinforced plastic decking from GangLong Fiberglass, consumers benefit from a comprehensive selection of products, detailed product information, and extensive customer support. By considering factors such as size, material compatibility, and installation methods, customers can confidently choose the best anti-slip strips for their projects, resulting in safer, more durable outdoor spaces.
Choosing the Right Marine Fiberglass Pipes for Harsh Conditions
Ensuring Safety with Non Slip Deck Strips on Fiberglass Reinforced Plastic Decking
Importance of Non-Slip Features
The incorporation of non-slip deck strips into fiberglass reinforced plastic decking is essential for creating safe and reliable outdoor surfaces, especially in environments where the risk of slipping is high. Fiberglass reinforced plastic decking, known for its strength, durability, and resistance to environmental factors, is an excellent choice for a variety of settings, from residential patios to industrial platforms. However, the addition of non-slip deck strips significantly enhances the safety profile of these installations, making them even more suitable for areas exposed to moisture or heavy foot traffic.
Non-slip deck strips are designed to provide additional traction on fiberglass reinforced plastic decking, preventing accidents caused by slippery surfaces. These strips can be integrated directly into the decking during the manufacturing process or added as aftermarket solutions. When integrated during production, non-slip features are often molded into the surface of the fiberglass reinforced plastic decking, creating a uniform, durable finish that maintains its slip-resistant properties over time. This method is particularly effective for large-scale installations where consistency and long-term performance are critical.
Aftermarket non-slip deck strips, on the other hand, offer flexibility for existing fiberglass reinforced plastic decking installations. These strips can be applied to areas that experience frequent moisture or are prone to becoming slippery, such as near pools, on stairways, or in high-traffic walkways. Companies like GangLong Fiberglass offer a range of non-slip strips specifically designed to adhere to fiberglass reinforced plastic decking, providing a quick and effective solution to enhance safety without the need for a complete deck overhaul.
The importance of non-slip deck strips in fiberglass reinforced plastic decking installations cannot be overstated. Slip-related accidents are a common cause of injury, particularly in commercial and public spaces where liability concerns are paramount. By integrating non-slip features, property owners and managers can significantly reduce the risk of such incidents, ensuring that their spaces are safe for all users. The use of non-slip deck strips is not just a safety measure; it is a proactive approach to preventing accidents and protecting the wellbeing of those who use these surfaces.
Performance Under Various Conditions
Non-slip deck strips are engineered to perform effectively across a wide range of environmental conditions, ensuring that fiberglass reinforced plastic decking remains safe regardless of the weather. Whether it’s rain, snow, or ice, these strips are designed to maintain their grip, providing consistent traction that reduces the likelihood of slips and falls.
In wet conditions, non-slip deck strips on fiberglass reinforced plastic decking play a crucial role in preventing accidents. Rain can quickly turn a smooth deck surface into a hazardous area, especially if the decking is located near water sources like pools or fountains. The textured surface of non-slip strips provides the necessary grip to keep users safe, even when the decking is wet. For instance, in a case study involving an outdoor restaurant patio in Seattle, where rain is frequent, the installation of non-slip deck strips on fiberglass reinforced plastic decking significantly reduced slip incidents, according to the project managers.
Snow and ice pose additional challenges, as they can create an even more slippery surface. Non-slip deck strips designed for use with fiberglass reinforced plastic decking are typically made from materials that remain effective even in freezing temperatures. These strips often feature a gritted or abrasive surface that enhances traction, ensuring that the decking remains safe to walk on during winter months. In colder climates, such as in parts of Canada where winter conditions are severe, non-slip strips have been successfully used on fiberglass reinforced plastic decking to prevent accidents on public walkways and residential decks. Companies like GangLong Fiberglass have developed specific formulations for their non-slip strips to perform well under these extreme conditions, offering a reliable solution for cold-weather safety.
Durability is another key factor in the performance of non-slip deck strips. These strips must withstand constant exposure to harsh environmental conditions without losing their effectiveness. High-quality non-slip strips for fiberglass reinforced plastic decking are typically UV-resistant, ensuring that they do not degrade or lose their grip over time, even with prolonged sun exposure. This is particularly important in regions with intense sunlight, where UV rays can cause materials to weaken and become brittle. GangLong Fiberglass’s non-slip strips, for example, are designed to maintain their integrity and performance for years, even under direct sunlight and heavy use.
Maintenance of non-slip deck strips is relatively straightforward but essential to ensure their long-term effectiveness. Regular cleaning to remove dirt, debris, and any buildup that could reduce the strips’ grip is necessary. Depending on the location and usage, periodic inspections may also be required to check for wear and tear. Replacing worn-out strips promptly ensures that fiberglass reinforced plastic decking continues to provide a safe surface for users. In commercial settings, such as shopping malls or public parks, maintenance teams often include these checks as part of their routine upkeep, helping to prevent accidents and extend the life of the decking.
Non-slip deck strips are a critical component in maintaining the safety and functionality of fiberglass reinforced plastic decking across various environmental conditions. Their ability to provide reliable traction in wet, icy, or high-traffic areas makes them an indispensable addition to any decking project where safety is a priority. With proper installation and maintenance, these strips ensure that fiberglass reinforced plastic decking remains a safe and secure surface for all users, regardless of the weather.
Choosing the Best Non Slip Composite Decking: Why Fiberglass Reinforced Plastic Decking Stands Out
Comparison with Other Materials
When it comes to selecting the best non-slip composite decking, fiberglass reinforced plastic decking (FRP) consistently outperforms other materials in both safety and durability, particularly in environments where moisture is a constant challenge. Fiberglass composite decking, in general, has gained popularity due to its combination of synthetic materials that offer resistance to weathering and decay. However, among the various types of composite decking available—such as wood-plastic composites (WPC) and polyvinyl chloride (PVC) decking—fiberglass reinforced plastic decking stands out for its superior non-slip properties and overall resilience.
Fiberglass reinforced plastic decking is inherently non-slip due to its unique composition. The glass fibers embedded within the polymer matrix provide a textured surface that naturally enhances traction. This is in stark contrast to wood-plastic composites, which, while durable, can become slippery when wet due to their smoother surface. For example, a study by the National Association of Home Builders (NAHB) found that FRP decking had a slip resistance coefficient significantly higher than WPC decking, making it a safer option for areas like pool decks, marinas, and boardwalks where moisture is prevalent.
Additionally, FRP’s resistance to mold and mildew growth further contributes to its non-slip characteristics. Unlike wood-based composites, which can absorb moisture and become breeding grounds for mold, fiberglass reinforced plastic decking remains impervious to water infiltration. This not only prevents the deck surface from becoming slippery but also reduces maintenance requirements over time. In high-humidity regions, such as the coastal areas of Florida, homeowners and property managers have reported fewer slip-related accidents and lower maintenance costs after switching to fiberglass reinforced plastic decking.
In terms of durability, fiberglass reinforced plastic decking outlasts many of its composite counterparts, particularly in harsh environments. PVC decking, while resistant to moisture and rot, can become brittle and slippery in cold temperatures. In contrast, FRP maintains its structural integrity and non-slip surface in a wide range of temperatures, from freezing winters to scorching summers. This makes it an ideal choice for outdoor spaces in diverse climates. For example, in the mountainous regions of Colorado, ski resorts have increasingly adopted FRP decking for their outdoor platforms due to its reliable performance in icy conditions.
Consumer Recommendations
For consumers seeking the best non-slip composite decking, fiberglass reinforced plastic decking offers a combination of safety, durability, and low maintenance that is unmatched by other materials. Its non-slip surface, which remains effective even in wet conditions, makes it the top choice for areas where safety is a priority. Industry standards such as those set by the American Society for Testing and Materials (ASTM) highlight FRP’s superior slip resistance, with FRP decking consistently meeting or exceeding the required safety thresholds.
Consumers should also consider the long-term benefits of choosing fiberglass reinforced plastic decking over other composite materials. While the initial cost of FRP decking may be higher than wood-plastic composites or PVC, the long-term savings in maintenance and the added safety make it a cost-effective choice. Homeowners who have installed FRP decking often report minimal upkeep, with no need for frequent treatments or replacements due to mold, rot, or UV damage. For instance, a survey conducted by the decking manufacturer Bedford Reinforced Plastics found that over 90% of customers were satisfied with the longevity and safety of their FRP decking, citing its slip resistance as a key factor in their positive experiences.
Moreover, fiberglass reinforced plastic decking is available in a variety of finishes and textures, allowing consumers to choose a product that not only meets safety requirements but also complements the aesthetic of their outdoor space. From gritted surfaces that provide maximum traction to smoother finishes that balance safety with barefoot comfort, FRP decking can be tailored to meet the specific needs of any project. This versatility, combined with its proven safety record, makes FRP the best choice for non-slip composite decking.
Consumer reviews further support the preference for fiberglass reinforced plastic decking in moisture-prone environments. For example, reviews on home improvement platforms such as Houzz and HomeAdvisor consistently rate FRP decking highly for its slip-resistant properties, particularly in poolside applications. Users praise its ability to stay cool underfoot in hot weather while providing a secure surface that reduces the risk of falls.
For those prioritizing safety in their outdoor spaces, fiberglass reinforced plastic decking represents the pinnacle of non-slip composite decking solutions. Its combination of superior traction, resistance to environmental wear, and ease of maintenance positions it as the ideal choice for anyone looking to invest in a decking material that offers both peace of mind and long-term value. Whether for residential patios, commercial boardwalks, or industrial platforms, FRP decking delivers the best in non-slip performance, ensuring a safe and enjoyable outdoor experience for all users.
High Pressure Fiberglass Pipe: Best Solutions
Ensuring Safety with Non Slip Fiberglass Reinforced Plastic Decking
Essential Safety Feature
The incorporation of non-slip features in fiberglass reinforced plastic decking is not just a design consideration but a crucial safety element, especially in public and commercial spaces where foot traffic is heavy and the risk of accidents is higher. Fiberglass reinforced plastic decking, known for its robustness and versatility, is often employed in environments such as outdoor walkways, poolside decks, and industrial platforms. In these settings, ensuring a non-slip surface is paramount to preventing injuries caused by slips and falls.
Fiberglass reinforced plastic decking is engineered with non-slip surfaces through a combination of advanced material selection and texture design. The primary material, fiberglass, is embedded within a polymer matrix that is not only strong and durable but also inherently resistant to moisture. This resistance to moisture is key to maintaining a non-slip surface, as wet conditions are a common cause of slipping accidents. The texture of fiberglass reinforced plastic decking can be customized during the manufacturing process to include gritted or abrasive surfaces that enhance traction. For example, in public boardwalks managed by cities like San Francisco, the use of gritted fiberglass reinforced plastic decking has significantly reduced slip-related incidents, even during the rainy season.
The choice of texture and material for non-slip fiberglass reinforced plastic decking depends on the specific application. In areas where aesthetics are as important as safety, such as hotel pool decks or upscale outdoor dining areas, manufacturers like GangLong Fiberglass offer decking options with a finer texture that provides a balance between comfort and slip resistance. This allows for a safer environment without compromising on the visual appeal or the comfort of walking barefoot on the decking.
In more industrial or high-risk environments, a coarser texture might be preferable. This type of surface is engineered to provide maximum grip, even when exposed to oil, grease, or other slippery substances. Companies like GangLong Fiberglass supply industrial clients with fiberglass reinforced plastic decking that features a heavy-duty gritted surface, designed to maintain its non-slip properties under the most challenging conditions. This is particularly important in industries such as manufacturing or warehousing, where the safety of workers is a top priority, and the cost of accidents can be substantial.
The importance of non-slip features in fiberglass reinforced plastic decking cannot be overstated, especially in public spaces where the safety of visitors is at stake. In addition to preventing injuries, non-slip decking also helps organizations avoid potential liability issues, making it a wise investment for any public or commercial space that values both safety and functionality.
Long-Term Maintenance
While fiberglass reinforced plastic decking is designed to be low-maintenance, it is still essential to carry out regular upkeep to ensure that the non-slip properties remain effective over time. The longevity of the non-slip surface depends on both the quality of the decking material and the maintenance practices employed.
Regular cleaning is the first step in maintaining the non-slip properties of fiberglass reinforced plastic decking. Dirt, algae, and other debris can accumulate on the surface, reducing its effectiveness and increasing the risk of slips. It is recommended to clean the decking with a mild detergent and a soft brush at least once a month, or more frequently in high-traffic areas or environments prone to dirt buildup. For example, public parks in urban areas like New York City schedule monthly cleanings of their fiberglass reinforced plastic decking to ensure that the surfaces remain safe for visitors.
In addition to cleaning, periodic inspections are necessary to identify any wear and tear on the non-slip surface. Over time, heavy use or exposure to harsh weather conditions can cause the gritted surface to wear down, reducing its slip-resistant properties. If the decking shows signs of significant wear, it may be necessary to reapply a non-slip coating or replace the affected panels. GangLong Fiberglass offers maintenance kits specifically designed for fiberglass reinforced plastic decking, including re-gritting solutions that restore the original non-slip texture without the need for complete replacement.
Another aspect of long-term maintenance is addressing any damage to the decking that could compromise its safety. Fiberglass reinforced plastic decking is highly resistant to impacts and general wear, but in the rare event of damage—such as cracks or chips—it is crucial to repair these issues promptly. Unrepaired damage can lead to uneven surfaces, which in turn increase the risk of trips and falls. Companies like GangLong Fiberglass provide repair services for fiberglass reinforced plastic decking, ensuring that any damage is fixed quickly and efficiently, maintaining the decking’s safety and functionality.
Finally, it’s important to consider the environmental conditions to which the decking is exposed. In areas with extreme weather conditions, such as the hot, arid climates of Arizona or the cold, snowy winters of Canada, additional protective measures may be necessary. This could include applying UV protectants or anti-icing agents to ensure that the non-slip properties are preserved despite the harsh elements.
Maintaining the non-slip properties of fiberglass reinforced plastic decking is a straightforward process that, when followed, ensures the decking remains safe and effective for many years. Regular cleaning, inspection, and prompt repair of any damage are key practices that help to preserve the integrity of the non-slip surface, providing peace of mind to property owners and ensuring the safety of all who use these spaces.
Enhancing Safety with Anti Slip Wood Deck Coating on Fiberglass Reinforced Plastic Decking
FRP Coating Solutions
Fiberglass reinforced plastic decking is well-regarded for its inherent durability and resistance to environmental factors, making it an excellent choice for outdoor applications. However, in certain situations, adding an anti-slip coating originally designed for wood decks can further enhance the safety of fiberglass reinforced plastic decking. These coatings, typically composed of textured polymers or grit-infused compounds, provide an additional layer of traction, making the decking safer for high-traffic areas or spaces prone to moisture.
Anti-slip coatings designed for wood decks are formulated to adhere to porous surfaces like wood, which naturally absorb the coating and create a strong bond. When these coatings are applied to fiberglass reinforced plastic decking, the results can be equally, if not more, effective. The non-porous surface of FRP, when properly prepared, can hold the coating securely, allowing it to provide the same level of slip resistance as it does on wood. Companies such as GangLong Fiberglass and GangLong Fiberglass, which produce popular anti-slip coatings for wood decks, have seen their products successfully adapted for use on fiberglass reinforced plastic decking, particularly in residential settings where safety and aesthetics are both important.
One key advantage of using anti-slip coatings on fiberglass reinforced plastic decking is the enhanced durability of the coated surface compared to wood. While wood may eventually deteriorate under the coating due to moisture infiltration or rot, fiberglass reinforced plastic decking remains unaffected by these issues. This means that the anti-slip coating, when applied to FRP, can last longer and require less maintenance over time. For instance, in coastal regions where both wood and FRP decking are exposed to saltwater, FRP decking with an anti-slip coating has been observed to maintain its slip-resistant properties for years, whereas wood decks might need frequent re-coating and repair.
Moreover, the color retention of anti-slip coatings on fiberglass reinforced plastic decking is often superior to that on wood. Because FRP is resistant to UV damage and does not expand or contract with temperature changes, the coatings do not crack or peel as they might on wood surfaces. This makes fiberglass reinforced plastic decking a more stable and long-lasting option for outdoor areas where safety and appearance are equally important.
Application and Longevity
Applying anti-slip coatings to fiberglass reinforced plastic decking requires careful preparation to ensure that the coating adheres properly and provides long-lasting slip resistance. The first step in the application process is to thoroughly clean the FRP decking surface. Any dirt, grease, or existing sealants must be removed to create a clean, smooth base for the coating. Using a mild detergent and water, followed by a rinse with clean water, is usually sufficient. In cases where the decking has been previously treated with other coatings or has developed stubborn stains, a more intensive cleaning method, such as pressure washing, might be necessary.
Once the surface is clean and dry, it’s important to lightly sand the fiberglass reinforced plastic decking to create a slightly roughened texture. This step is crucial because it allows the anti-slip coating to grip the FRP surface more effectively. A medium-grit sandpaper is typically recommended for this purpose. After sanding, the surface should be wiped down with a tack cloth to remove any dust or debris.
When applying the anti-slip coating, it’s essential to follow the manufacturer’s instructions regarding the number of coats and drying times. Generally, two to three thin coats provide better coverage and durability than a single thick coat. Each layer should be allowed to dry completely before applying the next. Application methods can vary depending on the product, but a roller is often the best tool for ensuring an even application over large areas. For smaller or more intricate sections, a brush may be used to apply the coating more precisely.
The longevity of the anti-slip coating on fiberglass reinforced plastic decking largely depends on the quality of the product used and the conditions to which the decking is exposed. High-quality coatings from reputable brands like GangLong Fiberglass can last several years with minimal maintenance, even in harsh outdoor environments. In areas with extreme weather conditions—such as intense sun, heavy rain, or snow—the coating might require periodic reapplication to maintain its effectiveness. However, because fiberglass reinforced plastic decking does not suffer from the same issues as wood, such as warping or rotting, the underlying surface remains in excellent condition, and only the coating itself needs attention.
To extend the lifespan of the anti-slip coating, regular maintenance is recommended. This includes keeping the surface clean and free from debris, which can wear down the coating over time. In areas where the coating might experience heavy foot traffic or exposure to abrasive materials, periodic inspections can help identify any worn areas that might need touch-ups.
Applying an anti-slip coating designed for wood decks to fiberglass reinforced plastic decking is an effective way to enhance safety and extend the usability of the decking surface. With proper preparation and maintenance, these coatings can provide a durable, slip-resistant surface that stands up to the challenges of outdoor environments, making fiberglass reinforced plastic decking an even more attractive option for both residential and commercial applications.
FAQS about Fiberglass Reinforced Plastic Decking
Yes, fiberglass reinforced plastic (FRP) is an excellent material known for its durability, corrosion resistance, and strength-to-weight ratio. FRP is especially popular in industrial and commercial applications where these properties are essential. For example, fiberglass reinforced plastic decking is a popular choice in environments that are exposed to harsh conditions such as chemicals, saltwater, and extreme weather. The material’s ability to withstand such conditions makes it a cost-effective and long-lasting option for decking, walkways, and platforms. Additionally, FRP does not rust, rot, or corrode, which significantly reduces maintenance costs over time. Its non-conductive and non-slip surface also enhances safety, making it a preferred material in various industries, including marine, chemical, and construction. Overall, FRP is a highly reliable material that offers numerous advantages for demanding applications.
Fiberglass reinforced plastic (FRP) is used in a wide range of applications due to its versatile properties. Fiberglass reinforced plastic decking is particularly common in industrial settings, where it is used to create durable and corrosion-resistant walkways, platforms, and stairs. Beyond decking, FRP is used in the construction of pipes, tanks, and grating, especially in environments where exposure to chemicals or moisture is a concern. In the marine industry, FRP is used to build boat hulls, docks, and even entire vessels because of its lightweight nature and resistance to saltwater corrosion. The material is also found in the automotive and aerospace industries for constructing lightweight, strong components. FRP’s non-conductive properties make it ideal for electrical insulation and applications where safety is a priority. Its versatility and robust performance make it a go-to material for engineers and designers across multiple industries.
FRP decking, or fiberglass reinforced plastic decking, is a type of decking material made from a composite of fiberglass and resin. This combination creates a strong, lightweight, and corrosion-resistant material that is ideal for use in environments where traditional materials like wood or metal might deteriorate quickly. FRP decking is often used in industrial and commercial settings, such as chemical plants, offshore platforms, and water treatment facilities, where exposure to harsh chemicals or saltwater is common. One of the key benefits of FRP decking is its longevity; it does not rot, rust, or warp, even in extreme conditions. Additionally, FRP decking is non-conductive and has a high strength-to-weight ratio, making it safe and easy to install. It is also available in various textures, including non-slip surfaces, which enhance safety in wet or oily conditions. Overall, FRP decking is a durable and low-maintenance solution for challenging environments.
Fibre reinforced plastic (FRP) and fibreglass are terms that are often used interchangeably, but they refer to slightly different concepts. Fibreglass is a type of fibre reinforced plastic that specifically uses glass fibres as the reinforcing material. Therefore, all fibreglass is FRP, but not all FRP is fibreglass. FRP can be reinforced with other types of fibres, such as carbon or aramid, depending on the specific application requirements. For instance, fiberglass reinforced plastic decking specifically uses glass fibres to provide strength and durability, making it suitable for use in corrosive environments. The choice between fibreglass and other types of fibre reinforcement depends on factors such as cost, strength, and environmental resistance. While fibreglass is widely used due to its cost-effectiveness and good overall performance, other types of FRP may be chosen for applications that require higher strength or greater heat resistance.
FRP (Fiber Reinforced Polymer) decking typically costs between $25 to $35 per square foot for materials, with additional costs for installation depending on the complexity of the project. This price can vary based on the specific type of FRP used, deck design, and supplier. FRP decking offers excellent strength, corrosion resistance, and longevity, making it a valuable investment for environments where traditional materials like wood or steel might degrade quickly. While the initial cost is higher than wood or steel, the reduced maintenance and extended lifespan often make FRP a cost-effective solution over time.
PVC decking, while durable and low-maintenance, has some drawbacks. It tends to be more expensive than traditional wood and composite decking options. PVC can become slippery when wet, posing a safety hazard. Additionally, it can retain heat, making the surface uncomfortable to walk on during hot weather. Another potential downside is its appearance—some users find PVC decking lacks the natural look of wood, which may not suit all aesthetic preferences. Over time, it can also fade or discolor due to prolonged UV exposure.
Fiberglass decks are incredibly durable, often lasting 25 to 50 years with proper maintenance. Their longevity depends on factors like the quality of materials, climate, and usage. Fiberglass is highly resistant to water, UV rays, and temperature fluctuations, making it ideal for outdoor use. Regular cleaning and sealing every few years can help maximize its lifespan. Despite its durability, cracks or damage caused by heavy impacts may require professional repairs, which can be costly.
GRP (Glass Reinforced Plastic) has some limitations despite its advantages. It is more expensive than traditional materials like wood or steel. GRP can also be brittle under certain conditions, making it susceptible to cracking or breaking if subjected to heavy impacts. Repairs to GRP structures can be challenging and costly, as they often require skilled professionals. Additionally, GRP manufacturing processes are not environmentally friendly, contributing to higher energy consumption and waste.
Fiberglass Reinforced Plastic (FRP) is a composite material made of a polymer matrix reinforced with glass fibers. It is lightweight yet strong, resistant to corrosion, and durable under various environmental conditions. FRP is widely used in construction, transportation, and marine industries for products like decking, bridges, and pipes. Its versatility and resistance to rust or chemical exposure make it a preferred material for applications requiring longevity and strength.
Fiberglass rebar offers several advantages over steel, especially in environments prone to corrosion. It is lightweight, corrosion-resistant, and non-conductive, making it suitable for applications like marine structures, bridges, and power plants. However, it is not as strong as steel in compression and is more expensive upfront. Fiberglass rebar is ideal for projects where its corrosion resistance and lightweight properties provide long-term benefits, but steel remains a better option for applications demanding high compressive strength and cost-efficiency.
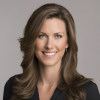
As the editor of GangLong Fiberglass, I have years of experience and in-depth research, focusing on cable tray products, fiberglass solutions, and grille systems. I incorporate years of industry insights and practical experience into every content, committed to promoting the progress of the industry. At GangLong Fiberglass, my commitment is reflected in every product, from innovative cable trays to durable fiberglass solutions and sturdy grille systems. As an authoritative voice in the industry, my goal is to provide valuable information to professionals and businesses and promote forward-looking solutions.