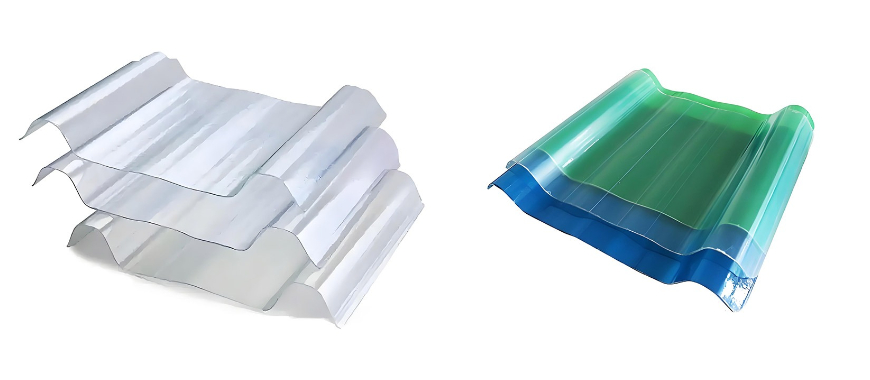
Fiberglass reinforced plastic plywood (FRP plywood) is a composite material that combines the structural strength of plywood with the enhanced durability and resistance of fiberglass reinforced plastic. By embedding fiberglass within the plywood, FRP plywood gains increased mechanical strength, moisture resistance, and corrosion resistance, making it more suitable for demanding environments. The key properties of fiberglass reinforced plastic plywood include being lightweight, strong, and highly versatile, allowing it to perform well in a variety of applications. Unlike traditional plywood, FRP plywood offers superior protection against environmental factors like moisture, chemicals, and wear. This makes it an ideal choice for industries such as construction, automotive, and marine, where strength and durability are essential. The addition of fiberglass reinforced plastic enhances the performance of plywood, providing a longer lifespan and greater resilience in harsh conditions.
Composition and Structure of Fiberglass Reinforced Plastic Plywood
Fiberglass reinforced plastic plywood (FRP plywood) is a durable composite material that blends the inherent strength of plywood with the protective properties of fiberglass. This combination makes it highly resilient to harsh environments, offering superior performance across a variety of industries. The composition of FRP plywood consists of a plywood core, fiberglass reinforced plastic surface layers, and strong adhesive bonding to integrate these components into a single cohesive material.
Core Material: Plywood
The core of fiberglass reinforced plastic plywood is typically made from high-quality plywood, which serves as the structural foundation of the material. Plywood can be crafted from various types of wood, such as birch, pine, poplar, or eucalyptus, each offering unique characteristics suited to different applications. Birch plywood is known for its strength and durability, making it ideal for heavy-duty applications, while pine plywood is more affordable and commonly used in general construction.
The plywood core is treated to improve its resistance to moisture, fire, and decay. These treatments ensure that the plywood does not weaken or degrade under exposure to water or fire, which is essential in environments where these factors are a concern. The treatment also enhances the material’s overall durability, making it suitable for both indoor and outdoor applications.
Surface Layer: Fiberglass Reinforced Plastic (FRP)
The surface of fiberglass reinforced plastic plywood is made of fiberglass reinforced plastic (FRP) that is applied as a skin or coating over the plywood core. The FRP layer typically consists of fiberglass mats or woven fibers combined with a polymer resin, such as polyester or vinyl ester. This layer is often gel-coated, which provides a smooth, glossy finish that is not only aesthetically pleasing but also functional. The gelcoat serves as a protective barrier, enhancing the surface’s durability and resistance to wear.
One of the standout features of FRP is its UV-resistant properties. The fiberglass layer is designed to withstand prolonged exposure to sunlight without degrading or losing its strength. This makes fiberglass reinforced plastic plywood highly weather-resistant, especially in applications exposed to outdoor conditions, where UV radiation can cause other materials to weaken or discolor over time.
Adhesive Bonding: Combining the Plywood Core with Fiberglass Layers
The plywood core and fiberglass reinforced plastic layers are bonded together using strong, durable adhesives. These adhesives are specifically formulated to create a strong bond that ensures the fiberglass surface layers remain securely attached to the plywood core. The bonding process is critical to the overall integrity and performance of the FRP plywood, as it ensures that the material remains stable and resistant to delamination under stress.
The adhesive used must also be resistant to moisture, chemicals, and temperature fluctuations, ensuring that the bond remains intact even in challenging environments. This strong adhesive bonding contributes to the overall durability of fiberglass reinforced plastic plywood, allowing it to maintain its structural integrity and resist environmental degradation for extended periods.
The combination of a robust plywood core, a durable fiberglass surface, and high-strength adhesive bonding creates a composite material that excels in applications requiring strength, moisture resistance, and long-lasting performance. Whether used in construction, transportation, or other demanding industries, fiberglass reinforced plastic plywood offers a reliable solution that enhances the capabilities of traditional plywood.
Top Uses of Fiberglass Insulation Strips in Construction
Benefits of Fiberglass Reinforced Plastic Plywood
Fiberglass reinforced plastic plywood (FRP plywood) offers numerous advantages that make it a superior choice for many demanding applications. By combining the strength of plywood with the durability of fiberglass, this material enhances performance, durability, and resistance to harsh environmental conditions. The unique properties of FRP plywood provide significant benefits, making it highly suitable for industries such as construction, automotive, marine, and agriculture.
Strength and Durability of Fiberglass Reinforced Plastic Plywood
Fiberglass reinforced plastic plywood significantly enhances the mechanical strength and durability of traditional plywood. The fiberglass layers embedded in the plywood core increase its resistance to impact, wear, and chemical exposure, ensuring that the material can withstand tough conditions without compromising its structural integrity. This makes FRP plywood ideal for use in applications that require both strength and long-term durability, such as in construction panels, vehicle flooring, and structural reinforcements.
Corrosion and Moisture Resistance of Fiberglass Reinforced Plastic Plywood
One of the key advantages of fiberglass reinforced plastic plywood is its superior resistance to moisture and corrosion. The FRP surface acts as a barrier, protecting the plywood core from water damage, rot, and degradation. This makes FRP plywood particularly useful in environments that are prone to high humidity or direct exposure to water, such as marine applications, agricultural settings, and industrial facilities. The material’s ability to resist corrosion from chemicals and salts also makes it well-suited for use in harsh environments like chemical plants, waste treatment facilities, and coastal construction projects.
Fire and Water Resistance
In addition to its moisture and corrosion resistance, fiberglass reinforced plastic plywood is treated to provide fire-resistant and waterproof properties. The treatment of the plywood core ensures that it performs well under exposure to fire and water, improving safety in applications where these factors are critical. For instance, in construction projects, FRP plywood can help reduce the risk of fire spreading by providing a barrier to flames, while its water-resistant properties prevent water infiltration that could lead to damage or decay over time. This makes it an excellent choice for high-risk areas, including public buildings, transportation infrastructure, and hazardous environments.
Lightweight Fiberglass Reinforced Plastic Plywood: A Durable and Versatile Material
Despite its remarkable strength and durability, fiberglass reinforced plastic plywood remains surprisingly lightweight. This is one of the key benefits that sets FRP plywood apart from other composite materials. The lightweight nature of the material makes it easier to handle, transport, and install, reducing labor costs and simplifying logistics. This is particularly important in applications where large panels or sheets need to be moved or installed in challenging locations, such as in construction or marine industries.
Additional Benefits of Fiberglass Reinforced Plastic Plywood
- Versatility: FRP plywood can be easily molded into various shapes and sizes, making it suitable for a wide range of applications, from structural components to decorative finishes.
- Aesthetic Appeal: The smooth, glossy surface of fiberglass reinforced plastic plywood not only enhances its durability but also provides an attractive finish, suitable for both functional and aesthetic purposes.
- Low Maintenance: The durability and resistance to environmental factors mean that FRP plywood requires minimal maintenance, reducing long-term operational costs.
Overall, fiberglass reinforced plastic plywood provides a versatile, durable, and cost-effective solution for industries that demand materials with high performance under tough conditions. Whether used in construction, marine applications, or automotive manufacturing, FRP plywood delivers a range of benefits that make it a superior choice over traditional plywood and other materials.
Benefits of Thin Fiberglass Insulation for Metal Buildings
Applications of Fiberglass Reinforced Plastic Plywood
Fiberglass reinforced plastic plywood (FRP plywood) is a versatile and durable material that finds use across various industries due to its exceptional strength, moisture resistance, and lightweight nature. The unique combination of plywood and fiberglass makes it ideal for applications that demand high performance in challenging environments. From construction to transportation, FRP plywood offers a reliable solution for a range of uses.
Truck & Trailer Bodies
One of the primary applications of fiberglass reinforced plastic plywood is in the construction of truck and trailer bodies. The material’s durability and lightweight nature make it an excellent choice for both dry freight and refrigerated truck bodies. FRP plywood panels are used to construct the sides, roofs, and floors of truck trailers, as they offer significant resistance to moisture, impact, and wear. The lightweight properties help reduce the overall weight of the vehicle, allowing for higher payloads and better fuel efficiency. Additionally, FRP plywood provides a smooth, easy-to-clean surface that is essential for maintaining hygiene in refrigerated trailers, where cleanliness is critical.
Construction & Modular Buildings
Fiberglass reinforced plastic plywood is increasingly used in the construction of modular buildings and prefabricated structures. Due to its strength and resistance to environmental factors, FRP plywood is commonly employed for making modular walls, floors, and roofing panels. It offers a cost-effective and long-lasting solution for temporary and permanent buildings, such as offices, classrooms, and housing units. The material’s resistance to moisture and fire makes it especially suitable for use in regions with extreme weather conditions or in areas that require enhanced safety features. FRP plywood can also be used in combination with other materials like steel or concrete to further enhance the building’s structural integrity.
Marine Applications
In the marine industry, fiberglass reinforced plastic plywood is used extensively for applications exposed to moisture, such as boat decks, bulkheads, and other structural elements of vessels. The high moisture resistance and strength-to-weight ratio of FRP plywood make it an ideal material for marine environments where traditional plywood would degrade quickly due to water exposure. Boat manufacturers use FRP plywood for flooring and other components that require durability, low maintenance, and long-term performance. The material is also resistant to the corrosive effects of seawater, making it particularly useful in saltwater applications, such as yachts, ferries, and fishing boats.
Agricultural Structures
Fiberglass reinforced plastic plywood is widely used in agricultural settings for the construction of farm equipment, storage units, and barns. The material’s resistance to moisture, chemicals, and extreme weather conditions makes it ideal for agricultural environments where durability and easy maintenance are key concerns. In barns and storage units, FRP plywood can be used for walls, doors, and floors, providing long-lasting performance even in the face of high humidity and exposure to fertilizers, pesticides, and other harsh chemicals. Its strength and resistance to wear make it suitable for use in farm equipment like silos, feed bins, and livestock enclosures, ensuring that these structures remain functional and secure for many years.
Recreational Vehicles (RVs) & Transportation
Fiberglass reinforced plastic plywood is commonly used in the construction of recreational vehicles (RVs), including for the walls, roofs, and floors. FRP plywood provides a strong and weather-resistant material that can withstand the challenges of outdoor environments, including exposure to moisture, UV radiation, and temperature fluctuations. The lightweight properties of FRP plywood help reduce the overall weight of the RV, contributing to better fuel efficiency and easier maneuverability. Additionally, the material’s durability ensures that RVs can withstand the wear and tear of frequent use, maintaining their structural integrity and aesthetic appearance for extended periods. Similarly, FRP plywood is used in transportation vehicles like buses and trailers, where strength, moisture resistance, and low maintenance are crucial.
Additional Applications
- Transportation: FRP plywood is also used in various forms of transportation infrastructure, such as in truck liners, floor panels, and partition walls for commercial vehicles.
- Sustainable Building: The increasing demand for eco-friendly materials in construction has also seen FRP plywood being used in green building projects, where its durability and low maintenance requirements align with sustainability goals.
Overall, the broad range of applications for fiberglass reinforced plastic plywood highlights its exceptional versatility, durability, and performance in industries that require high-strength materials capable of withstanding harsh conditions. Whether for structural components in transportation, construction, or agriculture, FRP plywood provides a reliable and long-lasting solution.
Pole Barn Fiberglass Insulation: Key Benefits and Options
Types of Fiberglass Reinforced Plastic Plywood
Fiberglass reinforced plastic plywood (FRP plywood) is available in various types, each designed to meet specific application requirements. The combination of fiberglass and plywood can be tailored to provide different levels of durability, flexibility, and resistance to environmental factors. Understanding the different types of FRP plywood helps industries select the most suitable material for their needs, whether for construction, marine use, or transportation.
Thermoset FRP Plywood
Thermoset fiberglass reinforced plastic plywood is designed for applications where high durability and resistance to high temperatures are crucial. This type of FRP plywood is made by combining a thermosetting resin with the plywood core, and once the resin hardens, it cannot be re-melted. The result is a highly durable material that can withstand extreme temperatures, making it ideal for use in harsh environments. Thermoset FRP plywood is often used in applications such as industrial flooring, truck bodies, and construction panels, where it is exposed to heat and high stress. The material’s resistance to chemicals, wear, and impact further enhances its performance in tough environments, making it a popular choice for heavy-duty applications.
Thermoplastic FRP Plywood
Thermoplastic fiberglass reinforced plastic plywood is characterized by its flexibility and impact resistance, making it suitable for applications that require a certain degree of bendability without compromising strength. Unlike thermoset FRP plywood, thermoplastic plywood can be re-melted and reshaped, allowing for greater design flexibility. This type of FRP plywood is often used in applications where flexibility and impact resistance are critical, such as in the automotive, aerospace, and marine industries. The ability to mold and form the material into different shapes without affecting its core strength makes it ideal for creating custom components or products that require impact resistance while maintaining a lightweight profile. Its versatility allows it to be used in vehicle body panels, boat interiors, and other applications where flexibility and toughness are essential.
Custom FRP Plywood
Custom fiberglass reinforced plastic plywood provides tailored solutions to meet specific size, thickness, and performance requirements. This type of FRP plywood is often produced through CNC machining, which ensures high precision and consistency in the final product. Custom FRP plywood is available in a range of thicknesses, allowing for greater control over its strength, durability, and other properties. It is commonly used in specialized applications where standard plywood or generic FRP plywood does not meet the exact specifications needed. For instance, custom FRP plywood is used for creating specialized panels in modular buildings, custom flooring in transportation vehicles, and bespoke structural components in marine construction. The ability to create FRP plywood to specific dimensions and strength levels ensures that it meets the unique demands of various industries.
Additional Types of FRP Plywood
In addition to thermoset, thermoplastic, and custom FRP plywood, there are other variations designed for specific uses, such as:
- Decorative FRP Plywood: This version of FRP plywood features an aesthetic surface that can be used in furniture, cabinetry, and interior finishes. The fiberglass surface is often designed with a glossy or textured finish, making it both functional and visually appealing.
- Fire-Retardant FRP Plywood: This specialized plywood is treated with fire-resistant chemicals, making it ideal for applications that require enhanced safety against fire hazards, such as in public buildings, transportation, and hazardous environments.
The different types of fiberglass reinforced plastic plywood provide a range of solutions for industries that require high-performance materials with specific properties. Whether you need the high-temperature resistance of thermoset FRP plywood, the flexibility of thermoplastic versions, or the precision and customization options offered by custom FRP plywood, there is a product to meet your specific needs. Each type of FRP plywood combines the strength of plywood with the durability and resistance of fiberglass, making it a versatile material for a wide range of demanding applications.
Manufacturing Process of Fiberglass Reinforced Plastic Plywood
The manufacturing process of fiberglass reinforced plastic plywood (FRP plywood) involves several stages that combine the strength of plywood with the durability of fiberglass and resin. The result is a high-performance material used in a wide range of industries, from construction to transportation. The process must ensure that the fiberglass reinforcement is seamlessly integrated into the plywood layers, providing enhanced strength, moisture resistance, and durability.
Step-by-Step Process
The manufacturing of fiberglass reinforced plastic plywood follows a carefully controlled process that combines plywood with fiberglass and resin to create a robust composite material. Below are the key steps involved in the production process:
- Preparation of Plywood Core: The plywood core, made from different wood types like birch, pine, or eucalyptus, is first prepared by cutting it into the required size and shape. The plywood is treated to enhance its moisture and fire resistance properties, ensuring it can withstand challenging environments.
- Layering with Fiberglass: The plywood core is then coated with fiberglass layers. The fiberglass cloth or mat is applied to the surface of the plywood, either manually or through automated systems. The fiberglass used can vary in terms of thickness and type, depending on the desired strength and performance.
- Resin Application: Once the fiberglass is in place, a resin (usually polyester, epoxy, or vinyl ester) is applied to bond the fiberglass to the plywood. The resin serves as the adhesive that holds the layers together and contributes to the strength and moisture resistance of the final product. This is typically done through methods such as vacuum infusion or hand lay-up techniques, where the resin is spread evenly across the fiberglass surface.
- Curing and Hardening: After the resin is applied, the composite material undergoes a curing process. This step allows the resin to harden and bond firmly with the fiberglass and plywood. Curing can take place in an oven or at room temperature, depending on the type of resin used. The curing process ensures that the fiberglass reinforced plastic plywood reaches its maximum strength and durability.
- Finishing: Once the material is cured, any excess resin is trimmed, and the surface is smoothed. The FRP plywood may also undergo additional treatments such as UV coating to improve weather resistance or enhance its aesthetic appearance. This final finishing ensures that the material is both functional and visually appealing.
Customization
Fiberglass reinforced plastic plywood can be customized to meet the specific requirements of different applications. Customization involves adjusting the size, thickness, and even the type of resin and fiberglass used in the manufacturing process. Advanced technologies like CNC (Computer Numerical Control) machining are often employed to precisely cut and shape the plywood to exact dimensions.
This level of customization is crucial in industries where specific performance characteristics are required, such as in the construction of modular buildings, truck bodies, or marine vessels. Custom FRP plywood can be produced in various thicknesses to meet strength requirements and tailored to fit the specific environmental challenges of a given project, such as exposure to moisture, UV radiation, or chemicals.
Quality Control
To ensure that fiberglass reinforced plastic plywood consistently meets industry standards and performs as expected, quality control is an essential part of the manufacturing process. Several rigorous testing and inspection procedures are carried out at various stages of production to verify the material’s strength, waterproofing capabilities, and surface finish.
- Strength Testing: FRP plywood undergoes mechanical testing to ensure it meets the required tensile and impact strength. This is critical for ensuring that the material can withstand the stresses it will face in real-world applications, such as in the construction of truck bodies or marine structures.
- Waterproofing Testing: Moisture resistance is a key characteristic of fiberglass reinforced plastic plywood. Samples of the material are subjected to water immersion tests to verify that they will not absorb moisture and weaken over time. This is especially important for applications in marine environments or industries where water exposure is common.
- Finish Quality: The final appearance and smoothness of the FRP plywood surface are also tested. The material’s aesthetic qualities, such as its gloss or matte finish, are examined to ensure they meet customer expectations, especially for uses in furniture or decorative applications.
By maintaining strict quality control standards throughout the manufacturing process, manufacturers ensure that fiberglass reinforced plastic plywood is consistent, reliable, and capable of performing in demanding environments.
The manufacturing process of fiberglass reinforced plastic plywood involves the careful layering of plywood with fiberglass and resin, followed by curing and finishing processes that result in a durable, high-performance material. Customization options allow for tailored sizes and properties to meet specific application requirements, while rigorous quality control ensures that the finished product delivers consistent performance and reliability. The careful integration of these elements makes FRP plywood a highly versatile material suitable for a range of industries, from construction to transportation.
FAQs about Fiberglass Reinforced Plastic Plywood
Fiberglass reinforced plastic (FRP) tends to be more expensive than other traditional materials due to several factors. First, the raw materials required for FRP production, such as fiberglass fibers and resin, can be costly. Fiberglass itself is made through a labor-intensive process that requires high temperatures to manufacture, which adds to the overall cost of production. The resin used to bind the fiberglass fibers also contributes to the expense, especially if higher-quality or specialized resins are used for specific applications, such as marine or aerospace uses. Second, the manufacturing process for FRP is more complex compared to simpler materials like wood or metal. Creating FRP involves layering fiberglass with resin, curing it under heat, and sometimes adding additional coatings or treatments for durability and UV resistance. This intricate process can increase both time and labor costs. Lastly, FRP’s superior properties, such as strength, corrosion resistance, and long-lasting durability, contribute to its higher price. Although the initial investment is higher, the long-term benefits, including minimal maintenance and extended lifespan, can make FRP a cost-effective choice for certain applications.
While fiberglass reinforced plastic (FRP) offers several advantages, including high strength, durability, and resistance to corrosion and chemicals, there are a few disadvantages to consider. One significant drawback is its relatively high cost compared to traditional materials like wood, plastic, or metal. The manufacturing process for FRP can be complex, involving multiple steps, which increases both production time and costs. Additionally, FRP can be brittle and prone to cracking or chipping if subjected to impact or sharp stress, especially when it is used in thin layers. The material is also not easily recyclable, which raises environmental concerns. Disposal of FRP materials can contribute to waste in landfills unless specifically managed through specialized recycling processes. Furthermore, while FRP is resistant to moisture, it is not immune to prolonged exposure to UV radiation, which can degrade the material over time, especially if the surface coating is not maintained. Proper care and maintenance are required to ensure its longevity.
Yes, you can apply FRP (fiberglass reinforced plastic) to plywood, and it is a common practice in many industries to create fiberglass reinforced plywood (FRP plywood). The process typically involves bonding a layer of FRP, which may consist of fiberglass mat or woven roving, to the surface of plywood using a strong adhesive or resin. This layer provides additional strength, durability, and resistance to environmental factors like moisture, corrosion, and abrasion. The FRP layer can be applied on both sides of the plywood or just on one side, depending on the specific application. This composite material is commonly used in truck bodies, construction, marine applications, and modular buildings, where the enhanced properties of both plywood and fiberglass are beneficial. However, proper preparation and bonding techniques must be followed to ensure the integrity and longevity of the bond between the plywood and FRP layer.
Fiberglass reinforced plywood (FRP plywood) is a composite material that combines the durability and strength of traditional plywood with the added benefits of fiberglass. It typically consists of a plywood core, such as birch, pine, or poplar, which is coated with a layer of fiberglass reinforced plastic (FRP) on both sides. The FRP layer is typically made from a combination of resin and fiberglass fibers, which provides enhanced strength, corrosion resistance, and durability. This combination creates a lightweight yet strong material ideal for a wide range of applications in industries like construction, marine, agriculture, and transportation. The surface of the FRP plywood is often gel-coated, offering added UV protection and weather resistance. Fiberglass reinforced plywood is known for its superior resistance to moisture, chemicals, and wear, making it a popular choice for environments exposed to harsh conditions.
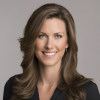
As the editor of GangLong Fiberglass, I have years of experience and in-depth research, focusing on cable tray products, fiberglass solutions, and grille systems. I incorporate years of industry insights and practical experience into every content, committed to promoting the progress of the industry. At GangLong Fiberglass, my commitment is reflected in every product, from innovative cable trays to durable fiberglass solutions and sturdy grille systems. As an authoritative voice in the industry, my goal is to provide valuable information to professionals and businesses and promote forward-looking solutions.