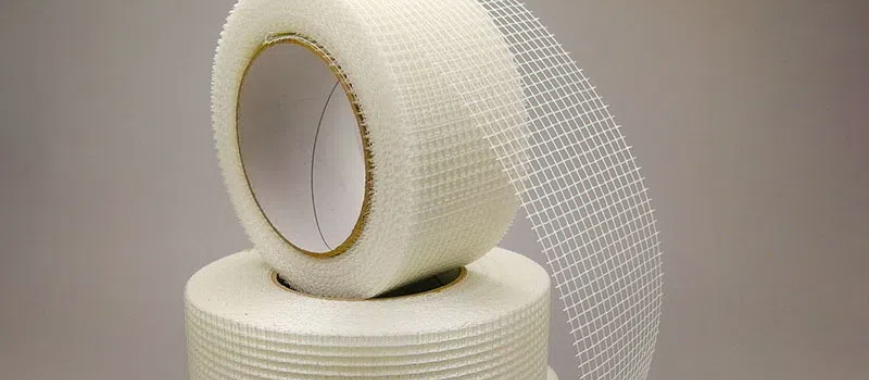
Fiberglass reinforced plastic pressure vessels (FRP pressure vessels) are composite structures made by combining fiberglass with resin. This combination results in a strong, durable, and corrosion-resistant vessel that is ideal for containing pressurized substances. The fiberglass provides excellent tensile strength, while the resin binds the fibers together and enhances the material’s resistance to chemicals and environmental factors. The key benefits of FRP pressure vessels include their lightweight nature, which offers a significant advantage in transportation and installation. Additionally, they have a high strength-to-weight ratio, making them ideal for applications that require both durability and reduced weight. These vessels are also cost-effective, especially in industries such as water treatment, oil & gas, chemical processing, and food-grade storage, where reliability and resistance to corrosion are crucial.
Types of Fiberglass Reinforced Plastic Pressure Vessels
Fiberglass reinforced plastic pressure vessels (FRP pressure vessels) are manufactured for a wide range of applications, leveraging their strength, corrosion resistance, and lightweight properties. Depending on the industry and the specific requirements, different types of FRP pressure vessels are used. Below are two key types of FRP pressure vessels and their applications.
FRP Vessels for Water Treatment
Fiberglass reinforced plastic pressure vessels are an ideal choice for water treatment applications. The primary reason for this is the material’s exceptional corrosion resistance. Water treatment plants often deal with highly corrosive environments due to the use of various chemicals and water with varying levels of salinity or pollutants. FRP pressure vessels are resistant to rust, ensuring a longer lifespan and reducing the need for frequent maintenance or replacement.
Additionally, the strength of FRP pressure vessels allows them to withstand high internal pressures, a critical feature in water filtration systems. These vessels are also lightweight, which simplifies installation and reduces transportation costs. The low maintenance requirements of FRP vessels make them a cost-effective solution for water treatment facilities, where reliability and efficiency are essential.
FRP Vessels for Chemical Processing
In the chemical processing industry, fiberglass reinforced plastic pressure vessels are indispensable due to their ability to handle harsh chemicals and extreme environmental conditions. These vessels are designed to withstand exposure to corrosive substances such as acids, alkalis, and solvents, making them suitable for applications like chemical filtration, storage, and mixing.
The inherent chemical resistance of FRP pressure vessels ensures that they do not degrade or corrode when exposed to aggressive chemicals, offering a much longer service life compared to traditional metal vessels. Furthermore, the customization options for FRP vessels allow them to be designed with features that meet the specific needs of chemical processes, including various shapes, sizes, and pressure ratings. This makes FRP vessels highly versatile for a wide range of chemical processing applications.
By choosing fiberglass reinforced plastic pressure vessels, industries can optimize their operations while reducing downtime and maintenance costs, making FRP a popular material in both water treatment and chemical processing sectors.
Pole Barn Fiberglass Insulation: Key Benefits and Options
Specifications and Features of Fiberglass Reinforced Plastic Pressure Vessels
Fiberglass reinforced plastic pressure vessels (FRP pressure vessels) offer a wide range of specifications and features designed to meet the rigorous demands of various industries. These vessels are engineered to ensure high performance, durability, and versatility in applications such as water treatment, chemical processing, and oil storage.
Material Composition
The construction of fiberglass reinforced plastic pressure vessels typically involves a composite material made from high-quality fiberglass and resin. The fiberglass fibers provide strength and flexibility, while the resin acts as a binding agent, giving the vessel its structural integrity. In some cases, additional materials like carbon or aramid fibers are incorporated into the construction to further enhance the strength and durability of the vessel, especially when exposed to extreme conditions or high pressures. This composite structure allows the vessels to remain lightweight yet strong, making them ideal for environments where both durability and ease of handling are important.
Key Specifications
Fiberglass reinforced plastic pressure vessels come with specific pressure ratings that ensure their suitability for a range of applications. A typical pressure rating for these vessels is around 150 PSI (pounds per square inch), but some specialized vessels can handle even higher pressures, depending on the material composition and intended use.
The size of FRP pressure vessels can vary significantly, with standard diameters and heights available to suit different applications. For example, the Pentair FRP Vessel Size Chart includes models such as FRP-12×48 and FRP-18×65, which refer to vessels with specific diameters and lengths. These standard sizes ensure that the vessels can be easily integrated into existing systems, providing flexibility for manufacturers and users alike. Custom sizes can also be manufactured to meet particular requirements for space and application needs.
Additional Features
FRP pressure vessels are often equipped with additional features to enhance their functionality and meet industry standards. Many vessels come with NSF/ANSI certifications, which are essential for applications involving food-grade products. These certifications ensure that the vessels meet safety and quality standards for storing and processing food-related materials, making them ideal for the food and beverage industry.
Furthermore, FRP pressure vessels can be designed with multiple inlet and outlet configurations, allowing for flexible installation in various systems. This feature is particularly important for complex filtration or chemical processes where specific flow patterns are required. Additionally, the ability to customize the sizes, fittings, and pressure ratings of FRP pressure vessels makes them highly adaptable to the specific needs of industries such as water treatment, oil & gas, and chemical processing.
By incorporating these features, fiberglass reinforced plastic pressure vessels provide a reliable, long-lasting solution that meets the demands of both commercial and industrial applications.
Fiberglass Cloth Insulation: Benefits for Walls and Clothing
What is the FRP Vessel Size Chart for Fiberglass Reinforced Plastic Pressure Vessels
The FRP vessel size chart is a critical tool for selecting the appropriate fiberglass reinforced plastic pressure vessels for various applications. Understanding how to interpret this chart ensures that the right vessel is chosen based on the system’s specific requirements. From water treatment to chemical processing, choosing the right size and configuration of FRP vessels is essential to maximize performance and efficiency.
Overview of Size Chart for Different Applications
The FRP vessel size chart typically includes different model numbers, such as FRP-12×48, FRP-24×72, and other size variants, which refer to the vessel’s diameter and height, respectively. For instance, the “12” in FRP-12×48 indicates the diameter of the vessel (12 inches), and the “48” represents the height of the vessel (48 inches). These dimensions are important because they directly influence the vessel’s capacity, allowing users to match the vessel size to the specific requirements of the system.
When choosing a fiberglass reinforced plastic pressure vessel, it’s essential to align the vessel size with the intended application. For example, smaller vessels such as FRP-12×48 may be suitable for residential water filtration systems, while larger vessels like FRP-24×72 are more appropriate for industrial or commercial water treatment applications that require a larger flow rate and storage capacity. The size chart helps determine which vessel is best for handling the desired flow rate, volume, and space constraints of a given installation.
Key Parameters to Consider
When selecting the appropriate FRP vessel using the size chart, several key parameters must be considered to ensure optimal performance:
- Flow Rate (GPM): The flow rate, measured in gallons per minute (GPM), is a critical factor in selecting the right size of FRP pressure vessel. Different vessels can handle different flow rates, so it’s important to ensure the vessel can accommodate the required flow for the intended system, whether it’s for water treatment, chemical filtration, or other industrial uses.
- Tank Volume (Gallons): The volume of the vessel, often measured in gallons, is directly related to its size and capacity. Larger vessels can hold more liquid, making them ideal for applications that require extended storage or higher volumes, such as in industrial or large-scale water treatment plants.
- Inlet/Outlet Sizes: The size of the inlet and outlet connections must match the system’s piping configuration. The FRP vessel size chart will provide these dimensions, ensuring compatibility with existing plumbing and minimizing the risk of installation issues.
- Operating Pressure: The operating pressure refers to the maximum pressure the vessel is designed to handle safely during operation. This specification is crucial in ensuring that the vessel can withstand the conditions of the application, particularly in industries like chemical processing or oil & gas, where high-pressure environments are common.
By carefully considering these parameters, users can select the most suitable fiberglass reinforced plastic pressure vessel for their needs, ensuring maximum efficiency, longevity, and safety in their operations.
Best Fiberglass Insulation 2×4 Walls Explained
Manufacturing and Construction of Fiberglass Reinforced Plastic Pressure Vessels
The manufacturing process of fiberglass reinforced plastic pressure vessels (FRP pressure vessels) involves advanced techniques that ensure strength, durability, and high resistance to environmental factors. These vessels are primarily used in industries that require robust and reliable containment solutions, such as water treatment, oil and gas, and chemical processing. The construction methods employed are designed to optimize the mechanical properties of the fiberglass and resin composite while addressing the specific challenges posed by the intended applications.
Filament Winding Process
One of the primary construction methods for fiberglass reinforced plastic pressure vessels is the filament winding process. In this technique, continuous strands of fiberglass are wound around a cylindrical mandrel in a precise pattern. The process is highly automated and ensures uniform thickness and optimal strength distribution throughout the vessel. The fiberglass strands are typically impregnated with resin during the winding process to bond the fibers together and create a solid composite material.
The filament winding process is particularly effective for producing large, pressure-resistant vessels as it allows for precise control over the orientation of the fibers, resulting in a vessel that can withstand high internal pressures without failing. The ability to apply multiple layers of fiberglass in various directions creates a vessel with superior mechanical properties, including resistance to external stresses such as impact and vibration.
Corrosion Resistance and Durability
Fiberglass reinforced plastic pressure vessels offer several key advantages over traditional metal vessels, especially when it comes to corrosion resistance and durability. The fiberglass composite material is inherently resistant to the corrosion that typically affects metal vessels, particularly when exposed to harsh chemicals, high humidity, or saline environments.
In contrast to steel or aluminum, which can corrode over time when exposed to water or corrosive substances, fiberglass does not degrade under such conditions. This makes fiberglass reinforced plastic pressure vessels ideal for use in water treatment, chemical processing, and marine applications, where corrosion resistance is critical for ensuring the vessel’s longevity and performance.
Some of the key advantages of using fiberglass for pressure vessels include:
- Corrosion resistance: Fiberglass reinforced plastic pressure vessels resist degradation from chemicals, seawater, and other corrosive elements.
- Longevity: The durability of fiberglass makes these vessels last longer, reducing the need for frequent maintenance or replacement.
- Lower maintenance costs: Due to their corrosion resistance, these vessels require less maintenance and are less prone to structural failure.
Pressure and Temperature Resistance
Fiberglass reinforced plastic pressure vessels are designed to handle a range of operating conditions, including high pressures and varying temperatures. These vessels typically have a maximum pressure rating of 10 bar (150 psi), which is sufficient for most industrial applications, such as water filtration, chemical storage, and even some high-pressure chemical processes.
FRP vessels maintain their structural integrity under pressure, thanks to the strength provided by the fiberglass reinforcement and the resin matrix. Furthermore, these vessels are resistant to extreme temperature variations, maintaining their functionality even in both high-temperature and low-temperature environments. This makes fiberglass reinforced plastic pressure vessels suitable for applications where temperature control is critical, such as in oil and gas or food-grade storage systems.
Key benefits of the pressure and temperature resistance of FRP pressure vessels include:
- High pressure tolerance: FRP vessels can withstand substantial internal pressure, making them suitable for a wide range of industrial applications.
- Thermal stability: The composite material can handle temperature fluctuations without significant degradation or failure.
- Safety: The ability to handle high pressure and temperature ensures these vessels are safe for use in critical applications.
Overall, the advanced construction and manufacturing methods used to produce fiberglass reinforced plastic pressure vessels ensure that they meet the high standards of strength, durability, and resistance needed for demanding industrial environments.
Maintenance and Servicing of Fiberglass Reinforced Plastic Pressure Vessels
Proper maintenance and servicing of fiberglass reinforced plastic pressure vessels (FRP pressure vessels) are crucial to ensure their continued performance, longevity, and reliability, especially in critical applications such as water treatment, chemical processing, and industrial storage. With the right care and attention, these vessels can provide many years of service without the need for frequent replacements, making them a cost-effective solution for various industries.
Maintenance Requirements
Fiberglass reinforced plastic pressure vessels require regular maintenance to function optimally. While FRP vessels are highly durable, routine inspections and care help identify any potential issues early and maintain peak performance. Key maintenance activities include:
- Periodic Inspections: Regular visual inspections are essential to check for signs of wear, cracks, or damage caused by environmental factors or excessive pressure. It’s important to assess the vessel for any surface cracks, discoloration, or weakening of the fiberglass laminate that may indicate stress or damage.
- Cleaning and Backwashing: For water treatment applications, regular cleaning is necessary to remove any accumulated debris or contaminants that could affect performance. This may involve backwashing to flush out particles and ensure efficient filtration. In industrial filtration settings, periodic backwashing helps maintain optimal flow rates and filtration efficiency.
- Carbon Replacement: If the FRP pressure vessel is part of a filtration system using activated carbon, replacing the carbon periodically is essential. Over time, the carbon loses its adsorptive capacity, requiring replenishment to maintain the vessel’s filtration efficiency.
Regular maintenance ensures that fiberglass reinforced plastic pressure vessels continue to meet the required standards of strength, performance, and resistance to environmental factors.
Handling and Installation
One of the key benefits of fiberglass reinforced plastic pressure vessels is their lightweight nature, which makes installation and handling much easier compared to traditional metal vessels. However, proper care during installation and handling is essential to avoid any damage that could compromise the vessel’s performance.
- Easy Installation: Due to their relatively low weight, FRP pressure vessels are easier to transport and install, reducing installation time and costs. They can be handled with standard equipment, and often require less manpower to position and install than heavier metal counterparts.
- Proper Handling Techniques: While lightweight, fiberglass vessels are still susceptible to damage from improper handling. It’s important to follow recommended handling guidelines to avoid scratches, cracks, or stress points that could weaken the vessel. For instance, using lifting straps and padding during transport can prevent unnecessary impacts that may lead to damage during installation.
Following proper handling and installation procedures ensures that fiberglass reinforced plastic pressure vessels are set up correctly and can function efficiently for their expected lifespan.
Long-Term Benefits
Fiberglass reinforced plastic pressure vessels provide long-term benefits when properly maintained. Regular servicing and handling practices contribute to:
- Increased Longevity: FRP pressure vessels are designed to withstand harsh environmental conditions, and their durability is enhanced when subjected to routine maintenance and care. By preventing premature damage, these vessels can last for decades in most industrial applications.
- Cost Savings: Regular maintenance reduces the risk of costly repairs or replacements. With proper care, the need for major repairs is minimized, making these vessels a cost-effective investment over time. Additionally, their resistance to corrosion and reduced maintenance requirements further lower the total cost of ownership.
- Consistent Performance: Proper upkeep ensures that FRP pressure vessels continue to perform at peak efficiency, minimizing downtime and disruptions in industrial processes. Maintaining the vessels’ strength, structural integrity, and operational efficiency contributes to optimal performance throughout their service life.
The maintenance and servicing of fiberglass reinforced plastic pressure vessels are essential to maximizing their lifespan and performance. Routine inspections, cleaning, and proper handling can significantly extend the life of the vessel and contribute to long-term cost savings and reliable operation.
FAQs about Fiberglass Reinforced Plastic Pressure Vessels
Fiberglass reinforced plastic (FRP) pressure vessels are widely used in various industries, primarily for their strength, durability, and resistance to corrosion. These vessels are typically utilized in applications involving pressurized fluids or gases, where their ability to withstand high pressure is crucial. Common uses of FRP pressure vessels include water treatment, where they house filtration media or contain pressurized water; in the oil and gas industry, where they store or transport pressurized fluids; and in chemical processing for the safe containment of chemicals under pressure. Their lightweight nature also makes them ideal for applications where weight is a concern, such as in offshore platforms and remote locations. FRP vessels are also used in food-grade storage, due to their ability to resist corrosion and contamination. These vessels offer superior strength-to-weight ratios and are resistant to environmental factors such as UV exposure, making them suitable for both indoor and outdoor applications.
Fiberglass reinforced plastic (FRP) is a versatile composite material that combines fiberglass with plastic resin to create a lightweight, durable, and corrosion-resistant material. FRP is used in a variety of industries due to its exceptional properties. It is commonly employed in the manufacturing of pressure vessels, as it offers high strength, chemical resistance, and the ability to withstand high pressures. In the construction industry, FRP is used for structural applications like building panels, roofing, and flooring because of its durability and low maintenance needs. The automotive industry also makes use of FRP for lightweight vehicle parts, contributing to fuel efficiency and performance. Additionally, FRP is used in boat building, pipes for chemical transport, and even in the aerospace industry. The versatility of fiberglass reinforced plastic makes it an ideal material in environments where weight, strength, and resistance to corrosion are key factors.
The pressure rating of FRP pressure vessels typically ranges from 150 PSI to 300 PSI, depending on the design and intended application. However, the pressure rating can vary significantly depending on the specific materials used, such as the type of resin, the number of fiberglass layers, and the construction method. Some specialized FRP pressure vessels, designed for higher pressures, can handle up to 10 bar (approximately 150 PSI), while others may be designed for even more demanding conditions. It’s important to consider the operational environment, including temperature and chemical exposure, when selecting an FRP vessel, as these factors can affect the pressure rating. When designing or purchasing FRP pressure vessels, always ensure that the specified pressure rating meets the requirements of the particular application to ensure safety and efficiency. Additionally, certifications and standards, such as those set by the American Society of Mechanical Engineers (ASME), help ensure that these vessels meet rigorous safety and performance criteria.
The American Society of Mechanical Engineers (ASME) standard for FRP tanks refers to the ASME RTP-1 (Reinforced Thermoset Plastic Corrosion-Resistant Equipment) standard. This standard governs the design, construction, and inspection of FRP pressure vessels and tanks, ensuring they meet rigorous quality and safety requirements. The ASME RTP-1 standard provides guidelines for determining the appropriate materials, design calculations, and testing procedures needed for safe and reliable operation. These include specifications for wall thickness, reinforcement, and stress analysis to prevent failure under pressure. The ASME certification is important in industries like water treatment, oil and gas, and chemical processing, where FRP pressure vessels are exposed to high pressures and potentially hazardous substances. Compliance with ASME standards ensures that the vessels meet industry-recognized safety, durability, and performance benchmarks. Manufacturers of FRP pressure vessels typically undergo inspections and certification processes to ensure compliance with these standards before the vessels are put into use.
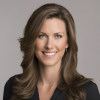
As the editor of GangLong Fiberglass, I have years of experience and in-depth research, focusing on cable tray products, fiberglass solutions, and grille systems. I incorporate years of industry insights and practical experience into every content, committed to promoting the progress of the industry. At GangLong Fiberglass, my commitment is reflected in every product, from innovative cable trays to durable fiberglass solutions and sturdy grille systems. As an authoritative voice in the industry, my goal is to provide valuable information to professionals and businesses and promote forward-looking solutions.