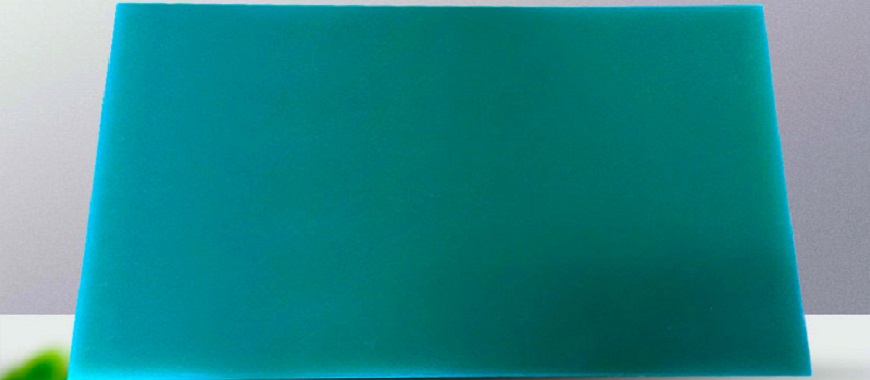
Fiberglass-reinforced plastic stacs (FRP stacks) have become a crucial component in various industrial applications, offering significant advantages over traditional materials like steel. These FRP stacks are increasingly replacing steel stacks due to their lightweight nature, corrosion resistance, and mechanical strength. In industries such as power generation, chemical processing, and waste management, fiberglass-reinforced plastic stacks are vital in withstanding harsh environments where steel would typically corrode or degrade. The lightweight nature of FRP allows for easier transportation and installation, while its corrosion resistance ensures a longer service life in aggressive atmospheres. Additionally, the mechanical strength of fiberglass-reinforced plastic stacks provides the durability necessary for handling high-pressure and high-temperature conditions, making them a reliable choice for modern industrial facilities.
What Are Fiberglass-Reinforced Plastic Stacs?
Fiberglass-reinforced plastic stacs are specialized structures commonly used in industrial exhaust systems and chimneys. These stacks are made by combining fiberglass with resin, creating a composite material that provides superior durability, corrosion resistance, and strength. This unique composition allows fiberglass-reinforced plastic stacs to perform well in harsh conditions, making them a preferred choice in industries that involve high temperatures, chemicals, and demanding environments.
Definition and Composition of Fiberglass-Reinforced Plastic Stacs
Fiberglass-reinforced plastic stacs are essentially tall, cylindrical or tubular structures designed to carry exhaust gases away from industrial facilities. The material used in these stacks consists of fiberglass, which is a woven fabric of glass fibers, combined with a resin matrix. This composite material is then formed into the desired shape to create a robust stack that can withstand various environmental factors. The fiberglass reinforcement helps improve the strength of the stack, while the resin component provides flexibility and resistance to corrosion.
The resin used in these stacks can vary depending on the specific requirements of the application. Common resins include polyester, vinyl ester, and epoxy, each offering different levels of chemical resistance, temperature tolerance, and mechanical strength. By adjusting the composition, manufacturers can customize the fiberglass-reinforced plastic stacks for specific industrial needs.
Description of Their Use in Industrial Exhaust Systems and Chimneys
Fiberglass-reinforced plastic stacs are widely used in industrial exhaust systems, especially in industries like power generation, chemical processing, and manufacturing. These stacks are responsible for venting exhaust gases from combustion processes, boilers, or other industrial equipment to the atmosphere, minimizing the environmental impact of pollutants.
Because fiberglass-reinforced plastic stacks are resistant to corrosion, they are particularly valuable in industries where corrosive gases are generated. For example, in the chemical industry, stacks may need to handle exhaust gases containing acids, bases, or other reactive chemicals. Fiberglass-reinforced plastic is highly resistant to chemical degradation, making it ideal for such applications.
In addition to their use in industrial exhaust systems, fiberglass-reinforced plastic stacks are also used in chimneys for residential or commercial buildings. Their lightweight nature and corrosion-resistant properties make them an excellent choice for venting systems that must endure the elements over time.
Key Characteristics That Make Them Suitable for Demanding Environments
Fiberglass-reinforced plastic stacs stand out due to several key characteristics that make them ideal for use in demanding environments:
- Corrosion Resistance: One of the most important features of fiberglass-reinforced plastic stacs is their resistance to corrosion. Unlike metal stacks, which can rust when exposed to moisture and chemicals, fiberglass-reinforced plastic does not corrode, even when exposed to harsh substances like sulfuric acid or chlorine.
- High Temperature Tolerance: These stacks can withstand high temperatures, making them suitable for industrial applications that involve hot gases. The resin and fiberglass used in the construction of the stacks are designed to resist heat degradation, ensuring long-term performance even under extreme conditions.
- Lightweight: Fiberglass-reinforced plastic stacks are much lighter than traditional metal stacks, making them easier to transport, handle, and install. Their lightweight nature also reduces the structural load on buildings and supports, which can lead to cost savings in construction and maintenance.
- Durability and Longevity: The durability of fiberglass-reinforced plastic stacs is another critical factor. These stacks are designed to last for many years with minimal maintenance, providing an excellent return on investment in industrial settings where reliability is essential.
- Customizability: As mentioned earlier, fiberglass-reinforced plastic stacks can be tailored to meet the specific requirements of a given application. The resin composition can be adjusted for varying levels of chemical resistance, and the design can be modified to accommodate different environmental factors.
Fiberglass-reinforced plastic stacks offer a combination of durability, corrosion resistance, and heat tolerance, making them the ideal choice for industrial exhaust systems and chimneys exposed to challenging conditions. Their unique composition and versatile characteristics ensure that they continue to be an integral part of many industries worldwide.
Why Shallow Fiberglass Tubs Are Perfect for Small Bathrooms
Applications of Fiberglass-Reinforced Plastic Stacs
Fiberglass-reinforced plastic stacs have a broad range of applications due to their durability, corrosion resistance, and ability to withstand extreme conditions. These properties make them particularly valuable in industries where exhaust gases need to be safely vented while minimizing environmental impact. From power generation to wastewater treatment, fiberglass-reinforced plastic stacks play a critical role in managing emissions across various sectors.
Power Generation: Coal-Fired Power Plants and Gas Exhaust Systems
One of the most common applications of fiberglass-reinforced plastic stacks is in power generation, particularly in coal-fired power plants and gas exhaust systems. These plants generate large quantities of exhaust gases, which need to be safely channeled out of the facility to prevent environmental contamination and ensure air quality. Fiberglass-reinforced plastic stacks provide a reliable solution for this critical task.
In coal-fired power plants, exhaust gases often contain sulfur dioxide (SO2), nitrogen oxides (NOx), and particulate matter, all of which can be harmful to the environment. Fiberglass-reinforced plastic stacs are resistant to the corrosive effects of these gases, offering long-lasting performance even under extreme conditions. Additionally, these stacks are capable of withstanding high temperatures that are typically produced during combustion processes. Their lightweight nature also helps reduce the load on plant infrastructure, making installation and maintenance easier.
In gas exhaust systems, whether in natural gas plants or oil refineries, fiberglass-reinforced plastic stacks are used to vent emissions such as carbon dioxide (CO2) and volatile organic compounds (VOCs). The ability of these stacks to endure both high temperatures and chemical exposure makes them a preferred material for managing emissions in the power generation industry.
Chemical Industry: Handling Corrosive Chemical Emissions
The chemical industry produces a wide range of emissions, many of which are highly corrosive and require specialized equipment to manage them safely. Fiberglass-reinforced plastic stacs are particularly well-suited for this purpose, offering exceptional resistance to corrosion from chemicals such as acids, bases, solvents, and chlorine.
In chemical plants, exhaust gases may contain hazardous substances like hydrochloric acid (HCl), sulfuric acid (H2SO4), or ammonia (NH3). Traditional metal stacks may corrode when exposed to these substances, leading to premature failure and increased maintenance costs. However, fiberglass-reinforced plastic stacks are designed to withstand this chemical exposure, ensuring long-term performance and reducing the risk of leaks or other safety issues.
Fiberglass-reinforced plastic stacks are also beneficial in environments where highly reactive gases are present. For example, in chlor-alkali plants, where chlorine gas is produced, fiberglass stacks can safely manage the venting of chlorine without the risk of corrosion or degradation over time. Their resilience against such harsh chemicals makes them an essential component in maintaining safe and efficient operations within the chemical industry.
Pulp and Paper Mills: Stack Liners for Managing Byproduct Emissions
In pulp and paper mills, fiberglass-reinforced plastic stacks are commonly used as liners to manage the byproduct emissions generated during the manufacturing process. The pulp and paper industry involves the use of chemicals like chlorine dioxide, hydrogen peroxide, and other bleaching agents, which can release harmful gases during production.
Fiberglass-reinforced plastic stacks are ideal for these applications due to their ability to resist the corrosive effects of the chemicals used in pulp processing. These stacks are employed to handle the exhaust gases that are produced during the pulping and bleaching stages. The stack liners provide a protective barrier that ensures the gases are vented safely without causing damage to the equipment.
Moreover, the chemical resistance and heat tolerance of fiberglass-reinforced plastic stacs ensure that the emissions, which are often hot and chemically reactive, can be safely transported away from the mill without compromising the integrity of the stack. This makes them an essential component in ensuring environmental compliance and worker safety in the pulp and paper industry.
Water Treatment: Odor Control and Exhaust Stacks in Wastewater Facilities
Fiberglass-reinforced plastic stacks also have important applications in water treatment, particularly in wastewater treatment plants. These plants handle large volumes of wastewater that can generate unpleasant odors and harmful gases, including hydrogen sulfide (H2S), methane (CH4), and ammonia (NH3).
To prevent these gases from being released into the environment, fiberglass-reinforced plastic stacks are used to vent the emissions safely. The corrosion-resistant nature of fiberglass-reinforced plastic ensures that the stacks will not degrade when exposed to the acidic and sometimes toxic gases found in wastewater systems. Additionally, the stacks are capable of handling the high moisture levels and fluctuating temperatures typical of wastewater treatment facilities.
Another key application in water treatment is odor control. Fiberglass-reinforced plastic stacs can be equipped with specialized scrubbers or filters to capture and neutralize odorous compounds before they are vented into the atmosphere. This helps improve air quality and ensures compliance with environmental regulations, which is especially important for treatment plants located near residential or commercial areas.
Fiberglass-reinforced plastic stacks play a vital role in various industries, from power generation and chemical processing to pulp and paper mills and wastewater treatment. Their ability to withstand high temperatures, corrosive chemicals, and extreme environmental conditions makes them an essential component in managing emissions and ensuring environmental and operational safety.
Skirted Fiberglass Tub: Affordable, Easy to Install, and Durable
Advantages of Fiberglass-Reinforced Plastic Stacs
Fiberglass-reinforced plastic stacks offer numerous advantages that make them an ideal choice for a wide range of industrial applications. Their unique composition, which combines fiberglass with resin, allows these stacks to perform exceptionally well in harsh environments where traditional materials may fail. The key advantages of fiberglass-reinforced plastic stacks make them a preferred option in industries such as power generation, chemical processing, and wastewater treatment.
Corrosion Resistance: Protection Against Harsh Chemical and Environmental Exposure
One of the standout advantages of fiberglass-reinforced plastic stacs is their exceptional corrosion resistance. Unlike metal stacks that are prone to rust and degradation when exposed to moisture or aggressive chemicals, fiberglass-reinforced plastic stacs remain unaffected by corrosive substances. In industries where exhaust gases contain acids, bases, or other reactive chemicals, these stacks provide reliable protection and ensure the safe venting of emissions without the risk of material failure. This corrosion resistance significantly extends the life of the stack, reducing the need for frequent repairs or replacements.
Custom Engineering: Adaptability to Unique Design Requirements
Fiberglass-reinforced plastic stacks are highly adaptable and can be custom-engineered to meet the specific needs of a given application. Whether it’s adjusting the stack’s height, diameter, or material composition, these stacks can be designed to handle varying levels of chemical exposure, temperature extremes, and structural loads. For example, specialized resins can be used to enhance the chemical resistance of the stack, while the design can be modified to accommodate seismic or wind loads in locations prone to natural disasters. This versatility makes fiberglass-reinforced plastic stacs a preferred choice in industries with unique operational requirements.
Thermal Stability: Performs Effectively in High-Temperature Environments
Fiberglass-reinforced plastic stacks are also known for their excellent thermal stability. These stacks can perform effectively in high-temperature environments, such as those found in coal-fired power plants or chemical processing facilities. Specialized resins used in the manufacturing process can withstand extreme temperatures, ensuring that the stack maintains its integrity even when exposed to hot gases or exhaust fumes. This thermal stability is essential for industries that require a durable stack that can endure the continuous flow of heated emissions without warping, cracking, or losing structural strength.
Low Maintenance: Longer Service Life with Reduced Repair and Replacement Needs
Another major advantage of fiberglass-reinforced plastic stacks is their low maintenance requirements. Because these stacks are resistant to corrosion, high temperatures, and chemical degradation, they generally require less upkeep than traditional metal stacks. Their durability and long lifespan reduce the frequency of repairs and replacements, which can be costly and time-consuming. With proper installation, fiberglass-reinforced plastic stacks can provide decades of reliable service, offering a cost-effective solution for industrial facilities.
Additional Advantages of Fiberglass-Reinforced Plastic Stacs
- Lightweight Construction: Fiberglass-reinforced plastic stacs are significantly lighter than their metal counterparts. This not only makes them easier to transport and install but also reduces the load on supporting structures, which can lead to cost savings in construction and installation.
- Cost-Effectiveness: While the initial cost of fiberglass-reinforced plastic stacks may be higher than that of metal stacks, their long-term benefits—such as reduced maintenance costs and extended service life—make them a more cost-effective solution over time.
- Environmental Benefits: The non-corrosive nature of fiberglass-reinforced plastic stacks ensures that emissions are safely vented without the risk of chemical leakage, thereby reducing environmental impact. This feature is especially important in industries that are subject to stringent environmental regulations.
Fiberglass-reinforced plastic stacs offer numerous advantages that make them indispensable in various industrial applications. Their corrosion resistance, adaptability to custom engineering needs, thermal stability, and low maintenance requirements make them the ideal choice for industries looking for durable, cost-effective, and environmentally friendly solutions for managing exhaust gases and emissions.
Is Thermoplastiv Vs Fiberglass Tub Wall Right for Your Bathroom
Structural Design of Fiberglass-Reinforced Plastic Stacs
The structural design of fiberglass-reinforced plastic stacs (FRP stacks) is crucial for ensuring their long-term performance, especially in demanding industrial environments. These stacks must withstand various physical, thermal, and chemical stresses while providing efficient venting of exhaust gases. The design of FRP stacks involves multiple considerations, from the support systems to the construction techniques and layered composition, each contributing to the stack’s durability and functionality.
Overview of Support Systems: Self-Supporting, Guided, or Steel-Supported Designs
The support system of a fiberglass-reinforced plastic stack is a critical aspect of its design. FRP stacks can be installed using different support configurations depending on the specific application, height, and load-bearing requirements.
- Self-Supporting Design: In this configuration, the stack is designed to stand independently without the need for external support structures. Self-supporting FRP stacks are typically used for shorter stacks where the stack itself can bear the load of the height and wind forces. This design is often used in smaller industrial setups or locations where space limitations prevent the use of additional support.
- Guided Design: For taller stacks, a guided design may be required. In this system, the FRP stack is anchored at the base and supported by guide wires or brackets at specific intervals along its height. This type of support allows the stack to remain stable even in environments where high wind loads or seismic activity could cause instability. The guide system ensures that the stack remains in position while allowing for some flexibility to accommodate thermal expansion and contraction.
- Steel-Supported Design: In cases where FRP stacks need to bear significant additional loads, such as heavy industrial exhaust gases or large diameters, a steel-supported design is used. This configuration involves a steel framework that supports the stack at the base and along its height, ensuring that the load is properly distributed. Steel supports are often employed in larger industrial facilities or when the stack needs to withstand extreme external conditions, such as high winds or seismic forces.
Construction Techniques: Filament Winding, Joining Methods
The construction of fiberglass-reinforced plastic stacs involves several advanced techniques that enhance their structural integrity and longevity.
- Filament Winding: Filament winding is a popular method used in the manufacturing of FRP stacks. In this process, continuous fibers of fiberglass are wound around a mandrel in a precise pattern, which is then impregnated with resin. The wound layers form a strong, durable, and lightweight composite structure. This method allows for the creation of uniform layers, ensuring that the stack has optimal strength and resistance to external pressures, such as wind and temperature fluctuations. Filament winding is especially beneficial for taller stacks or those requiring high structural strength.
- Joining Methods: The connection of different sections of fiberglass-reinforced plastic stacs is critical for maintaining the stack’s overall integrity. There are two primary joining methods used in FRP stack construction:
- Butt Joints: This method involves aligning the ends of two sections of the stack and joining them together with adhesive or resin. The joint is then reinforced with fiberglass tape or other materials to ensure a strong, durable connection.
- Flanged Connections: In this method, flanges are added to the ends of each section of the stack. The sections are then bolted together, with gaskets or seals used to ensure a tight, leak-proof connection. Flanged connections provide added flexibility in the assembly and allow for easier disassembly if maintenance or repairs are required.
Both of these methods ensure that the stack remains structurally sound over time and can withstand the pressures and stresses typical in industrial exhaust systems.
Layered Composition of FRP Stacks
The layered composition of fiberglass-reinforced plastic stacks is essential for their strength, durability, and resistance to various environmental factors. Each layer is designed to fulfill a specific purpose, contributing to the stack’s overall performance.
- Inner Resin-Rich Corrosion Barrier: The innermost layer of an FRP stack is a resin-rich corrosion barrier. This layer is designed to protect the stack from the corrosive effects of the gases that pass through it, such as sulfuric acid, hydrochloric acid, or other chemical emissions. The resin used in this layer is typically a high-performance material that provides excellent chemical resistance, preventing the stack from degrading over time due to exposure to aggressive substances. This corrosion barrier is particularly important in industries like chemical processing or wastewater treatment, where emissions can be highly acidic or alkaline.
- Middle Structural Wall with Glass Reinforcements: The middle layer of the stack serves as the structural core, providing the strength needed to support the stack and withstand external pressures. This layer is made from a combination of fiberglass and resin, with the fiberglass acting as reinforcement. The glass fibers are arranged in a specific pattern to maximize the stack’s strength and resistance to mechanical stress, such as wind forces, vibrations, or physical impacts. This structural wall ensures that the stack maintains its shape and integrity under various operating conditions.
- Outer Protective UV and Chemical-Resistant Coating: The outermost layer of an FRP stack is a protective coating designed to shield the stack from environmental factors such as UV radiation, extreme weather conditions, and chemical exposure. This layer is typically made from a UV-resistant resin that prevents the fiberglass from becoming brittle or degrading when exposed to sunlight. The outer coating also provides an extra layer of chemical resistance, ensuring that the stack can withstand harsh weather conditions, including rain, snow, and extreme temperature fluctuations. This protective layer ensures the stack remains operational for many years, even in the most demanding environments.
The structural design of fiberglass-reinforced plastic stacs combines advanced support systems, construction techniques, and a carefully engineered layered composition to create a highly durable and efficient solution for industrial exhaust systems. Whether designed for self-supporting, guided, or steel-supported installations, and constructed using filament winding or flanged connections, these stacks offer long-lasting performance in some of the most challenging industrial environments. The layered composition—featuring corrosion-resistant, structural, and protective coatings—ensures that fiberglass-reinforced plastic stacs continue to provide effective venting solutions while withstanding chemical, thermal, and mechanical stresses.
Challenges in Using Fiberglass-Reinforced Plastic Stacs
While fiberglass-reinforced plastic stacks (FRP stacks) offer numerous benefits for industrial applications, there are certain challenges associated with their use. These challenges primarily stem from the material’s properties and the conditions in which the stacks are deployed. Understanding these limitations is essential for ensuring that fiberglass-reinforced plastic stacs perform effectively over the long term. From high-temperature applications to repair complexities and the risks of improper installation, these factors need careful consideration.
Limitations in Extreme High-Temperature Applications
One of the main challenges in using fiberglass-reinforced plastic stacs is their performance in extreme high-temperature environments. Although FRP stacks are known for their excellent thermal stability compared to many other materials, they still have limitations in very high-temperature applications, such as those involving furnace exhausts or industrial processes that produce extreme heat.
Fiberglass-reinforced plastic stacks are typically designed to operate within a specific temperature range, with some resin types and fiberglass reinforcement offering resistance to temperatures of up to 250–300°C (482–572°F). However, in industries that require the venting of exhaust gases with temperatures exceeding these limits—such as certain power generation facilities or heavy industrial processes—fiberglass-reinforced plastic may not always be suitable. Prolonged exposure to temperatures beyond the stack’s maximum tolerance can lead to material degradation, warping, or even failure of the stack. In such cases, alternative materials like high-temperature resistant metals or specialized ceramics may be required.
Complex Repairs in Cases of Structural Damage
Although fiberglass-reinforced plastic stacs are designed for durability, they are not immune to damage. If an FRP stack suffers structural damage—due to a mechanical impact, excessive stress, or environmental factors like heavy winds or seismic activity—it can be challenging to repair. Unlike metal stacks, which can often be welded or patched with standard materials, repairs to fiberglass-reinforced plastic stacks require specialized knowledge and techniques.
For example, if the stack experiences cracking, delamination, or puncturing, repairs may involve a process known as “re-laminating,” where additional layers of fiberglass and resin are applied over the damaged area. This requires careful preparation, as improper application can compromise the stack’s structural integrity. Additionally, any repairs to fiberglass-reinforced plastic stacks need to be made using compatible resins and fibers, which can sometimes be difficult to source or match. These repair procedures can be time-consuming and may involve significant downtime for the facility, particularly if the damage is extensive.
Furthermore, ensuring a proper repair often demands skilled technicians familiar with the specific material properties of fiberglass-reinforced plastic. If repairs are not conducted properly, the stack may fail prematurely, leading to additional maintenance costs and safety concerns.
Sensitivity to Improper Installation or Design Flaws
The performance of fiberglass-reinforced plastic stacs is highly dependent on correct installation and design. Improper installation or design flaws can lead to serious issues, including structural failure, reduced efficiency, and even safety hazards.
- Improper Installation: FRP stacks require careful handling and installation to ensure that they are properly aligned and securely mounted. If the stack is not correctly supported or if the joints are not properly sealed, stress points can develop, leading to cracks or leaks. Additionally, fiberglass-reinforced plastic stacks are sensitive to physical damage during installation—if the stack is dropped, scratched, or exposed to heavy impacts, it could weaken the material and reduce its lifespan. For these reasons, experienced installers are essential for ensuring a correct setup.
- Design Flaws: The design of fiberglass-reinforced plastic stacs must be tailored to the specific conditions they will face, including wind loads, seismic activity, chemical exposure, and thermal stresses. A design flaw—such as improper thickness of the resin layers, inadequate reinforcement, or insufficient support systems—can result in the stack failing to withstand these forces. For example, a stack that is too thin may buckle under high winds or temperature changes, while one that is not properly reinforced may be prone to cracking under mechanical stress. These issues can compromise the stack’s structural integrity, resulting in frequent repairs or replacements.
To avoid these problems, it is crucial to involve experienced engineers during both the design and installation phases. This ensures that the fiberglass-reinforced plastic stack is correctly specified for the intended application, with all necessary support systems and protective coatings in place.
While fiberglass-reinforced plastic stacks offer many advantages, including corrosion resistance, thermal stability, and low maintenance, there are challenges that need to be addressed. These include their limitations in extreme high-temperature applications, the complexity of repairs in cases of structural damage, and the sensitivity to improper installation or design flaws. By carefully considering these factors and working with skilled engineers and technicians, many of these challenges can be mitigated, allowing fiberglass-reinforced plastic stacks to provide reliable and long-lasting service.
FAQs about Fiberglass-Reinforced Plastic Stacs
Fiberglass-reinforced plastic (FRP) is a composite material made by combining a polymer matrix, such as polyester or epoxy resin, with fiberglass reinforcement. This combination creates a lightweight yet incredibly strong material with exceptional durability. FRP is widely used in various industries, including aviation, construction, automotive, and marine, due to its high strength-to-weight ratio, corrosion resistance, and flexibility in design. Its layered structure typically includes a resin-rich surface, fiberglass reinforcements, and structural layers that enhance its mechanical properties. Additionally, FRP offers thermal stability and can be molded into complex shapes, making it ideal for custom applications. From industrial piping to aircraft components, FRP has become a go-to material for applications requiring strength and durability without the weight and maintenance needs of traditional materials like steel or aluminum.
While fiberglass-reinforced plastic (FRP) offers numerous advantages, it does have some limitations. One major drawback is its sensitivity to high temperatures. Standard FRP materials can lose structural integrity when exposed to prolonged heat above certain thresholds, typically around 100°C for general-purpose polyester and 200°C for specialized resins. Another challenge is its susceptibility to aging due to environmental factors such as UV radiation, weathering, and chemical exposure, which can degrade its surface over time. Repairing FRP can also be complex, particularly in detecting and addressing delamination or internal damage. Additionally, FRP has a relatively low modulus of elasticity compared to materials like steel, making it less rigid and prone to deformation under high stress. Despite these drawbacks, proper design, material selection, and maintenance can mitigate these issues, making FRP a valuable material in many applications.
Yes, fiberglass-reinforced plastic (FRP) is an excellent material for a wide range of applications due to its unique combination of properties. Its lightweight nature, combined with high tensile strength, makes it ideal for industries where weight reduction is critical, such as aerospace and automotive. FRP’s resistance to corrosion ensures long-lasting performance in harsh environments, such as chemical plants or marine settings. It also offers design flexibility, as it can be molded into complex shapes to meet specific requirements. Furthermore, FRP is a low-maintenance material with excellent durability, providing cost savings over its lifespan compared to traditional materials like steel or wood. Its insulating properties and non-conductive nature add to its versatility, making it suitable for electrical and thermal applications. While it has some limitations, such as heat sensitivity and repair challenges, the benefits of FRP far outweigh its drawbacks, making it a preferred choice in many industries.
Cutting fiberglass-reinforced plastic (FRP) requires proper tools and safety precautions due to its tough, abrasive nature. To achieve clean and precise cuts, use a tool with a carbide-tipped blade, such as a circular saw, jigsaw, or oscillating multi-tool. For straight cuts, a circular saw equipped with a fine-tooth blade is ideal, while a jigsaw or rotary tool is better suited for curved or detailed cuts. Always wear protective gear, including a dust mask, safety glasses, and gloves, as cutting FRP generates fine fiberglass particles that can irritate the skin, eyes, and respiratory system. Secure the material firmly to prevent movement during cutting, and work slowly to avoid chipping or cracking. To minimize dust, consider using a wet saw or attaching a vacuum to the cutting tool. After cutting, sand the edges to remove sharp fibers and achieve a smooth finish. Proper preparation and technique ensure clean, safe, and efficient cutting of FRP.
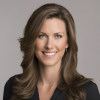
As the editor of GangLong Fiberglass, I have years of experience and in-depth research, focusing on cable tray products, fiberglass solutions, and grille systems. I incorporate years of industry insights and practical experience into every content, committed to promoting the progress of the industry. At GangLong Fiberglass, my commitment is reflected in every product, from innovative cable trays to durable fiberglass solutions and sturdy grille systems. As an authoritative voice in the industry, my goal is to provide valuable information to professionals and businesses and promote forward-looking solutions.