- Home
- Fiberglass Reinforced Polyester (FRP)
GangLong Fiberglass Supply Fiberglass Reinforced Polyester (FRP)
Fiberglass is often used as a generic term encompassing a range of products, while “Fiberglass Reinforced Polyester (FRP)” specifically refers to materials like grating and structural components. Although the terms are sometimes used interchangeably within the industry, they can denote different products. Fiberglass typically refers to the fiber material itself, which is used in various composite constructions. On the other hand, FRP (Fiberglass Reinforced Plastic) is a composite material made by reinforcing plastic with fiberglass. This combination enhances strength and durability. An excellent example of FRP application is fiberglass reinforced plastic decking, which offers superior resilience and low maintenance compared to traditional decking materials.
FRP exhibits exceptional properties such as high strength, durability, and resistance to corrosion and impact, making it highly valued across various industries like construction, automotive, and manufacturing. These qualities derive from the combination of polyester resin and fiberglass reinforcement, creating a robust material that excels in harsh environments and offers longevity and minimal maintenance needs.
Additionally, FRP is used in practical applications such as enclosures for protecting networking and security equipment. GangLong Fiberglass provides both standard and customized rugged enclosures made from molded Fiberglass Reinforced Polyester (FRP), tailored to meet specific customer requirements. This versatility and the protective capability of FRP make it an essential material for both structural components and protective panels in demanding applications.
Simplifying Your Life: Key Functionalities

Attributes | Details |
---|---|
Place of Origin | Hebei, China |
Brand Name | GangLong Fiberglass |
Application | Industrial, Construction, /Industrial, Agricultural Greenhouse, etc. |
Technology | Molding, Forming, Pultrusion |
Surface Treatment | Frosted, Concave, Smooth Surface |
Processing Services | Molding, Cutting, Handmade, Bending, Uncoiling, Welding, Punching |
Color | Black, Gray, Green, Blue, Yellow, etc., Customizable |
Material | Glass Fiber Reinforced Polyester |
Weight | Half the Weight of Cast Iron |
Length | Customized Length |
Shape | Customizable |
Advantage | Non-conductive |
Certification | ISO9001 |
Features | Fireproof, High Tensile Strength, Insulation and Anti-corrosion |
News
- Exploring the Benefits of Carbon Fiber Apparel
- How to Work with Carbon Fiber Successfully
- Carbon Fiber Suit: The Future of Lightweight Armor
- Is Carbon Fiber Armor the Future of Protection?
- Why White Carbon Fiber is Popular in Automotive Design
- Transparent Carbon Fiber Sheets: Strength Meets Clarity in Design
- Chopped Carbon Fiber Mat for Lightweight Reinforcement
- Carbon Fiber EG Hatch: Upgrade Your Civic Today
- The Benefits of Using Structural Carbon Fibre in Engineering
- How Many Layers of Layered Carbon Fiber Are Needed?
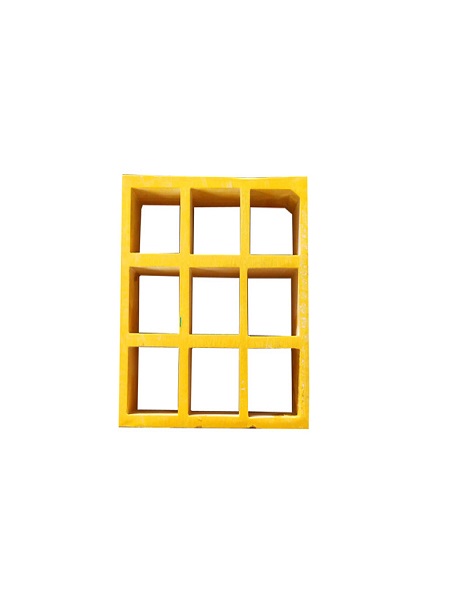
What is Fiberglass Reinforced Polyester (FRP)?
Fiberglass Reinforced Polyester (FRP), also known as reinforced thermoset plastic (RTP), reinforced thermoset resin plastic (RTRP), Glasfaserverstärkter Kunststoff (GFK), SRP, or GRP, is a composite material widely used in industries like transportation, construction, and hightraffic areas. This versatile material combines fiberglass reinforcement with polyester resin, where the resin acts as a matrix and the fiberglass enhances strength and structural integrity. Known for its costeffectiveness, ease of repair, ability to form complex shapes, smooth inner surface, thermal insulation, light weight, and resistance to high temperatures and corrosion, FRP is an ideal choice for applications requiring durability and resilience. Commonly found in shopping malls, airports, and conference centers, FRP stands the test of time in demanding environments.
Fiberglass Reinforced Polyester (FRP) is a composite material created by combining specific components that contribute to its strength, durability, and versatility. The main elements of FRP include: The polyester resin acts as the matrix or binder in the composite. It surrounds and holds the fiberglass reinforcement together, providing cohesion and distributing loads evenly. Types of Polyester Resins: Fiberglass provides the tensile strength and structural integrity of FRP. It reinforces the resin matrix and significantly enhances the composite’s mechanical properties. Forms of Fiberglass: By combining these elements, FRP achieves its unique balance of high strength, low weight, and resistance to environmental and mechanical stresses, making it a versatile material for diverse applications.Material Composition of Fiberglass Reinforced Polyester (FRP)
Gel Coat
Polyester Resin
Fiberglass Reinforcement
Additional Components
Benefits of Fiberglass Reinforced Polyester (FRP)
Fiberglass Reinforced Polyester (FRP) offers a wide range of benefits that make it an exceptional material for various applications. Its unique properties provide a combination of strength, durability, and versatility unmatched by traditional materials like steel, concrete, or wood. Below are the key benefits of FRP:
Lightweight Yet Strong
FRP has an outstanding strengthtoweight ratio, making it a superior choice for loadbearing applications. Weighing only 23 pounds per square foot, it is much lighter than traditional building materials, simplifying handling, transportation, and installation without compromising structural integrity.
Corrosion Resistance and Durability
FRP is highly resistant to rust, rot, and chemical corrosion, making it ideal for harsh environments such as marine, oil and gas, or chemical industries. This durability ensures a longer lifespan with reduced replacement and repair costs.
Low Maintenance Requirements
Its nonporous surface resists stains, mildew, and scratches, making FRP easy to clean and maintain. It does not weaken over time, remains waterproof, and can be quickly cleaned using standard methods like pressure washing.
Customizable Design
FRP can be molded into virtually any shape or curve, allowing for creative and complex designs. It also comes in a wide variety of finishes, colors, and textures, ensuring aesthetic flexibility alongside functional advantages.
UV Resistance
FRP is UV resistant, making it an excellent material for outdoor and marine environments where prolonged exposure to sunlight is expected. It maintains its structural integrity and appearance over time.
NonConductive
FRP is electrically nonconductive, offering a safer alternative in highvoltage areas such as substations and powerintensive facilities. This property eliminates the risk of electrical hazards from contact or step potentials.
AntiSlip Surface
With inherent antislip properties, FRP is a safer alternative to materials like steel grating. It provides better grip, reducing the risk of accidents in industrial or outdoor environments.
Fire Resistance
FRP products meet stringent fire safety standards, including ASTM E84 Class 1 flame retardant and ASTM D635 for selfextinguishing capabilities. This makes it suitable for applications requiring fireproof materials.
High Impact and Scratch Resistance
FRP can withstand heavy impacts without deformation, and its surface resists scratches and abrasions, maintaining its appearance and performance even in hightraffic areas.
Easy Installation
FRP products can be cut with standard tools and assembled with bolts and clips, eliminating the need for welding. This simplicity reduces installation time and costs significantly.
Hygienic and Waterproof
FRP provides excellent moisture resistance, ensuring hygienic protection in areas like food processing or hospitals. Its waterproof nature prevents mold and bacterial growth, making it ideal for sanitary environments.
By combining these features,Fiberglass Reinforced Polyester (FRP) emerges as a versatile, costeffective, and highperformance material suitable for a wide range of industries and applications.
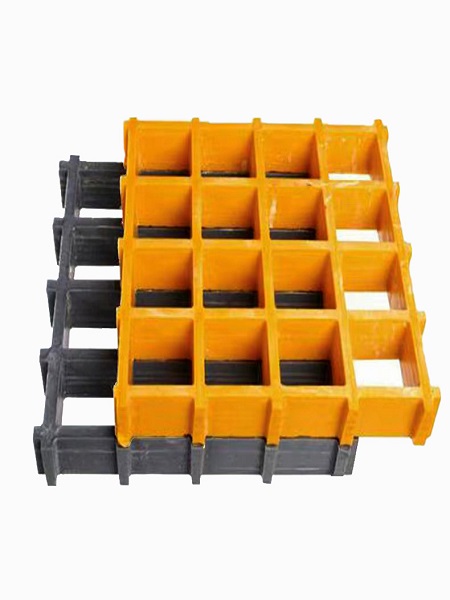
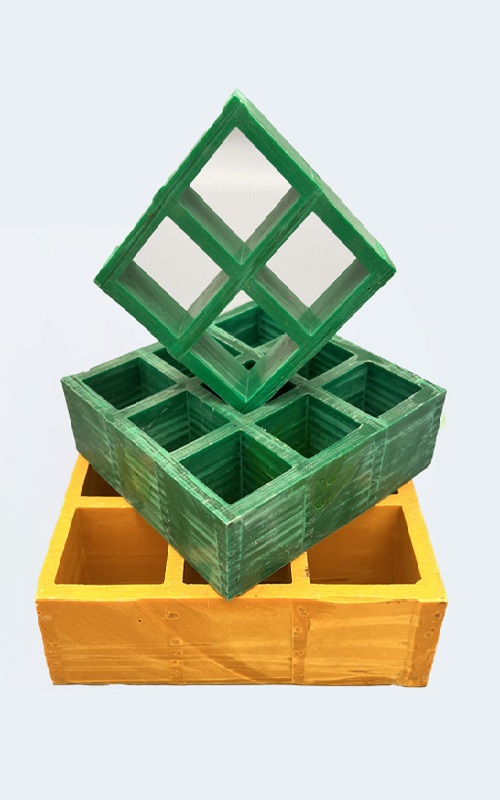
FRP Pricing and Costs
Fiberglass Reinforced Polyester (FRP) Price
The price of Fiberglass Reinforced Polyester (FRP) products can vary widely depending on several factors. On average, FRP products range from $30 to $100 per square foot. The cost is influenced by factors such as size, thickness, and the specific supplier. Larger or thicker panels and custom orders typically cost more due to increased material and manufacturing requirements. Additionally, FRP with specialized properties, such as enhanced fire resistance or UV protection, can also command higher prices. Choosing a reputable supplier who offers quality FRP can help ensure you receive a product that meets your needs while providing good value. This is especially important in the context of FRP pipe procurement, where the reliability of the material directly impacts the performance and longevity of the application.
Fiberglass Reinforced Polyester (FRP) Cost
The overall cost of Fiberglass Reinforced Polyester (FRP) includes not only the initial purchase price but also installation and maintenance expenses. For various applications, such as construction panels, automotive parts, or industrial components, FRP often proves to be a cost-effective option. For example, installing FRP panels in a commercial building may cost between $40 and $80 per square foot, including installation.
When comparing the cost of Fiberglass Reinforced Polyester (FRP) with other materials such as steel or aluminum, FRP often offers a lower total cost of ownership. Although steel or aluminum may have a lower initial purchase price, FRP’s resistance to corrosion and minimal maintenance needs can lead to lower long-term costs. FRP’s lightweight nature also reduces installation costs, as it typically requires less labor and equipment to handle compared to heavier metals.
Types of Fiberglass Reinforced Polyester (FRP) Resins
Fiberglass Reinforced Polyester (FRP) resins have evolved significantly over time, moving beyond traditional polyester resins to include advanced formulations that enhance durability, corrosion resistance, and fire retardancy. Modern resin technology allows for the inclusion of specialized chemical barrier layers within FRP products, further improving their performance in demanding environments. Below are the primary types of FRP resins used today:
Fire Retardant Resin
Designed to enhance flame resistance, fire retardant resins meet stringent safety standards, making them ideal for applications in highrisk environments requiring superior fire protection.
Vinyl Ester Resin
Known for its exceptional chemical resistance, vinyl ester resin is commonly used in environments exposed to harsh acids, alkalis, and solvents, ensuring longterm performance and durability.
Terephthalic Resin
Terephthalic resins provide excellent structural strength and resistance to heat, making them suitable for applications requiring high mechanical performance under thermal stress.
Bisphenolic Resin
This resin offers superior chemical resistance, particularly to highly acidic or caustic environments. It is often used in industrial settings like chemical storage tanks or pipelines.
Isophthalic Neo Pentyl Glycol Resin
Combining isophthalic resin properties with neo pentyl glycol, this resin delivers enhanced resistance to weathering, UV degradation, and chemical exposure, ensuring longevity in outdoor and industrial applications.
Isophthalic Resin
A step up from orthophthalic resin, isophthalic resin provides improved mechanical strength, durability, and resistance to water and chemicals, making it a versatile choice for marine and structural applications.
Orthophthalic Resin
As one of the most widely used resins in FRP, orthophthalic resin is costeffective and suitable for generalpurpose applications that do not require extreme chemical or environmental resistance.
ModernFiberglass Reinforced Polyester (FRP) Resins cater to a wide range of applications by offering tailored properties such as flame retardancy, chemical resistance, and structural integrity, ensuring optimal performance in diverse industries.
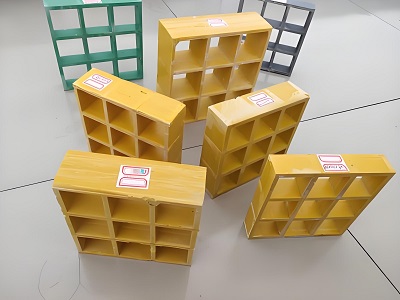
Thank you for your interest in our products. To receive our pricelist or for any inquiries, please fill out the form below. We will get back to you within 24 hours.
Applications of Fiberglass Reinforced Polyester (FRP)
Fiberglass Reinforced Polyester (FRP) is a versatile material with applications spanning multiple industries due to its durability, lightweight nature, corrosion resistance, and adaptability. Below is a comprehensive overview of the various uses of FRP:
Industrial Processing
FRP is extensively used in industrial markets for handling and processing wet or dry gases, storing fluids, and processing chemical fluids. Common cylindrical FRP products include spray headers, piping systems, chimney liners, duct systems, and storage tanks, which meet strict production standards to ensure reliability.
Chemical and Corrosive Environments
With its exceptional resistance to chemical corrosion, FRP is ideal for applications in industries such as oil and gas, utilities, wastewater treatment, and chemical processing. It is particularly effective for cable trays, duct systems, and storage solutions in harsh and corrosive environments.
OnSite Installations
FRP products are preferred for onsite installations due to their lightweight nature and ease of assembly. Certified laminators worldwide ensure the proper installation of FRP products, which often include custom designs for specific applications.
Structural Applications
FRP is commonly used in constructing ladders, stairs, platforms, handrails, and guardrails, particularly in environments requiring materials with high durability, strength, and corrosion resistance. These structures are found in industrial plants, public infrastructure, and entertainment facilities.
Marine and Aquatic Environments
FRP’s noncorrosive and UVresistant properties make it ideal for marine applications, such as aquariums, water parks, and other aquatic projects. It provides excellent insulation, a smooth surface, and structural integrity in waterexposed environments.
Food and Beverage Processing
The hygienic, stainresistant, and moistureproof properties of FRP make it a reliable material for the food and beverage industry. It is widely used in production facilities requiring sanitary and durable solutions.
Versatile Design Possibilities
FRP allows endless possibilities for mixing materials and designing custom products with varying thicknesses, mechanical layers, and chemical barrier layers (CBL). The inner layer, or CBL, provides direct contact with chemicals or fluids, while the structural layer ensures mechanical strength, expertly crafted by skilled technicians.
Fiberglass Reinforced Polyester (FRP) continues to be a preferred material in industries ranging from construction and utilities to entertainment and chemical processing, offering reliable, customizable, and costeffective solutions for demanding applications.
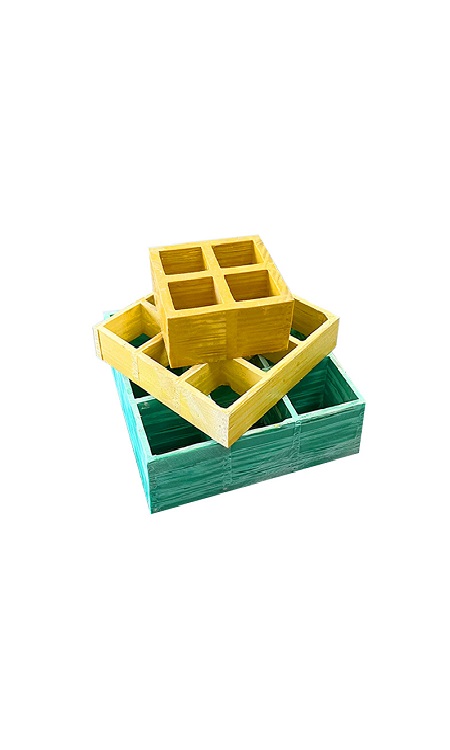
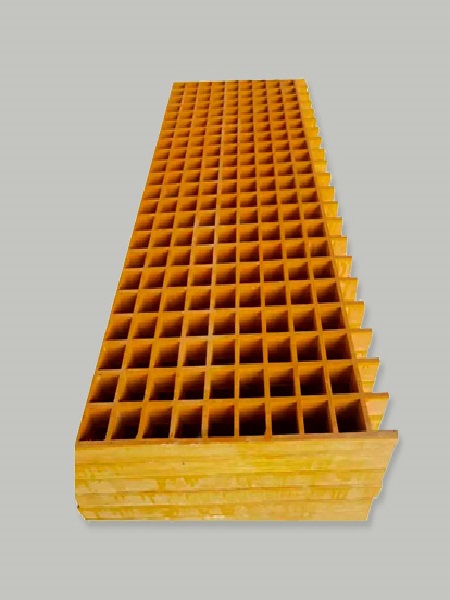
Comparing FRP with Other Materials
FRP vs Fiberglass Body Kit
When comparing Fiberglass Reinforced Polyester (FRP) with fiberglass body kits, it’s important to understand their distinct properties and uses. FRP is a composite material that combines polyester resin with fiberglass to create a versatile, durable material used in various industrial applications. It is known for its strength, corrosion resistance, and low maintenance needs.
Fiberglass body kits, on the other hand, are specifically designed for automotive use, typically consisting of fiberglass reinforced with a resin. While they share some similarities with FRP in terms of using fiberglass reinforcement, body kits are generally tailored for aesthetic and performance enhancements in vehicles.
Advantages of Fiberglass Reinforced Polyester (FRP):
Versatility: Suitable for a wide range of applications, including construction, industrial, and architectural uses.
Durability: High resistance to environmental factors such as moisture and chemicals.
Cost-Effective: Often more economical for large-scale applications due to lower maintenance and long-term performance.
Customization: Designed for specific vehicle models, offering aesthetic upgrades and performance improvements. Not Vehicle-Specific: While highly durable, it may not offer the same level of customization as fiberglass body kits for automotive needs. Limited Application: Primarily suited for automotive use and may not be ideal for other industrial or structural applications. Comparing Fiberglass Reinforced Polyester (FRP) with other plastics reveals significant differences in performance and application suitability. FRP, a type of fiber-reinforced plastic, combines polyester resin with fiberglass to enhance its strength and durability. Other plastics, such as polypropylene, polystyrene, and PVC, differ in their composition and properties. FRP vs Glass-Reinforced Plastic (GRP): GRP is a type of FRP specifically using glass fibers. While similar in terms of reinforcement, GRP might offer more specific applications and properties tailored to particular needs. FRP vs Polypropylene: Polypropylene is known for its chemical resistance and flexibility but lacks the strength and rigidity of FRP. FRP’s enhanced durability and strength make it suitable for demanding applications.Advantages of Fiberglass Body Kits:
Lightweight: Improves vehicle handling and fuel efficiency due to reduced weight.Disadvantages of FRP:
Disadvantages of Fiberglass Body Kits:
Fiber Reinforced Plastic (FRP) vs Other Plastics
Comparison with Other Types of FRP:
Comparison with Other Plastics:
FRP vs PVC: PVC is widely used for plumbing and construction but does not match FRP’s impact resistance and load-bearing capabilities. FRP’s superior performance in harsh environments makes it a better choice for high-stress applications.
FRP vs Polystyrene: Polystyrene is often used for insulation and packaging but is less robust compared to FRP. The high strength and durability of FRP make it a more suitable option for structural applications.
Difference Between Fiberglass and Fiberglass Reinforced Polyester (FRP)
Understanding the distinction between Fiberglass and Fiberglass Reinforced Polyester (FRP) can be complex due to overlapping terminologies. Below are the key points of difference, presented clearly for better understanding:
Definition of FRP
FRP stands for FiberReinforced Polymer, which refers to a composite material made from a polymer matrix reinforced with fibers.
 Polymers can be natural or synthetic, such as polypropylene or polystyrene. FRP can be reinforced with various fibers, including glass, carbon, or graphite, depending on the desired properties.
Definition of Fiberglass
Fiberglass specifically refers to composites where glass fibers are used as the reinforcement material.
 Fiberglass composites generally fall under the category of FRP, as they include fibers (glass) within a polymer matrix.
FRP Includes Various Fiber Types
FRP is a broader category and can be reinforced with different types of fibers, such as glass, carbon, or graphite, depending on the application.
 Fiberglass is a specific type of FRP that uses only glass fibers for reinforcement.Â
Not All FRP Is Fiberglass
Since FRP can use other types of fibers, such as carbon or aramid, not all FRP is fiberglass. For example, an FRP composite reinforced with carbon fibers would not be considered fiberglass.
Not All Fiberglass Is FRP
Fiberglass refers to the use of glass fibers as reinforcement. However, if the matrix material is not a polymer (e.g., cement or another binder), the composite cannot be classified as FRP.
Fiberglass specifically refers to Glass FiberReinforced Polymer (GFRP) when the base material is polymer.
Interchangeability in Terminology
Fiberglass and FRP are often used interchangeably, but this is technically accurate only when discussing composites made with glass fibers and a polymer matrix.
A fiberglass composite without a polymer base or an FRP composite without glass fibers is not interchangeable with the other.
Simplified Comparison
- Fiberglass: A type of FRP that uses glass fibers.
- FRP: A broader category that may include glass, carbon, or other fibers as reinforcement.
By breaking down these distinctions, it becomes clear thatFiberglass Reinforced Polyester (FRP) encompasses a variety of materials, while fiberglass is a more specific term referring only to composites with glass fiber reinforcement. Understanding the fiber and polymer combinations is essential to correctly categorize and apply these materials.
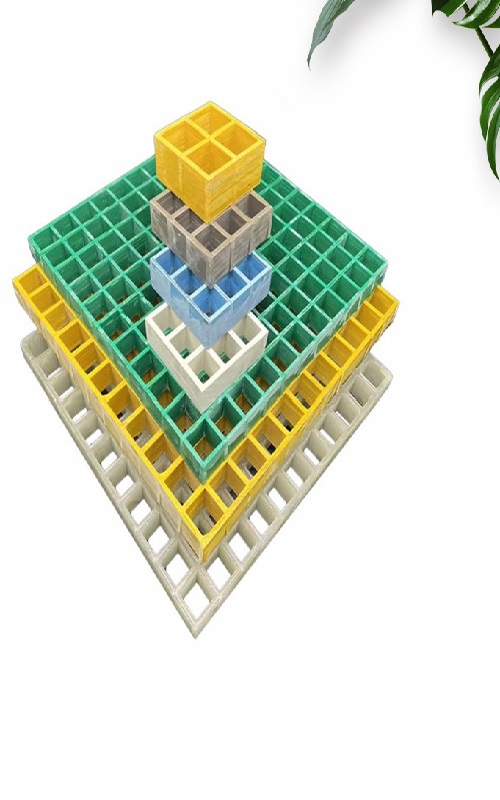
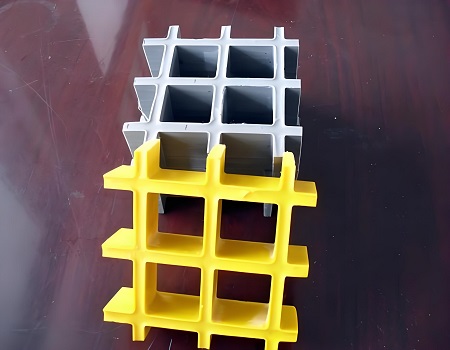
Comprehensive Guide to Fiberglass Reinforced Polyester (FRP) Panels
Fiberglass Reinforced Polyester (FRP) panels are versatile, durable, and lightweight materials widely used across industries for their strength and adaptability. Below is a detailed overview of FRP panels, organized into features, applications, and advantages.
What Are Fiberglass Reinforced Polyester (FRP) Panels?
FRP panels are thin, flexible plastic sheets made from highstrength polyester resin reinforced with glass fibers. These panels are ideal for walls, ceilings, and various structural applications, offering a tough, durable surface that is easy to clean and maintain. Available in finishes like embossed, smooth, or gelcoated and a variety of colors and sizes, they provide both aesthetic and functional benefits.
Features of Fiberglass Reinforced Polyester (FRP) Panels Used for wall cladding, ceilings, and partitions in areas exposed to moisture or corrosive substances.  Ideal for kitchens, bathrooms, locker rooms, and food processing plants due to their hygiene and durability.  Applied in lightweight body parts like bumpers, hoods, and spoilers to improve vehicle performance and fuel efficiency.  Durable and impactresistant, ensuring the longevity of automotive components under harsh conditions.  Protects linings, machinery covers, and structural components.  Resistant to abrasion, chemicals, and extreme temperatures, enhancing safety and reducing maintenance.  Frequently utilized in manufacturing, entertainment venues, water parks, aquariums, and special projects.  Resistant to corrosion, impact, and environmental damage, ensuring a longer lifespan compared to traditional materials.  Nonporous and stainresistant surface eliminates the need for frequent painting or sealing.  Reduces handling and installation costs while lowering structural loads in architectural and automotive applications.  Customizable to various shapes, sizes, and finishes for aesthetic and functional adaptability.  FRP panels combine durability, flexibility, and ease of use, making them indispensable across industries like construction, automotive, and industrial manufacturing. Their ability to withstand harsh environments, resist corrosion, and maintain structural integrity underscores their value as a modern, costeffective solution.Applications of Fiberglass Reinforced Polyester (FRP) Panels
Construction:Â
Automotive:Â Â
Industrial:Â Â
Other Uses:Â Â
Advantages of Fiberglass Reinforced Polyester (FRP) Panels
Durability:Â Â
Low Maintenance:Â Â
Lightweight:Â Â
Versatility:Â Â
Additional Information
FRP Material List
Fiberglass Reinforced Polyester (FRP) materials come in various forms, each designed to cater to specific applications and industries.
Chopped Strand Mat (CSM): This type of FRP material is composed of randomly oriented glass fibers held together with a binder. CSM is commonly used for creating parts with complex shapes and is particularly useful in fiberglass hand lay-up processes. It provides good surface finish and is ideal for applications that require moderate strength and flexibility.
Woven Roving: Woven roving consists of continuous glass fibers woven into a fabric. It offers higher strength and stiffness compared to chopped strand mat. Woven roving is often used in applications that demand high tensile strength, such as in boat hulls, tanks, and structural panels.
Unidirectional Fabric: This FRP material has fibers aligned in a single direction, providing maximum strength along that axis. Unidirectional fabric is used in applications where load is predominantly in one direction, such as in beams, spars, and reinforcements in construction projects
Carbon Fiber Reinforced Polymer (CFRP): Though not strictly a type of Fiberglass Reinforced Polyester (FRP), CFRP is often grouped under the same category due to its similar applications. CFRP is known for its high strength-to-weight ratio and is used in aerospace, automotive, and high-performance sports equipment.
Hybrid Fabrics: Hybrid fabrics combine different types of fibers, such as glass and carbon, to achieve a balance of properties. These materials are used in applications where a combination of strength, flexibility, and cost-effectiveness is required, like in sports equipment and automotive parts.
Polyester Resin: This is the most commonly used resin in Fiberglass Reinforced Polyester (FRP) applications. Polyester resin is cost-effective, easy to use, and offers good mechanical properties, making it ideal for a wide range of applications from automotive to marine industries.
Vinyl Ester Resin: Vinyl ester resin offers better chemical resistance and mechanical properties compared to polyester resin. It is often used in applications exposed to harsh chemicals, such as chemical storage tanks and pipelines.
Future Trends in FRP
As technology advances, so too does the development and application of Fiberglass Reinforced Polyester (FRP). The future of FRP is promising, with several emerging trends and innovations set to revolutionize the industry.
Advanced Resin Formulations: One of the key areas of innovation in Fiberglass Reinforced Polyester (FRP) is the development of advanced resin formulations. These new resins offer enhanced performance characteristics, such as increased durability, higher temperature resistance, and improved fire retardancy. These advancements will expand the applications of FRP, particularly in industries like construction and transportation where stringent safety and performance standards are required.
3D Printing of FRP Components: 3D printing technology is making significant inroads into the FRP industry. The ability to print FRP components with complex geometries opens up new possibilities for custom designs and rapid prototyping. This technology not only reduces material waste but also allows for more precise control over the mechanical properties of the final product.
Sustainable and Recyclable FRP: With growing environmental concerns, the FRP industry is focusing on developing sustainable and recyclable materials. Research is underway to create bio-based resins and fibers that reduce the carbon footprint of FRP products. Additionally, recycling processes are being refined to enable the reuse of FRP components, making the material more eco-friendly.
Integration with Smart Technologies: The integration of Fiberglass Reinforced Polyester (FRP) with smart technologies, such as sensors and IoT devices, is another trend to watch. This innovation allows for real-time monitoring of FRP structures, enabling predictive maintenance and enhancing safety in critical applications like bridges, pipelines, and wind turbines.
Hybrid Materials and Composites: The future of FRP also lies in the development of hybrid materials that combine FRP with other advanced materials, such as carbon fiber or Kevlar. These composites offer superior strength, flexibility, and lightweight properties, making them ideal for use in high-performance applications like aerospace and automotive industries.
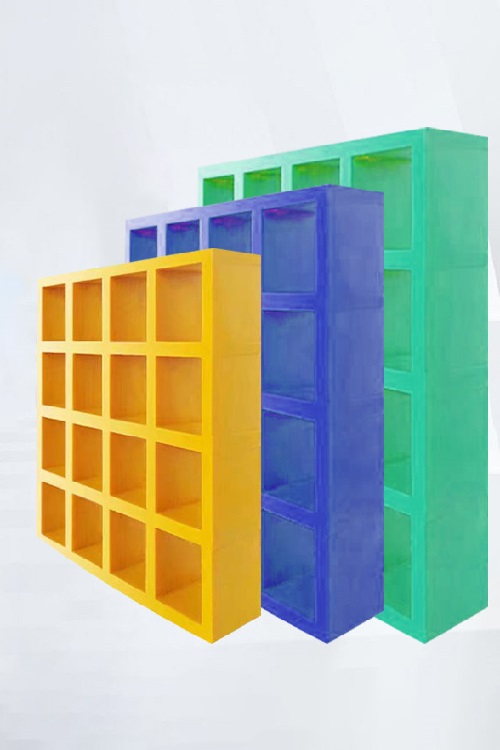
Supply Fiberglass Reinforced Polyester for Your Needs
Fiberglass Reinforced Polyester (FRP) is a highly versatile material widely used across various industries due to its excellent strength-to-weight ratio, durability, and resistance to environmental factors. The combination of polyester resin and fiberglass reinforcement results in a composite material that offers exceptional mechanical properties, making it suitable for demanding applications.
At GangLong Fiberglass, we specialize in the supply of high-quality fiberglass reinforced polyester, providing tailored solutions for a wide range of industrial, commercial, and construction projects. Whether you’re in need of raw materials for manufacturing or customized FRP components, we are committed to delivering products that meet your exact specifications.
Key Properties of Fiberglass Reinforced Polyester
High Strength and Durability: FRP composites offer superior strength compared to many traditional materials like steel and wood. The fiberglass reinforcement provides exceptional tensile strength, making it an ideal material for applications where durability and load-bearing capacity are critical.
Corrosion Resistance: One of the main advantages of fiberglass reinforced polyester is its resistance to corrosion. Unlike metals, which can rust or degrade over time, FRP resists damage from exposure to chemicals, water, and various environmental conditions. This makes it perfect for use in harsh environments, such as marine, chemical processing, and wastewater industries.
Lightweight: Fiberglass reinforced polyester is much lighter than steel, making it easier to handle, transport, and install. Its reduced weight also contributes to lower transportation and installation costs, as well as ease of use in applications where weight savings are important.
Thermal Insulation: FRP has natural insulating properties, making it effective at reducing heat transfer. This feature is beneficial in applications where temperature control is important, such as in electrical enclosures or piping systems.
Electrical Insulation: Another notable characteristic of FRP is its excellent electrical insulation properties. This makes it suitable for use in electrical applications where conductivity must be minimized, such as in utility poles or power distribution equipment.
Customizability: Fiberglass reinforced polyester can be customized to meet specific design and performance needs. The material can be molded into various shapes and sizes, and it is available in a variety of finishes, allowing for a wide range of applications across different industries.
Custom FRP Solutions
If you require a customized FRP solution, our team at GangLong Fiberglass is here to assist. We work closely with clients to understand the specific challenges of their projects and provide tailored solutions that meet their exact needs. From size and shape customization to specific mechanical properties, we ensure that our fiberglass reinforced polyester products perform optimally in your intended application.
FAQs about Fiberglass Reinforced Polyester (FRP)
Is FRP waterproof?
Is FRP better than steel?
What are the disadvantages of FRP composites?
Is FRP costly?
Does FRP break easily?
Which is better, FRP vs. GRP?
In practical terms, FRP and GRP share similar advantages: lightweight, high strength, corrosion resistance, and durability. FRP is sometimes preferred for specialized applications due to its broader range of fiber and resin combinations, offering tailored properties. GRP is more common for standard applications like water tanks, pipes, and boat hulls. Ultimately, the choice depends on project requirements. If glass fiber reinforcement suffices, GRP is ideal; for more demanding uses, FRP offers greater flexibility.
Is FRP stronger than aluminum?
However, the comparison depends on the specific application. Aluminum performs better in terms of rigidity and heat resistance, while FRP excels in flexibility and resistance to environmental factors. In weight-critical applications such as boats and aircraft, FRP often replaces aluminum due to its lighter nature and similar or superior strength. For long-term durability and low maintenance in corrosive conditions, FRP is the better choice, making it a strong competitor to aluminum.
What does FRP mean in boats?
The use of FRP revolutionized the boating industry, enabling the mass production of boats with consistent quality and performance. FRP boats are also highly customizable, allowing for complex shapes and innovative designs. While wooden or metal boats require significant upkeep, FRP boats offer a more durable, long-lasting alternative. This versatility has made FRP the material of choice for everything from small dinghies to luxury yachts.
Is fiberglass reinforced plastic good?
What are the disadvantages of GRP?
Cost: GRP can be more expensive than other materials, especially in initial costs, although this can be offset by its long-term durability.
Installation Complexity: GRP often requires specialized installation techniques and tools, which can increase labor costs.
Brittleness: GRP can be brittle compared to metals, making it susceptible to cracking or damage under high impact or stress.
UV Degradation: Over prolonged exposure to sunlight, GRP can suffer from UV degradation, leading to surface chalking or discoloration unless treated with UV inhibitors.
What are the disadvantages of fiberglass reinforced plastic?
Brittleness: FRP can crack or shatter under significant impact or heavy loads.
Limited Temperature Resistance: FRP may not perform well under extremely high temperatures, which can cause it to soften or degrade.
Chemical Sensitivity: While FRP is resistant to many chemicals, it can be sensitive to certain strong solvents or acids, which can lead to degradation.
Repair Difficulties: Repairing damaged FRP can be challenging, often requiring specialized techniques to restore its integrity.
What are the cons of GFRP?
High Initial Costs: GFRP can be expensive to produce, which may be a deterrent for some applications.
Fatigue Over Time: Under cyclic loading, GFRP can experience fatigue, leading to a reduction in its mechanical properties over time.
Environmental Concerns: Disposal and recycling of GFRP can be difficult and environmentally challenging, as it doesn't decompose easily.
Lower Toughness: Compared to metals, GFRP has lower toughness, meaning it might not absorb as much energy under impact before failing.
Is fiberglass better than plastic?
What are the advantages and disadvantages of fiberglass?
High Strength-to-Weight Ratio: Fiberglass is strong yet lightweight, making it ideal for structural applications.
Corrosion Resistance: It is highly resistant to rust, corrosion, and chemical exposure.
Durability: Fiberglass can withstand harsh environmental conditions, including UV radiation, saltwater, and extreme temperatures.
Low Maintenance: It requires minimal maintenance compared to metal or wood.
Disadvantages:
Brittleness: Fiberglass can be brittle and may crack or shatter under impact.
UV Sensitivity: Prolonged exposure to UV light can cause degradation unless treated with UV protectants.
Higher Initial Cost: The initial cost of fiberglass products can be higher than other materials, although they often offer better long-term value.
Is fiberglass as strong as Kevlar?
Is fiberglass plastic safe?
Which is better fiberglass or polycarbonate?
Fiberglass is better for applications requiring high strength, durability, and resistance to corrosion or extreme environmental conditions. It is ideal for structural components, gratings, and industrial enclosures.
Polycarbonate is better for applications requiring high impact resistance and transparency, such as safety shields, eyewear, and glazing. Polycarbonate is also more flexible and easier to mold than fiberglass.
What are the advantages and disadvantages of fibre reinforced plastics?
High Strength-to-Weight Ratio: Fiber reinforced plastics (FRP) offer excellent strength while remaining lightweight.
Corrosion Resistance: FRP is highly resistant to corrosion, making it ideal for harsh chemical environments.
Durability: FRP is durable and can withstand extreme weather, UV exposure, and mechanical stress.
Design Flexibility: FRP can be molded into complex shapes, allowing for versatile design options.
Disadvantages:
Brittleness: FRP can be brittle and prone to cracking under high impact or stress.
Cost: FRP can be more expensive to produce and install than traditional materials.
Repair Challenges: Repairing FRP can be difficult, requiring specialized techniques and materials.
Environmental Impact: FRP is not easily recyclable, and disposal can be environmentally challenging.
Which is better PVC or fiberglass?
PVC is cheaper, easier to install, and widely used in plumbing and electrical conduit applications. It is resistant to many chemicals but is less durable in extreme temperatures and less strong than fiberglass.
Fiberglass is stronger, more durable, and resistant to corrosion, making it better for structural applications and environments with harsh chemical exposure. Fiberglass also performs better in high-temperature environments.
Is FRP hazardous?
Is fiberglass good quality?
What is fiberglass reinforced polyester made of?
Fiberglass: This is a material made from very fine fibers of glass, which provides the structural reinforcement. It comes in various forms such as woven mats, chopped strands, or continuous filaments, depending on the desired strength and application.
Polyester Resin: This is a type of polymer that serves as the matrix or binding material. The resin surrounds and adheres to the fiberglass, forming a solid composite when it hardens (cures). Polyester resins are popular in FRP manufacturing because they offer good mechanical properties, chemical resistance, and are relatively cost-effective.
The combination of fiberglass and polyester resin creates a strong, lightweight, and durable composite material that is widely used in various industries, including construction, marine, automotive, and aerospace.
What happens when you touch fiberglass?
Is fiberglass made of plastic?
Is fibre-reinforced plastic waterproof?
Is fiberglass reinforced plastic strong?
Is a common term for glass reinforced polyester fiberglass?
What is polyester fiberglass used for?
Marine Industry: Boat hulls, decks, and other marine components due to its resistance to saltwater and moisture.
Construction: Roofing panels, cladding, and other structural components where lightweight and corrosion resistance are needed.
Automotive Industry: Body panels, hoods, and other components where lightweight and high strength are essential.
Aerospace: Non-structural components and fairings that require a lightweight, strong material.
Industrial Applications: Tanks, pipes, gratings, and enclosures in chemical plants and wastewater treatment facilities where resistance to chemicals and corrosion is crucial.
Where does fiberglass come from?
What is fiberglass polyester?
ls fibreglass fabric safe?
Is polyester fibreglass waterproof?
What are the disadvantages of polyester resin?
Brittleness: Polyester resin is relatively brittle compared to other resins like epoxy, making it more prone to cracking under impact or stress.
Lower Adhesion: It has lower adhesion properties, meaning it might not bond as well to certain surfaces or require additional surface preparation.
Shrinkage: Polyester resin tends to shrink as it cures, which can lead to warping or internal stresses in the finished product.
Chemical Sensitivity: While resistant to many chemicals, polyester resin can degrade when exposed to strong acids or solvents.
Odor and Fumes: Polyester resin emits strong, unpleasant fumes during curing, which can be harmful if inhaled. Proper ventilation and protective equipment are necessary during application.
Which is better, fiberglass or polyester?
Fiberglass: Refers to the reinforcing material made from glass fibers, known for its strength, flexibility, and durability. It is used in combination with resins (like polyester) to form composites.
Polyester: Typically refers to polyester resin in this context, which is used as a binding matrix for fiberglass. Polyester is less strong on its own but when combined with fiberglass, it forms a strong, lightweight composite material.
Therefore, neither is ""better"" in isolation; they complement each other in fiberglass composites. If comparing the raw materials, fiberglass is stronger, while polyester (as a resin) is more versatile when used in combination with fiberglass.
ls polyester fiber better than cotton?
Polyester Fiber: It is more durable, resistant to wrinkles, and dries quickly. It also has good shape retention and is less prone to shrinking or stretching. However, it is less breathable than cotton and may trap heat, making it less comfortable in hot weather.
Cotton: Cotton is natural, breathable, and comfortable to wear, especially in warm climates. It is also hypoallergenic and biodegradable. However, cotton wrinkles easily, takes longer to dry, and may shrink or lose shape over time.
For industrial or performance applications, polyester fiber may be preferred for its durability and low maintenance. For comfort and environmental reasons, cotton may be a better choice in clothing and textiles.
Is polyester fiber good quality?
How strong is fiberglass fabric?
ls fiberglass a resin or plastic?
How to tell if something is fiberglass?
Texture and Appearance: Fiberglass typically has a woven or textured appearance, especially on unfinished surfaces. You might see small glass fibers or a fabric-like pattern under a smooth surface.
Weight: Fiberglass is lightweight compared to metals but heavier than most plastics.
Flexibility and Strength: It has a certain amount of flexibility and resilience, but it is also strong and rigid when set in resin.
Surface Feel: Raw fiberglass surfaces may feel rough and can cause itching if touched. Finished fiberglass is often smooth.
Burn Test: If a small sample is safe to burn (in a controlled environment), fiberglass will not melt like plastic but will produce white ash and a glassy residue.
Visual inspection combined with these characteristics can help identify fiberglass.
Is fiber reinforced polymer the same as fiberglass?
What is the difference between polyester fiber and fiberglass fiber?
Fiberglass Fiber: Fiberglass fiber is made from very fine strands of glass. It is used as a reinforcement material in composites due to its high tensile strength, stiffness, and resistance to heat and corrosion.
The primary difference lies in their composition and applications: polyester fibers are used in soft goods, while fiberglass fibers are used for structural reinforcement in composites.
Is fiber reinforced polymer expensive?
Fiberglass FRP: Tends to be more cost-effective compared to other types of FRP like carbon fiber or aramid (Kevlar) reinforced polymers.
Carbon Fiber FRP: Is significantly more expensive due to the cost of carbon fiber and the complex manufacturing processes involved.
Overall: FRP can be more expensive upfront compared to traditional materials like steel or aluminum. However, its durability, corrosion resistance, and reduced maintenance costs often make it a cost-effective solution over the long term.
Is fibreglass stronger than plastic?
Is fiber reinforced polymer scratch resistant?
How durable is Fibre reinforced polymer?
Corrosion: Ideal for use in harsh chemical environments or outdoor applications.
Moisture and Water Damage: Does not rust or degrade like metal or wood in wet conditions.
Impact and Fatigue: Exhibits good impact resistance and can withstand repeated loading and stress over time.
Temperature Extremes: Certain types of FRP are designed to perform well under high or low temperatures, though this depends on the resin used.
The overall durability makes FRP suitable for long-term use in demanding industrial and structural applications.
What is fiberglass reinforced plastic used for?
Construction: Roofing panels, structural components, and bridges due to its strength and corrosion resistance.
Marine: Boat hulls, decks, and other marine components because of its resistance to saltwater and moisture.
Automotive: Body panels, hoods, and other components where lightweight and strength are important.
Industrial: Tanks, pipes, ducts, and gratings in chemical plants and wastewater treatment facilities.
Aerospace: Non-structural components and fairings where weight savings are critical.
FRP is favored in these industries due to its durability, lightweight nature, and resistance to environmental factors.
Which is better, GRP or FRP?
FRP (Fiber Reinforced Polymer): Is a broader term that includes GRP as well as other composites made with different fibers like carbon or aramid.
The ""better"" material depends on the application:
For general structural applications where cost is a concern, GRP might be the better choice.
For high-performance applications where weight savings and strength are critical (like aerospace or high-end automotive), other types of FRP (e.g., carbon fiber reinforced) may be preferable.
Is FRP good for cars?
Body Panels: Lightweight and durable, used in racing and performance cars.
Bumpers: For enhanced strength and impact resistance.
Interior Components: Where weight reduction is critical.
Underbody Components: Such as shields and deflectors, to resist corrosion and reduce weight.
FRP allows manufacturers to reduce the weight of vehicles, improving fuel efficiency and performance without sacrificing safety or durability.
What is Fibre reinforced polymer used for?
Construction: Rebar, panels, bridges, and other structural elements.
Marine: Boat hulls, decks, and docks.
Automotive: Body panels, chassis components, and underbody protection.
Aerospace: Lightweight components and structural parts.
Industrial: Chemical storage tanks, piping, and gratings.
Energy: Wind turbine blades and other renewable energy components.
FRP’s versatility and performance make it a valuable material in these demanding applications.
How strong is fiberglass reinforced nylon?
Higher Tensile Strength: The fiberglass reinforcement increases the tensile strength of the nylon, making it more suitable for load-bearing applications.
Improved Stiffness: The fiberglass fibers also increase the stiffness of the material, reducing its flexibility compared to unreinforced nylon.
Enhanced Dimensional Stability: Fiberglass reinforcement helps the nylon maintain its shape under heat and stress.
These properties make fiberglass reinforced nylon a popular choice in automotive, industrial, and consumer products where high strength and durability are required.
What is the difference between GRp and fibreglass?
Fiberglass: Refers to the glass fibers themselves, which are used as a reinforcing material in various composites.
GRP: Refers to the composite material made by embedding fiberglass in a plastic resin, typically polyester.
In essence, GRP is the finished composite product, while fiberglass is the reinforcing component within that product.
How strong is FRP material?
Tensile Strength: Can range from 50,000 to 200,000 psi or higher, depending on the specific FRP composite.
Impact Resistance: FRP materials have good impact resistance, especially when reinforced with high-strength fibers like carbon or aramid.
Flexural Strength: FRP composites often have high flexural strength, making them resistant to bending or deformation under load.
FRP materials are used in applications that require materials that are both strong and lightweight, offering advantages over traditional metals like steel and aluminum in specific environments.
Thank you for your interest in our products. To receive our pricelist or for any inquiries, please fill out the form below. We will get back to you within 24 hours.