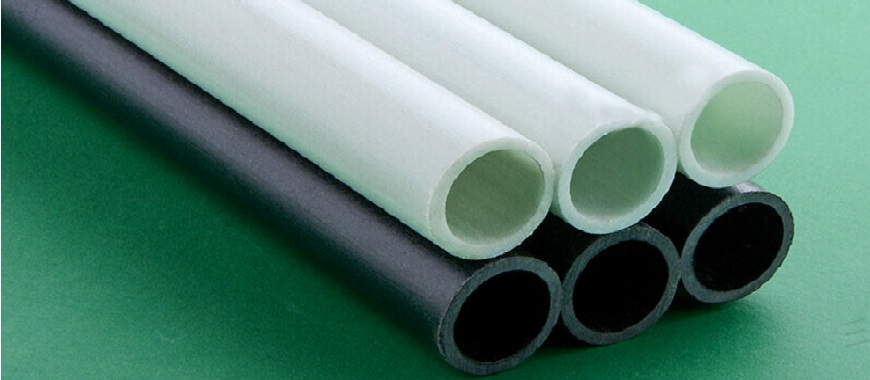
Flexible fiberglass tubes are essential components in various applications due to their unique properties. These tubes are manufactured by combining fiberglass filaments with epoxy resin, creating a composite material that offers both flexibility and strength. The process involves winding the fiberglass filaments and epoxy resin around a mandrel, followed by curing the tube to form a robust structure. While flexible fiberglass tubes excel in applications requiring adaptability, such as tent poles, antennas, or LARP boffer cores, the fiberglass scaffolding tube showcases the material’s potential for strength and stability in construction. Both types highlight the versatility of fiberglass in providing solutions tailored to specific demands, whether for lightweight structural reinforcement or heavy-duty support. Additionally, understanding the different fiberglass types helps in selecting the right material for a given application, as their properties can vary based on the intended use. Their non-conductive nature and excellent performance in acidic and corrosive environments further enhance their appeal, making them indispensable across industries. Flexible fiberglass tube is durable, lightweight, and customizable, resisting heat, chemicals, and moisture—ideal for industrial and recreational use.
Flexible Fiberglass Tube: A Comprehensive Product Overview
Explanation of Flexible Fiberglass Tubes as Composite Tubes
Flexible fiberglass tubes are a type of composite tubing that combines the durability of fiberglass with the flexibility required for various applications. These tubes are manufactured by weaving fiberglass filaments together and bonding them with high-quality epoxy resin. The process involves wrapping these fibers around a mandrel, then curing them to form a lightweight, yet sturdy structure. This method ensures that the tubes maintain a high degree of structural integrity while allowing flexibility not found in solid fiberglass rods or rigid tubes.
The composite nature of flexible fiberglass tubing means it offers the best of both worlds—fiberglass strength and flexibility. Unlike metal or plastic tubing, flexible fiberglass tubes are highly resistant to corrosion, do not conduct electricity, and are far lighter, making them ideal for industries that require strength without added weight.
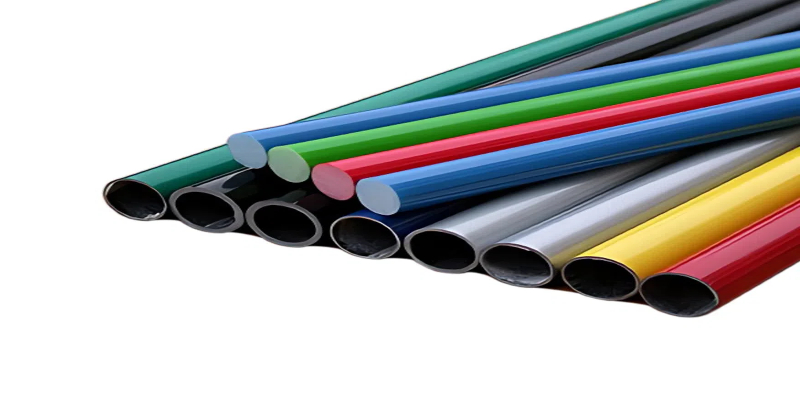
Comparison with Other Types of Fiberglass Tubes
When compared to other types of fiberglass tubes, flexible fiberglass tubes stand out primarily due to their unique balance of strength and flexibility. Traditional fiberglass tubes, such as rigid fiberglass or solid fiberglass pole, are known for their high tensile strength and durability. However, they lack the flexibility needed for applications requiring bending or movement. In contrast, flexible fiberglass tubing retains much of the strength of standard fiberglass while offering a significant increase in flexibility.
Additionally, flexible fiberglass tubing, especially in its flexible hollow fiberglass tube form, is notably lighter than rigid fiberglass tubes. This lightweight characteristic is a key benefit for users in industries such as outdoor recreation (for tent poles or fishing rods) or telecommunications (for antennas), where minimizing weight is critical for ease of use and transport. The combination of a high strength-to-weight ratio, flexibility, and non-conductive properties makes flexible fiberglass tubing an ideal choice for many specialized applications.
Flexible fiberglass tubes offer versatility and reliability. They provide a unique composite solution that meets the demands for flexibility without compromising on strength, offering substantial advantages over rigid and solid fiberglass pole alternatives.
How to Choose the Right Tapered Fiberglass Tube Size
Key Features of Flexible Fiberglass Tubes
Flexible fiberglass tubes offer a variety of features that make them highly versatile for a wide range of applications. Below is a detailed exploration of the key characteristics of flexible fiberglass tubing, illustrating its advantages over more rigid alternatives.
High Flexibility Compared to Rigid Fiberglass Tubes
One of the most significant features of flexible fiberglass tubes is their superior flexibility compared to rigid fiberglass tubes. While traditional fiberglass tubing is known for its high tensile strength, it often lacks the ability to bend or move without breaking. Flexible fiberglass tubing, on the other hand, is designed to accommodate bending and twisting without losing its structural integrity. This makes it ideal for applications where movement is necessary, such as in antennas or tent poles, where flexibility can improve durability and ease of installation. The combination of flexibility and fiberglass tube strength ensures that the tubing can withstand stress while maintaining its shape and function.
Feature | Flexible Fiberglass Tubes | Rigid Fiberglass Tubes |
---|---|---|
Flexibility | High | Low |
Bending Resistance | Moderate | High |
Preferred Application | Dynamic structures | Static structures |
Functional Capabilities of Flexible Fiberglass Tubing
The functionality of flexible fiberglass tubing is defined by its mechanical resilience, adaptability, and resistance to environmental factors. These tubes are designed to perform in demanding conditions while remaining lightweight and easy to install.
- Bendability for Complex Routing – One of the most significant advantages of flexible fiberglass tubing is its ability to bend and curve without breaking. This property makes it highly useful for tight spaces, intricate pathways, and dynamic applications where rigid tubing would fail.
- Electrical and Thermal Insulation – The non-conductive nature of fiberglass makes these tubes highly effective for electrical insulation applications. They are commonly used in antenna supports, power distribution systems, and telecommunication infrastructure, ensuring safe and interference-free operation.
- Environmental and Chemical Protection – Fiberglass tubing is highly resistant to corrosion, chemicals, and extreme environmental conditions. Unlike metal alternatives, these tubes do not rust, degrade, or weaken when exposed to moisture, acids, or harsh weather conditions, making them ideal for marine, chemical, and outdoor applications.
Key Characteristics of Flexible Fiberglass Tubing
The defining features of fiberglass tubing make it a preferred choice for structural reinforcement, lightweight applications, and environments requiring durability.
- Lightweight Yet Durable – A crucial benefit of flexible fiberglass tubing is its lightweight construction. Despite being much lighter than metal, it does not compromise on strength. The combination of fiberglass filaments and epoxy resin creates a structure that withstands stress while remaining easy to transport and handle. This characteristic is particularly valuable in industries like outdoor recreation and telecommunications, where reducing weight is critical for installation efficiency and cost savings.
- High Strength-to-Weight Ratio – The strength-to-weight ratio of flexible fiberglass tubes is one of their most valuable properties. This ratio determines how much load a material can bear relative to its weight, and fiberglass tubing excels in this aspect. It provides structural reinforcement without the bulk of steel or aluminum, making it ideal for tent poles, lightweight construction supports, and industrial frameworks.
- Fire and Heat Resistance – Fiberglass is inherently non-combustible, allowing these tubes to withstand high temperatures and fire hazards. This makes them suitable for use in fire-sensitive environments and high-temperature applications where traditional plastic or metal materials would fail.
Structural and Design Aspects of Flexible Fiberglass Tubing
The manufacturing process and structural design of flexible fiberglass tubing allow it to be customized for specific industry needs, ensuring consistent quality and performance.
- Multi-Layered Reinforcement – These tubes are composed of fiberglass-reinforced composites, enhancing their strength, flexibility, and resilience under stress. The material is engineered to withstand mechanical strain, bending, and environmental wear.
- RF and EM Transparency – Unlike metal conduits, fiberglass tubing is radio frequency (RF) and electromagnetic (EM) transparent, meaning it does not interfere with signals. This makes it an essential material for telecommunications, aerospace structures, and sensitive electronic enclosures.
- Ease of Installation and Manufacturing – Due to its lightweight nature and versatile manufacturing process, fiberglass tubing can be customized, cut, and installed with minimal effort, reducing installation costs and labor time. Its variety and consistency ensure reliable performance across different applications and industries.
Flexible fiberglass tubing offers a perfect balance of flexibility, strength, lightweight construction, and resistance to environmental stressors. Its high strength-to-weight ratio, non-conductive properties, and corrosion resistance make it an ideal material for electrical insulation, industrial piping, structural reinforcement, and outdoor applications. Compared to traditional materials like metal and plastic, fiberglass tubing provides superior longevity, cost efficiency, and adaptability. As technology advances, the demand for lightweight, durable, and high-performance tubing solutions will continue to drive the widespread adoption of fiberglass composites in various industries.
Green Thread Fiberglass Pipe: A Reliable Solution
Applications of Flexible Fiberglass Tube
The flexible fiberglass tube is a versatile material with a wide range of applications across several industries. Its unique combination of flexibility, durability, and lightweight properties makes it ideal for various purposes. Below, we explore some of the most common uses of flexible fiberglass tubes, highlighting their specific advantages in different fields.
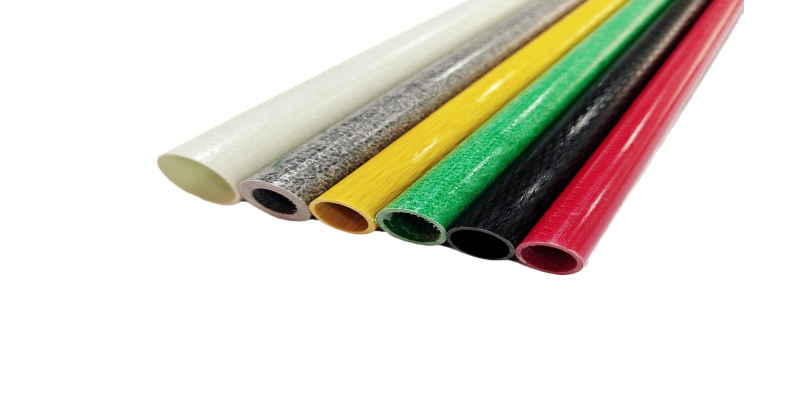
Tent Poles for Outdoor Camping
One of the most prominent applications of flexible fiberglass tubing is in the outdoor camping industry, particularly for tent poles. Tents rely on poles that are both strong and flexible to provide the necessary structural support while being lightweight for portability. Flexible fiberglass tubes excel in this regard. Their flexibility allows the tent poles to bend without breaking, ensuring the tent remains stable even in windy conditions. Furthermore, the lightweight nature of these tubes makes them easy to carry, an essential feature for backpackers and campers who need to minimize weight in their gear. In similar applications, a fiberglass bondage tube can offer similar benefits, providing durability and flexibility for other outdoor gear.
Flexible fiberglass tubing is highly resistant to corrosion and moisture, ensuring that tent poles made from this material can withstand long-term exposure to outdoor elements without deteriorating. Unlike metal poles that can rust or warp, fiberglass remains structurally sound, providing a reliable solution for outdoor enthusiasts.
Antenna Structures in Telecommunications
In the telecommunications industry, antennas require materials that are not only strong and durable but also flexible enough to withstand environmental stressors such as wind, temperature changes, and physical impacts. Flexible fiberglass tubes are an excellent choice for constructing antenna masts and supports due to their non-conductive properties, lightweight design, and flexibility.
The non-conductive nature of flexible fiberglass tubing is particularly important for telecommunications equipment, where electrical insulation is critical to prevent interference with signals. Moreover, the high strength-to-weight ratio ensures that antenna structures remain stable even in high-wind environments, providing a long-lasting and low-maintenance solution.
The inherent flexibility of these tubes allows for the slight bending and movement needed to absorb environmental stresses without causing damage to the antenna. This ensures consistent performance and reduces the risk of equipment failure in extreme conditions, making fiberglass tube/component products a preferred material for both small and large-scale antenna structures.
Fishing Rod Blanks
Fishing rods are another product that benefits greatly from the properties of flexible fiberglass tubing. In particular, fishing rod blanks made from fiberglass are known for their lightweight, flexible, and strong construction. These blanks serve as the core structure of fishing rods, and the flexibility provided by flexible fiberglass tubes enhances the rod’s ability to bend and flex under the pressure of a fish, reducing the risk of breaking while providing a better overall fishing experience.
Fishing fiberglass rod blank suppliers often provide high-quality blanks that are favored by anglers for their forgiving nature, especially in situations where strength and durability are paramount. While other materials such as graphite offer stiffness and sensitivity, flexible fiberglass tubing provides the balance needed for various fishing techniques, particularly when fishing for larger or more powerful fish species. The lightweight design of the fiberglass tube also ensures that the fishing rod remains easy to handle over long periods, reducing arm fatigue and enhancing user comfort.
Additional Applications
Beyond the primary uses mentioned, flexible fiberglass tubes are also employed in a wide array of other industries. In the construction industry, these tubes, along with fiberglass extruded tubes, are used in structural supports and reinforcements due to their high strength-to-weight ratio. Their non-conductive and corrosion-resistant nature makes them ideal for electrical insulation, where they play a role in various types of wiring and cable management systems.
Flexible fiberglass tubing is frequently used in recreational products such as bows for archery, boffer swords for live-action role-playing (LARP), and even in kite frames due to its flexibility and resilience. Its versatile nature continues to make it a go-to material for any application requiring a lightweight yet durable solution.
Elastomeric Coating: The Role of Fiberglass Tape
For businesses and industries with unique requirements, flexible fiberglass tubing also offers extensive customization options. Whether you need tubing in specific diameters, lengths, or even tailored for particular environmental conditions, manufacturers often provide customizable solutions to meet these needs. This flexibility in design ensures that the tubes can be adapted for specialized applications, whether in industrial, commercial, or recreational settings.
The versatility of flexible fiberglass tubing cannot be overstated. Its ability to provide strength, flexibility, and durability across multiple industries makes it a preferred choice for many professionals. For those seeking a material that can meet specific performance criteria, exploring the range of available products and customization options for flexible fiberglass tubing is highly recommended. Whether you’re designing new products or enhancing existing ones, flexible fiberglass tubes offer a dependable and adaptable solution tailored to meet your exact needs.
Types of Flexible Fiberglass Tubes
Flexible fiberglass tubes are available in multiple variations, each tailored to specific applications that demand a balance of strength, flexibility, and durability. These tubes are widely used in industrial, commercial, and recreational settings due to their lightweight nature, corrosion resistance, and ability to withstand environmental stresses such as high temperatures and chemical exposure. Choosing the right type of flexible fiberglass tube depends on several factors, including the intended operating environment, the mechanical stresses it will endure, and any special resistance requirements.
Below, we explore the major types of flexible fiberglass tubes, delving into their unique properties and applications to help you make the best choice for your needs.
Standard Flexible Fiberglass Tubes
Standard flexible fiberglass tubes are the most commonly used type, offering a well-balanced combination of strength, flexibility, and cost-effectiveness. These tubes are designed for general-purpose applications where moderate mechanical stress and environmental exposure are expected.
Key Features:
- Lightweight yet strong, making them easy to handle and install.
- Moderate flexibility allows them to bend without breaking, accommodating slight movement and vibration.
- Resistant to corrosion, moisture, and mild environmental conditions.
Applications:
- Used in lightweight structural supports, such as framework and casings.
- Ideal for protective covers, conduit systems, and electrical insulation.
- Commonly found in recreational equipment, DIY projects, and various industrial applications where extreme resistance is not required.
High-Temperature Flexible Fiberglass Tubes
In high-heat environments, traditional materials tend to weaken, melt, or degrade. High-temperature flexible fiberglass tubes are specifically designed to withstand extreme heat without losing structural integrity, making them indispensable in applications where thermal stability is crucial.
Key Features:
- Manufactured using heat-resistant resins that prevent softening or degradation at elevated temperatures.
- Can withstand exposure to open flames, making them useful in fire-prone environments.
- Maintains flexibility even under high heat conditions, reducing the risk of cracking or breaking.
Applications:
- Aerospace and automotive industries, where materials must endure extreme heat from engines and exhaust systems.
- Industrial furnaces, kilns, and heat insulation in manufacturing plants.
- Electrical insulation for high-temperature wiring and heat-sensitive components.
Chemically Resistant Flexible Fiberglass Tubes
Certain environments expose materials to aggressive chemicals that can weaken, corrode, or degrade them over time. Chemically resistant flexible fiberglass tubes are engineered to resist harsh chemicals, making them ideal for applications involving acids, solvents, and other corrosive substances.
Key Features:
- Special resin formulations provide high resistance to a broad range of chemicals.
- Non-reactive surface ensures longevity even in highly corrosive environments.
- Maintains mechanical strength and flexibility despite continuous chemical exposure.
Applications:
- Used in chemical processing plants, where exposure to corrosive fluids is common.
- Ideal for laboratory equipment, ensuring safe containment of reactive substances.
- Suitable for wastewater treatment plants, preventing degradation from sewage chemicals and industrial waste.
Custom-Shaped Flexible Fiberglass Tubes
Sometimes, standard tube shapes and sizes do not meet the requirements of specialized applications. Custom-shaped flexible fiberglass tubes are manufactured to precise specifications, ensuring optimal fit, performance, and efficiency. These tubes are used when unique mechanical properties, complex designs, or specific size constraints are necessary.
Key Features:
- Fully customizable in shape, size, and thickness based on application needs.
- Can be designed for enhanced flexibility, rigidity, or a combination of both.
- Provides tailored solutions for complex industrial and commercial applications.
Applications:
- Used in specialized machinery where exact dimensions and mechanical properties are required.
- Custom reinforcements for aerospace and automotive parts.
- Architectural and structural applications requiring unique fiberglass components.
Flexible fiberglass tubes offer a wide range of properties suited for various demanding applications. Whether you need a standard tube for general use, a heat-resistant option for high-temperature environments, a chemically resistant tube for corrosive conditions, or a custom-shaped solution for specialized needs, there is a fiberglass tube designed for your exact requirements. By understanding the distinct characteristics of each type, you can make informed decisions to ensure long-lasting performance and efficiency in your specific application.
Advantages of Using Flexible Fiberglass Tubes
Flexible fiberglass tubes offer numerous advantages over traditional materials such as metal, plastic, and wood. Their unique combination of strength, flexibility, durability, and environmental benefits makes them an ideal choice for various industrial and commercial applications. Whether used in construction, electrical insulation, or engineering projects, flexible fiberglass tubes provide long-term efficiency and cost savings. Below, we explore the key advantages of using flexible fiberglass tubes in different aspects.
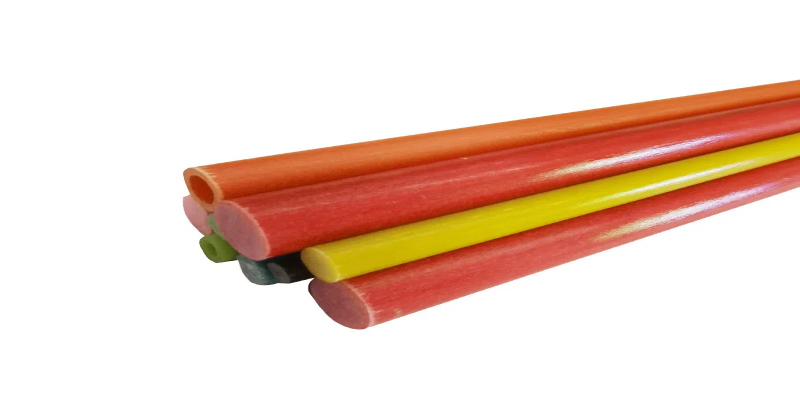
Economical and Efficient
One of the primary reasons for choosing flexible fiberglass tubes is their cost-effectiveness over time. Although the initial investment may be higher than some plastic alternatives, their durability and long service life make them a more economical choice in the long run.
Key Benefits:
- Reduced maintenance and replacement costs due to superior durability.
- Resistant to corrosion, moisture, and chemical damage, ensuring longer usability.
- Lightweight nature lowers transportation and installation costs, improving overall efficiency.
Environmentally Friendly
As sustainability becomes a priority in manufacturing and construction, flexible fiberglass tubes stand out as an eco-friendly material. Their production involves sustainable resources, and they have a lower environmental impact compared to many synthetic alternatives.
Key Benefits:
- Made from reinforced glass fibers, which are derived from natural materials.
- Longer lifespan reduces waste generation and the need for frequent replacements.
- Does not release harmful chemicals into the environment, unlike some plastics.
Versatile and Widely Used
Flexible fiberglass tubes are highly adaptable and are used across multiple industries, from construction and aerospace to telecommunications and marine applications. Their versatility makes them an essential material in various engineering and industrial projects.
Key Benefits:
- Suitable for structural applications, support frames, and lightweight reinforcements.
- Used in electrical insulation due to its non-conductive properties.
- Ideal for marine and outdoor environments because of its resistance to water and UV exposure.
Enhanced Safety Features
Safety is a crucial factor when selecting materials for industrial and engineering applications. Flexible fiberglass tubes offer several protective advantages, making them a preferred choice in high-risk environments.
Key Benefits:
- Non-conductive: Unlike metals, fiberglass does not conduct electricity, making it safer for electrical insulation and wiring protection.
- Fire-resistant: With high heat tolerance, flexible fiberglass tubes reduce fire hazards and are used in applications where flame resistance is required.
- Chemical and moisture resistance: Ensures protection against corrosion and degradation, maintaining structural integrity in harsh environments.
Flexible fiberglass tubes provide a well-rounded combination of durability, efficiency, sustainability, versatility, and safety. Their long lifespan and resistance to environmental stressors make them an economical choice for industries looking to reduce costs while maintaining high performance. Whether for structural support, insulation, or specialized applications, flexible fiberglass tubes continue to be a reliable and practical material across multiple sectors.
How to Choose a Manufacturer for Flexible Fiberglass Tubes
Selecting the right manufacturer for flexible fiberglass tubes is crucial to ensuring product quality, reliability, and long-term performance. A reputable manufacturer should offer high-quality materials, advanced production techniques, customization options, and excellent customer support. Several factors need to be considered when choosing a manufacturer, including their experience, production capabilities, certifications, and industry reputation. Below, we explore the key aspects to evaluate when selecting a flexible fiberglass tube manufacturer.
Experience and Industry Expertise
A manufacturer’s experience in producing flexible fiberglass tubes is a strong indicator of their ability to deliver high-quality products. Established companies with years of expertise tend to have refined production processes, better quality control, and a deep understanding of customer needs.
Key Considerations:
- Look for manufacturers with a proven track record in fiberglass tube production.
- Assess their experience in serving industries relevant to your needs, such as construction, automotive, or aerospace.
- Check their portfolio and past projects to determine the quality and variety of their fiberglass tubes.
Advanced Manufacturing Technology
The quality of flexible fiberglass tubes is directly influenced by the manufacturing technology and processes used by the manufacturer. A company with state-of-the-art production facilities can ensure consistent quality, precision, and efficiency in fiberglass tube manufacturing.
Key Considerations:
- Check if the manufacturer uses advanced resin infusion, pultrusion, or filament winding processes.
- Ensure they have modern equipment for quality control, such as automated testing and precision molding.
- Evaluate whether their production capabilities meet your specific requirements, such as flexibility, durability, and chemical resistance.
Product Quality and Certifications
A reliable manufacturer should meet international quality standards and have the necessary certifications to ensure the safety and performance of their flexible fiberglass tubes. Certifications indicate compliance with industry regulations and quality assurance protocols.
Key Considerations:
- Verify if the manufacturer holds certifications such as ISO 9001 (quality management) or UL certification (safety and performance compliance).
- Look for fiberglass tubes that meet ASTM or other industry-specific standards.
- Check if they perform rigorous testing for durability, heat resistance, and chemical resistance.
Customization and Product Variety
Different applications require different types of flexible fiberglass tubes. A manufacturer that offers customization options ensures that you get a product tailored to your specific needs.
Key Considerations:
- Choose a manufacturer that provides various tube types, including standard, high-temperature, and chemically resistant fiberglass tubes.
- Ensure they offer customization options in terms of dimensions, flexibility, wall thickness, and resin type.
- Inquire about their ability to create specialized shapes or reinforced designs for unique applications.
Reputation and Customer Reviews
A manufacturer’s reputation in the industry is a key factor in determining their reliability and product quality. Customer feedback, industry recognition, and case studies provide insight into their level of service and product performance.
Key Considerations:
- Look for online reviews, testimonials, or ratings from previous customers.
- Research the manufacturer’s reputation through industry forums, trade shows, or professional networks.
- Check if they have partnerships with well-known companies or industries that use fiberglass tubes.
Pricing and Cost Efficiency
While price is an important factor, it should not be the only consideration when selecting a manufacturer for flexible fiberglass tubes. The goal is to find a balance between cost and quality to ensure long-term value.
Key Considerations:
- Compare pricing with other manufacturers while considering material quality and durability.
- Beware of extremely low-cost options that may compromise product performance.
- Ask about bulk purchase discounts, shipping costs, and after-sales support.
Customer Service and Technical Support
A good manufacturer should provide excellent customer service, technical support, and assistance throughout the purchasing process. This ensures a smooth experience and helps resolve any issues that may arise.
Key Considerations:
- Evaluate their response time to inquiries and technical questions.
- Ensure they provide clear product documentation, installation guides, and maintenance recommendations.
- Check if they offer warranties, returns, or after-sales support for their fiberglass tubes.
Choosing the right manufacturer for flexible fiberglass tubes requires careful consideration of multiple factors, including experience, production technology, quality certifications, customization options, and customer service. A well-established manufacturer with advanced manufacturing capabilities and a strong reputation can provide high-quality fiberglass tubes that meet your specific needs. By evaluating these key aspects, you can ensure a reliable and long-lasting investment in flexible fiberglass tubes.
FAQs about Flexible Fiberglass Tube
Yes, fiberglass can be flexible depending on how it is manufactured. Traditional fiberglass is often known for its rigidity and strength, but when made into a flexible fiberglass tubing, it can have a significant amount of flexibility. This is achieved by combining fiberglass filaments with resins in a way that allows for movement and bending without breaking. Flexible fiberglass tubes are commonly used in applications that require durability but also the ability to bend, such as fishing rods, tent poles, and antennas. However, it’s important to note that not all fiberglass is flexible. Some forms, such as solid fiberglass rods or panels, are more rigid and designed to provide structural support without bending.
Fiberglass conduit can be flexible, though it largely depends on the specific type and application. Conduit made from flexible fiberglass tubing is often used in electrical systems where non-conductive, lightweight, and corrosion-resistant properties are essential. Flexible fiberglass conduit is especially useful in environments exposed to moisture or corrosive substances because it does not rust or deteriorate like metal conduit. The flexibility of fiberglass conduit allows for easier installation in tight or irregular spaces, reducing the need for additional connectors or fittings. However, like other fiberglass products, not all fiberglass conduits are equally flexible. Some are designed to be more rigid for use in high-stress applications where structural support is more critical.
Fiberglass resin itself is typically not flexible in its cured state. Fiberglass resin is a hard, durable substance that binds fiberglass filaments together to form a strong, rigid structure. Once the resin cures, it becomes a hard shell that is very resistant to bending. However, when used with flexible fiberglass tubing, the resin is applied in a way that allows the finished product to retain some flexibility. The flexibility comes from the way the fiberglass filaments are arranged, rather than from the resin itself. There are specific types of resins, like flexible epoxy resins, which offer some degree of bendability, but generally, fiberglass resin is designed to create a hard, rigid surface for maximum durability.
Fiberglass rods can indeed be flexible, depending on how they are made. Flexible fiberglass rods are used in a variety of applications where bending or flexing is necessary, such as in fishing rods or tent poles. These rods provide an excellent balance between strength and flexibility, making them ideal for situations where resistance to breakage is essential. For instance, fishing rods made from fiberglass can flex under the pressure of a catch, preventing them from snapping. However, not all fiberglass rods are made to be flexible. Some are designed to be more rigid for use in applications where stiffness and structural support are required, such as in building reinforcements or industrial settings. Therefore, whether a fiberglass rod is flexible or not depends on its specific design and intended use.
Flexible fiberglass tubes and rods are generally tougher and more impact-resistant than graphite (carbon fiber), though they are not necessarily stronger in terms of stiffness or tensile strength. Graphite rods are stiffer and lighter but more brittle, making them prone to breaking under sudden stress. In contrast, flexible fiberglass tubes offer a balance of strength and flexibility, making them ideal for applications requiring durability and moderate bending.
Yes, flexible fiberglass tubes and rods are highly effective in various applications. They provide excellent durability, resistance to environmental factors like moisture and chemicals, and a balance of strength and flexibility. Compared to other materials like metal or carbon fiber, fiberglass is lightweight, cost-effective, and less prone to corrosion, making it a great choice for industrial, recreational, and structural applications requiring moderate flexibility and strength.
Yes, flexible fiberglass tubes can hold significant weight, depending on their thickness, diameter, and structural composition. While not as rigid as metal, fiberglass has a high strength-to-weight ratio and can withstand heavy loads without breaking. It is commonly used in structural applications, such as support beams, tool handles, and lightweight frames, where both durability and flexibility are needed.
Yes, flexible fiberglass tubes are designed to bend without breaking. Unlike rigid materials like carbon fiber, fiberglass maintains strength while allowing for controlled flexing. This property makes it useful in applications requiring movement, such as fishing rods, antenna masts, and flexible support structures. The degree of flex depends on the thickness and composition of the fiberglass.
Yes, flexible fiberglass tubes and rods can be bent to a certain degree without breaking. Their flexibility depends on the diameter and the specific fiberglass composition. While they can withstand bending, excessive force or repeated stress can cause cracking or permanent deformation. Proper handling and gradual bending help maintain their integrity.
Yes, flexible fiberglass tubes can degrade over time due to prolonged exposure to UV radiation, extreme temperatures, and environmental factors like moisture and chemicals. However, fiberglass is highly durable, and with proper maintenance, it can last for decades. Protective coatings or additives can extend its lifespan and maintain its strength.
Yes, prolonged exposure to UV light, moisture, and chemical reactions can reduce the strength of flexible fiberglass tubes over time. However, this process is slow, and with proper care—such as protective coatings or indoor storage—fiberglass can retain its structural integrity for many years without significant strength loss.
Fiberglass itself cannot be softened like metals or plastics, but flexible fiberglass tubes can be temporarily heated to make them more pliable. Heating must be controlled, as excessive heat can weaken the material. Additionally, adding resins or specialized coatings can enhance flexibility for specific applications.
Corrugated fiberglass, like flexible fiberglass tubes, can last 20–50 years, depending on exposure to sunlight, moisture, and mechanical stress. UV-resistant coatings and proper maintenance significantly extend its lifespan, making it a durable material for roofing, siding, and industrial applications.
Flexible fiberglass tubes are significantly stronger than vinyl, offering higher tensile strength, impact resistance, and durability. Fiberglass can withstand heavier loads, temperature fluctuations, and environmental stress without deforming, whereas vinyl is more prone to warping, cracking, and wear over time.
Materials such as carbon fiber, steel, and certain high-performance composites are stronger than flexible fiberglass tubes. Carbon fiber, for example, has a much higher strength-to-weight ratio and stiffness, but it is more brittle and expensive. Steel offers superior tensile strength but is significantly heavier and prone to corrosion. While fiberglass is not the strongest material, it provides an excellent balance of strength, flexibility, and durability, making it ideal for applications requiring moderate strength with resistance to environmental factors like moisture and chemicals.
Flexible fiberglass tubes, while durable, have some weaknesses. They are not as stiff as carbon fiber or metals, meaning they can bend under heavy loads. Prolonged UV exposure can degrade the material over time, leading to brittleness. Additionally, fiberglass can be prone to surface wear and splintering if not properly coated. While it resists chemicals and moisture well, extreme impact forces can cause cracking.
If fiberglass particles from a flexible fiberglass tube get into your hand, avoid rubbing the area, as this can push the fibers deeper into the skin. Wash the affected area with warm water and mild soap to help remove fibers. Using adhesive tape can help lift embedded fibers. If irritation persists, apply a soothing lotion and monitor for any signs of infection. Wearing gloves while handling fiberglass is recommended to prevent exposure.
Fiberglass conduit, including flexible fiberglass tubes, is ideal for applications requiring non-corrosive, lightweight, and electrically non-conductive properties. It is commonly used in environments where exposure to chemicals, moisture, or extreme temperatures would degrade traditional metal conduits. Industries like telecommunications, wastewater treatment, and marine applications benefit from fiberglass conduit’s durability and resistance to environmental stress.
Fiberglass rods, including flexible fiberglass tubes, are more durable and resistant to moisture and environmental damage than bamboo rods. Bamboo rods offer a classic feel and natural flexibility but require more maintenance and are prone to cracking over time. Fiberglass rods provide better longevity, moderate flexibility, and resilience, making them ideal for applications where durability is key.
Fiberglass pipe insulation is better for high-temperature applications and provides superior thermal resistance, making it a great choice for industrial settings. Flexible fiberglass tubes used in insulation maintain their form under heat and resist moisture. Foam insulation, while easier to install and lightweight, is better suited for lower-temperature applications but may degrade faster in extreme conditions.
Flexible fiberglass tubes are stronger, more heat-resistant, and more durable than PVC. Fiberglass withstands higher temperatures, resists corrosion, and offers better mechanical strength. PVC, while cheaper and easier to work with, is more prone to degradation from UV exposure and extreme temperatures. For applications requiring strength and longevity, fiberglass is the better choice.
Fiberglass is generally stronger than acrylic in terms of impact resistance and durability. Flexible fiberglass tubes can handle bending and external forces better, while acrylic is more brittle and prone to cracking. However, acrylic has better optical clarity and is often used for aesthetic applications like windows and displays.
Polycarbonate is more impact-resistant than fiberglass, making it a better choice for applications requiring shatterproof properties. However, flexible fiberglass tubes offer better tensile strength and stiffness, making them ideal for structural applications where weight and flexibility are factors. Polycarbonate is commonly used for protective barriers, while fiberglass is preferred for reinforcement and durability.
Fiberglass is significantly stronger than polyester in terms of tensile strength and durability. While polyester is a flexible and lightweight material, it lacks the structural integrity and rigidity of flexible fiberglass tubes. Fiberglass is used in industrial, structural, and reinforcement applications where strength and longevity are required.
Fiberglass is generally more expensive than plastic due to its superior mechanical properties, durability, and resistance to environmental factors. While standard plastic materials such as PVC or polyethylene are cheaper to manufacture and process, flexible fiberglass tubes provide better strength, flexibility, and longevity. The higher cost of fiberglass comes from the raw materials used—typically glass fibers embedded in a resin matrix—and the complex manufacturing process. However, in applications requiring high strength, corrosion resistance, and flexibility, fiberglass can be a more cost-effective long-term solution. Unlike plastic, fiberglass does not degrade as quickly under UV exposure or chemical stress, making it a preferred choice in demanding applications. For those needing a balance of flexibility and durability, investing in fiberglass tubing may be more cost-efficient over time despite the initial cost being higher than standard plastic alternatives.
Fiberglass conduit is generally more expensive than PVC due to its enhanced durability, flexibility, and resistance to corrosion. While PVC conduit is widely used because of its low cost and ease of installation, it lacks the mechanical strength and temperature resistance of fiberglass. Flexible fiberglass tubes used as conduits offer higher impact resistance, non-conductivity, and resistance to extreme temperatures and chemicals, making them ideal for industrial and outdoor applications. In the long run, fiberglass conduits can be more cost-effective because they require less maintenance and replacement than PVC, especially in environments exposed to moisture, UV radiation, or corrosive substances. However, if cost is the primary concern and environmental factors are not an issue, PVC remains the more economical choice. The decision between the two depends on the application’s demands for strength, flexibility, and longevity.
Yes, flexible fiberglass tubes are generally more flexible than aluminum tubes of similar thickness. Fiberglass exhibits a higher degree of bendability and elasticity, making it more suitable for applications requiring shock absorption and adaptability to movement. Aluminum, while lightweight and strong, tends to be more rigid and may dent or deform under excessive stress, whereas fiberglass can bend and return to its original shape without significant deformation. Additionally, fiberglass offers vibration damping, which makes it ideal for structural applications in aerospace, marine, and industrial sectors where flexibility is required. Moreover, fiberglass does not conduct electricity, making it safer for electrical conduit applications compared to aluminum. In applications where a combination of flexibility, strength, and insulation properties is needed, flexible fiberglass tubing is the preferred choice over aluminum.
Yes, flexible fiberglass tubes are significantly more flexible than steel. While steel is stronger in terms of absolute tensile and compressive strength, it is rigid and prone to permanent deformation or breaking under excessive bending forces. Fiberglass, on the other hand, can bend without losing its structural integrity, making it more adaptable to curved installations and dynamic loads. This flexibility makes fiberglass tubing ideal for vibration-prone environments, flexible conduits, and structural components requiring adaptability. Additionally, fiberglass is lighter than steel, making it easier to handle and install in various applications. Its non-corrosive nature also gives it an edge in marine, chemical, and outdoor applications where steel might rust. While steel remains the material of choice for heavy-load structural applications, fiberglass is the better option for lightweight, flexible, and corrosion-resistant tubing solutions.
Fiberglass is not stretchable in the same way as elastic materials like rubber or thermoplastics. While flexible fiberglass tubes can bend and flex without breaking, they do not exhibit significant elongation when pulled under tension. Fiberglass is composed of glass fibers embedded in a polymer resin matrix, giving it excellent tensile strength but very low elasticity. If excessive tensile stress is applied, fiberglass will eventually fracture rather than stretch. However, its ability to bend without permanent deformation makes it suitable for applications requiring flexibility without stretching, such as flexible piping, reinforcement structures, and electrical conduit systems. While fiberglass itself does not stretch, certain composite formulations allow for enhanced flexibility without compromising strength.
Yes, fiberglass is very strong in tension. Flexible fiberglass tubes benefit from the high tensile strength of glass fibers, which can withstand substantial stretching forces before breaking. This property makes fiberglass an excellent material for applications requiring durability under tension, such as reinforcement rods, cables, and pressure-resistant tubing. Compared to metals like steel, fiberglass has a higher strength-to-weight ratio, meaning it can handle significant loads without adding excessive weight. Its ability to maintain structural integrity under stress is why it is widely used in composite structures, aerospace, and marine industries. However, fiberglass’s tensile strength depends on the fiber orientation, meaning that unidirectional fiberglass composites have the highest tensile strength along the fiber direction. For flexible tubing applications, fiberglass remains a strong and reliable material under tensile forces.
No, fiberglass is not stronger than Kevlar in terms of tensile strength. Kevlar, an aramid fiber, is specifically designed for high-tensile strength and impact resistance, making it the preferred choice for bulletproof vests, aerospace applications, and high-performance composites. However, fiberglass excels in compressive strength, corrosion resistance, and overall rigidity, making it more suitable for structural and tubing applications. While Kevlar is more impact-resistant, fiberglass offers greater durability in environments exposed to moisture, chemicals, and extreme temperatures. Flexible fiberglass tubes are used in applications requiring strength with flexibility, whereas Kevlar is often employed in scenarios demanding exceptional tensile strength and lightweight performance. Ultimately, the choice between fiberglass and Kevlar depends on the specific mechanical requirements of the application.
Yes, fiberglass is stronger than most plastics in terms of tensile strength, impact resistance, and durability. Flexible fiberglass tubes are reinforced with glass fibers, giving them higher mechanical strength and resistance to deformation compared to conventional plastics like PVC, polyethylene, or polypropylene. Fiberglass can withstand higher loads, extreme temperatures, and harsh environmental conditions, making it ideal for structural, electrical, and industrial applications. Unlike plastic, which may warp or degrade under UV exposure, fiberglass maintains its integrity over time, especially in outdoor or chemically exposed environments. While plastics are cheaper and easier to manufacture, fiberglass offers a superior strength-to-weight ratio and a longer lifespan, making it the preferred material for demanding applications where flexibility and strength are essential.
The three main types of fiberglass are:
E-Glass (Electrical Glass) – The most common type, known for its good strength, electrical insulation properties, and affordability. It is widely used in fiberglass tubing, boat hulls, and insulation materials.
S-Glass (Structural Glass) – Offers higher tensile strength and durability than E-glass. It is used in aerospace, military, and high-performance applications requiring superior strength and impact resistance.
C-Glass (Chemical Glass) – Designed for enhanced chemical resistance, making it suitable for pipes, storage tanks, and industrial applications exposed to corrosive substances.
For flexible fiberglass tubes, E-glass is the most common, but S-glass may be used for high-strength applications.
When you touch fiberglass, especially in its raw or unfinished form, tiny glass fibers can penetrate the skin, causing irritation, itching, and discomfort. These fibers are microscopic and sharp, leading to a prickly sensation and sometimes redness or a rash. In flexible fiberglass tubing, the fibers are typically embedded in resin, reducing direct skin exposure. However, cutting or sanding fiberglass tubing can release fibers into the air, which can cause skin irritation and respiratory issues if inhaled. To handle fiberglass safely, it’s recommended to wear gloves, long sleeves, and a mask when working with raw or exposed fiberglass materials. If fiberglass dust comes into contact with the skin, washing with cold water (to close pores) and mild soap can help remove the fibers and reduce irritation.
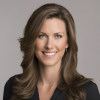
As the editor of GangLong Fiberglass, I have years of experience and in-depth research, focusing on cable tray products, fiberglass solutions, and grille systems. I incorporate years of industry insights and practical experience into every content, committed to promoting the progress of the industry. At GangLong Fiberglass, my commitment is reflected in every product, from innovative cable trays to durable fiberglass solutions and sturdy grille systems. As an authoritative voice in the industry, my goal is to provide valuable information to professionals and businesses and promote forward-looking solutions.