- Home
- FRP Cable Ladder
FRP Cable Ladder Tray Systems
GangLong Fiberglass’s lightweight yet tough FRP Cable Ladder—corrosion resistant for harsh industrial & marine environments. ABS/NEMA/IEC certified.FRP Cable Ladder are engineered for extreme environments. The FRP cable ladders’ resistance to corrosion and other harsh conditions makes them a reliable, long-term solution that enhances operational efficiency and reduces maintenance costs.
GangLong Fiberglass’s cable tray meet rigorous standards and are designed for high strength and loading capability while minimizing weight. The use of FRP cable ladder and FRP cable tray ensures significant safety and efficiency improvements during installation due to their lightweight nature. Additionally, FRP is non-magnetic and non-conductive, reducing shock hazards and interference with radio waves and microwaves. GangLong Fiberglass’s FRP cable ladder offer durability and cost-effectiveness, suitable for chemical plants, refineries, and other demanding industrial settings.
Simplifying Your Life: Key Functionalities
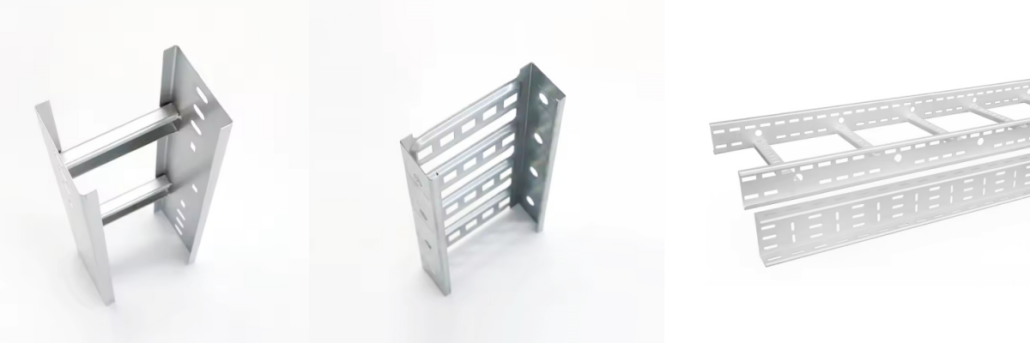
Attribute | Details |
---|---|
Type | FRP Cable Ladder |
Material | FRP (Fiberglass Reinforced Plastic), Pre-galvanized steel, stainless steel (SS304/316), aluminum |
Width Options | 50mm-1000mm |
Length Options | 2m - 10m |
Side Rail Height | 12mm-200mm |
Thickness | 0.8mm-7mm |
Surface Finish | Smooth, hot-dipped galvanized (HDG), powder-coated, pre-galvanized (PG) |
Applications | Indoor and outdoor environments, high-corrosion areas, power electric systems, Cable management solutions for power applications, construction, and industrial facilities |
Features | Aging-resistant, corrosion-resistant, high load capacity |
Colors | Customized (green, silver, orange, white, black) |
Certifications | CE, NEMA, ISO9001, UL, cUL |
Customization | Sizes, colors, and specifications |
MOQ | Standard sizes available for all quantities |
Packaging Details | Bubble film, pallets, cartons for accessories, double-layer bubble wrapping as required |
Sample Availability | Free samples available |
Delivery Time | 7-20 days depending on quantity |
Production Techniques | Molded, pultruded, laser cutting |
Project Capability | OEM and ODM services |
Quality Assurance | 100% tested for performance and durability |
News
- Exploring the Benefits of Carbon Fiber Apparel
- How to Work with Carbon Fiber Successfully
- Carbon Fiber Suit: The Future of Lightweight Armor
- Is Carbon Fiber Armor the Future of Protection?
- Why White Carbon Fiber is Popular in Automotive Design
- Transparent Carbon Fiber Sheets: Strength Meets Clarity in Design
- Chopped Carbon Fiber Mat for Lightweight Reinforcement
- Carbon Fiber EG Hatch: Upgrade Your Civic Today
- The Benefits of Using Structural Carbon Fibre in Engineering
- How Many Layers of Layered Carbon Fiber Are Needed?
FRP Cable Ladder: Standard Height
An FRP (Fiberglass Reinforced Plastic) Cable Ladder is a type of cable management system designed to support and route electrical and communication cables in various industrial and commercial environments. The standard height of an FRP cable ladder refers to the typical vertical dimension or height of the side rails, which provide structural support for the cables placed within the ladder.
- Common Height Range: The height of the side rails can vary, but common standard heights are typically between 100 mm (4 inches) to 300 mm (12 inches). This measurement is taken from the base of the ladder to the top of the side rails.
- Adjustability: Some FRP cable ladders come with adjustable heights or allow for customization in terms of side rail height to accommodate different cable sizes and installation needs.
Factors Influencing Standard Height
The height of a cable ladder plays a crucial role in ensuring the proper installation, safety, and efficiency of cable management systems. Several factors determine the required height of the cable ladder, which include:
Cable Size and Load
The size and load-bearing capacity of the cables being used significantly influence the required ladder height. Larger cables or cables with higher load demands require taller side rails to prevent sagging and ensure proper support. Cables arranged in bundles also need more space to avoid pressure on their insulation, which could lead to damage over time.
Installation Environment
Environmental factors like temperature, humidity, and exposure to corrosive substances affect the ladder height. In challenging environments such as offshore or industrial areas, taller ladders made of corrosion-resistant materials, like FRP, are essential to ensure safety and performance. These ladders also need to accommodate temperature changes, moisture, and harsh chemicals, ensuring durability and effective cable management.
Safety and Accessibility
Adequate ladder height is essential for ease of maintenance, safety, and accessibility. A higher ladder allows more clearance between the cables and surrounding structures, making it easier for maintenance personnel to perform their tasks. It also improves airflow, ensuring cables remain cool and reducing the risk of overheating. In some cases, safety regulations require minimum clearance to meet operational and safety standards.
Standards and Compliance
FRP cable ladders often comply with international standards such as:
- IEC 61537 for cable management systems.
- ASTM D638 for the material properties of FRP.
- UL 94 for fire resistance in electrical installations.
The standard height of an FRP cable ladder plays a significant role in its effectiveness in supporting cables while maintaining durability and safety in various demanding environments. Understanding the specific needs of the cable system, the environment, and load-bearing requirements will help in choosing the correct ladder height for optimal performance.
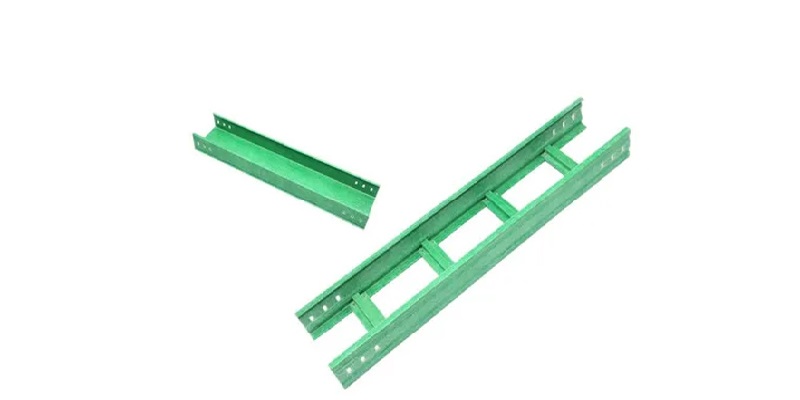
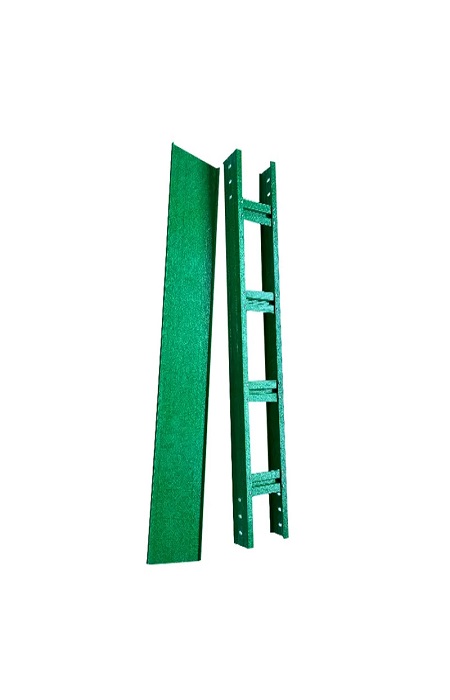
FRP Cable Ladder: Made in Different Resin Materials
An FRP (Fiberglass Reinforced Plastic) Cable Ladder can be manufactured using a variety of resin materials, each chosen based on its specific advantages for different operational conditions. The resin material used in the production of these ladders determines their strength, durability, resistance to environmental factors, and overall suitability for various applications. Below are the five common types of resin materials used in the construction of FRP cable ladders:
Polyester Resin (Unsaturated Polyester Resin)
Polyester resin is one of the most cost-effective and commonly used materials for FRP cable ladders. It offers decent mechanical properties and is suitable for general industrial applications. While it provides moderate corrosion resistance, it is not ideal for highly corrosive environments. Polyester resin also offers moderate UV stability, making it a good choice for outdoor use, though it may degrade faster under prolonged UV exposure. This resin is commonly used in general manufacturing, automotive, and agriculture industries.
Vinyl Ester Resin
Vinyl ester resin is known for its superior corrosion resistance, making it ideal for harsh chemical environments. It offers enhanced strength, durability, and heat resistance compared to polyester resin, making it suitable for more demanding applications. This resin is highly resistant to chemicals and environmental stresses, providing long-lasting durability in industries such as chemical processing, power generation, and offshore applications, where exposure to aggressive substances is common.
Epoxy Resin
Epoxy resin offers high strength, excellent adhesion, and superior corrosion resistance. It provides excellent UV stability, ensuring long-term durability for outdoor applications. Known for its superior mechanical properties, epoxy resin is suitable for demanding environments where high strength and chemical resistance are necessary. It is commonly used in critical industries like marine, aerospace, and high-performance industrial sectors, where both strength and corrosion resistance are essential for optimal performance.
Phenolic Resin
Phenolic resin is highly valued for its fire-resistant properties, making it an excellent choice for applications where fire safety is a top priority. It is also durable in high-temperature environments, though its corrosion resistance is moderate compared to other resins. This resin is commonly used in power plants, chemical factories, and other areas requiring high-temperature tolerance and fire resistance, providing added safety in industries where these properties are crucial.
Polyurethane Resin
Polyurethane resin is known for its flexibility, toughness, and impact resistance. It also provides good protection against chemicals, moisture, and water. The resin has solid UV resistance, making it suitable for both indoor and outdoor applications. Polyurethane is commonly used in environments requiring resistance to abrasion, impact, and environmental exposure, such as in the automotive, construction, and electrical industries, where durability and resilience are key.
FRP Cable Ladder: Installation Cost
The installation cost of an FRP (Fiberglass Reinforced Plastic) cable ladder depends on various factors, including the material type, ladder size, installation complexity, and the specific environment in which it is being installed. Below are the key elements that influence the total cost of installation:
1. Material Costs
- Type of Resin Used: The type of resin used in the FRP cable ladder (polyester, vinyl ester, epoxy, phenolic, or brominated) significantly impacts the price. High-performance resins (e.g., epoxy, vinyl ester) tend to be more expensive than general-purpose polyester resins.
- Ladder Size and Configuration: Larger cable ladders (wider or taller side rails, longer lengths) naturally cost more, both in terms of material and shipping. Custom configurations, such as ladders with specific supports or brackets, also add to the cost.
- Finish and Features: Some FRP cable ladders may have additional features like UV resistance, fire retardancy, or special coatings, which can increase the price.
Estimated Material Costs:
- Polyester resin-based FRP cable ladders: $20 to $40 per linear meter.
- Vinyl ester or epoxy resin-based FRP cable ladders: $40 to $80 per linear meter.
- Phenolic resin or brominated FRP cable ladders (high fire resistance): $50 to $120 per linear meter.
2. Labor Costs
Labor costs will vary depending on the complexity of the installation, the location, and the skill level of the workers involved. Installation generally includes the following:
- Site Preparation: Clearing the installation area, marking the layout, and ensuring all necessary supports are in place.
- Assembly: Unpacking, assembling, and securing the cable ladder system, including cutting, mounting, and fixing the ladders to the supports.
- Electrical Connections: Depending on the application, installing cables, wiring, and ensuring proper grounding may require licensed electricians, adding to labor costs.
- Safety Measures: If the installation site is hazardous (e.g., offshore, in high-temperature areas, or at great heights), additional safety equipment and precautions may be required, which can increase labor costs.
Estimated Labor Costs:
- Labor for basic FRP ladder installation: $15 to $30 per linear meter.
- For complex installations (e.g., in difficult-to-reach areas or high-risk environments): $30 to $60 per linear meter or more.
3. Installation Complexity
- Site Conditions: Difficult or challenging site conditions (e.g., confined spaces, extreme heights, offshore environments) may require specialized equipment, additional support structures, or extra precautions, all of which increase the overall installation cost.
- Customization Needs: If the installation requires custom bends, cuts, or fittings, or if there are special requirements (e.g., fire-resistant or explosion-proof specifications), additional work will be required, which increases both material and labor costs.
- Height and Supports: FRP cable ladders typically require mounting brackets, suspension supports, or frames. These additional components (if custom or designed for a specific load-bearing requirement) add to the installation cost.
Estimated Additional Costs for Complexity:
- Mounting brackets, supports, or frames: $10 to $30 per meter, depending on complexity.
- Custom cutting or fabrication of special shapes: $50 to $100 per hour.
- For high-risk or high-altitude installations (e.g., offshore, mining): Costs can be $100+ per linear meter, depending on safety and logistical needs.
4. Transport and Delivery
- Shipping Costs: FRP cable ladders, especially large or custom systems, may incur significant shipping or freight charges. The farther the delivery location, the higher the cost.
- Handling and Storage: On-site handling, unloading, and storage costs may also be factored into the overall installation cost, particularly for large quantities.
Estimated Shipping and Delivery Costs:
- Domestic shipping for standard installations: $500 to $1,500, depending on the size of the order.
- International shipping or delivery to remote areas: $2,000 to $5,000+.
5. Additional Costs
- Testing and Inspection: After installation, the system may need to be inspected or tested (e.g., electrical grounding, load-bearing capacity) to ensure compliance with safety standards, especially in industries like power generation, chemicals, or telecommunications.
- Maintenance Costs: Some FRP cable ladder systems may require ongoing maintenance or periodic inspections to ensure they remain in good condition, especially if exposed to extreme conditions. These costs should be factored into the long-term budget.
Total Estimated Installation Cost
To estimate the total installation cost, it is important to consider both material and labor costs along with site-specific factors. Below are estimated total costs based on installation in typical industrial environments:
Basic Installation (Standard Conditions, Polyester FRP Ladders):
- Material (per meter): $20 to $40
- Labor (per meter): $15 to $30
- Total (per meter): $35 to $70
Advanced Installation (Complex Environment, Vinyl Ester or Epoxy FRP Ladders):
- Material (per meter): $40 to $80
- Labor (per meter): $30 to $60
- Additional Supports and Custom Work: $10 to $30 per meter
- Total (per meter): $80 to $170+
Specialized Installation (High-Risk, Offshore, or Mining):
- Material (per meter): $50 to $120
- Labor (per meter): $60 to $100
- Specialized Support and Safety Measures: $50+ per meter
- Total (per meter): $160 to $350+
Example Total Project Cost:
For a medium-sized industrial project (e.g., 100 meters of FRP cable ladder installation):
- Basic Installation: $3,500 to $7,000
- Advanced Installation: $8,000 to $17,000
- Specialized Installation: $16,000 to $35,000+
These costs are rough estimates and can vary widely based on factors like project location, site-specific requirements, labor rates, and environmental conditions.
The installation cost of FRP cable ladders varies depending on the type of resin, the complexity of the installation site, the ladder configuration, and the necessary supports. For a basic installation, the cost can range from $35 to $70 per meter, while more complex or high-risk installations (e.g., offshore, industrial plants) could cost $160 to $350 per meter or more. Always consult with a qualified contractor to get a more accurate estimate based on the specifics of your project.
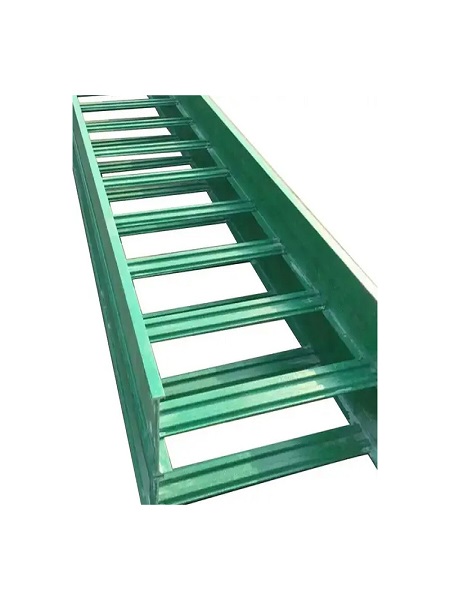
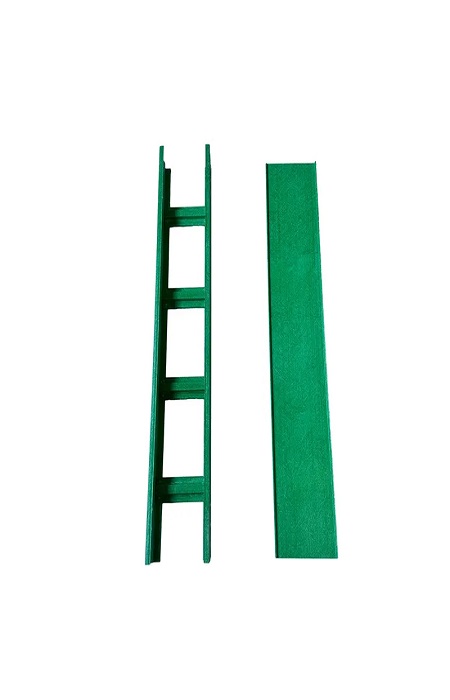
FRP Cable Ladder Advantages
Durability and Corrosion Resistance
The primary advantage of using an FRP Cable Ladder is its exceptional durability and resistance to corrosive environments. Unlike metal ladders, fiberglass does not rust, corrode, or degrade when exposed to harsh chemicals, moisture, or saline environments. This makes the FRP Cable Ladder particularly suitable for use in chemical plants, wastewater treatment facilities, offshore platforms, and other harsh industrial settings.
Electrical and Thermal Insulation
FRP Cable Ladder systems offer excellent electrical and thermal insulation properties, making them safe for use in electrical substations, power generation plants, and along routes that require protection from electrical interference and heat dissipation issues. This insulation capability is crucial in preventing electrical shocks and ensuring the integrity of the cables remains intact.
Versatility in Applications
FRP Cable Ladder systems are incredibly versatile and can be used in a variety of settings, not just industrial ones. They are also suitable for commercial buildings, data centers, and telecommunications facilities where robust cable management is necessary. The adaptability of FRP Cable Ladder systems allows them to be installed in visible areas where aesthetics are important, as they can be manufactured in various colors to match or complement existing décor.
Long-term Cost Efficiency
While the initial cost of FRP Cable Ladder may be higher than some alternatives, their longevity and minimal maintenance requirements make them a cost-effective solution in the long run. The durability of fiberglass ensures that the ladders will not need to be replaced due to corrosion or degradation, and their maintenance needs are significantly lower than those of metal alternatives.
Characteristics of FRP Cable Ladder Systems
GangLong Fiberglass’s fiberglass cable ladder, widely recognized under the FRP Cable Ladder category, offer a suite of features designed to meet the most demanding of industrial environments. The GangLong Fiberglass’s FRP Cable Ladder system is engineered to provide superior performance in a range of applications, combining durability, functionality, and safety with a modern design ethos.
High Corrosion Resistance
One of the hallmark features of the GangLong Fiberglass‘s FRP Cable Ladder is its exceptional resistance to corrosion. Unlike traditional metal ladders, these fiberglass structures are immune to the deteriorative effects of rust, chemicals, and saltwater. This makes them ideal for harsh environments such as chemical processing plants, offshore oil rigs, and coastal areas where the saline air would typically degrade metal rapidly.
Enhanced Strength and Durability
The GangLong Fiberglass’s FRP Cable Ladder systems are manufactured using high-quality fiberglass and resin materials, ensuring a high strength-to-weight ratio. This durability does not only contribute to the longevity of the ladder system but also supports heavier loads of cables and equipment, providing a reliable cable management solution that withstands the test of time and heavy use.
Non-Conductive Properties
Safety is paramount in environments where electrical hazards are present. The GangLong Fiberglass’s FRP Cable Ladder is non-conductive, which significantly reduces the risk of electrical shock to personnel and damage to sensitive equipment. This feature is particularly valuable in power generation, transmission, and distribution applications.
Fire Retardancy
GangLong Fiberglass ‘s FRP Cable Ladder systems are available with fire-retardant properties, meeting various industry fire codes and standards. This addition enhances the safety profile of the installations, making them suitable for use in sectors where fire risks are a concern, such as underground tunnels, industrial plants, and commercial buildings.
Lightweight and Easy Installation
Another significant advantage of the GangLong Fiberglass’s FRP Cable Ladder is its lightweight nature compared to traditional materials like steel. This quality makes the ladder system easier and less costly to transport, handle, and install, requiring fewer personnel and lighter equipment. The ease of installation not only reduces initial project costs but also expedites the overall timeline of construction and maintenance projects.
Customizability
The adaptability of the GangLong Fiberglass’s FRP Cable Ladder allows for extensive customization options to suit specific project needs. Available in various sizes, shapes, and colors, these ladder systems can be tailored to match environmental demands and aesthetic preferences, ensuring that functional installations do not compromise the visual coherence of the site.
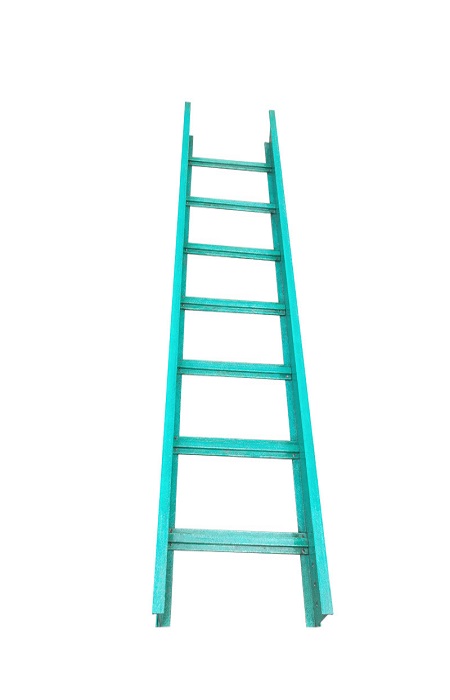
Thank you for your interest in our products. To receive our pricelist or for any inquiries, please fill out the form below. We will get back to you within 24 hours.
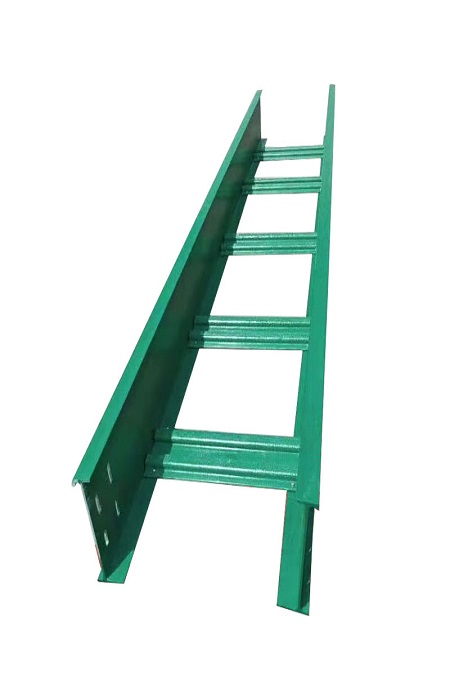
Accessories of FRP Cable Ladder
To enhance the functionality and adaptability of the FRP Cable Ladder systems, a variety of accessories are available. These accessories not only aid in the installation and maintenance of the cable ladder systems but also ensure that they can be customized to meet the specific needs of any project. Each accessory plays a critical role in optimizing the performance and safety of the FRP Cable Ladder installations across various industries.
Splice Plates
Splice plates are used to connect two sections of an FRP Cable Ladder together, ensuring a continuous run. These are particularly important in long runs where multiple sections of cable ladder are required. Splice plates are designed to provide a strong, secure connection while maintaining the integrity and strength of the cable ladder system.
Hold-Down Clamps
Hold-down clamps are essential for securing the FRP Cable Ladder to support structures, especially in environments where vibration or movement could displace the ladder. These clamps are designed to fit securely around the ladder rails and can be bolted or welded to the supporting structure, providing stability and preventing shifting.
Ladder Covers
Ladder covers are an optional accessory for FRP Cable Ladder systems, offering protection from dust, debris, and other environmental elements. Covers can be especially useful in outdoor or harsh industrial environments where additional protection for the cables is necessary to prevent contamination or damage.
Vertical and Horizontal Bends
To accommodate changes in direction along the cable path, vertical and horizontal bends are available for FRP Cable Ladder systems. These bends are manufactured to fit seamlessly with straight ladder sections, maintaining a uniform appearance and integrity throughout the installation. They are available in various angles to suit specific routing requirements.
Riser Links
Riser links are used to create vertical sections in cable ladder installations, allowing cables to be routed from one level to another efficiently. These links ensure that the FRP Cable Ladder can be extended vertically without compromising load capacity or stability.
Barrier Strips
Barrier strips can be installed within the FRP Cable Ladder to segregate different types of cables, such as power and data, which may need to be separated to prevent electromagnetic interference or for organizational purposes. These strips are easy to install and can be added to existing installations if needed.
End Caps
End caps provide a neat finish to the ends of the FRP Cable Ladder sections, protecting the exposed edges from wear and damage while also preventing the entry of pests or debris into the cable management system.
Expansion Joints
In environments where temperature fluctuations are significant, expansion joints are used to accommodate the thermal expansion and contraction of the FRP Cable Ladder. This accessory helps prevent structural damage caused by temperature-induced movements.
Types of FRP Cable Ladder
The FRP Cable Ladder is a critical component in modern infrastructure, offering robust, durable solutions for cable management across various sectors including industrial, commercial, and utilities. Each type of FRP Cable Ladder is designed to meet specific environmental and load requirements, ensuring safety, efficiency, and longevity of the cable management system.
Standard Ladder Type FRP Cable Ladder
The standard ladder type FRP Cable Ladder is the most commonly used configuration. It features a series of evenly spaced rungs between two longitudinal side rails, providing excellent support and free air circulation for the cables. This type is particularly suited for environments where heat dissipation is crucial, such as in power stations or industrial settings with high operating temperatures.
Wide Span FRP Cable Ladder
Wide span FRP Cable Ladder systems are designed to cover longer distances with fewer supports. This type is ideal for installations where it is not feasible to have frequent support structures. Wide span ladders reduce the total number of required supports and associated installation costs, making them a cost-effective solution for large-scale projects.
Heavy Duty FRP Cable Ladder
Heavy duty FRP Cable Ladder systems are built to withstand higher loads and are typically used in industrial applications where heavy cables and equipment need support. These ladders are reinforced with additional materials to handle the extra weight and are ideal for power distribution settings and industrial facilities with heavy machinery.
Fire Retardant FRP Cable Ladder
Fire retardant FRP Cable Ladder types are essential in environments where there is a high risk of fire. These ladders are treated with fire-retardant resins that significantly reduce the risk of fire spreading through the cable management system. They are commonly used in oil and gas facilities, chemical plants, and anywhere else where fire safety is a paramount concern.
Corrosion-Resistant FRP Cable Ladder
In environments where chemical exposure or corrosive conditions prevail, corrosion-resistant FRP Cable Ladder systems offer an unmatched advantage. These ladders are manufactured with materials that resist chemical degradation, making them perfect for chemical plants, wastewater treatment facilities, and marine applications.
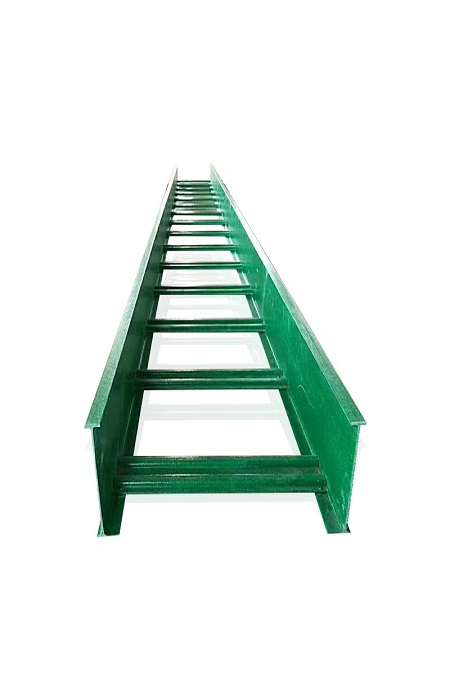
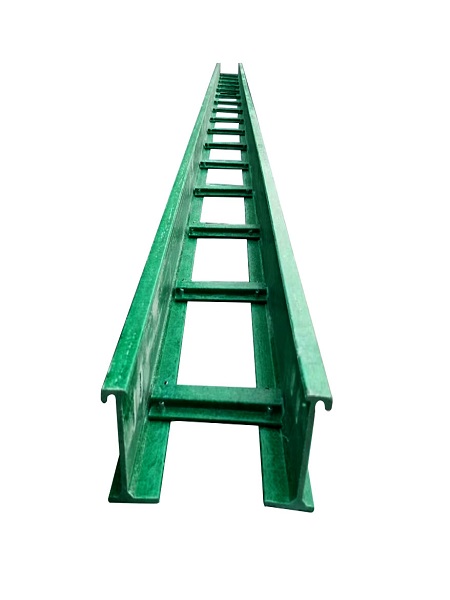
Specifications of FRP Cable Ladder
The specifications of an FRP Cable Ladder play a crucial role in ensuring that the ladder system meets the required standards for safety, durability, and functionality in various environmental conditions. These specifications vary widely depending on the intended use and the challenges presented by the installation environment.
Material Composition
FRP Cable Ladder systems are made from fiber-reinforced plastic, a composite material that combines fiberglass with a resin matrix. The type of resin used (e.g., polyester, vinyl ester, or epoxy) can vary based on the required resistance to corrosion, UV exposure, and chemical interaction. The composition directly affects the ladder’s strength, durability, and performance in harsh environments.
Load Capacity
The load capacity of an FRP Cable Ladder is defined by its ability to support a certain weight without significant deformation. This capacity is crucial for applications involving heavy cables and equipment. Specifications typically include the maximum load per meter and the deflection rate under load, which engineers use to determine the suitability of a ladder system for specific applications.
Dimensions
Dimensions are a critical specification for any FRP Cable Ladder system. These include the length, width, and height of the ladder, as well as the spacing between rungs. The dimensional specifications must accommodate the volume and type of cables to be managed, ensuring there is adequate space for installation, air circulation, and maintenance activities.
Fire Resistance
For environments where fire risk is a concern, the fire resistance of an FRP Cable Ladder is specified by its ability to withstand and contain fire to a certain standard. This is often measured by the ladder’s performance in fire safety tests, which determine how the material behaves under fire exposure.
Corrosion Resistance
Given that FRP Cable Ladder systems are often used in corrosive environments, their resistance to various chemicals and corrosive conditions is specified based on the type of resin used in the fiberglass composition. The specifications should indicate the types of environments the ladder is suited for, such as marine settings, chemical plants, or outdoor exposure.
UV Resistance
UV resistance is an essential specification for FRP Cable Ladder systems used in outdoor installations. The specification details the ladder’s ability to resist degradation from UV light exposure, which is critical for maintaining structural integrity and longevity.
Temperature Range
The operational temperature range specifies the minimum and maximum temperatures that the FRP Cable Ladder can withstand while maintaining structural integrity and performance. This is particularly important for installations in extreme climates or near heat-producing equipment.
Color and Surface Finish
While often overlooked, the color and surface finish of an FRP Cable Ladder can be specified for aesthetic reasons or to enhance visibility in safety-critical applications. Additionally, surface finishes may include textures or coatings that improve grip or reduce static build-up.
Applications of FRP Cable Ladder
The FRP Cable Ladder is engineered to serve a wide array of industries, providing robust, durable, and efficient solutions for cable management under various environmental and operational conditions. Due to its superior properties, such as corrosion resistance, electrical and thermal insulation, and high strength-to-weight ratio, the FRP Cable Ladder finds applications across diverse sectors.
Industrial Facilities
In industrial environments, such as manufacturing plants, chemical processing facilities, and refineries, FRP Cable Ladder systems are essential for managing and protecting cables that power heavy machinery and equipment. These settings often expose cable management systems to harsh chemicals, extreme temperatures, and abrasive conditions where the non-corrosive and high strength characteristics of FRP are particularly beneficial.
Utility and Power Distribution
FRP Cable Ladder systems are widely used in the utility sector, particularly in power generation and distribution networks. Their non-conductive nature makes them ideal for safely routing electrical cables, reducing the risk of electrical hazards. They are used extensively in substations, power plants, and along transmission lines where durability and electrical insulation are critical.
Offshore and Marine Applications
Click edit button to change this text. Lorem ipsum dolor sit amet, consectetur adipiscing elit. Ut elit tellus, luctus nec ullamcorper mattis, pulvinar dapibus leo.
Telecommunications
In the telecommunications industry, FRP Cable Ladder systems facilitate the organization and protection of fiber optic cables and other communication lines. These systems provide a secure pathway for sensitive cables, protecting them from environmental exposure and mechanical damage, which is crucial for maintaining network integrity and functionality.
Transportation Infrastructure
FRP Cable Ladder systems are also vital in the transportation sector, including applications within airports, railway systems, and bridges. These applications benefit from the lightweight and easy-to-install nature of FRP, which is crucial for projects that require quick and efficient assembly within tight construction schedules.
Architectural and Commercial Buildings
Within commercial and architectural contexts, FRP Cable Ladder systems help manage the extensive network of cables required for modern building operations, including electrical, HVAC, and data communication systems. The adaptability and aesthetic options available with FRP systems allow them to be integrated seamlessly into building designs, offering functional strength without compromising on style.
Renewable Energy Installations
Renewable energy facilities, such as solar farms and wind turbines, utilize FRP Cable Ladder systems to manage and protect cables from environmental stressors like UV radiation and variable weather conditions. The lightweight and durable nature of FRP is ideal for such applications, where exposure to the elements is constant and maintenance access can be challenging.
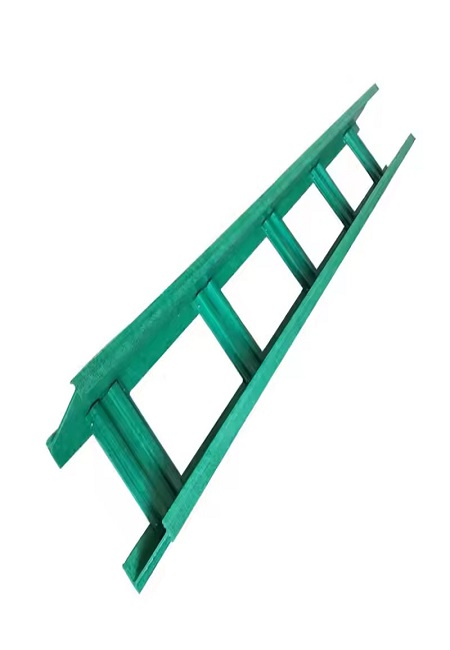
FAQs about FRP Cable Ladder
What is the Meaning of FRP Ladder?
What is FRP in Fiber Cable?
What is FRP cable ladder?
Corrosion Resistance: Suitable for harsh environments where metal ladders might corrode.
Lightweight and Durable: Easier to install and transport while offering a long service life.
Non-Conductive: Provides electrical insulation, making it safe for electrical installations.
High Strength-to-Weight Ratio: Strong enough to support heavy cables while being lightweight.
What does FRP stand for in electrical?
Is FRP the same as fiberglass?
FRP (Fiber Reinforced Plastic): A broad category of composite materials that include fibers like glass, carbon, aramid, or basalt, reinforced in a plastic matrix.
Fiberglass: A specific type of FRP where the reinforcing fiber is glass. It is the most common form of FRP, often used in construction, automotive, and industrial applications.
So, while all fiberglass is FRP, not all FRP is fiberglass.
What is FRP board used for?
Wall and Ceiling Panels: In commercial and industrial settings, particularly in environments requiring easy cleaning and resistance to moisture and chemicals.
Structural Components: For load-bearing applications where high strength and durability are needed.
Protective Linings: In tanks, vessels, and other equipment exposed to corrosive substances.
What is the difference between FRP and GRp pole?
FRP (Fiber Reinforced Plastic) Pole: Refers to any pole made from plastic reinforced with fibers, which can include glass, carbon, aramid, or basalt.
GRP (Glass Reinforced Plastic) Pole: A specific type of FRP pole reinforced with glass fibers. GRP is widely used due to its strength, durability, and cost-effectiveness.
In essence, GRP is a subset of FRP, and when referring to poles, GRP is specifically made with glass fibers, offering excellent corrosion resistance and strength.
What is the difference between FRP and carbon fiber?
FRP (Fiber Reinforced Plastic): A general term for composite materials made by reinforcing plastic with various fibers, such as glass, carbon, or aramid.
Carbon Fiber: A type of FRP where the reinforcement is specifically carbon fibers. Carbon fiber offers higher strength, stiffness, and lightweight properties compared to glass fiber but is more expensive.
Carbon fiber is typically used in high-performance applications, such as aerospace, automotive, and sports equipment, where strength-to-weight ratio is critical.
What is the difference between GRP and FRP cable tray?
GRP Cable Tray: Specifically uses glass fibers for reinforcement, offering excellent corrosion resistance, high strength, and cost-effectiveness.
FRP Cable Tray: Can be made with various types of fibers, including glass, carbon, or aramid. The choice of fiber depends on the application requirements, such as the need for higher strength (carbon fiber) or impact resistance (aramid fiber).
In most industrial contexts, GRP is commonly used because it provides a good balance of cost and performance.
Why are ladders made of fiberglass better than wood or aluminum?
Non-Conductive: Fiberglass ladders are electrically non-conductive, making them safer for use around electrical work.
Durability: Fiberglass is resistant to weather, chemicals, and corrosion, providing a longer lifespan, especially in outdoor or industrial environments.
Strength: Fiberglass ladders can support heavy loads without bending or warping, unlike aluminum ladders, which may dent or bend under stress.
Safety: Unlike wood, fiberglass doesn’t rot or absorb moisture, reducing the risk of weakening over time.
What are the benefits of FRp ladder?
Corrosion Resistance: Suitable for use in corrosive environments, such as chemical plants and offshore platforms.
Non-Conductive: Provides electrical insulation, making it safe for use near electrical equipment.
Lightweight and Strong: Easier to handle and transport while providing high strength and stability.
Durability: Resistant to weathering, chemicals, and moisture, ensuring a long lifespan with minimal maintenance.
Fire Resistance: Some FRP ladders are made with fire-retardant materials, enhancing safety in fire-prone environments.
Why are FRP cable trays used?
Corrosion Resistance: Ideal for environments where exposure to chemicals, moisture, or saltwater would corrode metal trays.
Lightweight: Easier to handle, transport, and install, reducing labor costs.
Non-Conductive: Provides electrical insulation, reducing the risk of short circuits or electrical hazards.
Durability: Long-lasting with minimal maintenance, offering a cost-effective solution over time.
Fire Resistance: Some FRP cable trays are made with fire-retardant materials, enhancing safety in environments where fire risk is a concern.
What is the difference between FRP ladder and Aluminium ladder?
Non-Conductive: Fiberglass ladders are non-conductive, making them ideal for electrical work and environments where contact with live wires is possible.
Corrosion Resistance: Resistant to moisture, chemicals, and corrosion, making them suitable for outdoor and industrial environments.
Heavier: Typically heavier than aluminum ladders, which can make them harder to move but provides added stability.
Durability: More durable in harsh environments as they don’t rust, corrode, or deteriorate easily.
Aluminum Ladder:
Lightweight: Aluminum ladders are lighter and easier to carry, making them convenient for frequent movement or transport.
Conductive: Aluminum conducts electricity, making it unsuitable for use near electrical hazards.
Corrosion-Prone: Although resistant to rust, aluminum can corrode in certain environments, particularly those involving saltwater or strong chemicals.
Less Durable in Harsh Conditions: Aluminum can bend or dent more easily under heavy loads or impact.
Which is safer aluminum or fiberglass ladder?
Can fiberglass ladders be left outside?
Weather Resistance: Fiberglass is resistant to moisture, sunlight, and most weather conditions, making it suitable for outdoor storage.
UV Exposure: Prolonged exposure to direct sunlight can cause the fiberglass to degrade over time, leading to a loss of strength and durability. It’s recommended to store the ladder in a shaded area or cover it when not in use to extend its lifespan.
Maintenance: Regular inspection for any signs of damage or wear, especially after extended outdoor exposure, is advisable.
What is the most durable and safest type of ladder?
High Durability: Resistant to corrosion, chemicals, and weather, making them suitable for both indoor and outdoor use.
Electrical Safety: Non-conductive properties make them the safest choice for electrical work.
Stability: Heavier weight adds to the ladder’s stability, reducing the risk of tipping.
Is fiberglass stronger than aluminum?
Do fiberglass ladders last?
How to tell if a ladder is fiberglass?
Color: Fiberglass ladders are typically bright orange, yellow, or green, which differentiates them from aluminum (usually silver) or wood ladders.
Weight: Fiberglass ladders are heavier than aluminum ladders.
Surface Texture: The surface of a fiberglass ladder is typically smooth and sometimes has a slightly grainy texture due to the fiber reinforcement.
Labeling: Check the manufacturer’s label, which should indicate the material as fiberglass.
Why buy a fibreglass ladder?
Electrical Safety: Ideal for use around electrical work due to its non-conductive properties.
Durability: Resistant to corrosion, chemicals, and weather, making it suitable for harsh environments.
Strength: Fiberglass ladders are strong and can support heavy loads without bending or warping.
Versatility: Suitable for both indoor and outdoor use across various industries, including construction, maintenance, and electrical work.
Why do electricians use fiberglass ladders?
Which ladder is better steel or aluminium?
Steel Ladder:
Stronger and More Durable: Steel ladders are sturdier and can support heavier loads without bending.
Corrosion-Prone: Steel can rust if not properly coated or maintained, making it less suitable for outdoor use unless it’s galvanized or stainless steel.
Heavier: Steel ladders are heavier, making them harder to move around.
Aluminum Ladder:
Lightweight: Easier to carry and maneuver, making it convenient for frequent use.
Corrosion-Resistant: Does not rust but can corrode in certain environments, such as exposure to saltwater.
Less Durable: More prone to bending or denting under heavy loads.
Aluminum ladders are generally better for light to medium-duty work where portability is key, while steel ladders are better for heavy-duty applications requiring maximum strength and durability.
What is the best type of ladder to use?
For Electrical Work: A fiberglass ladder is best due to its non-conductive properties.
For General Use: An aluminum ladder is ideal for light to medium-duty tasks due to its lightweight and ease of handling.
For Heavy-Duty Work: A steel ladder or a high-rated fiberglass ladder (Type IA or Type IAA) is best, offering maximum strength and durability.
For Outdoor Use: Fiberglass ladders are preferred due to their weather resistance and durability.
What is FRP in cable?
What does FRP stand for?
Is FRP still used?
Is FRP stronger than steel?
Corrosion Resistance: FRP does not rust or corrode, making it more durable in harsh environments.
Weight: FRP is much lighter than steel, which reduces the overall load and makes it easier to handle and install.
What are the 4 main types of FRP?
Glass Fiber Reinforced Plastic (GFRP): The most common type, using glass fibers. GFRP is widely used due to its good balance of strength, durability, and cost-effectiveness.
Carbon Fiber Reinforced Plastic (CFRP): Uses carbon fibers, known for their high strength, stiffness, and lightweight properties. CFRP is often used in high-performance applications like aerospace and sports equipment.
Aramid Fiber Reinforced Plastic (AFRP): Uses aramid fibers (e.g., Kevlar), known for their exceptional toughness and impact resistance. AFRP is used in applications requiring high durability and resistance to impact.
Basalt Fiber Reinforced Plastic (BFRP): Uses basalt fibers, which offer good thermal stability and resistance to chemicals. BFRP is used in construction and automotive applications.
Is FRP better than PVC?
Strength: FRP is much stronger and more rigid than PVC, making it suitable for structural applications.
Corrosion Resistance: Both materials resist corrosion, but FRP can withstand harsher chemical environments.
Temperature Tolerance: FRP can tolerate higher temperatures compared to PVC, which can soften or deform under heat.
Cost: PVC is cheaper and easier to work with, making it suitable for less demanding applications where cost is a primary concern.
What is FRP good for?
Corrosion Resistance: Ideal for environments where exposure to chemicals, moisture, or saltwater is common, such as in chemical plants, wastewater treatment facilities, and marine environments.
High Strength-to-Weight Ratio: Suitable for structural applications where lightweight and high strength are required, such as in construction, automotive, and aerospace industries.
Electrical Insulation: Used in electrical applications for cable trays, ladders, and enclosures due to its non-conductive properties.
Durability: Offers a long lifespan with minimal maintenance, even in harsh conditions.
Why is FRP used in fiber cable?
Provide Tensile Strength: Helps the cable withstand pulling forces during installation and prevents stretching that could damage the delicate optical fibers.
Maintain Cable Shape: Ensures that the cable retains its structure, preventing kinks or bends that could disrupt the signal transmission.
Enhance Durability: Protects the optical fibers from mechanical stresses, environmental factors, and physical damage.
What is the function of FRP?
Strengthen Structures: In construction, automotive, and aerospace applications.
Provide Corrosion Resistance: In environments exposed to chemicals, moisture, and saltwater.
Offer Electrical Insulation: In electrical and industrial applications.
Reduce Weight: In transportation and structural applications where weight is a critical factor.
Is FRP better than carbon fiber?
Carbon Fiber (CFRP): A type of FRP where carbon fibers are used as the reinforcement. It is stronger, stiffer, and lighter than other types of FRP, making it ideal for high-performance applications like aerospace, automotive, and sports equipment. However, it is more expensive.
FRP (General): Includes a range of fiber reinforcements like glass, aramid, and basalt, offering a balance between cost and performance. GFRP (Glass Fiber Reinforced Plastic) is the most common and is more cost-effective than carbon fiber but not as strong or lightweight.
In summary, carbon fiber is better for applications requiring maximum strength and minimal weight, while other types of FRP might be better for cost-sensitive projects requiring durability and corrosion resistance.
What is the use of FRP?
Construction: For structural components like beams, panels, and reinforcement in buildings and bridges.
Industrial: In chemical plants, wastewater treatment facilities, and offshore platforms for tanks, pipes, grating, and cable trays.
Automotive and Aerospace: For lightweight, high-strength parts such as body panels, frames, and structural components.
Marine: In the construction of boats, docks, and other marine structures due to its resistance to saltwater corrosion.
Electrical: For non-conductive cable trays, ladders, enclosures, and support structures in environments requiring electrical insulation.
What is the purpose of FRP ladder?
Electrical Work: Due to their non-conductive properties, FRP ladders are ideal for use around electrical installations, reducing the risk of electric shock.
Industrial and Chemical Environments: FRP ladders resist corrosion from chemicals, moisture, and saltwater, making them suitable for harsh industrial environments.
Outdoor Use: FRP ladders are durable in various weather conditions and do not rust or degrade like metal ladders.
What are the disadvantages of fibreglass ladders?
Heavier Weight: Fiberglass ladders are generally heavier than aluminum ladders, making them more difficult to transport and maneuver.
Cost: Fiberglass ladders are typically more expensive than aluminum or wood ladders, which can be a consideration for budget-conscious buyers.
Degradation Over Time: Prolonged exposure to sunlight (UV radiation) can cause the fiberglass material to degrade, leading to a reduction in strength and durability over time.
Brittleness: Fiberglass can become brittle, especially if it has been exposed to UV rays for extended periods, which may lead to cracking or splintering under stress.
What are the disadvantages of FRP in construction?
Higher Initial Cost: FRP materials are generally more expensive than traditional materials like steel or concrete, which can be a limiting factor for some projects.
Brittleness: FRP can be more brittle than metals, leading to sudden failure without significant deformation, especially under impact or stress.
Limited Temperature Resistance: FRP materials can lose strength at high temperatures, making them unsuitable for applications where fire resistance is critical unless they are specially formulated.
UV Degradation: Prolonged exposure to ultraviolet (UV) light can degrade FRP, leading to a reduction in mechanical properties unless UV-resistant coatings are applied.
Why do we need FRP?
Corrosion Resistance: FRP is highly resistant to chemicals, moisture, and saltwater, making it ideal for use in harsh environments where metal would corrode.
Lightweight Strength: FRP provides high strength-to-weight ratios, making it strong yet lightweight, which is beneficial in applications requiring ease of handling and installation.
Electrical Insulation: FRP is non-conductive, making it safe for use in electrical applications and environments where electrical hazards are a concern.
Durability: FRP has a long lifespan with minimal maintenance, offering cost savings over time in applications where durability is essential.
Are fiberglass ladders worth it?
Safety: Their non-conductive properties make them ideal for electrical work, reducing the risk of electric shock.
Durability: Fiberglass ladders are resistant to corrosion, chemicals, and weather, making them long-lasting and suitable for various environments.
Strength: They offer high strength and stability, supporting heavy loads without bending or warping.
While they are more expensive upfront, their safety, durability, and versatility often justify the cost, especially in professional and industrial settings.
Do fiberglass ladders crack?
Do fiberglass ladders degrade?
UV Radiation: Prolonged exposure to sunlight can cause the fiberglass to weaken and degrade, leading to reduced strength and brittleness.
Extreme Weather Conditions: While fiberglass is resistant to many environmental factors, constant exposure to extreme conditions (e.g., high humidity, saltwater, or chemicals) can eventually lead to degradation.
Improper Use or Storage: Mishandling, dropping, or storing the ladder in harsh conditions can accelerate wear and tear.
Why electricians use fiberglass ladders because metal ladders?
Non-Conductive Properties: Fiberglass does not conduct electricity, making it much safer to use around live wires and electrical equipment, thereby reducing the risk of electric shock.
Safety Standards: Many safety regulations and industry standards require the use of non-conductive ladders in electrical work to ensure the safety of workers.
Durability: Fiberglass ladders are durable and resistant to environmental factors that could compromise safety, such as corrosion or rust, which can affect metal ladders.
What are the advantages of FRp in construction?
Corrosion Resistance: FRP is highly resistant to chemicals, moisture, and saltwater, making it ideal for use in environments where traditional materials would corrode.
Lightweight: FRP is much lighter than metals, which makes it easier to handle, transport, and install, reducing labor costs.
High Strength-to-Weight Ratio: Despite being lightweight, FRP is strong and can support significant loads, making it suitable for structural applications.
Durability: FRP has a long lifespan and requires minimal maintenance, making it a cost-effective choice over the life of the structure.
Customizability: FRP can be molded into various shapes and sizes, allowing for greater design flexibility in construction projects.
What has the most effect on fiberglass ladders?
What are the advantages of fibreglass ladders?
Electrical Insulation: Non-conductive properties make them safe for use around electrical installations, reducing the risk of electric shock.
Corrosion Resistance: Fiberglass ladders resist corrosion from chemicals, moisture, and saltwater, making them ideal for both indoor and outdoor use.
Strength and Stability: Fiberglass ladders are strong and can support heavy loads without bending or warping, providing a stable platform for work at heights.
Durability: They have a long lifespan and can withstand harsh environmental conditions, requiring minimal maintenance.
Safety: Fiberglass ladders are designed to meet stringent safety standards, making them a preferred choice in professional and industrial settings.
Thank you for your interest in our products. To receive our pricelist or for any inquiries, please fill out the form below. We will get back to you within 24 hours.