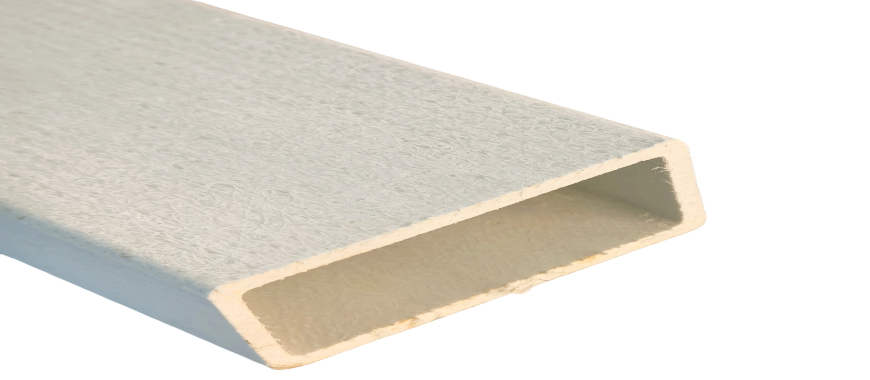
FRP pipe piles are structural elements made from Fiberglass Reinforced Plastic, used primarily in construction and industrial applications. These piles offer superior strength, corrosion resistance, and durability, making them an ideal choice for environments exposed to harsh conditions, such as coastal or marine areas. FRP pipe piles are lightweight yet strong, allowing for easier transportation and installation compared to traditional materials like steel or concrete. Their primary purpose is to support structures by transferring loads from the surface to deeper, more stable soil layers, ensuring long-lasting foundations. They are commonly used in projects such as bridges, seawalls, and industrial infrastructure. FRP pipe piles are durable, corrosion-resistant, and outperform traditional materials in marine, industrial, and retaining wall uses.
What Are FRP Pipe Piles?
FRP pipe piles, constructed from Fiberglass Reinforced Plastic, are advanced structural components used in construction and engineering projects, especially in environments that demand high durability and resistance to corrosion. These piles are essential for providing structural support in both marine and land-based projects, where traditional materials like steel or timber may fall short due to exposure to harsh elements. FRP pipe piles are known for their exceptional strength, lightweight nature, and ability to withstand extreme conditions, making them a popular choice for long-term infrastructure solutions.
FRP pipe piles are essential structural components used in a variety of construction and engineering projects, particularly in environments where traditional materials may fall short. Made from Fiberglass Reinforced Plastic (FRP), these piles offer a combination of strength, durability, and corrosion resistance that makes them suitable for use in harsh environments like marine and coastal areas. The unique properties of FRP pipe piles make them an increasingly popular choice for projects requiring long-lasting, low-maintenance solutions.
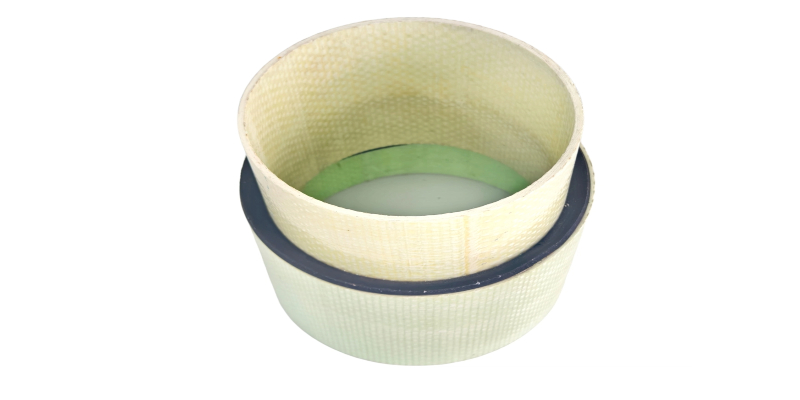
Load-Bearing Capabilities of FRP Pipe Piles
The load-bearing capabilities of FRP pipe piles are a key factor in their suitability for various construction applications. Despite their lightweight nature, FRP piles are capable of supporting significant loads, making them ideal for use in both vertical and lateral load-bearing scenarios. Their ability to distribute loads effectively helps prevent settlement and ensures the stability of the structure they support.
In marine applications, FRP pipe piles are often used to support docks, piers, and other waterfront structures. They can withstand the dynamic forces generated by waves, currents, and tides, providing a stable and secure foundation. On land, FRP pipe piles are used in applications such as retaining walls, foundations, and slope stabilization. Their high load-bearing capacity and resistance to environmental factors make them a versatile solution for a wide range of construction needs.
Environmental Benefits of FRP Pipe Piles
The use of FRP pipe piles offers several environmental benefits, particularly in sensitive ecosystems like wetlands and coastal areas. Unlike traditional materials, FRP does not leach harmful substances into the surrounding environment. This inert nature makes it an environmentally friendly option for projects that require minimal impact on the ecosystem.
FRP pipe piles also contribute to sustainability by reducing the need for frequent replacements and maintenance. Their durability and resistance to environmental factors mean that they have a longer service life than materials like timber or steel. This longevity reduces the consumption of raw materials and the environmental impact associated with the production, transportation, and installation of replacement piles.
Furthermore, the lightweight nature of FRP pipe piles reduces the energy consumption during transportation and installation. Less fuel is required to transport these piles to the construction site, and smaller, less energy-intensive equipment can be used for installation. These factors contribute to a lower carbon footprint for construction projects that utilize FRP pipe piles.
Cost-Effectiveness of FRP Pipe Piles
FRP pipe piles offer a cost-effective solution for many construction projects. While the initial cost of FRP piles may be higher than some traditional materials, their long-term benefits often result in overall cost savings. The durability and low maintenance requirements of FRP pipe piles reduce the need for frequent repairs and replacements, resulting in lower lifecycle costs.
The lightweight nature of FRP pipe piles also contributes to cost savings during transportation and installation. Reduced transportation costs, combined with the use of smaller installation equipment, help lower the overall project costs. Additionally, the faster installation process associated with FRP piles minimizes construction time and associated labor costs.
Installation Techniques for FRP Pipe Piles
Installing FRP pipe piles requires careful planning and execution to ensure they provide the desired structural integrity and longevity. The installation process varies depending on the environment, such as marine or land-based settings, but certain best practices apply universally. Proper alignment and handling during installation are crucial to maintaining the structural integrity of the piles and ensuring they perform optimally in their designated roles.
For marine applications, the installation of FRP pipe piles often involves driving them into the seabed using specialized equipment. This process must account for factors like water depth, soil type, and wave action. To ensure a stable and secure foundation, it is important to use driving techniques that minimize stress and prevent damage to the piles. Using equipment like pile drivers with cushioned heads can help absorb the impact forces and reduce the risk of fractures in the FRP material. The use of FRP pipe racks during storage and transportation can help keep the piles organized and prevent damage before they are installed, ensuring a smoother installation process.
In land-based projects, FRP pipe piles are commonly installed using methods such as pre-drilling or jetting. These techniques involve creating a pre-formed hole or using high-pressure water jets to aid in the insertion of the pile. This approach is particularly useful in dense soil conditions, where driving the pile directly may be challenging. By preparing the ground in advance, these methods help achieve the correct alignment and depth for the piles, ensuring a stable foundation.
Cutting FRP pipe piles involves using specialized tools, such as diamond-bladed saws or water jet cutters, to cut through the durable composite material. The process requires precision to ensure smooth, clean cuts without damaging the structure or compromising the integrity of the pile. FRP pipe piles are typically used in marine, civil, and industrial applications due to their corrosion resistance and strength.
To ensure proper alignment during installation, it is essential to use accurate positioning equipment and techniques. Laser guides, GPS systems, and other alignment tools can help maintain the correct vertical and horizontal placement of the piles. Proper alignment is crucial to the overall stability and load-bearing capacity of the structure. After installation, it is important to inspect the piles for any signs of damage or misalignment, making necessary adjustments to maintain the structural integrity of the project. GangLong Fiberglass provides detailed guidance on the best installation practices for their products, ensuring that projects are completed successfully.
The Manufacturing Process of FRP Pipe Piles
The production of FRP pipe piles involves a specialized process known as filament winding, where fiberglass filaments are wound around a mandrel to create a strong, uniform structure. This technique is similar to the production of fiberglass filament wound tubes, which also use filament winding to achieve strength and durability. The resulting piles are then coated with resins that enhance their durability, UV resistance, and corrosion resistance. This process ensures that FRP pipe piles are capable of withstanding the demands of harsh environments.
Manufacturers like GangLong Fiberglass take great care in selecting high-quality materials for their FRP pipe piles, ensuring that they meet industry standards and project requirements. By using advanced manufacturing techniques, these companies can produce FRP pipe piles that are not only strong but also lightweight and easy to install.
Filament Winding: Creating the Core Structure
The filament winding process is the foundation of FRP pipe pile manufacturing.
Filament winding involves wrapping fiberglass filaments around a rotating mandrel in precise patterns to create a robust cylindrical structure. This technique ensures uniform distribution of fiberglass, giving the pipe piles exceptional strength and durability. The angle and tension of the winding are carefully controlled to meet specific load-bearing and design requirements, depending on the intended application. Once the fibers are wound, they are impregnated with a polymer resin, which acts as a bonding matrix and provides added rigidity.
Resin Coating: Enhancing Durability
After the filament-wound core is complete, the next critical step is resin coating.
The FRP pipe piles are coated with high-performance resins, such as polyester, vinyl ester, or epoxy. This coating improves their resistance to UV rays, moisture, and chemicals, making them ideal for marine and industrial environments. The resins are cured either through heat or UV exposure to form a hardened, protective layer. This ensures the piles maintain their structural integrity even in corrosive or aggressive conditions, such as saltwater or acidic soils.
Material Selection: Ensuring Quality Standards
Material selection plays a vital role in the performance of FRP pipe piles.
Manufacturers, such as GangLong Fiberglass, prioritize high-quality raw materials, including fiberglass filaments and premium-grade resins. By choosing materials that meet stringent industry standards, they ensure the finished product performs reliably under demanding conditions. The careful selection of materials contributes to the superior strength, flexibility, and long service life of the pipe piles.
Advanced Techniques: Precision and Consistency
Manufacturing techniques are continually refined to achieve better performance and efficiency.
In addition to filament winding, manufacturers utilize advanced curing and finishing processes to ensure dimensional accuracy and uniformity. Automation and quality control systems are often integrated into the production line to maintain consistency and adherence to project specifications. These techniques result in FRP pipe piles that are not only strong but also lightweight and easy to transport and install.
Final Inspection and Testing: Guaranteeing Performance
The final stage involves rigorous quality checks to ensure reliability.
Once the FRP pipe piles are manufactured, they undergo thorough inspection and testing for strength, durability, and resistance properties. This includes tests for mechanical performance, such as tensile strength, as well as environmental resistance tests to ensure the piles can withstand UV exposure, chemicals, and moisture. Only after passing these checks are the piles deemed ready for delivery to project sites.
The manufacturing process of FRP pipe piles combines precision engineering with high-quality materials to produce a product that excels in strength, durability, and environmental resistance. By following these steps, manufacturers deliver FRP pipe piles capable of meeting the demands of modern construction and infrastructure projects.
Advantages of FRP Pipe Piles
The advantages of FRP pipe piles make them highly valuable in several industrial sectors. Below are the key benefits:
Corrosion Resistance
FRP pipe piles are highly resistant to corrosion, which is particularly important in environments where exposure to moisture, chemicals, or saltwater is a concern. Unlike steel or concrete, FRP does not corrode when exposed to such elements, making it an ideal choice for projects near or in bodies of water. This corrosion resistance leads to longer-lasting infrastructure and lower overall maintenance costs.
Lightweight Yet Strong
One of the standout features of FRP pipe piles is their lightweight nature, which makes transportation and installation much easier compared to traditional materials. Despite being lightweight, FRP pipe piles are incredibly strong and can bear heavy loads. This unique combination of strength and lightness allows for more efficient installation processes and reduced labor costs.
High Strength-to-Weight Ratio
FRP pipe piles have a high strength-to-weight ratio, which makes them an attractive choice for projects that require materials capable of withstanding high loads without adding excessive weight to the overall structure. This is particularly important in projects like bridges and tall buildings, where weight is a critical factor in the design and structural integrity.
Customization and Flexibility
FRP pipe piles can be easily customized to meet specific project requirements. Whether a construction project requires unique lengths, diameters, or load-bearing capacities, FRP pipe piles can be tailored to fit. Manufacturers like GangLong Fiberglass offer a wide variety of custom-made FRP pipe piles designed to meet specific industrial needs, ensuring that every project gets the right support structure.
Environmentally Friendly
As industries move toward more sustainable practices, FRP pipe piles stand out as an environmentally friendly option. They require less energy to manufacture than traditional materials like steel or concrete, and their long lifespan means fewer resources are consumed over time for repairs or replacements. Additionally, FRP pipe piles do not release harmful chemicals into the environment, making them a safer option for ecosystems.
Advantages of Using FRP Pipe Piles in Construction
FRP pipe piles offer several advantages over traditional materials like steel, concrete, and timber. One of the most significant benefits is their corrosion resistance. In marine environments, where saltwater and moisture can quickly degrade conventional materials, FRP pipe piles provide a long-lasting solution. They are not susceptible to rust, rot, or chemical attack, making them ideal for use in coastal and offshore structures such as piers, jetties, and seawalls.
Another advantage of FRP pipe piles is their high strength-to-weight ratio. Despite being lightweight, FRP materials are exceptionally strong and can withstand high loads and stresses. This characteristic makes them easier to handle and transport, reducing installation costs and time. The lightweight nature of FRP pipe piles also makes them suitable for use in areas with soft soil or weak foundations, where heavy materials may cause settlement or instability.
FRP pipe piles from GangLong Fiberglass are also highly customizable. They can be manufactured to specific lengths, diameters, and wall thicknesses to meet the unique requirements of each project. This level of customization allows engineers to design structures that are optimized for their intended use, ensuring maximum performance and efficiency. Additionally, the non-conductive nature of FRP makes these piles a safe choice for use in environments where electrical conductivity poses a risk, such as near power lines or in areas prone to lightning strikes.
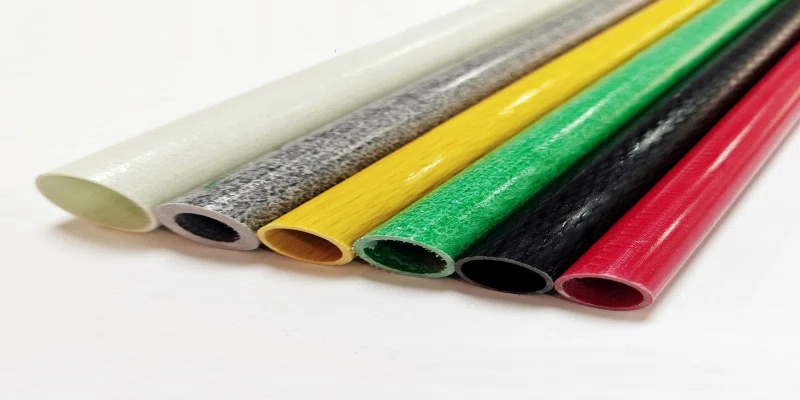
The Future of FRP Pipe Piles in Construction
As industries continue to evolve, the demand for durable, lightweight, and environmentally friendly materials like FRP pipe piles will likely grow. Innovations in material science are expected to further enhance the performance of FRP pipe piles, making them an even more attractive option for construction projects around the world.
Emerging trends include the use of FRP pipe pile in green building initiatives and sustainable infrastructure projects. With their long lifespan, low maintenance requirements, and minimal environmental impact, FRP pipe piles are well-positioned to become a standard material in the future of construction. GangLong Fiberglass is at the forefront of these innovations, constantly working to improve their product offerings to meet the needs of modern construction.
Durability and Longevity of FRP Pipe Piles
FRP pipe piles are known for their exceptional durability and long service life, even in the most challenging environments. The density of FRP pipe also contributes significantly to its performance, as a higher density enhances strength and stability, making the piles more resistant to external forces and environmental stresses.Their resistance to corrosion, chemical attack, and UV radiation ensures that they maintain their structural integrity over time. This durability is particularly important in marine and coastal applications, where exposure to saltwater, waves, and harsh weather conditions can quickly deteriorate traditional materials.
The use of high-quality materials and advanced manufacturing processes ensures that FRP pipe piles from GangLong Fiberglass can withstand the stresses and loads they encounter in service. They are designed to resist impact, abrasion, and fatigue, providing a reliable foundation for a wide range of structures. This reliability is crucial in applications where safety and performance are paramount, such as bridge supports, offshore platforms, and waterfront structures.
Maintenance and Inspection of FRP Pipe Piles
While FRP pipe piles are known for their low maintenance requirements, regular inspections are still necessary to ensure their continued performance and integrity. Inspections should focus on identifying any signs of damage, such as cracks, fractures, or wear, that could compromise the structural integrity of the piles. Routine maintenance activities may include cleaning the piles to remove marine growth or debris that could affect their performance.
In marine applications, underwater inspections are often necessary to assess the condition of the piles below the waterline. This process typically involves the use of divers or remotely operated vehicles (ROVs) equipped with cameras and other inspection tools. These inspections help identify any issues that may require attention, such as damage caused by impact, abrasion, or corrosion.
What Are the Design Considerations for FRP Pipe Piles?
Designing a project that incorporates FRP pipe piles requires careful consideration of several factors, including adherence to the FRP Pipe Code, to ensure optimal performance and compliance with industry standards.These considerations include the size and shape of the piles, the soil or seabed conditions, the anticipated loads, and the environmental factors to which the piles will be exposed. By taking these factors into account, engineers can design structures that maximize the benefits of FRP pipe piles.
Size and Shape of the Piles
The size and shape of FRP pipe piles are critical to their performance and depend on various factors, such as load requirements and installation conditions.
When designing FRP pipe piles, engineers first assess the load-bearing capacity needed for the specific application. The pile’s diameter and wall thickness are adjusted accordingly to handle the required load. In some cases, additional features like tapered ends or fins are incorporated, especially in marine environments, to enhance penetration and stability when driving the piles into the seabed. The shape and dimensions are also influenced by the depth at which the piles will be installed and the potential for external forces like tidal currents or wave impact. Proper sizing ensures that the pile can resist bending, compression, and other forces it may encounter during its service life.
Soil and Seabed Conditions
The type of soil or seabed conditions significantly impacts the design of FRP pipe piles.
Soil composition, density, and stability are key factors when designing FRP pipe piles, as they directly affect how the pile will transfer loads to the ground. In soft or loose soil conditions, larger-diameter piles or additional support measures may be required to ensure adequate stability and minimize settlement. In marine environments, engineers must also account for the effects of scour, a process where water movement erodes the soil around the pile, weakening its foundation. Special considerations, such as increasing the pile’s embedment depth or using larger-diameter piles, may be necessary to counteract these forces and provide a stable base. Engineers must evaluate soil reports and perform geotechnical studies to determine the right design to achieve the desired stability and performance.
Anticipated Loads
FRP pipe piles must be designed to bear the loads they will encounter throughout their life, whether from structural weight, environmental forces, or both.
The design process involves assessing the types and magnitudes of loads that the FRP pipe piles will be subjected to, such as vertical, lateral, and dynamic loads. This includes the weight of the structure, equipment, or materials being supported by the piles, as well as forces from wind, waves, or seismic activity. In marine applications, additional consideration must be given to the impact of wave action, tides, and currents, which can apply dynamic forces to the piles. Engineers must calculate the maximum load the piles can bear and design them accordingly, ensuring that the material’s strength is not exceeded under normal or extreme conditions. The proper distribution of these loads is crucial to avoid pile failure or excessive settlement over time.
Environmental Factors
Environmental conditions are essential when designing FRP pipe piles, particularly in marine and coastal applications.
FRP pipe piles are often chosen for their excellent corrosion resistance, making them ideal for environments exposed to moisture, saltwater, and chemical agents. However, engineers must still account for other environmental factors such as temperature fluctuations, UV radiation, and biological growth that could affect the pile’s longevity. In marine applications, exposure to saltwater and the potential for marine organisms attaching to the surface of the piles can impact their performance over time. Protective coatings may be applied to the FRP piles to enhance their resistance to UV degradation and marine biofouling. Additionally, the piles must be designed to withstand the forces generated by tidal movements, waves, and winds in coastal and offshore projects. Proper consideration of these environmental factors ensures that FRP pipe piles can last for many years, providing stable and reliable support.
Compliance with Industry Standards
Adherence to the relevant standards and codes ensures that FRP pipe piles meet safety, performance, and regulatory requirements.
To ensure that FRP pipe piles meet the necessary quality and safety standards, they must comply with the FRP Pipe Code and other relevant building codes and industry guidelines. These codes provide specifications for material strength, manufacturing techniques, load capacities, and environmental performance. Engineers must ensure that their designs meet these requirements and undergo testing and certification processes to verify compliance. By following these standards, engineers ensure that the FRP pipe piles will perform as expected, offering structural integrity and safety throughout their lifespan.
Designing FRP pipe piles requires a comprehensive approach that considers size, shape, soil conditions, anticipated loads, and environmental factors. By addressing these considerations, engineers can create pipe piles that provide superior strength, stability, and longevity, ensuring the success of projects across various industries, including marine and industrial applications.
How About the Customization Options for FRP Pipe Piles?
FRP (Fiber Reinforced Polymer) pipe piles are versatile and can be customized to meet the unique requirements of diverse engineering projects. Customization enables engineers to optimize FRP pipe piles for specific environmental conditions, structural demands, and long-term performance goals. By tailoring characteristics such as diameter, wall thickness, length, and surface finish, FRP pipe piles can provide the desired strength, durability, and resistance for varied applications. Below is a detailed exploration of the customization options available for FRP pipe piles, highlighting how these modifications address project-specific challenges.
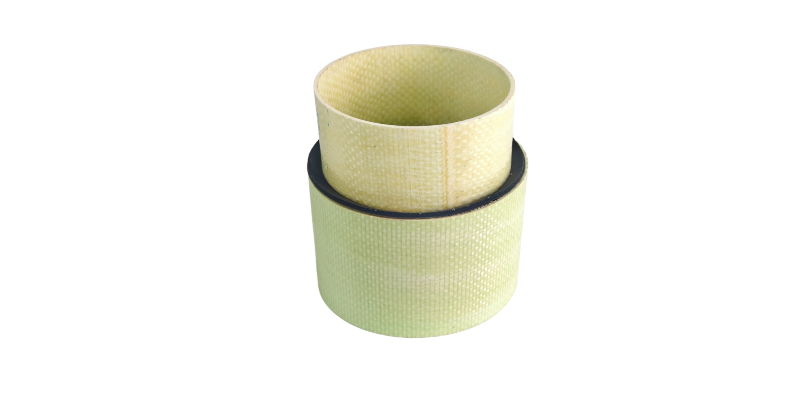
Diameter Customization
The diameter of FRP pipe piles can be customized to suit different load-bearing and soil penetration requirements.
The diameter of a pipe pile is critical in determining its ability to handle axial and lateral loads. Customizing this dimension allows engineers to design piles that fit the specific structural needs of a project, whether for a light structure like a boardwalk or a heavy-duty foundation for bridges or ports.
Larger diameters are typically used in applications requiring higher load capacities or in softer soil conditions where greater surface area is needed for stability. Conversely, smaller diameters may be sufficient for less demanding projects. Manufacturers like GangLong Fiberglass offer a wide range of diameter options to ensure compatibility with structural demands, minimizing unnecessary material use and costs.
Wall Thickness Adjustments
Wall thickness is a key factor in determining the strength and durability of FRP pipe piles.
Thicker walls enhance the structural integrity of the piles, making them more resistant to external forces, wear, and environmental degradation. Customizing the wall thickness enables engineers to design piles that meet the exact performance requirements of a project.
In coastal or marine environments where piles face abrasive forces from waves, sand, and floating debris, increased wall thickness can provide additional protection. Similarly, in high-load applications, thicker walls prevent buckling and improve long-term performance. Customizing wall thickness ensures the pile’s capacity matches the project’s specific load and environmental challenges.
Length Customization
The length of FRP pipe piles is another variable that can be customized based on soil conditions and project specifications.
The length of a pile determines how deeply it can penetrate the ground, affecting its load-bearing capacity and stability. Customizable lengths allow FRP pipe piles to adapt to varying site conditions, from shallow foundations to deep, challenging terrains.
Longer piles are often required for projects with loose or unstable soils, ensuring the structure reaches a stable stratum for support. On the other hand, shorter piles are suitable for applications with firm soil layers close to the surface. FRP pipe piles can also be manufactured in modular sections that are joined during installation, offering flexibility for transportation and assembly on-site.
Surface Finish Options
Surface finish customization enhances the pile’s resistance to environmental factors and specific operational challenges.
The surface finish of FRP pipe piles can be tailored to improve resistance to abrasion, UV exposure, and chemical attacks. This ensures that the piles remain functional and maintain their structural integrity even in harsh environments.
For projects in coastal or offshore environments, an abrasion-resistant coating can be applied to protect against wear from sand, water currents, and debris. In industrial settings, chemical-resistant finishes safeguard against exposure to corrosive substances. Anti-UV coatings can also be incorporated for installations exposed to prolonged sunlight, preventing material degradation.
Tailored Material Compositions
Customization can extend to the composition of the FRP material, including the type of fibers and resin used.
Selecting the appropriate fiber (e.g., glass, carbon, or basalt) and resin (e.g., polyester, epoxy) allows the piles to be optimized for strength, flexibility, and environmental compatibility.
For high-performance applications, carbon fibers may be chosen for their superior strength-to-weight ratio, while glass fibers are a cost-effective option for general-purpose use. Epoxy resins offer excellent chemical resistance, while polyester resins are suitable for less demanding conditions. By adjusting the material composition, FRP pipe piles can be designed to meet the most challenging structural and environmental requirements.
The ability to customize FRP pipe piles makes them a highly adaptable solution for a wide range of construction projects. With options for diameter, wall thickness, length, surface finish, and material composition, engineers can create piles that are perfectly suited to the unique demands of their applications. These customization capabilities not only ensure optimal performance but also provide cost-effective solutions by tailoring the material and design to the specific challenges of each project.
Epoxy FRP Pipe: Enhancing Corrosion Resistance
FRP Pipe Piles: A Key Element in Modern Construction
FRP pipe piles have become an essential component in a variety of construction projects, especially those in environments where traditional materials may be prone to degradation over time. Fiberglass Reinforced Plastic (FRP) pipe piles are engineered for durability, resistance to corrosion, and ease of installation, making them highly suitable for a wide range of industrial applications. Their unique properties have made them a preferred choice for infrastructure projects that require reliable and long-lasting materials. In this article, we will explore how FRP pipe piles function, their advantages, and their applications in key construction industries.
The Key of FRP Pipe Piles in Modern Infrastructure
FRP pipe piles are structural supports made from Fiberglass Reinforced Plastic, a composite material known for its high strength and resistance to environmental damage. FRP pipe piles are particularly valuable in coastal and marine projects, where environmental factors such as moisture, saltwater, and chemical exposure can quickly deteriorate other types of materials. These piles serve to transfer loads from the structure down to stable soil layers, ensuring the integrity and longevity of the build, such as the projects of the FRP Pipe Bridge, where durability is crucial.
Their purpose is not limited to just structural stability; FRP pipe piles also help reduce long-term maintenance costs due to their resistance to corrosion and low upkeep requirements. As a result, these piles are increasingly being used in projects ranging from bridges and seawalls to industrial plants and environmental protection systems.
Key Applications of FRP Pipe Piles
FRP pipe piles are used across a wide range of industries, from coastal infrastructure to industrial plants. Below, we outline some of the primary applications of FRP pipe piles in different sectors.
Coastal and Marine Construction Projects
One of the most common uses of FRP pipe piles is in coastal and marine construction. Structures built in or near water, such as seawalls, docks, and piers, are constantly exposed to moisture, saltwater, and the corrosive elements of the marine environment. Traditional materials like steel and wood are prone to degradation over time in these conditions, but FRP pipe piles provide a much more durable alternative.
FRP pipe piles offer excellent resistance to both saltwater corrosion and marine life, which can weaken traditional piles. Their lightweight nature also makes it easier to install them in remote or hard-to-reach locations, often a challenge in marine construction projects. GangLong Fiberglass manufactures specialized FRP pipe piles designed for marine environments, ensuring the longevity and stability of such structures.
Bridge Foundations and Supports
FRP pipe piles are also increasingly being used in the construction of bridges and their support systems. Bridges are subjected to constant stress from traffic, wind, and environmental factors. The use of FRP pipe piles provides a solution that can withstand these stresses without corroding or degrading over time.
Because FRP pipe piles are resistant to moisture and other corrosive elements, they are an excellent choice for bridge projects that span water or are located in areas with high humidity. Additionally, the lightweight nature of FRP pipe piles allows for quicker and less costly installation, reducing the overall time and expense associated with bridge construction projects.
Environmental Protection Structures
In projects designed to protect the environment, such as erosion control structures or wastewater treatment plants, FRP pipe piles offer the durability and resistance needed to ensure long-term success. For example, in erosion control projects, FRP pipe piles can be used to anchor barriers or retaining walls, preventing soil erosion in areas prone to flooding or heavy rainfall.
Wastewater treatment facilities often rely on piping systems and support structures that are exposed to a variety of chemicals and contaminants. FRP pipe piles are resistant to these corrosive elements, making them a reliable option for such applications. In addition to their durability, FRP pipe piles are a more environmentally friendly choice compared to traditional materials, as they require fewer repairs and replacements over time.
Industrial Plants and Piping Systems
FRP pipe piles play a significant role in industrial settings where high durability and corrosion resistance are essential. In industries like chemical processing, oil refining, and power generation, piping systems are often exposed to harsh chemicals and extreme temperatures. FRP pipe piles provide the necessary structural support to ensure that these piping systems remain intact and functional despite challenging conditions.
For instance, in chemical plants, FRP pipe piles can support pipes that transport corrosive liquids, reducing the likelihood of structural failure. Similarly, in power plants, these piles can support critical infrastructure exposed to high heat and pressure, ensuring continued operation without the need for constant maintenance.
Types of fiberglass insulation: Making the right choice
Future Developments in FRP Pipe Pile Technology
The future of FRP pipe piles looks promising as advancements in materials, manufacturing processes, and integration of new technologies continue to push the boundaries of their performance. Researchers and engineers are focused on enhancing the strength, durability, and versatility of FRP materials to ensure that they remain a reliable solution for modern construction projects. Additionally, the introduction of smart technologies for real-time monitoring and predictive maintenance will help improve the long-term reliability and sustainability of FRP pipe piles. Below are some of the key areas where future developments are likely to make a significant impact.
Advancements in Material Science
The future of FRP pipe piles will see improvements in material science, leading to stronger, more durable products.
Researchers are continually exploring new fibers, resins, and composite materials that can be used to enhance the strength and durability of FRP pipe piles. One area of focus is the development of high-performance resins that offer better resistance to environmental factors such as UV degradation, moisture, and chemicals. New fiber technologies, including carbon fiber or hybrid fiber-reinforced composites, could be integrated into FRP piles to further boost strength while keeping the material lightweight. The goal is to create pipe piles that can withstand even more extreme conditions, making them suitable for a broader range of applications, from offshore oil rigs to extreme environmental conditions. As a result, future FRP pipe piles will be more resilient, longer-lasting, and able to support more demanding loads.
Enhanced Manufacturing Processes
Future innovations in manufacturing will further improve the efficiency and customization of FRP pipe piles.
Advancements in filament winding techniques and other manufacturing processes will allow for greater precision and faster production of FRP pipe piles. Automation, for example, is likely to become more integrated into the manufacturing process, enabling more consistent quality control, reducing labor costs, and increasing production efficiency. Additionally, 3D printing or additive manufacturing could be employed to create more complex geometries or tailor-made designs for specific projects. These developments will make FRP pipe piles more adaptable to various design requirements, enabling engineers to create custom solutions for unique site conditions. Furthermore, these advanced manufacturing processes will reduce production time and cost, making FRP pipe piles even more accessible to a wider range of industries.
Integration of Smart Technologies
Incorporating smart technologies into FRP pipe piles will revolutionize their long-term performance and maintenance.
The integration of sensors into FRP pipe piles is a significant step towards improving their functionality and lifespan. Sensors can monitor critical parameters such as strain, temperature, humidity, and vibrations, providing real-time data on the pile’s condition. This data can be used for predictive maintenance, alerting engineers when maintenance is required before any serious issues arise, thus preventing costly damage or downtime. This will allow for more efficient and timely interventions, minimizing the need for routine inspections and extending the lifespan of FRP pipe piles. Additionally, the real-time monitoring capabilities can provide valuable insights into how the piles perform under different environmental conditions, leading to the optimization of future pile designs. With the rise of smart infrastructure, FRP pipe piles are likely to become integral components of more intelligent and sustainable construction projects.
Sustainability and Environmental Impact
Sustainability is an increasingly important factor in the development of FRP pipe piles, with efforts being made to reduce their environmental impact.
As demand for sustainable construction solutions rises, there is a growing focus on making FRP pipe piles more eco-friendly. Future developments may include the use of recycled fibers or bio-based resins in the manufacturing of FRP piles, reducing the environmental footprint of production. Additionally, the long lifespan and low maintenance requirements of FRP pipe piles make them an inherently sustainable option for construction projects. By incorporating renewable materials and optimizing manufacturing processes to reduce waste, the environmental impact of FRP pipe piles can be minimized. These advancements will further solidify FRP pipe piles as a leading solution in eco-conscious construction, making them more attractive for projects with sustainability goals.
Adaptability to New Applications
With continuous advancements, FRP pipe piles will become more versatile, finding applications in an even wider array of industries.
As the material science and manufacturing processes evolve, FRP pipe piles will become more adaptable to different project requirements. They are already used in marine structures, retaining walls, and foundations, but future developments could extend their application to other industries such as renewable energy, transportation infrastructure, and high-risk construction zones. For instance, FRP pipe piles could be adapted for use in offshore wind farms, where their lightweight, corrosion-resistant properties are ideal for submerged conditions. Additionally, as the demand for resilient and long-lasting structures grows, FRP pipe piles may find applications in disaster-prone areas or regions with severe environmental conditions. By enhancing their versatility, FRP pipe piles will continue to meet the evolving needs of the global construction industry.
Future developments in FRP pipe pile technology will focus on enhancing material performance, optimizing manufacturing processes, and integrating smart technologies for improved monitoring and maintenance. These innovations will lead to stronger, more durable, and versatile FRP pipe piles that can meet the demands of an expanding range of applications. As these advancements unfold, FRP pipe piles will play an increasingly critical role in sustainable and resilient construction projects, providing long-lasting solutions to modern infrastructure challenges.
Choosing FRP Pipe Adhesive for Durable Piping Connections
FAQs about Frp Pipe Piles
The cost of FRP piles varies depending on several factors, including the size, length, design specifications, and the complexity of the project. Generally, FRP piles tend to have a higher initial cost compared to traditional materials like wood, steel, or concrete. However, their long-term benefits, such as durability, corrosion resistance, and minimal maintenance requirements, often lead to cost savings over the lifespan of the project. In addition to the material cost, other expenses such as transportation, installation, and any custom fabrication required should be considered when estimating the total investment for FRP piles. GangLong Fiberglass offers a range of FRP pile products designed to provide an optimal balance between performance and cost, tailored to suit specific project needs. The price can vary depending on market conditions, the scope of the project, and any additional features such as coatings or custom finishes that enhance the pile’s performance in specific environments.
While FRP pipes offer numerous advantages, such as corrosion resistance, lightweight construction, and durability, they also have some disadvantages. One of the primary concerns is the higher upfront cost compared to traditional piping materials like PVC, steel, or concrete. This higher initial investment can be a barrier for projects with limited budgets. Additionally, FRP pipes can be susceptible to mechanical damage, such as cracking or splintering, especially during handling, transportation, or installation if not done carefully. They can also be affected by UV exposure over time, which may lead to surface degradation if not properly protected with UV-resistant coatings. Furthermore, while FRP pipes are chemically resistant, they may not be suitable for all chemical environments, particularly those involving certain solvents or highly acidic substances. GangLong Fiberglass offers FRP pipes that are designed to mitigate these disadvantages through careful design, protective coatings, and adherence to quality manufacturing standards.
FRP pipes, while highly advantageous in many applications, can present certain challenges. One common issue is their sensitivity to improper installation. Unlike metal pipes, FRP pipes require specialized handling and installation techniques to avoid damage. Incorrect installation can lead to issues like joint failures, cracking, or stress damage, which can compromise the integrity of the piping system. Another problem is the potential for delamination, where the layers of the FRP material separate due to impact, excessive stress, or manufacturing defects. This can result in a loss of structural strength and potential leaks. Additionally, although FRP pipes are generally resistant to a wide range of chemicals, exposure to certain aggressive chemicals not compatible with the resin system can cause degradation over time. GangLong Fiberglass addresses these problems by providing high-quality FRP pipes that are designed and manufactured with precision, and by offering comprehensive installation guidelines to ensure the longevity and reliability of the piping system.
FRP stands for Fiberglass Reinforced Plastic. It is a composite material made by combining a polymer matrix (such as epoxy, vinyl ester, or polyester resin) with fiberglass reinforcement. FRP pipe piles are known for their lightweight, high strength, and resistance to corrosion, making them suitable for harsh environments. In the context of pipe piles, FRP is used for applications such as retaining walls, marine foundations, and load-bearing piles. This material’s durability and chemical resistance make it a practical alternative to traditional materials like steel or concrete in many scenarios.
FRP pipe piles do not crack easily under normal operating conditions. The material’s high tensile strength and flexibility make it resistant to cracking due to mechanical stress. However, FRP can crack if subjected to excessive impact, sharp concentrated loads, or if improperly designed or installed. Over time, prolonged exposure to UV radiation or chemical environments without appropriate protective coatings may also degrade the resin matrix, potentially leading to surface cracking. That said, compared to traditional materials like concrete or brittle plastics, FRP is less prone to cracking and better suited for applications where impact resistance and flexibility are required. Proper design, maintenance, and installation help mitigate the risk of cracking.
Modern FRP pipe piles do not contain asbestos. Historically, some composite materials included asbestos fibers for reinforcement, but this practice was discontinued due to health and safety concerns. Today’s FRP is reinforced with fiberglass or carbon fibers, which are non-toxic and safer to handle. Manufacturers adhere to strict environmental and safety standards to ensure their products are asbestos-free. For applications like pipe piles, fiberglass reinforcement is preferred for its strength, corrosion resistance, and ease of fabrication, making it a sustainable and safe choice. When purchasing FRP products, it is still advisable to verify material certifications to ensure compliance with health and safety regulations.
Installing FRP pipe piles involves several key steps:
Site Preparation: Assess soil conditions and ensure proper alignment for installation.
Pile Placement: Drive or drill the FRP pipe piles into the ground using impact hammers, vibratory drivers, or hydraulic presses. FRP piles can be installed similarly to steel piles but require lower driving energy due to their lighter weight.
Cutting and Jointing: Cut piles to the desired length using saws or grinders and connect them with mechanical joints, adhesives, or flanges as needed.
Grouting: Fill the hollow core with concrete or grout for added strength and stability if required.
Inspection: Ensure alignment, depth, and structural integrity meet design specifications.
The lightweight nature of FRP simplifies transportation and installation, reducing labor and equipment costs compared to traditional steel or concrete piles.
FRP pipe piles can fail due to several mechanisms:
Mechanical Overload: Excessive loading beyond design capacity can cause cracking, buckling, or delamination of the composite layers.
Environmental Degradation: Prolonged UV exposure, chemical attack, or water ingress can degrade the resin matrix, leading to loss of strength.
Impact Damage: Heavy impacts during handling or installation may create localized fractures or weaken the pile.
Manufacturing Defects: Poor-quality resin, improper fiber alignment, or voids within the composite can compromise the pile’s structural integrity.
Failures are rare when FRP is properly designed, manufactured, and installed. Routine inspections and maintenance ensure the long-term performance of FRP piles.
FRP pipe piles have a service life of 50 to 100 years, depending on environmental conditions and application. They are highly durable due to their resistance to corrosion, UV degradation, and chemical attack. Unlike steel, which can rust, or concrete, which may crack or deteriorate in marine or aggressive environments, FRP maintains its structural integrity over decades. Advances in resin technology and coatings further enhance the longevity of FRP. While the initial cost may be higher than traditional materials, the reduced maintenance and extended lifespan make FRP a cost-effective solution over its life cycle.
The wall thickness of FRP pipe piles typically ranges from 3 mm to 50 mm, depending on the diameter, application, and design specifications. For structural applications like pipe piles, the wall thickness is optimized to balance weight and load-bearing capacity. Thicker walls are used for high-load or high-pressure applications, while thinner walls suffice for lightweight structures. The manufacturing process, such as filament winding or pultrusion, allows precise control of thickness and fiber orientation to meet specific engineering requirements.
FRP is generally more expensive than steel in terms of upfront material cost. However, FRP pipe piles offer lower lifecycle costs due to their minimal maintenance requirements, corrosion resistance, and long service life. Steel piles may need periodic painting, galvanizing, or replacement in corrosive environments, while FRP avoids these expenses. Additionally, the lightweight nature of FRP reduces transportation and installation costs. When considering overall project costs, FRP often proves to be more economical, especially in marine, chemical, or highly corrosive environments where steel requires extensive protection.
Yes, FRP is widely used today across various industries, including construction, marine engineering, and infrastructure development. FRP pipe piles are increasingly adopted for their corrosion resistance, lightweight properties, and sustainability compared to traditional materials. They are used in retaining walls, seawalls, bridge foundations, and industrial piping systems. Advances in material science and manufacturing techniques continue to expand FRP’s applications, making it a preferred choice for projects requiring durability and resistance to harsh environmental conditions.
Yes, FRP is stronger than PVC in terms of tensile strength, flexural strength, and load-bearing capacity. While PVC is a lightweight and cost-effective material for low-pressure applications, it lacks the structural integrity and durability required for heavy-duty uses like pipe piles. FRP’s combination of fiberglass reinforcement and polymer resin provides superior mechanical properties, enabling it to withstand high loads and environmental stress. Additionally, FRP is more resistant to UV radiation, impact, and chemical exposure than PVC, making it a better choice for long-term structural applications.
Fiberglass refers to the raw reinforcement material made of fine glass fibers, while FRP (Fiberglass Reinforced Plastic) is a composite material combining fiberglass with a polymer resin. Fiberglass provides tensile strength and rigidity, while the resin binds the fibers, offering shape, durability, and resistance to environmental factors. In the context of FRP pipe piles, the composite structure makes FRP stronger, more durable, and corrosion-resistant compared to raw fiberglass. Fiberglass alone is brittle and unsuitable for structural applications, whereas FRP’s matrix ensures it can handle heavy loads and harsh environments, such as those found in marine or industrial projects.
The key difference lies in the resin used. FRP (Fiberglass Reinforced Plastic) typically uses polyester or vinyl ester resin, whereas GRE (Glass Reinforced Epoxy) uses epoxy resin as the matrix. GRE pipes are known for higher mechanical strength, heat resistance, and better chemical compatibility compared to standard FRP pipes. For FRP pipe piles, the choice depends on the application; GRE is preferred in industries where extreme heat or aggressive chemicals are present, while standard FRP is more cost-effective for general-purpose uses like marine piles, retaining walls, or lightweight structural supports.
FRP and GRP (Glass Reinforced Plastic) are often used interchangeably, but technically, GRP specifically refers to fiberglass-reinforced materials. FRP is a broader term encompassing composites reinforced with other materials, such as carbon fibers. In practical terms, for pipe piles, GRP and FRP often refer to the same material. GRP pipes emphasize the use of glass fiber reinforcement, which provides excellent corrosion resistance, making them ideal for applications like seawalls and underwater foundations. The difference is more about terminology, as both are widely used in similar structural applications.
FRP and HDPE pipes differ in material composition and performance. FRP is a composite material with fiberglass reinforcement, offering high strength, rigidity, and corrosion resistance. HDPE (High-Density Polyethylene) is a thermoplastic known for its flexibility, impact resistance, and low cost. For pipe piles, FRP is superior in load-bearing capacity and durability, particularly in corrosive or marine environments, while HDPE is better suited for applications requiring lightweight, flexible piping. FRP is preferred for structural applications like retaining walls or load-bearing piles, whereas HDPE is more commonly used for low-pressure fluid transport.
The pressure rating of FRP pipe depends on its design and application. FRP pipe piles are not typically rated for high internal pressures as they are used structurally rather than for fluid transport. However, standard FRP pipes used in industrial applications can handle pressures ranging from 50 psi to 1,500 psi. For pipe piles, the emphasis is on external loads and axial strength rather than internal pressure, and design specifications are adjusted based on soil conditions, load requirements, and installation depth.
The purpose of FRP in pipe piles is to provide a durable, lightweight, and corrosion-resistant alternative to traditional materials like steel or concrete. FRP is used in structural applications such as retaining walls, bridge foundations, and marine environments, where its resistance to water, chemicals, and UV radiation ensures long-term performance. In addition, FRP pipe piles reduce installation costs due to their lightweight nature and eliminate the need for extensive maintenance, making them ideal for projects in harsh or remote environments.
For pipe piles, FRP is better than HDPE due to its superior strength, rigidity, and load-bearing capacity. FRP excels in structural applications where durability and resistance to environmental factors like corrosion or UV radiation are critical. HDPE, while more flexible and cost-effective, lacks the structural integrity required for load-bearing applications such as retaining walls or deep foundations. However, HDPE may be preferred for fluid transport in non-structural applications. For FRP pipe piles, FRP’s long service life and minimal maintenance outweigh HDPE’s lower upfront cost.
FRP is expensive primarily due to its manufacturing process and material costs. The production of fiberglass reinforcement, resin matrices, and composite fabrication requires specialized equipment and expertise. Additionally, FRP’s performance benefits, such as corrosion resistance, lightweight design, and long lifespan, justify its higher initial cost. For pipe piles, the expense is offset by reduced installation, transportation, and maintenance costs over the product’s lifecycle. FRP’s unique ability to perform in harsh environments without degradation makes it a cost-effective choice despite the upfront investment.
FRP (Fiber Reinforced Polymer) is not inherently stronger than steel in all respects but excels in specific applications. Its tensile strength can exceed steel when comparing weight-to-strength ratios, as FRP is significantly lighter. This makes it advantageous in construction projects requiring reduced load stress. Steel, however, has superior compressive strength and is more resistant to impact forces, making it better suited for high-load scenarios. For pipe piles, FRP’s strength-to-weight ratio offers long-term durability and reduced maintenance compared to steel, especially in corrosive environments like marine or chemical installations. Steel may still outperform FRP in extreme load-bearing applications where its high modulus of elasticity is essential. The decision to use FRP or steel depends on factors like environmental exposure, required strength, and longevity, with FRP often chosen for its corrosion resistance and light weight.
Yes, FRP is inherently waterproof due to its composite structure of fibers embedded in a resin matrix. This makes FRP an excellent choice for pipe piles in marine, subterranean, and high-moisture environments. Unlike materials like wood or uncoated steel, FRP does not absorb water, swell, or corrode. Additionally, FRP can be engineered with enhanced water-resistant properties, making it particularly effective in applications like sea walls, jetties, and submerged pipe piling systems. However, while FRP resists water intrusion, its durability depends on the quality of the resin and the manufacturing process. Proper sealing and installation are crucial to prevent potential joint or fitting failures, especially in extreme environments. Its waterproof characteristics, coupled with resistance to chemical and biological degradation, make FRP a preferred material for long-term water-exposed applications.
PVC is generally cheaper than FRP due to differences in material composition and manufacturing complexity. PVC, a thermoplastic polymer, is mass-produced and widely used in applications requiring cost-effective solutions. On the other hand, FRP is a composite material made from high-strength fibers and resin, which involves a more complex and costly manufacturing process. While PVC may be a more economical choice for low-stress applications, it lacks the structural strength, thermal stability, and corrosion resistance of FRP. For pipe piles, PVC may only be suitable for light-duty applications, whereas FRP is ideal for high-performance requirements, especially in corrosive or load-bearing environments. Although FRP has a higher upfront cost, its long lifespan and reduced maintenance often make it a more cost-effective solution over time.
Common pipe pile sizes vary based on application, with diameters typically ranging from 4 inches to 48 inches or more. For FRP pipe piles, sizes are often customized to meet specific structural and environmental needs. Wall thickness can vary from 0.25 inches to 1 inch or more, depending on load requirements and environmental conditions. Standard lengths range from 20 to 40 feet, but longer lengths can be achieved by splicing or manufacturing bespoke sizes. FRP pipe piles are often designed with a focus on lightweight properties, making them easier to transport and install than traditional steel or concrete piles. Larger diameters and wall thicknesses are used for heavy-load applications like marine foundations, while smaller sizes are suitable for retaining walls and light structural support.
The four main types of FRP are categorized based on the fiber reinforcement used:
Glass Fiber Reinforced Polymer (GFRP): Most common type, offering good strength and corrosion resistance at a relatively low cost.
Carbon Fiber Reinforced Polymer (CFRP): Known for high strength-to-weight ratio and stiffness, ideal for high-performance applications.
Aramid Fiber Reinforced Polymer (AFRP): Offers high impact resistance and flexibility, commonly used in dynamic loading conditions.
Basalt Fiber Reinforced Polymer (BFRP): Emerging material offering similar properties to GFRP but with higher thermal and chemical resistance.
Each type of FRP has specific benefits and is chosen based on the application requirements. In pipe piles, GFRP is often the preferred choice due to its cost-effectiveness and durability in corrosive environments.
While FRP has many advantages, it also has some disadvantages in construction:
High Initial Cost: FRP materials are more expensive than traditional materials like steel, concrete, or PVC.
Low Modulus of Elasticity: FRP is less stiff than steel, which can lead to greater deflection under heavy loads.
Brittleness: FRP lacks ductility, meaning it can fail suddenly without significant deformation.
Specialized Installation: Handling and installation require expertise, as improper techniques can compromise its structural integrity.
UV Degradation: Prolonged exposure to sunlight can degrade the material if not properly coated or protected.
Despite these challenges, FRP’s benefits often outweigh its disadvantages in environments requiring corrosion resistance and lightweight materials.
Pipe piling grades are typically classified by material strength and intended use. For steel pipe piles, grades such as ASTM A252 (Grade 1, Grade 2, and Grade 3) are common, with Grade 3 offering the highest strength. For FRP pipe piles, the grading is less standardized and often depends on the fiber type (e.g., GFRP, CFRP) and the resin system (e.g., polyester, epoxy). Manufacturers often provide specifications such as tensile strength, compressive strength, and stiffness to guide selection. Unlike steel, FRP grading focuses more on performance characteristics like corrosion resistance, durability, and environmental suitability rather than standard strength categories.
FRP pipes are used in various applications requiring corrosion resistance, lightweight properties, and durability. Common uses include:
Marine Environments: As pipe piles for piers, docks, and seawalls, resisting saltwater corrosion.
Chemical Plants: Handling corrosive fluids and gases.
Subterranean Applications: In water supply and drainage systems.
Oil & Gas Industries: Transporting hydrocarbons and handling wastewater.
Structural Support: In building foundations and retaining walls.
FRP pipes excel in situations where traditional materials like steel or concrete would degrade rapidly due to chemical or environmental exposure.
Hard plastic pipes are commonly referred to by their specific material names, such as PVC (Polyvinyl Chloride), CPVC (Chlorinated Polyvinyl Chloride), or HDPE (High-Density Polyethylene). In the context of FRP pipe piles, the term might refer to the rigid nature of FRP pipes, which combine hard thermosetting resins with reinforcing fibers. These materials provide structural rigidity and durability for demanding applications. PVC and HDPE are more commonly used in general plumbing and light-duty projects, while FRP is reserved for high-performance, corrosion-resistant applications.
A pile is a structural element driven into the ground to support loads from a structure, often used in deep foundation systems. Piles are designed to bear axial and lateral loads and are used in construction projects like bridges, buildings, and marine installations. FRP pipe piles fall into this category, offering durability and corrosion resistance.
A pole, on the other hand, is a slender vertical structure typically used for support or as a standalone element, such as utility poles or light poles. Poles generally bear less load than piles and are not embedded as deeply. In summary, piles are load-bearing and foundational, while poles are more lightweight and functional.
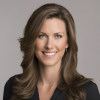
As the editor of GangLong Fiberglass, I have years of experience and in-depth research, focusing on cable tray products, fiberglass solutions, and grille systems. I incorporate years of industry insights and practical experience into every content, committed to promoting the progress of the industry. At GangLong Fiberglass, my commitment is reflected in every product, from innovative cable trays to durable fiberglass solutions and sturdy grille systems. As an authoritative voice in the industry, my goal is to provide valuable information to professionals and businesses and promote forward-looking solutions.