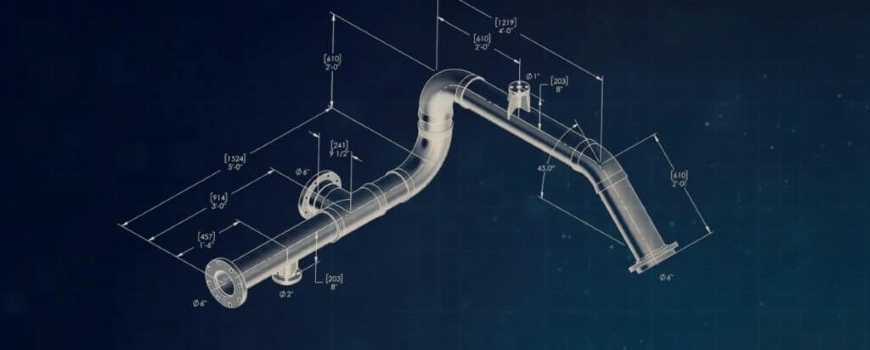
FRP pipe temperature limits refer to the maximum and minimum temperatures that fiberglass-reinforced plastic pipes can withstand without compromising performance. These limits are primarily influenced by the type of resin used in manufacturing. FRP pipe temperature limits range from -57°C to 149°C, with specialized resins extending performance for extreme conditions. GangLong Fiberglass offers FRP pipes designed to perform efficiently within these temperature ranges, ensuring durability in a variety of industrial applications. By considering the FRP pipe friction factor, these pipes maintain optimal flow characteristics and reduce energy consumption, further enhancing their suitability for demanding environments. It is essential to choose the appropriate FRP pipe temperature limits based on the specific operating conditions to maintain the integrity of the pipe system.
Simplifying Your Life: Key Functionalities
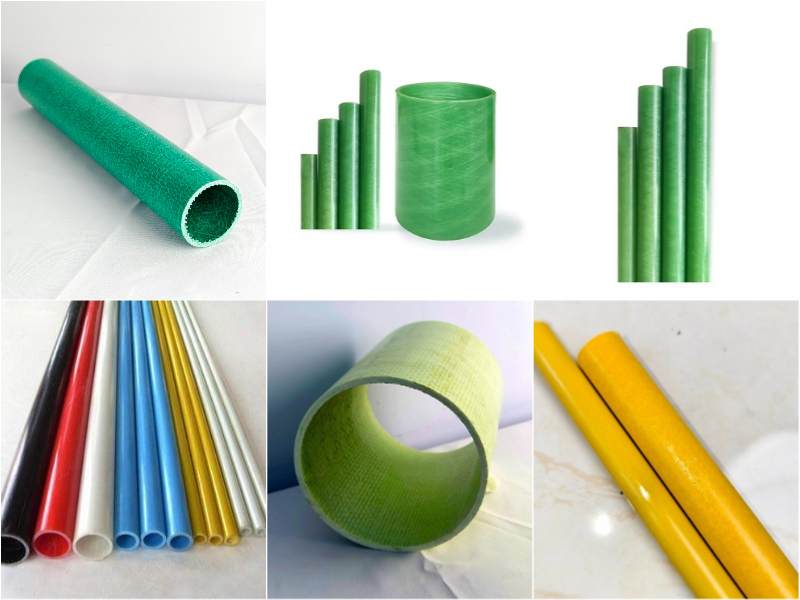
Attributes | Details |
---|---|
Place of Origin | Hebei, China |
Brand Name | GangLong Fiberglass |
Product Name | FRP Pipe |
Material | Fiberglass Reinforced Plastic |
Technology | Pultrusion |
Surface Treatment | Customized |
Processing Services | Bending, Forming, Cutting |
Color | Customized Color |
Shape | Customized Shape |
Size | Customized Size |
Thickness | Customized Thickness |
Diameter | Customized Diameter |
Length | Customized Length |
Quality | High Quality |
Features | Insulated Support Chain, High Strength, Excellent Corrosion Resistance |
Applications | Transporting Water, Sewage, Chemicals; Exhaust, Cable Tray |
Certificate | ISO9001 |
Port | All Ports in China |
Sales Unit | Single Item |
Supply Capacity | 2000 Meters Per Month |
Piping Design and Temperature Effects on Fiberglass Pipe
Key Design Considerations for Fiberglass Piping Systems
In the design of fiberglass piping systems, understanding and accounting for temperature fluctuations is essential for ensuring long-term efficiency and performance. As the temperature changes, the piping material expands and contracts, which can impact the overall system stability. FRP pipe temperature limits must be considered to avoid exceeding the operational boundaries of the material, as extreme temperatures can compromise the structural integrity of the pipes. Proper system design addresses this by using unrestrained or restrained piping configurations to accommodate thermal expansion and contraction within the safe temperature range for fiberglass pipes.
Unrestrained Systems
Unrestrained fiberglass pipes are generally designed to operate near their installation temperature. The primary design consideration in such systems is the support span spacing. When a piping system faces temperature-induced expansion or contraction, flexibility is incorporated, usually by integrating directional changes (e.g., elbows or tees) that provide space for movement. If the directional changes are not sufficient, expansion joints or loops should be added to avoid overstressing the system. This type of design minimizes the risk of damage but requires careful consideration of flexibility and support to manage thermal movements effectively.
Restrained Systems
Fully restrained or “anchored and guided” piping systems prevent thermal movement by using anchors. These systems are particularly beneficial for locations where the piping needs to be securely fixed in place. Anchors are placed at the ends of straight runs and at directional changes (like elbows or tees) to transmit loads to the support structure. These systems experience internal loads due to temperature changes, which help maintain equilibrium but require careful substructure design to handle the stresses. For fiberglass systems, the anchor loads are significantly smaller compared to steel systems, as fiberglass is less stiff and responds differently to thermal changes.
Material Properties and Thermal Movement
The behavior of fiberglass pipes under temperature variations is largely governed by two critical material properties: the coefficient of thermal expansion (α) and the axial moduli of elasticity.
Coefficient of Thermal Expansion
Fiberglass has a higher coefficient of expansion compared to steel, roughly twice that of steel. This means that fiberglass pipes experience more significant movement with temperature changes in unrestrained systems. For example, if steel pipes expand by 1 inch over 100 feet, fiberglass pipes will expand by 2 inches under the same conditions. In the case of thermal expansion, fiberglass pipes require more allowance for movement, making proper support spacing even more critical.
Axial Moduli of Elasticity
Fiberglass pipes exhibit both axial compression and axial tensile moduli. The axial compression modulus of elasticity for fiberglass is between 3% and 10% of that of steel, making it more flexible and less prone to damage from thermal stresses. The lower axial modulus means that fiberglass piping is less likely to develop bending stresses when exposed to thermal movement, leading to a reduced need for heavy anchoring systems compared to steel pipes.
Comparison with Thermoplastic Pipes
Thermoplastic pipes, such as PVC, typically have an even higher coefficient of expansion than fiberglass—more than four times that of fiberglass. This greater expansion results in even more significant thermal movement, which makes thermoplastic pipes more vulnerable to buckling at elevated temperatures. Additionally, thermoplastic pipes have much lower moduli of elasticity, which rapidly decrease as temperatures rise above 100°F. This makes thermoplastic pipes susceptible to distortion, requiring extensive support systems at elevated temperatures.
Impact of Temperature Gradient and Thermal Stresses
In any piping system, the temperature gradient plays a pivotal role in determining how the system will react to thermal changes. A positive temperature gradient occurs when the operating temperature is higher than the installation temperature, leading to expansion. Conversely, a negative temperature gradient occurs when the operating temperature is lower, causing contraction. Many piping systems will encounter both positive and negative gradients during their life cycle, which must be taken into account during design.
Positive Temperature Gradient
When the operating temperature is higher than the installation temperature, the temperature gradient is positive. This causes the system to expand and requires careful design to accommodate this movement.
Negative Temperature Gradient
A negative temperature gradient occurs when the operating temperature is lower than the installation temperature, causing the piping system to contract. This condition must also be considered in the design to prevent issues like stress or buckling.
What are FRP Pipe Temperature Limits
What Are FRP Pipe Temperature Limits and Their Impact on Performance
FRP (Fiberglass Reinforced Plastic) pipes are widely used in industries requiring durable, corrosion-resistant materials, especially in environments exposed to chemicals and varying temperatures. One of the critical factors that influence the performance and longevity of these pipes is their temperature limit. Understanding FRP pipe temperature limits is essential for ensuring the right material is chosen for specific applications, especially in industries like chemical processing, oil and gas, and wastewater management. In this article, we’ll explore how temperature affects FRP pipes, the role of resin selection, and what factors determine their suitability in high-temperature environments.
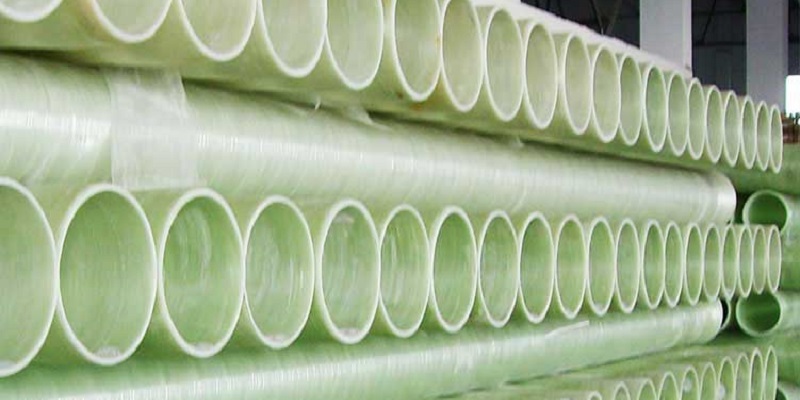
The Importance of Resin Selection for Temperature Resistance
The resin system used in FRP (Fiberglass Reinforced Plastic) pipes plays a crucial role in determining their temperature resistance and overall performance in various industrial environments. Different types of resins offer varying levels of thermal resistance, which directly impacts the pipe’s ability to withstand heat and maintain structural integrity over time. The primary resins used in FRP pipes are polyester, vinyl ester, and epoxy, each offering distinct advantages based on the specific temperature requirements of the application.
- Polyester Resins: These are the most common and cost-effective resins used for general-purpose applications. Polyester resins offer good mechanical properties but typically have a lower temperature tolerance, usually up to 200°F (93°C). They are suitable for environments where temperatures do not fluctuate dramatically and remain within moderate ranges.
- Vinyl Ester Resins: For more demanding applications, vinyl ester resins are preferred. They provide superior heat resistance and excellent chemical resistance. Vinyl ester resins can withstand temperatures up to 250°F (121°C), making them suitable for environments with higher temperature exposure or where pipes may be exposed to aggressive chemicals. Additionally, vinyl ester resins are known for their enhanced resistance to thermal cycling, making them a great choice for systems subject to frequent temperature fluctuations.
- Epoxy Resins: Epoxy resins offer the highest thermal resistance among common FRP materials. These resins can withstand temperatures up to 300°F (149°C) or higher, depending on the specific formulation. Epoxy-based FRP pipes are ideal for extreme conditions, such as in chemical processing, oil and gas industries, or high-temperature fluid handling systems, where superior strength and heat resistance are critical.
When selecting FRP pipes for high-temperature applications, it’s essential to consider the expected operating conditions and choose the right resin system that aligns with those requirements. For example, in a chemical processing plant where pipes must withstand both high temperatures and corrosive chemicals, vinyl ester resins would offer the best combination of heat resistance and corrosion protection. In contrast, epoxy resins would be optimal for industries that demand the highest performance, such as in the oil and gas sector or power generation.
In conclusion, selecting the right resin is vital to ensuring that FRP pipes will perform effectively without degradation in high-temperature environments. Whether for moderate or extreme temperature conditions, understanding the resin options available and consulting product specifications is key to selecting FRP pipes that will meet both performance and durability needs over time. GangLong Fiberglass offers a wide range of FRP pipes designed with various resin systems, providing tailored solutions for diverse temperature and chemical resistance requirements.
How Operating Conditions Affect FRP Pipe Performance
Operating conditions, including the type of fluid or gas being transported and environmental factors, play a crucial role in determining the temperature limits of FRP (Fiberglass Reinforced Plastic) pipes. The ability of FRP pipes to withstand temperature fluctuations is influenced not only by the resin type and pipe design but also by the external conditions under which the pipes operate.
Type of Media
The chemical composition and temperature of the fluid or gas being transported through the pipe directly affect the temperature limits. For instance, corrosive liquids or gases, such as acids, solvents, or high-temperature chemicals, can accelerate the degradation of the pipe material, especially when exposed to high temperatures. This is because elevated temperatures can increase the rate of chemical reactions, compromising the resin’s structural integrity. Therefore, selecting the appropriate resin system—such as vinyl ester or epoxy—is crucial to ensuring that the pipe can resist both high temperatures and the corrosive effects of the transported media.
Fluctuating Temperatures
In applications where the temperature fluctuates frequently or experiences rapid changes, such as in thermal cycling, additional stresses are placed on the FRP pipe. Expansion and contraction during temperature changes can lead to mechanical fatigue, affecting the pipe’s integrity over time. FRP pipes used in these environments must be designed with sufficient flexibility and strength to endure thermal cycling without failure. This includes selecting the appropriate resin and pipe thickness, as well as considering protective coatings that can help manage temperature-induced stress.
Ambient Temperature
The surrounding environmental temperature also plays a significant role in determining the temperature limits of FRP pipes. For outdoor installations in hot or cold climates, additional protective measures, such as UV-resistant coatings or insulation, may be necessary. Extreme heat or cold can affect the physical properties of the pipe material, so it’s important to ensure that the FRP pipe is suited to handle these external temperature extremes while maintaining its structural and thermal performance.
Pressure Levels
The pressure exerted by the fluid or gas inside the pipe is another key factor influencing FRP pipe temperature limits. High-pressure environments, especially when combined with elevated temperatures, can place additional strain on the pipe, making it more susceptible to failure. It’s important to select FRP pipes that are rated to handle both the pressure and temperature demands of the system. Understanding the pressure-temperature relationship and ensuring the selected FRP pipe can withstand these conditions is vital for maintaining safe and reliable operation.
To ensure the longevity and performance of FRP pipes, it is essential to carefully assess all operating conditions, including the type of media, temperature fluctuations, ambient temperatures, and pressure levels. By choosing the right resin system, pipe thickness, and protective coatings, project managers can select FRP pipes that meet the specific demands of the application, ensuring the system remains within safe temperature limits and operates effectively over the long term.
The Role of Pipe Thickness in Temperature Resistance
The thickness of an FRP (Fiberglass Reinforced Plastic) pipe wall is a critical factor in determining its temperature limits and overall performance in high-temperature environments. Thicker pipe walls enhance the pipe’s ability to withstand elevated temperatures by providing better insulation, reducing the rate of heat transfer, and increasing the pipe’s structural integrity. This is particularly important in applications where the pipe is exposed to prolonged heat or extreme temperature fluctuations.
Standard Thickness for Moderate Temperatures
For typical industrial applications where temperature conditions remain stable and moderate, FRP pipes are manufactured with a standard thickness that provides adequate insulation and protection. These pipes are suitable for HVAC systems, water treatment facilities, and other general-purpose applications, where temperatures typically remain within predictable and moderate ranges. Standard thickness pipes can usually handle temperatures up to 200°F (93°C) without significant degradation.
Increased Thickness for High-Temperature Environments
In high-temperature applications, such as those found in chemical processing, power generation, or industries dealing with high-temperature fluids or gases, FRP pipes with increased wall thickness are required. Thicker pipes are more capable of maintaining their performance under extreme conditions by providing enhanced thermal insulation and structural durability. These pipes are designed to withstand prolonged exposure to temperatures exceeding 250°F (121°C) or even 300°F (149°C) depending on the resin type and thickness.
Impact on Pressure Ratings
Thicker FRP pipe walls also improve the pipe’s pressure rating, enabling the pipe to handle higher internal pressures, particularly in high-temperature environments where heat-induced expansion can increase internal stress. The added wall thickness helps prevent deformation, cracking, or rupture by maintaining the pipe’s shape under both high pressure and temperature.
Customization for Specific Applications
GangLong Fiberglass offers customizable FRP pipes with varying thickness options to meet specific temperature and pressure requirements for diverse industrial projects. Whether for moderate temperature systems or extreme heat applications, selecting the appropriate wall thickness ensures the pipe’s longevity, prevents premature failure, and ensures optimal performance over time.
By carefully considering pipe thickness, industrial professionals can ensure the FRP pipe meets the required temperature limits and maintains structural integrity, providing long-term durability and reliability under challenging thermal and pressure conditions.
Factors Influencing FRP Pipe Temperature Limits
Temperature Resistance Based on FRP Pipe Sizes
FRP pipe sizes can also affect how well the pipes handle elevated temperatures. Larger diameter pipes, for example, may have different thermal properties than smaller pipes due to differences in wall thickness and material composition. Understanding how pipe size influences FRP pipe temperature limits is key to designing a system that will function effectively over a wide range of temperatures.
Larger pipes may require thicker walls to maintain their strength at high temperatures, while smaller pipes can often manage with thinner walls. GangLong Fiberglass offers a variety of pipe sizes and configurations to meet the specific needs of different applications. By selecting the right size and wall thickness, engineers can ensure that their FRP pipe system will perform reliably even under challenging thermal conditions.
Proper sizing is crucial for maintaining thermal resistance, ensuring that the pipes do not overheat or degrade when exposed to elevated temperatures. Working with experienced manufacturers like GangLong Fiberglass helps to ensure that the pipes selected will meet the specific needs of the project, both in terms of size and temperature performance.
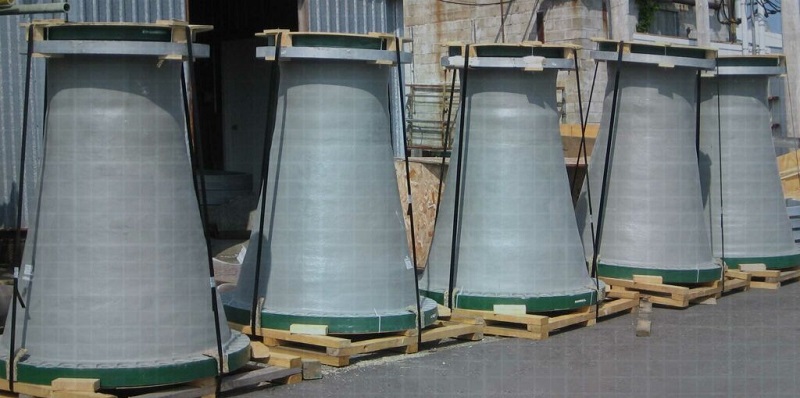
The Influence of Pressure Ratings on Temperature Limits
The relationship between pressure and temperature is a critical consideration when selecting FRP (Fiberglass Reinforced Plastic) pipes for industrial applications. As the temperature of the pipe increases, its ability to withstand internal pressure generally decreases. This happens because elevated temperatures can soften the resin matrix, reducing the pipe’s overall strength and structural integrity. This decrease in pressure tolerance is particularly important in environments where both high pressure and high temperatures are present, such as in chemical processing plants, power generation facilities, and other industries that handle extreme operating conditions.
Impact of Temperature on Pressure Tolerance
At higher temperatures, the resin matrix used in FRP pipes becomes more pliable, which reduces its ability to resist the internal pressure exerted by the transported fluid or gas. As a result, the pipe becomes more susceptible to deformation, leakage, or rupture if the pressure exceeds its rated capacity. For instance, an FRP pipe rated for 200 psi at ambient temperature may only be able to withstand 150 psi at 250°F (121°C). This temperature-pressure interaction highlights the importance of choosing the right pipe for systems subject to both thermal and pressure stresses.
Selecting the Right Pipe for High-Temperature, High-Pressure Environments
When selecting FRP pipes for high-temperature and high-pressure environments, it is essential to choose products with higher pressure ratings that are designed to maintain performance at elevated temperatures. The type of resin used is key in this selection process. Resins such as vinyl ester and epoxy are better suited for high-temperature applications and offer improved pressure retention compared to standard polyester resins. These resins help ensure that the FRP pipe maintains its structural integrity under both thermal and pressure-induced stresses.
Importance of Pressure Ratings in FRP Pipe Selection
GangLong Fiberglass provides detailed pressure ratings for their FRP pipes, specifying the maximum pressure tolerances at various temperatures. Engineers and system designers must carefully consider these ratings when selecting the right pipe for their specific needs. Exceeding the specified pressure rating at elevated temperatures can result in catastrophic failures, such as pipe rupture or leakage. Therefore, understanding the pressure-temperature relationship is essential for ensuring the safe and reliable operation of FRP piping systems in demanding applications.
By adhering to the manufacturer’s guidelines and selecting the correct FRP pipe based on both pressure and temperature limits, system designers can ensure optimal performance and prevent failures caused by thermal and pressure-related issues.
Why Choose Brown Fiberglass Insulation for Attics and Walls
High-Temperature Applications for FRP Pipes
Maximum Temperature Limits for FRP Pipes and Fiberglass Insulation
When FRP pipes are insulated with fiberglass, the insulation itself also has temperature limits that must be considered. Fiberglass insulation is commonly used to protect FRP pipes from external temperature fluctuations or to prevent heat loss in applications where maintaining the temperature of the fluid being transported is critical.
Fiberglass insulation can typically withstand temperatures up to 1000°F (538°C), making it highly effective for use in applications where high heat is a concern. However, it’s important to ensure that both the insulation and the FRP pipe have compatible temperature ratings. While the insulation may be able to handle extreme heat, the underlying FRP pipe could still be subject to damage if the temperature exceeds its resin-based limits.
In situations where both the pipe and insulation are exposed to high temperatures, selecting the correct combination of materials is essential for maintaining system integrity. GangLong Fiberglass offers guidance on matching FRP pipes with appropriate fiberglass insulation to ensure optimal performance in high-temperature applications.
Maintenance Considerations for FRP Pipes in Extreme Temperatures
Regular maintenance is key to ensuring that FRP pipes maintain their performance, especially in high-temperature applications. Even though FRP pipes are known for their durability and corrosion resistance, prolonged exposure to elevated temperatures can gradually affect their performance if not properly monitored.
Inspection: Periodic inspections should be conducted to check for signs of wear, cracks, or chemical damage, especially in high-temperature environments. These inspections can help identify potential problems before they lead to system failures.
Cleaning: Keeping FRP pipes clean is another important maintenance step. In some industries, chemical residues or scale buildup can occur inside the pipes, which may impact their performance at high temperatures. Regular cleaning can help ensure that the internal surfaces of the pipes remain free from obstructions that could reduce efficiency.
Temperature Monitoring: Installing temperature monitoring systems can help maintain optimal conditions for FRP pipes, especially in environments where temperature fluctuations are common. Monitoring systems allow operators to track temperature changes in real-time and make adjustments to prevent exceeding the frp pipe temperature limits.
GangLong Fiberglass offers a range of maintenance solutions and support services to help clients keep their FRP pipe systems in optimal condition, even in challenging high-temperature applications.
Importance of FRP Pipe Span Charts in Industrial Piping
Practical Guide for Selecting FRP Pipes Based on Temperature Limits
How to Use FRP Pipe Catalogs to Select the Right Temperature-Resistant Pipe
When selecting FRP pipes for specific projects, especially in high-temperature environments, it is essential to consult detailed product catalogues, which provide comprehensive data on temperature limits, pressure ratings, chemical resistance, and more. FRP pipe catalogues, such as those offered by manufacturers like GangLong Fiberglass, are invaluable resources for engineers, contractors, and system designers. They help ensure that the correct pipe is chosen to meet the specific requirements of a project, from temperature tolerance to chemical exposure.
These catalogues provide key information such as the maximum operating temperature for each pipe type, which is critical for ensuring the selected pipes will perform safely and efficiently in environments exposed to heat. In addition to temperature limits, catalogues also include pressure ratings, which indicate the maximum pressure that the pipes can withstand at various temperatures. This is crucial in applications where both high pressure and high temperature are present, such as in chemical processing or power generation systems.
Beyond temperature and pressure specifications, FRP pipe catalogs also include details about chemical compatibility. Different resin systems, such as polyester, vinyl ester, and epoxy, offer varying levels of resistance to chemicals, which directly impact the pipe’s ability to perform under specific conditions. By consulting the catalog, system designers can select the most appropriate resin type that will offer the best performance in the intended environment, especially when cutting FRP pipe for installation or modification.
In addition to performance specifications, these catalogues often provide insights on pipe sizes, installation practices, and maintenance recommendations. Understanding these factors helps ensure the correct installation of the pipes and prolongs their service life. Some catalogues may also include compatibility information with insulation materials, which is vital for maintaining the thermal efficiency of the system and preventing thermal stress.
By using the detailed product data provided in FRP pipe catalogues, engineers and contractors can make informed decisions that ensure the reliability and longevity of their piping systems, while minimizing the risk of failure due to temperature, pressure, or chemical-related stresses. This careful selection process ensures that the FRP pipes will operate within their specified temperature limits, providing a safe and effective solution for high-temperature applications.
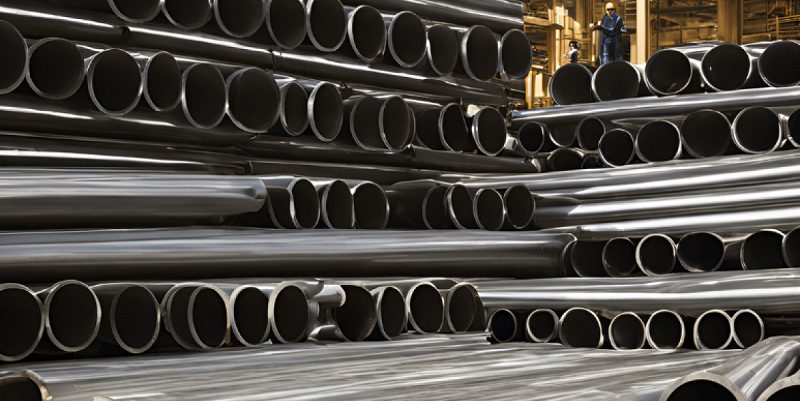
Key Considerations When Choosing FRP Pipes for Temperature Sensitivity
The performance and longevity of FRP (Fiberglass Reinforced Plastic) pipes are significantly influenced by their temperature tolerance, which is primarily determined by the type of resin used in their construction. When exposed to temperatures beyond their designed limits, FRP pipes can undergo structural changes such as softening, cracking, or a loss of mechanical strength. This highlights the importance of understanding FRP pipe temperature limits to ensure system integrity and prevent potential failure.
Standard Temperature Ranges
Standard FRP pipes, like those manufactured by GangLong Fiberglass, are generally designed to withstand temperatures ranging from 180°F to 210°F (82°C to 99°C), making them suitable for moderate temperature environments. However, when higher temperature resistance is required, specialized resins such as vinyl ester or epoxy are used to extend the temperature tolerance up to 300°F (150°C) or higher. These high-performance resins provide superior heat resistance, allowing the pipes to endure harsh thermal conditions without compromising their structural integrity.
Impact of Temperature on Resin and Pipe Performance
Temperature exposure not only affects the mechanical properties of FRP pipes but can also impact their chemical resistance. At elevated temperatures, the resin matrix that binds the fiberglass fibers can degrade, reducing the pipe’s ability to resist corrosive chemicals. This degradation is further accelerated when high temperatures are combined with aggressive chemicals, making it essential to choose the right resin type for both temperature and chemical compatibility. High-performance resins like epoxy and vinyl ester are better equipped to handle these conditions, ensuring longer service life in extreme environments.
Importance of Selecting the Right Resin
The resin type plays a critical role in defining the temperature limits of FRP pipes. While polyester resins are commonly used for standard applications, they are generally suitable for environments where temperatures do not exceed 200°F (93°C). In contrast, vinyl ester and epoxy resins are more suitable for high-temperature applications, as they can withstand temperatures of up to 300°F (150°C) and beyond. These resins offer enhanced thermal resistance, making them ideal for industries like chemical processing, oil and gas, and power generation, where both high temperatures and corrosive environments are common.
Long-Term Performance and Durability
Exposure to temperatures above the specified limits can lead to permanent damage to FRP pipes, such as cracking, embrittlement, or structural failure. Prolonged exposure to high temperatures can also cause gradual degradation of the pipe’s mechanical properties, even if the temperature remains within the specified limits. This underscores the importance of selecting a resin with a temperature tolerance margin that accounts for both expected operating conditions and potential fluctuations in temperature.
In high-temperature applications, it’s crucial to select FRP pipes with a resin system that can withstand prolonged exposure to elevated temperatures without suffering from premature aging, cracking, or delamination. Choosing the appropriate pipe material with a sufficient temperature tolerance ensures that the system remains reliable and safe throughout its operational life.
GangLong Fiberglass FRP Pipe Options
GangLong Fiberglass offers a wide range of FRP pipes designed for different temperature and pressure requirements. By consulting product specifications, engineers can select the right pipes based on their temperature limits, chemical resistance, and other performance factors. Detailed product data helps ensure that the chosen FRP pipes will meet the required standards for the intended application, ensuring long-term performance and preventing failure due to temperature stress.
In summary, understanding FRP pipe temperature limits is crucial for selecting the right material for any project. Engineers and system designers must carefully consider the resin type, temperature range, and chemical resistance when choosing FRP pipes for high-temperature environments. By ensuring that the selected pipes meet the specific temperature and pressure requirements, the reliability and safety of the piping system can be optimized, reducing the risk of failure and extending the lifespan of the system.
How to Install Fiberglass Insulation Around Outlets Correctly
FAQs about Frp Pipe Temperature Limits
FRP (Fiberglass Reinforced Plastic) tanks are designed to withstand varying temperatures depending on their construction and the resins used in their production. Generally, FRP tanks can handle temperatures between 180°F and 210°F (82°C to 99°C) with standard polyester or vinyl ester resins. However, with the use of specialized high-temperature resins, FRP tanks can withstand temperatures up to 300°F (150°C) or higher. These high-temperature-resistant tanks are used in industries such as chemical processing, where they encounter heated fluids, chemicals, and corrosive materials. When selecting an FRP tank for your specific application, it is crucial to assess the type of chemicals, exposure duration, and temperature range to ensure the tank remains functional and durable over time.
Fiberglass, in its basic form, can generally tolerate temperatures up to 1000°F (538°C), but this is primarily in situations where the fiberglass is used as a thermal insulation material. When fiberglass is used in composite structures like FRP (Fiberglass Reinforced Plastic), the temperature limit is typically determined by the type of resin system employed in the composite. Standard fiberglass composites, using polyester or vinyl ester resins, have a working temperature range of 200°F to 300°F (93°C to 150°C). For more specialized uses, high-temperature resins like phenolic or epoxy are required, which can push the temperature resistance even further. Fiberglass’s performance at higher temperatures depends on its application, resin system, and exposure duration.
The temperature limit for fiberglass reinforced plastic (FRP) varies depending on the resin matrix used during its production. In general, standard FRP materials can withstand temperatures up to 200°F (93°C). However, high-performance resins like vinyl ester or epoxy allow FRP to endure much higher temperatures, sometimes exceeding 300°F (150°C). For environments with extremely high or low temperatures, specialized FRP products can be engineered with additives that improve their heat resistance. Beyond just temperature tolerance, FRP’s performance is also affected by exposure duration and other environmental factors like humidity, chemicals, and mechanical loads. It’s essential to choose the right FRP material tailored to the specific conditions of your application to ensure its longevity and effectiveness.
Fiberglass reinforced plastic (FRP) pipes can typically withstand temperatures ranging from -40°F to 250°F (-40°C to 121°C), depending on the resin used and the specific formulation of the pipe. The maximum temperature tolerance for FRP pipes varies, with some formulations designed to handle higher temperatures up to 300°F (149°C) for short periods. However, continuous exposure to temperatures above 250°F can cause degradation in the resin matrix, leading to potential weakening of the pipe. Special high-temperature FRP materials with enhanced thermal properties are also available for more extreme conditions. FRP pipes are commonly used in chemical processing, oil and gas, and water treatment industries where temperature stability is essential. When selecting FRP pipes, it’s crucial to ensure they are designed to handle the specific operating conditions, including temperature ranges, for the application.
The temperature tolerance of plastic pipes depends on the material used. For example, PVC (polyvinyl chloride) pipes typically withstand temperatures up to 140°F (60°C), while CPVC (chlorinated polyvinyl chloride) pipes can handle temperatures up to 200°F (93°C). Polyethylene (PE) pipes are generally limited to around 140°F (60°C) as well. Plastic pipes are suitable for cold water systems, low to medium-temperature fluid handling, and HVAC systems. However, they are not ideal for high-temperature applications like steam or hot water systems. Exposing plastic pipes to temperatures beyond their rated limits can cause them to soften, deform, or lose structural integrity. For applications involving high-temperature fluids, FRP pipes or metal pipes are more commonly used due to their higher heat resistance.
FRP (fiberglass reinforced plastic) linings are commonly used to protect pipes, tanks, and other equipment from corrosion and wear in industries like chemical processing, water treatment, and food production. The temperature range for FRP linings typically spans from -20°F to 250°F (-29°C to 121°C), depending on the resin type and specific application. Some high-performance FRP linings are designed to handle temperatures as high as 300°F (149°C) for brief periods. It is crucial to select the right resin and formulation for the environment and temperature conditions in which the FRP lining will be used, as prolonged exposure to extreme temperatures beyond the specified limits can lead to resin degradation and failure. Proper installation and maintenance are key to ensuring that FRP linings perform effectively under the expected thermal conditions.
Fiberglass, when used in various forms like pipes, insulation, or other applications, has a maximum temperature limit that depends on the resin binder used. Generally, fiberglass can tolerate continuous operating temperatures up to 250°F (121°C). However, specific formulations, such as those using epoxy resins, can withstand temperatures up to 300°F (149°C) for short durations. Fiberglass-based products, such as FRP pipes, are designed to perform reliably within this range. For more extreme temperatures, special high-temperature fiberglass products with reinforced resins are used in industries such as aerospace and chemical processing. It’s important to note that prolonged exposure to temperatures beyond the recommended limits can cause the resin matrix to weaken, leading to reduced mechanical strength and potential failure.
Yes, FRP (fiberglass reinforced plastic) can be used outside and is highly suited for outdoor applications due to its resistance to environmental factors like moisture, UV radiation, and temperature fluctuations. FRP pipes and other fiberglass products are commonly used in outdoor settings such as chemical processing plants, water distribution systems, and oil and gas infrastructure. The materials used in FRP pipes are inherently resistant to corrosion and rust, making them ideal for exposed environments where metal pipes might corrode. However, UV exposure can degrade the resin over time, so it is often recommended to use UV-resistant coatings or protective jackets to extend the lifespan of FRP pipes when used outdoors. With proper maintenance, FRP can perform reliably in challenging weather conditions for years.
Fiberglass can generally withstand temperatures up to 250°F (121°C) continuously, with some specialized formulations able to tolerate short bursts of heat up to 300°F (149°C). The maximum heat resistance depends on the resin system used in the fiberglass composite. Epoxy-based fiberglass can offer higher heat resistance compared to polyester-based fiberglass, which is more commonly used for general applications. When exposed to temperatures beyond the fiberglass’s thermal tolerance, the resin matrix may begin to degrade, leading to reduced strength and potential failure of the material. For high-heat applications, such as industrial processes or insulation systems, fiberglass is a versatile and reliable material, but its temperature limitations must be carefully considered.
Yes, FRP (fiberglass reinforced plastic) is heat resistant, but its resistance to high temperatures depends on the type of resin used in its construction. Generally, FRP pipes can withstand temperatures up to 250°F (121°C) without significant degradation. Some specialized formulations, such as epoxy-based FRP, can handle higher temperatures, reaching 300°F (149°C) for short periods. However, FRP is not suitable for applications with continuous exposure to very high temperatures (above 300°F), as prolonged exposure can cause the resin to degrade and lose strength. In industries where heat resistance is critical, FRP pipes provide an effective solution for managing temperature fluctuations without compromising structural integrity.
Yes, FRP (fiberglass reinforced plastic) pipes can be heated and bent to a certain extent. However, the process of heating and bending FRP pipes must be done within the material’s temperature limits. FRP is typically molded or bent when heated to a specific temperature range, typically between 200°F and 250°F (93°C to 121°C), to allow for flexibility without damaging the material. Once the pipe cools, it retains its new shape. It’s important to ensure that the heating process does not exceed the resin’s thermal tolerance, as excessive heat can degrade the material. Heating and bending are useful in applications where custom pipe shapes or angles are required, such as in tight spaces or complex industrial systems.
Fiberglass can generally withstand temperatures up to 250°F (121°C) continuously. Some fiberglass formulations with epoxy resins are capable of enduring higher temperatures, up to 300°F (149°C) for short periods. However, prolonged exposure to temperatures beyond these limits can lead to resin degradation and loss of material strength. The heat resistance of fiberglass depends not only on the resin but also on the type of reinforcement used, such as fiberglass mat or woven roving. For high-temperature applications, FRP pipes or fiberglass insulation with specific high-temperature resins can be chosen to ensure optimal performance in extreme heat conditions.
Plastic pipes, such as PVC and CPVC, are commonly used for water systems, but their temperature tolerance differs. PVC pipes can typically handle water temperatures up to 140°F (60°C). For higher temperatures, CPVC pipes are a better choice, as they can withstand temperatures up to 200°F (93°C). Plastic pipes like polyethylene (PE) and polypropylene (PP) are not suitable for hot water systems, as they may soften or deform at elevated temperatures. For high-temperature water applications, such as hot water systems or steam lines, FRP pipes or metal pipes are preferred due to their higher heat resistance.
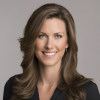
As the editor of GangLong Fiberglass, I have years of experience and in-depth research, focusing on cable tray products, fiberglass solutions, and grille systems. I incorporate years of industry insights and practical experience into every content, committed to promoting the progress of the industry. At GangLong Fiberglass, my commitment is reflected in every product, from innovative cable trays to durable fiberglass solutions and sturdy grille systems. As an authoritative voice in the industry, my goal is to provide valuable information to professionals and businesses and promote forward-looking solutions.