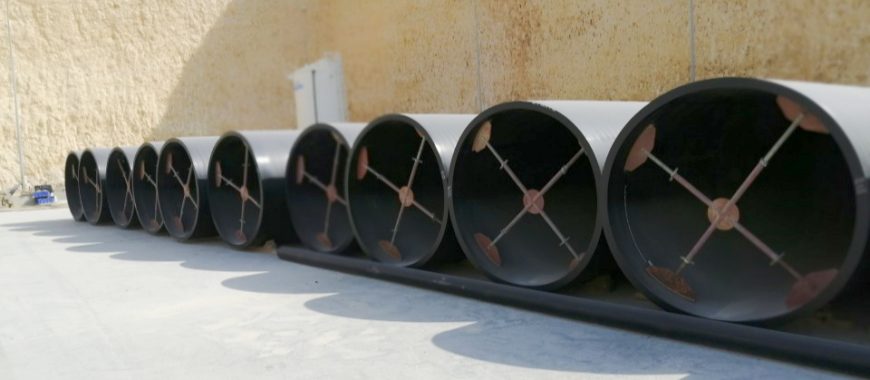
When comparing HDPE vs FRP pipe, it’s essential to understand their key differences in industrial applications. HDPE (High-Density Polyethylene) is flexible, lightweight, and cost-effective, making it ideal for low-pressure applications like water distribution and gas pipelines. On the other hand, FRP (Fiberglass Reinforced Plastic) pipes, such as those produced by GangLong Fiberglass, offer superior strength, corrosion resistance, and high-temperature tolerance, making them better suited for harsh environments such as chemical processing and wastewater treatment. HDPE vs FRP Pipe:HDPE has a much lower strength than FRP that much less suitable material for high strength applications. While HDPE is easier to install, frp pipe provides a longer lifespan and is more reliable under extreme conditions, especially where high pressure and chemical exposure are factors.
HDPE vs FRP Pipe Physical Properties
When comparing HDPE (High-Density Polyethylene) and FRP (Fiberglass Reinforced Plastic) pipes, their physical properties differ significantly. These properties influence their performance, durability, and suitability for various applications. Here’s a detailed comparison of the physical properties of both types of pipes:
Material Composition
- HDPE Pipe: Made from high-density polyethylene, a thermoplastic polymer that is flexible and resistant to impact, abrasion, and chemicals. It is not reinforced with other materials.
- FRP Pipe: Made from a resin matrix (typically polyester, vinyl ester, or epoxy) reinforced with fiberglass. The fiberglass reinforcement gives it high tensile strength and rigidity, as well as resistance to corrosion and chemical attack.
Tensile Strength
- HDPE Pipe:
- Tensile Strength: Approximately 25–40 MPa (megapascals).
- Properties: HDPE pipes are known for their flexibility and impact resistance, but their tensile strength is lower than that of FRP pipes. This makes HDPE pipes more suitable for applications where flexibility and ease of installation are more important than high strength.
- FRP Pipe:
- Tensile Strength: Approximately 90–160 MPa, depending on the type of fiberglass and resin used.
- Properties: FRP pipes are much stronger in terms of tensile strength due to the fiberglass reinforcement. This makes them ideal for high-pressure applications or environments where pipes are subject to significant mechanical stress.
Impact Resistance
- HDPE Pipe:
- Impact Resistance: High.
- Properties: HDPE pipes are known for their excellent impact resistance. This property makes them ideal for installation in environments where pipes might be subject to external forces or where accidental impacts might occur.
- FRP Pipe:
- Impact Resistance: Moderate.
- Properties: FRP pipes have good impact resistance, but they are more brittle than HDPE. In certain conditions, such as extreme temperatures or high-impact situations, FRP pipes can be more prone to cracking or breaking.
UV Resistance
- HDPE Pipe:
- UV Resistance: Moderate.
- Properties: HDPE pipes are susceptible to degradation from UV exposure. Without UV stabilizers, HDPE pipes may become brittle and crack when exposed to sunlight over time. UV-resistant coatings can help extend the life of HDPE pipes in outdoor applications.
- FRP Pipe:
- UV Resistance: High.
- Properties: FRP pipes generally have better resistance to UV radiation, especially when treated with UV-resistant resins. This makes them more suitable for outdoor applications where exposure to sunlight is a concern.
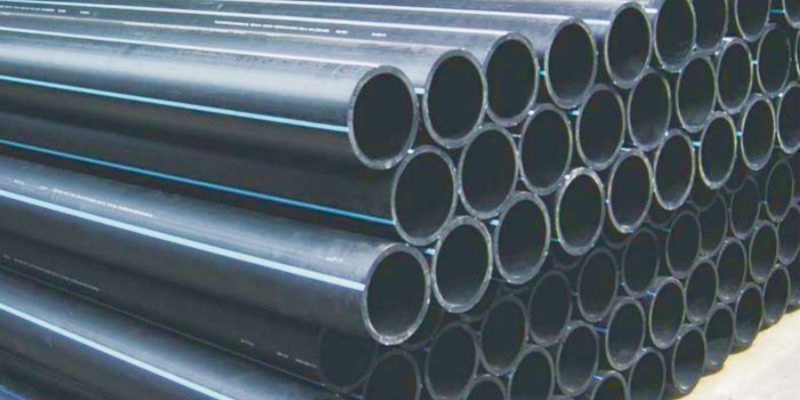
HDPE vs FRP Pipe:Price
When comparing HDPE (High-Density Polyethylene) and FRP (Fiberglass Reinforced Plastic) pipes in terms of price, there are several factors to consider. Generally, the price difference between HDPE and FRP pipes is substantial, and the final cost will depend on various elements such as pipe diameter, material quality, installation requirements, and the specific application.
Cost of HDPE Pipes
- Price Range: HDPE pipes are generally more affordable than FRP pipes.
- Cost per Meter: The price of HDPE pipes can range from $1 to $10 per meter depending on factors like diameter, thickness, and grade. For example:
- Small diameter pipes (e.g., 25mm to 50mm) may cost around $1 to $3 per meter.
- Larger diameter pipes (e.g., 200mm to 500mm) may cost around $5 to $10 per meter.
- Factors Affecting Cost: The cost can vary based on the location (e.g., local suppliers or imported), pipe grade (e.g., HDPE 100 or HDPE 80), and quantity purchased. Bulk purchasing often reduces costs.
- Installation Costs: HDPE pipes are easier and less costly to install due to their flexibility, lightweight nature, and simple jointing methods (heat fusion, electrofusion, or mechanical joints). This reduces overall project costs.
Cost of FRP Pipes
- Price Range: FRP pipes are significantly more expensive than HDPE pipes due to their superior strength, chemical resistance, and corrosion resistance.
- Cost per Meter: FRP pipes generally range from $10 to $50 per meter, depending on the resin type, fiberglass reinforcement, and pipe diameter. For example:
- Small diameter FRP pipes (e.g., 50mm to 100mm) can cost between $10 and $20 per meter.
- Larger diameter FRP pipes (e.g., 300mm to 600mm) can range from $20 to $50 per meter.
- Factors Affecting Cost: The price of FRP pipes can vary based on the type of resin used (polyester, vinyl ester, epoxy), the amount of fiberglass reinforcement, pipe diameter, and pipe length. Custom FRP pipes with specialized coatings or features for high-temperature or high-pressure applications tend to be on the higher end of the price spectrum.
- Installation Costs: Installation of FRP pipes tends to be more expensive than HDPE pipes due to the more complex jointing methods (such as flanged connections or adhesive bonding) and the heavier weight of FRP pipes, which makes them more difficult to handle.
Price Comparison: HDPE vs. FRP
Property | HDPE Pipes | FRP Pipes |
---|---|---|
Price per Meter | $1 to $10 | $10 to $50 |
Material | Thermoplastic, cost-effective, commonly used | Reinforced with fiberglass, more durable but expensive |
Installation Cost | Lower (easier to install) | Higher (more complex handling and installation) |
Life Cycle Cost | Lower initial cost, but lower durability in extreme environments | Higher initial cost, but longer lifespan and superior performance in harsh environments |
Cost Efficiency Considerations
- HDPE Pipes:
- Initial Investment: HDPE pipes offer a lower initial investment. This makes them ideal for general applications like water distribution, sewage, and low-pressure systems.
- Operational and Maintenance Costs: HDPE pipes require less maintenance and are resistant to corrosion, but they may not be as durable as FRP pipes in highly corrosive environments. For applications where the environment is not particularly harsh, HDPE pipes are cost-effective in the long term.
- Lifespan: While HDPE pipes are durable, their lifespan is generally shorter than FRP pipes (typically 50–100 years for HDPE, compared to 75–100+ years for FRP). However, if the application does not involve harsh chemicals or extreme conditions, HDPE pipes offer a good balance of cost and performance.
- FRP Pipes:
- Initial Investment: FRP pipes have a higher upfront cost, but their longer lifespan and superior corrosion and chemical resistance make them cost-effective for applications that demand high durability. These pipes are ideal for industries such as chemical processing, oil and gas, and offshore environments.
- Operational and Maintenance Costs: FRP pipes generally require less maintenance due to their superior resistance to corrosion, UV degradation, and chemical exposure. In extreme environments, they can have a much lower cost of ownership over time compared to HDPE pipes.
- Lifespan: FRP pipes last longer than HDPE pipes, making them the better choice for long-term investments, especially in corrosive or high-temperature environments where HDPE might degrade more quickly.
Factors Influencing Price Fluctuations
- Material Availability: Prices for both HDPE and FRP pipes can fluctuate depending on the cost of raw materials. For example, fluctuations in oil prices (which affect polyethylene production) or fiberglass raw materials can affect the cost of both types of pipes.
- Geographical Location: The cost of both HDPE and FRP pipes can vary based on the location of production and proximity to suppliers. Pipes manufactured locally or regionally may have lower transportation costs.
- Order Volume: Larger orders typically result in lower per-meter costs for both HDPE and FRP pipes. Bulk purchases can help reduce the overall price for both materials.
Ultimately, the decision between HDPE and FRP pipes should consider not only the initial cost but also the long-term operational, maintenance, and durability factors relevant to the specific application.
HDPE vs FRP Pipe: Key Differences in Industrial Applications
The debate surrounding HDPE vs FRP pipe revolves around their differences in material properties, applications, and performance under specific industrial conditions. Both HDPE (High-Density Polyethylene) and FRP (Fiberglass Reinforced Plastic) pipes are widely used in industries such as water treatment, chemical processing, and oil and gas. However, each pipe type offers unique advantages that make them suitable for different environments. By understanding the key differences between HDPE vs FRP pipe, industries can make more informed decisions about which material is best suited for their projects.
What Are the Material Properties of HDPE vs FRP Pipe?
The material composition of HDPE vs FRP pipe significantly affects their performance, durability, and applications.
HDPE Pipes: HDPE pipes are made from high-density polyethylene, a thermoplastic material known for its flexibility and toughness. The material’s elasticity allows HDPE pipes to withstand ground movement and external stress without cracking, making them ideal for environments where flexibility is required. These pipes are particularly effective in areas with seismic activity or unstable soil conditions. HDPE is also known for its impact resistance, meaning it can handle external forces without damage. GangLong Fiberglass offers HDPE pipes that meet industry standards and perform reliably under various conditions.
FRP Pipes: FRP pipes, on the other hand, are made from a combination of fiberglass and resin. The fiberglass gives the pipe strength, while the resin binds the fibers together and provides chemical resistance. This construction gives FRP pipes excellent strength-to-weight ratios, making them incredibly strong while remaining lightweight. FRP pipes are often preferred in environments where chemical resistance, high pressure, and temperature resistance are key concerns. GangLong Fiberglass produces high-quality FRP pipes using specialized resin formulations that enhance performance in industrial settings.
The debate around HDPE vs FRP pipe centers on their material composition, structural performance, and suitability for different industrial environments. Both types of pipes are widely used across industries, but they serve different purposes depending on the specific requirements of the project. HDPE (High-Density Polyethylene) and FRP (Fiberglass Reinforced Plastic) pipes are known for their durability and corrosion resistance, but they offer distinct advantages in various applications, such as water distribution, chemical processing, and wastewater management. Understanding the differences between HDPE vs FRP pipe can help determine the best material for any given project.
The first difference between HDPE vs FRP pipe lies in their material composition. HDPE pipes are made from high-density polyethylene, a thermoplastic polymer known for its flexibility and impact resistance. This material allows HDPE pipes to handle environmental stress and pressure changes well. They are particularly suited for projects that require a high degree of flexibility and resistance to crack propagation.
On the other hand, FRP pipes, including frp pipe piles, are constructed from a composite of fiberglass and resin. The fibers provide strength, while the resin matrix holds them together and contributes to the pipe’s resistance to chemicals, heat, and corrosion. FRP pipes are designed to withstand harsh industrial conditions, offering superior performance in terms of structural strength and longevity. GangLong Fiberglass manufactures FRP pipes with specialized resins to meet a variety of industrial demands, ensuring both reliability and durability.
How about the Corrosion Resistance in HDPE vs FRP Pipe?
Corrosion resistance is one of the key factors to consider when comparing HDPE vs FRP pipe. Both materials are known for their resistance to corrosion, making them ideal for transporting fluids that might otherwise degrade metal pipes. However, the degree of corrosion resistance varies depending on the specific conditions.
HDPE Pipes: HDPE pipes are highly resistant to most types of chemical corrosion. They are particularly effective in applications involving water, wastewater, and chemicals that have a neutral pH. HDPE pipes do not rust or corrode, making them an excellent choice for underground installations or environments where moisture is prevalent.
FRP Pipes: FRP pipes offer exceptional corrosion resistance across a wider range of chemical environments, including highly acidic or alkaline conditions. The specific resin used in FRP pipes determines their resistance to different chemicals, influencing the frp pipe pressure rating. FRP pipes are ideal for transporting highly corrosive fluids such as acids, solvents, and aggressive chemicals, making them a popular choice in industries like chemical processing and oil and gas. GangLong Fiberglass offers FRP pipes with custom resin formulations to match the specific needs of corrosive environments.
Durability and Strength of HDPE vs FRP Pipe
Durability and structural strength are important when selecting between HDPE vs FRP pipe, as the lifespan and maintenance costs of the pipe system can be affected by these factors.
FRP pipes, such as those produced by GangLong Fiberglass, are composite materials composed of a polymer matrix reinforced with fiberglass. The fiberglass reinforcement gives FRP pipes superior mechanical strength, durability, and resistance to chemicals and extreme temperatures. These characteristics make FRP pipes a preferred choice for industries that operate in aggressive environments, such as chemical processing, wastewater treatment, and power generation.
One of the standout features of FRP pipes is their ability to withstand high pressure and temperature conditions. FRP pipes can operate effectively in temperatures up to 150°C (302°F) or higher, depending on the resin type used in their construction. This makes FRP pipes ideal for carrying high-temperature fluids or for use in processes where temperature fluctuations are common.
FRP pipes also have a very high tensile strength, which allows them to handle heavy loads without deforming. Their structural rigidity ensures that they maintain their shape and performance over time, even in high-pressure applications. This makes FRP pipes well-suited for underground installations where soil pressure may be exerted on the pipes over time.
FRP pipes, such as those produced by GangLong Fiberglass, are known for their exceptional strength, durability, and resistance to corrosion. Unlike HDPE, FRP pipes are made from a composite material that consists of a polymer matrix reinforced with fiberglass. This construction makes FRP pipes ideal for harsh industrial environments where chemical resistance, strength, and long-term reliability are critical.
One of the primary advantages of FRP pipes is their ability to handle high temperatures and pressures. FRP pipes can withstand operating temperatures up to 120°C (248°F) or even higher, depending on the resin system used. This makes them a superior choice for applications in chemical processing, wastewater treatment, and industries where pipes are exposed to aggressive chemicals, high pressure, or extreme temperatures.
HDPE Pipes: HDPE pipes are flexible and have a high resistance to impact, which makes them ideal for applications that require pipes to bend or move with shifting ground, such as in seismic zones or under heavy traffic loads.HDPE pipes can absorb impacts and resist cracking, but they may not be as strong in terms of overall pressure resistance compared to FRP pipes in the discussion of frp vs steel pipe.
FRP Pipes: FRP pipes are known for their structural strength and rigidity, making them well-suited for high-pressure applications. FRP pipes have higher tensile strength than HDPE pipes, which allows them to perform well in systems where pressure resistance is essential. Additionally, FRP pipes can handle higher temperatures without losing their structural integrity. GangLong Fiberglass manufactures FRP pipes to meet the high demands of industrial systems, where both strength and heat resistance are required for safe operation.
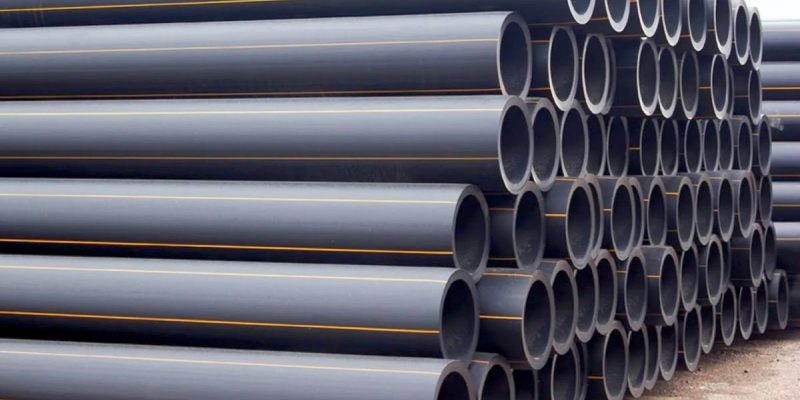
Temperature Limits of HDPE vs FRP Pipe
Another critical difference between HDPE vs FRP pipe is their temperature tolerance. The ability of a pipe to handle high or low temperatures without losing performance is essential in many industrial settings, especially in systems that transport hot or corrosive fluids.
HDPE Pipes: HDPE pipes are generally limited in their temperature tolerance, with maximum operating temperatures typically around 140°F (60°C). In applications where fluids are exposed to higher temperatures, HDPE pipes may become less effective, and their structural integrity could be compromised. This makes them less suitable for applications that require high-temperature resistance.
FRP Pipes: FRP pipes, in contrast, offer superior temperature resistance. Depending on the resin used, FRP pipes can handle temperatures up to 300°F (149°C) or higher, making them a better option for high-temperature applications. They are commonly used in chemical plants and industrial settings where temperature control is critical. GangLong Fiberglass produces high-performance FRP pipes, including Green Thread Fiberglass Pipe, with specialized resins to ensure their reliability in extreme temperature environments.
Installation and Maintenance of HDPE vs FRP Pipe
Ease of installation and the associated maintenance requirements are also important factors when comparing HDPE vs FRP pipe. The differences in how these pipes are installed can impact the overall cost and efficiency of a project.
HDPE Pipes: HDPE pipes are lightweight and flexible, which makes them easier to transport and install, particularly in areas with difficult access. Their flexibility allows them to be fused together using heat, creating strong, leak-proof joints. However, HDPE pipes may require additional support structures in high-pressure or high-temperature environments.
FRP Pipes: FRP pipes are more rigid and typically require a more complex installation process. However, their strength and durability often result in lower long-term maintenance costs. FRP pipes require special fittings and adhesives for proper installation, but once installed, they offer superior performance and a longer service life compared to HDPE pipes. GangLong Fiberglass provides a range of installation services and custom solutions to ensure the proper installation and longevity of FRP pipe systems.
Cost Considerations of HDPE vs FRP Pipe
Cost is always a factor when choosing materials for a piping system. While the initial cost of the pipe is important, long-term operational and maintenance costs should also be considered when evaluating HDPE vs FRP pipe.
HDPE Pipes: HDPE pipes tend to have a lower upfront cost compared to FRP pipes. They are relatively inexpensive to manufacture and install, which makes them a popular choice for projects with budget constraints. However, depending on the application, HDPE pipes may require more frequent maintenance or replacement due to their lower resistance to extreme conditions.
FRP Pipes: While FRP pipes may have a higher initial cost, they offer significant savings in the long run due to their durability, resistance to corrosion, and ability to handle higher pressures and temperatures. The longevity of FRP pipes often translates into lower maintenance costs and fewer replacements over the life of the system, making them a cost-effective option for industries that require high performance and reliability. GangLong Fiberglass offers FRP pipe solutions tailored to both initial budget considerations and long-term operational needs.
What Are the Best Applications for HDPE vs FRP Pipe?
The best choice between HDPE vs FRP pipe depends on the specific requirements of the project and the environment in which the pipes will be used.
HDPE Pipes: HDPE pipes are ideal for applications that require flexibility, lightweight materials, and resistance to impact. They are commonly used in water distribution systems, irrigation projects, and areas with shifting ground or frequent pressure changes. HDPE pipes are also widely used in wastewater systems and certain chemical applications where extreme conditions are not a factor.
FRP Pipes: FRP pipes excel in applications that demand high strength, corrosion resistance, and temperature tolerance. They are well-suited for chemical processing plants, oil and gas refineries, and industrial wastewater systems. FRP pipes are often used in environments where other materials would fail due to corrosion, heat, or pressure, making them the preferred choice for heavy-duty applications. GangLong Fiberglass offers FRP pipe solutions for industries that require the highest levels of performance and durability.
Key Factors Determining FRP Pipe Temperature Limits in Industry
HDPE vs FRP Pipe: Key Considerations for Industrial Applications
When it comes to industrial piping systems, selecting the right material is crucial for ensuring safety, durability, and efficiency. Two of the most common materials used for piping in various industries are HDPE (High-Density Polyethylene) and FRP (Fiberglass Reinforced Plastic). Both materials offer unique advantages, but it is essential to understand the key differences between hdpe vs frp pipe to make an informed decision for your specific project needs.
What is HDPE Pipe and Its Key Characteristics
HDPE is a thermoplastic made from petroleum. Its main advantages lie in its flexibility, impact resistance, and relatively low cost. HDPE pipes are commonly used for applications such as water distribution, gas pipelines, and drainage systems. The material is well-suited for outdoor use, particularly in systems that require trenchless installation techniques like directional drilling or pipe bursting, due to its flexibility.
One of the standout features of HDPE pipes is their ability to withstand low temperatures and their resistance to cracking. This makes them an ideal choice for environments where freezing temperatures may pose a risk to other piping materials. Additionally, HDPE pipes are known for their smooth interior surfaces, which help reduce friction, making them highly efficient for fluid transport.
However, HDPE pipes have their limitations. They are not well-suited for high-temperature environments, as they begin to soften around 120°C (248°F). HDPE pipes also have lower strength compared to FRP pipes, meaning they may not be the best choice for applications requiring high-pressure resistance or long-term structural integrity in demanding conditions.
Material Properties of HDPE vs FRP Pipe
Understanding the material properties of both HDPE and FRP pipes is essential for selecting the right material for your application. The material properties not only affect the performance of the pipes but also influence factors such as installation, maintenance, and overall cost.
Strength and Flexibility
HDPE pipes are known for their flexibility, which allows them to bend and conform to the landscape without breaking. This makes them ideal for applications where ground movement or shifting soil is a concern. However, this flexibility comes at the cost of reduced structural strength. HDPE pipes are not as strong as FRP pipes and may deform under heavy loads or high-pressure conditions.
On the other hand, FRP pipes offer greater structural strength and rigidity. The fiberglass reinforcement provides enhanced mechanical properties, making FRP pipes highly resistant to deformation and breakage. This strength allows FRP pipes to withstand higher pressures and heavy loads, making them suitable for more demanding applications.
Corrosion Resistance
Both HDPE and FRP pipes offer excellent corrosion resistance, but they achieve this through different mechanisms. HDPE pipes are naturally resistant to most chemicals, which makes them a good choice for applications where the pipes are exposed to corrosive substances like acids, alkalis, or organic solvents.
Rigidity
When comparing hdpe vs frp pipe, one of the most noticeable differences is the level of strength and rigidity. HDPE pipes are flexible, which allows them to bend and absorb impacts, but this flexibility comes at the cost of lower strength. HDPE pipes are more likely to deform under high pressure or heavy loads, which can be a disadvantage in certain industrial applications where structural integrity is essential.
FRP pipes, by contrast, are much more rigid and can handle higher mechanical loads without deforming. The fiberglass reinforcement provides additional strength, allowing FRP pipes to withstand higher pressure levels and remain structurally sound even under heavy loads. This makes FRP pipes a better option for environments that demand high strength, such as underground pipelines subjected to soil and traffic loads.
Temperature Resistance
The temperature resistance of pipes is a critical factor for many industrial applications. HDPE pipes can operate in low-temperature environments, but they have limited heat resistance. At temperatures above 60°C (140°F), the material begins to lose strength, and by 120°C (248°F), the pipes may soften and become unusable for high-temperature applications.
FRP pipes are designed to handle much higher temperatures. Depending on the resin system used, FRP pipes can operate at temperatures ranging from 120°C (248°F) to over 200°C (392°F). This makes them ideal for applications where pipes are exposed to hot fluids, steam, or high-temperature industrial processes. The ability of FRP pipes to maintain their structural integrity at high temperatures is one of their key advantages over HDPE.
FRP pipes, however, are specifically designed to resist corrosion in even the harshest environments. The fiberglass reinforcement and resin matrix provide a barrier that prevents chemicals from penetrating the pipe, making FRP pipes highly resistant to aggressive chemicals such as sulfuric acid, hydrochloric acid, and chlorine. This superior corrosion resistance makes FRP pipes the preferred choice in industries like chemical processing, wastewater treatment, and power generation.
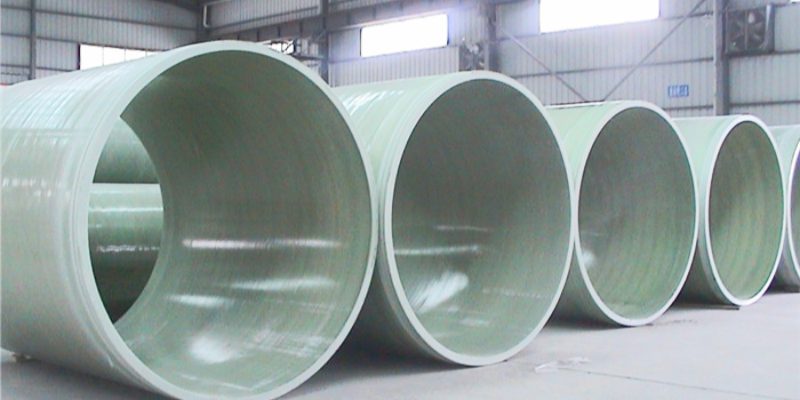
Top Benefits of Using Green Fiberglass Insulation in Homes
HDPE vs FRP Pipe:Design, Lifespan, Density Comparative
When comparing HDPE (High-Density Polyethylene) pipes with FRP (Fiberglass Reinforced Plastic) pipes in terms of design, lifespan, and density, there are several key differences to consider. Here’s a detailed comparison:
1. Design
- HDPE Pipe Design:
- Material: HDPE pipes are made from a thermoplastic polymer (high-density polyethylene), which gives them a smooth surface that reduces friction and enhances flow efficiency. The design is relatively simple, and they are typically produced in a continuous extrusion process.
- Flexibility: HDPE pipes are flexible, which makes them ideal for applications in areas with frequent ground movement or where pipes need to be bent or curved around obstacles. Their flexibility also reduces the need for additional fittings in some cases.
- Jointing: HDPE pipes are typically joined using heat fusion (welding), mechanical joints, or electrofusion. This results in strong, leak-proof joints that are resistant to various environmental factors.
- Applications: HDPE is used in water supply systems, sewerage systems, gas distribution networks, and even in mining applications. Its design is suited for underground installations and for applications where ease of handling and installation are priorities.
- FRP Pipe Design:
- Material: FRP pipes are made by reinforcing a plastic matrix (typically polyester or vinyl ester resin) with fiberglass. This design gives the pipe strength and durability while maintaining its lightweight properties.
- Rigidity: Unlike HDPE, FRP pipes are generally rigid and non-flexible. The strength of the fiberglass reinforcement means that they can withstand higher internal pressures, making them ideal for heavy-duty applications.
- Customizability: FRP pipes can be designed with different layers of reinforcement depending on the application’s requirements. For example, they can be made with a combination of fiberglass layers and resin types to optimize strength, corrosion resistance, or thermal insulation.
- Applications: FRP pipes are commonly used in industries requiring resistance to chemicals, corrosion, and high temperatures, such as chemical processing, oil and gas industries, and offshore applications.
2. Lifespan
- HDPE Pipe Lifespan:
- Durability: HDPE pipes are highly durable and resistant to wear, abrasion, and impact. Under normal conditions, they have an expected lifespan of 50-100 years, depending on environmental conditions and application specifics.
- Corrosion Resistance: HDPE is resistant to corrosion, particularly from acids, bases, and salts. However, exposure to UV radiation and certain chemicals (like some solvents) can degrade the material over time unless stabilizers are added.
- Factors Affecting Lifespan: The lifespan of HDPE pipes can be influenced by factors such as pressure, temperature, and the presence of UV radiation. In environments with high UV exposure, protective coatings or UV-resistant additives are typically required.
- FRP Pipe Lifespan:
- Longer Lifespan: FRP pipes have a longer lifespan than HDPE pipes, often exceeding 75 years in optimal conditions. They are particularly resistant to environmental factors like corrosion, chemical degradation, and UV exposure, which contributes to their extended service life.
- Corrosion Resistance: The fiberglass-reinforced plastic composition of FRP pipes gives them excellent resistance to corrosive substances, including acids, alkalis, salts, and seawater. This makes them ideal for industries where pipes may come into contact with aggressive chemicals or harsh weather conditions.
- Resistant to Microbial Growth: FRP pipes are also resistant to microbial growth, unlike some other materials like metal, which can corrode or degrade in the presence of bacteria or fungi.
3. Density
- HDPE Pipe Density:
- Density: HDPE has a relatively low density, typically around 0.95 to 0.97 g/cm³. This low density contributes to its lightweight nature, making it easier to transport, handle, and install, especially in large-scale projects.
- Lightweight: The low density of HDPE makes it an ideal material for applications where handling weight is a concern, such as in trenchless installations or long-distance pipe runs.
- FRP Pipe Density:
- Density: FRP pipes have a higher density, typically ranging from 1.8 to 2.0 g/cm³, due to the fiberglass reinforcement. Despite being heavier than HDPE pipes, they are still much lighter than metal pipes.
- Strength-to-Weight Ratio: While the density is higher than HDPE, FRP pipes have a superior strength-to-weight ratio, meaning they offer greater strength without a significant increase in weight. This makes them ideal for applications where high pressure and strength are needed, but weight is still a consideration.
- Handling Considerations: The higher density of FRP pipes can make them slightly more difficult to handle and transport compared to HDPE pipes, but they still offer ease of handling compared to metal alternatives.
Characteristic | HDPE Pipes | FRP Pipes |
---|---|---|
Design | Flexible, simple, suitable for underground installations | Rigid, customizable, ideal for high-pressure or corrosive applications |
Lifespan | 50-100 years (with UV exposure and chemical degradation risk) | 75+ years (resistant to UV, corrosion, and chemical degradation) |
Density | Light, 0.95–0.97 g/cm³, easier to handle and install | Heavier, 1.8–2.0 g/cm³, but offers superior strength-to-weight ratio |
- HDPE pipes are best suited for applications where flexibility, ease of handling, and cost-effectiveness are important. They are ideal for water supply, gas distribution, and other general piping needs where the environment is not overly harsh or corrosive.
- FRP pipes are more appropriate for demanding applications in harsh environments, such as chemical processing, oil and gas, and offshore industries. Their superior strength, corrosion resistance, and longevity make them the ideal choice when durability and resistance to extreme conditions are prioritized.
Both materials have distinct advantages, and the choice between HDPE and FRP pipes depends largely on the specific needs of the project, including environmental conditions, pressure requirements, and lifespan expectations.
Key Fiberglass Insulation Manufacturers Leading the Market
FAQs about Hdpe vs Frp Pipe
HDPE (High-Density Polyethylene) and PPR (Polypropylene Random Copolymer) pipes are both popular choices for water distribution and plumbing applications, but each has its strengths and limitations. HDPE pipes are flexible, impact-resistant, and known for their chemical resistance, making them ideal for outdoor installations, water mains, and systems where the pipes may be exposed to shifting soil or harsh environmental conditions. HDPE pipes are also lightweight, easy to transport, and suitable for trenchless installations due to their flexibility.
PPR pipes, on the other hand, are highly resistant to scaling and corrosion, making them ideal for hot and cold water applications in indoor plumbing systems. PPR pipes have a higher resistance to heat compared to HDPE, which makes them suitable for carrying hot water and being used in heating systems. They are also less prone to chemical degradation and can withstand higher pressures than HDPE, making them a good choice for residential and commercial water systems.
In general, HDPE is better for external, flexible applications like water mains and gas distribution, while PPR is a better choice for indoor plumbing and heating systems where resistance to hot water and chemical stability are more important.
HDPE pipes are generally not recommended for fire protection systems. While HDPE offers excellent resistance to many chemicals and has a high degree of flexibility, it has relatively low heat resistance. HDPE begins to soften at temperatures around 120°C (248°F) and melts at higher temperatures, which makes it unsuitable for use in fire protection systems where pipes must remain functional during and after exposure to fire.
Fire protection systems require materials that can withstand high heat and maintain structural integrity in the event of a fire. HDPE is more suited for water distribution, gas piping, and drainage systems where heat exposure is minimal. For fire protection systems, materials such as steel, ductile iron, or copper are typically used due to their higher melting points and durability in high-temperature environments. If corrosion resistance is needed in fire protection systems, specialized materials such as FRP (Fiberglass Reinforced Plastic) or other fire-resistant composites may be considered.
While HDPE pipes are highly popular due to their flexibility, chemical resistance, and low cost, they also come with some disadvantages that need to be considered depending on the application. One of the primary drawbacks of HDPE pipes is their lower pressure resistance compared to materials like steel or FRP. HDPE pipes may deform under high pressure or in extreme temperature conditions, limiting their use in high-pressure or high-temperature environments. They also have lower tensile strength, which makes them less suitable for situations requiring high structural integrity.
Another disadvantage is that HDPE is sensitive to UV light. Prolonged exposure to sunlight can cause the material to degrade over time, resulting in a reduced lifespan if not properly protected or buried. Additionally, while HDPE pipes are relatively easy to install, they require special fusion welding techniques to join sections, which may involve additional training or equipment. HDPE pipes can also expand and contract significantly with temperature changes, which may lead to issues with joint integrity over time if not installed correctly.
Fiberglass Reinforced Plastic (FRP) pipes have some disadvantages, such as higher initial cost compared to other materials like HDPE. They are also more brittle and prone to cracking under high impact, especially when subjected to mechanical stress or extreme temperatures. While FRP pipes offer excellent corrosion resistance, they can be vulnerable to UV degradation over time unless treated with UV stabilizers. Additionally, installation requires more specialized techniques and labor, which can increase the overall cost. In some applications, the weight of larger FRP pipes may also pose handling and installation challenges.
Yes, FRP pipes can be used for fire protection systems, but they must be selected carefully. Standard FRP pipes are typically not fire-resistant unless specifically engineered to meet fire resistance standards. Specialized fire-resistant coatings or resins are often applied to enhance their fire-resistant properties. FRP pipes used in fire protection should meet regulatory standards like UL (Underwriters Laboratories) or FM Global approval. They can be used in some applications like water mist systems, but the choice of resin and construction must ensure that the pipe will not fail in a high-temperature environment.
HDPE (High-Density Polyethylene) and GRP (Glass Reinforced Plastic) pipes differ in material composition and applications. HDPE is a flexible thermoplastic, lightweight, and resistant to many chemicals and abrasion, making it suitable for water, gas, and sewage systems. It is cost-effective, with easy installation methods. On the other hand, GRP pipes are rigid, made from a resin matrix reinforced with fiberglass, offering superior strength, corrosion resistance, and durability in harsh environments. GRP pipes are often used in industries like chemical processing, water treatment, and offshore applications where high pressure and chemical resistance are required.
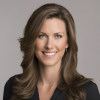
As the editor of GangLong Fiberglass, I have years of experience and in-depth research, focusing on cable tray products, fiberglass solutions, and grille systems. I incorporate years of industry insights and practical experience into every content, committed to promoting the progress of the industry. At GangLong Fiberglass, my commitment is reflected in every product, from innovative cable trays to durable fiberglass solutions and sturdy grille systems. As an authoritative voice in the industry, my goal is to provide valuable information to professionals and businesses and promote forward-looking solutions.