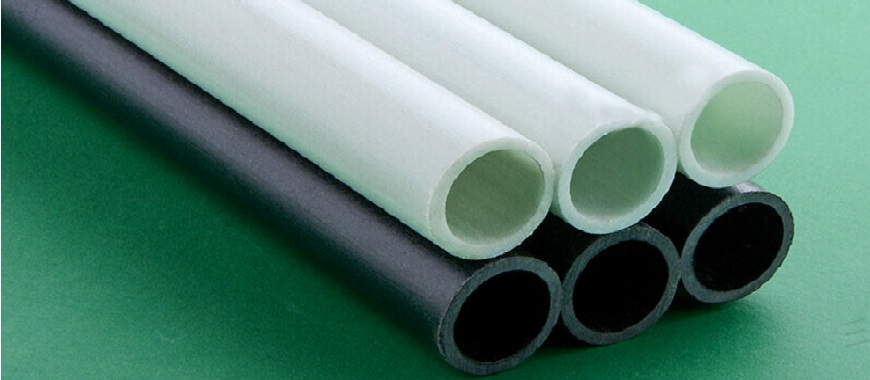
Large diameter fiberglass tubes are increasingly essential in both industrial and commercial applications. Their demand is growing due to their superior performance in harsh environments. Industries such as water treatment, chemical processing, and marine engineering highly value these tubes for their durability and reliability. The unique fiberglass tube properties, such as resistance to corrosion and excellent strength-to-weight ratio, make them the preferred choice over traditional materials. They are resistant to corrosion, ensuring longevity in environments exposed to moisture or chemicals. Additionally, these tubes are lightweight, making transportation and installation easier, while maintaining impressive strength for structural integrity. For industries requiring custom solutions, large diameter fiberglass tubes provide flexibility in design and performance, further enhancing their widespread use. Large diameter fiberglass tubes, available in sizes like 150mm to 200mm, offer high strength, corrosion resistance, and easy maintenance for various projects.
Large Diameter Fiberglass Tube Price: Key Factors and Cost Comparison
Understanding the price of large diameter fiberglass tubes requires examining several key factors that influence their cost. These tubes are valued for their performance, but the final price can vary based on material composition, manufacturing processes, customization, and compliance with industry standards. Let’s explore each of these aspects to gain a clearer picture of the cost structure.
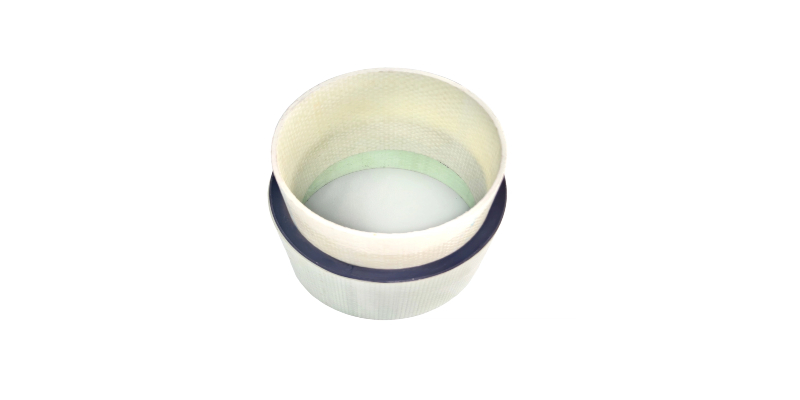
Material Composition
One of the most important factors affecting the price of large diameter fiberglass tubes is the type of materials used. These tubes are typically made from a combination of resins and reinforcement materials, such as fiberglass. The choice of resin, such as polyester or vinyl ester, can significantly impact the final cost. Higher-quality resins offer better corrosion resistance and durability but are often more expensive. Additionally, the amount and type of reinforcement fibers, which provide strength, also play a crucial role in determining the price.
Manufacturing Process
The method used to manufacture large diameter fiberglass tubes is another critical factor. Two common processes are filament winding and contact molding. Filament winding involves winding continuous fibers around a mandrel, creating strong, lightweight tubes with precise wall thickness. This process is often more cost-effective for producing high volumes. In contrast, contact molding uses hand lay-up techniques and typically results in a thicker wall with higher resin content. Though contact molding can be more expensive, it is ideal for custom or small-batch orders where high strength is needed.
Customization Options
Large diameter fiberglass tubes can be customized in terms of size, shape, and fittings to meet specific project requirements. Customization increases the overall price due to additional labor and specialized materials. However, many industries require specific tube dimensions, flanges, or couplings, which must be considered during production. While standard tubes may offer lower prices, customized solutions provide added value for unique applications, ensuring the tubes meet exact performance criteria.
Industry Standards and Certifications
Compliance with industry standards and certifications also plays a role in determining the price of large diameter fiberglass tubes. These standards, such as ASTM or AWWA certifications, guarantee that the tubes meet specific performance and safety requirements. While tubes adhering to these standards may cost more, they ensure reliability and longevity in demanding environments, making them a smart long-term investment.
Price Range and Cost-Effectiveness
The price of large diameter fiberglass tubes can vary widely depending on the factors mentioned above. Small diameter fiberglass tubes, such as those with diameters of 6 to 12 inches, may be more affordable, while larger tubes, like those exceeding 72 inches in diameter, will be more expensive. However, innovations in small diameter fiberglass tube production have led to more efficient manufacturing processes, making these tubes even more cost-effective. Small diameter fiberglass tubes are often a more budget-friendly option, making them an attractive choice for projects with cost constraints. Custom orders and higher-quality materials will also drive up costs. Despite the higher initial investment, fiberglass tubes are more cost-effective over time compared to traditional materials like steel or PVC. They offer low maintenance, long lifespan, and resistance to corrosion, reducing repair and replacement costs.
Flexible Fiberglass Tube: Lightweight and Durable Options
Finding Large Diameter Fiberglass Tubes Near You: A Complete Guide
When searching for large diameter fiberglass tubes, it’s important to know where to look and what factors to consider. Whether you’re looking for a fiberglass tube near me or sourcing from online vendors, understanding your options can save time and money. Let’s explore how you can find the right large diameter fiberglass tube, with a special focus on availability, popular brands like GangLong Fiberglass, and the advantages of local purchasing versus distant suppliers.
Sourcing Large Diameter Fiberglass Tubes Locally and Online
One of the first things to consider when looking for a large diameter fiberglass tube is whether you want to purchase it locally or from an online vendor. Local suppliers may offer faster delivery times and more personalized customer service, making them ideal for urgent projects or when specific advice is needed. Many industrial hubs feature specialized suppliers that stock a range of fiberglass tubes in various sizes.
If local options are limited, online vendors can provide access to a wider selection. Websites from established manufacturers like GangLong Fiberglass make it easy to browse available products, specifications, and pricing. Some online platforms also offer customization options, allowing you to order tubes tailored to your specific requirements.
Availability in Industrial Hubs and Specialized Suppliers
Large diameter fiberglass tubes are widely available in major industrial hubs, where infrastructure projects and industrial applications drive demand. These hubs often have specialized suppliers that can meet the needs of local industries. For instance, regions with a strong presence in water treatment, marine engineering, or chemical processing are likely to have a greater number of suppliers offering these tubes.
Well-known brands like GangLong Fiberglass have established networks of distributors and retailers that supply large diameter fiberglass tubes across various regions. This ensures that even if you’re not located in an industrial hub, you can still source high-quality tubes without difficulty.
Popular Manufacturers and Distributors of Large Diameter Fiberglass Tubes
At GangLong Fiberglass, we take pride in our expertise in producing durable, high-performance fiberglass tubes. Our products are widely used across various industries, including wastewater treatment, power plants, and marine applications. As the manufacturer, we offer a broad range of large diameter fiberglass tubes, ensuring that we can meet the specific size and specifications required for your project. We are committed to providing high-quality, reliable solutions for all your fiberglass tube needs.
Local vs. Distant Suppliers: What’s Best?
When deciding between local and distant suppliers, consider the trade-offs.
- Purchasing large diameter fiberglass tubes locally offers several benefits:
- Faster delivery times: You can receive your order quickly, reducing project delays.
- Personalized customer service: Local suppliers may provide more direct communication and faster responses to inquiries.
- Easy returns and exchanges: Dealing with nearby suppliers makes logistics simpler if issues arise.
On the other hand, buying from distant suppliers or online vendors like GangLong Fiberglass can offer a wider variety of products and potential cost savings:
- Wider selection: Distant suppliers may offer a larger inventory and customization options.
- Bulk discounts: If you need a large quantity of tubes, buying from online suppliers can often lead to significant savings.
Thick Wall Fiberglass Tube: A Comprehensive Applications
Large Diameter Fiberglass Tubes for Sale: Sizes, Specifications, and Applications
When it comes to purchasing large diameter fiberglass tubes, understanding the available sizes and specifications is key. These tubes are designed for a variety of industrial applications, each requiring specific dimensions and features to meet performance standards. Below, we explore the common sizes on the market, their applications, and how to choose the right tube for your project.
Common Sizes and Specifications of Large Diameter Fiberglass Tubes
Large diameter fiberglass tubes come in a range of sizes to accommodate different project requirements. Standard diameters for these tubes typically range from 6 inches to 162 inches, providing flexibility for both small and large-scale projects. The most common lengths available are 20 feet and 40 feet, though custom lengths and diameters can be requested for specialized applications. Many manufacturers, including those producing high-quality large diameter fiberglass tubes, also offer custom options, allowing clients to specify particular wall thicknesses, shapes, or additional fittings to meet specific needs.
Custom Sizes and Features Available
For projects requiring non-standard sizes, custom large diameter fiberglass tubes are often the best solution. These custom orders can include unique diameter measurements, special coatings for enhanced durability, and the integration of specific features like couplings, flanges, or reinforced sections. Customization ensures that the tubes perform optimally in their intended application, providing enhanced longevity and structural integrity.
Applications of Large Diameter Fiberglass Tubes
Large diameter fiberglass tubes are widely used in industries where durability, corrosion resistance, and lightweight materials are essential.
Below are some of the most common applications
- Wastewater Treatment Plants: Fiberglass tubes are resistant to chemical corrosion and moisture, making them ideal for water treatment facilities.
- Industrial Pipelines: Desalination plants and power utilities rely on these tubes for the safe and efficient transport of water, steam, and chemicals.
- Marine Applications: Dock and pier construction projects benefit from the non-corrosive properties of fiberglass, especially in saltwater environments.
These industries value the high strength-to-weight ratio and long service life of large diameter fiberglass tubes, which perform reliably even in harsh conditions.
Best Practices for Evaluating and Selecting Fiberglass Tubes
When selecting large diameter fiberglass tubes for a specific project, it’s important to evaluate several factors:
- Application Requirements: Consider the environmental conditions the tube will face, such as exposure to chemicals, water, or extreme temperatures.
- Size and Wall Thickness: Ensure that the chosen diameter and wall thickness match the structural demands of the project.
- Customization Needs: Determine whether standard tubes are sufficient, or if custom features like specialized fittings are required.
By carefully evaluating these factors, you can ensure that your large diameter fiberglass tube selection provides optimal performance for your specific application.
How to Choose the Right Tapered Fiberglass Tube Size
Support and Purchasing Assistance for Large Diameter Fiberglass Tubes
When purchasing large diameter fiberglass tubes, having access to expert support can make the process much smoother and more efficient. Professional assistance is available from sales and engineering teams to guide you through the selection and purchasing process, ensuring that the products meet your specific requirements. Whether you are dealing with a complex installation or need customized solutions, the right support can help avoid potential challenges.
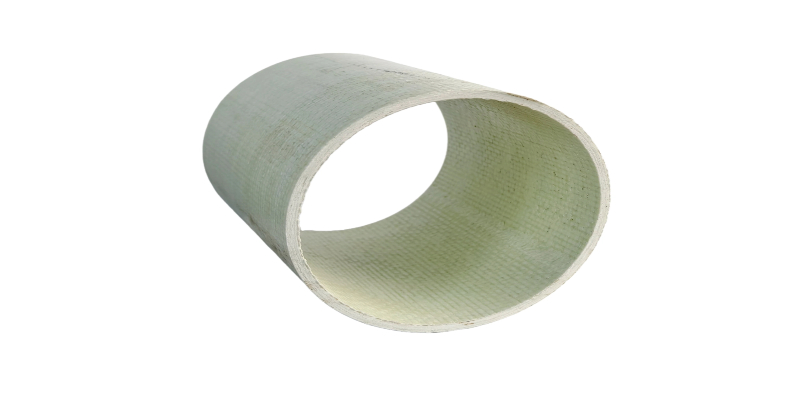
Professional Assistance for Large Diameter Fiberglass Tubes
Sales and engineering teams are ready to provide detailed guidance on large diameter fiberglass tubes. They can help identify the correct tube size, wall thickness, and any necessary fittings for your project. These professionals have extensive knowledge of industry standards and can ensure that the selected tubes are suited to your application, whether it’s for water treatment, industrial pipelines, or chemical processing plants.
Their expertise extends to helping with complex projects where standard options may not meet your needs. In these cases, custom large diameter fiberglass tubes can be designed to fit your specific requirements. Customization can include unique sizes, shapes, or added features like special flanges or couplings.
Custom Solutions, Pricing, and Availability
For those needing more than standard solutions, sales teams can offer custom options tailored to your project. You are encouraged to inquire about the pricing and availability of large diameter fiberglass tubes based on your specific requirements. Custom solutions may involve different tube diameters, lengths, and reinforcement levels, all of which affect pricing. The sales teams can also provide insights on bulk pricing or special discounts for large orders, ensuring that your purchase is cost-effective.
Additionally, obtaining detailed project timelines and delivery estimates from the team can help in planning your project efficiently. Knowing the availability of specific tube sizes or custom designs will allow for better coordination of project schedules and installation.
Additional Resources for Detailed Planning
For more detailed planning, many manufacturers and distributors offer valuable resources such as technical bulletins, case studies, and product specifications. These resources can provide a deeper understanding of the technical capabilities of large diameter fiberglass tubes, helping you make more informed decisions. Technical bulletins can highlight material properties, performance standards, and installation guidelines, ensuring your project is planned correctly from start to finish.
Case studies from past projects can serve as a helpful reference, showcasing how large diameter fiberglass tubes have been successfully used in various industries. These examples can provide insight into best practices and innovative applications, helping you visualize how the tubes can be integrated into your own project.
Why Choose Large Diameter Fiberglass Tubes: Benefits and Next Steps
Large diameter fiberglass tubes have become a preferred solution across a wide range of industries, from wastewater treatment and industrial pipelines to marine applications. Their combination of corrosion resistance, lightweight design, and high strength makes them an ideal choice for both above ground and buried installations. These tubes offer superior longevity and durability compared to traditional materials, reducing maintenance costs and ensuring reliable performance in harsh environments.
For industries requiring custom designs, large diameter fiberglass tubes offer flexibility, with various sizes, shapes, and fittings available to meet specific project needs. Whether your project involves chemical processing, water systems, or marine engineering, these tubes provide a high-performance solution that can be tailored to your requirements.
Contact Suppliers for Quotes and Custom Solutions
If you’re considering large diameter fiberglass tubes for your next project, now is the time to reach out to trusted suppliers. They can provide detailed quotes, availability, and guidance on custom solutions that fit your exact specifications. Whether you need advice on materials, sizes, or installation processes, professional sales and engineering teams are ready to assist.
For more information on available products, custom options, or to request a quote, please contact your supplier today. Be sure to explore related products and services, as well as FAQs and support resources that can provide further assistance during the planning and purchasing process. Reliable customer support is always available to answer questions and ensure your project runs smoothly.
By choosing large diameter fiberglass tubes, you invest in a solution that offers unparalleled durability and performance, making them a smart choice for your next project.
Key Considerations When Purchasing Large Diameter Fiberglass Tube
When purchasing large diameter fiberglass tubes, it’s essential to consider more than just the diameter. Several other factors significantly impact the performance, durability, and suitability of the tubes for your specific application. These include material properties, pressure ratings, strength, environmental resistance, and customization options. By understanding these aspects, you can make a more informed decision that aligns with the needs of your project. Below are key features to consider when purchasing large diameter fiberglass tubes.
Material Composition and Resin Type
The material composition of a fiberglass tube is crucial because it determines the tube’s resistance to environmental factors, as well as its strength and durability. The resin type used in the manufacturing process plays a major role in the tube’s ability to resist corrosion, high temperatures, and chemical degradation.
Fiberglass tubes are typically made using high-quality, corrosion-resistant resins such as epoxy, polyester, or vinyl ester. The resin choice affects factors like the tube’s overall longevity and its ability to handle specific environmental conditions. For instance, epoxy resins provide better resistance to chemicals, while polyester resins are more suitable for general-purpose applications. It’s important to choose a resin that aligns with the operating conditions of your system.
Pressure and Temperature Ratings
Understanding the pressure and temperature ratings of large diameter fiberglass tubes is vital for ensuring that the tubes will perform under the specific conditions of your project. Fiberglass tubes are engineered to handle various pressure levels, but not all tubes are suitable for high-pressure systems.
Before purchasing, you should evaluate the operating pressure and temperature range of the system where the fiberglass tubes will be installed. This will help ensure that the tubes can withstand the required stress without cracking, deformation, or failure. High-quality fiberglass tubes typically have pressure ratings that can range from standard to high-pressure thresholds, and temperature ratings are critical in systems involving steam, hot water, or extreme cold.
Strength and Load-Bearing Capacity
The strength of a large diameter fiberglass tube is another key consideration, especially when the tube will be subjected to heavy loads or mechanical stress. Fiberglass tubes are known for their high strength-to-weight ratio, but the specific strength can vary depending on the manufacturing process, resin type, and fiber content.
For applications that require tubes to bear substantial loads, such as construction, piping systems, or transportation of heavy fluids, it’s crucial to choose a tube with appropriate tensile strength and impact resistance. Fiber-wound fiberglass tubes are particularly well-suited for these demanding applications, as they offer superior strength while maintaining lightweight properties.
Corrosion Resistance and Environmental Compatibility
One of the most significant benefits of large diameter fiberglass tubes is their resistance to corrosion. Unlike metal pipes, fiberglass tubes are not susceptible to rust or chemical degradation, making them ideal for industries like chemical processing, water treatment, and oil and gas.
When purchasing fiberglass tubes, it is important to ensure that the tubes are compatible with the specific chemicals or environmental conditions they will be exposed to. For example, fiberglass tubes used in wastewater treatment may need enhanced chemical resistance, while those exposed to saltwater in marine environments should have additional protection against corrosion from chloride.
Customization and Fabrication Options
Finally, many projects require fiberglass tubes to be customized to fit specific design parameters. Customization options include varying lengths, shapes (round or square), wall thickness, and diameter sizes. For large diameter fiberglass tubes, customization is often necessary to ensure that the pipes meet the precise requirements of a project.
When purchasing large diameter fiberglass tubes, check whether the supplier offers custom fabrication services that can tailor the tubes to your project’s specifications. Custom lengths and fittings are particularly important for large-scale industrial applications, ensuring that the tubes integrate seamlessly with existing infrastructure.
When purchasing large diameter fiberglass tubes, it’s essential to consider factors such as material composition, pressure and temperature ratings, strength, environmental resistance, and customization options. These features, along with the diameter, will determine the tube’s overall performance and suitability for your specific needs.
Advantages and Disadvantages of Large Diameter Fiberglass Tube Compared to Other Sizes
Large-diameter fiberglass tubes play a crucial role in various industries, including construction, infrastructure, and industrial fluid transport. Compared to smaller-diameter fiberglass tubes, they offer unique benefits such as increased load-bearing capacity, efficient material transport, and structural stability. However, they also come with specific challenges, including higher costs, complex installation, and transportation difficulties. To better understand the strengths and weaknesses of large-diameter fiberglass tubes relative to smaller sizes, we will analyze them from multiple perspectives, including structural performance, cost-effectiveness, installation and transportation, application range, and maintenance requirements.
Structural Performance and Load-Bearing Capacity
One of the most significant advantages of large-diameter fiberglass tubes is their ability to handle higher loads and provide greater structural stability. Their wider cross-sectional area allows them to withstand higher internal and external pressures, making them ideal for applications that require durability and resilience.
Advantages:
- Superior strength-to-weight ratio, allowing them to support heavy loads without excessive material weight.
- Increased resistance to bending and deformation, making them suitable for structural applications like bridge supports and large-scale piping systems.
- Enhanced ability to handle high-pressure fluid transport compared to smaller tubes.
Disadvantages:
- More material is required for manufacturing, leading to a heavier overall structure, which can impact handling and mobility.
- In some cases, the stiffness of large-diameter tubes can reduce flexibility, making them less adaptable to certain dynamic applications.
Cost-Effectiveness and Material Efficiency
While large-diameter fiberglass tubes offer excellent performance, they also come at a higher cost. The choice between different tube sizes often depends on the balance between cost-effectiveness and material efficiency.
Advantages:
- In applications requiring large fluid volumes or high-strength structures, fewer large-diameter tubes may be more efficient than using multiple smaller tubes.
- Reduced need for multiple connection points, which can lower long-term maintenance costs.
- High durability leads to longer service life, making them a worthwhile investment in large-scale infrastructure projects.
Disadvantages:
- Higher initial material and manufacturing costs compared to smaller tubes.
- More expensive to replace or repair due to their size and specialized production requirements.
Installation and Transportation Challenges
The larger the tube, the more challenging it is to handle, transport, and install. While smaller tubes are easier to maneuver, large-diameter fiberglass tubes require specialized logistics and equipment.
Advantages:
- Fewer connections and joints reduce the complexity of multi-section installations, improving system integrity.
- Suitable for underground and long-distance pipelines, reducing overall labor requirements in large projects.
Disadvantages:
- Difficulties in transportation due to their size, requiring larger vehicles and specialized handling equipment.
- Heavier weight can lead to higher installation costs, requiring cranes and additional labor.
- More space is needed for storage, which can be a logistical challenge in some environments.
Application Range and Industry Suitability
Large-diameter fiberglass tubes are more suited to specific applications where smaller tubes may not be practical. However, their use depends on industry requirements and operational constraints.
Advantages:
- Ideal for high-volume fluid transport in industries such as oil and gas, wastewater treatment, and chemical processing.
- Used in construction for support columns, wind turbine structures, and bridge reinforcements.
- Offers excellent resistance to environmental factors like corrosion, making them suitable for marine and offshore applications.
Disadvantages:
- Limited versatility compared to smaller tubes, which can be used in more compact or flexible applications.
- May not be necessary for low-capacity or lightweight applications where smaller tubes would suffice.
Maintenance and Long-Term Durability
Fiberglass tubes, regardless of size, require periodic inspection and maintenance. However, larger diameters come with both benefits and challenges in this regard.
Advantages:
- Large-diameter tubes tend to have thicker walls, making them more resistant to external damage and environmental wear.
- They typically require fewer joints, reducing the likelihood of leaks and maintenance points.
- Corrosion-resistant properties ensure a long lifespan, especially in harsh environments.
Disadvantages:
- Inspection and repair can be more difficult due to the size and accessibility constraints.
- Specialized maintenance equipment may be required, increasing operational costs over time.
Large-diameter fiberglass tubes offer significant advantages in structural strength, fluid transport, and durability, making them essential for large-scale industrial and construction applications. However, they also present challenges in terms of cost, installation complexity, and transportation logistics. When selecting the appropriate tube size, industries must weigh the benefits of increased capacity and strength against the potential drawbacks of higher expenses and handling difficulties. By understanding these trade-offs, businesses can make informed decisions to maximize efficiency and cost-effectiveness in their projects.
Key Features of Large Diameter Fiberglass Tube
Large diameter fiberglass tubes offer an array of features that make them highly suitable for a wide range of industrial and construction applications. These tubes are designed to meet the demands of heavy-duty projects while ensuring efficiency, durability, and ease of maintenance. The key features include corrosion resistance, non-conductivity, non-magnetism, lightweight construction, high strength, dimensional stability, and low maintenance costs. Understanding these attributes will help you select the right fiberglass tube for your needs, ensuring optimal performance and long-term reliability. Below are the primary features of large diameter fiberglass tubes.

Corrosion-Resistant Properties
One of the standout features of large diameter fiberglass tubes is their exceptional resistance to corrosion. Unlike traditional metal pipes, which are prone to rusting and deterioration when exposed to moisture or chemicals, fiberglass tubes remain unaffected by these elements. This corrosion resistance is particularly valuable in environments where the pipes come into contact with water, chemicals, or saline solutions, such as in water treatment facilities, chemical plants, or marine environments.
The corrosion resistance of fiberglass tubes ensures that they maintain their structural integrity over time, even when exposed to harsh environmental conditions. This reduces the need for frequent replacements or repairs, making them a cost-effective option for industries that require long-lasting, reliable piping systems.
Non-Conductive Properties
Large diameter fiberglass tubes are non-conductive, making them an ideal choice for applications where electrical conductivity must be avoided. This feature is especially important in industries that work with electrical systems, high-voltage lines, or sensitive equipment. Fiberglass tubes are not susceptible to electrical interference or short circuits, ensuring the safety and stability of the overall system.
Being non-conductive also makes fiberglass tubes an excellent choice for systems that transport sensitive materials or fluids that may be affected by electrical currents. Their ability to provide electrical isolation adds an extra layer of security in environments like power plants, manufacturing facilities, and laboratories.
Non-Magnetic Features
Another key advantage of large diameter fiberglass tubes is that they are non-magnetic. This property is critical in industries where magnetic fields must be kept at a minimum, such as in the aerospace, electronics, and medical sectors. Magnetic materials can interfere with sensitive equipment, processes, or measurements, so the use of non-magnetic fiberglass pipes ensures that there are no adverse effects on nearby machinery or systems.
The non-magnetic nature of fiberglass tubes makes them a reliable and safe option for environments that require precise and interference-free operations, particularly where strong magnetic fields may be present.
Lightweight Construction
Large diameter fiberglass tubes are significantly lighter than traditional metal pipes, which makes them easier to handle, transport, and install. The lightweight nature of fiberglass contributes to reduced transportation costs and labor during installation. Additionally, the lightweight characteristic reduces the overall strain on supporting structures, making the tubes an excellent choice for large-scale projects, such as infrastructure development and large industrial systems.
This ease of handling is particularly beneficial when working with long lengths of pipe, reducing the time and resources required for installation. The reduced weight does not compromise the tube’s strength, making fiberglass a versatile and practical option for various applications.
High Strength and Durability
Despite being lightweight, large diameter fiberglass tubes are renowned for their high strength and durability. The fiber-reinforced structure of fiberglass provides superior tensile strength, making it ideal for heavy-duty applications that involve high pressure, temperature fluctuations, or mechanical stress. Fiberglass pipes can withstand extreme forces without cracking or deforming, ensuring that they perform reliably over time.
The high strength of fiberglass tubes also means they are capable of withstanding impacts, making them suitable for use in environments where accidental damage could occur. Their durability extends the service life of the pipes, reducing the frequency of repairs and replacements.
Stable Dimensions
Large diameter fiberglass tubes are dimensionally stable, meaning their size and shape remain consistent even under varying environmental conditions. This stability ensures that the pipes maintain their form and fit over time, which is crucial for long-term installations. Changes in temperature, pressure, or humidity often cause other materials, such as metal or plastic pipes, to expand or contract, leading to issues with leaks, misalignments, or failure. However, fiberglass tubes resist such dimensional changes, ensuring secure, reliable connections and minimizing the need for adjustments.
The dimensional stability of fiberglass tubes allows for precise installations and the ability to maintain performance over many years, even in fluctuating conditions.
Low Maintenance Costs
Due to their resistance to corrosion, strength, and durability, large diameter fiberglass tubes require minimal maintenance throughout their service life. The lack of corrosion and the stability of the material reduce the risk of leaks, cracks, or other failures, meaning fewer repairs are needed over time. Additionally, fiberglass does not require regular treatments or inspections like metal pipes do, saving on labor and repair costs.
The long-lasting nature of fiberglass pipes means that, despite their initial cost, they are often more cost-effective in the long run compared to other materials that may require frequent maintenance or replacement. This low-maintenance feature makes fiberglass an excellent choice for industries looking to reduce overall operational costs.
Large diameter fiberglass tubes offer a range of features that make them ideal for heavy-duty and long-term applications. Their corrosion resistance, non-conductivity, non-magnetic properties, lightweight construction, high strength, dimensional stability, and low maintenance costs combine to provide a durable, cost-effective solution for a variety of industries.
How to Cut Large Diameter Fiberglass Tube into Suitable Lengths
Cutting a large diameter fiberglass tube into precise lengths requires careful planning, the right tools, and proper safety measures. Unlike cutting traditional materials such as metal or PVC, fiberglass requires special handling to prevent splintering, ensure clean edges, and maintain structural integrity. The process involves selecting the appropriate cutting tools, following specific cutting techniques, and implementing safety measures to protect both the worker and the material. Additionally, post-cut finishing and surface treatment are crucial to achieving a smooth and reliable final product. Below, we will explore the process in detail through different aspects, including tool selection, cutting techniques, safety precautions, and post-cut finishing.
Selecting the Right Cutting Tools
Choosing the appropriate cutting tool is essential for achieving a clean and precise cut without damaging the fiberglass tube. Since fiberglass is a composite material made of glass fibers and resin, traditional cutting tools may not be effective and could result in frayed edges or excessive dust production.
- Diamond Blade Saw – Ideal for high-precision cuts, a diamond-tipped blade minimizes fiber fraying and delivers a smooth edge. It is commonly used for industrial applications.
- Carbide-Tipped Circular Saw – A more accessible option that provides good cutting efficiency, especially when working with thicker fiberglass tubes.
- Angle Grinder with Cutting Disc – Useful for on-site modifications, though it may require extra finishing due to rougher edges.
- Band Saw with Fine-Tooth Blade – Works well for controlled, low-vibration cutting, reducing material stress and ensuring cleaner cuts.
Effective Cutting Techniques for Large Diameter Tubes
Once the appropriate tool is selected, using the right cutting technique is crucial to prevent cracking, delamination, or uneven cuts. The method chosen depends on the tube thickness, diameter, and project requirements.
- Marking the Cut Line – Use a measuring tape and chalk line to ensure straight and accurate cuts. Applying masking tape along the cut line can help reduce splintering.
- Slow and Steady Cutting – Avoid applying excessive force when cutting. Instead, let the tool gradually slice through the material to prevent cracks or fiber unraveling.
- Rotational Cutting (For Large Tubes) – For extra-large diameter tubes, rotating the tube while keeping the saw in place can ensure a more even and consistent cut.
- Cooling and Dust Control – Using a wet cutting technique (such as spraying water) can minimize dust and heat buildup, preserving both the cutting blade and the fiberglass integrity.
Safety Precautions When Cutting Fiberglass
Fiberglass cutting generates fine particles that can irritate the skin, eyes, and respiratory system. Proper safety measures should always be followed to protect workers and maintain a safe work environment.
- Personal Protective Equipment (PPE):
- Respirator or Dust Mask – Prevents inhalation of fiberglass dust, which can be hazardous to lung health.
- Safety Glasses or Face Shield – Protects the eyes from airborne particles.
- Gloves and Long-Sleeved Clothing – Reduces skin irritation caused by fiberglass dust.
- Ventilation: Cutting fiberglass in a well-ventilated area or using an extraction system helps reduce airborne dust concentration.
- Tool Safety: Ensure all cutting tools are properly secured and operated according to manufacturer guidelines to prevent kickbacks or blade damage.
Post-Cut Finishing and Surface Treatment
After cutting, the edges of the fiberglass tube may have sharp or frayed fibers, requiring finishing to ensure smooth surfaces and prevent injuries.
- Edge Smoothing – Use sandpaper, a file, or a deburring tool to remove rough edges and create a clean finish.
- Sealing the Cut End – Applying resin, epoxy, or protective tape helps prevent future fiber exposure and strengthens the tube’s cut edge.
- Cleaning the Tube – Wipe down the tube with a damp cloth or compressed air to remove residual dust and debris before installation or further processing.
Cutting a large diameter fiberglass tube requires careful planning, the right tools, and proper execution to ensure precision and durability. Using specialized cutting equipment, following controlled cutting techniques, prioritizing safety precautions, and performing post-cut finishing all contribute to a successful cutting process. Whether the tube is being prepared for industrial piping, structural applications, or electrical conduit systems, adhering to these best practices will result in high-quality and reliable cuts.
FAQs about Large Diameter Fiberglass Tube
Fiberglass tubing is incredibly strong, especially considering its lightweight composition. The strength-to-weight ratio is one of its most significant benefits. Fiberglass tubing can withstand high pressure, extreme temperatures, and harsh environments without losing its integrity. Its durability makes it an excellent choice for industries that require both strength and corrosion resistance, such as chemical processing and marine applications. Typically, fiberglass tubing can support significant structural loads while being much lighter than steel or aluminum. The strength depends on factors such as wall thickness, diameter, and the specific resin used in production, but it remains one of the most reliable materials for industrial use.
Cutting a fiberglass tube is a straightforward process but requires some specific tools and safety precautions. First, always wear protective gear like gloves, goggles, and a mask to avoid inhaling fiberglass dust. A fine-tooth saw, such as a hacksaw or a circular saw with a carbide-tipped blade, works best for cutting fiberglass tubing. You should mark the cutting line clearly before starting, and make sure to cut slowly and evenly to prevent splintering. It’s important to use low pressure while cutting, allowing the saw to do the work. After cutting, edges can be smoothed with sandpaper to remove roughness.
Fiberglass tubes are versatile and used across various industries due to their strength, corrosion resistance, and lightweight properties. They are commonly found in municipal water systems, industrial pipelines, and chemical processing plants. Fiberglass tubes are also used in marine construction, such as docks and piers, because of their resistance to saltwater corrosion. Additionally, they are favored in infrastructure projects that require durable yet lightweight materials, like bridges or wastewater treatment facilities. Their non-conductive nature makes them ideal for electrical applications, while their ability to withstand high pressures makes them useful in ammonia processing and desalination systems.
Fiberglass pipes come in a wide range of sizes to suit various applications. The diameters typically start from as small as 2 inches (50 mm) and can go up to 144 inches (3.6 meters) or more. Large diameter fiberglass pipes are often used in industrial settings, water treatment, and chemical processing. Standard sizes include 4-inch (100 mm), 6-inch (150 mm), 8-inch (200 mm), and upwards. However, larger diameters, ranging from 10 inches (250 mm) to 72 inches (1.8 meters) or beyond, are commonly used for larger infrastructure projects. The size of the pipe required depends on factors like flow rate, pressure rating, and the specific requirements of the project. When selecting a fiberglass pipe, it is essential to consult with a supplier or engineer to determine the correct size based on the needs of the application and local regulations.
Fiberglass pipes are known for their longevity and durability. Under proper conditions, large diameter fiberglass pipes can last 50 years or more. Their resistance to corrosion, chemical degradation, and environmental factors contributes significantly to their extended lifespan. Unlike metal pipes, fiberglass does not rust, making it ideal for use in aggressive environments, such as water treatment facilities or chemical plants. Additionally, the strength of fiberglass can withstand extreme temperatures and pressures. However, the actual lifespan may depend on factors like installation quality, maintenance, exposure to UV light, and specific environmental conditions. Regular inspections and maintenance are essential to ensure that fiberglass pipes perform optimally over their extended service life. Their low maintenance requirements are another reason fiberglass is often chosen for infrastructure projects.
Fiberglass pipes are typically associated with insulation, rather than foam. The insulation is often applied to fiberglass pipes to improve thermal efficiency, reduce heat loss, and prevent condensation. Fiberglass insulation is made from spun glass fibers and is commonly used for both residential and industrial applications. It is designed to be placed around the pipe to protect against extreme temperatures and enhance energy conservation. In some cases, the fiberglass pipe itself may have an outer layer of foam or resin for added strength and insulation properties, but the primary material for insulation is fiberglass. Foam may also be used for insulation around other types of pipes, but fiberglass pipe insulation is more effective for high-temperature environments and areas where energy efficiency is a concern.
Fiberglass pipes offer numerous advantages, especially in large diameter applications. One of the key benefits is their resistance to corrosion, which makes them ideal for transporting chemicals, water, or wastewater. Unlike metal pipes, fiberglass pipes are not susceptible to rust or degradation from aggressive chemicals, ensuring a longer lifespan. Fiberglass is also lightweight, making installation easier and more cost-effective, especially for large diameter pipes. It can handle high temperatures and pressure without compromising structural integrity, making it suitable for both hot and cold water systems. Additionally, fiberglass pipes are environmentally friendly since they are made from non-toxic materials and are recyclable. Overall, their durability, low maintenance, and cost-effectiveness in the long run make fiberglass pipes a preferred choice in many industries, including oil and gas, mining, and water treatment.
Determining the correct size for a fiberglass pipe involves several factors, including the flow rate, pressure requirements, and the specific purpose of the pipe. First, calculate the required flow rate in gallons per minute (GPM) or liters per second (L/s) for the system. The pipe size will need to accommodate this flow while maintaining adequate pressure levels. It’s important to consider the pipe’s pressure rating, as larger pipes are often used for higher pressure systems. Additionally, consider factors like the type of fluid being transported, temperature, and the distance the pipe will cover. Consulting with a professional or using engineering software can help you select the right diameter. It’s essential to ensure the pipe is neither too small (which would restrict flow) nor too large (which could increase costs unnecessarily).
The thickness of fiberglass pipe insulation depends on various factors such as the pipe’s temperature, the surrounding environment, and the level of energy efficiency desired. For large diameter fiberglass pipes, insulation thickness typically ranges from 1 inch (25 mm) to 3 inches (75 mm), though it may go thicker in extreme conditions. If the pipe is carrying hot water or steam, a thicker insulation layer will be required to prevent heat loss. In cold environments or for pipes carrying cold water, insulation thickness helps prevent freezing. Building codes or standards may also provide guidelines for required insulation thickness. For energy-efficient systems, a thicker layer of fiberglass insulation will reduce energy consumption, while also offering protection against condensation and improving system performance.
Glass Reinforced Plastic (GRP) pipes, which are often used as large diameter fiberglass pipes, typically come in standard lengths of 20 feet (6 meters). However, the length can vary depending on the manufacturer and the specific project requirements. Custom lengths can also be fabricated to meet the specific needs of the installation. Longer sections are advantageous for large infrastructure projects, as fewer joints are needed, reducing the potential for leaks or failure. When installing GRP pipes, it is important to consider factors like transportation, handling, and installation logistics. The length of the pipes chosen will depend on the installation site’s space and the contractor’s preference for minimizing the number of joints. Longer lengths are typically used for projects like water supply systems, sewage networks, and industrial piping.
Large-diameter fiberglass mortar tubes have a long lifespan due to their durability and resistance to environmental factors. When properly maintained, they can last anywhere from 5 to 15 years, depending on the frequency of use, exposure to UV rays, and storage conditions. Unlike cardboard or PVC alternatives, fiberglass mortar tubes do not degrade quickly from moisture or temperature fluctuations. However, repeated exposure to high-velocity projectiles or explosive forces can gradually weaken the internal structure, necessitating regular inspections for cracks, delamination, or fiber wear. To extend their lifespan, users should store them in a dry, shaded area and inspect them for signs of damage after each use. Over time, fiberglass materials may become brittle if subjected to extreme conditions, but their longevity makes them a preferred choice for heavy-duty applications such as pyrotechnics, industrial launching systems, and military-grade mortars.
Yes, large-diameter fiberglass mortar tubes are designed to be reusable, making them a cost-effective and durable solution for repeated applications. Their high-strength composite construction allows them to withstand multiple firings without significant wear or deformation. Unlike single-use materials such as cardboard, fiberglass mortar tubes maintain their structural integrity even after exposure to high-pressure launches. However, their reusability depends on proper care and maintenance. Users should conduct routine inspections for internal and external damage, such as cracks, resin breakdown, or fiber exposure. Any signs of structural weakening could pose safety risks and should be addressed before reuse. Additionally, cleaning and proper storage help prolong their lifespan. Industries such as fireworks displays and military operations rely on fiberglass mortar tubes for their ability to handle repeated stress while maintaining consistent performance.
Glass tubes are widely used across various industries, but when considering large-diameter fiberglass tubes, their applications differ significantly from traditional glass tubes. Fiberglass-reinforced plastic (FRP) tubes are commonly used in structural, industrial, and utility applications due to their lightweight strength and resistance to corrosion. They are frequently employed in chemical processing, wastewater management, electrical conduit systems, marine applications, and aerospace engineering. In construction, fiberglass tubes serve as support columns, protective casings, and lightweight structural components. Their non-conductive nature makes them an ideal choice for electrical and communication infrastructure. Unlike standard glass tubes, which are fragile and primarily used in laboratory settings, fiberglass tubes provide high durability, impact resistance, and thermal insulation, making them a preferred alternative to traditional materials like steel or aluminum in large-scale projects.
Large-diameter fiberglass conduits offer numerous advantages, making them an essential choice in industries requiring durable and non-corrosive piping systems. Some key benefits include:
Corrosion Resistance – Unlike metal conduits, fiberglass does not rust or deteriorate when exposed to moisture, chemicals, or extreme temperatures, making it ideal for underground and marine applications.
Lightweight Strength – Despite its high strength-to-weight ratio, fiberglass is significantly lighter than steel or concrete, reducing transportation and installation costs.
Non-Conductivity – Fiberglass is an excellent insulator, eliminating the risk of electrical conductivity, which is crucial for power and communication infrastructure.
Durability – It resists environmental stress, impact, and UV degradation, providing a long lifespan with minimal maintenance.
Customizability – Available in various diameters and thicknesses, fiberglass conduits can be tailored for specific industrial needs, ensuring efficiency and reliability in large-scale projects.
Large-diameter fiberglass pipes exhibit exceptional strength, often outperforming traditional materials like PVC, concrete, or even steel in certain applications. Their strength primarily comes from the fiberglass-reinforced polymer (FRP) composite structure, which allows for high tensile strength, impact resistance, and pressure tolerance. Fiberglass pipes can withstand pressures ranging from 150 to 450 psi (pounds per square inch) or more, depending on the manufacturing process and intended application. They are also resistant to thermal expansion and contraction, which helps maintain structural integrity in fluctuating temperatures. Compared to metal pipes, fiberglass pipes are less prone to deformation, cracking, or corrosion, making them ideal for industrial fluid transport, oil and gas pipelines, water treatment plants, and underground utilities. Despite their lightweight construction, their load-bearing capacity is substantial, allowing them to function effectively in high-stress environments.
While Glass Reinforced Plastic (GRP) pipes offer numerous benefits, they also come with some drawbacks that must be considered:
Initial Cost – GRP pipes tend to have a higher upfront cost compared to materials like PVC or standard steel, which can be a limiting factor for budget-conscious projects.
Impact Sensitivity – While strong, GRP pipes can be brittle under excessive impact, leading to potential cracking or delamination if not handled properly.
Complex Installation – Specialized tools and trained personnel are often required for proper joining and installation, increasing labor costs.
Temperature Limitations – Though resistant to many environmental factors, GRP pipes may not perform well in extreme high-temperature conditions, potentially leading to resin degradation.
Limited Load-Bearing Capacity – While effective for many applications, GRP pipes might not be suitable for extremely high-pressure loads compared to traditional steel pipes in certain heavy-duty industries.
Despite these disadvantages, GRP pipes remain a preferred choice for industries requiring corrosion-resistant, lightweight, and durable solutions in large-diameter pipeline systems.
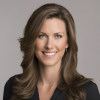
As the editor of GangLong Fiberglass, I have years of experience and in-depth research, focusing on cable tray products, fiberglass solutions, and grille systems. I incorporate years of industry insights and practical experience into every content, committed to promoting the progress of the industry. At GangLong Fiberglass, my commitment is reflected in every product, from innovative cable trays to durable fiberglass solutions and sturdy grille systems. As an authoritative voice in the industry, my goal is to provide valuable information to professionals and businesses and promote forward-looking solutions.