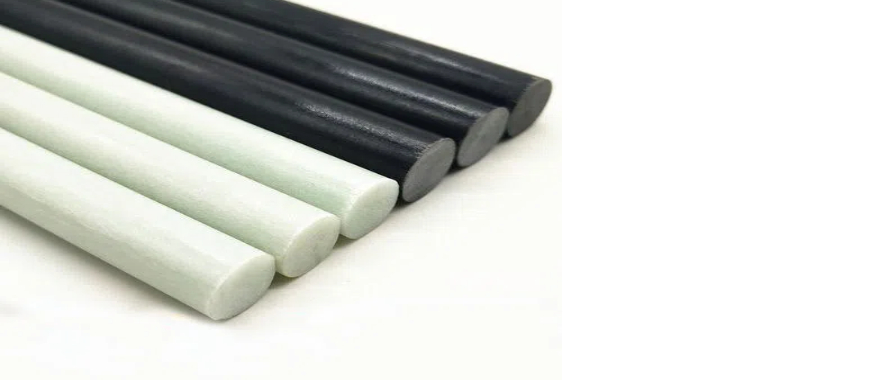
A multi-conductor cable with fiberglass rod in center is a specialized type of cable that consists of multiple conductors encased in an insulating material, with a fiberglass rod running through the center. This fiberglass rod is crucial for providing mechanical strength and flexibility, making the cable ideal for various demanding applications. The central fiberglass core helps maintain the shape of the cable, ensuring that it does not bend or distort easily, even under tension. These cables are widely used in industries such as construction, telecommunications, and electrical installations due to their strength, durability, and flexibility. Whether used for power distribution or signal transmission, the multi-conductor cable with fiberglass rod in center ensures reliability and long-lasting performance.
Key Features of Multi-Conductor Cable with Fiberglass Rod in Center
Enhanced Structural Integrity
The multi-conductor cable with a fiberglass rod in the center boasts superior structural strength compared to traditional cables. The fiberglass rod acts as a central spine, giving the cable rigidity and preventing it from sagging, twisting, or becoming deformed over time. This added support ensures the cable maintains its shape, making it less prone to damage during handling and installation. The robust structure also reduces the risk of internal conductor misalignment or breakage, which can cause signal loss or electrical failure.
Superior Durability
The inclusion of fiberglass in the core significantly improves the cable’s durability. Fiberglass is a lightweight yet incredibly strong material that is resistant to wear, corrosion, and harsh environmental conditions. This makes the cable ideal for applications where it will be exposed to heavy mechanical stress, such as construction sites, outdoor environments, or factory floors. The fiberglass rod strengthens the cable against tensile forces, ensuring that it can endure long-term use without becoming brittle or compromised.
- Weather Resistance: The fiberglass rod does not degrade under exposure to UV rays, moisture, or extreme temperatures, unlike some plastic or metal materials. This makes it particularly useful for outdoor applications.
- Chemical Resistance: Fiberglass is resistant to many chemicals and solvents, further extending the cable’s lifespan, especially in industrial environments where exposure to oils, fuels, or corrosive substances is common.
Flexibility and Easy Handling
Despite the added strength of the fiberglass rod, the cable remains highly flexible. The rod allows the cable to bend without losing its structural integrity, making it much easier to route through tight spaces or around corners. This flexibility is crucial in environments where cables must be installed in complex pathways, such as in machinery, building systems, or telecommunications setups. The ability to install the cable in confined or difficult spaces reduces the need for additional fittings or adjustments, saving time and cost.
- Tight Bend Radius: The fiberglass core helps maintain the cable’s flexibility while ensuring it does not bend too sharply, preventing damage to the internal conductors.
- Ease of Installation: The cable’s flexibility and strength make it much easier to install compared to rigid alternatives, reducing installation time and effort.
High Tensile Strength
One of the standout features of the multi-conductor cable with a fiberglass rod is its high tensile strength. The fiberglass core serves as a load-bearing support, allowing the cable to handle greater mechanical stresses without snapping or breaking. This is particularly beneficial for applications where cables are subjected to frequent pulling, stretching, or tensioning.
- Pulling and Stretching Resistance: The fiberglass rod helps the cable withstand the forces encountered during installation or when exposed to dynamic stresses, such as in mobile equipment or cranes.
- Prevention of Cable Damage: This strength minimizes the risk of damage during transportation or installation, providing a longer service life even in challenging conditions.
Lightweight Construction
Fiberglass is much lighter than metal alternatives, which results in a more lightweight cable. This lighter weight is particularly advantageous in installations that require the movement or handling of large volumes of cable, such as in large-scale projects, remote installations, or areas with limited access. A lightweight cable is easier to transport, handle, and install, reducing labor costs and the likelihood of damage during installation.
Resilience to Physical Stress
The multi-conductor cable with fiberglass reinforcement is highly resistant to physical stress. It can withstand impacts, bending, and stretching without compromising the integrity of its internal conductors. The fiberglass core acts as a buffer, absorbing external forces and preventing them from damaging the individual conductors inside. This resilience is particularly important in industrial, automotive, or construction applications where cables may be exposed to rough handling, heavy loads, or accidental impacts.
- Shock and Vibration Resistance: The cable’s ability to absorb physical shock and vibration makes it suitable for machinery and equipment that are subject to frequent movement or mechanical stress.
- Impact Resistance: The fiberglass rod helps maintain the cable’s integrity when it is dropped, struck, or otherwise subjected to sudden impact forces.
Improved Electrical Performance
The multi-conductor cable with a fiberglass rod in the center often features high-quality conductors, typically made of copper or aluminum, which ensure optimal electrical conductivity. The reinforced structure ensures that the conductors remain properly aligned and protected, reducing signal loss, interference, or electrical resistance that could otherwise affect the performance of electrical systems. The combination of durable insulation and a strong central core also minimizes the risk of electrical shorts due to damage or degradation of the internal wires.
Versatility in Application
These cables are highly versatile and can be used across a wide range of industries, including:
- Telecommunications: For reliable signal transmission over long distances.
- Power Distribution: In both industrial and commercial settings, where cables need to carry high loads of power while being flexible and resistant to physical stress.
- Data Transmission: Ensuring minimal signal loss and maximum integrity during data transfer, even in harsh environments.
- Industrial Automation: Providing the durability and flexibility needed for robotics, machinery, and control systems.
- Construction and Outdoor Installations: Resistant to weather and physical impacts, making it ideal for underground or aerial installations in outdoor environments.
Long-Term Reliability and Low Maintenance
The combination of fiberglass and conductive materials (copper or aluminum) contributes to the long-term reliability of the cable. The fiberglass rod prevents internal conductor damage and minimizes the likelihood of physical wear. This results in fewer repairs or replacements, offering significant cost savings in the long run. Additionally, the cable’s resistance to environmental factors like moisture, UV light, and chemicals ensures that it can continue to perform reliably for years, even in challenging conditions.
Cost-Effective Investment
Although multi-conductor cables with fiberglass reinforcement might have a higher upfront cost compared to standard cables, their enhanced durability, flexibility, and long-term reliability make them a cost-effective choice for long-term projects. The need for fewer replacements and reduced maintenance costs offset the initial investment, making them an ideal choice for mission-critical applications where reliability is paramount.
The multi-conductor cable with fiberglass rod in the center is a highly durable, flexible, and reliable solution for a wide range of applications. By incorporating a fiberglass core, the cable achieves a unique balance of strength, flexibility, and resistance to environmental factors, making it ideal for both indoor and outdoor installations. Its ability to withstand mechanical stress, resist physical damage, and maintain consistent electrical performance over time ensures it is well-suited for industries such as construction, telecommunications, industrial automation, and data transmission. The cable’s enhanced durability and ease of installation make it a top choice for demanding environments, providing a long-lasting, cost-effective solution.
Best Multi-Conductor Cables with Fiberglass Rod in Center: Top Recommendations
When selecting the best multi-conductor cable with a fiberglass rod in the center, it’s essential to match the cable’s specifications to the requirements of your specific application. Factors such as conductor size, insulation type, temperature rating, mechanical strength, and environmental resistance should be carefully considered. Below are some of the top recommendations for multi-conductor cables with fiberglass rods, each offering unique features to meet a variety of needs:
Type THHN (Thermoplastic High Heat-Resistant Nylon-coated)
Key Features:
- Flexibility: The THHN cable is known for its excellent flexibility, making it suitable for a wide range of installations, particularly in spaces that require tight bends or flexibility in routing.
- High Temperature Resistance: THHN cables can withstand temperatures up to 90°C (194°F) in dry conditions and 75°C (167°F) in wet conditions. This makes them ideal for applications in hot environments or industrial systems that deal with high heat.
- Fiberglass Rod for Strength: The fiberglass rod in the center adds strength and support, preventing cable deformation and enhancing its tensile strength during installation and operation.
- Applications: Commonly used in industrial, commercial, and residential settings, THHN cables are widely used in power distribution, control circuits, and machinery wiring.
Best For: Industrial settings, machinery control systems, and power distribution in environments where both flexibility and heat resistance are critical.
Type UF-B (Underground Feeder)
Key Features:
- Direct Burial Rating: Type UF-B cables are specifically designed for direct burial applications. With a robust outer sheath and a fiberglass core, they provide excellent mechanical protection against external stresses and are ideal for outdoor, underground installations.
- Moisture and UV Resistance: The cable is highly resistant to moisture, UV rays, and temperature fluctuations, making it perfect for use in harsh outdoor environments where exposure to elements is common.
- Fiberglass Reinforcement: The fiberglass rod offers mechanical support, ensuring that the cable remains intact even under high tensile forces or while buried underground.
- Applications: Ideal for power distribution in residential or commercial properties, especially when cables need to be buried underground for long periods without degradation.
Best For: Direct burial applications, outdoor power and lighting installations, and feeder lines in harsh environments.
Shielded Multi-Conductor Cables with Fiberglass Rod
Key Features:
- Shielding for Electrical Interference: These cables are equipped with shielding (such as foil or braided shields) to protect sensitive signals from electrical noise and interference. The addition of a fiberglass rod ensures that the shielding and conductors remain intact and properly aligned even during installation.
- Enhanced Flexibility and Mechanical Strength: The fiberglass rod provides the necessary core strength, while the shielding ensures that the cable maintains its electrical integrity, even in environments with high electromagnetic interference (EMI).
- Moisture and UV Resistance: The shielding and the fiberglass rod ensure the cable is well-protected against environmental stressors, including moisture, UV radiation, and physical wear.
- Applications: Commonly used in data transmission, communication systems, and industrial applications where the integrity of electrical signals is critical, such as in robotics, industrial automation, and telecommunications.
Best For: Applications requiring signal integrity, such as data transmission, communication systems, or industrial automation in environments prone to electrical interference.
Type XHHW (Cross-Linked High Heat-Resistant Wire) with Fiberglass Core
Key Features:
- Superior Heat Resistance: XHHW cables are known for their high heat resistance. With a temperature rating of up to 90°C (194°F) in both wet and dry conditions, they are suitable for high-temperature environments like industrial plants or electrical panels.
- Fiberglass Rod Support: The inclusion of a fiberglass rod in the center increases the overall strength of the cable, allowing it to resist physical stress during installation or operation.
- Cross-Linked Insulation: XHHW cables feature cross-linked polyethylene (XLP) insulation, which provides superior electrical properties and resistance to moisture, oils, and chemicals, making them ideal for industrial settings.
- Applications: These cables are used in commercial and industrial electrical systems, particularly in power distribution, control circuits, and for installations requiring robust environmental and mechanical protection.
Best For: Heavy-duty industrial applications, power and control circuits, and environments with high heat, moisture, or chemical exposure.
Type SJOOW (Service Junior Oil-Resistant Weather-Resistant)
Key Features:
- Oil and Weather Resistant: SJOOW cables are specifically designed to resist oil, water, and extreme weather conditions, making them perfect for applications in factories, construction sites, and outdoor equipment.
- Flexibility: These cables remain highly flexible, even at low temperatures, and can be coiled or bent without risk of damage. The fiberglass rod provides additional support and helps maintain the cable’s structure, even during flexible usage.
- Mechanical Strength: The fiberglass core reinforces the cable’s overall mechanical strength, which is critical for applications where the cable might be subjected to physical abuse, such as in industrial machinery or outdoor installations.
- Applications: Commonly used in machinery, portable power tools, and construction equipment that require a durable and flexible cable to operate reliably in harsh environments.
Best For: Portable power applications, machinery in outdoor or industrial settings, and construction sites.
Type MV-105 (Medium Voltage) with Fiberglass Rod
Key Features:
- Medium Voltage Rating: These cables are designed for medium voltage applications, typically ranging from 2 kV to 35 kV, making them ideal for industrial power distribution systems.
- Fiberglass Rod for Structural Integrity: The fiberglass rod in the center ensures the cable remains strong and resistant to external pressures, which is essential in high-tension or underground installations.
- Robust Insulation: MV-105 cables feature robust, cross-linked polyethylene (XLPE) insulation, which provides exceptional resistance to electrical stresses, temperature variations, and environmental factors.
- Applications: These cables are used in medium voltage power distribution systems, such as those found in substations, factories, and large commercial buildings.
Best For: Power distribution in medium-voltage industrial and commercial settings, including electrical substations and underground power lines.
The best multi-conductor cables with fiberglass rods in the center offer superior flexibility, durability, and protection against mechanical and environmental stresses. When selecting a cable, consider the specific requirements of your application, such as temperature resistance, flexibility, shielding, and installation environment. The cables listed above provide a wide range of options to suit different needs, from heavy-duty industrial systems to outdoor and direct-burial installations, ensuring reliable performance and longevity in demanding conditions.
By choosing the right cable based on your project’s specifications—whether for power distribution, data transmission, or signal integrity—you ensure both the safety and efficiency of your electrical systems.ou can ensure that the multi-conductor cable with fiberglass rod in center performs optimally and lasts for years.
Top Cable Tray Brands for Reliable Cable Management
Advantages of Using Multi-Conductor Cable with Fiberglass Rod in Center
Enhanced Mechanical Strength
Factors Contributing to Mechanical Strength
The mechanical strength of a multi-conductor cable with a fiberglass rod in the center is primarily due to the high tensile strength of fiberglass, a material known for its stiffness and robustness. Fiberglass, unlike other reinforcement materials like steel, offers the ideal combination of lightweight and strength. The core of fiberglass fibers is woven into a rigid structure that resists stretching and deformation under tension. Additionally, the fiberglass core is not only strong in terms of pulling force, but it also helps distribute stress evenly across the entire length of the cable, preventing any one point from bearing too much load. This makes the cable significantly more durable compared to standard cables, which may lack such reinforcement.
Benefits of Mechanical Strength
- Increased Pulling Capability
The fiberglass core enhances the pulling strength of the cable, allowing it to be safely installed over long distances without the risk of breakage or excessive stretching. This is especially useful when the cable needs to be pulled through long conduits or across challenging terrains, where traditional cables might fail. - Resistance to Deformation Under Stress
The fiberglass core ensures that the cable remains resistant to deformation even in high-stress conditions, such as when it is dragged over rough surfaces or bent excessively during installation. This makes the cable much more durable and less likely to suffer from permanent damage during installation or use. - Reduced Risk of Stress Fractures
One significant advantage of the fiberglass reinforcement is that it helps reduce the likelihood of stress fractures or other types of failure. The fiberglass core is designed to absorb and distribute large amounts of stress, which prevents localized points of weakness that might otherwise cause the cable to fail. - Enhanced Durability During Handling
Since the fiberglass rod is capable of absorbing significant mechanical stress, it reduces the risk of mechanical damage during handling. This is particularly important in environments where the cable is frequently manipulated or subjected to physical forces, such as in construction or industrial applications. - Critical Benefit for Long-Term Physical Force Resistance
For projects where the cable will be exposed to constant physical forces over an extended period, the fiberglass core offers critical protection. The added strength helps ensure that the cable can withstand continuous stress without compromising electrical performance or suffering from premature wear and tear.
Role in Preventing Cable Damage
The role of the fiberglass rod in preventing cable damage cannot be overstated. Unlike unreinforced cables, which may be vulnerable to crushing, abrasion, or stretching, the fiberglass core provides structural integrity that absorbs external impacts. When external forces such as mechanical pressure are applied, the fiberglass helps distribute the force, preventing localized damage. This ensures that the cable is much less likely to suffer from dents, breaks, or cracks. In environments where cables are subject to physical strain, the fiberglass core ensures that the electrical conductors remain unharmed, maintaining the cable’s reliable performance throughout its lifespan.
Advantages in Long-Distance Installation
When it comes to long-distance installations, particularly in complex environments like underground pathways or overhead utility lines, the added mechanical strength of the fiberglass rod is a game-changer. Standard cables, when pulled over long distances, are prone to stretching, sagging, or even snapping under high tension. However, with a fiberglass-reinforced cable, the tensile strength is greatly enhanced, reducing the risk of stretching or breakage. This added strength allows for fewer installation issues, making the process smoother and faster. This benefit is especially valuable in telecommunication, power transmission, and fiber optic installations, where long-distance cable runs are common.
Disadvantages of Increased Mechanical Strength
While the increased mechanical strength provides a host of benefits, there are some potential downsides to consider. The increased rigidity due to the fiberglass core can reduce the cable’s overall flexibility, making it more difficult to install in spaces that require a high degree of maneuverability. In installations where tight bends or small conduits are involved, the stiff nature of the cable might make it harder to fit or route around obstacles. Additionally, the rigid structure may make it more challenging to handle or coil the cable, which could slow down the installation process. Therefore, while fiberglass increases strength, it also imposes certain limitations in terms of flexibility.
Protection Against Physical Damage
- Protective Shield for Internal Conductors
The fiberglass rod at the center of the cable serves as a primary defense for the internal conductors, providing an essential layer of protection. By acting as a structural support, the fiberglass rod ensures that the conductors inside the cable remain intact and undamaged, even under harsh conditions. This shield is vital in preventing damage that could disrupt the cable’s function and compromise its performance. - Prevention of Crushing and Compression Damage
In environments where cables are subject to heavy loads or physical pressure, such as on construction sites or in industrial settings, cables are often at risk of being crushed or compressed. The fiberglass core absorbs and distributes these forces, preventing them from reaching the delicate electrical conductors inside. This protective function ensures that the cable maintains its structural integrity and continues to operate reliably, even when subjected to external pressures. - Protection Against Bending and Kinking
Cables installed in tight spaces or subjected to sharp bends are vulnerable to being damaged by excessive bending or kinking. The fiberglass rod provides additional rigidity to the cable, preventing it from bending too sharply and potentially damaging the conductors inside. This is particularly important during installation or in environments where cables must navigate around obstacles, as it reduces the likelihood of permanent damage caused by tight turns or twists. - Abrasion Resistance
In many industrial and outdoor environments, cables can experience abrasion from being dragged along rough surfaces or in contact with sharp edges. The fiberglass rod adds a layer of abrasion resistance, preventing the outer layers of the cable from being worn down or damaged by friction. This added protection is especially important in high-wear environments, such as underground conduit systems, outdoor installations, or areas with constant movement. - Ensures Reliable Power and Signal Transmission
The primary role of the fiberglass rod is to preserve the cable’s ability to deliver power or signals reliably. By protecting the internal conductors from physical damage, the fiberglass rod ensures that the cable continues to function optimally, transmitting signals or power without interruption. This is crucial in applications like telecommunications, data transmission, and power distribution, where consistent performance is essential for the operation of larger systems. - Maintenance of Cable Integrity in Harsh Environments
In challenging environments, such as construction sites, outdoor installations, or remote areas, cables are often exposed to a range of physical threats. The fiberglass core acts as an added layer of security, ensuring that the cable remains intact and functional despite being exposed to rough handling or physical abuse. This added protection ensures that the cable maintains its reliability, reducing the need for frequent repairs or replacements. - Reduced Risk of Internal Conductor Damage
Without the fiberglass rod, cables can be susceptible to internal conductor damage, especially in scenarios where external forces are applied. For example, crushing can lead to broken or severed conductors, which can cause power failure or signal loss. The fiberglass core reduces these risks, ensuring that the electrical pathways remain secure and undamaged, even if the cable is physically stressed.
Increased Cable Lifespan
- Enhanced Durability
The fiberglass core significantly contributes to the overall durability of multi-conductor cables. By offering additional mechanical strength and resistance to physical damage, the fiberglass rod helps the cable withstand harsh conditions over a prolonged period. This increased durability ensures that the cable is less prone to wear and tear caused by environmental factors, handling, or external stresses, extending its functional lifespan compared to traditional cables without such reinforcement. - Reduced Risk of Failure Over Time
One of the key advantages of using a fiberglass-reinforced cable is that the rod helps distribute mechanical stresses more evenly, reducing the chances of localized damage that can lead to failure. Without this added protection, standard cables might suffer from stress fractures, deformation, or wire breakage over time, especially in high-stress environments. The fiberglass rod absorbs much of the strain, reducing the risk of such failures and ensuring that the cable remains intact and functional for much longer. - Protection Against Environmental Factors
In addition to mechanical protection, fiberglass offers resistance to environmental damage such as corrosion, moisture, and temperature extremes. Unlike metal cores, which can corrode or degrade when exposed to water or harsh chemicals, fiberglass is impervious to moisture and rust, ensuring that the cable remains protected in wet or corrosive environments. This characteristic makes fiberglass-reinforced cables ideal for outdoor and industrial applications where exposure to elements like rain, chemicals, or fluctuating temperatures can degrade standard cables quickly. - Long-Term Cost Savings
The durability of a fiberglass-core cable leads to significant cost savings over time. Since these cables are less likely to experience wear or failure, they require fewer replacements or repairs, reducing the long-term maintenance costs. This is especially beneficial in large-scale projects, such as data centers, telecommunications networks, or power grids, where frequent cable replacements or maintenance could result in substantial costs. Investing in a more durable cable with a fiberglass core ultimately results in fewer disruptions and lower operational expenses. - Ideal for Long-Term, High-Impact Installations
For projects that involve long-term installations, where the cable will be exposed to physical forces and environmental stressors over many years, fiberglass-reinforced cables offer superior longevity. Whether installed in construction zones, underground tunnels, or outdoor environments, these cables are built to withstand the rigors of time and offer reliable service over extended periods. Their ability to perform in high-stress applications makes them an ideal choice for infrastructure that must endure constant use and harsh environments, such as in utilities or transportation systems. - Fewer Maintenance Interruptions
The increased lifespan of fiberglass-core cables directly leads to fewer maintenance interruptions. With standard cables, wear and tear can cause failures that interrupt service, leading to costly repairs and downtime. However, with the added strength and protection of fiberglass, these cables are less susceptible to damage, minimizing the frequency of inspections, repairs, or replacements. This makes them a more reliable choice for mission-critical applications where system uptime is essential. - Enhanced Reliability in High-Demand Applications
The added mechanical strength and protection of fiberglass make these cables especially reliable in high-demand environments, such as power distribution systems, fiber optic installations, and communication networks. In these applications, cables must provide uninterrupted service over many years. The fiberglass rod helps ensure that the cable maintains consistent performance without degradation, even under continuous physical stress, high temperatures, or exposure to harsh chemicals. This long-term reliability ensures the cable continues to deliver power or signals effectively throughout its lifespan.
Advantages of Using a One Touch Cable Tray
Multi-Conductor Cable with Fiberglass Rod in Center for Sale
When looking to purchase a multi-conductor cable with a fiberglass rod in the center, there are multiple options available both online and through local suppliers. These cables are widely used in various industries, from telecommunications to power distribution, and can be found in many different specifications to suit diverse project requirements.
- Customization Options
These cables come in a variety of lengths, conductor sizes, and insulation types. Depending on your specific needs, you can select cables that offer different features, such as extra-heavy-duty insulation, or cables designed for use in harsh environmental conditions. Be sure to choose the cable that best matches your installation environment, whether it involves underground applications, outdoor exposure, or installations requiring high tensile strength. - Price Variability and Comparison
The price of multi-conductor cables with fiberglass rods can vary significantly depending on factors like cable length, conductor size, and insulation material. For example, cables designed for more specialized applications—such as those needing additional protection against chemicals or temperature extremes—may be priced higher. It’s advisable to compare prices from multiple suppliers to find the most cost-effective option that meets your quality standards. Bulk purchases are often eligible for discounts, and many suppliers also offer free shipping for large orders, which can reduce the overall cost for commercial or industrial projects.
Where to Buy
- Online Platforms and Local Suppliers
Major online platforms like Cbrofiberglass provide a broad range of multi-conductor cables with fiberglass rods, sourced from a variety of trusted manufacturers. These platforms often allow you to filter by cable specifications, including conductor material, insulation type, and fiber reinforcement, making it easier to find exactly what you need for your project. Shopping online also provides the added benefit of customer reviews and ratings, which can help you make a more informed decision. - Key Considerations for Purchase
When purchasing, consider key factors such as delivery times, especially if you’re working with a tight timeline. Some suppliers may offer expedited shipping options or more flexible ordering volumes, catering to both small-scale and large-scale projects. Additionally, be sure to check the warranty and return policies offered by the seller, as these can provide added peace of mind in case of any issues during installation.
Popular Online Stores
- Cbrofiberglass
Cbrofiberglass is a reliable platform that offers a wide variety of multi-conductor cables with fiberglass rods. The website features product descriptions, specifications, and customer reviews, which can assist in finding the most suitable cable for your needs. The reviews often highlight the performance and durability of the cables in real-world conditions, helping you gauge the reliability and quality of the product before making a purchase.
Fitting Cable Tray Guide: Step-by-Step Installation Tips
Installation Tips for Multi-Conductor Cables with Fiberglass Rod in Center
Preparing for Installation
Before beginning the installation of a multi-conductor cable with a fiberglass rod in the center, it’s crucial to ensure you have the correct tools and safety equipment to carry out the job efficiently and safely. Proper preparation will not only ensure smooth installation but also protect both the cable and yourself.
- Tools and Equipment
You will need the appropriate cutting tools, such as cable cutters or wire strippers, to ensure clean cuts without damaging the cable. A cable puller (or winch) is also recommended for long-distance pulls, as it helps in minimizing the strain on the cable during installation. Additionally, protective gloves are essential to avoid any injuries from the cable’s edges or sharp insulation, and safety goggles are advisable when working in environments with flying debris. - Handling the Cable Carefully
One of the key aspects of working with multi-conductor cables with fiberglass rods is careful handling. The fiberglass core provides critical mechanical strength and structural support, but it can be damaged if mishandled. Avoid pulling or twisting the cable too forcefully, as kinking or bending the cable too sharply can compromise the structural integrity of the fiberglass core. Also, be cautious about abrasion on the cable’s surface, which could damage the insulation and affect the performance.
Step-by-Step Installation Guide
Proper installation is essential to ensure the cable functions optimally throughout its lifespan. Here is a detailed, step-by-step guide to help you successfully install the multi-conductor cable with a fiberglass rod in the center:
Measure and Cut the Cable
- Before starting, measure the length of cable you’ll need for your installation. It’s always a good idea to add a little extra length to account for any potential adjustments or changes in the installation path. Once you’ve measured, use cable cutters to trim the cable cleanly to the required length.
- Tip: When cutting the cable, make sure to use a tool that is appropriate for the cable’s thickness to avoid damaging the insulation or fiberglass rod inside. A sharp blade or a specialized cable cutter can provide a clean cut, preventing any unnecessary fraying or internal damage.
Prepare the Path
- Clear the Installation Path: Make sure the entire path where the cable will be laid is clear of any debris, dirt, or sharp objects that could potentially damage the cable or insulation.
- If the cable will be run through conduits, inspect the conduits to ensure they are clean and free from any debris, rust, or sharp edges. If necessary, use a conduit brush or vacuum to remove any dirt or rough spots that could scrape or damage the insulation.
- Pre-measure Conduit Size: Check that the conduit is wide enough to accommodate the cable without causing it to bend sharply. A tight fit inside the conduit could stress the cable and compromise the fiberglass core, affecting its durability and performance.
Install the Cable
- Use a Cable Puller: For longer installations or tight spaces, it’s highly recommended to use a cable puller or winch. These devices help manage the tension applied to the cable and ensure a smooth, controlled pull.
- Minimize Sharp Bends: As you guide the cable through the space or conduit, make sure it doesn’t bend too sharply. A sharp bend can damage the fiberglass core, which could negatively affect the mechanical strength and performance of the cable.
- Avoid Over-Stretching: Keep the pulling force within reasonable limits to avoid excessive strain on the cable. When pulling the cable over long distances, take breaks to ensure the cable doesn’t stretch or pull unevenly.
Secure the Cable
- Once the cable is in position, it’s important to secure the cable along the installation route to prevent any movement that could lead to damage or excessive strain.
- Use cable ties or clamps to fasten the cable at appropriate intervals. These should be placed at regular intervals to maintain the cable’s position and ensure it remains secure while avoiding any tight pinching that could cause internal damage.
- If the cable runs through conduits or along walls, ensure that the cable is supported at regular points to prevent sagging or unnecessary stress on the cable. Cable trays or hooks can be used to help maintain proper alignment and tension during use.
Additional Installation Considerations
- Environmental Factors: Consider the environment in which the cable will be installed. If the cable is used outdoors, ensure that it is weatherproofed and that the installation path is protected from the elements, especially if the cable is exposed to extreme temperature fluctuations or moisture.
- Avoid Overloading: Ensure that the cable is not carrying a load that exceeds its rated capacity. This includes ensuring proper voltage and current are within safe operating limits, preventing overheating or damage.
FAQs about Multi-conductor Cable with Fiberglass Rod in Center
An electrical cable with a conductor in its center typically refers to a coaxial cable or a multi-conductor cable with a central conductor. In coaxial cables, the central conductor is usually made of copper or aluminum and is surrounded by insulation, shielding, and an outer jacket. This structure is designed to carry electrical signals while minimizing interference from external sources. The conductor at the center serves as the primary medium for transmitting the signal. Coaxial cables are widely used in telecommunications, internet connections, and video signal transmission due to their ability to transmit high-frequency signals with low attenuation.
In other types of cables, such as multi-conductor cables with fiberglass rods, the central core could be made of fiberglass instead of a conductor. The fiberglass rod acts as a structural support for the cable, providing strength and flexibility. These cables are commonly used in harsh environments where strength and flexibility are crucial, like in industrial or outdoor installations. They are also used in specific power and signal distribution applications. It’s important to select the right type of cable with a conductor in its center based on the specific electrical requirements of your project.
Connecting fiberglass rods typically requires a few specific techniques depending on the application and the type of rod being used. Fiberglass rods are often used in electrical and construction applications, such as for cable pulling, reinforcing structures, or as part of composite systems.
One of the most common methods of connecting fiberglass rods is by using fiberglass rod connectors. These are specially designed to join two or more fiberglass rods securely. The connectors are usually threaded or designed to clamp onto the ends of the rods, creating a strong and stable bond. For example, if you’re using fiberglass rods for pulling electrical cables, connectors can help extend the length of the rod to cover longer distances.
Another method of joining fiberglass rods is by using epoxy or adhesive bonding. This method is often used when a permanent connection is needed, such as in manufacturing or structural applications. It’s essential to select the correct adhesive that is compatible with fiberglass to ensure a secure and durable connection.
In some cases, mechanical fasteners, like stainless steel pins, screws, or bolts, may be used to join the rods, particularly when there is a need for a more robust connection or when working in heavy-duty environments. It’s important to follow the manufacturer’s instructions and safety guidelines when connecting fiberglass rods to ensure the integrity and safety of the structure or installation.
Fiberglass is not commonly used as the main component in the conductive part of electrical wires, but it is often used as an insulation material or reinforcement in certain types of wires and cables. In electrical wiring, the conductor (typically made of copper or aluminum) is responsible for carrying the electrical current, while fiberglass plays a role in protecting and reinforcing the wire.
For instance, in fiberglass-insulated wires, the fiberglass is used as a protective layer around the conductor. This insulation provides excellent durability and resistance to heat, corrosion, and physical wear. Fiberglass insulation is particularly useful in high-temperature environments where traditional plastic insulations may not perform well. It’s also used in high-voltage cables and industrial applications, where its ability to withstand extreme conditions is a key advantage.
Fiberglass is also often incorporated into fiberglass-reinforced cables, where it is used as a strengthening element to prevent the cable from being damaged during installation or use. The fiberglass rod at the center of these cables helps to increase the cable’s tensile strength, making them suitable for heavy-duty applications, such as construction, telecommunications, and even marine environments. While fiberglass is not present in the conductive parts of electrical wires, it plays a crucial role in improving the overall performance and longevity of certain cables and wires.
Fiberglass rods are versatile components used in a wide range of industries for their strength, flexibility, and lightweight properties. They are commonly used in construction, telecommunications, electrical installations, and recreational activities. Here are some of the primary uses of fiberglass rods:
Cable Pulling: Fiberglass rods are commonly used for pulling cables through conduits or other tight spaces. They are ideal for this purpose because of their lightweight, flexible nature, which allows them to navigate around corners and obstacles with ease. These rods can extend long distances and help electricians or technicians pull wires or cables through walls, ceilings, and underground pipes without the need for large, bulky equipment.
Reinforcement in Composite Materials: In the manufacturing of composite structures, fiberglass rods are often used as a reinforcement element. They help improve the strength and structural integrity of materials, making them suitable for use in boats, automotive parts, and structural components.
Fishing Poles: Fiberglass rods are often used in fishing poles due to their flexibility and durability. While not as light or sensitive as carbon fiber rods, fiberglass rods are more affordable and provide a durable solution for general fishing, especially for beginners.
Towers and Antenna Support: Fiberglass rods are used to support antennas and communication towers. They provide a non-corrosive and weather-resistant option, making them ideal for outdoor installations that are exposed to harsh environmental conditions.
Structural Applications: Fiberglass rods are also used in structural applications where high strength-to-weight ratios are needed. They are used to reinforce concrete, support lightweight frames, or form part of larger composite systems used in construction and manufacturing.
The diverse applications of fiberglass rods make them an essential component in various industries, offering strength, resistance to corrosion, and flexibility where traditional materials like metal or wood may not be suitable.
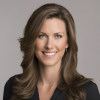
As the editor of GangLong Fiberglass, I have years of experience and in-depth research, focusing on cable tray products, fiberglass solutions, and grille systems. I incorporate years of industry insights and practical experience into every content, committed to promoting the progress of the industry. At GangLong Fiberglass, my commitment is reflected in every product, from innovative cable trays to durable fiberglass solutions and sturdy grille systems. As an authoritative voice in the industry, my goal is to provide valuable information to professionals and businesses and promote forward-looking solutions.