- Home
- Stainless Steel Cable Tray
Stainless Steel Cable Tray – Wire Basket Design
Stainless Steel Cable Tray-lightweight, cost-effective wire basket for cable management. CSA, UL, NEMA certified. Durable straight sections. GangLong Fiberglass is a leading manufacturer of Stainless Steel Cable Tray Systems, offering various options including Medium to Heavy Duty, Straight Edge, Return Flange, and Wire Basket types. GangLong Fiberglass’s Stainless Steel Cable Tray system is known for its performance, safety, and economy. It adapts to complex configurations while offering maximum strength with minimal weight. The system’s ease of on-site fitting creation and its range of unique and universal accessories enable fast installation and flexible routing.
Stainless steel cable tray and FRP cable tray have become increasingly popular, especially in industrial and commercial settings. Stainless steel cable trays are essential for managing and protecting electrical cables, while FRP cable trays offer additional advantages such as corrosion resistance and lightweight construction. Their durability and corrosion resistance make them ideal for harsh environments with exposure to chemicals or extreme temperatures. They provide a reliable solution for maintaining organized cable systems, ensuring long-term performance and reducing maintenance costs.
Simplifying Your Life: Key Functionalities
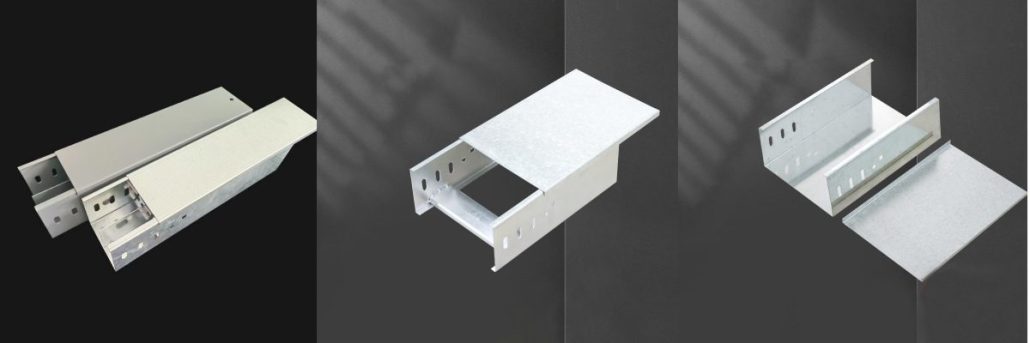
Attribute | Details |
---|---|
Product Name | Stainless Steel Cable Tray |
Material | Stainless Steel (SS304, SS316, SS316L), Galvanized Steel (Q235) |
Type | Ventilated or Perforated Trough, Wire Mesh Tray, Cable Ladder, Cable Trunking, Wire Way |
Width | 50mm to 1200mm |
Length | Customizable |
Side Rail Height | 12mm - 300mm |
Max. Working Load | Dependent on size and specifications |
Thickness | 0.8mm to 3.0mm |
Surface Finish | Electro Galvanized, Hot Dipped Galvanized, Electrolytic Polishing, Powder Coated, Pre-Galvanized |
Color Options | Custom Colors |
Certification | CE, UL, ISO, SGS, NEMA, IEC |
Application | Cable support, electrical installations, construction projects, power plants, infrastructure projects |
Accessories | Connector, Mounting Brackets, End Caps |
Packaging | Bubble Bags, Inner Boxes, Cartons |
Customization | OEM and ODM options available |
Installation | Easy installation with connectors and accessories |
Advantages | Durable, corrosion-resistant, easy to install, customizable sizes, flexible for various industrial applications |
News
- Exploring the Benefits of Carbon Fiber Apparel
- How to Work with Carbon Fiber Successfully
- Carbon Fiber Suit: The Future of Lightweight Armor
- Is Carbon Fiber Armor the Future of Protection?
- Why White Carbon Fiber is Popular in Automotive Design
- Transparent Carbon Fiber Sheets: Strength Meets Clarity in Design
- Chopped Carbon Fiber Mat for Lightweight Reinforcement
- Carbon Fiber EG Hatch: Upgrade Your Civic Today
- The Benefits of Using Structural Carbon Fibre in Engineering
- How Many Layers of Layered Carbon Fiber Are Needed?
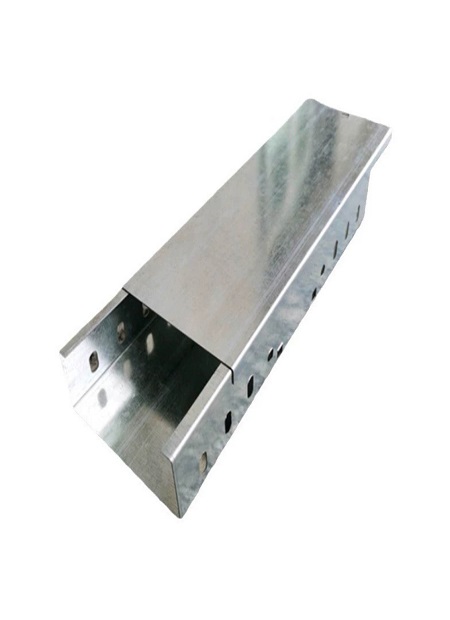
Stainless Steel Cable Tray Sizes and Specifications
When selecting a Stainless Steel Cable Tray, it is essential to consider the various sizes and configurations available to ensure the tray meets the demands of your project. Stainless Steel Cable Tray systems typically come in standard dimensions to accommodate a range of cable management needs. Common sizes include widths of 100 mm, 200 mm, and 300 mm, with depths ranging from 50 mm to 150 mm. Lengths are often available in standard increments such as 1 meter, 2 meters, and 3 meters.
For projects with specific requirements, GangLong Fiberglass manufacturer offers Stainless Steel Cable Tray customization options. Custom sizes and configurations can be tailored to fit unique installations, allowing for precise alignment with existing infrastructure or bespoke project needs. This flexibility ensures that the Stainless Steel Cable Tray provides optimal support and coverage, maintaining the integrity and efficiency of your cable management system.
Stainless steel cable trays are commonly used for supporting electrical cables in industrial and commercial settings, known for their durability, corrosion resistance, and ability to withstand harsh environments. Below is a detailed description of common sizes and specifications for stainless steel cable trays:
1. Types of Stainless Steel Cable Trays
Ladder Type Cable Tray
Ladder-type cable trays consist of two side rails connected by rungs, resembling a ladder. They are ideal for supporting heavy-duty cables in environments that require high heat dissipation, such as industrial facilities and data centers. The open design allows for excellent airflow, preventing overheating. This type of tray is typically used for large cable bundles and high-load applications, ensuring both strength and proper ventilation.
Perforated Cable Tray
Perforated cable trays feature a flat base with evenly spaced holes, allowing airflow to prevent overheating of cables. This design is suitable for smaller and medium-sized cables that require ventilation. Commonly used in telecommunications and office buildings, perforated trays offer a balance between support and airflow. The perforations reduce tray weight, making it easier to install while still providing adequate support for cable runs in various commercial and residential settings.
Solid Bottom Cable Tray
Solid bottom cable trays have a completely enclosed bottom that protects cables from dust, debris, and other contaminants. This type is best for environments where cable protection is critical, such as in food processing, pharmaceutical, and chemical industries. While it lacks ventilation features, the solid base ensures maximum cable security, preventing external environmental factors from interfering with the cables and providing a secure environment for sensitive wiring.
Wire Mesh Cable Tray
Wire mesh cable trays are constructed with a mesh framework, making them lightweight, flexible, and easy to install. They are ideal for shorter cable runs and areas that require frequent adjustments or modifications. Often used in commercial buildings, wire mesh trays provide a versatile solution for quick installations and easy cable routing. Their flexibility allows for frequent changes to the cable layout without extensive modifications, making them suitable for dynamic environments.
2. Material Specifications
- Stainless Steel Grades: Typically made from 304 or 316 stainless steel, with 316 offering superior corrosion resistance, particularly in saltwater or chemical environments.
- Thickness: Ranges from 1.2 mm to 3.0 mm, depending on load requirements. Thicker trays are used for supporting heavier cables.
- Finish Options: Generally available in polished, brushed, or electro-polished finishes, enhancing corrosion resistance and appearance.
3. Size Specifications
- Width: Standard widths include 50 mm, 100 mm, 150 mm, 200 mm, 300 mm, 400 mm, 500 mm, and 600 mm. Custom widths can be made for specific applications.
- Height: Common side rail heights are 25 mm, 50 mm, 75 mm, 100 mm, and 150 mm. Higher side rails provide greater strength and load-bearing capacity.
- Length: Typically manufactured in 2-meter or 3-meter standard lengths, though custom lengths may also be available.
4. Load and Span Capabilities
- Load Rating: The load-bearing capacity of stainless steel cable trays varies based on width, thickness, and tray type. Ladder trays usually offer higher load ratings due to their robust structure.
- Span Distance: Cable trays are designed to be supported at intervals (spans) of 1.5 meters, 2 meters, 2.5 meters, or 3 meters. The appropriate span depends on the load rating and application.
5. Accessories
- Fittings: Includes bends (horizontal/vertical), tees, and crosses to guide cables around obstacles or along specific routes.
- Covers: Available in solid or perforated designs, providing added protection for cables from environmental factors.
- Brackets and Support Systems: Wall brackets, floor stands, and ceiling hangers are used to secure cable trays in place based on installation needs.
6. Compliance and Standards
- Stainless steel cable trays are manufactured in accordance with international standards such as NEMA VE 1 (National Electrical Manufacturers Association) and IEC (International Electrotechnical Commission) standards, ensuring consistent quality, performance, and safety.
Stainless steel cable trays are widely used in petrochemical plants, marine environments, food processing facilities, and other demanding industries. These trays offer a long-lasting, corrosion-resistant solution for safely supporting and organizing electrical cables.
Heavy Duty Return Flange Stainless Steel Cable Tray
A Heavy Duty Return Flange Stainless Steel Cable Tray is designed to provide robust support and protection for large cable bundles in demanding industrial environments. Here’s an in-depth look at its features, specifications, and typical applications:
1. Key Features:
- Return Flange Design: The return flange along the edges adds extra rigidity to the tray, preventing bending or flexing under heavy loads. It also helps shield cables from damage by minimizing sharp edges.
- Heavy Duty Construction: Made to support significant weights, this type of tray is ideal for large cable bundles or heavy-duty cables.
- Corrosion Resistance: Constructed from stainless steel, typically grades 304 or 316, offering excellent corrosion resistance, especially in chemically aggressive or high-humidity environments.
2. Material and Finish Options:
- Stainless Steel Grades: Often available in 304 for general applications and 316 for marine or highly corrosive environments.
- Thickness: Generally ranges from 1.5 mm to 3 mm, providing enhanced strength and load-bearing capability.
- Surface Finishes: Electro-polished or brushed finishes are common for increased corrosion resistance and a clean appearance.
3. Size Specifications:
- Width: Standard widths include 100 mm, 150 mm, 200 mm, 300 mm, 400 mm, 450 mm, 500 mm, and up to 600 mm or more, based on application needs.
- Height: Side rail heights typically range from 50 mm to 150 mm for added cable protection.
- Length: Standard lengths are 2 meters or 3 meters, though custom lengths may be available from certain manufacturers.
4. Load and Span Capabilities:
- Load Rating: Designed to support high loads, often rated for heavy-duty applications in industrial settings.
- Span Distance: Typically supported at intervals (spans) of 1.5 meters to 3 meters, with longer spans requiring a higher gauge of material.
5. Installation and Accessories:
- Mounting Options: Can be installed on walls, ceilings, or floors using brackets and support arms suited for heavy-duty loads.
- Accessories: Includes fittings like horizontal and vertical bends, tees, and crosses to manage cable routing in complex installations.
- Covers: Heavy-duty return flange cable trays often come with optional covers to protect cables from dust, water, and other contaminants.
6. Applications:
- Industries: Ideal for use in oil and gas, petrochemical plants, marine environments, power generation, and food processing facilities where durability and corrosion resistance are critical.
- Environmental Conditions: Suitable for indoor and outdoor installations, especially in environments exposed to corrosive substances, moisture, or extreme temperatures.
7. Compliance and Standards:
- Typically manufactured in compliance with NEMA (National Electrical Manufacturers Association) and IEC (International Electrotechnical Commission) standards, ensuring quality, performance, and safety.
A heavy-duty return flange stainless steel cable tray is a reliable and durable solution for managing and protecting cables in high-stress industrial settings, offering exceptional support and longevity.
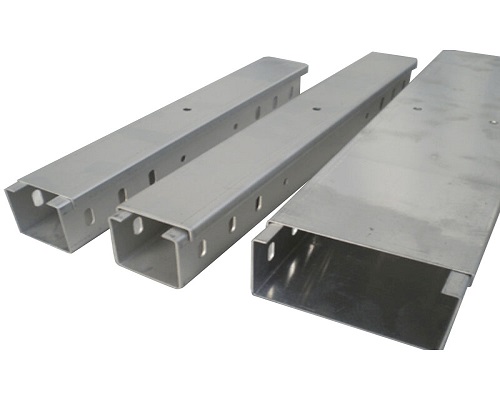
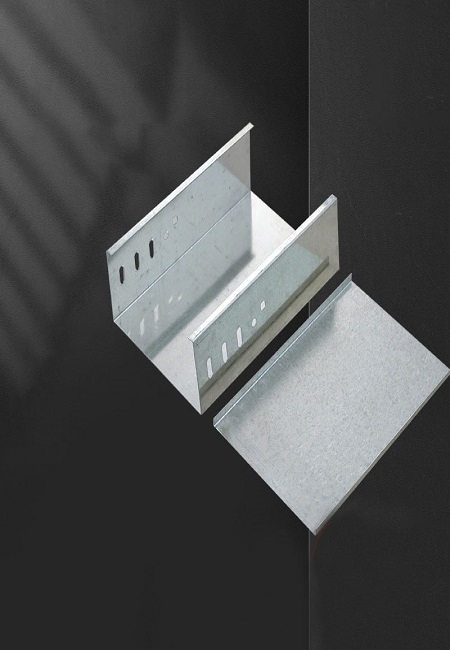
Stainless Steel Cable Tray Wire Basket
A Stainless Steel Cable Tray Wire Basket is designed to support and organize low-voltage, power, and data cables. These trays offer versatility, are lightweight, and are easy to install in commercial and industrial settings. Below are the key features, specifications, and benefits of stainless steel wire basket trays:
1. Key Features
Mesh Design
Constructed with a grid or wire mesh pattern, these trays allow for excellent airflow and heat dissipation. This feature helps prevent cable overheating, especially important for data and telecommunications cables. The open structure enhances ventilation, which is crucial for maintaining cable performance in high-demand environments.
Lightweight yet Strong
Made from stainless steel, these trays are both durable and lightweight. They support moderate loads without adding excessive weight to the installation structure. The combination of strength and lightness makes them ideal for use in a variety of applications without compromising on reliability or stability.
Corrosion Resistant
Stainless steel, particularly grades 304 or 316, ensures that the trays are resistant to corrosion. This makes them suitable for both indoor and outdoor use, even in harsh environments like those exposed to moisture or chemicals. Their corrosion resistance ensures long-lasting durability and reliability in demanding conditions.
Flexible Routing
The wire mesh structure allows for flexible cable routing, which makes installation and modifications easy. Cables can be accessed, added, or removed without the need for extensive disassembly, offering flexibility for future changes in cable layouts or systems.
2. Material Specifications
Stainless Steel Grades
Wire basket trays are typically available in stainless steel grades 304 for general use and 316 for environments with high corrosion risks. These grades ensure that the trays are strong, durable, and able to withstand harsh environmental conditions, making them ideal for both industrial and commercial applications.
Wire Thickness
The wire thickness for these trays typically ranges from 3 mm to 6 mm. This range provides a good balance between lightweight construction and the ability to support moderate to heavy loads, making the trays versatile for various cable management needs.
Surface Finish
Stainless steel wire baskets often come with either a brushed or polished finish. These finishes enhance corrosion resistance while improving the aesthetic appearance of the trays. The finishes also add an extra layer of protection, ensuring the trays withstand environmental elements over time.
3. Size Specifications
Width
Standard widths for stainless steel wire baskets range from 50 mm to 600 mm. Wider options are available for larger cable bundles or more complex installations. These varying widths allow for flexibility in different cable management systems, accommodating diverse project needs.
Depth (Height)
The depth of the trays typically ranges from 25 mm to 100 mm, depending on the required cable capacity. This range allows for a wide selection, ensuring that the trays can handle cables of various sizes and thicknesses while maintaining their structural integrity.
Length
Stainless steel wire baskets are usually available in 2-meter or 3-meter standard sections, with custom lengths available for specialized projects. This flexibility in length allows for easy customization and ensures that the trays fit perfectly within the required space.
4. Load and Span Capabilities
- Load Capacity: The load-bearing capacity depends on the tray width, depth, and wire thickness. Wire basket trays are usually designed for medium to light loads, such as data and communication cables.
- Span Distance: Typical support spans are 1.5 to 2 meters, though heavier gauges may allow for longer spans.
5. Installation and Accessories
- Mounting Options: Wire basket trays can be mounted on walls, ceilings, or under raised floors using brackets, hangers, or clamps. Wall and ceiling mounts are common for overhead installations.
- Accessories: Includes accessories like bends, tees, crosses, dividers, and clips, allowing for flexible routing and organization. Wire baskets are easily cut and reshaped to accommodate unique installation paths.
- Covers: Optional covers are available to protect cables from dust, moisture, and physical damage.
6. Applications
- Industries: Widely used in IT and data centers, telecommunications, commercial buildings, manufacturing facilities, and food processing plants.
- Environmental Suitability: Suitable for use in cleanrooms, chemical plants, and marine environments where corrosion resistance is essential.
7. Compliance and Standards
Stainless steel wire basket trays are manufactured to meet NEMA and IEC standards, ensuring compliance with safety and quality requirements for cable management.
8. Benefits of Using Stainless Steel Wire Basket Cable Trays:
Improved Airflow
The open structure of wire basket trays allows airflow around cables, reducing the risk of overheating. This is particularly beneficial in high-demand environments where cable temperature management is essential for maintaining performance.
Ease of Access
The wire mesh structure ensures that cables are easily accessible for addition, removal, or adjustments. This ease of access minimizes downtime during installation or future system modifications, providing a flexible solution for evolving cable management needs.
Cost-Effective
Stainless steel wire baskets provide a cost-effective solution for cable management. Their durability and adaptability reduce installation time and labor costs, making them an economical choice for businesses looking to streamline their cable management systems without sacrificing performance.
Wire Mesh and Stainless Steel Cable Tray
Wire Mesh and Stainless Steel Cable Trays are both popular cable management solutions, offering different features suited to specific applications. Here’s a comparison to understand their unique advantages, construction, and common uses.
Feature | Wire Mesh Cable Tray | Stainless Steel Cable Tray |
---|---|---|
Material | Stainless steel, galvanized steel, PVC-coated steel | Stainless steel (304 or 316 grades) |
Structure | Open mesh grid structure for ventilation | Solid, perforated, or ladder design for various applications |
Strength | Lightweight and flexible, suitable for lighter loads | Heavy-duty, designed to handle heavy loads |
Ventilation | Excellent airflow, preventing cable overheating | Perforated or ladder trays allow airflow, solid trays offer protection from dust and debris |
Ease of Installation | Easy to install, shape, and modify on-site | Requires more installation effort, but is robust and durable |
Load Capacity | Suitable for lighter cables and smaller setups | Suitable for heavy-duty industrial cables |
Environmental Suitability | Suitable for less demanding environments | Ideal for harsh environments, both indoors and outdoors |
Durability | Corrosion-resistant, especially in stainless steel variants | Highly durable and corrosion-resistant, especially 316 grade stainless steel |
Cable Access & Adjustments | Easy to add or remove cables, flexible layouts | More fixed and rigid, adjustments are less frequent but highly stable |
Common Sizes | Width: 50 mm - 600 mm, Depth: 25 mm - 100 mm | Width: 100 mm - 600 mm, Height: 50 mm - 150 mm |
Standard Length | 2 meters or 3 meters (custom lengths available) | 2 meters or 3 meters (custom lengths available) |
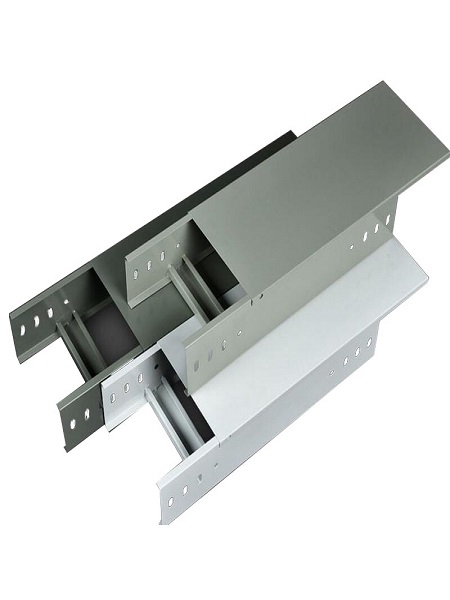
Stainless Steel Cable Tray Heavy Duty
A Heavy Duty Stainless Steel Cable Tray is specifically designed to support and protect large, heavy cable bundles in industrial and harsh environments. These trays are crafted to handle substantial weights and endure challenging conditions, making them ideal for various heavy-duty applications. Here’s an in-depth look at their features, specifications, and usage:
1. Key Features:
- Heavy Duty Construction: Designed to support large loads of cables, these trays are reinforced to prevent bending, flexing, or sagging, even under heavy cable weights.
- High Corrosion Resistance: Made from stainless steel, typically grades 304 or 316, which provides excellent resistance against rust, chemicals, and harsh weather.
- Enhanced Strength and Stability: Often features a thicker gauge material and a return flange design for added structural stability.
- Temperature and Weather Resistant: Withstands a wide range of temperatures and is resistant to extreme weather conditions, making it suitable for outdoor use.
2. Types of Heavy Duty Stainless Steel Cable Trays:
- Ladder Type Tray: Has side rails connected by rungs, offering strong support for large cable loads while allowing for maximum ventilation, which helps prevent overheating.
- Perforated Type Tray: Features a perforated bottom, which provides ventilation while also offering more surface area for cable support. Suitable for heavy-duty applications where some airflow is necessary.
- Solid Bottom Tray: Completely enclosed to protect cables from dust, debris, and physical damage, ideal for sensitive cables in harsh industrial conditions.
3. Material and Finish Options:
- Stainless Steel Grades: Typically available in 304 stainless steel for standard corrosion resistance or 316 stainless steel for environments with higher exposure to chemicals, saltwater, or humidity.
- Thickness: Typically ranges from 1.5 mm to 3.0 mm, with heavier gauges offering greater load support.
- Surface Finishes: Options include electro-polished, brushed, or even powder-coated finishes for enhanced durability and aesthetics.
4. Size Specifications:
- Width: Standard widths range from 100 mm, 150 mm, 200 mm, 300 mm, 400 mm, 450 mm, up to 600 mm or more, depending on the required cable capacity.
- Height (Depth): Side rail heights commonly range from 50 mm to 150 mm to increase load-bearing capacity.
- Length: Generally manufactured in 2-meter or 3-meter sections, although custom lengths can be made based on project specifications.
5. Load and Span Capabilities:
- Load Rating: Heavy-duty stainless steel cable trays are designed to handle high loads, which is essential for large industrial facilities with extensive cable systems.
- Span Distance: These trays are typically supported at spans of 1.5 meters to 3 meters. For longer spans, thicker material and reinforced designs may be required to prevent sagging under heavy loads.
6. Installation and Accessories:
- Mounting Options: Heavy-duty cable trays are mounted using robust brackets and support arms to ensure secure attachment to walls, ceilings, or floors.
- Fittings: Available fittings include bends, tees, crosses, and reducers, allowing cables to be routed efficiently around obstacles.
- Covers: Solid and ventilated covers are available to protect cables from dust, debris, and external environmental factors.
7. Applications:
- Industrial Facilities: Widely used in heavy industries like oil and gas, petrochemical plants, refineries, and power generation facilities where robust support for heavy cables is necessary.
- Marine and Offshore Environments: Stainless steel offers excellent corrosion resistance, making these trays ideal for saltwater-exposed applications like marine vessels and offshore platforms.
- Food and Pharmaceutical Industries: The high sanitary standards of stainless steel make it suitable for environments where cleanliness and corrosion resistance are critical.
8. Compliance and Standards:
- Heavy-duty stainless steel cable trays are manufactured in compliance with standards such as NEMA VE 1 (National Electrical Manufacturers Association) and IEC (International Electrotechnical Commission) standards, ensuring consistent performance, quality, and safety.
Benefits of Heavy Duty Stainless Steel Cable Trays:
- Durability: Withstands heavy loads, making it suitable for large industrial cable runs.
- Corrosion Resistance: Provides long-lasting performance in harsh or corrosive environments.
- High Temperature Resistance: Suitable for environments with high temperatures, making it reliable in manufacturing and power plants.
- Ease of Maintenance: Stainless steel is easy to clean and maintain, reducing long-term maintenance costs.
Heavy-duty stainless steel cable trays offer a durable, corrosion-resistant solution for managing and protecting large-scale cable installations. Their design and material specifications make them ideal for the most demanding environments, ensuring cables are supported safely and effectively.
Thank you for your interest in our products. To receive our pricelist or for any inquiries, please fill out the form below. We will get back to you within 24 hours.
Stainless Steel Wire Mesh Cable Tray
Stainless Steel Wire Mesh Cable Tray systems offer a versatile solution for cable management. These trays are designed with a wire mesh construction, which provides several notable benefits.
Description and Benefits: The Stainless Steel Wire Mesh Cable Tray is made from durable stainless steel wires woven together, forming a sturdy mesh. In comparison, an aluminium cable tray offers similar benefits, including lightweight construction and corrosion resistance, making both options suitable for efficient cable management in various environments.This design allows for excellent ventilation, which helps in preventing cable overheating. Additionally, the open structure of wire mesh trays facilitates easy inspection and maintenance of cables, ensuring that they remain accessible for adjustments or repairs. The stainless steel material used is highly resistant to corrosion, making these trays ideal for use in harsh environments such as chemical processing facilities, food and beverage industries, and outdoor settings.
Comparison with Solid Trays: Compared to solid Stainless Steel Cable Tray options, wire mesh trays offer distinct advantages. While solid trays provide a more enclosed pathway for cables, wire mesh trays excel in environments where ventilation and heat dissipation are critical. Solid trays might be preferred for locations requiring additional protection from physical damage or contaminants, whereas wire mesh trays are ideal for applications where air circulation and ease of access are more crucial. Both types have their own merits depending on the specific needs of the installation, but the wire mesh design of the Stainless Steel Wire Mesh Cable Tray particularly stands out for its practical and functional benefits in dynamic and demanding environments. Additionally, when using cable tray fittings, the versatility and adaptability of wire mesh trays can enhance overall system performance and reliability.
Stainless Steel Cable Tray Price List
When considering the Stainless Steel Cable Tray price list, several factors influence the overall cost. Stainless Steel Cable Tray systems generally fall within specific price ranges that vary according to size, gauge, and customization options. For standard sizes, prices typically range from $10 to $50 per foot, with larger or more specialized trays commanding higher prices. Heavy-duty or custom-made trays can exceed these ranges, often costing $60 or more per foot, depending on their specifications.
Factors Affecting Price include the quality of the stainless steel used, which can vary between grades such as 304 and 316, with 316 being more expensive due to its superior corrosion resistance. Additional features like integrated covers, custom lengths, and specific load-bearing capacities also impact the final price. Moreover, order volume can play a significant role; bulk purchases may receive discounts, reducing the per-unit cost. Understanding these elements helps in budgeting for Stainless Steel Cable Tray systems that meet both project requirements and financial constraints.
Stainless steel cable trays are essential components in electrical installations, offering durability and corrosion resistance. Their prices vary based on factors such as material grade, dimensions, design, and manufacturer. Below is an overview of typical pricing:
1. Material Grade:
- 304 Stainless Steel: Commonly used for general applications; moderately priced.
- 316 Stainless Steel: Offers enhanced corrosion resistance, suitable for harsh environments; generally more expensive.
2. Dimensions:
- Width: Standard widths range from 50 mm to 600 mm.
- Height: Common heights are between 25 mm and 150 mm.
- Length: Typically available in 2-meter or 3-meter sections.
3. Design Types:
- Perforated Cable Trays: Feature a flat, perforated base for ventilation.
- Ladder Type Cable Trays: Consist of side rails connected by rungs, resembling a ladder.
- Wire Mesh Cable Trays: Constructed from a mesh structure, offering flexibility and ease of installation.
Approximate Price Ranges:
- Perforated Cable Trays: Prices range from $0.90 to $9.90 per piece, depending on size and material.
- Ladder Type Cable Trays: Typically priced between $0.50 and $9.90 per piece.
- Wire Mesh Cable Trays: Generally range from $0.50 to $5.00 per meter.
Additional Considerations:
- Surface Finish: Options like electro-galvanized, hot-dip galvanized, or powder-coated finishes can influence the price.
- Accessories: Fittings such as bends, tees, and covers are usually sold separately and add to the overall cost.
- Quantity: Bulk purchases often qualify for discounts.
Note: Prices are subject to change based on market conditions, manufacturer pricing, and regional factors. For the most accurate and up-to-date pricing, it’s advisable to contact suppliers directly or visit their official websites.
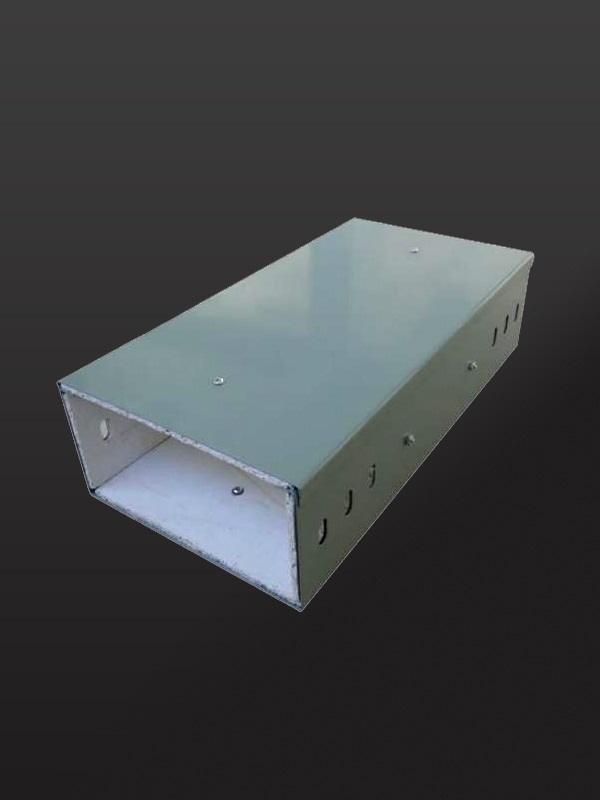
Fiberglass Stainless Steel Cable Tray Supply
At Hebei Ganglong Technology Co., Ltd., we specialize in supplying high-quality fiberglass stainless steel cable trays for efficient cable management. Our trays combine the best features of fiberglass and stainless steel, ensuring strength, corrosion resistance, and long-lasting performance. We provide reliable solutions to meet various industrial, commercial, and residential needs, making us a trusted partner in cable management.
Our Products & Services
Wide Range of Products
We offer a variety of fiberglass stainless steel cable trays in different sizes, styles, and configurations. Our range includes heavy-duty trays for industrial environments and lighter systems for commercial buildings. This diversity allows us to cater to a wide range of cable management requirements, from power distribution to data transmission.
Reliable & On-Time Delivery
Our optimized supply chain ensures quick and reliable delivery. Whether you are handling large-scale infrastructure projects or smaller installations, we guarantee timely fulfillment. We understand the importance of keeping your projects on track and are committed to meeting delivery schedules for your cable tray needs.
High-Quality Standards
All our cable trays are manufactured to meet industry standards using top-grade fiberglass and stainless steel. Our trays are durable, corrosion-resistant, and able to withstand harsh environments. We rigorously test each tray to ensure it meets or exceeds performance, safety, and durability requirements, providing reliable solutions for your cable management needs.
Customized Solutions
We offer tailored solutions to meet your specific project needs. From custom dimensions and finishes to specialized configurations, we collaborate closely with clients to ensure the trays are the right fit. Our team ensures that every product is designed to meet the unique requirements of your installation.
Global Reach
With over 76,000 miles of cable tray installations globally, we have the expertise to handle international shipping and delivery. We ensure that your trays arrive on time and in full, regardless of your project’s location. Our strong reputation for quality and reliable delivery spans across continents.
Competitive Pricing
We provide cost-effective solutions without compromising on quality. As a direct supplier of fiberglass stainless steel cable trays, we offer competitive prices, ensuring that you receive the best value while maintaining high performance and safety standards for your cable management system.
Industries We Serve
Our fiberglass stainless steel cable trays are widely used across various industries, including:
- Industrial and Manufacturing Facilities
Providing reliable cable management for power distribution and machinery wiring in factories and plants. Data Centers
Organizing and protecting high-speed data cables for uninterrupted communication and data transfer.- Oil and Gas
Supplying corrosion-resistant cable trays for offshore and onshore facilities in harsh environments. Commercial Buildings and Infrastructure
Offering clean, organized cable management solutions for offices, hospitals, shopping malls, and public buildings.
FAQs about Stainless Steel Cable Tray
What is the life expectancy of cable tray?
What are the 3 main types of cable tray?
Ladder Cable Tray: This type features two side rails connected by rungs, resembling a ladder. It offers excellent ventilation, making it ideal for heavy-duty cables that generate heat. It's commonly used in industrial settings.
Solid Bottom Cable Tray: This type has a flat, solid base with side walls. It provides maximum protection for cables but offers limited ventilation. It is used in environments where cables need to be shielded from external elements or where protection from falling debris is essential.
Perforated Cable Tray: This type has a flat base with small holes or slots (perforations) throughout. It offers a balance between ventilation and protection, allowing some airflow while providing better support for cables than ladder trays. It is widely used in commercial and industrial installations.
What is the material grade of cable tray?
Mild Steel (Pre-galvanized or Hot-dip Galvanized): Used for general-purpose applications, providing good corrosion resistance.
Stainless Steel (304, 316): Used in corrosive environments, such as chemical plants or offshore installations. Grade 316 stainless steel offers higher corrosion resistance than 304.
Aluminum: Lightweight and corrosion-resistant, often used in environments where weight is a concern or where additional corrosion resistance is needed.
Fiberglass Reinforced Plastic (FRP): Non-metallic and resistant to corrosion, often used in harsh chemical environments or where non-conductivity is required.
The material grade is chosen based on factors like load-bearing requirements, environmental conditions, and cost.
What is another name for a cable tray?
What is the standard for cable tray?
What is the difference between cable tray and raceway?
Design and Structure: A cable tray is an open or semi-open structure that supports and organizes cables, allowing for easy access and ventilation. A raceway is a fully enclosed conduit or channel that protects cables from environmental factors and physical damage.
Accessibility: Cable trays provide easy access for cable installation, maintenance, and upgrades. Raceways, being enclosed, require more effort to access cables, making changes and maintenance more difficult.
Applications: Cable trays are used in environments where ventilation, flexibility, and easy access to cables are priorities. Raceways are used where maximum protection for cables is required, such as in hazardous locations or where cables need to be concealed.
Ventilation: Cable trays allow for natural ventilation around the cables, reducing the risk of overheating. Raceways, being enclosed, offer limited or no ventilation.
When to use wire mesh cable tray?
Data Centers: For managing high volumes of data cables, where flexibility and easy access are critical.
Telecommunications: Ideal for installations with frequent cable changes, additions, or rerouting.
Lightweight Cables: Suitable for supporting lighter cables that do not require the heavy-duty support of a solid or ladder tray.
Ventilation Needs: In environments where heat dissipation is important, such as around IT equipment.
Flexibility: When the installation requires a flexible, easy-to-configure cable management solution.
What is the difference between a perforated cable tray and a channel cable tray?
Design:
Perforated Cable Tray: Has a flat base with holes or slots (perforations) along the length, allowing for ventilation and drainage. It provides a balance between protecting cables and allowing air circulation.
Channel Cable Tray: A U-shaped or C-shaped tray with solid sides and bottom, offering full support and protection for the cables but with limited or no ventilation.
Ventilation:
Perforated Cable Tray: Allows airflow and reduces the risk of cable overheating.
Channel Cable Tray: Offers minimal ventilation, making it suitable for applications where cables need to be fully protected.
Applications:
Perforated Cable Tray: Used in environments where both support and ventilation are needed, such as in commercial buildings.
Channel Cable Tray: Used where cables require more protection from environmental factors but don’t need as much ventilation.
What is the difference between cable duct and cable tray?
Design and Structure:
Cable Duct: An enclosed channel, usually made of plastic or metal, that routes cables along walls, ceilings, or floors. It fully encloses the cables, protecting them from dust, moisture, and physical damage.
Cable Tray: An open or semi-open system that supports cables along a route. It allows for ventilation and easy access to the cables.
Accessibility:
Cable Duct: Offers less accessibility for cable maintenance and upgrades because the cables are enclosed.
Cable Tray: Provides easy access for adding, removing, or maintaining cables.
Applications:
Cable Duct: Used where cables need to be protected from environmental factors or hidden for aesthetic reasons.
Cable Tray: Used in industrial or commercial settings where large numbers of cables need to be supported and where ventilation and accessibility are important.
How do you keep stainless steel cable from rusting?
Use High-Quality Stainless Steel: Ensure that the cable is made from a high-grade stainless steel, such as 316, which has better corrosion resistance than lower grades.
Apply a Protective Coating: Use a marine-grade sealant, wax, or corrosion inhibitor specifically designed for stainless steel to create a protective barrier.
Regular Cleaning: Clean the cable regularly with water and mild detergent to remove any contaminants, such as salt, that can lead to corrosion.
Avoid Exposure to Harsh Environments: Minimize exposure to highly corrosive environments, such as salty or acidic conditions, or use a protective cover.
Dry the Cable: Always dry the cable after it has been exposed to water to prevent moisture buildup, which can lead to rusting.
How do you seal stainless steel so it doesn't rust?
Use a Stainless Steel Sealant: Apply a sealant or clear coat designed for stainless steel. These products create a thin, protective layer that prevents moisture and air from reaching the metal surface.
Wax or Polish: Regularly applying a wax or stainless steel polish can help seal the surface and provide an additional barrier against corrosion.
Passivation: This chemical process removes surface contaminants and enhances the natural oxide layer of the stainless steel, improving its resistance to rust.
What can l spray stainless steel with to keep from rusting?
Corrosion Inhibitor: Products like Boeshield T-9 or similar corrosion inhibitors designed for stainless steel can be sprayed on to protect against rust.
Stainless Steel Cleaner with Protectant: Some stainless steel cleaners include a protective component that can be sprayed on to clean and protect the metal.
WD-40: While not specifically for stainless steel, WD-40 can provide temporary protection by displacing moisture and creating a barrier against rust.
Does wd40 prevent rust on stainless steel?
Why does my stainless steel keep rusting?
Exposure to Chlorides: Salt, chlorine, and other chlorides can damage the protective oxide layer on stainless steel, leading to rust.
Low-Grade Stainless Steel: Lower grades, such as 304, are more prone to rusting, especially in harsh environments.
Surface Contamination: If iron particles or other contaminants come into contact with the stainless steel, they can lead to rust spots.
Lack of Maintenance: Without regular cleaning, contaminants can accumulate on the surface, leading to corrosion over time.
Improper Installation: Improper handling, such as using non-stainless steel tools or fasteners, can introduce contaminants that cause rusting.
How do you make stainless steel rust proof?
Passivation: Treat the stainless steel with a passivation solution to remove surface contaminants and enhance the oxide layer that protects against rust.
Apply Protective Coatings: Use a high-quality, clear protective coating designed for stainless steel to create a barrier against moisture and contaminants.
Regular Maintenance: Clean the stainless steel regularly with appropriate cleaners to remove contaminants and maintain its protective oxide layer.
Choose the Right Grade: Use high-grade stainless steel (e.g., 316) in environments that are more prone to corrosion.
What prevents corrosion in stainless steel?
Chromium Content: The chromium in stainless steel forms a passive oxide layer on the surface that protects against corrosion.
Regular Cleaning: Removing dirt, salt, and other contaminants helps maintain the protective oxide layer.
Use of Protective Coatings: Applying sealants, waxes, or corrosion inhibitors adds an extra layer of protection.
Proper Material Selection: Choosing the right grade of stainless steel for the specific environment (e.g., 316 for marine environments) helps prevent corrosion.
What kills rust on stainless steel?
Use a Stainless Steel Cleaner: Products specifically designed for stainless steel can remove rust without damaging the surface.
Baking Soda Paste: Mix baking soda with water to form a paste, apply it to the rust, and gently scrub with a soft brush or cloth.
Vinegar: Soak a cloth in vinegar and place it on the rust spot for a few minutes, then scrub gently. The acetic acid in vinegar helps dissolve rust.
Oxalic Acid Cleaners: These are more aggressive and effective for tougher rust spots, but they should be used with caution and according to the manufacturer’s instructions.
How do you weatherproof stainless steel?
Apply a Protective Coating: Use a weather-resistant coating or sealant designed for stainless steel to protect it from the elements.
Regular Maintenance: Clean the stainless steel regularly to remove any contaminants that could lead to corrosion.
Use the Right Grade: For outdoor or harsh environments, use stainless steel grades like 316 that are more resistant to corrosion.
Keep Dry: Ensure that the stainless steel is dried after exposure to water to prevent moisture-related corrosion.
How do you keep stainless steel from tarnishing?
Regular Cleaning: Clean the stainless steel regularly with a mild detergent or a cleaner designed for stainless steel to remove any contaminants that can cause tarnishing.
Apply a Protective Polish: Use a stainless steel polish that creates a protective layer and enhances the metal’s natural shine.
Avoid Harsh Chemicals: Do not use abrasive cleaners or bleach, as these can damage the surface and lead to tarnishing.
Store Properly: If the stainless steel item is not in use, store it in a dry, cool place to avoid exposure to humidity and contaminants.
What procedure is used to protect a stainless steel cable from corrosion?
Apply a Protective Coating: Coat the cable with a corrosion-resistant sealant or wax designed for stainless steel.
Passivation: Use the passivation process to remove surface contaminants and enhance the natural oxide layer.
Use a Corrosion Inhibitor: Regularly apply a corrosion inhibitor spray to the cable, especially if it is exposed to harsh environments.
Regular Inspection and Cleaning: Inspect the cable regularly for signs of corrosion and clean it to remove any contaminants that could lead to rust.
Choose the Right Grade: Use a stainless steel cable with a higher corrosion resistance grade (e.g., 316) if the cable is used in a corrosive environment.
How do you keep stainless steel from discoloring?
Regular Cleaning: Clean the stainless steel frequently with a mild cleaner to remove contaminants that could cause discoloration.
Avoid High Temperatures: Prolonged exposure to high heat can cause discoloration; avoid overheating stainless steel, especially in kitchenware.
Use a Polish or Protectant: Apply a stainless steel polish that creates a protective layer, preventing discoloration.
Proper Handling: Avoid contact with harsh chemicals, such as bleach or chloride-based cleaners, which can cause discoloration.
How do you keep stainless steel pans from rusting?
Dry Thoroughly: Always dry stainless steel pans immediately after washing to prevent moisture from causing rust.
Season the Pan: Apply a thin layer of oil after washing and drying to create a protective barrier against moisture.
Avoid Harsh Detergents: Use mild detergents and avoid harsh cleaning agents that can strip the protective layer of the stainless steel.
Store Properly: Store pans in a dry environment, ideally hanging them to prevent moisture buildup.
Which cable tray is best?
Ladder Cable Tray: Best for heavy-duty industrial applications where ventilation is crucial. It supports large, heavy cables and is suitable for long spans.
Perforated Cable Tray: Ideal for applications where both ventilation and some level of protection are needed. It is commonly used in commercial and light industrial settings.
Solid Bottom Cable Tray: Best for environments where maximum protection for cables is required, such as in environments with falling debris or where the cables need to be shielded from dust and other contaminants.
How can l tell the quality of my cable tray?
Material Grade: Check if the cable tray is made from high-quality materials, such as stainless steel (316 for corrosive environments) or aluminum.
Coating: Ensure that the coating (e.g., hot-dip galvanization or powder coating) is evenly applied and adheres well to the surface, providing corrosion resistance.
Structural Integrity: Inspect for uniform thickness, smooth edges, and proper welds or joints. High-quality trays have consistent construction without visible defects.
Load Capacity: Verify the tray’s load-bearing capacity according to manufacturer specifications. A high-quality tray should meet or exceed industry standards.
Certification: Look for compliance with relevant standards, such as NEMA VE 1, which indicates the tray has been tested for quality and performance.
What is the most widely used coating for cable tray?
Electroplating (Zinc Coating): Used for less corrosive environments, offering a thinner layer of protection.
Powder Coating: Provides additional protection and can be applied in different colors, often used in indoor settings for aesthetic purposes.
PVC Coating: Adds a layer of chemical resistance, often used in environments with harsh chemicals.
What are the disadvantages of a solid bottom cable tray?
Poor Ventilation: Solid bottom trays do not allow airflow around the cables, which can lead to overheating, especially with high-current cables.
Heavier Weight: They are heavier than other types of trays, making them more challenging to install and requiring stronger support structures.
Limited Access: Adding or removing cables is more difficult compared to open or perforated trays since the cables are enclosed.
Moisture Accumulation: In humid or wet environments, moisture can accumulate inside the tray, leading to potential corrosion or damage to the cables.
Which cable tray material is best for corrosive environments?
How often should you ground a cable tray?
Is MC cable rated for cable tray?
What is the best metal cable?
Copper: Best for electrical conductivity, commonly used in power cables, data cables, and communication cables. It offers excellent flexibility and resistance to corrosion.
Aluminum: Used in large-scale power distribution due to its lighter weight and lower cost compared to copper. However, it is less conductive and more prone to oxidation.
Stainless Steel: Used in environments requiring mechanical strength and corrosion resistance, such as in control and instrumentation cables in harsh environments.
How often should l support a cable tray?
What makes a cable tray rated?
Load Capacity: The maximum weight the tray can support, determined by its design, material, and construction.
Environmental Suitability: The tray’s ability to withstand specific environmental conditions, such as exposure to chemicals, temperature extremes, or moisture.
Compliance with Standards: The tray meets relevant industry standards, such as NEMA VE 1, which certifies its performance, safety, and durability.
Fire Resistance: The tray’s ability to maintain integrity during a fire, often determined by its material and any fire-resistant coatings applied.
What is the difference between a cable ladder and a cable tray?
Design:
Cable Ladder: Consists of two side rails connected by rungs, creating an open ladder-like structure. It allows maximum ventilation and is ideal for heavy-duty cables.
Cable Tray: A more enclosed structure, which can be solid-bottom, perforated, or wire mesh. It provides continuous support and offers varying degrees of protection and ventilation.
Applications:
Cable Ladder: Used in industrial settings where heavy cables need support over long distances and ventilation is critical.
Cable Tray: Used in a wider range of environments, including commercial and light industrial, where different levels of cable protection and support are required.
Strength and Load Capacity:
Cable Ladder: Typically has a higher load capacity, suitable for heavier and larger cables.
Cable Tray: Supports lighter loads, with options for more enclosed cable management.
Which cables should not be in the same tray?
Power and Data Cables: High-voltage power cables and data or communication cables should not be placed together to avoid electromagnetic interference (EMI), which can disrupt signal integrity.
High-Voltage and Low-Voltage Cables: Mixing high-voltage and low-voltage cables can cause safety hazards and may require physical separation or barriers.
Incompatible Insulations: Cables with different insulation types that might react negatively to each other (e.g., PVC and certain rubbers) should not be placed together.
Class 1, Class 2, and Class 3 Circuits: NEC regulations often require these different circuit classes to be separated to avoid interference and ensure safety.
What is the difference between cable tray and channel tray?
Design:
Cable Tray: A broader category that includes various types such as ladder, perforated, and solid-bottom trays. It is typically wider and can support multiple cables along a route.
Channel Tray: A U-shaped or C-shaped tray that is narrower and often used for supporting single or small groups of cables. It offers more protection than open trays but less ventilation.
Applications:
Cable Tray: Used for organizing and supporting a large number of cables over longer distances in industrial and commercial settings.
Channel Tray: Used for smaller cable runs or where additional protection is needed, often in control rooms or smaller installations.
Is cable tray cheaper than conduit?
Can l run thhn in cable tray?
Why is steel conduit so expensive?
Material Costs: Steel is a durable and strong material, but it's more expensive to produce than other materials like PVC.
Manufacturing Process: The process of forming, galvanizing, and threading steel conduit adds to its cost.
Durability and Strength: Steel conduits are highly resistant to physical damage, fire, and corrosion, making them more costly but also more reliable in demanding environments.
Labor Costs: Installation of steel conduit is labor-intensive, requiring precise cutting, threading, and bending, which further increases overall costs.
What is the difference between cable raceway and cable tray?
Design:
Cable Raceway: A fully enclosed channel that protects cables from environmental factors and physical damage. It is typically used in indoor applications where aesthetics and protection are priorities.
Cable Tray: An open or semi-open structure that supports and organizes cables, allowing for easy access, maintenance, and ventilation.
Applications:
Cable Raceway: Used in environments where cables need to be concealed and fully protected, such as in office buildings or data centers.
Cable Tray: Used in industrial and commercial settings where a large number of cables need to be supported and where accessibility and flexibility are important.
Accessibility:
Cable Raceway: Offers limited accessibility since it is enclosed, making cable modifications more challenging.
Cable Tray: Provides easy access to cables for maintenance and upgrades.
Can you run cable tray wire in conduit?
Is metal or PVC conduit cheaper?
What are the disadvantages of solid bottom cable tray?
Poor Ventilation: Solid bottom trays do not allow for airflow around the cables, which can lead to overheating, especially with high-current cables.
Heavier Weight: They are heavier than other tray types, making them more challenging to install and requiring stronger support structures.
Limited Access: Adding, removing, or modifying cables is more difficult compared to open trays since the cables are enclosed.
Moisture Accumulation: In humid or wet environments, moisture can accumulate inside the tray, potentially leading to corrosion or damage to the cables.
What is the difference between cable trunking and cable tray?
Design:
Cable Trunking: A fully enclosed rectangular or square channel used to route and protect cables along walls or ceilings. It keeps cables hidden and protected from physical damage.
Cable Tray: An open or semi-open structure used to support and organize cables over longer distances, allowing for ventilation and easy access.
Applications:
Cable Trunking: Used where cables need to be concealed for aesthetic reasons or protection, often in commercial or residential buildings.
Cable Tray: Used in industrial or commercial settings where large numbers of cables need support and where accessibility and flexibility are important.
Accessibility:
Cable Trunking: Offers less accessibility for cable maintenance and upgrades, as the cables are enclosed.
Cable Tray: Provides easier access to cables for maintenance and upgrades.
What is the difference between cable tray and wireway?
Design:
Cable Tray: An open or semi-open system used to support and organize multiple cables along a route, allowing for ventilation and easy access.
Wireway: An enclosed rectangular channel, often with a removable cover, used to protect and route smaller numbers of cables. It provides more protection than a cable tray.
Applications:
Cable Tray: Used in industrial and commercial settings where large numbers of cables need to be supported over long distances.
Wireway: Used in applications where cables need protection from physical damage, but not as much as a conduit would provide, often in control rooms or smaller installations.
Accessibility:
Cable Tray: Offers easy access for maintenance and cable modifications.
Wireway: Provides access through removable covers, but it is more enclosed than a cable tray.
Is tray cable rated for direct burial?
Which type of cable tray is best?
Ladder Cable Tray: Best for heavy-duty applications requiring maximum ventilation and support over long distances.
Perforated Cable Tray: Best for environments where both ventilation and cable protection are needed, commonly used in commercial and light industrial settings.
Solid Bottom Cable Tray: Best for environments requiring maximum protection for cables, such as areas with falling debris or where cables need to be shielded from dust and other contaminants.
Thank you for your interest in our products. To receive our pricelist or for any inquiries, please fill out the form below. We will get back to you within 24 hours.