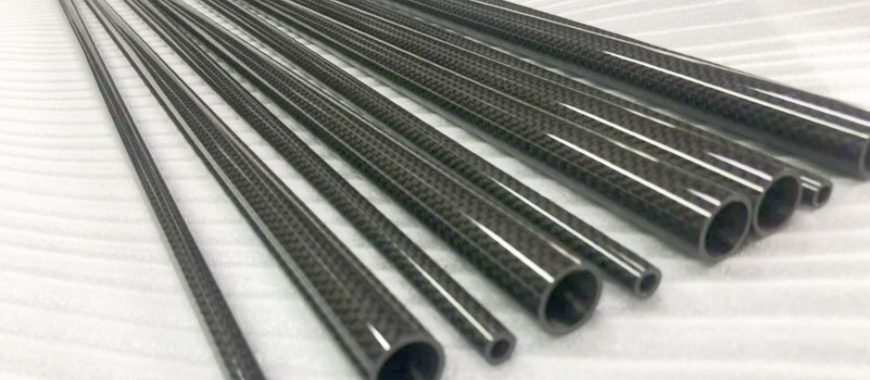
What is a tapered fiberglass tube and why are sizes important? Tapered fiberglass tubes, which are a type of fiberglass tubes, come in both standard and custom sizes, offering flexibility for various industries. These tubes are designed with a gradual change in diameter, which affects their strength, weight, and usability in different applications. The size of a tapered fiberglass tube is crucial because it determines the tube’s performance, particularly in load-bearing applications and areas requiring precise fits. To ensure the right specifications are met, working directly with a fiberglass tube factory is essential, as they can provide custom sizes tailored to specific needs. Tapered fiberglass tubes for a variety of industrial applications have a continuous taper and are stiff, strong, and lightweight. Industry-specific needs, such as aerospace or construction, may demand different dimensions, making it essential to choose the right size for optimal performance.
Types of Tapered Fiberglass Tube
Tapered fiberglass tubes are cylindrical structures made from a composite material consisting of fiberglass and resin. They are designed with a gradual reduction in diameter from one end to the other, making them particularly useful in various engineering and industrial applications where strength, durability, and a reduction in weight are essential. Below is a detailed description of different types of tapered fiberglass tubes:
Standard Tapered Fiberglass Tubes
These are the most common type of tapered fiberglass tubes. They are manufactured by layering fiberglass fabrics or mats impregnated with resin in a mold, which is then cured under heat and pressure. The tube’s diameter tapers from the base to the top in a smooth, consistent manner. These tubes are typically used in industries such as construction, sports equipment, and marine applications.
- Applications: Fishing rods, flagpoles, fiberglass antenna tubes, structural supports.
- Characteristics: High tensile strength, corrosion resistance, lightweight, and customizable in terms of diameter and length.
Conical Fiberglass Tubes
A specific type of tapered tube with a more defined conical shape, where the diameter decreases uniformly along the length of the tube, creating a sharp, conical end. This design is typically used when there is a need for precise flow control or to create an aerodynamic shape.
- Applications: Aircraft components, wind turbine blades, fluid transport systems, and rocket nozzles.
- Characteristics: Highly efficient in directing airflow or fluid, provides strength with reduced material usage.
Fiberglass Pultruded Tubes
These tapered tubes are manufactured through a process called pultrusion, where fiberglass strands are pulled through a die and impregnated with resin. The tapering effect can be created by adjusting the die or by using variable resin content. Pultruded tubes offer superior mechanical properties, particularly in terms of bending strength and resistance to impact.
- Applications: Bridge supports, scaffolding, structural beams.
- Characteristics: Excellent for long, continuous lengths, high stiffness-to-weight ratio, and resistance to environmental factors like UV light and moisture.
Fiberglass Rolled Tubes
These tubes are made by rolling fiberglass cloth or mat around a mandrel and then curing it in an oven. The tapering effect is achieved by gradually reducing the diameter of the mandrel as the tube is formed. This type of tube can be used in custom shapes or sizes and is often used in specialized applications.
- Applications: Custom industrial parts, pipes for fluid flow, lightweight structural components.
- Characteristics: Flexible for custom sizes, cost-effective for small runs, and can be adapted for a variety of applications.
Fiberglass Laminated Tubes
Laminated fiberglass tubes are constructed by layering sheets of fiberglass fabric or cloth, which are then impregnated with resin and bonded together to form the tube. These tubes can have a tapered design, with the number and thickness of layers varying along the length of the tube. The tapering can be achieved by using different layer thicknesses at different sections of the tube.
- Applications: Marine applications, power poles, industrial support structures.
- Characteristics: High strength-to-weight ratio, ability to withstand high-stress environments, customizable for specific applications.
Carbon-Fiber Reinforced Fiberglass Tubes
These are hybrid tubes made from both fiberglass and carbon fiber. The tapered design is typically created using pultrusion or molding techniques, with a higher concentration of carbon fiber at the narrow end for increased stiffness and performance.
- Applications: Aerospace, automotive, high-performance sporting equipment.
- Characteristics: Superior strength, lightweight, high stiffness, and resistance to thermal expansion.
Fiberglass Spiral-Wound Tubes
These tubes are made by winding fiberglass filaments around a central mandrel in a spiral pattern. The taper is formed by adjusting the angle of the winding or the spacing between layers. This method allows for high levels of control over the fiberglass tube strength and properties along the length.
- Applications: Pipes for chemicals, transportation systems, structural components for harsh environments.
- Characteristics: High resistance to chemicals and corrosion, suitable for high-pressure applications, customizable in diameter and taper degree.
Tapered fiberglass tubes come in various forms and manufacturing techniques, each suited for different industrial, construction, and technological applications. Their versatility, strength, and lightweight nature make them a valuable component in many engineering projects.
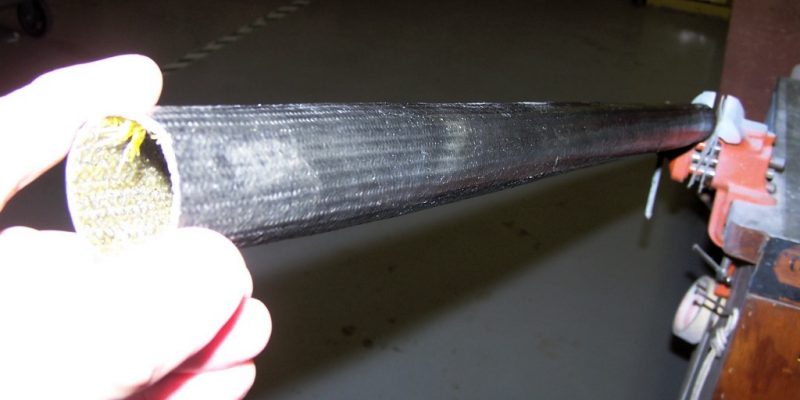
Shapes of Tapered Fiberglass Tube
Tapered fiberglass tubes can be shaped in several ways to meet specific design requirements. Here are some common shapes:
Conical Shape
- The most common taper, where the tube gradually narrows from a larger diameter at the base to a smaller one at the tip. This shape is often used for applications requiring smooth aerodynamic flow or fluid control.
- Applications: Rocket nozzles, antenna masts, wind turbine blades.
Straight Tapered
- A uniform, gradual reduction in diameter along the length of the tube, maintaining a consistent taper from one end to the other.
- Applications: Flagpoles, fishing rods, structural components.
Reverse Tapered
- In this design, the tube starts with a smaller diameter and gradually widens toward the base. It is less common but can be used for specific design purposes where an increasing diameter at the base is needed.
- Applications: Certain support structures, pipes for fluid flow that need wider openings at the bottom.
Stepped Taper
- This type of taper features distinct, stepped sections where the tube transitions between multiple diameters rather than having a smooth, continuous reduction. This shape can offer mechanical advantages in load distribution.
- Applications: Transmission towers, supports, and various industrial uses.
Bell-Shaped Taper
- A variation of the conical taper with a flared end, often used when a larger opening is needed for coupling or fitting purposes. The opening can expand outward in a more pronounced bell shape.
- Applications: Flanged components, ducts, and exhaust pipes.
Elliptical Taper
- The tube tapers from a circular to an elliptical cross-section as it narrows. This is a more specialized form used in cases where aerodynamic efficiency or specific load-bearing characteristics are required.
- Applications: Aircraft structures, custom aerospace components.
Variable Taper
- A tube with a taper that changes along its length, with the rate of reduction in diameter not being uniform. This is typically achieved by varying the material thickness or layering technique, offering increased customization for structural or load-bearing purposes.
- Applications: Specialized engineering parts, custom vehicle components.
Each shape is designed to optimize performance for particular applications, whether for mechanical strength, aerodynamic efficiency, or structural integrity.
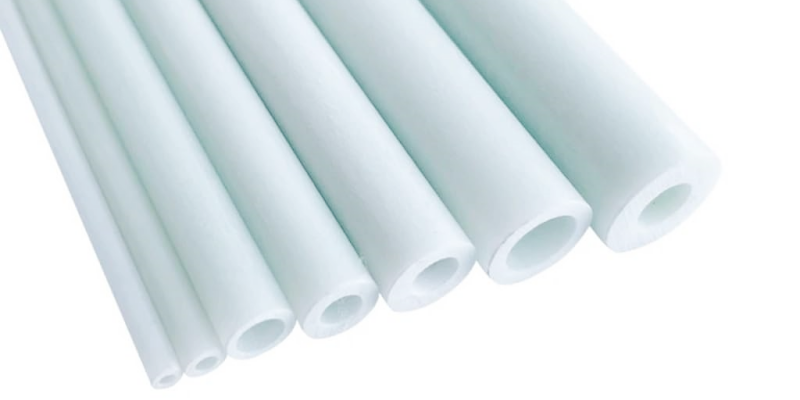
Tapered Fiberglass Tube: Max Temperature
The maximum temperature a tapered fiberglass tube can withstand depends on several factors, including the type of resin used in the composite, the fiberglass reinforcement, and the manufacturing process. Below are general temperature ranges based on common resin systems used for fiberglass tubes:
Polyester Resin
- Maximum Temperature: ~ 120°C (248°F)
- Polyester resin is commonly used for fiberglass products due to its affordability and ease of production. However, it has relatively low thermal resistance, and fiberglass tubes made with polyester resin are generally not suitable for high-temperature applications.
Vinyl Ester Resin
- Maximum Temperature: ~ 150°C (302°F)
- Vinyl ester resins provide better temperature resistance and are more durable than polyester. They are often used in environments that experience higher temperatures or exposure to chemicals.
Epoxy Resin
- Maximum Temperature: ~ 150°C to 200°C (302°F to 392°F)
- Epoxy resin offers excellent thermal resistance, chemical stability, and mechanical properties. Fiberglass tubes made with epoxy resin can typically withstand higher temperatures compared to polyester or vinyl ester tubes, making them suitable for more demanding applications.
Phenolic Resin
- Maximum Temperature: ~ 200°C to 250°C (392°F to 482°F)
- Phenolic resins are used in high-temperature applications because they have excellent heat resistance and can endure long-term exposure to elevated temperatures. Fiberglass tubes made with phenolic resins are suitable for industrial and aerospace applications.
High-Performance Resins (e.g., BMI or PEEK)
- Maximum Temperature: ~ 250°C to 350°C (482°F to 662°F)
- High-performance resins like Bismaleimide (BMI) or Polyetheretherketone (PEEK) are used in specialized high-temperature applications, such as aerospace and automotive industries. These resins allow fiberglass tubes to operate effectively in environments with extreme temperatures.
Temperature Resistance Considerations:
- Resin Choice: The resin is the most significant factor in determining the maximum temperature of a fiberglass tube. As mentioned, epoxy and phenolic resins provide higher heat resistance than polyester and vinyl ester resins.
- Fiberglass Material: Standard fiberglass has a melting point around 1000°C to 1200°C (1832°F to 2192°F), but the resin limits the overall temperature tolerance.
- Continuous vs. Intermittent Exposure: The listed maximum temperatures are typically for continuous exposure. Intermittent or short-term exposure to higher temperatures might be possible but could affect the material’s long-term durability.
- Thermal Cycling: Repeated heating and cooling cycles can affect the performance of the tube, especially if the resin used has low thermal shock resistance.
The maximum temperature for a tapered fiberglass tube depends on the resin, but in general:
- Polyester: Up to ~120°C (248°F)
- Vinyl Ester: Up to ~150°C (302°F)
- Epoxy: Up to ~150°C to 200°C (302°F to 392°F)
- Phenolic: Up to ~200°C to 250°C (392°F to 482°F)
- High-Performance Resins (BMI, PEEK): Up to ~250°C to 350°C (482°F to 662°F)
For high-temperature applications, selecting a fiberglass tube with an appropriate resin system is essential for ensuring the tube’s durability and performance under heat.
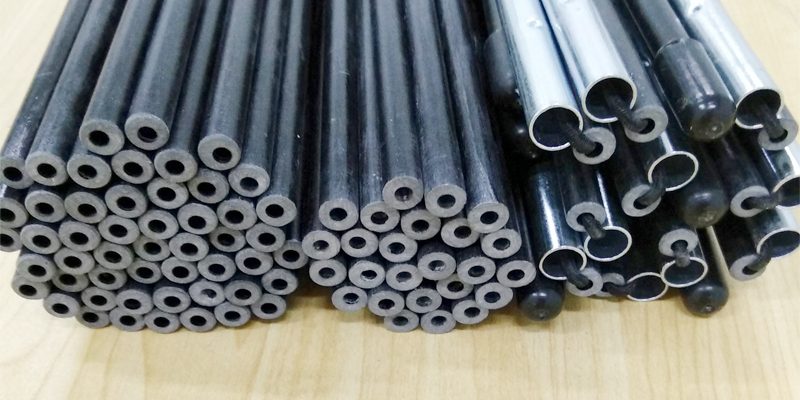
Tapered Fiberglass Tube for Sale
Tapered fiberglass tubes refer to a specialized type of tube that is crafted using fiberglass materials and features a tapered design. This design allows the tube to have one end that is wider than the other, providing unique structural and mechanical benefits. Tapered fiberglass tubes are highly versatile and used across many industries due to their lightweight nature, strength, and resistance to environmental factors. They are often used in construction, marine, and industrial applications, making them a preferred choice for professionals looking for high-performance materials.
These tubes are often preferred over traditional materials like metal or wood because they provide excellent durability, corrosion resistance, and flexibility. Additionally, tapered fiberglass tubes offer the advantage of being easy to handle and install, even in complex projects. Given their resistance to chemicals, moisture, and extreme weather conditions, tapered fiberglass tubes are ideal for outdoor and industrial applications.
Where to Find Tapered Fiberglass Tube for Sale
When it comes to purchasing tapered fiberglass tube, there are several options available depending on your needs. You can find these tubes through specialized suppliers like GangLong Fiberglass, or by searching for a fiberglass tube near me, which offer a range of products suitable for various industries. One option for finding tapered fiberglass tubes is by searching online marketplaces, where both standard and custom sizes are available for sale. These marketplaces often carry an extensive range of stock, allowing you to compare prices and availability.
For those with specific project requirements, custom orders are also an option. Many suppliers, including GangLong Fiberglass, offer customized solutions where you can specify the dimensions, taper, and material composition of the tube to meet your unique needs. Whether you are looking for a small order for a personal project or bulk purchasing for industrial use, buying directly from suppliers can ensure that you receive exactly what you need.
Options for Buying Tapered Fiberglass Tube in Bulk
If you’re working on large-scale industrial or construction projects, purchasing tapered fiberglass tube in bulk can offer several advantages. Bulk purchases often come with discounts, making it a cost-effective solution. Suppliers like GangLong Fiberglass typically offer tiered pricing, where the cost per unit decreases as the quantity ordered increases.
Another benefit of bulk purchasing is the ability to secure a consistent supply of materials. This is particularly important for industries that rely on tapered fiberglass tube for ongoing projects. By working with a supplier that can meet your long-term needs, you ensure that you’ll have a steady supply of quality tubes without worrying about stock shortages.
In addition, many suppliers provide flexible payment options or long-term contracts for bulk orders. This can help manage cash flow and ensure that your projects stay within budget. Bulk orders can also often be customized to meet specific project requirements, allowing you to order the exact sizes, shapes, and tapers needed.
Customization of Tapered Fiberglass Tube for Specific Projects
Customization is a key aspect when it comes to tapered fiberglass tube. Different projects often require specific tube dimensions, and many suppliers like GangLong Fiberglass offer customization options to ensure the tubes meet the required specifications. You can select the exact length, taper, and diameter needed, which can be critical for applications where precision is essential.
For example, some projects may require tapered fiberglass tubes with specific wall thicknesses or unique taper ratios. Having the ability to customize these aspects allows for greater flexibility in the design and implementation of the project. Additionally, certain industries may require tubes with enhanced durability or specific chemical resistances, and customized orders can cater to these needs.
Customization can also extend to the surface finish of the tapered fiberglass tube. Depending on the intended use, you may want a smooth finish for aesthetic reasons or a textured finish for added grip. In all cases, working with a supplier like GangLong Fiberglass that offers a wide range of customization options ensures you get exactly what you need.
Common Sales and Promotions on Tapered Fiberglass Tube
Taking advantage of sales and promotions on tapered fiberglass tube can result in significant cost savings, especially for large projects. Suppliers like GangLong Fiberglass frequently offer promotions or discounts on specific products, particularly for bulk orders or during off-peak seasons. These promotions may include percentage discounts, free shipping, or bundled deals for purchasing multiple products.
To stay informed about these promotions, it’s a good idea to sign up for newsletters or regularly check the supplier’s website. This way, you can be alerted when a sale is running and plan your purchases accordingly. Additionally, many suppliers offer loyalty programs or discounts for repeat customers, which can further reduce costs over time.
How to Compare Prices for Tapered Fiberglass Tube
When purchasing tapered fiberglass tube, it’s important to compare prices across different suppliers to ensure you’re getting the best value. Several factors affect the pricing of these tubes, including the size, material composition, and level of customization required. For example, a standard-sized tapered fiberglass tube will typically cost less than a custom-sized one with a unique taper or wall thickness.
When comparing prices, also consider factors like shipping costs, especially if you are purchasing large or heavy items. Some suppliers, like GangLong Fiberglass, may offer free shipping or discounted rates for bulk orders, which can make a significant difference in the overall cost.
It’s also worth evaluating the quality of the materials used. High-quality fiberglass tubes may come with a higher upfront cost but offer better long-term durability and performance, reducing the need for replacements or repairs. Ensure that the supplier you choose offers products that meet your specific industry standards.
The Key of Tapered Fiberglass Tube
A tapered fiberglass tube is a type of composite material characterized by its tapered shape, with one end having a larger diameter than the other. This design enhances its structural efficiency while reducing overall weight. Tapered fiberglass tubes are widely used across industries such as aerospace, construction, marine, and sports equipment due to their superior strength-to-weight ratio, resistance to corrosion, and excellent insulation properties. The versatility of tapered fiberglass tube/component makes them ideal for a variety of applications, ranging from antenna masts to pole vaulting poles. As a highly customizable product, tapered fiberglass tube components can be manufactured in different sizes, lengths, and thicknesses to meet specific project needs. At GangLong Fiberglass, we offer a range of tapered fiberglass tube components designed to deliver performance, reliability, and durability in challenging environments.
The Key of Tapered Fiberglass Tube Sizes
The size of a tapered fiberglass tube plays a critical role in determining its performance and application suitability. Standard sizes often cater to common industrial needs, but custom sizing is also available for more specialized uses. These tubes typically have a gradual change in diameter, offering a combination of flexibility, strength, and weight optimization. The larger end of the tube provides structural stability, while the smaller end reduces weight, making the tapered fiberglass tube a popular choice in industries where both strength and reduced weight are crucial. For applications requiring greater strength and load-bearing capacity, tapered large diameter fiberglass tubes are also commonly used. These tubes have a significantly larger diameter at the wider end, offering enhanced strength while still maintaining the lightweight and tapered design for optimized performance.
Tapered fiberglass tubes are often available in lengths ranging from 1 meter to 6 meters or more, depending on the application. For example, GangLong Fiberglass offers tubes in sizes such as 1.5 inches at the larger end tapering to 0.5 inches at the smaller end, ideal for sporting applications like fishing poles or kite spars. The size of the tube must be selected based on the intended use, as larger tubes may offer more strength but also add weight, while smaller tubes may provide the required flexibility for lightweight applications. The availability of both standard and custom sizes ensures that the right tapered fiberglass tube can be selected for each specific project, ensuring optimal performance.
Advantages of Tapered Fiberglass Tube in Industrial Applications
Tapered fiberglass tube offers several advantages for industrial applications, making it a preferred choice for many professionals. First, its lightweight yet durable construction allows for easier handling and installation compared to metal alternatives. This reduces labor costs and speeds up project timelines.
Additionally, tapered fiberglass tube is highly resistant to corrosion, making it ideal for use in harsh environments where other materials might degrade. It also has excellent insulating properties, which can be beneficial in industries dealing with electricity or heat.
Furthermore, tapered fiberglass tube is known for its flexibility, allowing it to withstand stress and strain without breaking. This makes it suitable for dynamic applications where the material must bend or flex without compromising its structural integrity.
What are the Factors Affecting Tapered Fiberglass Tube Price
The price of a tapered fiberglass tube is influenced by several factors, including size, material, customization, and production methods. Larger tubes or tubes made from higher-grade materials, such as enhanced resin systems, typically cost more. The manufacturing process also affects the price; for instance, pultrusion, filament winding, and fiberglass hand lay-up methods offer different cost structures depending on the volume and complexity of the tube design.
Customizations such as specific tapers, lengths, and thicknesses can increase the overall cost. At GangLong Fiberglass, the price for a standard tapered fiberglass tube can range from $10 to $50 per unit, depending on the specifications. In comparison, highly customized tubes with special reinforcement or advanced resin systems could cost upwards of $100 per unit. Volume orders also influence pricing, with bulk purchases typically resulting in lower per-unit costs.
Furthermore, the location of production and material sourcing also play a role in determining the final price. Imported materials or tubes manufactured using advanced machinery may carry higher costs, but these also ensure a high level of quality and performance. Understanding the factors affecting price can help buyers make more informed decisions when sourcing tapered fiberglass tubes.
The Key of Tapered Fiberglass Tube Suppliers
When selecting a tapered fiberglass tube supplier, it is important to consider their track record in delivering high-quality products, their customization options, and the scope of their inventory. GangLong Fiberglass, for instance, offers an extensive range of tapered fiberglass tubes and excels in providing both standard and custom solutions. The ability to source materials domestically or internationally ensures that suppliers can meet varying demands for durability, performance, and cost-effectiveness.
Suppliers that offer additional services, such as cutting, drilling, and finishing, add value by reducing the time and effort required for project completion. Additionally, partnering with a supplier that provides customer support and technical expertise ensures that buyers get the right product for their specific applications. At GangLong Fiberglass, we provide personalized assistance in choosing the correct sizes, tapers, and material compositions based on the project requirements, ensuring that every customer gets a solution tailored to their needs.
Suppliers who offer quick delivery and flexible order quantities are also highly preferred, especially for projects with tight deadlines. Finding a reliable supplier who balances quality, cost, and delivery efficiency is key to the successful procurement of tapered fiberglass tubes. This is particularly important in FRP pipe procurement, where these factors significantly influence the overall success of your project and ensure that the materials meet the required specifications and performance standards.
How About Locating Tapered Fiberglass Tube Near Me
Locating a supplier or distributor of tapered fiberglass tubes near your location offers several advantages, including faster delivery times, reduced shipping costs, and easier communication with the supplier. Using online platforms and directories, such as industrial supply websites or composite material marketplaces, can help identify nearby sources for tapered fiberglass tubes. Websites like GangLong Fiberglass provide detailed product listings and have options to filter by location, allowing buyers to find local distributors or manufacturers quickly.
Purchasing locally also ensures that any issues related to customization or order specifications can be addressed promptly. Many local suppliers offer additional services such as custom cutting or assembly, which can reduce overall project time and complexity. The proximity of the supplier often results in shorter lead times, allowing businesses to meet tight project deadlines without the risk of long international shipping delays.
Another advantage of sourcing locally is the potential for building long-term relationships with distributors, which may lead to cost savings, priority service, and better communication over time. Local suppliers may also offer pickup options, further reducing costs associated with delivery.
The Key of Exploring Tapered Fiberglass Tube for Sale
When looking for tapered fiberglass tubes for sale, it is important to consider both the quality of the product and the reliability of the seller. GangLong Fiberglass offers a wide variety of tapered fiberglass tubes available for immediate purchase, catering to various industries from construction to sports. Whether you need tubes for structural reinforcement or for recreational applications, it’s important to ensure the seller provides both quality assurance and support.
Online platforms provide a convenient way to browse a wide range of tapered fiberglass tubes for sale. These platforms often allow for easy comparison of prices, materials, and tube sizes, enabling buyers to find the most suitable product for their application. Many sellers, including GangLong Fiberglass, offer detailed specifications, including length, diameter, and taper ratio, which helps buyers make informed purchasing decisions.
It’s also essential to consider the seller’s return policy, especially for customized products. In some cases, incorrect dimensions or specifications may require an exchange or return, so working with a seller who offers a flexible return policy can save time and money in the long run. Additionally, checking for customer reviews and ratings can provide insights into the seller’s reputation for delivering high-quality products and customer service.
How About Choosing the Right Tapered Fiberglass Tube for Your Project
Choosing the right tapered fiberglass tube for your project involves considering several key factors, including the tube’s size, material composition, and the specific requirements of the application. A tapered fiberglass tube designed for aerospace applications, for instance, may require different specifications than a tube used in construction or sporting equipment. The tube’s length, taper ratio, and wall thickness all play important roles in determining its suitability for a given project.
At GangLong Fiberglass, we offer a variety of tapered fiberglass tubes designed to meet the needs of diverse industries. Our range of options includes tubes with varying diameters, lengths, and material compositions to ensure that our customers get the best possible product for their applications. Whether you need a tube for a high-performance engineering project or a lightweight solution for recreational purposes, selecting the right size and specifications is critical to the success of the project.
The Meaning of Tapered Fiberglass Tube: What You Need to Know
Tapered fiberglass tube is a versatile and durable material used in a wide range of applications, from construction and marine industries to aerospace and outdoor installations. Made by gradually reducing the diameter of the tube from one end to the other, the tapered design offers unique benefits in terms of flexibility, strength, and lightweight construction. Whether you are looking for enhanced resistance to environmental factors or a cost-effective material that is easy to install, tapered fiberglass tube provides a solution for various project needs.
Tapered fiberglass tube is known for its excellent performance characteristics, including resistance to corrosion, high tensile strength, and lightweight properties. It is an ideal alternative to materials like steel or aluminum, particularly in industries that require materials that can withstand harsh conditions without compromising structural integrity. The combination of its tapered shape and fiberglass composition makes it an essential component in industries that require flexibility, durability, and a high strength-to-weight ratio.
Guide to Finding Reliable Suppliers for Tapered Fiberglass Tube
When sourcing tapered fiberglass tube for a project, it is essential to choose a reliable supplier that can meet your needs for quality, delivery, and customization. Working with a trusted supplier like GangLong Fiberglass ensures that you receive high-quality products that meet industry standards and specifications. Selecting the right supplier can make a significant difference in the success of your project, particularly when dealing with complex orders that require precise dimensions and unique designs.
One of the key factors to consider when choosing a supplier is their ability to provide a wide range of tapered fiberglass tube options. Whether you need standard sizes or customized solutions, it is crucial to work with a supplier that offers flexibility in terms of product offerings. In addition to size variations, you should also consider whether the supplier can meet your needs for surface finishes, colors, and specific material properties.
Another important consideration when selecting a tapered fiberglass tube supplier is their ability to deliver on time. Delays in receiving materials can have a significant impact on project timelines, particularly for large-scale industrial or construction applications. A reliable supplier like GangLong Fiberglass will offer clear communication regarding lead times and shipping options to ensure that you receive your materials when needed.
Considerations When Choosing Suppliers for Tapered Fiberglass Tube
Several critical factors should be evaluated when selecting a supplier for tapered fiberglass tube, including quality control, customization capabilities, and customer support. These considerations will ensure that you receive not only high-quality materials but also the service needed to support your project from start to finish.
Quality Control: One of the most important aspects of working with a tapered fiberglass tube supplier is their commitment to quality control. Ensure that the supplier follows strict manufacturing processes to produce tubes that meet industry standards and specifications. Suppliers like GangLong Fiberglass typically implement quality checks at every stage of production, from material selection to final inspection. This ensures that the tubes you receive are free from defects and meet your exact specifications.
Customization Capabilities: Not all projects require standard-sized tubes, and many industries need custom-designed tapered fiberglass tubes for specific applications. When choosing a supplier, make sure they offer customization services, including the ability to produce tubes with unique taper ratios, wall thicknesses, or specific chemical resistances. GangLong Fiberglass offers extensive customization options, allowing you to select the exact dimensions and material properties needed for your project.
Customer Support: Excellent customer support is critical when sourcing tapered fiberglass tube. A good supplier will work closely with you to understand your project needs and provide tailored solutions. They should be responsive to inquiries, provide clear timelines for production and delivery, and offer technical support if needed. GangLong Fiberglass is known for its strong commitment to customer satisfaction, providing ongoing support throughout the purchasing process.
Characteristics of Trustworthy Tapered Fiberglass Tube Suppliers
Choosing a trustworthy supplier for tapered fiberglass tube is vital for ensuring that your project runs smoothly. There are several characteristics to look for in a supplier to assess their reliability and suitability for long-term partnerships.
Product Quality: A reliable supplier will consistently provide high-quality tapered fiberglass tube that meets or exceeds industry standards. They will use high-grade fiberglass materials and advanced manufacturing techniques to produce durable and long-lasting products. Suppliers like GangLong Fiberglass maintain stringent quality control processes to ensure their products deliver reliable performance.
Certifications and Industry Experience: Look for a supplier that has a proven track record in the industry and is recognized for their quality and expertise. Certifications from recognized organizations or compliance with international standards indicate that the supplier adheres to the best practices in manufacturing and quality assurance. GangLong Fiberglass has years of experience in the production of tapered fiberglass tubes and is recognized for its commitment to quality.
On-Time Delivery: A trustworthy supplier will ensure that your materials are delivered on time, every time. Delays in receiving your tapered fiberglass tube can lead to costly setbacks in your project timeline. A reliable supplier like GangLong Fiberglass will have an efficient production and shipping process in place to ensure timely delivery, whether you are ordering a small batch or large quantities for an industrial project.
Flexible Ordering Options: Whether you need standard or customized tapered fiberglass tubes, a trustworthy supplier will offer flexible ordering options that cater to your specific needs. This includes the ability to place bulk orders, request custom sizes, or choose from various material finishes. GangLong Fiberglass provides a range of options to ensure that customers receive exactly what they need for their projects.
Technical Expertise: A reliable supplier will have the technical expertise necessary to assist with product selection, customization, and troubleshooting. Whether you need advice on the best type of tapered fiberglass tube for your project or assistance with installation, a knowledgeable supplier like GangLong Fiberglass can provide the guidance you need.
Strong Customer Relationships: Trustworthy suppliers prioritize building long-term relationships with their customers. They offer excellent customer service, address concerns promptly, and strive to exceed customer expectations. GangLong Fiberglass is known for its strong commitment to customer satisfaction, offering personalized support to ensure that every project is successful.
Importance of Quality Control in Tapered Fiberglass Tube Manufacturing
The quality of tapered fiberglass tube is critical to its performance and longevity. As such, it is essential to work with a supplier that prioritizes quality control at every stage of the manufacturing process. Suppliers like GangLong Fiberglass implement rigorous quality assurance processes to ensure that each tube meets precise specifications and performs as expected.
The quality control process for tapered fiberglass tube typically involves several key steps. First, the raw materials used in production are carefully selected to ensure they meet high standards for durability and strength. During production, the tubes are continuously inspected to ensure that the taper is consistent and that there are no defects in the fiberglass.
After production, the finished tubes undergo further inspection to ensure that they meet industry standards and customer specifications. This includes checking the dimensions, taper, and surface finish of each tube. Only products that pass these stringent quality checks are approved for shipping.
By working with a supplier like GangLong Fiberglass that emphasizes quality control, you can be confident that the tapered fiberglass tube you receive will perform reliably and meet the demands of your project.
Customizing Tapered Fiberglass Tube for Specialized Applications
One of the greatest advantages of tapered fiberglass tube is the ability to customize it for specialized applications. Whether you are working in construction, marine, or industrial sectors, customized tapered fiberglass tubes can be tailored to meet your specific project requirements.
Customization options for tapered fiberglass tube include the ability to select the exact taper ratio, wall thickness, and diameter needed for your application. This allows you to create tubes that are perfectly suited for the structural or mechanical demands of your project. GangLong Fiberglass offers extensive customization services, ensuring that you receive tubes that meet your exact specifications.
In addition to dimensional customization, you can also choose specific material properties for your tapered fiberglass tube. For example, some applications may require tubes that offer enhanced resistance to chemicals, UV radiation, or high temperatures. By customizing the material composition of the tube, you can ensure that it performs reliably in even the most demanding environments.
Surface finishes are another area where customization can make a difference. Depending on your needs, you can choose from a range of finishes, including smooth, textured, or painted surfaces. A smooth surface finish may be ideal for applications where aesthetics are important, while a textured finish can provide added grip or abrasion resistance.
Customization is particularly important in industries where precision is critical. For example, in the aerospace or automotive industries, even small variations in tube dimensions or material properties can have a significant impact on performance. By working with a supplier like GangLong Fiberglass that offers a wide range of customization options, you can be confident that your tapered fiberglass tube will meet the exact requirements of your project.
Shipping and Delivery Considerations for Tapered Fiberglass Tube
When ordering tapered fiberglass tube, it is important to consider the shipping and delivery options offered by your supplier. Ensuring that your materials arrive on time and in good condition is critical to the success of your project. A reliable supplier like GangLong Fiberglass will provide a range of shipping options to meet your needs, whether you are ordering a single tube or a bulk shipment.
One of the key considerations when shipping tapered fiberglass tube is the length and size of the tubes. Long or oversized tubes may require special shipping arrangements, including custom packaging or freight services. GangLong Fiberglass offers flexible shipping solutions that ensure your tubes are securely packaged and delivered without damage.
In addition to packaging, it is important to consider the lead time for production and shipping. Depending on the size and complexity of your order, production times may vary. By working with a supplier that provides clear communication about lead times, such as GangLong Fiberglass, you can plan your project timeline accordingly.
Shipping costs are another factor to consider, particularly for bulk orders. Some suppliers offer discounted or free shipping for large orders, which can help reduce overall project costs. GangLong Fiberglass offers competitive shipping rates and will work with you to find the most cost-effective delivery option for your order.
Threaded Fiberglass Pipe: A Comprehensive Guide
The Key of Tapered Fiberglass Tube Price
Tapered fiberglass tubes are an essential component in a variety of industries due to their strength, durability, and lightweight nature. However, when considering their purchase, price is one of the most critical factors. Understanding the price ranges, the factors that influence pricing, and how to compare different options effectively can help businesses and individuals make informed decisions that ensure cost-efficiency without compromising on quality.
Factors Influencing the Price of a Tapered Fiberglass Tube
The price of a tapered fiberglass tube is influenced by several factors, including size, material type, customization, and production processes. These factors can significantly affect the overall cost of a tube, making it essential to understand each one in detail.
- Size
The size of a tapered fiberglass tube plays a significant role in determining its price. Larger tubes, which require more raw materials and longer production times, tend to be more expensive. For example, a tube that is 6 meters long with a taper from 3 inches at the larger end to 1 inch at the smaller end will cost more than a smaller 2-meter tube with a similar taper. Additionally, the wall thickness of the tube, such as with a thick wall fiberglass tube, also affects the price. Thicker walls provide more strength but require more materials, which increases the cost. - Material Type
The type of material used in manufacturing tapered fiberglass tubes also impacts the price. Some tubes are made with standard fiberglass, while others incorporate specialized resins or coatings for additional durability, chemical resistance, or specific environmental requirements. For instance, tubes designed for high-temperature applications or corrosive environments may require a higher-grade resin, such as vinyl ester or epoxy, which increases the cost. At GangLong Fiberglass, we offer a variety of material options tailored to specific industrial needs, each with its associated price point. - Customization
Customization is another key factor affecting the price of tapered fiberglass tubes. Standard, off-the-shelf tubes are typically more affordable, but customized tubes—tailored to specific lengths, diameters, or tapers—come at a premium. Customization may also include additional features like special finishes, colors, or mechanical properties. For example, GangLong Fiberglass provides tubes with a variety of custom options, such as tapered tubes reinforced with additional layers for enhanced strength or tubes with a particular taper ratio suited to niche applications. Custom orders often require special molds or production techniques, which increase the cost. - Production Processes
The method used to produce the tapered fiberglass tube can also affect its price. For instance, pultrusion is a cost-effective method for producing long, straight composite tubes, but it may not be suitable for complex tapered designs. Tapered tubes often require hand lay-up or filament winding techniques, which are more labor-intensive and time-consuming, leading to higher costs. These methods ensure that the tube maintains the required strength and uniformity along its tapered length, but they also increase the price due to the additional work involved in the production process.
The Price Ranges for Tapered Fiberglass Tube
Tapered fiberglass tubes come in a range of prices depending on the factors outlined above. For standard, off-the-shelf tubes, prices may start as low as $20 for small tubes used in hobbyist or light industrial applications. For larger or more specialized tubes, the price can range between $50 and $200 per unit.
Custom orders, which involve specific sizes, tapers, or material requirements, generally command a higher price. A custom tapered fiberglass tube designed for a high-performance application, such as aerospace or heavy industrial use, can cost anywhere from $200 to $500 or more, depending on the complexity of the design and the materials used. At GangLong Fiberglass, our standard tapered tubes are competitively priced, with custom designs available at variable costs based on the client’s specifications.
Volume also plays a role in determining price. Purchasing in bulk often leads to lower per-unit costs, making it more economical for larger projects. For example, an order of 100 standard tubes may reduce the cost per tube by 10-20%, making bulk orders a cost-effective option for large-scale industrial projects.
The Key of Tapered Fiberglass Tube for Various Industrial Applications
Tapered fiberglass tubes are used across many industries, including aerospace, construction, marine, and automotive. The specific requirements of these industries often dictate the need for customized solutions, which can influence both the price and the performance of the tube.
In aerospace applications, for example, tapered fiberglass tubes are often chosen for their lightweight properties and high strength, helping to reduce overall vehicle weight while maintaining structural integrity. In the construction industry, tapered tubes are used in projects that require long-lasting materials resistant to corrosion and environmental degradation. For these industries, investing in a higher-priced, high-performance tapered fiberglass tube can yield significant long-term benefits.
At GangLong Fiberglass, we cater to a wide range of industries by offering tapered fiberglass tubes in various sizes, materials, and finishes. Whether it’s for a large construction project or a specialized aerospace application, our tubes are designed to meet the rigorous demands of each industry while offering a competitive price.
Final Thoughts on Tapered Fiberglass Tube Pricing
The price of a tapered fiberglass tube is influenced by many factors, including size, material, customization, and production processes. By understanding these factors and carefully comparing options, businesses and individuals can make informed decisions that balance cost with performance. Whether you’re looking for a standard tube or a fully customized solution, GangLong Fiberglass offers a wide range of products designed to meet diverse industrial needs at competitive prices.
Top Benefits of Using Silicone Fiberglass Tube in Equipment
Manufacturers of Tapered Fiberglass Tube
Tapered fiberglass tube is a type of cylindrical structure made from high-strength fiberglass materials that features a decreasing diameter from one end to the other. This design is particularly effective in applications where the structure needs to be both lightweight and strong, with the tapering offering enhanced flexibility and load distribution. These tubes are commonly used in industries such as construction, marine, telecommunications, and sports equipment manufacturing.
Tapered fiberglass tube has gained popularity due to its resistance to corrosion, environmental degradation, and electrical conductivity, making it a versatile material for a wide range of applications. The tapering allows for a more efficient use of materials while maintaining strength and reducing weight, which is particularly beneficial in industries that require lightweight but durable structures.
The manufacturing process of tapered fiberglass tube typically involves layering fiberglass and resin in specific patterns to create a tube with consistent mechanical properties. These tubes can be customized to meet the specific needs of various industries, including different lengths, diameters, and wall thicknesses. Companies like GangLong Fiberglass specialize in producing high-quality tapered fiberglass tubes that meet the unique requirements of their clients.
Leading Tapered Fiberglass Tube Manufacturers
Finding the right manufacturer for tapered fiberglass tube is crucial to ensuring the quality, durability, and performance of the product. Global and local manufacturers play an essential role in the supply of these tubes, with each company offering its own set of specialties, from standard tubes to highly customized solutions. Manufacturers like GangLong Fiberglass have become industry leaders by focusing on innovation, quality control, and customer service.
Leading manufacturers are known for their ability to produce a wide variety of tapered fiberglass tubes to meet the diverse needs of industries. From small-scale orders for specialized applications to large-scale production runs, these manufacturers cater to various project sizes and complexities. Many of them also offer customization options, allowing clients to specify the exact dimensions, tapers, and finishes they need for their projects.
One of the key factors that differentiate high-quality manufacturers from others is their focus on innovation. The top manufacturers, like GangLong Fiberglass, are continually investing in research and development to improve the manufacturing processes, explore new materials, and enhance the performance of their products. This dedication to innovation allows them to stay competitive in the market and meet the ever-evolving demands of industries that rely on tapered fiberglass tubes.
Key Factors That Differentiate High-Quality Tapered Fiberglass Tube Manufacturers
Several factors set leading tapered fiberglass tube manufacturers apart from their competitors. When choosing a manufacturer, it is essential to consider the following elements to ensure you receive high-quality products that meet your specific needs.
Material Quality: The quality of the materials used in the production of tapered fiberglass tube plays a critical role in its performance. High-quality manufacturers, like GangLong Fiberglass, source premium-grade fiberglass and resin to ensure their tubes are strong, durable, and resistant to environmental factors such as UV radiation, moisture, and chemicals. The consistency and purity of the materials used will directly affect the strength and longevity of the final product.
Certifications and Industry Standards: A high-quality manufacturer will adhere to industry standards and obtain the necessary certifications for their products. This ensures that the tapered fiberglass tubes meet safety and performance requirements, especially for industries where safety is paramount, such as aerospace or construction. Manufacturers like GangLong Fiberglass are often certified by recognized industry bodies, providing clients with the assurance that their products are reliable and meet the highest standards.
Technological Capabilities: Advanced manufacturing technologies enable high-quality manufacturers to produce tapered fiberglass tubes with precision and consistency. Leading companies invest in state-of-the-art equipment and techniques, allowing them to create tubes with complex tapers, custom wall thicknesses, and smooth finishes. The use of technology also allows manufacturers like GangLong Fiberglass to offer innovative solutions, such as tubes with enhanced mechanical properties or special coatings that increase durability.
Customization and Flexibility: Not every project requires standard-sized tubes, and leading manufacturers understand the importance of offering customized solutions. GangLong Fiberglass is known for its ability to produce custom tapered fiberglass tubes based on specific client requirements. Whether you need tubes with unique tapers, varying lengths, or specific material properties, working with a manufacturer that offers flexibility and customization ensures that your project’s exact needs are met.
Quality Control: Stringent quality control measures are essential to ensure that every tapered fiberglass tube meets the required specifications. High-quality manufacturers like GangLong Fiberglass implement quality control checks at every stage of the manufacturing process, from material selection to the final inspection of the finished product. This attention to detail ensures that the tubes are free from defects, meet industry standards, and perform reliably in their intended applications.
How Manufacturers Innovate to Meet Industry Demands for Tapered Fiberglass Tubes
As industries continue to evolve, so do the demands for materials like tapered fiberglass tube. Manufacturers must innovate to keep up with the changing requirements of their clients, whether it be through the development of new materials, improvements in production processes, or enhanced customization options. Leading manufacturers like GangLong Fiberglass are at the forefront of innovation in the fiberglass industry, continuously exploring new ways to improve their products and meet industry demands.
Research and Development: One of the primary ways manufacturers innovate is through research and development. By experimenting with new fiberglass composites, resins, and additives, manufacturers can create tubes with enhanced properties such as increased strength, higher resistance to chemicals, or improved flexibility. For example, GangLong Fiberglass has invested heavily in R&D to develop specialized tubes that are highly resistant to extreme temperatures, making them ideal for use in industrial or aerospace applications.
Automation and Precision Manufacturing: Another area of innovation is in the manufacturing process itself. Automation has allowed manufacturers to produce tapered fiberglass tubes with greater precision and efficiency, reducing the likelihood of defects and ensuring consistency across large production runs. Automated processes also enable manufacturers like GangLong Fiberglass to offer faster lead times, which is critical for industries that require quick turnaround on orders.
Sustainability Initiatives: As sustainability becomes a key focus for many industries, leading manufacturers are looking for ways to reduce the environmental impact of their production processes. GangLong Fiberglass, for example, has implemented eco-friendly practices in their manufacturing facilities, such as reducing waste, recycling materials, and using energy-efficient technologies. These initiatives not only benefit the environment but also help manufacturers stay competitive in a market that increasingly values sustainability.
Customization and Niche Applications: The demand for customized solutions continues to grow, and manufacturers are responding by offering more flexible production options. This includes the ability to produce tapered fiberglass tubes in a wide range of sizes, tapers, and material properties, allowing for greater versatility in their use. Manufacturers like GangLong Fiberglass are particularly known for their ability to cater to niche applications, such as producing tubes for specific marine, industrial, or telecommunications applications.
Enhanced Coatings and Surface Treatments: Surface treatments and coatings are another area where manufacturers are innovating. By developing new coatings that improve the performance of tapered fiberglass tubes, manufacturers can enhance their resistance to abrasion, UV radiation, or chemical exposure. GangLong Fiberglass offers a range of coating options, allowing clients to choose the best solution for their specific application needs.
The Importance of Choosing the Right Tapered Fiberglass Tube Manufacturer
Selecting the right manufacturer for your tapered fiberglass tube needs is crucial to the success of your project. The quality, durability, and performance of the tubes will directly impact the reliability and longevity of the structures or systems in which they are used. Working with a trusted manufacturer like GangLong Fiberglass ensures that you receive high-quality products that meet industry standards and are tailored to your specific needs.
The right manufacturer will also offer support throughout the project, from helping you choose the right tube dimensions to providing technical assistance during installation. This level of service is essential for ensuring that your project runs smoothly and that any issues are addressed promptly. Additionally, a reliable manufacturer will offer transparent pricing, delivery timelines, and clear communication, helping you stay on budget and on schedule.
By choosing a manufacturer that prioritizes quality, innovation, and customer service, you can be confident that the tapered fiberglass tube you receive will perform as expected and contribute to the overall success of your project. GangLong Fiberglass has a long-standing reputation for providing high-quality products, excellent customer support, and innovative solutions, making them a leading choice for clients across various industries.
Manufacturing Process of Red Thread Fiberglass Pipe Explained
How to Choose High Quality Tapered Fiberglass Tube
Choosing a high-quality tapered fiberglass tube involves considering several key factors that affect its performance, durability, and suitability for specific applications. Here’s a detailed guide on what to look for when selecting a high-quality tapered fiberglass tube:
1. Material Composition and Resin Type
- Fiberglass Reinforcement: High-quality fiberglass tubes typically use E-glass or S-glass fibers. E-glass is the most common and offers good strength-to-weight ratio and electrical insulation properties, while S-glass provides higher strength and is more suitable for applications that require high mechanical properties.
- Resin Type: The resin used in the tube’s construction plays a major role in temperature resistance, chemical resistance, and overall durability. Choose the appropriate resin based on your application:
- Polyester: Lower cost but less heat and chemical resistance.
- Vinyl Ester: Better resistance to heat, chemicals, and moisture.
- Epoxy: Superior strength, heat resistance, and durability.
- Phenolic or High-Performance Resins: If you’re dealing with extreme temperatures or specialized applications like aerospace, look for tubes made with high-performance resins.
2. Manufacturing Process
- Pultrusion: Pultruded fiberglass tubes are typically stronger and more consistent in terms of mechanical properties. This process involves pulling continuous fibers through a resin bath and a heated die, ensuring a uniform wall thickness and strength.
- Hand Lay-Up or Filament Winding: These processes can be used for custom applications but may not always offer the same level of consistency and strength as pultrusion.
- Molding: Some tapered tubes are created using compression or resin transfer molding (RTM), which can be used for complex geometries or larger tube sizes.
3. Dimensional Accuracy and Taper Uniformity
- Ensure that the tube’s taper is consistent along its entire length. High-quality tubes should have a smooth, uniform taper with no irregularities or bulges. This is particularly important for applications like structural supports or components that require precise load distribution.
- Measure the inner and outer diameters at both ends of the tube to confirm that they fall within the specified tolerances.
4. Wall Thickness and Strength-to-Weight Ratio
- Wall Thickness: The wall thickness of the tube should be adequate for the specific application. A thicker wall provides greater strength and rigidity but increases the weight, while a thinner wall reduces weight but may compromise strength. Choose based on your load-bearing and strength requirements.
- Strength-to-Weight Ratio: Fiberglass tubes should provide the right balance between strength and weight. High-quality tubes will be lightweight yet strong enough to handle the intended loads and forces.
5. Temperature Resistance
- Select a tapered fiberglass tube with a resin system that can withstand the maximum temperatures it will encounter in its application. Ensure the tube’s resin type is appropriate for the operating temperature range.
- For high-temperature applications, choose epoxy, vinyl ester, or phenolic resins over polyester resin.
6. Corrosion and Chemical Resistance
- Fiberglass is generally highly resistant to corrosion, but the specific resin type and the environmental conditions should be considered. Vinyl ester and epoxy resins offer better chemical resistance compared to polyester.
- If the tube will be exposed to harsh chemicals, ensure it is compatible with the substances involved.
7. Surface Finish and Aesthetic Quality
- Smooth Surface: A smooth and consistent surface is a sign of a well-manufactured tube. Imperfections, rough patches, or bubbles in the surface can indicate poor quality, and may weaken the tube or affect its appearance.
- Finish Type: Depending on the application, the surface finish of the fiberglass tube can be glossy, matte, or textured. The finish may also affect the bonding properties if the tube needs to be joined with other components.
8. Impact and Fatigue Resistance
- A high-quality tapered fiberglass tube should have excellent impact resistance and fatigue resistance, especially if the tube will experience repeated stress or dynamic loads.
- Impact Testing: Look for manufacturers who conduct impact testing to ensure the tube can withstand physical shocks without cracking or breaking.
- Fatigue Resistance: For applications with cyclical loading, ensure the tube is designed for fatigue resistance, meaning it can withstand repeated stress cycles without failure.
9. UV Resistance
- If the fiberglass tube will be used outdoors or exposed to sunlight, UV resistance is important to prevent degradation due to UV exposure.
- Some fiberglass tubes come with UV-resistant coatings or are made from UV-stabilized resins. Ensure the tube is capable of maintaining its integrity when exposed to sunlight for prolonged periods.
10. Customization and Design Flexibility
- A high-quality tapered fiberglass tube should be customizable to meet the specific requirements of your project. This includes the ability to adjust the taper angle, diameter, wall thickness, length, and resin type.
- Some manufacturers offer custom molds or the ability to design the tube to exact specifications, which is useful for specialized applications in aerospace, automotive, or industrial sectors.
11. Testing and Certifications
- Look for tubes that are tested according to industry standards. High-quality tubes are often subjected to various tests, including tensile strength tests, thermal testing, impact testing, and chemical resistance tests.
- Certifications such as ISO 9001 (for quality management systems) or industry-specific certifications (e.g., for aerospace, marine, or automotive applications) can give assurance of quality.
12. Supplier Reputation and Reviews
- Choose a manufacturer or supplier with a good reputation for producing high-quality fiberglass products. Look for companies with experience in producing tapered fiberglass tubes for your specific application.
- Customer reviews and testimonials can provide valuable insights into the quality of the tubes and the supplier’s customer service.
13. Price vs. Performance
- While it’s tempting to choose the cheapest option, performance and quality should always take precedence. A high-quality tapered fiberglass tube may have a higher initial cost, but it will often provide better performance, durability, and longevity, resulting in lower maintenance and replacement costs over time.
When selecting a high-quality tapered fiberglass tube, consider:
- The type of fiberglass and resin used for optimal strength, heat resistance, and chemical durability.
- The manufacturing process, ensuring the tube is made with precision and consistency.
- Dimensional accuracy, taper uniformity, and wall thickness that align with your application’s requirements.
- Performance factors like temperature resistance, corrosion resistance, impact strength, and fatigue resistance.
- Supplier reputation, quality certifications, and whether the tube meets your application’s specific standards.
By carefully evaluating these factors, you can ensure you select a high-quality tapered fiberglass tube that will perform well and last under your specific conditions.
FAQs about Tapered Fiberglass Tube
Cutting fiberglass tubes requires specific tools to avoid damaging the material or creating hazardous dust. The best method is to use a fine-toothed hacksaw or a rotary tool with a fiberglass-cutting blade. You can also use a pipe cutter designed for fiberglass. Before cutting, it’s important to wear protective gear, such as gloves, goggles, and a mask, as fiberglass dust can be harmful. To ensure a clean cut, measure and mark the tube carefully. After cutting, smooth the edges with sandpaper to remove any rough spots.
Fiberglass tubes have a wide range of applications due to their lightweight, durable, and corrosion-resistant properties. They are commonly used in industries like construction, automotive, aerospace, and telecommunications. These tubes are often found in structural supports, antenna poles, marine applications (such as boat masts), and various sporting goods, such as fishing rods and tent poles. Their strength-to-weight ratio makes them ideal for applications requiring both durability and lightness. Fiberglass tubes are also used in the construction of wind turbine blades and other components that need to withstand harsh environmental conditions.
Yes, carbon fiber tubes can be cut, but it requires special tools and techniques. The most common way to cut carbon fiber tubes is by using a rotary tool with a diamond-coated blade or a carbide-tipped saw blade. Unlike fiberglass, carbon fiber is harder and denser, so cutting can produce harmful dust. Therefore, it’s essential to wear a respirator, goggles, and gloves to protect against the fine particles. For precise cuts, masking tape can be applied to the tube to prevent fraying and ensure clean edges. It’s important to use a slow, controlled cutting technique to avoid damaging the tube.
Yes, carbon fiber tubes are incredibly strong and lightweight, making them ideal for high-performance applications. Carbon fiber is known for its excellent strength-to-weight ratio, which means that it can be both stiff and strong without being heavy. This makes carbon fiber tubes popular in aerospace, automotive, and sports equipment industries. The material is resistant to fatigue, corrosion, and high temperatures, offering superior performance under stress. However, carbon fiber is more brittle compared to metals like steel, so it may fail under impact or when subjected to sharp bending forces, making proper handling and design crucial for durability.
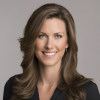
As the editor of GangLong Fiberglass, I have years of experience and in-depth research, focusing on cable tray products, fiberglass solutions, and grille systems. I incorporate years of industry insights and practical experience into every content, committed to promoting the progress of the industry. At GangLong Fiberglass, my commitment is reflected in every product, from innovative cable trays to durable fiberglass solutions and sturdy grille systems. As an authoritative voice in the industry, my goal is to provide valuable information to professionals and businesses and promote forward-looking solutions.