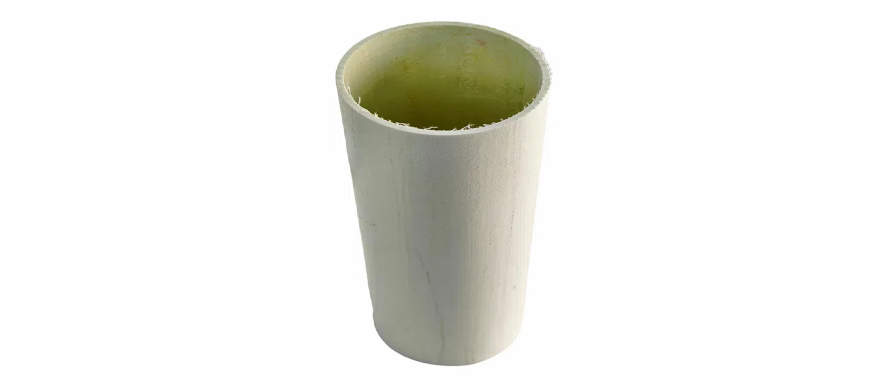
Threaded fiberglass pipe comes in a variety of sizes to suit different industrial applications. Common sizes typically range from small-diameter pipes for light-duty uses to larger pipes designed for high-pressure systems. Industry standards, such as ASTM and ASME, ensure that these pipes meet the necessary requirements for durability and performance. The size of threaded fiberglass pipe significantly impacts its ability to handle pressure, temperature, and corrosive materials, particularly in applications involving Centrifugally Cast Fiberglass Pipe, which is designed for enhanced durability and performance.Selecting the appropriate size is crucial to ensure efficient operation, longevity, and safety in specific projects. Proper sizing enhances the pipe’s effectiveness in various environments, including chemical processing and wastewater management. Threaded fiberglass pipe is ideal for corrosive applications, hot water, and underground fuel handling, featuring amine-cured epoxy resin and glass fibers.
What is Threaded Fiberglass Pipe?
Threaded fiberglass pipe is a type of piping system designed to offer superior performance in a variety of challenging environments. Made from a composite material that combines fiberglass and resin, this type of pipe is highly resistant to corrosion, extreme temperatures, and harsh chemicals. Its threaded design allows for easy installation and secure connections, making it a popular choice for industries such as chemical processing, wastewater treatment, and oil and gas. The versatility of threaded fiberglass pipe, particularly Green Thread Fiberglass Pipe, has made it a go-to solution for projects where durability and reliability are essential.
Threaded fiberglass pipe systems are lightweight, yet strong, making them easier to handle and install than traditional metal pipes. The threaded ends allow for simple connection to fittings, valves, and other pipe sections, which reduces installation time and labor costs. This design also minimizes the need for welding or adhesive bonding, which are commonly required with other types of pipes.
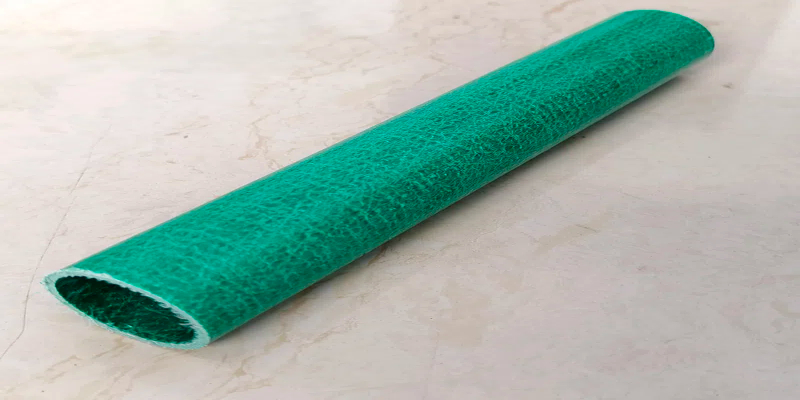
Features and Benefits of Threaded Fiberglass Pipe
Threaded fiberglass pipe offers a wide range of features and benefits that make it an attractive option for many industries. Some of the key advantages include:
- Corrosion Resistance: Unlike metal pipes, threaded fiberglass pipe does not rust or corrode when exposed to moisture, saltwater, or a variety of chemicals. This makes it ideal for use in harsh environments such as marine applications, chemical processing plants, and water treatment facilities.
- Lightweight Design: Fiberglass is significantly lighter than steel or copper, which makes threaded fiberglass pipe much easier to transport and install. The reduced weight also lowers transportation costs and minimizes the need for heavy lifting equipment during installation.
- High Strength-to-Weight Ratio: Despite being lightweight, threaded fiberglass pipe is incredibly strong and durable. It can withstand high pressures and extreme temperatures, making it suitable for demanding industrial applications.
- Temperature and Chemical Resistance: Threaded fiberglass pipe can handle a wide range of temperatures and is resistant to many acids, alkalis, and other aggressive chemicals. This makes it a popular choice for use in industries that require pipes to withstand tough conditions.
- Longevity and Low Maintenance: Threaded fiberglass pipe systems have a long service life, often lasting several decades without the need for significant maintenance. This reduces the total cost of ownership and ensures reliable performance over the long term.
- Customizable Sizes and Configurations: Threaded fiberglass pipe is available in a variety of sizes and configurations, allowing it to be customized for specific applications. Whether you need a small diameter pipe for a laboratory setup or a larger size for industrial piping, GangLong Fiberglass can provide the right solution.
Advantages of Threaded Fiberglass Pipe Over Other Materials
Threaded fiberglass pipe offers several advantages over other materials, such as steel, copper, or PVC. These benefits make it an increasingly popular choice in industries where durability, cost-effectiveness, and ease of installation are priorities.
- Corrosion Resistance: Unlike metal pipes, which can rust or corrode when exposed to moisture, chemicals, or saltwater, threaded fiberglass pipe is highly resistant to corrosion. This makes it ideal for use in harsh environments, such as chemical processing plants or offshore oil rigs, where other materials may degrade quickly.
- Lightweight and Easy to Install: Fiberglass is significantly lighter than steel or copper, making threaded fiberglass pipe easier to handle, transport, and install. The threaded design further simplifies the installation process, as it eliminates the need for welding or specialized equipment. This reduces labor costs and project timelines, making it a cost-effective solution for many applications.
- Durability and Strength: Despite its lightweight nature, threaded fiberglass pipe is incredibly strong and durable. It can withstand high pressures and extreme temperatures, making it suitable for use in demanding applications, such as oil and gas pipelines or power generation facilities.
- Chemical Resistance: Threaded fiberglass pipe is also resistant to a wide range of chemicals, including acids, alkalis, and solvents. This makes it a preferred material for transporting aggressive substances that would cause traditional metal pipes to fail.
- Low Maintenance: Once installed, threaded fiberglass pipe requires little to no maintenance, as it is not prone to the common issues that affect metal pipes, such as corrosion or scaling. This leads to lower long-term costs and fewer disruptions to operations.
Specific Applications and Industries for Threaded Fiberglass Pipe
Similar to fiberglass tubes, threaded fiberglass pipe is also a high-performance material used in various industrial and commercial applications. Threaded fiberglass pipe is widely used in industries where harsh operating conditions and long-term reliability are critical. Below are some of the most common applications for threaded fiberglass pipe:
- Chemical Processing: In chemical plants, threaded fiberglass pipe is used to transport aggressive chemicals that would corrode traditional metal pipes. Its resistance to acids, bases, and solvents makes it a preferred choice in this industry.
- Oil and Gas: Threaded fiberglass pipe is often utilized in the oil and gas industry, particularly in offshore platforms and pipelines. Its ability to resist saltwater corrosion and handle high pressures makes it ideal for transporting oil, gas, and other petrochemicals.
- Water and Wastewater Treatment: In municipal water treatment facilities, threaded fiberglass pipe is commonly used to convey water, sewage, and industrial waste. The corrosion resistance of the pipe ensures that it remains operational even in harsh environments where metal pipes would degrade.
- Marine Applications: Due to its excellent resistance to saltwater and marine environments, threaded fiberglass pipe is often used in boat building, dock construction, and marine pipelines. Its lightweight design also makes it easy to handle on ships and other vessels.
- Power Generation: In power plants, threaded fiberglass pipe is used to carry cooling water, steam, and other fluids under high pressure and temperature conditions. Its durability ensures long-term performance, even in the most demanding environments.
- Food and Beverage: Threaded fiberglass pipe is also used in the food and beverage industry, where sanitary conditions and resistance to corrosion are critical. The pipe’s smooth interior surface reduces the risk of bacterial growth and contamination.
How Threaded Fiberglass Pipe Compares with Other GangLong Fiberglass Pipe Brands
When choosing between different GangLong Fiberglass products, it’s important to consider the specific needs of your project. Threaded fiberglass pipe offers several advantages over other types of GangLong Fiberglass pipes, particularly in applications where easy installation, corrosion resistance, and strength are required.
However, other GangLong Fiberglass products may offer specialized features that make them better suited for certain environments. For example, GangLong Fiberglass’s Red Thread line offers additional chemical resistance and may be preferred in extremely aggressive chemical environments. Additionally, transparent fiber pipe is an excellent option when visual inspection of the contents is important, as it provides clarity along with the same durability and resistance offered by other fiberglass products. When choosing between different GangLong Fiberglass pipes, consider the operating conditions, required strength, and installation complexity.
Overall, threaded fiberglass pipe from GangLong Fiberglass is a reliable, versatile, and durable option for a wide range of industrial applications, offering significant benefits over traditional materials such as steel and PVC.
Threaded Fiberglass Pipe Sizes
Threaded fiberglass pipes are available in various sizes to meet the diverse needs of industries. The standard sizes typically range from ½ inch to 12 inches in diameter, with customized sizes available upon request from manufacturers like GangLong Fiberglass. These pipes are designed to handle different pressures, with larger diameters being more suitable for high-pressure applications, while smaller sizes are used in low-pressure environments.
The length of threaded fiberglass pipes can also vary, with standard lengths ranging from 10 to 40 feet. The sizing of the pipes is essential to ensure they meet the pressure and flow rate requirements of the system in which they are installed. GangLong Fiberglass provides detailed specifications to help customers select the right pipe size for their applications.
In addition to standard sizes, the wall thickness of threaded fiberglass pipes can also be customized. Thicker walls provide additional strength and durability, particularly in high-pressure applications, while thinner walls are more cost-effective for lower pressure systems. Understanding the specific requirements of your project will help you choose the appropriate pipe size and wall thickness.
Threaded Fiberglass Pipe Fittings
Threaded fiberglass pipe fittings are crucial for the successful installation of the piping system. These fittings allow for the connection, redirection, and termination of the pipes within the system. Common fittings include elbows, tees, couplings, and end caps, each designed to fulfill specific purposes in the pipeline structure.
GangLong Fiberglass offers a wide range of threaded fiberglass pipe fittings to complement their pipe products. These fittings are designed to be as durable and corrosion-resistant as the pipes themselves, ensuring long-term reliability. The ease of connecting and disconnecting threaded fittings allows for maintenance and repairs to be conducted without major disruptions to operations.
It is also important to note that these fittings come in various pressure ratings, just like the pipes. Choosing the correct fittings with matching pressure ratings is essential to maintaining the integrity of the entire system. GangLong Fiberglass provides detailed specifications for each fitting, ensuring proper selection and compatibility with the threaded fiberglass pipes.
Types of Fittings Compatible with Threaded Fiberglass Pipe
The threaded design of fiberglass pipe allows it to be easily connected to a range of fittings that suit various applications. The most common types of fittings compatible with threaded fiberglass pipe include:
- Elbows: Elbow fittings are used to change the direction of flow in a piping system. These fittings come in various angles, such as 45 degrees or 90 degrees, and are threaded to easily connect with the pipe.
- Tees: Tee fittings allow for the splitting or combining of flow within a pipeline. They are often used in applications where different lines need to be connected to a main pipe. With threaded fiberglass pipe, tee fittings make it easy to branch off into multiple lines.
- Couplings: Couplings are used to join two lengths of threaded fiberglass pipe together. These fittings are essential for extending the reach of the piping system while maintaining a secure, leak-proof connection.
- Adapters: Adapters are used to connect threaded fiberglass pipe to other types of piping or equipment. These fittings allow for versatility in system design, enabling connections between different materials or sizes of pipe.
- Caps and Plugs: These fittings are used to close off the end of a threaded fiberglass pipe system, preventing the flow of liquids or gases. They are particularly useful in applications that require temporary or permanent closure of the pipe.
Manufacturers like GangLong Fiberglass provide a wide range of fittings specifically designed for use with their threaded fiberglass pipe products, ensuring compatibility and long-term durability in any environment.
Benefits of Using Fiberglass Fittings in Various Environments
The use of fiberglass fittings with threaded fiberglass pipe offers numerous benefits, particularly in environments where traditional materials may struggle to perform effectively. Some of the key advantages include:
- Corrosion Resistance: One of the most significant benefits of using fiberglass fittings is their resistance to corrosion. Unlike metal fittings, which can rust or corrode when exposed to moisture, chemicals, or saltwater, fiberglass fittings remain unaffected. This makes them ideal for use in chemical plants, water treatment facilities, and marine environments.
- Lightweight: Fiberglass fittings, like the pipes themselves, are much lighter than metal alternatives. This makes them easier to handle during installation and reduces the overall weight of the piping system, which can be beneficial in applications where weight limitations are a concern, such as on offshore oil platforms or in aerospace.
- Durability: Despite being lightweight, fiberglass fittings are incredibly strong and durable. They can withstand high pressures and extreme temperatures, making them suitable for a wide range of industrial applications. The combination of strength and durability ensures that the piping system will perform reliably over time, even in harsh conditions.
- Low Maintenance: Fiberglass fittings, when used with threaded fiberglass pipe, require very little maintenance over their lifetime. The material is resistant to scaling, corrosion, and chemical degradation, which minimizes the need for repairs or replacements. This results in lower overall maintenance costs and less downtime for repairs.
- Chemical Resistance: Fiberglass fittings are highly resistant to a wide range of chemicals, including acids, alkalis, and solvents. This makes them a preferred choice in industries where aggressive substances are being transported, such as chemical processing and pharmaceutical manufacturing.
Applications of Threaded Fiberglass Pipe and Fittings
Threaded fiberglass pipe and its compatible fittings are widely used in a variety of industries due to their durability, corrosion resistance, and versatility. Some of the most common applications include:
- Chemical Processing: In chemical plants, threaded fiberglass pipe and fittings are used to transport highly corrosive chemicals that would quickly degrade traditional metal piping systems. The chemical resistance of fiberglass ensures that the system remains safe and reliable over time.
- Water and Wastewater Treatment: Threaded fiberglass pipe is commonly used in water treatment facilities for transporting both clean water and wastewater. Its resistance to corrosion and scaling makes it ideal for use in these environments, where long-term durability is essential.
- Oil and Gas: In the oil and gas industry, threaded fiberglass pipe is used in applications ranging from onshore pipelines to offshore drilling platforms. The lightweight nature of fiberglass makes it easy to install in remote or hard-to-reach locations, while its resistance to saltwater corrosion ensures reliable performance in marine environments.
- Marine Applications: Fiberglass pipe, including marine fiberglass pipes which are commonly used in the marine industry for transporting seawater, fuel, or other liquids. The resistance to saltwater corrosion, combined with the lightweight nature of the pipe, makes it an ideal choice for shipbuilding and offshore structures.
- Power Generation: Power plants often use threaded fiberglass pipe to transport steam, cooling water, or other fluids under high pressure. The strength and temperature resistance of fiberglass make it well-suited for these demanding applications.
Finding the Right Size and Fittings for Threaded Fiberglass Pipe
Choosing the correct size and fittings for your threaded fiberglass pipe is critical to ensuring optimal performance in your application. Threaded fiberglass pipe is available in a wide range of diameters, lengths, and wall thicknesses, and selecting the right size depends on factors such as the pressure requirements, fluid type, and temperature conditions.
When selecting the size, it’s important to consult the pressure rating and temperature tolerance of the threaded fiberglass pipe. These specifications will help you determine whether the pipe can handle the conditions of your specific application without failing. For example, GangLong Fiberglass offers threaded fiberglass pipe in sizes ranging from small diameters for laboratory setups to large-diameter pipes for industrial use, ensuring that you can find the perfect fit for your project.
In addition to selecting the right pipe size, it’s essential to choose the proper fittings for your threaded fiberglass pipe. Threaded connections make it easy to attach various fittings, such as elbows, tees, and couplings, but it’s important to ensure that these fittings are compatible with the specific type of pipe you are using. GangLong Fiberglass offers a wide range of fittings designed to work seamlessly with their threaded fiberglass pipe products, ensuring a secure and reliable connection.
Threaded Fiberglass Pipe Price
The price of threaded fiberglass pipe is influenced by several factors, including material costs, manufacturing processes, pipe size, and pressure rating. While fiberglass is generally more cost-effective than traditional materials such as steel or copper, the price can still vary based on these factors.
GangLong Fiberglass provides competitive pricing on threaded fiberglass pipes, with cost variations depending on the pipe’s size, length, and wall thickness. Smaller pipes with lower pressure ratings are typically less expensive than larger, high-pressure pipes. Additionally, custom orders with specific size requirements may have higher prices due to the additional manufacturing processes involved.
Despite the initial costs, threaded fiberglass pipe offers long-term cost savings due to its low maintenance requirements and durability. Compared to materials like metal, which can corrode or degrade over time, fiberglass offers a longer service life, reducing the need for frequent replacements or repairs.
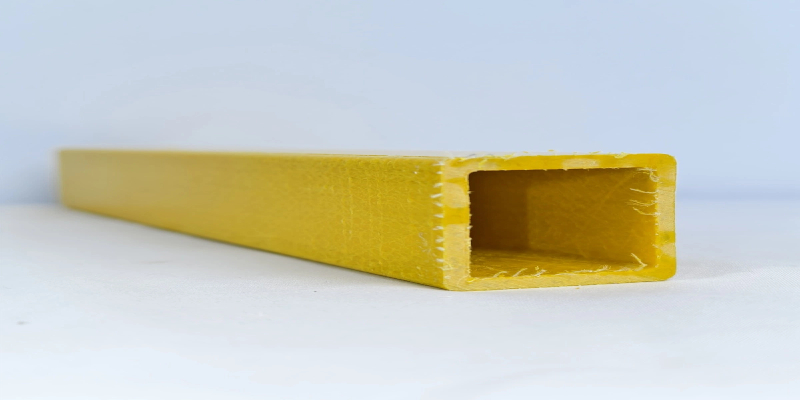
Evaluating Threaded Fiberglass Pipe Prices
The cost of threaded fiberglass pipes is influenced by several factors. First, the price of raw materials such as fiberglass and resin plays a significant role in determining the final price. The cost of these materials fluctuates based on market demand and availability, which in turn affects the overall cost of the pipes.
Another important factor is the manufacturing process. Threaded fiberglass pipes require specialized production techniques, including resin impregnation and heat curing, which can add to the manufacturing costs. Higher quality pipes, such as those offered by GangLong Fiberglass, are subjected to rigorous quality control and testing processes, which may also impact the price.
Comparing the cost efficiency of threaded fiberglass pipes with other materials is essential for industries considering their use. While fiberglass may have a higher initial cost compared to materials like PVC, its long-term benefits, such as durability and low maintenance, often outweigh the initial expense. Over time, industries may find that using fiberglass pipes leads to significant cost savings due to fewer replacements and repairs.
Regional price variations also exist, with the cost of threaded fiberglass pipes differing based on location and transportation expenses. Sourcing pipes locally from suppliers like GangLong Fiberglass can help reduce these costs, as customers can save on shipping and delivery fees.
Regional Price Variations and Sourcing Strategies
Threaded fiberglass pipe prices can vary depending on the region due to factors such as transportation costs, local demand, and availability of raw materials. In regions with high demand for industrial piping, prices may be higher due to increased competition for resources. Conversely, in areas where fiberglass manufacturing facilities are more prevalent, prices may be lower due to reduced transportation costs.
Sourcing strategies also play a critical role in determining the final price of threaded fiberglass pipes. Industries looking to reduce costs can benefit from sourcing pipes from local suppliers, such as GangLong Fiberglass, which can offer more competitive pricing and faster delivery times. Developing long-term supply agreements with manufacturers can also help secure lower prices and ensure a consistent supply of pipes for ongoing projects.
By carefully evaluating regional price variations and sourcing strategies, industries can optimize their procurement processes and minimize costs.
Threaded Fiberglass Pipe Near Me
When sourcing threaded fiberglass pipe, finding a local supplier can reduce shipping costs and lead times. GangLong Fiberglass serves customers across various regions, providing high-quality threaded fiberglass pipes for different applications. Many industries prefer sourcing locally to ensure faster delivery and reduce the environmental impact of long-distance shipping.
GangLong Fiberglass offers a network of distributors and partners that allow customers to easily access their products. Finding a nearby supplier of threaded fiberglass pipes can also offer the benefit of personalized service and faster response times for custom orders. In addition, local suppliers often provide installation services, helping industries set up their piping systems more efficiently.
Threaded Fiberglass Pipe for Sale
For industries looking to purchase threaded fiberglass pipes, GangLong Fiberglass offers a wide selection of products for sale. Their catalog includes various pipe sizes, fittings, and accessories, all designed to meet the specific needs of their customers. GangLong Fiberglass ensures that their products meet industry standards and are tested for quality, ensuring reliability in any application.
When purchasing threaded fiberglass pipes, it is essential to consider factors such as the required pipe size, pressure rating, and fittings. GangLong Fiberglass provides consultation services to help customers choose the best products for their projects. By offering pipes for sale directly from the manufacturer, GangLong Fiberglass ensures competitive pricing and consistent quality control.
Additionally, customers can explore discounts for bulk purchases or long-term supply agreements. Buying in bulk from GangLong Fiberglass not only reduces costs but also ensures that industries have a reliable supply of pipes and fittings for their ongoing projects.
Red Thread Fiberglass Pipe
Red Thread fiberglass pipe is a specialized type of threaded fiberglass pipe designed for demanding industrial applications, known for its distinctive red color and exceptional durability. This pipe type is often used in industries such as oil and gas, chemical processing, and water treatment, where it must endure harsh environments and handle corrosive materials. Manufactured with advanced techniques and engineered to withstand high-pressure and high-temperature conditions, Red Thread fiberglass pipe offers a reliable and durable solution for fluid transport in complex piping systems. Below, we dive into the key features and benefits of this innovative piping solution.
Superior Durability and Strength
The primary feature of Red Thread fiberglass pipe is its superior durability, which makes it highly reliable in environments that challenge other materials. Fiberglass itself is known for its resistance to corrosion, ensuring that the Red Thread pipe will not deteriorate when exposed to harsh chemicals or extreme temperatures. This makes it an ideal choice for industries such as chemical processing, where pipelines must safely transport a variety of aggressive substances. The Red Thread fiberglass pipe is also resistant to UV degradation, so it performs well even in outdoor installations that are subject to sunlight and weather fluctuations.
Additionally, the pipe is filament-wound, which enhances its strength and structural integrity, making it able to withstand high-pressure conditions commonly found in oil and gas industries. The reinforcement with a resin-rich liner and surface veil provides additional protection against wear and tear, extending the overall lifespan of the system.
Customization and Versatility
Red Thread fiberglass pipe is available in a wide range of sizes and pressure ratings, allowing it to be tailored to specific application needs. Whether for transporting high-temperature liquids, gas, or produced water, these pipes can be customized to handle the unique requirements of each installation. With varying pressure ratings, industries can select the right type of pipe for the specific flow rate and pressure conditions of their operation. This versatility also extends to its use in diverse environments, including underground fuel handling, water treatment facilities, and other industrial settings where both strength and corrosion resistance are paramount.
Visual Indicator for Identification
One of the key benefits of Red Thread fiberglass pipe is its distinctive red color, which serves as a visual indicator of its unique properties. The red color helps workers easily identify these pipes in complex piping systems, ensuring that the correct materials are being used for the appropriate applications. In large industrial facilities or intricate pipeline networks, this visual cue is particularly valuable for safety, maintenance, and troubleshooting.
The red color also adds to the aesthetic quality of the system, which is important in environments where appearance and functionality are both considered. This color-coding system enhances efficiency in both the installation and maintenance phases, helping technicians quickly locate and assess the pipes when necessary.
Manufacturing Excellence
GangLong Fiberglass, a leading manufacturer of Red Thread fiberglass pipes, uses advanced manufacturing techniques to produce pipes that meet the highest industry standards. The pipes undergo rigorous quality control processes to ensure that each product is capable of withstanding extreme conditions. The use of amine-cured epoxy resin combined with high-quality glass fibers makes these pipes resistant to a wide range of chemicals and pressures. The filament-wound design also ensures uniformity and reliability in the final product, ensuring that every pipe performs at its best over its long lifespan.
Proven Performance in Harsh Environments
Red Thread fiberglass pipe has a proven track record in industries that demand the highest level of performance from their piping systems. In the oil and gas industry, these pipes are trusted for transporting corrosive substances under high pressure, where failure is not an option. Similarly, chemical processing plants rely on the durability of Red Thread fiberglass pipes for safe and efficient fluid transport. Their resistance to corrosion and extreme conditions ensures that they maintain their integrity and function in even the most challenging environments. This proven performance history provides peace of mind for industries that rely on the continued operation of their piping systems.
Red Thread fiberglass pipe offers industries a versatile, durable, and reliable solution for fluid transport in harsh and demanding environments. With its superior resistance to corrosion, customizable size and pressure ratings, visual identification features, and proven performance, Red Thread fiberglass pipe is a top choice for sectors such as oil and gas, chemical processing, and water treatment. Manufactured using advanced techniques, these pipes meet the highest industry standards, providing a long-lasting and dependable solution for a variety of fluid transport needs.
Top Benefits of Using Silicone Fiberglass Tube in Equipment
Importance of Choosing Certified Dealers for Threaded Fiberglass Pipe
Choosing certified dealers when purchasing threaded fiberglass pipe is essential for several reasons. Certified dealers ensure that the products you are buying meet all relevant safety and quality standards. These dealers are typically trained by the manufacturer, such as GangLong Fiberglass, to provide accurate product information, technical support, and proper installation guidelines.
Certified dealers are more likely to offer a wider selection of genuine products and can provide you with detailed information about the specific properties of the pipes, including their chemical resistance, pressure ratings, and performance in various environments. When buying from uncertified sources, you run the risk of receiving counterfeit or substandard products that may not perform as expected, leading to costly repairs or replacements down the line.
Certified dealers also typically offer warranties and after-sales support, ensuring that any issues you may encounter with your threaded fiberglass pipe are promptly addressed. This added security makes certified dealers a safer and more reliable choice for purchasing threaded fiberglass pipe, especially for large-scale industrial projects.
Tips for Locating Threaded Fiberglass Pipe Suppliers in Local Markets
When searching for threaded fiberglass pipe in your local area, finding reputable suppliers is critical to ensuring that the product you purchase meets industry standards. The first step in locating suppliers is to conduct thorough research. Begin by checking local directories and online platforms for suppliers that specialize in fiberglass products or piping systems. Look for businesses that have been in operation for a number of years and have built a reputation for quality and reliability.
Visiting trade shows or industry-specific events can also be a useful way to meet with suppliers face-to-face and assess the range of products they offer. You may also want to consult with engineers or professionals who have experience in selecting and installing threaded fiberglass pipe for recommendations on the best local suppliers.
Another helpful tip is to inquire directly with manufacturers like GangLong Fiberglass about authorized distributors in your area. Many manufacturers maintain lists of certified dealers, ensuring that you get the highest-quality products and access to any warranties or technical support the manufacturer may offer.
How to Evaluate the Quality of Threaded Fiberglass Pipe Locally
Evaluating the quality of threaded fiberglass pipe before making a purchase is crucial to ensure that you are getting a product that will meet your specific requirements. The first step in assessing quality is to review the specifications provided by the supplier. You should check the pressure ratings, temperature tolerance, and chemical resistance of the threaded fiberglass pipe to ensure that it is suitable for the intended application. Many manufacturers, including GangLong Fiberglass, offer detailed technical data sheets that outline the performance characteristics of their pipes.
Another key factor to evaluate is the manufacturing process used to produce the threaded fiberglass pipe. High-quality pipes are typically produced using advanced techniques that ensure a uniform resin-to-glass ratio, providing strength and durability. Ask your supplier about their manufacturing standards and certifications, such as ISO or ASTM compliance, to ensure that their products meet international quality benchmarks.
Inspecting the pipes physically can also provide valuable insights into their quality. Look for any signs of defects, such as cracks, uneven surfaces, or weak threading, which may indicate poor manufacturing practices. It’s also essential to ensure that the threads are clean and well-formed, as poorly threaded ends can lead to leaks or weak connections during installation.
Finally, it’s a good idea to ask for references or reviews from previous customers who have used the same product. This can give you a sense of how the threaded fiberglass pipe has performed in real-world applications and whether the supplier has a good track record for delivering quality products.
Maintenance Threaded Fiberglass Pipe
Threaded fiberglass pipes are a popular choice across many industries due to their unique properties, including exceptional durability, resistance to corrosion, and minimal maintenance needs. These characteristics make them a highly practical and cost-effective option for industries that require long-lasting and low-maintenance piping solutions. Unlike traditional metal pipes that can corrode over time and require frequent repairs or replacements, threaded fiberglass pipes offer a much more reliable solution. This article will explore the various aspects of maintaining threaded fiberglass pipes, discussing their longevity, resistance to environmental stressors, and how their performance impacts industrial settings where minimal maintenance is critical.
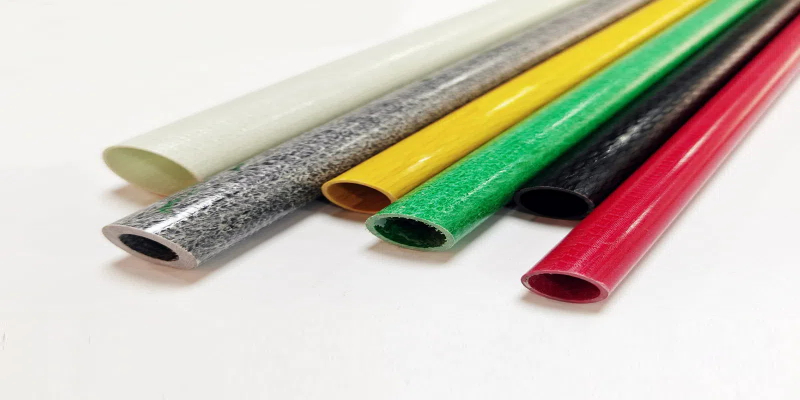
Longevity and Durability: Reduced Maintenance Over Time
One of the most significant advantages of threaded fiberglass pipe is its outstanding longevity. This material is designed to last for decades, far exceeding the lifespan of traditional metal pipes. The inherent properties of fiberglass—such as its resistance to corrosion, scaling, and degradation from harsh chemicals—ensure that these pipes maintain their integrity over extended periods without the need for constant repairs. In addition to corrosion resistance, fiberglass pipes are also designed to withstand temperature fluctuations and UV exposure, making them versatile for both indoor and outdoor applications. As a result, industries such as oil and gas, water treatment, and chemical processing benefit from the reduced need for maintenance and repair activities, allowing operations to continue without interruptions.
Corrosion Resistance: Minimizing the Need for Regular Inspections
Traditional piping materials such as steel, copper, and cast iron are prone to corrosion when exposed to moisture, chemicals, or extreme environmental conditions. This corrosion can cause leaks, weakening of the pipes, and potential system failures. Threaded fiberglass pipes, however, are highly resistant to corrosion due to the unique properties of fiberglass material. These pipes do not rust or deteriorate when exposed to water, moisture, or chemical compounds. This makes them ideal for use in environments where corrosion is a significant concern, such as in chemical plants, sewage systems, and marine applications. With minimal corrosion risk, threaded fiberglass pipes require far fewer inspections and repairs compared to metal alternatives, reducing overall maintenance costs.
Resistance to Abrasion and Mechanical Wear
Threaded fiberglass pipes excel in environments where pipes are subject to mechanical wear and abrasive materials. Fiberglass is a highly durable material that resists abrasion, meaning the pipes are less likely to suffer from damage due to physical impacts or the passage of abrasive substances through the pipe. In industries like mining, construction, and material handling, pipes often come into contact with rough or abrasive materials that can cause severe wear on traditional pipe systems. With threaded fiberglass pipes, companies experience less downtime due to pipe failures or repairs caused by abrasion. The added resistance to mechanical wear extends the lifespan of the pipes, ensuring continued, efficient operation without frequent maintenance requirements.
Low Maintenance Requirements: Minimizing Operational Interruptions
One of the most significant benefits of threaded fiberglass pipe is its minimal need for maintenance, which translates into fewer operational interruptions. In industries where downtime is costly, the durability of fiberglass pipes becomes a major advantage. Since these pipes are resistant to corrosion, abrasion, and other environmental stresses, they typically do not require the regular inspections, repairs, or replacements that metal pipes might need. This low-maintenance characteristic helps companies save on labor costs, repair materials, and the potential cost of system shutdowns. Furthermore, when maintenance is needed, it tends to be less frequent and simpler, as fiberglass pipes are less prone to common issues like leaks or blockages.
Environmental Considerations: Sustainability and Reduced Maintenance Impact
Threaded fiberglass pipes also offer advantages from an environmental perspective. Because they have a longer lifespan and require less maintenance, the frequency of replacements is reduced. This leads to less material waste over time, making fiberglass pipes a more sustainable option compared to their metal counterparts, which often need to be replaced more regularly. Moreover, the durability and corrosion resistance of fiberglass pipes help reduce the need for toxic or harmful chemical treatments often necessary with metal pipes to prevent degradation. This makes threaded fiberglass pipes a more eco-friendly choice, supporting both operational efficiency and environmental sustainability.
Threaded fiberglass pipes stand out as a durable, low-maintenance piping solution suitable for various industrial applications. Their resistance to corrosion, mechanical wear, and abrasions reduces the frequency of repairs and inspections, making them a cost-effective option for industries where minimizing downtime is critical. With a lifespan that extends decades, fiberglass pipes provide long-term value, ensuring reliable performance in even the harshest environments. This minimal maintenance requirement, coupled with their resistance to environmental stressors, makes threaded fiberglass pipe an excellent choice for businesses looking to reduce operational costs and enhance system reliability.
Future Trends in the Use of Threaded Fiberglass Pipe
The demand for more cost-effective, environmentally friendly, and high-performing piping solutions is driving significant growth in the use of threaded fiberglass pipe and fiberglass composite tube. Over the coming years, industries are expected to adopt these solutions more widely, thanks to innovations in materials, manufacturing processes, and application technologies. As the need for robust and reliable piping systems increases in sectors like oil and gas, chemical processing, and water treatment, advancements in composite materials and threading technology will further enhance the performance, strength, and ease of installation of these piping solutions. Below, we explore the key future trends that will shape the use of threaded fiberglass pipe in the near future.
Advancements in Composite Materials
The use of composite materials in threaded fiberglass pipes is expected to be one of the most significant developments in the coming years. The incorporation of advanced composite materials can enhance the strength, durability, and overall performance of fiberglass pipes. Fiberglass composite tubes, for instance, may incorporate resins and fibers designed to withstand even harsher conditions, including more aggressive chemicals, higher temperatures, and extreme pressure environments. By combining fiberglass with other high-performance materials, manufacturers can produce pipes that are both stronger and lighter, reducing the need for heavy construction equipment during installation while increasing the lifespan of the pipes in demanding applications.
This trend also reflects an increased interest in eco-friendly materials. Manufacturers are exploring sustainable resins and fibers to create more environmentally conscious fiberglass pipes without sacrificing performance. As environmental regulations become stricter, the adoption of greener composite materials in the production of threaded fiberglass pipes and fiberglass composite tubes will continue to rise, aligning with the global shift toward sustainability.
Improved Threading and Connection Technology
As the demand for reliability and ease of installation grows, improvements in threading technology are expected to enhance the overall functionality of threaded fiberglass pipes. The traditional threading process is already efficient, but future advancements may allow for even more secure and reliable connections. Innovations in this area could include threading systems that provide superior sealing capabilities and resistance to wear, preventing leaks or failures that could occur under high pressure or in corrosive environments.
Furthermore, the threading process could become faster and more automated, streamlining the manufacturing process and reducing costs. Enhanced thread designs may also improve the performance of fiberglass composite tubes, offering higher connection integrity in applications such as underground fuel handling and water transport. These improvements will make the installation process even simpler and more efficient, potentially leading to reduced labor costs and faster project timelines.
Enhanced Durability and Resistance
The durability of threaded fiberglass pipes is already one of their key selling points, but future trends suggest that even greater resistance to corrosion, abrasion, and environmental stress will be developed. New coating technologies and more robust internal linings are expected to enhance the resistance of these pipes to chemicals, saltwater, and other corrosive substances. Fiberglass composite tubes, in particular, will benefit from these innovations, as composite materials can be tailored to resist specific environmental conditions more effectively than traditional fiberglass alone.
Additionally, greater attention will be given to the performance of fiberglass pipes in extreme temperature fluctuations and high-pressure systems. The pipes may be engineered with materials capable of handling temperature changes that could otherwise cause damage to other pipe materials. As a result, threaded fiberglass pipes will become even more versatile, capable of performing reliably in industries such as petrochemical processing, marine infrastructure, and industrial wastewater systems.
Integration with Smart Technologies
Another future trend in threaded fiberglass pipe usage is the integration with smart technologies. As industries increasingly adopt digital solutions for monitoring and maintenance, there is potential for fiberglass pipes to be equipped with embedded sensors that monitor pressure, temperature, and chemical composition in real-time. These sensors could provide valuable data to ensure that the pipes are operating within safe parameters, alerting maintenance teams to potential issues before they become critical. This will help extend the life of the pipes, reduce downtime, and enhance the safety of critical systems.
Fiberglass composite tubes, in particular, could play a crucial role in smart infrastructure, where real-time data and automated systems are essential for monitoring and maintaining operational efficiency. The combination of smart sensors with the inherent benefits of fiberglass pipes would create a next-generation piping solution for various industrial applications.
Expansion into New Industries
As threaded fiberglass pipe technology continues to evolve, we can expect to see its adoption spread into industries that were previously dominated by traditional pipe materials like steel or PVC. The enhanced properties of fiberglass pipes—such as resistance to corrosion, lighter weight, and ease of installation—make them an attractive option for infrastructure projects, including sewage and stormwater management, underground fuel systems, and district heating networks.
The cost-effectiveness and versatility of fiberglass pipes, along with their long-term performance advantages, will drive their adoption in these new sectors. As more industries recognize the advantages of using fiberglass composite tubes for fluid transport, the demand for threaded fiberglass pipes will continue to grow, further solidifying their place as a preferred solution in many industrial applications.
The future of threaded fiberglass pipes looks promising, with ongoing advancements in composite materials, threading technology, and overall durability expected to enhance their performance and expand their use in diverse industries. With the potential for lighter, stronger, and more environmentally friendly solutions, as well as smarter and more efficient installation processes, threaded fiberglass pipes and fiberglass composite tubes will play an increasingly critical role in fluid transport systems. These innovations are set to improve the reliability, efficiency, and sustainability of industrial piping infrastructure, ensuring that threaded fiberglass pipe remains a leading choice for complex and demanding applications.
Installation Tips and Best Practices for Threaded Fiberglass Pipe
Proper installation is essential to ensure the long-term performance of threaded fiberglass pipe. Following best practices during the installation process will help to avoid issues such as leaks, pressure drops, or pipe damage. Here are some important tips to consider:
- Inspect Threads Before Installation: Before connecting any fittings to the threaded fiberglass pipe, inspect the threads carefully for any signs of damage or debris. Damaged or dirty threads can lead to poor connections and potential leaks. Clean the threads thoroughly and ensure that they are in good condition before proceeding with installation.
- Use Appropriate Sealants: While the threads on fiberglass pipe provide a secure connection, as with threaded fiberglass rods, it is important to use the appropriate sealant to ensure a leak-proof joint. Thread sealants, such as PTFE tape or pipe thread compound, should be applied to the threads before connecting the fittings. This helps to create a tight seal and prevent leaks.
- Avoid Over-Tightening: When connecting fittings to threaded fiberglass pipe, it’s important not to over-tighten the joints. Over-tightening can damage the threads or even crack the fiberglass material. Tighten the fittings by hand and then use a wrench to make a final adjustment, ensuring a snug fit without excessive force.
- Support the Pipe Properly: Fiberglass pipe, though lightweight, still requires proper support to prevent sagging or stress on the joints. Install pipe supports at regular intervals to ensure that the pipe remains properly aligned and supported throughout its length. This is particularly important in long runs of pipe or in vertical installations.
- Allow for Expansion and Contraction: Like all materials, fiberglass pipe will expand and contract with changes in temperature. When designing and installing the piping system, it’s important to account for this by including expansion joints or flexible connections in areas where temperature fluctuations are expected.
- Test the System After Installation: Once the threaded fiberglass pipe and fittings have been installed, it’s important to test the system for leaks and pressure integrity. Perform a pressure test by running the system at its expected operating pressure and inspecting for any signs of leaks or weak connections. Address any issues immediately before placing the system into full operation.
Key Advantages of Using Hollow Fiberglass Tube in Construction
FAQs about Threaded Fiberglass Pipe
Plastic pipes, including PVC and polyethylene pipes, typically need to be replaced after 25 to 40 years, depending on factors such as environmental conditions, usage, and maintenance. While plastic pipes are resistant to corrosion, they can degrade over time due to exposure to UV light, chemical reactions, and physical stress. For instance, UV radiation can weaken the material, leading to brittleness and cracking. Additionally, factors like water pressure, temperature fluctuations, and ground movement can accelerate wear. Regular inspections and proper maintenance can extend the life of plastic pipes, but eventually, they will need to be replaced as they approach the end of their lifespan. Fiberglass pipes, on the other hand, often outlast plastic pipes, making them a more durable choice for long-term use in various applications.
The thickness of fiberglass pipes varies depending on the application and manufacturer. Generally, threaded fiberglass pipes range from 0.25 inches (6.35 mm) to over 1 inch (25 mm) in wall thickness. Thicker pipes are typically used for high-pressure or high-temperature applications where additional strength and insulation are required. The wall thickness is often determined by factors such as the pipe’s intended use, the materials it will carry, and the operating pressure it must withstand. Fiberglass pipes are often designed to be durable and capable of withstanding corrosive environments, so their thickness is optimized for these conditions. The ability to customize the thickness of fiberglass pipes for different needs makes them versatile for a wide range of industrial and infrastructure projects.
Fiberglass pipe is favored in various industries for its combination of durability, lightweight design, and corrosion resistance. Unlike traditional materials such as steel or PVC, fiberglass pipes do not rust or degrade when exposed to harsh chemicals, water, or extreme weather conditions, making them ideal for chemical plants, water treatment facilities, and underground pipelines. The strength-to-weight ratio of fiberglass is also impressive, making it easier and more cost-effective to transport and install compared to heavier pipe materials. Additionally, fiberglass offers superior insulation properties, which can help reduce energy costs in industrial applications. The use of fiberglass pipes also reduces the need for frequent repairs and replacements, leading to long-term cost savings. With their reliability and low maintenance requirements, fiberglass pipes are a trusted solution for many piping needs.
The longest-lasting pipe material is typically fiberglass. Fiberglass pipes are highly resistant to corrosion, chemical degradation, and other environmental factors that can deteriorate other materials like steel or PVC. Under ideal conditions, fiberglass pipes can last 50 to 75 years or longer. In comparison, steel pipes are prone to rust, and PVC pipes, while durable, have a lower lifespan of around 25 to 40 years due to their susceptibility to UV degradation and impact damage. Additionally, materials like copper and concrete have shorter lifespans due to corrosion and wear over time. Fiberglass’s resistance to environmental stressors, coupled with its strength, makes it the longest-lasting pipe material for a wide range of applications, especially in industries that deal with harsh chemicals or high temperatures.
Fiberglass pipe insulation is generally safe when installed and handled properly. It is commonly used to prevent heat loss, reduce energy costs, and protect against freezing temperatures. However, it is important to take precautions during installation and maintenance because fiberglass insulation can irritate the skin, eyes, and respiratory system. Wearing protective gear such as gloves, safety goggles, and a dust mask is crucial to avoid exposure to airborne fiberglass particles. Additionally, while fiberglass itself is non-combustible, it’s important to ensure that the insulation material is installed according to fire safety standards to avoid potential hazards. In conclusion, fiberglass pipe insulation is safe when handled with care and proper protective measures are followed.
Fiberglass pipe, including threaded fiberglass pipes, is renowned for its durability and long lifespan. On average, fiberglass pipes can last 50 to 75 years or even longer when properly maintained. The material is resistant to corrosion, which is a major factor in pipe degradation over time. Unlike metal pipes that are vulnerable to rust and chemical reactions, fiberglass remains unaffected by most corrosive substances, making it an excellent choice for industries such as chemical processing, water treatment, and wastewater management. However, environmental factors such as extreme temperatures or physical damage may shorten the pipe’s lifespan. Overall, the combination of resistance to corrosion, reduced maintenance needs, and strength makes threaded fiberglass pipe a long-lasting solution for various applications.
Yes, fiberglass can be used to repair PVC pipes, especially in cases where the pipe has a small crack, leak, or damage. Fiberglass repair kits are commonly used for this purpose and involve applying a resin-impregnated fiberglass cloth or tape over the damaged area. The resin hardens after application, forming a durable, waterproof, and strong bond that seals the crack. However, it’s important to ensure the pipe is dry and clean before applying the fiberglass repair. While fiberglass provides a temporary or emergency repair, it is not a long-term solution. Depending on the severity of the damage, it’s often best to replace the damaged section of the PVC pipe entirely.
Both foam and fiberglass pipe insulation have their advantages, and the better option depends on the application. Foam insulation is lighter, more flexible, and easier to install, making it a good choice for residential and low-temperature environments. It’s also cost-effective and provides decent thermal protection. Fiberglass pipe insulation, however, offers superior heat resistance and durability, making it ideal for high-temperature applications or industrial settings. It’s fire-resistant and provides better insulation against heat loss. If you’re looking for insulation for pipes exposed to high temperatures, fiberglass is generally the better choice. For lower-temperature or residential applications, foam can be an adequate, cost-efficient solution.
The R-value of fiberglass pipe insulation typically ranges from R-3 to R-15, depending on the thickness and type of insulation. The R-value measures the material’s resistance to heat flow, with higher values indicating better insulation. A 1-inch thick fiberglass insulation typically offers an R-value of about R-3 to R-4. For higher temperature applications or colder climates, a thicker layer of insulation with a higher R-value may be necessary to provide adequate thermal protection. The R-value is an important factor to consider when selecting insulation, as it directly influences energy efficiency and the ability to maintain consistent temperatures in pipes.
Fiberglass pipe insulation is water-resistant to a certain extent, but it can still absorb moisture if exposed to high humidity or water. When fiberglass insulation gets wet, it loses much of its thermal resistance and can become a breeding ground for mold and mildew. To avoid these issues, fiberglass insulation should be kept dry. For outdoor or humid environments, fiberglass pipe insulation often comes with a vapor barrier or jacketing, which helps prevent moisture from penetrating. If the insulation gets wet, it should be removed and replaced to ensure its thermal performance and to prevent long-term damage to the pipe system.
Yes, fiberglass insulation can help keep pipes from freezing, especially when combined with other protective measures. Fiberglass pipe insulation works by slowing down heat transfer, helping to maintain the temperature within the pipes. In colder climates, it can be effective in preventing freezing by reducing the likelihood of temperature drops in exposed pipes. However, it’s important to note that fiberglass insulation alone may not provide sufficient protection during extremely cold temperatures or if pipes are located in unheated areas like basements or attics. To maximize freeze protection, it’s recommended to use fiberglass insulation along with pipe heating cables or consider additional layers of insulation.
Fiberglass pipe insulation is highly heat-resistant, typically capable of withstanding temperatures between -20°F to 1000°F (-29°C to 538°C). This wide range of temperatures makes it suitable for a variety of piping systems, including steam, hot water, and even cryogenic pipes. Fiberglass insulation is often used for high-temperature industrial applications, where it helps maintain consistent temperatures and prevents energy loss. However, the exact temperature tolerance can vary depending on the type of fiberglass used and any additional coatings or treatments applied to the material. Always check the manufacturer’s specifications for maximum temperature limits before installing fiberglass pipe insulation in extreme conditions.
Fiberglass pipe insulation is not foam; they are two distinct materials with different properties. Fiberglass pipe insulation consists of fine glass fibers bound together in a blanket or rigid form. It provides excellent thermal resistance, soundproofing, and fire resistance. On the other hand, foam pipe insulation is made of a variety of materials, such as polyethylene, neoprene, or polyurethane, and it is typically lighter and more flexible than fiberglass. Fiberglass insulation is more durable and often preferred for high-temperature applications due to its superior heat resistance. While foam insulation is better for simple home use and provides a quick installation, fiberglass pipe insulation is typically more effective in industrial settings, especially where higher insulation values or fire resistance are required.
The thickness of fiberglass pipe insulation generally depends on the pipe’s diameter and the environment in which it’s used. For typical residential or commercial pipes, the insulation thickness ranges from 1 inch to 3 inches. For pipes exposed to extreme temperature fluctuations or requiring greater thermal resistance, a thicker insulation layer is recommended. A 1-inch layer may suffice for pipes in moderate climates, while thicker layers (2-3 inches) provide better insulation in colder areas, ensuring energy efficiency and reducing the risk of freezing. The required thickness also depends on the desired R-value (thermal resistance), with thicker insulation offering a higher R-value, which improves thermal performance. Always check local building codes and energy guidelines, as they may dictate specific insulation requirements.
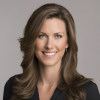
As the editor of GangLong Fiberglass, I have years of experience and in-depth research, focusing on cable tray products, fiberglass solutions, and grille systems. I incorporate years of industry insights and practical experience into every content, committed to promoting the progress of the industry. At GangLong Fiberglass, my commitment is reflected in every product, from innovative cable trays to durable fiberglass solutions and sturdy grille systems. As an authoritative voice in the industry, my goal is to provide valuable information to professionals and businesses and promote forward-looking solutions.